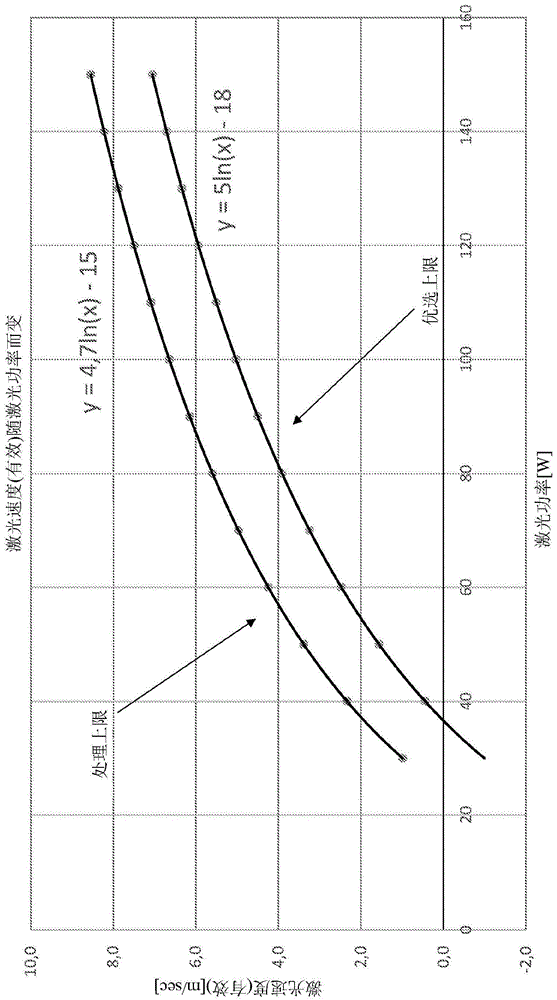
本发明涉及一种激光切割金属-陶瓷衬底的方法。本发明的另一主题为一种通过根据本发明的方法获得的金属-陶瓷衬底和激光切割金属-陶瓷衬底的用途。激光切割也称为激光光束切割,是指通过连续或脉冲式激光辐射经由材料烧蚀来分离固体。根据现有技术水平,几乎每一种类型的材料,例如金属、电介质和有机材料,都可以通过激光辐射切割。出现的一个问题,特别是在用激光光束切割金属材料时出现的一个问题为微粒排放,其会在激光切割线附近产生不合需要的金属沉积物。相应的沉积物在电子组件中的铜层的加工中,例如在dcb衬底中特别麻烦。这些沉积物会导致电绝缘性降低和隔离距离减小,这最终会导致对基于dcb衬底的电路的破坏。直接铜粘结衬底(dcb,也称为dbc)为大功率电子应用中使用最广泛的电路载体。dcb技术为一种连接技术,通过所述技术,在高温下,在铜(通常为铜箔)与陶瓷之间产生共晶粘结。dcb衬底适合需要良好热解耦的高功率应用。dcb由充当绝缘层的陶瓷衬底和用于确保电导率的铜化合物组成,陶瓷衬底如al2o3(或其它陶瓷材料,如zta、aln、氮化硅(si3n4))。dcb衬底为电力电子模组的主干且极其强大,例如与印刷电路板(printedcircuitboard,pcb)相比。首先,其携带半导体芯片且用以散热。另一方面,其确保对散热片和反相器外壳绝缘。为了最佳可靠性和性能,模组必须在热分布和耐温性以及负载反向稳定性方面具有良好特性。在此,个别层的分层现象提出了特别的挑战。金属-陶瓷衬底,例如通过dcb工艺获得的金属-陶瓷衬底,通常具有功能性凹槽。这些功能性凹槽例如为孔,经由所述孔,金属-陶瓷衬底通过用螺钉拧紧或穿孔镀敷(通孔)而固定。此类凹槽通常通过蚀刻掉金属覆盖层且随后例如通过激光烧蚀切穿陶瓷衬底而插入。这导致在金属陶瓷衬底中产生边缘结构,其中金属边缘相对于陶瓷边缘向后缩进。相对于陶瓷边缘向后缩进的金属边缘的缺点在于,所得金属-陶瓷衬底不太稳定,且在温度和负载改变期间可能发生金属层与衬底的分层。向后缩进的金属边缘的另一个缺点为陶瓷衬底的机械稳定性降低,这可能例如通过裂缝的形成而表现出来。此外,如上所述,将凹槽以常规方式引入金属-陶瓷衬底需要蚀刻掉金属覆盖层和激光烧蚀陶瓷衬底的两步工艺,这从经济观点来看是不利的。从此现有技术出发,本发明的目标首先在于提供一种激光烧蚀金属-陶瓷衬底的方法,利用所述方法,可以提供在金属层和/或陶瓷衬底中具有凹槽的金属-陶瓷衬底,所述金属-陶瓷衬底具有稳定的电绝缘。本发明的另一目标为提供一种在金属层和/或陶瓷衬底中设有凹槽的金属-陶瓷衬底,其优选机械稳定且优选没有裂缝。包含陶瓷衬底且在陶瓷衬底上设有至少一个金属层的金属-陶瓷衬底的激光烧蚀方法旨在实现金属-陶瓷衬底的经济型生产。这些目标是通过烧蚀金属-陶瓷衬底的方法实现。根据本发明的方法的特征在于所述方法是通过激光进行,所述激光在基本上避免在金属-陶瓷衬底上形成固体金属粒子(其有别于在烧蚀边缘附近通过激光烧蚀释放的金属粒子)的工艺条件下使用。此外,所述目标优选通过使用激光烧蚀金属-陶瓷衬底的方法实现,所述激光在允许同时激光烧蚀金属层和陶瓷衬底的工艺条件下使用。附图说明图1显示激光功率(w)与激光速度(m/sec)之间的关系。当根据本发明的方法在基本上避免在金属-陶瓷衬底上形成固体金属粒子(其有别于在烧蚀边缘附近通过激光烧蚀释放的金属粒子)的工艺条件下进行时,获得具有稳定绝缘特性的金属-陶瓷衬底,因为绝缘特性没有因为在金属-陶瓷衬底上沉积金属粒子而受到干扰。当根据本发明的方法在可以同时激光烧蚀金属层和陶瓷衬底的工艺条件下进行时,一方面避免了需要其它方法步骤的经济方法,且同时获得金属敷物(metallization)和陶瓷衬底具有齐平边缘的金属-陶瓷衬底。因此,提供一种机械稳定且避免金属层与衬底在温度和负载改变期间分层的金属-陶瓷衬底。通过根据本发明的方法处理的金属-陶瓷衬底在通过激光烧蚀形成的边缘侧基本上不含金属粒子。在本发明的情形下,术语“基本上不含金属粒子”应理解为意指通过激光烧蚀形成的金属粒子的残留如此之低,以致于对金属-陶瓷衬底的绝缘特性的损害不会达到干扰金属-陶瓷衬底用作电力电子应用的电路载体的程度。特定地说,根据本发明的方法是基于以下事实:在通过激光烧蚀形成的边缘侧,基本上避免经由激光烧蚀形成金属粒子。在本发明的情形下,“在通过激光烧蚀形成的边缘侧”的区域应特别理解为金属-陶瓷衬底的在使用除根据本发明的工艺条件外的工艺条件时发生金属粒子的沉积的区域。沉积物在通过激光烧蚀产生的凹槽中和/或在基本上平行于凹槽的相应边缘的区域中延伸,从凹槽边缘计算,宽度一般至多200μm、优选至多100μm、优选至多50μm、优选至多45μm、更优选至多40μm、更优选至多35μm、甚至更优选至多30μm。这个范围是指通过激光烧蚀在金属-陶瓷衬底中产生的凹槽。因此,在本发明的情形下,术语“在通过激光烧蚀形成的边缘侧”(“在烧蚀边缘附近”)“基本上不含金属粒子”应理解为意指表面积的小于50%、优选表面积的小于40%、更优选表面积的小于20%、更优选表面积的小于10%、更优选表面积的小于5%覆盖有在前述宽度范围中通过激光烧蚀产生的金属粒子。下面描述激光的优选实施例,利用所述激光基本上可防止在金属-陶瓷衬底的激光烧蚀处形成金属粒子且利用所述激光同时激光烧蚀金属层和陶瓷衬底是可能的。在本发明的情形下,虽然根据本发明,优选使用皮秒激光,但是激光可选自纳秒激光、皮秒激光或飞秒激光。而且,如果皮秒激光具有优选0.1至100ps、更优选0.5至50ps、再更优选1至30ps的脉冲持续时间,即激光脉冲持续时间,则进一步优选。利用所选脉冲持续时间,可以引导激光工艺,使得基本上不会出现金属残留,且因此基本上不会形成沉积在金属-陶瓷衬底的表面上的金属粒子。因为在本发明的情形下,基本上仅形成冷粉尘而不形成熔融相,且因为所选择的从光束源至衬底表面的距离足够大,所以可以使用处理气体,但这不是绝对必要的。激光的处理速度优选为至少0.2m/sec、更优选至少0.50m/sec、更优选至少0.60m/sec、更优选至少0.70m/sec、更优选至少0.80m/sec、更优选至少1.00m/sec。激光的处理速度优选为至多10.00m/sec、更优选至多8.00m/sec、更优选至多6.00m/sec、更优选至多5.00m/sec、更优选至多4.00m/sec。激光的处理速度为优选0.50至10.00m/sec、更优选0.60至8.00m/sec、更优选0.70至6.00m/sec、更优选0.80至5.00m/sec、更优选1.00至4.00m/sec。在本发明中,进一步发现,在激光功率(w=瓦特(watt))与激光的最大处理速度(m/sec)之间存在技术关系,其中将处理速度定义为有效激光速度(在本发明中,有效激光速度为在烧蚀期间施加的有效激光速度(相比于相对激光速度而言,相对激光速度考虑交叉次数(有效激光速度=相对激光速度/金属敷物上的交叉))。在本发明中,定义有效激光速度(实际激光速度),但是在金属敷物上进行不止一次交叉的情况下,本发明的数值结果对于相对激光速度也为有效的。在本发明的一个优选实施例中,已发现,激光的有效最大处理速度和激光功率遵循以下关系:y≤4.7lnx-15(1)其中x=激光功率,w;且y=最大激光处理速度(有效),m/sec。此关系意指指定激光功率下激光的最大处理速度y优选满足上文所提及的必要条件(1)。在本发明的一更优选实施例中,已发现,激光的有效最大处理速度和激光功率一般遵循以下关系:y≤5.0lnx-18(2)其中x=激光功率,w;且y=最大激光处理速度(有效),m/sec。此关系意指指定激光功率下激光的最大处理速度y更优选满足上文所提及的必要条件(2)。激光的最低处理速度优选如上文所提及:激光的处理速度优选为至少0.20m/sec、更优选至少0.50m/sec、更优选至少0.60m/sec、更优选至少0.70m/sec、更优选至少0.80m/sec、更优选至少1.00m/sec。因此,存在本发明的优选实施例,其概述于下表中:激光的最低处理速度(m/sec)激光的最高处理速度(m/sec)0.20y≤4.7lnx-150.50y≤4.7lnx-150.60y≤4.7lnx-150.70y≤4.7lnx-150.80y≤4.7lnx-151.00y≤4.7lnx-150.20y≤5.0lnx-180.50y≤5.0lnx-180.60y≤5.0lnx-180.70y≤5.0lnx-180.80y≤5.0lnx-181.00y≤5.0lnx-18其中x=激光功率,w;且y=最大激光处理速度(有效)。具体地说,在如下施加不同但是固定的激光功率的情况下,所要求保护的发明覆盖进一步优选实施例:激光的最低处理速度:0.2m/sec激光功率(w)激光的最低处理速度(m/sec)激光的最高处理速度(m/sec)400.202.30500.203.40600.204.20700.205.00800.205.60900.206.101000.206.601100.207.101200.207.501300.207.901400.208.201500.208.50激光的最低处理速度:0.5m/sec激光功率(w)激光的最低处理速度(m/sec)激光的最高处理速度(m/sec)400.502.30500.503.40600.504.20700.505.00800.505.60900.506.101000.506.601100.507.101200.507.501300.507.901400.508.201500.508.50激光的最低处理速度:0.60m/sec激光的最低处理速度:0.70m/sec激光功率(w)激光的最低处理速度(m/sec)激光的最高处理速度(m/sec)400.702.30500.703.40600.704.20700.705.00800.705.60900.706.101000.706.601100.707.101200.707.501300.707.901400.708.201500.708.50激光的最低处理速度:0.80m/sec激光功率(w)激光的最低处理速度(m/sec)激光的最高处理速度(m/sec)400.802.30500.803.40600.804.20700.805.00800.805.60900.806.101000.806.601100.807.101200.807.501300.807.901400.808.201500.808.50激光的最低处理速度:1.00m/sec激光功率(w)激光的最低处理速度(m/sec)激光的最高处理速度(m/sec)401.002.30501.003.40601.004.20701.005.00801.005.60901.006.101001.006.601101.007.101201.007.501301.007.901401.008.201501.008.50此外,在如下施加不同但是固定的激光功率的情况下,所要求保护的发明覆盖更进一步优选的实施例:激光的最低处理速度:0.2m/sec激光功率(w)激光的最低处理速度(m/sec)激光的最高处理速度(m/sec)400.201.00500.201.60600.202.50700.203.20800.203.90900.204.501000.205.001100.205.501200.205.901300.206.301400.206.701500.207.10激光的最低处理速度:0.50m/sec激光功率(w)激光的最低处理速度(m/sec)激光的最高处理速度(m/sec)400.501.00500.501.60600.502.50700.503.20800.503.90900.504.501000.505.001100.505.501200.505.901300.506.301400.506.701500.507.10激光的最低处理速度:0.60m/sec激光功率(w)激光的最低处理速度(m/sec)激光的最高处理速度(m/sec)400.601.00500.601.60600.602.50700.603.20800.603.90900.604.501000.605.001100.605.501200.605.901300.606.301400.606.701500.607.10激光的最低处理速度:0.70m/sec激光功率(w)激光的最低处理速度(m/sec)激光的最高处理速度(m/sec)400.701.00500.701.60600.702.50700.703.20800.703.90900.704.501000.705.001100.705.501200.705.901300.706.301400.706.701500.707.10激光的最低处理速度:0.80m/sec激光功率(w)激光的最低处理速度(m/sec)激光的最高处理速度(m/sec)400.801.00500.801.60600.802.50700.803.20800.803.90900.804.501000.805.001100.805.501200.805.901300.806.301400.806.701500.807.10激光的最低处理速度:1.00m/sec激光功率(w)激光的最低处理速度(m/sec)激光的最高处理速度(m/sec)401.001.00501.001.60601.002.50701.003.20801.003.90901.004.501001.005.001101.005.501201.005.901301.006.301401.006.701501.007.10根据本发明,已发现,在过于低的处理速度下,特别是在低于0.5m/s的激光处理速度下,一般不可避免地形成沉积在金属-陶瓷衬底的表面上的金属粒子。因此,根据本发明,激光处理速度优选超过0.5m/s。在本发明的情形下,通过激光烧蚀产生的金属粒子会沉积在金属敷物上和陶瓷衬底上。在根据本发明的方法中,有可能在激光的一次交叉或若干次交叉中切穿金属-陶瓷衬底。因此,有可能仅切穿金属敷物,也可能切穿金属敷物和金属-陶瓷衬底。脉冲能量,即单一激光脉冲的能量含量,优选为10至500μj、更优选50至400μj、甚至更优选100至350μj。皮秒激光具有的功率优选为20至400w、更优选40至200w、甚至更优选50至180w、再更优选60至160瓦特、再更优选80至130瓦特、再更优选90至120瓦特。在本发明的一个优选实施例中,所用激光为红外线激光。本发明的基本任务尤其通过使用红外线激光,更优选使用皮秒红外线激光来解决,其中,在不受理论束缚的情况下,假设皮秒红外线光束的光可特别有效地耦合至陶瓷衬底的表面或金属覆盖层的表面中,即其特别有效地被陶瓷衬底或金属覆盖层吸收。此外,红外线激光具有高能量效率,其也有利于解决以上任务。使用红外线激光处理金属-陶瓷衬底的金属材料的另一优点在于,红外线激光光可以直接从二极管光产生,而绿色激光光首先以60%的效率从红外线激光光产生且继而一定以也为60%的另一效率由绿色激光光产生紫外线激光光。相比于例如co2激光,皮秒红外线激光可以布置成显著地进一步远离待处理的金属材料,其结果是,可以实现较高的聚焦深度。此外,与co2激光相比,通过红外线激光,可以实现足够高的聚焦深度。当在本发明中使用红外线激光时,红外线激光的频率优选为350至650khz、更优选375至625khz、再更优选400至600khz。当在本发明中使用红外线激光时,红外线激光的脉冲能量优选为100至300μj、更优选125至275μj、再更优选150至250μj。根据本发明的方法可以在处理气体存在下进行。处理气体例如为氧气。根据本发明的方法优选在具有能吸收由激光处理引起的粉尘的抽吸装置的装置中进行。在一定程度上,需要在金属-陶瓷衬底的金属材料中引入轮廓,其与直线不同。这些轮廓例如可为在金属材料的拐角处的孔或圆角。此类轮廓可以通过在根据本发明的方法中使用激光切割金属材料而获得。也有可能通过激光烧蚀金属材料和陶瓷材料而在金属-陶瓷衬底中产生相应的轮廓。如果在本发明的情形下,使用激光切断金属-陶瓷材料的金属材料,则切割边缘所具有的角度与通过垂直于金属层或金属-陶瓷衬底所形成的直角通常偏离至多30°,更优选至多25°。这导致激光入口顶部的孔比底部的孔大。本发明用红外线激光、特别是皮秒红外线激光分离金属-陶瓷衬底的金属材料与陶瓷材料的另一优点在于,在底部,即在激光出口侧,不会因为熔融相而形成毛刺,原本必须在额外的程序步骤中移除所形成的毛刺。考虑到上述实施例,有可能用相同的激光且在相同的工艺参数下处理金属覆盖层和陶瓷衬底。因此,可以经济地实现具有结构化金属覆盖层的金属-陶瓷衬底的生产。具体地说,以下各者是可能的:i)仅部分烧蚀上层金属覆盖层或切穿陶瓷,和例如在金属覆盖层中产生精细结构,精细结构无法由蚀刻工艺产生;ii)切穿金属覆盖层和陶瓷衬底直至下层金属覆盖层(因此,可以产生穿孔基础。当用导电材料填充适当盲孔时,制得穿孔。填充材料例如为金属胶、金属模制品,例如圆筒,或电镀生成的材料。);iii)完全切穿金属覆盖层和陶瓷衬底以便产生功能性凹槽,例如用于用螺钉拧紧。根据本发明的程序参数适合同时激光烧蚀金属敷物和陶瓷衬底。在一个优选实施例中,在本发明中,仅烧蚀金属敷物、特别是铜。本发明的激光烧蚀金属-陶瓷衬底的方法可以在处理气体存在下进行,其中举例来说,可以使用氧气或压缩空气作为处理气体。如上所陈述,不强制使用处理气体,但可以建议使用处理气体来保护光束源免受污染。在此情况下,使用压缩空气将为优选的替代方案。因为在根据本发明的方法中,激光处理产生粉尘,所以如果所用装置具有能吸收激光处理所产生的粉尘的抽吸装置将是尤其优选的。抽吸装置例如可以由围绕所投射的激光光的抽吸管或抽吸箱形成,且其下边缘与金属-陶瓷衬底的表面之间的距离优选为0.5至10cm、更优选0.75至7.5cm、更优选1至5cm。在本发明的情形下,金属-陶瓷衬底的激光烧蚀例如可以通过激光光束对金属-陶瓷衬底的金属表面的作用而进行。通过选择以上工艺参数,这减少了沉积在金属-陶瓷衬底的表面上的金属粒子的形成。在本发明的情形下,金属-陶瓷衬底的激光烧蚀也可例如通过激光光束对陶瓷衬底的作用而发生。如果经由激光烧蚀产生用于固定金属-陶瓷衬底的凹槽,则此方法是优选的,因为在此情况下,用于固定的构件(例如螺钉)主要与金属材料接触,因此陶瓷材料因为固定构件所施加的应力减小而成片剥落。本发明的另一目标为一种通过上述方法获得的金属-陶瓷衬底。此金属-陶瓷衬底就通过激光烧蚀产生的凹槽上的金属层和陶瓷层而言特别具有齐平边缘。在此情况下,凹槽也可为金属-陶瓷衬底的末端边缘。术语“金属层和陶瓷衬底的齐平边缘”在本发明的情形下应理解为意指金属边缘和陶瓷衬底的边缘所具有的平行于边缘的最大偏离为优选最大20μm、更优选最大15μm、更优选最大10μm、甚至更优选最大5μm。本发明的金属-陶瓷衬底可以具有通过用红外线激光处理获得的轮廓,所述轮廓偏离直线且通过使用激光光束切割陶瓷衬底而形成。此外,根据本发明的金属-陶瓷衬底可能在拐角展现孔和/或圆角,其是因为切穿陶瓷衬底而产生的。通过红外线激光方法用皮秒红外线激光获得的金属-陶瓷衬底所具有的切割边缘的角度与直角偏离优选至多30°,更优选至多25°。如果通过红外线激光方法在金属-陶瓷衬底中引入孔,则在陶瓷衬底的两侧,孔大小可以不同。然而,优选地,金属-陶瓷衬底在孔和/或圆角处呈现无毛刺。因为根据本发明的红外线激光方法,可获得在陶瓷衬底的金属覆盖层上具有编码的金属-陶瓷衬底。此编码优选通过用红外线激光烧蚀金属覆盖层而实现。此外,通过根据本发明的方法,可获得金属-陶瓷衬底,其中陶瓷衬底上的金属敷物有至少一个边缘减小或其中金属敷物具有至少一个用于容纳电子组件、尤其是芯片的凹槽,其中凹槽通过激光处理产生。根据本发明的陶瓷-金属衬底优选为直接铜粘结衬底(directcopperbondedsubstrate,dcb衬底)、活性金属硬焊衬底(activemetalbrazingsubstrate,amb衬底)或直接铝粘结衬底(directaluminumbondedsubstrate,dab衬底)。在本发明的另一实施例中,陶瓷-金属衬底可为根据现有技术而非以前公开的国际专利申请案pct/ep2016/082161的陶瓷-金属衬底。下面更详细地描述在本发明的情形下优选使用的陶瓷衬底:陶瓷衬底优选含有至少一种选自由金属氧化物、半金属氮化物和金属氮化物组成的群组的化合物。金属氧化物和金属氮化物优选选自由氧化铝、氮化铝和氮化硅组成的群组。至少一种化合物优选具有在0.01μm至100μm范围内的晶粒大小。特定地,至少一种化合物为氧化铝,其中氧化铝更优选具有在0.01μm至25μm范围内的晶粒大小。此外,至少一种化合物优选具有含中位值d50和算术平均值darith的晶粒大小的数目分布,其中d50与darith的比率优选在0.50至1.50范围内,优选在0.75至1.10范围内,更优选在0.78至1.05范围内,尤其优选在0.80至1.00范围内。更优选地,至少一种化合物为氧化铝且氧化铝优选具有含中位值d50和算术平均值darith的晶粒大小的数目分布,其中d50与darith的比率优选在0.75至1.10范围内,优选在0.78至1.05范围内,甚至更优选在0.80至1.00范围内。在本发明的情形下,这些值不应视为晶粒大小分布的严格上限和下限,而是可以变化+/-10%。然而,在一个优选实施例中,其为不可削低的下限和不可超过的上限。如所属领域的技术人员所熟知,晶粒大小分布可以参照晶粒数目(即数目分布)或者参照晶粒的质量(即质量分布)或体积而确定。在本发明的情形下,晶粒大小分布是基于晶粒数目确定。如一般所知,晶粒大小分布的特征值包括其d50值、d5值和d95值。关于d50值,其常称为中位值,50%的晶粒具有小于d50值的直径。晶粒大小分布的算术平均值darith由个别晶粒的晶粒大小的总和除以晶粒数目产生。晶粒大小分布的对称性可以由所述分布的中值d50与算术平均值darith的比率(即,商d50/darith,也称为晶粒大小数目分布的对称性值)表示。此商值越接近1.0,晶粒大小分布越对称。专家熟悉例如在起始衬底的制造期间适合调整陶瓷衬底中、特别是氧化铝中的晶粒大小分布的对称性的方法。举例来说,晶粒大小分布的对称性可受起始衬底制造期间的烧结持续时间和烧结温度的影响。本发明还涉及具有前述特征的激光的用途,其用于烧蚀金属-陶瓷衬底。在以上所提及的所有实施例中,优选使用dcb衬底。实例参照以下实例进一步解释本发明,以下实例说明本发明。根据所属领域的技术人员已知的标准程序制备若干dcb衬底。使用al2o3陶瓷作为衬底且使用铜箔来制备衬底上的金属覆盖层。al2o3陶瓷衬底以0.25与0.40mm之间的厚度使用,而金属铜覆盖层则以0.38至0.63mm之间的厚度使用。按以下这组激光参数进行实验:激光输出功率:可变高达100w激光源:红外线脉冲长度:0.1至100ps脉冲能量:10至500μj斑直径:30μm激光频率:350至650khz在实验中,烧蚀陶瓷衬底(al2o3)上的金属(铜)。如下评估所得金属陶瓷衬底:以上所示的表证明,从右至左(其意指从高激光功率至低激光功率和从低激光速度至高激光速度),上面的金属(铜)被烧蚀的金属陶瓷衬底的外观改进。另一方面,从左至右(其意指激光通过金属陶瓷衬底的数目减小),由以上所示的表得到经济合理的处理。以粗体表示的值是优选的。基于以上所示的表中所提供的资料,可以推导出激光功率(w)与激光速度(m/sec,有效)之间的数学关系。图1中的图表显示激光功率(w)与激光速度(m/sec)之间的前述关系:在这个图1的图表中,激光功率与激光速度的不可用的组合和优选范围(+至+++和外推的)以对数函数形式呈现,其定义如下:一般可接受范围:y≤4.7lnx-15优选范围:y≤5.0lnx-18,其中x=激光功率,w;且y=激光速度(有效)。这意指:在100w的激光功率下,根据本发明的激光速度为小于6.6m/sec(一般可接受范围)和5.0m/sec(优选范围)。考虑到激光功率与激光速度(有效)之间的这种关系,进行其它实例且获得以下发现:基于以上发现,可以得出以下陈述:(1)激光功率激光功率优选为30w或更大。激光功率进一步优选为60w或更大(出于经济原因)。激光功率更优选为80w或更大。(2)激光速度激光速度(有效)优选为0.2m/sec或更大。激光速度进一步优选为0.5m/sec或更大。激光速度更优选为0.75m/sec或更大。以上所呈现的结果是基于以下实例:第一实例-根据本发明a.如上文所提及的参数b.激光功率:70瓦特c.激光速度(有效):1.0m/secd.陶瓷厚度0.63mm;铜厚度0.30mme.结果:i.良好光学外观ii.仅少量熔融相;仅少量铜氧化iii.表面的光学粗糙度低iv.处理速度可接受的第二实例-根据本发明a.如上文所提及的参数b.激光功率:100瓦特c.激光速度(有效):1.5m/secd.陶瓷厚度0.38mm;铜厚度0.30mme.结果:i.可接受的光学外观ii.较多熔融相和铜氧化iii.表面的光学粗糙度较高iv.处理速度低第三实例-根据本发明a.如上文所提及的参数b.激光功率:50瓦特c.激光速度(有效):3.0m/secd.陶瓷厚度0.63mm;铜厚度0.25mme.结果:i.极佳光学外观ii.几乎没有熔融相和铜氧化iii.几乎没有表面光学粗糙度iv.处理速度非常低;出于经济原因,此程序不太适合。第四实例-非根据本发明a.如上文所提及的参数b.激光功率:60瓦特c.激光速度(有效):6m/secd.陶瓷厚度0.38mm;铜厚度0.20mme.结果:i.铜烧蚀得非常缓慢ii.处理速度过低iii.几乎无残留iv.表面的光学粗糙度非常低v.处理速度如此低,以致于出于经济原因,不能施加所述工艺第五实例-根据本发明a.如上文所提及的参数b.激光功率:90瓦特c.激光速度(有效):0.25m/secd.陶瓷厚度0.63mm;铜厚度0.30mme.结果:i.许多熔融相保持于表面上ii.铜氧化程度高iii.几乎无残留iv.表面的光学粗糙度非常高v.关于对质量要求低的应用,给出了具有高经济效率的参数区域第六实例-非根据本发明a.如上文所提及的参数b.激光功率:100瓦特c.激光速度(有效):0.15m/secd.陶瓷厚度0.63mm;铜厚度0.40mme.结果:i.铜烧蚀质量非常差;预期不使用这些工艺参数ii.材料在处理期间变得非常温热iii.工艺参数在技术上不可行。当前第1页1 2 3