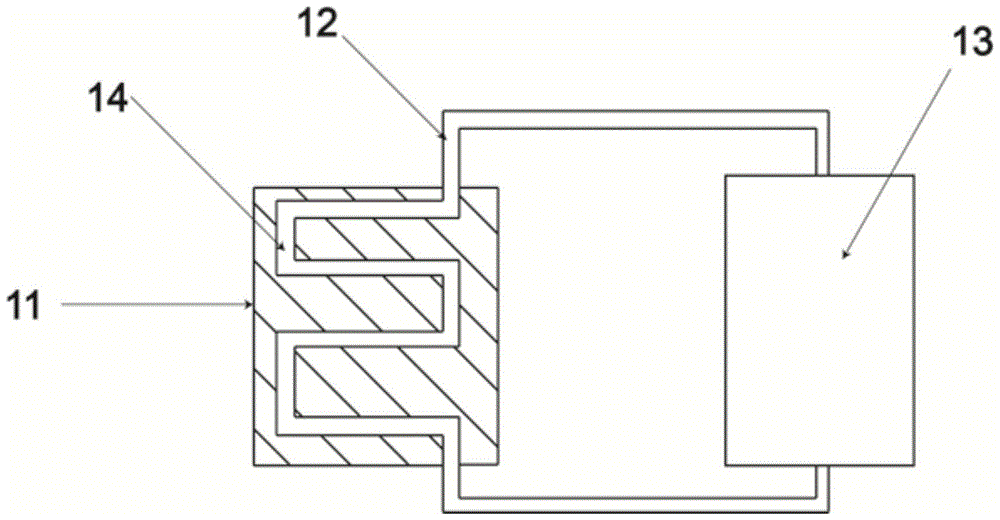
本发明属于高能束增材制造技术领域,具体涉及一种成形区域温度梯度可控的高能束选区熔化方法与设备,尤其适用于大尺寸、高性能、高精度、复杂结构定向凝固金属构件与单晶金属构件的高效率成形。
背景技术:高能束选区熔化技术是一种新兴的基于粉末床铺设的增材制造技术,其过程可概括如下:首先用三维软件设计出待成形零部件的3D模型并转换成STL格式;再由切片软件进行切片处理生成二维高能束扫描轨迹;然后在基板表面预置一层具有一定厚度的粉末,并根据预设轨迹控制高能束(激光束或电子束)对粉末床进行选区熔化,进而冷却、凝固形成沉积层;扫描完成后将基板下降一个与预置粉末层厚度相当的距离;不断重复上述铺粉、扫描与基板下降的过程,直至完成整个零部件的成形。由于高能束选区熔化技术采用聚焦束斑极小(通常为0.1~0.5mm)的高能束在厚度仅为0.02~0.2mm的粉层上快速扫描,高能束辐照所形成的熔池尺寸通常为微米级。此时,熔池下方的基板或零部件已凝固部分可作为有效的散热体,令熔池内部产生极高的温度梯度,使熔池的定向凝固成为可能。此外,高能束选区熔化技术可以成形常规方法难以加工的复杂、精细结构件。因此,有望利用高能束选区熔化技术制造在航空航天等领域具有重要意义的高性能、复杂结构定向凝固金属构件与单晶金属构件。目前,国内外已有部分研究者开展了利用高能束选区熔化技术成形定向凝固金属构件与单晶金属构件的研究。在国内文献【选区激光熔化成形SRR99镍基单晶的基础研究】(华中科技大学硕士学位论文,2013年)中,研究者利用激光选区熔化技术获得了高度为2mm的SRR99镍基单晶实体。在国外文献【TexturesformedinaCoCrMoalloybyselectivelasermelting】(DOI:http://dx.doi.org/10.1016/j.jallcom.2015.01.096)中,研究者同样通过激光选区熔化技术制造出边长为10mm的单晶CoCrMo立方体。在国外文献【Sitespecificcontrolofcrystallographicgrainorientationthroughelectronbeamadditivemanufacturing】(DOI:10.1179/1743284714Y.0000000734)中,研究者则利用电子束选区熔化技术实现了体积为25.4×25.4×12.7mm3的Inconel718镍基高温合金构件的定向凝固成形。然而,现有高能束选区熔化技术所成功制造的定向凝固产品或单晶产品的尺寸仅为毫米级,无法在真正意义上实现高性能、大尺寸、复杂结构定向凝固金属构件与单晶金属构件的高效、近净成形。
技术实现要素:针对现有高能束选区熔化技术的不足,本发明提出了一种成形区域温度梯度可控的高能束选区熔化方法与设备,旨在实现大尺寸、高性能、高精度、复杂结构定向凝固金属构件与单晶金属构件的高效率成形。本发明提供的一种高能束选区熔化方法,该方法为高能束选区熔化制造过程预设特征温度梯度区间[G1,G2],G1为使熔池实现定向凝固的最小温度梯度,G2为避免成形件残余应力超出其屈服强度而为熔池所设置的最大温度梯度;在定向凝固金属构件与单晶金属构件的高能束选区熔化制造过程中,以成形区域的稳定温度作为边界条件实时计算熔池内部温度梯度区间,并通过对成形区域施加合适的热流条件实现对成形区域及所述熔池内部温度梯度区间的实时调控,使所述熔池内部温度梯度区间尽量保持在所述特征温度梯度区间内,直至获得所需尺寸、性能、精度和显微结构的金属构件。本发明提供的一种高能束选区熔化设备,包括成形组件,其特征在于,所述成形组件中设置有测温模块和温控模块;测温模块包括一个粉末床测温子模块以及N个成形缸测温子模块,N≥1;所述粉末床测温子模块位于成形缸体上方,用于测量零部件成形过程中粉末床表面的温度场分布;所述N个成形缸测温子模块位于成形缸体侧壁外侧并将后者紧密环绕,用于测量成形缸体侧壁的温度场分布;粉末床测温子模块与成形缸测温子模块还用于将其测得的成形区域温度场分布传输至控制系统;温控模块包括一个基板温控子模块以及M个成形缸温控子模块,M≥1(M与N可相等或不等);所述基板温控子模块与基板相连且位于基板下方,它根据控制系统所发送的控制信号,为基板提供合适的热流条件;所述M个成形缸温控子模块位于成形缸体侧壁外侧并将后者紧密环绕,它们根据控制系统所发送的控制信号,为成型缸侧壁提供合适的热流条件;本发明具有以下技术效果:(1)本发明可以实时监控高能束选区熔化成形区域的温度梯度,并在必要时对其进行调控,以确保熔池的定向凝固条件,实现大尺寸、高性能、高精度、复杂结构定向凝固金属构件与单晶金属构件的高效成形;(2)本发明可根据实际加工需要灵活调整测温模块与温控模块的结构及其所包含子模块的数量,进而在保证完成定向凝固构件与单晶构件成形的前提下降低制造、运行与维护成本;(3)利用本发明可灵活改变成形过程各阶段的温度梯度分布,制造功能/结构梯度零部件。附图说明图1为本发明所公布的第一种优选的成形区域温度梯度可控的高能束选区熔化设备的成形组件与高能束输出模块示意图;图2为实施例1所涉及的降温子集成块的构成示意图;图3为本发明所公布的第二种优选的成形区域温度梯度可控的高能束选区熔化设备的成形组件与高能束输出模块示意图;图4为本发明所公布的第三种优选的成形区域温度梯度可控的高能束选区熔化设备的基板温控子模块71示意图;图5为本发明所公布的第三种优选的成形区域温度梯度可控的高能束选区熔化设备的成形缸温控子模块72示意图。具体实施方式申请人通过研究发现:现有高能束选区熔化技术在制造定向凝固金属构件与单晶金属构件时,由于成形区域内不可避免的热积累效应,基板与零部件已凝固部分的温度常随扫描沉积层数的增加而逐渐上升。这一问题致使熔池内部的温度梯度常随加工层数增加而不断下降,难以在整个制造过程中维持熔池的定向凝固条件。因此,必须在高能束选区熔化制造过程中有效控制成形区域的温度梯度,才能制备出大尺寸、高性能、高精度、复杂结构定向凝固金属构件与单晶金属构件。本发明实例提供的高能束选区熔化方法,具体包括下述步骤:(1)将基板安装在成形缸体内部并调平;其中,基板的材料应与待加工零件相同,基板的晶体取向亦应与待加工零件所需的晶体取向相同;(2)控制系统根据待加工零件CAD模型生成高能束扫描轨迹;气氛控制模块为成形区域提供惰性气体保护环境或真空环境;(3)利用凝固理论,根据待加工材料与高能束选区熔化参数可以计算出使熔池实现定向凝固的最小温度梯度其中,V为高能束扫描速度;K、g为与待加工材料相关的常数,可通过材料学、冶金学相关数据库查得;(4)为避免成形件残余应力超出其屈服强度,须为熔池设置最大温度梯度G2(G2>G1);G2的具体数值应满足:当熔池内部最大温度梯度达到G2时,成形件不出现变形或裂纹;G1、G2共同组成特征温度梯度区间[G1,G2];(5)将基板上升至成形缸体的顶部,铺粉器在前者上方预置一层具有一定厚度的粉末并重复第(6)步至第(10)步,直至完成定向凝固金属构件或者单晶金属构件的成形;(6)为成形区域提供合适的热流条件,并实时测量成形区域的稳定温度,使得以其为边界条件,计算出的熔池内部温度梯度区间[G3,G4]被特征温度梯度区间[G1,G2]所包含,即满足G1<G3<G4<G2;(7)高能束输出模块根据已生成的扫描轨迹选择性熔化粉末层;扫描结束后,将基板下降一个与粉层厚度相同的距离,重新铺粉并扫描加工下一层;(8)下一层的扫描加工完成后,再次将各测温子模块所实际测定的成形区域的稳定温度作为边界条件并传输至控制系统,控制系统利用该温度边界条件,根据成熟的有限元理论或有限差分理论所计算出的熔池内部温度梯度区间[G3,G4];(9)将基板再次下降一个与粉层厚度相同的距离,并在基板上再次预置一层粉末;(10)若满足G1<G3<G4<G2,则重复步骤(7)~(9);若G3≦G1或G4≧G2,则转入第(6)步。与现有高能束选区熔化成形设备相比,本发明主要是对成形组件进行了改进,所提供设备的成形组件除包括成形缸体、基板、基板升降驱动系统外,还包含了测温模块与温控模块;其中,基板位于成形缸体内部;测温模块由一个位于成形缸体上方的粉末床测温子模块与N个位于成形缸体侧壁外侧的成形缸测温子模块构成(N≥1);位于成形缸体上方的粉末床测温子模块由若干红外测温仪或激光测温仪构成,用以通过非接触的方式测量零部件成形过程中粉末床表面的温度场;位于成形缸体侧壁外侧的成形缸测温子模块由若干热电偶、红外测温仪或激光测温仪构成,用以通过非接触或接触的方式测量成形缸体侧壁的温度分布;温控模块由一个位于基板下方的基板温控子模块与M个位于成形缸体侧壁外侧的成形缸温控子模块构成(M≥1,M与N可相等或不等);每个基板温控子模块与成形缸温控子模块不仅可由一个降温子集成块构成,亦可由一组或多组降温子集成块与升温子集成块交替放置而构成;降温子集成块由冷却端、冷却介质循环通道、制冷单元构成;冷却端可选用导热能力较好的金属材料,其表面应紧贴成形缸侧壁或基板底部的对应位置;冷却端内部包含冷却介质回路,该回路通过冷却介质循环通道与制冷单元相连;冷却介质循环通道可选用商用耐低温软管或者金属管;制冷单元可选用不同类型的商用低温冷却液循环供给设备、电制冷设备、液氮、液氩或者其它低温气体,并通过冷却介质循环通道为冷却端提供冷却介质,使冷却端的温度可在-120℃~+20℃范围内调节,进而使降温子集成块能为成形缸侧壁或基板底部的对应位置施加合适的热流条件;升温子集成块可选用商用热电阻或电磁、电感加热装置,其温度可在+20℃~+300℃范围内调节,进而为成形缸侧壁或基板底部的对应位置施加合适的热流条件;基板升降驱动系统可带动基板、基板温控子模块沿成形缸体中心线方向垂直上下运动;根据实际需要,本发明所提供设备可包含一个或多个成形组件;所述控制系统用于生成高能束扫描轨迹,接收测温模块所提供的成形区域温度并计算熔池温度梯度,控制高能束输出模块、气氛控制模块、粉末供给回收模块与成形组件之间的协调运转;所述高能束输出模块位于成形组件上方,并为后者提供高能束能量源,其数量不少于一个;当选用激光束作为高能束能量源时,高能束输出模块包含激光器、扫描振镜和相应的激光辅助传导装置;当选用电子束作为高能束能量源时,高能束输出模块包含电子枪、电子偏转器和相应的电子束辅助传导装置;所述气氛控制模块用于实时调控高能束选区熔化成形区域的气氛,可提供惰性气体保护环境或真空环境;所述粉末供给回收模块包含粉末供给系统、铺粉器、粉末回收系统;铺粉器用于接受粉末供给系统提供的粉末原料,并将粉末在基板或零部件已成形部分的上表面以一定厚度均匀铺置;铺粉完成后多余的粉末由铺粉器送入粉末回收系统。当待加工材料的定向凝固能力较强,或待成形件尺寸较小时,可将所述M个成形缸温控子模块去除,以兼顾成形质量与成本。由于本发明所提供设备的温控子模块可同时包含一组或多组降温子集成块与升温子集成块,通过对降温子集成块与升温子集成块进行联动控制,还可为成形区域提供不同的温度梯度,以使熔池满足其他凝固条件。同时,本发明所提供设备的温控/测温子模块的数量、放置形式也可根据实际需要灵活调整。因此,本发明还提供了上述技术方案的几种具体优选方案及其对应的技术流程。下面通过借助实施例及附图更加详细地说明本发明,但下列实施例及附图仅是说明性的,本发明的保护范围并不受这些实施例的限制。此外,下面所描述的本发明各个实施方式中所涉及到的技术特征只要彼此之间未构成冲突就可以相互组合。实施例1本发明所公布的第一种优选的成形区域温度梯度可控的高能束选区熔化设备包括成形组件、控制系统、高能束输出模块、气氛控制模块和粉末供给回收模块。如图1所示,成形组件由成形缸体1、基板2、测温模块3、温控模块4和基板升降驱动系统5组成。其中,基板2位于成形缸体1内部;测温模块3包含测温子模块61~6n(n≧2):粉末床测温子模块61位于成形缸体1上方不影响高能束输出模块8正常工作的任意位置,其内部包含若干红外测温仪或激光测温仪,用以测量零部件成形过程中粉末床表面的温度场分布;成形缸测温子模块62~6n位于成形缸体侧壁9的外侧,前者呈现环形并将后者紧紧环绕;成形缸测温子模块62~6n均可包含若干热电偶、红外测温仪或激光测温仪,用以测量成形缸体侧壁9的温度场分布。温控模块4包含温控子模块71~7n,其中基板温控子模块71位于基板2下方并与后者下表面紧密接触;成形缸温控子模块72~7n位于成形缸体侧壁9的外侧,前者呈现环形并将后者紧紧环绕。;基板温控子模块71与成形缸温控子模块72~7n均包含一个降温子集成块10;如图2所示,降温子集成块10由冷却端11、冷却介质循环通道12和制冷单元13构成;冷却端11可选用导热能力较好的金属材料,其表面应紧贴成形缸侧壁或基板底部的对应位置;冷却端11内部包含冷却介质回路14,该回路通过冷却介质循环通道12与制冷单元13相连;冷却介质循环通道12可选用商用耐低温软管或者金属管;制冷单元13可选用不同类型的商用低温冷却液循环供给设备、电制冷设备、液氮、液氩或者其它低温气体,使冷却端11的温度可在-120℃~+20℃范围内调节,进而使降温子集成块10能为成形缸侧壁或基板底部的对应位置施加合适的热流条件;成形缸温控子模块72~7n与成形缸测温子模块62~6n沿成形缸体1中心线方向自上至下呈周期性交错排列,并将整个成形缸体侧壁9均匀包围;基板升降驱动系统5位于基板2与基板温控子模块71下方,并可带动基板2与基板温控子模块71沿成形缸体1中心线方向进行垂直往复运动。所述控制系统用于生成高能束二维扫描轨迹,接收测温子模块61~6n所提供的成形区域温度并计算熔池温度梯度,控制高能束输出模块8、气氛控制模块、粉末供给回收模块与成形组件之间的协调运转;高能束输出模块8位于成形组件上方,并为后者提供高能束能量源。气氛控制模块用于实时调控高能束选区熔化成形区域的气氛,可提供惰性气体保护环境或真空环境。粉末供给回收模块包含粉末供给系统、铺粉器、粉末回收系统;铺粉器用于接受粉末供给系统提供的粉末原料,并将粉末在基板或零部件已成形部分的上表面以一定厚度均匀铺置;铺粉完成后多余的粉末由铺粉器送入粉末回收系统。下面具体阐述利用上述设备高效成形尺寸为5×5×10cm3的高性能、高精度SRR99镍基单晶长方体构件的方法:(1)选用SRR99镍基单晶基板,将基板安装在成形缸体内部并调平;其中,基板呈(001)晶面平行于上表面的晶体取向;(2)选用激光束作为加工用高能束;控制系统根据长方体构件的CAD模型生成激光束扫描轨迹;气氛控制模块为成形区域提供氩气保护环境,使成形区域氧含量低于200ppm;设置激光选区熔化成形参数为:激光功率180W,激光光斑直径0.1mm,铺粉层厚度0.02mm,相邻扫描线间距0.08mm,激光扫描速度300mm/s;(3)利用凝固理论,并根据预设的激光扫描速度与SRR99镍基合金的相关常数计算出使熔池实现定向凝固的最小温度梯度G1=1.07×107K/m;(4)为避免因残余应力超出其屈服强度而使成形件产生变形或裂纹,根据前期预实验为熔池设置最大温度梯度G2=5×1010K/m;G1、G2共同组成特征温度梯度区间[G1,G2];(5)将基板上升至成形缸体的顶部,铺粉器在前者上方预置一层厚度为0.02mm的SRR99镍基合金粉末;(6)开启温控子模块71~7n,并设置其所包含降温子集成块10的温度T(1)~T(n)为:0℃=T(2)=T(3)=…=T(n)=T(1)=0℃;各降温子集成块10温度设置完毕后,成形区域接受温控子模块的热流条件发生温度变化,将测温子模块61~6n所测定成形区域重新稳定后的温度作为边界条件并传输至控制系统,控制系统利用该温度边界条件,根据成熟的有限元理论所计算出的熔池内部温度梯度区间为[G3=6×108K/m,G4=6.1×109K/m],前者完全被特征温度梯度区间[G1,G2]所包含,即满足G1<G3<G4<G2;(7)高能束输出模块在控制系统的驱动下,根据已生成的扫描轨迹发射激光束并选择性熔化粉末层;扫描结束后,将基板下降0.02mm,重新铺粉并扫描加工下一层;(8)下一层的扫描加工完成后,再次将各测温子模块所实际测定的成形区域的稳定温度作为边界条件并传输至控制系统,控制系统利用该温度边界条件,根据成熟的有限元理论所计算出的熔池内部温度梯度区间[G3,G4]仍被特征温度梯度区间[G1,G2]所包含,即满足G1<G3<G4<G2;(9)不断重复上述铺粉、激光束选择性熔化、熔池温度梯度区间计算的过程,直至完成第3022层粉末层的选择性熔化;在此期间,控制系统所计算出的熔池内部温度梯度区间[G3,G4]始终被特征温度梯度区间[G1,G2]所包含,即满足G1<G3<G4<G2;(10)再次铺粉并完成第3023层粉末层的选择性熔化后,由于基板及零件已成形部分的热积累,控制系统所计算出的熔池内部温度梯度区间[G3=9.8×106K/m,G4=2.3×108K/m]没有完全被特征温度梯度区间[G1,G2]所包含;(11)重新设置温控子模块71~7n所包含降温子集成块10的温度T(1)~T(n)为:-20℃=T(2)=T(3)=…=T(n)>T(1)=-50℃;各降温子集成块10温度设置完毕后,成形区域接受温控子模块的热流条件发生温度变化,将测温子模块61~6n所测定成形区域重新稳定后的温度作为边界条件并传输至控制系统,控制系统利用该温度边界条件,根据成熟的有限元理论所计算出的熔池内部温度梯度区间为[G3=3×109K/m,G4=2×1010K/m],前者完全被特征温度梯度区间[G1,G2]所包含,即满足G1<G3<G4<G2;(12)不断重复上述铺粉、激光束选择性熔化、熔池温度梯度区间计算的过程,直至完成SRR99镍基单晶长方体构件的快速制造;在此期间,控制系统所计算出的熔池内部温度梯度区间[G3,G4]始终被特征温度梯度区间[G1,G2]所包含,即满足G1<G3<G4<G2;由于同时具备位于基板底部的基板温控子模块71与位于成形缸侧壁外侧的成型缸温控子模块72~7n,本实施例所公布的高能束选区熔化设备对成形区域温度梯度的调控能力极强。当配合使用本实施例所公布的高能束选区熔化方法时,可以实现各种大尺寸、高性能、高精度、复杂结构的单晶/定向凝固金属零部件的高效成形。实施例2当待成形金属构件的尺寸较小,或待成形金属构件的单晶/定向凝固结构形成趋势较强时,还可选用下述第二种优选的成形区域温度梯度可调控的高能束选区熔化设备,进而兼顾定向凝固/单晶金属产品的质量与加工成本。本发明所涉及的第二种优选的成形区域温度梯度可控的高能束选区熔化设备仍包括成形组件、控制系统、高能束输出模块、气氛控制模块与粉末供给回收模块。其中,控制系统、高能束输出模块、气氛控制模块与粉末供给回收模块的结构、功能仍与实施例1中所公布的相同,而成形组件的内部构成则予以较大改进。如图3所示,此时成形组件由成形缸体1、基板2、测温模块3、温控模块4、基板升降驱动系统5组成。其中,基板2位于成形缸体1内部;测温模块3仍由测温子模块61~6n构成,其结构、功能仍与实施例1中所公布的相同;温控模块4仅包含一个基板温控子模块71;基板温控子模块71位于基板2下方并与后者下表面紧密接触,其内部构成与实施例1中的基板温控子模块71相同;基板升降驱动系统5的结构、功能仍与实施例1中所公布的相同。利用上述设备可以在兼顾质量与成本的条件下实现小尺寸、高性能、高精度、复杂结构定向凝固金属构件或单晶金属零部件的高效率成形,其具体方法与实施例1所公布的方法大体相同。唯一不同之处在于,此时仅需调控基板温控子模块71的温度以使熔池温度梯度区间始终位于特征温度梯度区间内部,从而令操作大大简化。下面具体阐述利用上述设备高效成形尺寸为1×1×1cm3的高性能、高精度SRR99镍基单晶立方体构件的方法:(1)选用SRR99镍基单晶基板,将基板安装在成形缸体内部并调平;其中,基板呈(001)晶面平行于上表面的晶体取向;(2)选用激光束作为加工用高能束;控制系统根据长方体构件的CAD模型生成激光束扫描轨迹;气氛控制模块为成形区域提供氩气保护环境,使成形区域氧含量低于200ppm;设置激光选区熔化成形参数为:激光功率200W,激光光斑直径0.1mm,铺粉层厚度0.02mm,相邻扫描线间距0.08mm,激光扫描速度100mm/s;(3)利用凝固理论,并根据预设的激光扫描速度与SRR99镍基合金的相关常数计算出使熔池实现定向凝固的最小温度梯度G1=7.78×106K/m;(4)为避免因残余应力超出其屈服强度而使成形件产生变形或裂纹,根据前期预实验为熔池设置最大温度梯度G2=1×1010K/m;G1、G2共同组成特征温度梯度区间[G1,G2];(5)将基板上升至成形缸体的顶部,铺粉器在前者上方预置一层厚度为0.02mm的SRR99镍基合金粉末;(6)开启温控子模块71,并设置其所包含降温子集成块10的温度T(1)为:T(1)=0℃;设置完毕后,成形区域接受温控子模块的热流条件发生温度变化,将测温子模块61~6n所测定成形区域重新稳定后的温度作为边界条件并传输至控制系统,控制系统利用该温度边界条件,根据成熟的有限差分理论所计算出的熔池内部温度梯度区间为[G3=3×108K/m,G4=5.2×109K/m],前者完全被特征温度梯度区间[G1,G2]所包含,即满足G1<G3<G4<G2;(7)高能束输出模块在控制系统的驱动下,根据已生成的扫描轨迹发射激光束并选择性熔化粉末层;扫描结束后,将基板下降0.02mm,重新铺粉并扫描加工下一层;(8)下一层的扫描加工完成后,再次将各测温子模块所实际测定的成形区域的稳定温度作为边界条件并传输至控制系统,控制系统利用该温度边界条件,根据成熟的有限差分理论所计算出的熔池内部温度梯度区间[G3,G4]仍被特征温度梯度区间[G1,G2]所包含,即满足G1<G3<G4<G2;(9)不断重复上述铺粉、激光束选择性熔化、熔池温度梯度区间计算的过程,直至完成第376层粉末层的选择性熔化;在此期间,控制系统所计算出的熔池内部温度梯度区间[G3,G4]始终被特征温度梯度区间[G1,G2]所包含,即满足G1<G3<G4<G2;(10)再次铺粉并完成第377层粉末层的选择性熔化后,由于基板及零件已成形部分的热积累,控制系统所计算出的熔池内部温度梯度区间[G3=7.72×106K/m,G4=1.4×108K/m]没有完全被特征温度梯度区间[G1,G2]所包含;(11)重新设置温控子模块71所包含降温子集成块10的温度T(1)为:T(1)=-20℃;设置完毕后,成形区域接受温控子模块的热流条件发生温度变化,将测温子模块61~6n所测定成形区域重新稳定后的温度作为边界条件并传输至控制系统,控制系统利用该温度边界条件,根据成熟的有限差分理论所计算出的熔池内部温度梯度区间为[G3=7.7×108K/m,G4=8.9×109K/m],前者完全被特征温度梯度区间[G1,G2]所包含,即满足G1<G3<G4<G2;(12)不断重复上述铺粉、激光束选择性熔化、熔池温度梯度区间计算的过程,直至完成SRR99镍基单晶立方体构件的快速制造;在此期间,控制系统所计算出的熔池内部温度梯度区间[G3,G4]始终被特征温度梯度区间[G1,G2]所包含,即满足G1<G3<G4<G2;实施例3利用本发明不仅可以使成形区域的温度梯度始终满足定向凝固条件,进而实现金属构件的定向凝固或者单晶零部件的高效成形,还可以根据实际加工需要,灵活改变成形过程各阶段的温度梯度分布,进而制造出各种类型的功能/结构梯度构件。为实现这种目的,实施例3公布了第三种优选的成形区域温度梯度可控的高能束选区熔化设备。该设备的整体结构仍可与实施例1所公布的设备一致,区别在于,本实施例对高能束选区熔化设备所包含的温控子模块71~7n的内部结构与功能进行了较大改进。如图4所示,位于基板2下方的基板温控子模块71由数量相同的降温子集成块和升温子集成块组合而成(m≧1)。降温子集成块的构成、功能均与实施例1所公布的降温子集成块10相同;升温子集成块可选用商用热电阻或电磁、电感加热装置,使其温度可在+20℃~+300℃之间任意调节。降温子集成块和升温子集成块相互交叉平行排列,他们的上表面均紧贴基板2的下表面。为避免降温子集成块和升温子集成块相互影响,在相邻的降温子集成块和升温子集成块之间放置绝热层16,绝热层16可选用商用绝热材料。如图5所示,位于成形缸体侧壁9外侧的成形缸温控子模块72由两个垂直放置的降温子集成块和升温子集成块组成,降温子集成块和升温子集成块的内部构成分别与基板温控子模块71中的降温子集成块和升温子集成块相同。降温子集成块和升温子集成块之间同样放置绝热层16。成形缸温控子模块73~7n的结构与成形缸温控子模块72相同。利用第三种优选的成形区域温度梯度可控的高能束选区熔化设备制造功能/结构梯度构件的控制流程为:(1)将基板2安装在成形缸体内部并调平;其中,基板2的材料、组织结构应满足待加工零件最下方的功能/结构需求;(2)控制系统根据待加工零件CAD模型生成高能束扫描轨迹;气氛控制模块根据实际需要为成形区域提供惰性气体保护环境或真空环境;(3)根据梯度构件不同高度位置处的具体结构/功能要求,将成形过程分为j个阶段(j≧2),并为每个阶段设置不同的熔池特征温度梯度区间(4)将基板2上升至成形缸体1的顶部,铺粉器在前者上方预置一层具有一定厚度的粉末并重复第(5)步至第(9)步,直至完成第1成形阶段;(5)开启温控子模块71~7n,并遵循下述条件设置其所包含的降温子集成块与升温子集成块的温度:温控子模块71~7n所包含的降温子集成块与升温子集成块的温度设置完毕后,成形区域接受其所施加的热流条件发生温度变化,将测温子模块61~6n所测定成形区域稳定后的温度作为边界条件并传输至控制系统,控制系统利用该温度边界条件,根据成熟的有限元理论或有限差分理论所计算出的熔池内部温度梯度区间[G3,G4]应被第一成形阶段的特征温度梯度区间所包含,即满足(6)高能束输出模块8根据已生成的扫描轨迹选择性熔化粉末层;扫描完成后,将基板2下降与一个粉层厚度相同的距离,重新铺粉并扫描加工下一层;(7)下一层的扫描加工完成后,再次将测温子模块61~6n所实际测定的成形区域温度作为边界条件并传输至控制系统,控制系统利用该温度边界条件,根据成熟的有限元理论或有限差分理论所计算出的熔池内部温度梯度区间[G3,G4];(8)将基板2再次下降一个与粉层厚度相同的距离,并在基板2上再次预置一层粉末;(9)若满足则重复步骤(6)~(8);若或则转入步骤(5);(10)根据第二成形阶段的特征温度梯度区间仿照步骤(5)~(9)重置温控子模块71~7n所包含的降温子集成块与升温子集成块的温度并在成形过程中适当予以调整,使熔池温度梯度区间[G3,G4]在第二成形阶段始终被熔池特征温度梯度区间所包含,即满足直至完成第二成形阶段;(11)依照上述步骤,依次完成后续j-2个成形阶段,进而实现功能/结构梯度构件的成形。下面结合一个镍基梯度构件的快速制造过程来更为直观的描述上述成形区域温度梯度可控的高能束选区熔化方法。其中,待成形梯度构件材料仍为SRR99镍基合金,其形状呈尺寸为5×5×15cm3的长方体;由于使用需要,该构件最上方5×5×1cm3的部分须为等轴凝固结构,而下方剩余5×5×14cm3的部分则须为单晶凝固结构。成形该梯度构件的方法如下:(1)选用SRR99镍基单晶基板,将基板安装在成形缸体内部并调平;其中,基板呈(001)晶面平行于上表面的晶体取向;(2)选用激光束作为加工用高能束;控制系统根据长方体构件的CAD模型生成激光束扫描轨迹;气氛控制模块为成形区域提供氩气保护环境,使成形区域氧含量低于200ppm;设置激光选区熔化成形参数为:激光功率200W,激光光斑直径0.1mm,铺粉层厚度0.02mm,相邻扫描线间距0.08mm,激光扫描速度100mm/s;(3)利用凝固理论,并根据预设的激光扫描速度与SRR99镍基合金的相关常数计算出使熔池实现定向凝固的最小温度梯度为避免残余应力超出其屈服强度而使成形件产生变形或裂纹,根据前期预实验为熔池设置最大温度梯度共同组成第一成形阶段的特征温度梯度区间(4)利用凝固理论,并根据预设的激光扫描速度与SRR99镍基合金的相关常数计算出使熔池不发生定向凝固的最大温度梯度为避免等轴凝固部分晶粒过于粗大而降低力学性能,根据前期预实验为熔池设置最小温度梯度共同组成第二成形阶段的特征温度梯度区间(5)将基板上升至成形缸体的顶部,铺粉器在前者上方预置一层厚度为0.02mm的SRR99镍基合金粉末;(6)设置温控子模块71~7n所包含的所有降温子集成块的温度为:-80℃;关闭温控子模块71~7n所包含的所有升温子集成块;各降温子集成块的温度设置完毕后,成形区域接受温控子模块的热流条件发生温度变化,将测温子模块61~6n所测定成形区域重新稳定后的温度作为边界条件并传输至控制系统,控制系统利用该温度边界条件,根据成熟的有限元理论所计算出的熔池内部温度梯度区间为[G3=4.5×109K/m,G4=2.8×1010K/m],前者完全被第一成形阶段的特征温度梯度区间所包含,即满足(7)高能束输出模块在控制系统的驱动下,根据已生成的扫描轨迹发射激光束并选择性熔化粉末层;扫描结束后,将基板下降0.02mm,重新铺粉并扫描加工下一层;(8)下一层的扫描加工完成后,再次将各测温子模块所实际测定的成形区域的稳定温度作为边界条件并传输至控制系统,控制系统利用该温度边界条件,根据成熟的有限元理论所计算出的熔池内部温度梯度区间[G3,G4]仍被第一成形阶段的特征温度梯度区间所包含,即满足(9)不断重复上述铺粉、激光束选择性熔化、熔池温度梯度区间计算的过程,直至完成第一成形阶段;在此期间,控制系统所计算出的熔池内部温度梯度区间[G3,G4]始终被第一成形阶段的特征温度梯度区间所包含,即满足(10)设置温控子模块71~7n所包含的所有升温子集成块的温度为:300℃;关闭温控子模块71~7n所包含的所有降温子集成块;各升温子集成块的温度设置完毕后,成形区域接受温控子模块的热流条件发生温度变化,将测温子模块61~6n所测定成形区域重新稳定后的温度作为边界条件并传输至控制系统,控制系统利用该温度边界条件,根据成熟的有限元理论所计算出的熔池内部温度梯度区间为[G3=8×105K/m,G4=6.9×106K/m],前者完全被第二成形阶段的特征温度梯度区间所包含,即满足(11)将基板下降0.02mm,并不断重复上述铺粉、激光束选择性熔化、熔池温度梯度区间计算的过程,直至完成第二成形阶段,进而实现镍基梯度构件的快速制造;在此期间,控制系统所计算出的熔池内部温度梯度区间[G3,G4]始终被第二成形阶段的特征温度梯度区间所包含,即满足值得说明的是,尽管上述实施例所公布的高能束选区熔化设备仅包含一个成形组件与一个高能束输出模块,但本发明所设计的思想可以方便的扩展到包含多个成形组件与多个高能束输出模块的高能束选区熔化设备当中。当高能束选区熔化设备包含多个成形组件时,为实现对成形区域温度梯度的实时调控,可使每个成形组件的组成、结构与控制流程均与上述实施例中所提及的相同。当高能束选区熔化设备包含多个高能束输出模块时,亦可使成形组件(一个或多个)的组成、结构与控制流程均与上述实施例中所提及的相同。此外,尽管本发明特别适用于各种类型定向凝固金属构件、单晶金属构件、结构/功能梯度构件的快速制造,利用本发明完成其他普通金属构件的快速制造也是方便可行的。以上所述仅为本发明的较佳实例,但本发明不应该局限于上述实例和附图所公开的内容。凡是不脱离本发明所公开的精神下完成的等效或修改,仍应视为本发明保护范围之内。