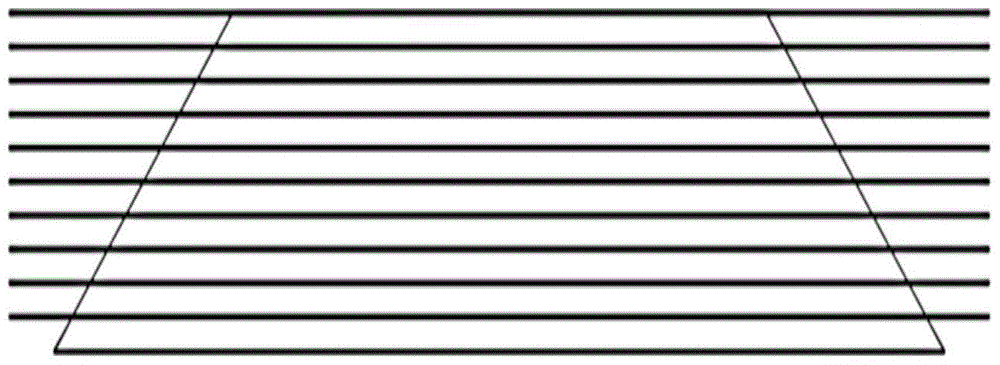
本发明属于增材制造技术领域,涉及一种分层块体金属增材制造方法。
背景技术:金属增材制造技术是利用高能束熔化金属粉末,逐点堆积成形三维实体的方法。此方法改变了传统去除材料的减材加工方式,实现了高柔性化“增材”的近净成形。金属增材制造技术以其具有无模具制造、工序简单、材料利用率高、综合性能优异等特点,受到制造业的广泛关注。但是,由于金属增材制造技术采用逐点堆积的方法成形,对于厚壁构件或截面较大的构件,因成形过程中长时间连续堆积会造成应力累积,导致零件开裂或变形等问题,影响厚壁构件、大型构件的成形质量。
技术实现要素:本发明的目的是提供一种分层块体金属增材制造方法,解决了现有金属增材制造过程中应力过度累积而导致零件开裂或变形的问题。本发明所采用的技术方案是,分层块体金属增材制造方法,包括以下步骤:步骤1:根据零件的结构设计出零件三维模型,确定零件模型成形生长方向;步骤2:利用切分软件将经步骤1获得的零件三维模型在成形生长方向上进行分层块处理,将最下层层块记为1号层块,次层记为2号层块,依次排序,直至最顶层,得到多层块,并生成多层块信息;步骤3:利用切分软件将步骤2获得的每层层块切分为多个厚度相同的基础单块和与基础单块形状互补的互补单块,分别对每层的基础单块和互补单块进行排序,并生成各层单块信息;步骤4:利用切分软件将步骤3已排序的每个单块进行切片分层,得到多层切片,并生成多层切片信息;步骤5:将经步骤2生成的多层块信息、经步骤3生成的单块信息和经步骤4生成的多层切片信息传输到金属增材制造设备中;步骤6:启动金属增材制造设备,按顺序逐层块、逐单块进行零件增材制造,最终获得成形零件。本发明的特点还在于,基础单块和互补单块为带有坡度或斜角的凸台式单块。基础单块的横截面形状为正方形、正六边形、圆形或正三角形。步骤2中,所述多层块的每层厚度h的范围为:10mm≤h≤100mm。步骤3中,单块排序的具体方法为:步骤3.1:对基础单块排序:随机选取任意基础单块,定义为1号单块,然后以1号单块为基准,距离1号单块最远的基础单块定义为2号单块;在剩余基础单块中与1号单块、2号单块距离之和最大的基础单块定义为3号单块;距离前三号单块距离之和最大的基础单块定义为4号单块;距离前四号单块距离之和最大的基础单块定义为5号单块;依次排序,第n个单块为与n-1、n-2、n-3、n-4、n-5号单块距离之和最大的基础单块,按上述方法排序,直至最后一个基础单块,定义为m号单块;步骤3.2:对互补单块排序:利用步骤3.1中与基础单块相同的排序方法对互补单块排序,互补单块起始序号为m+1号,直至最后一个互补单块。步骤4中,多层切片的每层高度Δh的范围为:0.5mm≤Δh≤3mm步骤6中,金属增材制造过程包括以下步骤:步骤6.1:根据零件结构特征规划零件切片扫描轨迹;步骤6.2:从1号层块的1号单块开始,利用金属增材制造设备逐单块、逐层块成形,直至成形完最后一个单块。步骤6.1中,零件切片扫描轨迹的规划方法为:在零件单层切片的轮廓线处随机选取一点作为起始点,以该点切线为基准,在零件单层切片轮廓范围内形成平行线系,每条平行线为单层切片增材制造成形熔池扫描运动轨迹中轴线,相邻平行线首尾相连形成单层切片成形熔池扫描运动轨迹,相邻平行线间距为光斑或熔池的运行单道间距,记为d,光斑半径或熔池半径≤d<光斑直径或熔池直径。金属增材制造设备为激光立体成形设备、氩弧焊立体成形设备或电子束立体成形设备。步骤6中,采用激光立体成形设备的加工参数为:激光功率500~8000W,光斑直径0.5~8mm,光斑运行单道间距0.25~4mm,光斑移动速度10~30mm/min。本发明的有益效果是:分层块体金属增材制造方法,将零件模型进行分层块、分单块处理,并且通过采用特定的单块成形顺序,有效的解决了现有金属增材制造过程中因长时间连续成形导致的应力聚集问题,有效缓解了堆积成形应力集中,大大降低激光成形时成形构件内部的残余应力,提高了产品的良品率,从而降低生产成本。同时,本发明通过将层块切分为多个带有坡度或斜角的凸台式单块,有效地解决了组成层块的相邻单块之间的结合问题,使得相邻单块结合紧密,使整个成形件力学性能优异。附图说明图1为本发明一种分层块体金属增材制造方法中分层块、分单块的示意图;图2是本发明分层块体金属增材制造方法中单块切片的示意图。具体实施方式下面结合附图和实施例对本发明进行详细说明。本发明分层块体金属增材制造方法,具体实施步骤如下:步骤1:根据零件的结构设计出零件三维模型,确定零件模型成形生长方向;步骤2:如图1所示,利用切分软件将经步骤1获得的零件三维模型在成形生长方向上进行分层块处理,将最下层层块记为1号层块,次层记为2号层块,依次排序,直至最顶层,得到多层块,并生成多层块信息,其中,多层块的每层厚度h的范围为:10mm≤h≤100mm;步骤3:如图1所示,利用切分软件将步骤2获得的每层层块切分为多个厚度相同的基础单块和与基础单块形状互补的互补单块,对每个基础单块和互补单块进行排序,并生成单块信息,其中,基础单块和互补单块为带有坡度或斜角的凸台式单块,基础单块的横截面形状为正方形、正六边形、圆形或正三角形;单块排序的具体方法为:步骤3.1:对基础单块排序:随机选取任意基础单块,定义为1号单块,然后以1号单块为基准,距离1号单块最远的基础单块定义为2号单块;在剩余基础单块中与1号单块、2号单块距离之和最大的基础单块定义为3号单块;距离前三号单块距离之和最大的基础单块定义为4号单块;距离前四号单块距离之和最大的基础单块定义为5号单块;依次排序,第n个单块为与n-1、n-2、n-3、n-4、n-5号单块距离之和最大的基础单块,按上述方法排序,直至最后一个基础单块,定义为m号单块;步骤3.2:对互补单块排序:利用步骤3.1中与基础单块相同的排序方法对互补单块排序,互补单块起始序号为m+1号,直至最后一个互补单块;步骤4:如图2所示,利用切分软件将步骤3已排序的每个单块进行切片分层,得到多层切片,并生成多层切片信息,其中,多层切片的每层高度Δh的范围为:0.5mm≤Δh≤3mm;步骤5:将经步骤2生成的多层块信息、经步骤3生成的单块信息和经步骤4生成的多层切片信息传输到金属增材制造设备中;步骤6:启动金属增材制造设备,进行零件增材制造,其中,金属增材制造设备为激光立体成形设备、氩弧焊立体成形设备或电子束立体成形设备;激光立体成形设备的加工参数为:激光功率500~8000W,光斑直径0.5~8mm,光斑运行单道间距0.25~4mm,光斑移动速度10~30mm/min;零件增材制造过程包括以下步骤:步骤6.1:根据零件结构特征规划零件切片扫描轨迹:在零件单层切片的轮廓线处随机选取一点作为起始点,以该点切线为基准,在零件单层切片轮廓范围内形成平行线系,每条平行线为单层切片增材制造成形熔池扫描运动轨迹中轴线,相邻平行线首尾相连形成单层切片成形熔池扫描运动轨迹,相邻平行线间距为光斑或熔池的运行单道间距,记为d,光斑半径或熔池半径≤d<光斑直径或熔池直径;步骤6.2:从1号层块的1号单块开始,利用金属增材制造设备逐单块、逐层块成形,直至成形完最后一个单块,最终获得成形零件。实施例1以分层块体激光立体成形钛合金长方体为例,长方体尺寸为700×800×1400mm,具体实施步骤如下:根据零件的结构设计出零件三维模型,确定零件模型成形生长方向,即选择700×800mm的构件表面作为与基材的贴合面,以1400mm的高度方向为构件成形生长方向;利用切分软件将获得的零件三维模型在成形生长方向上进行分层块处理,钛合金长方体模型被切分为140块层块,多层块的每层厚度h为10mm,将最下层层块记为1号层块,次层记为2号层块,依次排序,直至最顶层为140号层块,并生成多层块信息;将每层块切分为上下表面为正方形的带有坡度或斜角的基础单块,基础单块上表面边长为30mm,下表面边长为50mm,表面尺寸为700×800mm的层块被分割成224块基础单块,以及在700×800×10mm层块体内与上述基础单块互补的255块互补单块,并对基础单块和互补单块排序,其中,对基础单块排序:随机选取任意基础单块,定义为1号单块,然后以1号单块为基准,距离1号单块最远的基础单块定义为2号单块;在剩余基础单块中与1号单块、2号单块距离之和最大的基础单块定义为3号单块;距离前三号单块距离之和最大的基础单块定义为4号单块;距离前四号单块距离之和最大的基础单块定义为5号单块;依次排序,第n个单块为与n-1、n-2、n-3、n-4、n-5号单块距离之和最大的基础单块,按上述方法排序,直至最后一个基础单块,定义为m号单块;再对互补单块排序,互补单块起始序号为m+1号,直至最后一个互补单块,钛合金长方体共计排序67060块单块。利用切分软件将已排序的每个单块进行切片分层,获得形状为正方形,每层高度Δh为0.5mm的单块切片,每个单块共计50块切片,生成多层切片信息;将生成的多层块信息、单块信息和多层切片信息传输到金属增材制造设备中,规划零件切片扫描轨迹:在零件单层切片的轮廓线处随机选取一点作为起始点,以该点切线为基准,在零件单层切片轮廓范围内形成平行线系,每条平行线为单层切片增材制造成形熔池扫描运动轨迹中轴线,相邻平行线首尾相连形成单层切片成形熔池扫描运动轨迹,相邻平行线间距为光斑或熔池的运行单道间距,记为d,d=0.25mm,然后,启动激光立体成形设备,按照成形排序从零件的1号层块的1号单块开始,逐单块、逐层块成形,直至成形完所有67060块单块,最终获得成形零件;其中,激光功率500W,光斑直径0.5mm,光斑运行单道间距0.25mm,光斑移动速度10mm/min。实施例2以分层块体激光立体成形钛合金长方体为例,长方体尺寸为700×800×1400mm,具体实施步骤如下:根据零件的结构设计出零件三维模型,确定零件模型成形生长方向,即选择700×800mm的构件表面作为与基材的贴合面,以1400mm的高度方向为构件成形生长方向;利用切分软件将获得的零件三维模型在成形生长方向上进行分层块处理,钛合金长方体模型被切分为28块层块,多层块的每层厚度h为50mm,将最下层层块记为1号层块,次层记为2号层块,依次排序,直至最顶层层块,并生成多层块信息;将每层块切分为上下表面为正方形的带有坡度或斜角的基础单块,基础单块上表面边长为30mm,下表面边长为50mm,表面尺寸为700×800mm的层块被分割成基础单块及与上述基础单块互补的互补单块,并对基础单块和互补单块排序,其中,对基础单块排序:随机选取任意基础单块,定义为1号单块,然后以1号单块为基准,距离1号单块最远的基础单块定义为2号单块;在剩余基础单块中与1号单块、2号单块距离之和最大的基础单块定义为3号单块;距离前三号单块距离之和最大的基础单块定义为4号单块;距离前四号单块距离之和最大的基础单块定义为5号单块;依次排序,第n个单块为与n-1、n-2、n-3、n-4、n-5号单块距离之和最大的基础单块,按上述方法排序,直至最后一个基础单块,定义为m号单块;再对互补单块排序,互补单块起始序号为m+1号,直至最后一个互补单块。利用切分软件将已排序的每个单块进行切片分层,获得形状为正方形,每层高度Δh为1mm的单块切片,生成多层切片信息;将生成的多层块信息、单块信息和多层切片信息传输到金属增材制造设备中,规划零件切片扫描轨迹:在零件单层切片的轮廓线处随机选取一点作为起始点,以该点切线为基准,在零件单层切片轮廓范围内形成平行线系,每条平行线为单层切片增材制造成形熔池扫描运动轨迹中轴线,相邻平行线首尾相连形成单层切片成形熔池扫描运动轨迹,相邻平行线间距为光斑或熔池的运行单道间距,记为d,d=3mm,然后,启动激光立体成形设备,按照成形排序从零件的1号层块的1号单块开始,逐单块、逐层块成形,最终获得成形零件;其中,激光功率2000W,光斑直径4mm,光斑运行单道间距2mm,光斑移动速度20mm/min。实施例3以分层块体激光立体成形Φ1000mm不锈钢棒材为例,不锈钢棒材高700mm,具体实施方法如下:根据零件的结构设计出零件三维模型,确定零件模型成形生长方向,即选择底面作为与基材贴合面,以高度方向为构件成形生长方向,利用切分软件将将不锈钢棒模型在成形生长方向上切分层块,每层厚度h为100mm,模型被切分为7块层块。最下层层块为1号层块,次层为2号层块,顶层层块为7号层块,并生成多层块信息;将每层块切分为上下表面为正方形的带有坡度或斜角的基础单块,基础单块上表面边长为60mm,下表面边长为100mm,其余间隙部分为上大下小的互补单块,并对基础单块和互补单块排序,其中,对基础单块排序:随机选取任意基础单块,定义为1号单块,然后以1号单块为基准,距离1号单块最远的基础单块定义为2号单块;在剩余基础单块中与1号单块、2号单块距离之和最大的基础单块定义为3号单块;距离前三号单块距离之和最大的基础单块定义为4号单块;距离前四号单块距离之和最大的基础单块定义为5号单块;依次排序,第n个单块为与n-1、n-2、n-3、n-4、n-5号单块距离之和最大的基础单块,按上述方法排序,直至最后一个基础单块,定义为m号单块;再对互补单块排序,互补单块起始序号为m+1号,直至最后一个互补单块。利用切分软件将已排序的每个单块进行切片分层,获得形状为正方形每层高度Δh为3mm的单块切片,每个单块被切分成50层,生成多层切片信息,将生成的多层块信息、单块信息和多层切片信息传输到金属增材制造设备中,规划零件切片扫描轨迹:在零件单层切片的轮廓线处随机选取一点作为起始点,以该点切线为基准,在零件单层切片轮廓范围内形成平行线系,每条平行线为单层切片增材制造成形熔池扫描运动轨迹中轴线,相邻平行线首尾相连形成单层切片成形熔池扫描运动轨迹,相邻平行线间距为光斑或熔池的运行单道间距,记为d,d=4mm,然后,启动激光立体成形设备,按照成形排序从零件的1号层块的1号单块开始,逐单块、逐层块成形,最终获得成形零件;其中,激光功率8000W,光斑直径8mm,光斑运行单道间距4mm,光斑移动速度30mm/min。上述实施例1、2、3中也可以使用氩弧焊立体成形设备或电子束立体成形设备成形。以上内容是结合具体/优选的实施方式对本发明作出的进一步详细说明,不能认定本发明的具体实施只局限于这些。对于本发明所属技术领域的普通技术人员来说,在不脱离本发明构思的前提下,其还可以对这些已描述的实施方式做出若干替代或变型,而这些替代或变型方式都应当视为属于本发明的保护范围。