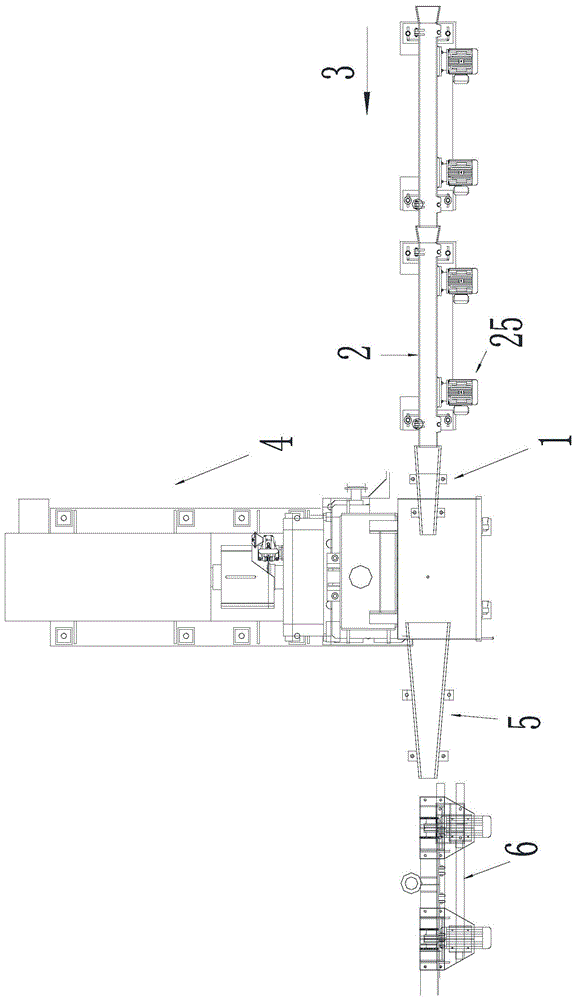
本实用新型涉及轧钢领域,具体涉及棒材多线切分轧制装置,即一种3#飞剪前导槽。
背景技术:
:热轧带肋钢筋俗称螺纹钢,广泛运用于房屋、桥梁、道路等建筑。目前,螺纹钢已经由单线或单支生产,发展成为多线切分生产,即将一支大螺纹钢在轧机上切分成多支小螺纹钢进行轧制,多线切分生产是单线或单支生产效率的数倍,例如,两切分就是将一支大螺纹钢切分成两支小螺纹钢进行轧制,四切分就是将一支大螺纹钢切分成四支小螺纹钢进行轧制,理论上,两切分是单线或单支生产效率的两倍,四切分是单线或单支生产效率的四倍。在多线切分生产中,成品钢在经过精轧机后,横向切分成多支钢支,每支钢支一般能达到上百米长,然后进入3#飞剪切分倍尺,纵向剪切成几十米左右的长度,然后进入冷床。在3#飞剪切分倍尺后,在同一剪后通道内,会出现有的钢支在剪后通道内规则的行走,而有的钢支在剪后通道内(例如在3#飞剪后第二段导槽或其他3#飞剪后其他部位的导槽)不规则的行走摆动,这一现象极大地影响了钢支在上冷床前通道内的稳定性,容易造成裙板钢支追尾堵钢,影响后续快速到来的钢支的正常行进,从而造成上冷床前通道内乱钢,形成废品,而且影响整个轧制线的生产。综上所述,现有技术中存在以下问题:棒材轧制多线切分时,成品钢经过3#飞剪后行走歪斜的问题。技术实现要素:本实用新型提供一种3#飞剪前导槽,目的是提高3#剪切分倍尺后钢头(钢支的头部)行走平直性。为此,本实用新型提出一种3#飞剪前导槽,所述3#飞剪前导槽包括:依次衔接的3#飞剪前第一段导槽和3#飞剪前第二段导槽;3#飞剪前第二段导槽的长度大于3#飞剪前第一段导槽的长度;3#飞剪前第一段导槽为喇叭口形状;3#飞剪前第二段导槽包括:矩形的主导槽和连接所述矩形的主导槽的锥形辅助导槽;所述矩形的主导槽的出口伸入到3#飞剪前第一段导槽的入口中;其中,棒材钢支行进的方向为从3#飞剪前第二段导槽到3#飞剪前第一段导槽的方向,3#飞剪前第一段导槽位于3#飞剪与3#飞剪前第二段导槽之间;3#飞剪前第二段导槽具有两个侧壁和设置在两个侧壁之间的底壁,3#飞剪前第二段导槽设有变频支撑辊道;所述变频支撑辊道包括:变频电机和连接变频电机的支撑辊,所述变频电机设置在3#飞剪前第二段导槽的侧壁上,3#飞剪前第二段导槽的两个侧壁之间形成有开口,所述支撑辊设置在所述开口中,所述支撑辊的轴线平行3#飞剪前第二段导槽的底壁;所述支撑辊的数目为两个,分别为首端的支撑辊和尾端的支撑辊,首端的支撑辊位于3#飞剪与尾端的支撑辊之间;首端的支撑辊和尾端的支撑辊的间距为1米。进一步的,所述支撑辊设置在所述矩形的主导槽的侧壁上。进一步的,首端的支撑辊距离3#飞剪剪切中心为1550mm至1750mm。进一步的,首端的支撑辊距离矩形的主导槽的前缘为450mm至550mm。进一步的,3#飞剪后依次连接有3#飞剪后第一段导槽和3#飞剪后第二段导槽,3#飞剪后第一段导槽为喇叭口形状,3#飞剪后第二段导槽与3#飞剪前第二段导槽结构相同。进一步的,所述3#飞剪前导槽用于棒材的四线切分,3#飞剪前第二段导槽具有输送四支棒材钢支的槽宽。进一步的,所述支撑辊的尺寸为ф180mm×380mm;所述变频电机的型号:YVP100L2-4,P=2.2KW;传动方式:交流变频,单独传动连续正向运转。进一步的,3#飞剪采用的电机型号为Z355-6C,额定功率为355KW,3#飞剪的剪刃线速度超过棒材钢支运行速度2--10%,最大剪切力400KN,回转半径:505mm,棒材钢支进入3#飞剪前第二段导槽的锥形辅助导槽的速度为3--18m/s,棒材钢支剪切后的长度为84至108m。本实用新型利用新增(变频)支撑辊的附加速度给切分倍尺后的钢支头部以有力支撑,以提高钢支在剪后的行走直线性及稳定性。本实用新型改变了多线切分的钢在经过3#飞剪切分后就行走歪斜的情况,提高了行走稳定性,减少了钢头在通道被撞击变形的可能性,最终达到杜绝钢支在动裙板上飞出追尾上一支钢造成堵钢的情况。附图说明图1为本实用新型的3#飞剪前导槽的整体结构示意图;图2为本实用新型的3#飞剪前第二段导槽的主视结构示意图;图3为本实用新型的3#飞剪前第二段导槽的俯视结构示意图。附图标号说明:1、3#飞剪前第一段导槽;2、3#飞剪前第二段导槽;21、主导槽;22、锥形辅助导槽;3、棒材钢支行进的方向;4、3#飞剪;25、变频支撑辊道;251、变频电机;252、支撑辊;253、变频辊面水平线;5、3#飞剪后第一段导槽;6、3#飞剪后第二段导槽。具体实施方式为了对本实用新型的技术特征、目的和效果有更加清楚的理解,现对照附图说明本实用新型。1、原理和问题分析:在日常生产中,申请人的轧制线常常出现在3#飞剪切分倍尺后,在同一剪后通道内,会出现有的钢支在剪后通道内规则的行走,而有的钢支在剪后通道内不规则的行走摆动的问题。对于这一问题,申请人百思不得其解。因为是同样的一根坯料,经过同样的加热、初轧、精轧、在同样的轧机上切分成4支棒材钢支,然后经过同样的穿水冷却装置,依次同时进入同样的3#飞剪前第一段导槽和3#飞剪前第二段导槽,经过3#飞剪剪切,依次同时进入同样的3#飞剪后第一段导槽和3#飞剪后第二段导槽,此时,却发生了有的钢支在剪后通道内不规则的行走摆动,导致追尾、乱钢的问题。申请人发现:在4切分的过程中,4支棒材钢支的形成和运动都是在同样的条件下,然而,有两支棒材钢支正常行走,另外两支棒材钢支却不直线行走、而是斜线行走或者撞到剪后通道的裙板或侧板上。对于这些问题,申请人经过长时间的研究,找了许多影响因素,认为是在3#飞剪后到出现追尾、乱钢的剪后通道之间出现了问题,而其他环节没有问题,所以应该主要关注在3#飞剪后第一段导槽和3#飞剪后第二段导槽上面。为此,申请人仔细检查3#飞剪后第一段导槽底壁的制作是否均匀、是否摩擦系数相同,3#飞剪后第二段导槽的底壁的制作是否均匀、是否摩擦系数相同,3#飞剪是否存在轴向偏心,3#飞剪后第一段导槽的两个侧壁是否薄厚不一,影响散热,3#飞剪后第二段导槽的两个侧壁是否薄厚不一,3#飞剪后第一段导槽和3#飞剪后第二段导槽的宽度是否不足。申请人改进了所有这些因素后,仍然没有解决问题。申请人经过多次的排查的失败和摸索,决定另起炉灶,将排查的因素扩大到从加热到3#飞剪之间的其他环节。为了解决这一难题,申请人仔细研究从加热到3#飞剪之间的各个环节,确实也没有发现有什么异常,在现场也没有看出或发现有任何问题。但是,由于这一问题长期得不到解决,申请人认为肯定是表面上的现象掩饰了问题的关键。申请人分别从理论角度和实际观察进行了分析。申请人改进了观察的方法,将人工观察和普通的视频录像改为高速视频拍照,就像医学上做B超一样,对各个环节进行细致分析,终于发现:在棒材钢支进入3#飞剪前第二段导槽的时候,4支棒材钢支中,有两支的速度稍微比另外两支的速度要低一些,这个速度差别为1-2%(大概为0.13米/秒),肉眼几乎感觉不出来,而且也没有人注意,没有人会想到会这样。申请人又继续分析了其原因。经过对精轧机的分析,申请人发现:在最后一架精轧机上,虽然理论上轧辊在各个轧槽上的压下是相同的,然而在实际轧制中,由于4支棒材钢支的分布距离电机端或轴承座端的距离不同,所以轧制4支棒材钢支的各个轧槽的压下也有细微的不同,导致,两个中间位置的轧槽的压下不同于另外两个边缘处的轧槽的压下,产生轧制半径的细微差别。这样,轧机在高速轧制中,会出现4支棒材钢支中,有两支的线速度稍微比另外两支的线速度要稍微低一些,尤其是在一个轧辊使用周期的后期,申请人发现:由于轧辊的磨损,这种速度差要比一个轧辊使用周期的前期更大一些。经过精轧后,棒材钢支进入飞剪(有的工艺是经过穿水冷却装置进入飞剪),经过飞剪剪切后进入剪后通道,由于飞剪的剪切速度一般要比棒材钢支速度大一定的比例,精轧后的棒材钢支之间的速度差被扩大了,导致进入剪后通道时,同一剪后通道内的棒材钢支有的能保持正常的直行行走所需的速度,有的则小于保持正常的直行行走所需的速度,受通道的摩擦以及通道的入口的锥度影响,速度低的棒材钢支会斜线行走或者撞到剪后通道的裙板或侧板上经过上述分析,申请人发现这一问题的原因是综合的:虽然问题出现在剪切之后,但是原因发生在于剪切之前的阶段,而不是剪切之后的阶段,根源在于切分轧制中精轧机各个轧槽的轧制半径不同,线速度不同,扩大因素在于飞剪的剪切进一步扩大了同一剪后通道内的棒材钢支的速度差,导致速度低的棒材钢支难以保持直行所需的速度值,从而导致斜线行走或者撞到剪后通道的裙板或侧板上。因此,申请人开始着手改进精轧机各个轧槽的轧制半径不同的问题。然而,申请人发现,无论怎样改进,精轧机各个轧槽的轧制半径总会存在差别,而且这一差别的减弱不明显。申请人也曾想改进穿水冷却工艺。可是穿水冷却工艺体系要求比较完整,难以大幅度改进其中的工艺参数。技术攻关又遇到了瓶颈。虽然找到了问题的原因,但申请人在改进轧机和穿水冷却的技术上都没有起到预期效果,申请人又转变思路,不在纠缠于产生速度差的根源上,而是另辟蹊径,在有速度差的情况下,增加速度低的棒材钢支的速度,以减小或消灭速度差,使得速度低的棒材钢支也能获得直行所需的速度值。为此,申请人确定了一个快捷而方便的办法,那就是,在精轧后,进入飞剪前,减小或消灭棒材钢支的速度差。为此,申请人在精轧后,进入飞剪前的导槽部位,即3#飞剪前第一段导槽和3#飞剪前第二段导槽的区域范围内,同时给4支棒材钢支以足够的速度,该速度能增加原来速度低的2支棒材钢支的速度,基本上使得4支棒材钢支重新获得相同的速度,这样,经过剪切,4支棒材钢支也不会有明显的速度差,最终实际生产证明,这一技术巧妙的解决了钢支在剪后通道内不规则的行走摆动,解决了追尾、乱钢的技术难题。2、解决方案的落实如图1、图2和图3所示,本实用新型的3#飞剪前导槽包括:依次衔接的3#飞剪前第一段导槽1和3#飞剪前第二段导槽2;3#飞剪前第二段导槽2的长度大于3#飞剪前第一段导槽1的长度;3#飞剪前第一段导槽1为喇叭口形状,由钢板制成;3#飞剪前第一段导槽1紧邻3#飞剪4,3#飞剪前第一段导槽1起到聚拢棒材钢支的作用,将棒材钢支聚拢到3#飞剪4处以便剪切;3#飞剪前第二段导槽2的上游可以再依次连接导槽、穿水冷却装置和精轧机组,进入3#飞剪前第二段导槽2中的棒材钢支是经过精轧轧制和/或穿水冷却处理后的;如图2和图3所示,3#飞剪前第二段导槽2包括:矩形的主导槽21和连接所述矩形的主导槽的锥形辅助导槽22;矩形的主导槽21的截面沿长度方向相同,对棒材钢支起主要的运输和导向作用,锥形辅助导槽22为喇叭口形状,起到聚拢作用,将棒材钢支聚拢到矩形的主导槽21内,所述矩形的主导槽21的出口伸入到3#飞剪前第一段导槽1的入口中;其中,棒材钢支行进的方向3为从3#飞剪前第二段导槽到3#飞剪前第一段导槽的方向,3#飞剪前第一段导槽1位于3#飞剪4与3#飞剪前第二段导槽2之间;如图1所示,3#飞剪前第二段导槽2设有变频支撑辊道25;如图2和图3所示,3#飞剪前第二段导槽具有两个侧壁和设置在两个侧壁之间的底壁,3#飞剪前第二段导槽的两个侧壁之间形成有开口,所述支撑辊设置在所述开口中,所述支撑辊的轴线平行3#飞剪前第二段导槽的底壁。所述变频支撑辊道25包括:变频电机251和连接变频电机的支撑辊252,所述变频电机251设置在3#飞剪前第二段导槽的侧壁上,3#飞剪前第二段导槽2的底壁上设有开口,所述支撑辊252设置在所述开口中;或者是支撑辊252设置在3#飞剪前第二段导槽2内;所述支撑辊252的轴线平行3#飞剪前第二段导槽的底壁,如图2所示,变频辊面水平线253为支撑辊的最高位置,是支撑棒材钢支的支撑面,要高出3#飞剪前第二段导槽的底壁,用以支撑棒材钢支。进一步的,所述支撑辊设置在所述矩形的主导槽的侧壁上,便于传动和安装。进一步的,所述支撑辊的数目为两个,分别为首端的支撑辊和尾端的支撑辊,首端的支撑辊位于3#飞剪与尾端的支撑辊之间,以便分担和提供足够的功率和足够的支撑以及速度补充。进一步的,两个所述支撑辊的间距为1米,这样,钢支既能保证水平剪切效果,又不会碰撞到飞剪刀臂。进一步的,首端的支撑辊距离3#飞剪剪切中心为1550mm至1750mm,既能保证水平剪切效果,又不会碰撞到飞剪刀臂。进一步的,首端的支撑辊距离矩形的主导槽的前缘(图2中主导槽21的最左竖边)为450mm至550mm。这样,钢支在导槽内行走波动小,而且与上一个变频辊间距为一米左右,统一了辊间距对轧件弹跳有稳定作用。进一步的,3#飞剪后依次连接有3#飞剪后第一段导槽5和3#飞剪后第二段导槽6,3#飞剪后第一段导槽5为喇叭口形状,3#飞剪后第二段导槽6与3#飞剪前第二段导槽2结构相同。3#飞剪后第二段导槽长度较长,比3#飞剪前第二段导槽2要长几倍甚至几十倍,起到将剪切后的棒材钢支输送到冷床的作用。3#飞剪后第二段导槽也设有变频支撑辊道,以保证剪切后,各棒材钢支都有一定速度直行。进一步的,所述3#飞剪前导槽用于棒材的四线切分,是普通轧制的4倍效率,3#飞剪前第二段导槽输送四支棒材钢支。棒材钢支可以为直径12mm和14mm的两种规格。轧件剪切截面及运行速度见表1:序号轧件规格(mm)轧件面积(mm2)轧件速度(m/s)备注112226.213.2切分轧制214307.813.5切分轧制表1:轧件剪切截面及运行速度表(轧件速度为精轧机出口速度)进一步的,所述支撑辊的尺寸为ф180mm×380mm;所述变频电机的型号:YVP100L2-4,P=2.2KW;传动方式:交流变频,单独传动连续正向运转。变频支撑辊道的线速度为13.5m/s,能使得四支棒材钢支重新获得同样的速度。进一步的,3#飞剪采用的电机型号为Z355-6C,额定功率为355KW,剪切转速530r/min,3#飞剪的剪刃线速度超过棒材钢支运行速度2--10%,最低剪切温度:550℃,轧件热态抗拉强度:≤300MPa,最大剪切力400KN,回转半径:505mm,棒材钢支进入3#飞剪前第二段导槽的锥形辅助导槽的速度为3--18m/s,棒材钢支剪切后的长度为84至108m。3#飞剪的上述参数与切分轧制的其他参数相配合,保证正常的剪切和剪切后棒材钢支的正常行走。本实用新型改变了多线切分的钢在经过3#飞剪切分后就行走歪斜的情况,提高了行走稳定性,减少了钢头在通道被撞击变形的可能性,最终达到杜绝钢支在动裙板上飞出追尾上一支钢造成堵钢的情况,减少了废品,减少了处理故障的时间,提高了整个轧制线的生产效率,在一个轧辊使用周期的前期,效率可提高10%以上,到一个轧辊使用周期的后期,故障减少时间更多,效率提高更明显,效率可以提高20%。以上所述仅为本实用新型示意性的具体实施方式,并非用以限定本实用新型的范围。为本实用新型的各组成部分在不冲突的条件下可以相互组合,任何本领域的技术人员,在不脱离本实用新型的构思和原则的前提下所作出的等同变化与修改,均应属于本实用新型保护的范围。当前第1页1 2 3