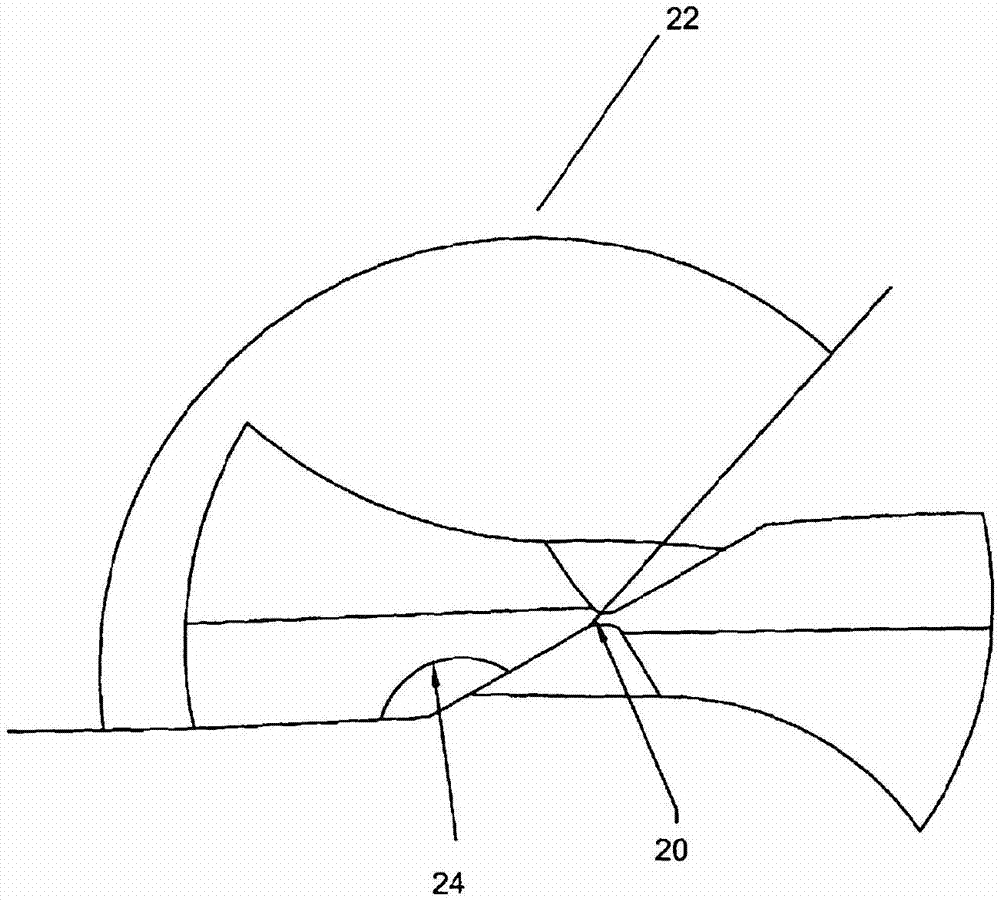
本发明涉及一种钻头,具体为一种适用于纤维增强复合材料制孔加工的钻头,属于纤维增强复合材料装配制孔应用
技术领域:
。
背景技术:
:纤维增强复合材料,如cfrp、gfrp和afrp在航空航天领域中应用广泛,在纤维增强复合材料装配过程中需要进行大量的制孔操作,且对于制孔质量要求较高,对于制孔加工是一种挑战。纤维增强复合材料在制孔过程中容易出现孔壁烧蚀、划伤、分层,钻孔入口和出口容易出现劈裂、毛刺等缺陷,直接影响零件的服役性能。纤增强复合材料明显的各向异性,也使得其制孔刀具与传统的金属加工刀具明显不同,要求刀具能够具有良好的切削锋利性与特殊的几何结构,实现纤维切断。而且,纤维增强复合材料一般都具有良好的耐磨性,对刀具磨损严重,因此,针对上述问题提出一种适用于纤维增强复合材料制孔加工的钻头。技术实现要素:本发明的目的就在于为了解决上述问题而提供一种适用于纤维增强复合材料制孔加工的钻头,钻头具有确定起始螺旋角和最终螺旋角的可变螺旋,以及确定的第一后角和第二后角,使钻削扭矩最小化。钻头可以在钻削纤维增强复合材料获得良好的制孔质量。本发明通过以下技术方案来实现上述目的,一种适用于纤维增强复合材料制孔加工的钻头,包括钻头主体以及与所述钻头主体连接为整体的头部,所述钻头主体与所述头部之间设有第一倒角和第二倒角;所述钻头主体上设有螺旋槽,且所述螺旋槽的一侧的所述钻头主体上设有排屑槽;所述头部上设有导向机构,且所述头部的端部设有钻头刀尖;所述钻头刀尖的中心处设有横刃,且所述横刃所在平面形成主切削面;所述主切削面所在的边缘设有切削刃,与所述主切削面相连的所述头部上形成副切削面;所述主切削面的后角为10°至20°,所述副切削面的后角为10°至40°,至少有一个所述切削刃从所述钻头刀尖延伸至钻头主体,每个刀刃的螺旋角在刀尖处为25°到45°,延伸至刀柄为0°到30°。其中,其中主切削面的后角为10°至30°,优选10°至20°,副切削面的后角为10°至40°,优选20°至35°;至少一个切削刃从钻头刀尖延伸到钻头主体,其螺旋角是可变螺旋,所述切削刃的起始螺旋角为45°至55°,最终螺旋角5°至30°,优选10°至20°。优选的,螺旋角从起始螺旋角连续减小到最终螺旋角,螺旋切削刃没有螺旋角不变的任何直线部分。沿着螺旋线距离变化的螺旋角的变化率是连续的。因此,螺旋切削刃没有任何部分是螺旋角变化率恒定的。螺旋角函数优选为非线性函数,例如指数函数。螺旋角函数特别优选的是随起始螺旋角到最终螺旋角减小的样条函数。适合的样条函数是任何非线性样条函数,例如指数,二次或三次样条函数。在纤维增强复合材料在制孔过程中,如上所述的可变螺旋角设计和主切削面和副切削面组合可以显著降低扭矩。相对较大的起始螺旋角有助于快速且干净地切割纤维增强复合材料。此外,大的起始螺旋角也提供低切削阻力。主切削面和副切削面组合可以提高孔加工质量,特别是当钻削本文所述的纤维增强复合材料时的出孔质量。本发明人进行的实验已经表明,加工后的纤维增强复合材料出口劈裂较少。在实例中,特别是适用自动钻孔的实例中,主后角应为11°至19°,优选为13°至17°,最优选为约15°。在实例中,特别是适用自动钻孔的实例中,副后角为15°至25°,优选为17°至23°,最优选为约20°。钻头仅具有两个切削刃。然而,也可以有两个以上的切削刃,例如三或四个切削刃。在实施方案中,优选两或三个切削刃。钻头具有导向结构,钻头导向结构具有定心尖端,定心点进一步提高了钻头性能,适合协助精确定位。特别地,延长导向结构长度有助于形成高质量的孔。本发明人发现具有至少2mm长度的导向结构是特别有效的。导向结构长度优选至少2.5mm~5mm。导向结构的直径为钻头直径的40%至60%,优选为44%至50%,最优选为约47%。通常,钻头直径是通过钻头边缘转点测量,即在钻头的最宽处测量的直径。当钻头包括导向结构时,钻头直径也在钻头主体的最宽部分测量,通常在钻头主体的最前端。在钻头主体和导向结构之间存在过渡部分时,钻头直径是钻头主体邻近过渡部分的直径。在钻头上增加导向结构的另外一个好处就是可以重新修磨。具体来说,包含导向结构的钻头,在实例中,至少能重新研磨两次。在存在导向结构的情况下,可以实现性能的进一步改进。本发明人发现,设置有双倒角的钻头可以降低加工过程中的扭矩,改善尖端和钻头主体之间的切割过渡。钻头在导向结构和钻头本体之间有过渡部分,过渡部分在导向结构之后延伸的部分有第一倒角,在第一倒角后面延伸的部分有第二倒角。过渡部分长度优选至少5mm,最优选至少8mm。过渡部分的长度是轴向的长度方向。第一倒角部分合适长度至少3mm,优选至少4mm。倒角部的长度是轴向的长度。第二倒角部分合适长度至少2mm,优选至少3mm。倒角部的长度是轴向的长度。合适的第一倒角部分的长度应大于第二倒角部分的长度。第一倒角部分比第二倒角部分长至少10%,优选长大约20%。第二倒角部分角度为5°至15°,优选为8°至12°,最优选为约10°。倒角角度是由倒角平面与平行于钻头轴线的平面形成的角度。第一倒角部分合适角度为10°至20°,优选为12°至18°,最优选为约15°。第一倒角部分角度应大于第二倒角部分角度。第一倒角部分角度应比第二倒角部分角度大至少20%,优选地至少大30%。钻头刀尖包括横刃,如本文所述的相对较小的横刃长度有助于减小扭矩。横刃角度优选为100°至125°,更优选为105°至120°。在实例中,特别是适用自动钻孔的实例中,横刃角度为110°至120°,优选为114°至118°,最优选地为约116°。横刃长度优选为0.03mm至0.15mm,更优选为0.06mm至0.14mm,最优选约0.1mm。在钻头仅有两个切削刃的情况下,上述横刃长度尤其适用。在钻头有3个切削刃的情况下,优选的横刃长度为0.03mm至0.07mm,优选为0.03mm至0.05mm。锋角是位于切削刃和次切削刃之间的平行于钻头轴线并平行于两个切削刃的平面上的夹角。钻头锋角至少为80°,优选至少85°,最优选至少89°。钻头锋角应不超过140°,优选不超过120°。锋角的这些值(上限和下限)可以以任何组合存在于实例中。在实施方案中,特别是适于自动钻孔的情况下,锋角为80°至90°,最优选约85°。如本文所述的锋角有助于减小扭矩并加工出良好的出口孔质量。轴向前角应不超过20°,优选不超过15°,最优选不超过11°。钻头包括右手或左手螺旋。右手螺旋是首选。钻头直径为1mm至50mm,优选1至20mm,最优选2mm至15mm。适当地,对于直径为6.5mm或更大(例如6.5mm至15mm)的钻头,起始螺旋角应小于40°,优选在28°至32°的范围内,最终螺旋角在0°至20°的范围内,优选为8°至12°。螺旋角从起始到最终减小至少10°,优选至少15°。对于直径小于6.5mm(例如2mm至<6.5mm)的钻头,起始螺旋角至少为40°,优选在48°至52°的范围内,并且终止螺旋角在0°至35°的范围内,优选8°至12°。螺旋角从起始到最终减小至少20°,优选至少30°。所述纤维增强复合材料是碳纤维增强塑料(cfrp)、玻璃增强塑料(gfrp)或芳纶纤维复合材料(afrp);所述钻孔步骤包括手动制孔或数控制孔;所述方法是叠层材料制孔。钻头材料由碳化物制成。首选的碳化物是碳化钨(wc)。特别优选的钴浓度为总硬质合金重量的3wt%至10wt%,更优选为5wt%至7w%,最优选为约6wt%。钻头有涂层,可部分或完全涂覆。优选涂层是耐磨涂层,具有比未涂层的刀具更低的摩擦系数。合适的涂层包括基于金属氮化物的涂层(例如tin,altin等),基于金属氧化物的涂层(例如alxoy,alxcryo等),碳基涂层(例如dlc,金刚石涂层等)。金刚石涂层是首选。本发明的有益效果是:1、钻头具有确定起始螺旋角和最终螺旋角的可变螺旋,以及确定的第一后角和第二后角,使钻削扭矩最小化;2、钻头具有主横刃和第二横刃,以及确定的钻头刀尖角和横刃前角,可以在钻削纤维增强复合材料获得良好的制孔质量;3、在加工含有纤维的复合材料时的扭矩问题可以通过一系列的刀具特征来解决,即特定的起始和终止角度的可变螺旋,以及初级和次级面的特定后角。附图说明图1为本发明的实例一的可变螺旋钻头的侧视图;图2为图1钻头的端面轴向视图;图3为图1钻头的放大视图;图4为本发明实例中钻削cfrp材料的出口孔质量测试的结果图;图5为本发明实例中其他钻头钻削cfrp材料的出口孔质量测试的结果图。图中:1、切削刃,2、排屑槽,3、主切削面,4、钻头主体,5、副切削面,6、头部,7、钻头刀尖,8、螺旋槽,10、导向结构,12、锋角,14、第一倒角,16、第二倒角,20、横刃,22、主横刃角,24、次横刃角,30、主间隙,32、次级间隙。34、轴向前角。具体实施方式下面将结合本发明实施例中的附图,对本发明实施例中的技术方案进行清楚、完整地描述,显然,所描述的实施例仅仅是本发明一部分实施例,而不是全部的实施例。基于本发明中的实施例,本领域普通技术人员在没有做出创造性劳动前提下所获得的所有其他实施例,都属于本发明保护的范围。请参阅图1-5所示,一种适用于纤维增强复合材料制孔加工的钻头,包括钻头主体4以及与所述钻头主体4连接为整体的头部6,所述钻头主体4与所述头部6之间设有第一倒角14和第二倒角16;所述钻头主体4上设有螺旋槽8,且所述螺旋槽8的一侧的所述钻头主体4上设有排屑槽2;所述头部6上设有导向机构10,且所述头部6的端部设有钻头刀尖7;所述钻头刀尖7的中心处设有横刃20,且所述横刃20所在平面形成主切削面3;所述主切削面3所在的边缘设有切削刃1,与所述主切削面3相连的所述头部6上形成副切削面5;所述主切削面3的后角为10°至20°,所述副切削面5的后角为10°至40°,至少有一个所述切削刃1从所述钻头刀尖7延伸至钻头主体4,每个刀刃的螺旋角在刀尖处为25°到45°,延伸至刀柄为0°到30°。所述螺旋角从初始角度到终止角度减小至少15°,且起始螺旋角平滑地连续地过渡到终止螺旋角,且起始螺旋角为45°到55°,终止螺旋角为8°到15°。所述起始螺旋角为25°到35°,终止螺旋角为8°到15°。所述主切削面3的后角为10°到20°,副切削面5的后角为15°-30°。所述的钻头仅有两个切削刃1,每个切削刃1包含一个后边缘角;所述切削刃1上设置有主间隙30和次间隙32。所述钻头刀尖7有倒角,倒角尺寸为1.5-2.5mm,锋角12为85°到110°,轴向前角34为8°到15°。在倒角和钻头主体之间有过渡部分,在倒角部分后面有第一部分的倒角过渡部分,以及在第一过渡倒角部分后的第二过渡倒角部分和可选的在第二过渡倒角部分后的第三过渡倒角部分。所述横刃20为0.05至0.15mm,所述横刃20形成主横刃角22为100°至125°,次横刃角24为145°到155°。一种适用于纤维增强复合材料制孔加工的钻头,所述纤维增强复合材料是碳纤维增强塑料(cfrp)、玻璃增强塑料(gfrp)或芳纶纤维复合材料(afrp);所述钻孔步骤包括手动制孔或数控制孔;所述方法是叠层材料制孔。所述方法包括用钻头钻削纤维增强复合材料的步骤。图1展示本发明的钻头。钻头包括柄(未展示),钻头主体4和头部6。两个螺旋槽8从钻头刀尖7延伸到钻头主体4。在螺旋起始处的螺旋角相对较大,为50°,在螺旋的末端且相对较小,为10°。对于起始角度,其他角度也是可以的,例如25°至60°,适当地为40°至60°,对于终止角度为0°至35°。使用样条函数形成螺旋。选择样条函数使得螺旋角从起始处随着轴向距离的变化是平滑和连续的。这与传统的螺旋角阶梯变化的可变螺旋钻相比,传统可变螺旋钻使得在螺旋角之间是台阶过渡。相比之下,该实例具有平滑且连续的螺旋角变化,不再是阶梯变化。这具有显著的优点,即沿着排屑槽可以更有效地去除和排出材料。排屑槽2的宽度以及沿排屑槽2的长度基本上是恒定的。钻头还包括延伸导向结构10。导向结构10尖端处的切削刃1形成锋角12为90°。其他角度也是可能的,例如80°至140°。钻头包括在相对较窄的导向结构10和较宽的钻头主体4之间的逐渐过渡部分。双倒角用于减小扭矩并增加切削阻力,以抵消在倒角和钻头主体4之间的过渡点切割期间发生的推动作用。具体来说,钻头包括角度为15°长度为5mm的第一倒角部分14,和角度为10°长度为4mm的第二倒角16,其他倒角和长度可以如上所述。实际上,可以有额外的倒角(即第三,第四等倒角)。导向结构10的直径为钻头直径的47%。如本文所解释的,在钻头的最宽点处测量钻头直径,在这种情况下,钻头直径与钻头主体4最靠近第二倒角16的最远处尺寸相同。延伸导向结构10长3mm,从紧邻第一倒角14的最前部的点到紧邻点进行测量。其他引导长度也是可能的,例如2mm到6mm。延长的导向结构10结构可以循环利用,从而允许相同钻头多次使用。图2展示了钻头的轴向视图。横刃20具有0.1mm的长度和110°的横刃角度22。如本文所述其他横刃20长度和横刃20角度是可能的。图3展示了头部6,特别是导向结构10的放大视图。该点的切削刃1和次切削刃设置有主间隙30(也称为主面或侧面间隙)和次级间隙32(也称为作为次面或侧面间隙)。各自的角度(也称为间隙)分别为10°和20°。在具有其他相同几何形状的另一实例中,相应的倒角为25°和20°。其他主间隙角和次间隙角也是可能的,例如分别为5°至40°(优选10°至40°)和10°至40°。钻头具有8°的轴向前角34。在具有其他相同几何形状的另一实例中,轴向前角34为10°。其他前角可能是例如3°至15°。将本发明的钻头性能与其他钻头性能相比较。通过测量轴向力和孔质量来量化钻头性能。试验中的试验工件是10mm厚的cfrp材料。测试结果如表1所示。测试刀具本发明钻头其他测试钻头轴向力64n97n出口质量(如图4)良好(图4)劈裂(图5)本发明钻头具有良好的出口质量,较小的钻削轴向力,非常适合加工纤维增强复合材料。对于本领域技术人员而言,显然本发明不限于上述示范性实施例的细节,而且在不背离本发明的精神或基本特征的情况下,能够以其他的具体形式实现本发明。因此,无论从哪一点来看,均应将实施例看作是示范性的,而且是非限制性的,本发明的范围由所附权利要求而不是上述说明限定,因此旨在将落在权利要求的等同要件的含义和范围内的所有变化囊括在本发明内。不应将权利要求中的任何附图标记视为限制所涉及的权利要求。此外,应当理解,虽然本说明书按照实施方式加以描述,但并非每个实施方式仅包含一个独立的技术方案,说明书的这种叙述方式仅仅是为清楚起见,本领域技术人员应当将说明书作为一个整体,各实施例中的技术方案也可以经适当组合,形成本领域技术人员可以理解的其他实施方式。当前第1页12