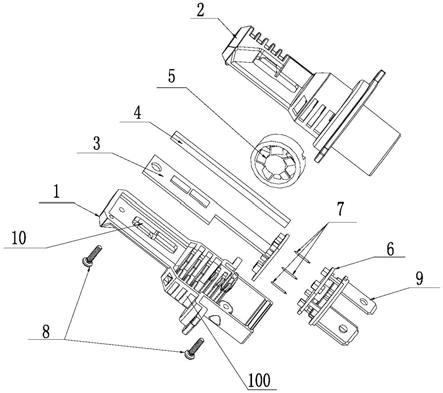
一种一体化led汽车灯
技术领域
[0001]
本实用新型涉及电光源的技术领域,特别是一种一体化led汽车灯。
背景技术:[0002]
现有led汽车车灯普遍存在以下缺点:
[0003]
1、产品大多由灯体、外置驱动、连接线和接插头构成,安装时占用空间大,部分可能无法安装,且外置驱动、连接线不易紧固,容易因颠簸磨损产生线路损坏、甚至短路起火等风险。
[0004]
2、现有的一体化led汽车灯,由于结构尺寸限制,导热、散热设计均不够优化,存在led工作温度高、光效低、实际寿命短、可靠性差等问题。
[0005]
现有的一体化led汽车灯,为了保证散热,大多尺寸会超出法规限制,会出现部分车型无法安装,甚至影响配光达不到法规要求给安全行车带来影响。
技术实现要素:[0006]
本实用新型的目的就是解决现有技术中的问题,提出一种一体化led汽车灯,整体结构紧凑、导热散热效率高,能够实现led车灯的高光效、长寿命和高可靠性。
[0007]
为实现上述目的,本实用新型提出了一种一体化led汽车灯,包括左灯体、右灯体、光源组件、超导热管、风扇、驱动组件、紧固螺丝、电源插头,所述左灯体、右灯体通过若干个紧固螺丝组合构成的灯体,所述光源组件、超导热管安装于灯体的内腔中,所述光源组件上设有led光源,所述左灯体、右灯体上与led光源相对应的位置设有出光口,所述灯体的尾部具有散热部,所述散热部的内部设有若干个鳍片,所述超导热管的尾部固定于散热部上,所述散热部的内腔中安装有风扇,所述灯体的尾部安装有驱动组件和电源插头。
[0008]
作为优选,所述左灯体、右灯体呈对称设置,所述灯体的内腔中具有并列布置的光源安装槽和导热管安装槽,所述光源组件、超导热管分别安装于光源安装槽、导热管安装槽中,所述超导热管设置于光源组件距离led光源较近的一侧。
[0009]
作为优选,所述散热部的内部设有若干个采用截面垂直分布的鳍片,所述鳍片与灯体几何中心线相垂直,相邻的鳍片之间开设有散热出风孔,所述散热部与超导热管相连一侧的鳍片上设有导热管卡槽,另一侧设有风扇安装槽,所述风扇安装于风扇安装槽内,所述鳍片由风扇安装槽分隔于灯体的两侧,具有导热管卡槽的一侧鳍片的长度大于另一侧鳍片的长度。
[0010]
作为优选,所述鳍片为弧形,所述散热部上具有导热管卡槽一侧的最后一片鳍片上开设导风道,所述导风道设置于导热管卡槽的后方。
[0011]
作为优选,所述风扇外轮廓为圆形或近似圆形,所述风扇安装槽设置于灯体几何中心偏心一侧,所述风扇的吹风方向为朝向超导热管一侧方向。
[0012]
作为优选,所述光源组件包括光源板和驱动子板,所述光源板上具有供紧固螺丝穿出的安装孔,所述驱动组件与驱动子板通过软线相连接,所述驱动组件与电源插头相焊
接固定,所述驱动子板的两侧具有采用削边处理形成的第一削边部,所述驱动组件的两侧具有采用削边处理形成的第二削边部。
[0013]
作为优选,所述灯体的前端还安装有卡扣,所述卡扣内与灯体相抵靠的一侧具有密封环槽,所述密封环槽内安装有硅胶圈。
[0014]
作为优选,所述风扇安装于散热部的尾端,所述风扇的吹风方向为朝向灯体前端方向,所述风扇的外轮廓采用方形或近似方形。
[0015]
作为优选,所述散热部的内部设有若干个采用水平分布鳍片,所述鳍片与灯体几何中心线相平行,相邻的鳍片之间开设有散热出风孔。
[0016]
作为优选,所述驱动组件水平设置,与鳍片相平行,所述光源组件为双面铜基板,所述光源组件与驱动组件采用板对板焊接固定,所述驱动组件与电源插头通过软线相连接。
[0017]
本实用新型的有益效果:本实用新型采用优化的一体化结构设计,具有结构紧凑、导热散热效率高的特点。外形尺寸符合法规要求,可以实现所有按照法规要求设计车灯的无损替换;安装便捷,无需辅助工具或额外接线;导、散热效率高,可以保证led工作于安全结温,实现led车灯的高光效、长寿命和高可靠性。对配光影响小,可以有效保证配光符合法规要求,保证行车安全。
[0018]
本实用新型的特征及优点将通过实施例结合附图进行详细说明。
附图说明
[0019]
图1是本实用新型实施例1的爆炸示意图;
[0020]
图2是本实用新型实施例1的左灯体的立体结构示意图;
[0021]
图3是本实用新型实施例1的左灯体的主视示意图;
[0022]
图4是本实用新型实施例1的光源组件的立体结构示意图;
[0023]
图5是本实用新型实施例1的驱动组件的立体结构示意图;
[0024]
图6是本实用新型实施例2的爆炸示意图。
具体实施方式
[0025]
实施例1
[0026]
参阅图1至图5本实用新型一种一体化led汽车灯,包括左灯体1、右灯体2、光源组件3、超导热管4、风扇5、驱动组件6、紧固螺丝8、电源插头9,所述左灯体1、右灯体2通过若干个紧固螺丝8组合构成的灯体,所述光源组件3、超导热管4安装于灯体的内腔中,所述光源组件3上设有led光源,所述左灯体1、右灯体2上与led光源相对应的位置设有出光口10,所述灯体的尾部具有散热部100,所述散热部100的内部设有若干个鳍片1001,所述超导热管4的尾部固定于散热部100上,所述散热部100的内腔中安装有风扇5,所述灯体的尾部安装有驱动组件6和电源插头9。
[0027]
本实施例1中采用远近光一体的双光设计方案,参阅图1至图3,所述左灯体1、右灯体2呈对称设置,所述灯体的内腔中具有并列布置的光源安装槽101和导热管安装槽102,所述光源组件3、超导热管4分别安装于光源安装槽101、导热管安装槽102中,优化的引入超导热管4进行高效的导热、散热,所述超导热管4设置于光源组件3距离led光源较近的一侧。
[0028]
进一步地,采用优化的散热鳍片设计:为保证结构尺寸不超出法规限制,散热鳍片采用内置设计,针对不同灯体采用不同的强制对流散热优化设计,在本实施例1中,所述散热部100的内部设有若干个采用截面垂直分布的鳍片1001,所述鳍片1001与灯体几何中心线相垂直,相邻的鳍片1001之间开设有散热出风孔,所述散热部100与超导热管4相连一侧的鳍片上设有导热管卡槽1002,另一侧设有风扇安装槽1003,所述风扇5安装于风扇安装槽1003内,所述鳍片1001由风扇安装槽1003分隔于灯体的两侧,具有导热管卡槽1002的一侧鳍片1001的长度大于另一侧鳍片1001的长度。鳍片1001采用沿截面垂直分布,同时采用在超导热管侧长、对侧短的设计,有利于最大化利用热管的超导热能力,如图2和图3所示。
[0029]
进一步地,为优化驱动散热,鳍片1001设计为弧形,所述散热部100上具有导热管卡槽1002一侧的最后一片鳍片1001上开设导风道14,所述导风道14设置于导热管卡槽1002的后方。配合驱动散热优化设计为驱动提供散热优化。
[0030]
进一步地,优化的风扇强制对流散热:在本实施例1中风扇5外轮廓为圆形或近似圆形,所述风扇安装槽1003设置于灯体几何中心偏心一侧,所述风扇5的吹风方向为朝向超导热管4一侧方向。当采用厚度6mm风扇5时,风扇安装槽1003中心优化的偏心距离为距离灯体几何中心约4mm。
[0031]
进一步地,采用优化的驱动散热设计:在本实施例1中,驱动优化的设计位两部分,主要器件均设计在驱动组件6上,后级控制电路设计在光源组件3上的驱动子板32上,以分散发热器件,提高散热效率。
[0032]
更进一步地,采用优化的连接线设计:采用板对板硬连接与软线连接相结合的设计在简化工艺的同时提高焊接误差容许。具体的,参阅图4和图5,所述光源组件3包括光源板31和驱动子板32,所述光源板31上具有供紧固螺丝8穿出的安装孔,所述驱动组件6与驱动子板32通过软线7相连接,所述驱动组件6与电源插头9相焊接固定,可以有效防止因焊接位置偏差产生的无法安装、安装变形和可靠性降低等问题。所述驱动子板32的两侧具有采用削边处理形成的第一削边部321,所述驱动组件6的两侧具有采用削边处理形成的第二削边部61,配合鳍片13导风道14的设计,形成风扇吹风循环通道,优化驱动散热设计。
[0033]
实施例2
[0034]
参阅图6本实用新型一种一体化led汽车灯,包括左灯体1、右灯体2、光源组件3、超导热管4、风扇5、驱动组件6、紧固螺丝8、电源插头9,所述左灯体1、右灯体2通过若干个紧固螺丝8组合构成的灯体,所述光源组件3、超导热管4安装于灯体的内腔中,所述光源组件3上设有led光源,所述左灯体1、右灯体2上与led光源相对应的位置设有出光口10,所述灯体的尾部具有散热部100,所述散热部100的内部设有若干个鳍片1001,所述超导热管4的尾部固定于散热部100上,所述散热部100的内腔中安装有风扇5,所述灯体的尾部安装有驱动组件6和电源插头9,所述灯体的前端还安装有卡扣12,所述卡扣12内与灯体相抵靠的一侧具有密封环槽,所述密封环槽内安装有硅胶圈11,所述光源组件3为双面铜基板。
[0035]
本实施例2中采用单光设计方案,所述左灯体1、右灯体2呈对称设置,所述灯体的内腔中具有并列布置的光源安装槽101和导热管安装槽102,所述光源组件3、超导热管4分别安装于光源安装槽101、导热管安装槽102中,所述超导热管4设置于光源组件3距离led光源较近的一侧。
[0036]
进一步地,优化的风扇强制对流散热,具体的,在本实施例2中风扇5安装于散热部
100的尾端,风扇5的吹风方向为朝向灯体前端方向,所述风扇5的外轮廓采用方形或近似方形。
[0037]
进一步地,采用优化的散热鳍片设计:为保证结构尺寸不超出法规限制,散热鳍片采用内置设计,针对不同灯体采用不同的强制对流散热优化设计,在本实施例2中,所述散热部100的内部设有若干个采用水平分布鳍片1001,所述鳍片1001与灯体几何中心线相平行,相邻的鳍片1001之间开设有散热出风孔。鳍片采用水平分布,配合灯体的水平开口,优化强制对流散热。
[0038]
进一步地,采用优化的驱动散热设计,具体的,所述驱动组件6水平设置,与鳍片1001相平行,配合水平散热鳍片和灯体水平方向散热出风口,形成高效的强制对流散热设计。采用优化的连接线设计:采用板对板硬连接与软线连接相结合的设计在简化工艺的同时提高焊接误差容许。在本实施例2中,所述光源组件3与驱动组件6采用板对板焊接固定,所述驱动组件6与电源插头9通过软线7相连接,可以有效防止因焊接位置偏差产生的无法安装、安装变形和可靠性降低等问题。
[0039]
上述实施例是对本实用新型的说明,不是对本实用新型的限定,任何对本实用新型简单变换后的方案均属于本实用新型的保护范围。