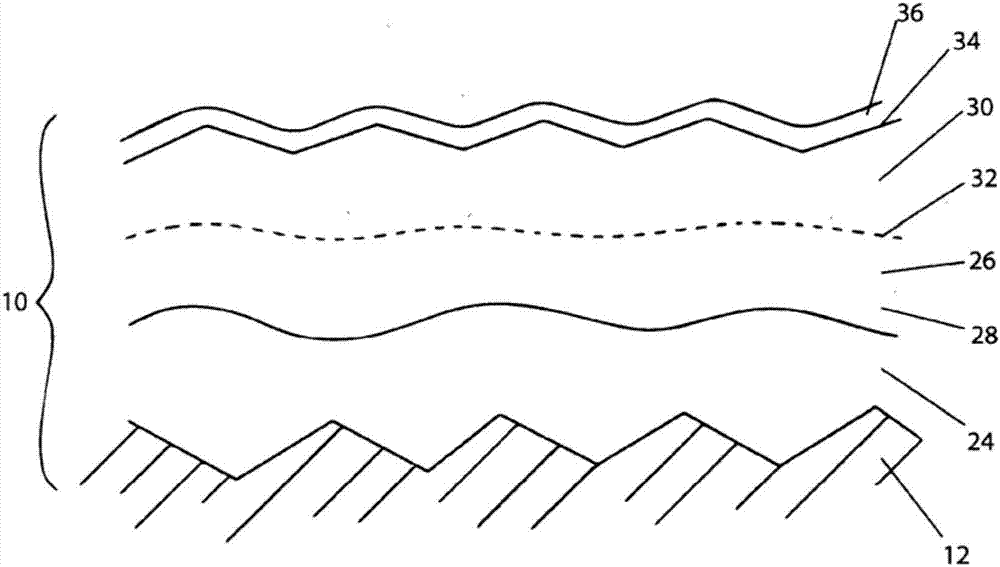
本发明涉及一种涂覆钢板的方法和一种用于钢板的涂层,以及具体涉及但不限于对航空母舰上使用的承重钢板表面进行涂覆的方法。
背景技术:
:诸如航空母舰等轮船通常由钢制成,包括作为飞机起飞和着陆跑道的最高甲板表面。通常通过施加一层有机涂料,对这些甲板表面进行保护。然而,该涂料不能承受使用喷气发动机的飞机起飞和着陆期间产生的气体洗涤,使用喷气发动机有利于垂直起飞或降落或者短距起飞和垂直降落(stovl)。这种气体洗涤能够导致表面温度从环境温度至2000摄氏度的变化,在每次演习中会引起小块油漆被烧掉。因此这种损坏会使甲板表面易受腐蚀。需要这样的表面涂层,其能够应对包括从环境温度开始在-50摄氏度至+50摄氏度范围内的温度快速变化。涂层必须提供允许安全地在上面行走的不滑或防滑表面,其必须足够坚固以承受在起飞和着陆期间施加至涂层的力,并且在损坏时易于修理。技术实现要素:本发明的优选实施方式试图克服现有技术的上述缺陷。根据本发明的一方面,提供一种涂覆钢板的方法,其包括如下步骤:处理待涂覆的钢板表面;对所述钢板施加第一金属沉积涂层,所述第一涂层包括铝;对所述第一涂层施加第二金属沉积涂层,所述第二涂层包括铝和至少一种第一掺杂材料;以及对所述第二金属沉积涂层施加屏蔽涂层。通过对钢板施加铝的第一涂层、铝加一种掺杂材料的第二涂层和屏蔽涂层,能够提供一系列的优点。板材被保护以防止腐蚀,并且提供对于在上行走安全的不滑或防滑表面,以及提供适当的耐摩擦表面以运行飞机。该表面能够被涂色,并且还足以抵抗温度的快速变化,来自垂直起飞飞机的气体洗涤不会损害表面或钢材。该表面还提供足够摩擦阻力,以允许其他飞机的起飞着陆。在优选实施方式中,通过喷砂处理所述钢板的表面。通过对钢材表面的喷砂处理,生成大致无氧化物且适当粗糙的表面,其确保钢板材料与第一涂层的铝的牢固结合。在另一优选实施方式中,喷砂处理使用包括棕刚玉的砂,其具有适当棱角并且坚固,以提供用以优化第一涂层的铝的粘附性的所需轮廓。在优选实施方式中,第一涂层还包括至少一个第二掺杂材料,其增强第一涂层的耐腐蚀性和/或便于修理。在另一优选实施方式中,第二掺杂材料包括锌、钼、镓、锡和铟中的至少一种。额外的掺杂物延长了海事环境中第一涂层牺牲特性的寿命,并提高了第一涂层修复机制的通用性。在另一优选实施方式中,第一金属沉积涂层施加为75微米至200微米之间的厚度。第二金属沉积涂层能够以包括第一阶段和第二阶段的多个阶段施加,并且其中,在涂层施加中使用的颗粒加速器操作为使在第一阶段中加速颗粒比第二阶段中更快。第二金属沉积涂层还能够以包括第一阶段和第二阶段的多个阶段施加,并且其中,在涂层施加中使用的颗粒加速器操作为使在第一阶段生成的表面具有比在第二阶段生成的表面粗糙度更小的表面粗糙度。通过在多个阶段施加第二金属沉积涂层并且在第二阶段颗粒较低的加速,从而导致生成的表面的更大的粗糙度,提供了这样的优点,第一金属沉积涂层与第二金属沉积涂层之间的结合很牢固(由于第一阶段中对碰撞增大的颗粒速度),但第二金属沉积涂层的最上层表面足够粗糙(由于第二阶段中对碰撞降低的颗粒速度),以有助于提供不滑或防滑表面。在另一优选实施方式中,第二金属沉积涂层施加为150微米至300微米的厚度。在一种优选实施方式中,屏蔽涂层包括无机耐热涂层材料。通过对屏蔽涂层使用无机耐热涂层材料,提供这样的优点,屏蔽涂层有助于保护第一和第二金属沉积涂层,并且由喷射的气体洗涤产生的高温不会损坏屏蔽涂层。结果,本发明的涂层能够被认为膨胀型(intumescent)。在另一优选实施方式中,屏蔽涂层包括硅酸钾涂层材料。硅酸钾涂层提供上述优点并且能够以方便的厚度施加。在另一优选实施方式中,屏蔽涂层施加至5微米至25微米之间的厚度。通过提供上述厚度的屏蔽涂层,提供如下优点,屏蔽涂层跟随并且大致重制第二金属沉积涂层的轮廓因此有助于生成不滑表面。在优选实施方式中,使用下述金属沉积技术中的至少一种施加所述第一和第二金属沉积涂层中的至少一个:电弧喷涂、线材喷涂、双丝电弧喷涂、大气等离子喷涂和冷喷涂。根据本发明的另一方面,提供一种用于钢板的涂层,该涂层包括:第一金属沉积涂层,其包括铝,并施加至钢板的处理的表面;第二金属沉积涂层,其包括铝和至少一种第一掺杂材料,并施加至所述第一金属沉积涂层;屏蔽涂层,其施加至所述第二金属沉积涂层。第一涂层还可包括至少一种第二掺杂材料。第二掺杂材料可包括锌、钼、镓、锡和铟中的至少一种。在一种优选实施方式中,第一金属沉积涂层具有75微米至200微米之间的厚度。第一掺杂材料可包括下述中的至少一种:钛、铬、锰、硼、氧化铝、氧化钛、氧化铬、氧化锰、氧化硼、氮化硼、碳化硼和碳化钨。在一种优选实施方式中,第二金属沉积涂层以多个阶段施加,该多个阶段包括第一阶段和第二阶段,并且其中,在所述第一阶段生成的表面比在所述第二阶段生成的表面粗糙度具有更小的表面粗糙度。在另一优选实施方式中,第二金属沉积涂层施加至150微米至300微米之间的厚度。在一种优选实施方式中,屏蔽涂层包括无机耐热涂层材料。在另一种优选实施方式中,屏蔽涂层包括硅酸钾涂层材料。在另一优选实施方式中,屏蔽涂层施加至5微米至25微米之间的厚度。根据本发明的另一方面,提供一种板状材料,其包括:钢板材料;以及如上述列出的施加至所述钢板材料的涂层。在一种优选实施方式中,钢材包括硬化钢。在另一种优选实施方式中,钢材包括碳锰钢。根据本发明的另一方面,提供包括如上列出的至少一种板材的一种物品。在一种优选实施方式中,板材形成承重表面。在另一优选实施方式中,物品为直升机着陆平台、潜艇、石油钻机、化学加工厂、能源生产厂、集装箱和弹药箱中的任意一个。根据本发明的另一方面,提供一种对钢板施加涂层的装置,该装置包括:框架,用于支撑多个金属沉积涂层施加器;施加器移动装置,用于相对于所述框架移动所述施加器;至少一个施加器,用于对钢板施加至少一个第一金属沉积涂层和至少一个第二金属沉积涂层;以及至少一个处理器,用于控制所述施加器和所述施加器移动装置。通过设置上述装置,提供如下优点,可适当并均匀地涂覆板材的较大表面例如航空母舰的甲板,以生成具有一致标准的表面。在一种优选实施方式中,施加器使用电弧喷涂、线材喷涂、双丝电弧喷涂、空气等离子喷涂和冷喷涂中的至少一种金属沉积技术。该装置可包括多个施加器,用于对钢板施加至少一个第一金属沉积涂层和至少一个第二金属沉积涂层。附图说明现在参照下述附图,对仅作为实施例且不构成任何限制的本发明的优选实施方式进行描述,其中:图1是示出本发明方法的流程图;图2是本发明板材和涂层的示意性截面演示;图3是本发明中使用的板材处理表面(preparedsurfaceofsheetmaterial)的显微照片图像;图4是本发明中使用的板材处理表面的横截面的显微照片;图5是不适合在本发明中使用的板材处理表面的横截面的显微照片;图6是示出本发明方法的流程图;图7是应用本发明涂层的装置的轴测图;以及图8是图7的装置的另一轴测图。具体实施方式参照图1和图2,以图1和图6中列出的系列步骤,进行在钢板12上施加涂层10的方法,图1代表图6中示出的更完整过程的简化版本。在过程的开始,处理钢板材料12用于接收涂层10,涂层10将施加在其至少一个表面上。钢板的厚度取决于其应用的用途,因此不受本发明的约束或限制。此外,词语“板”是指单个钢板或结合在一起的多个钢板,钢板形成平坦或大致平坦的表面并不是本发明的限制。涂层的目的是对钢材生成保护性的不滑或防滑表面。该钢材用于承载例如人、车辆或飞机等重量的任意适当的承重场合。表面处理(在图1和图6中以14示出)的主要功能是暴露钢材的大致无氧化物表面并产生足够的表面粗糙度,以确保钢材12与涂层10之间的牢固结合。该表面处理技术的一个实例是喷砂处理(以16示出),其中,优选为棕刚玉的砂在大于80磅/平方英寸(psi)压力下的压缩气流中加速,并且在板状钢处以45度至90度之间的角度被引导至处理表面。在步骤18处进行检验,并且在步骤20处确定通过或未通过。检验步骤可包括检查处理表面的显微照片,并且图3中示出100倍放大率的可接受的表面显微照片,其中示出的尖锐边缘提供指示这样的表面,该表面会与施加至其的涂层产生良好结合。图4和图5也是显微照片(100倍放大率),示出喷砂表面的截面。图4示出可接受的喷砂表面实例,并且图5示出由于不具有足够的粗糙度而不能接受的表面实例。下述表格列出用于喷砂表面的优选主要粗糙度参数,使用粗糙度测量技术测量的粗糙度对该领域技术人员为熟知的。参数说明可接受的范围(微米)ra绝对值的平均数并且描述平均粗糙度≥4(通常为4-5.5)rp最大峰高≥15rku峰的平均锐度≥3rsm轮廓峰元的平均宽度≤500rt在样品长度中最大峰-谷高度30-60在步骤16的喷砂之前,可应用其他的表面处理技术。这些技术包括除油污和除漆,并且后者可使用喷砂进行,但使用另一种砂诸如微粒或粒料。也可以使用氯化物指示剂类型或该领域技术人员熟悉的相似技术对该表面进行油脂和存在的氯化物的检测。接着步骤14中的表面处理,在步骤22中进行金属沉积。通过将两种不同成分的金属连续沉积在钢材12上,以两个不同涂层进行该金属沉积。在步骤25中应用第一金属沉积涂层24,并且其至少包括铝。第一金属沉积涂层24可包括掺杂成分,包括但不限于诸如锌、钼、镓、锡和铟等金属。第一金属沉积涂层24可通过电弧喷涂施加,但也可以接受其他的金属沉积/喷涂处理,包括但不限于线材喷涂、双丝电弧喷涂、大气等离子喷涂和冷喷涂。第一金属沉积涂层通常具有75微米至200微米之间的厚度。第一金属沉积涂层优选在同一表面上经旁通喷枪数次施加为系列层。在施加第一金属沉积涂层24之后,在第一涂层24的上面施加第二金属沉积涂层26(步骤27)。第二金属沉积涂层包括铝和至少一种其他掺杂成分,包括但不限于诸如钛、铬、锰、硼、氧化铝、氧化钛、氧化铬、氧化锰、氧化硼、氮化硼、碳化硼和碳化钨等金属。使用与用于施加第一金属沉积涂层24的任意相同的技术施加第二金属沉积涂层26。第二金属沉积涂层通常具有150微米至300微米之间的厚度,并且分两个阶段施加。这两个阶段优选使用相同的金属组合,但能够通过当进行喷涂时来自喷枪金属颗粒加速的不同进行区分。在该施加的第一阶段,生成第二涂层26的第一阶段28,来自喷枪的喷涂颗粒以与生成第二涂层26的第二阶段30更快的速率被加速。在第一阶段,快速运动的颗粒增加的动量使得第二涂层26与第一涂层24之间牢固的粘附以及高密度。然而,在第二涂层的第一阶段结束时所产生的临时表面(以32表示)不具有用以提供良好的不滑或防滑表面的足够粗糙度。通过放慢并降低第二阶段中颗粒的动量(通过大约一半地降低喷枪中加速气体的压力),生成更加粗糙的表面(以34表示)。一旦施加了第一和第二金属沉积涂层并且在步骤29进行检验,则在步骤31确定通过或未通过。检验可包括视觉检验、表面粗糙度测量和弯曲试验(取没有形成被保护主要表面的部分的钢材样品,并使用预定力以预定直径弯曲,以确保金属沉积涂层与钢材之间的良好粘附)。通过施加屏蔽涂层36(步骤33)完成涂层10。屏蔽涂层是诸如硅酸钾密封剂等无机耐热材料。密封剂作为防止铝氧化的屏障,并且施加在5微米至25微米厚度之间的层中,该层比第一金属沉积涂层和第二金属沉积涂层更薄。该厚度足够小,使第二金属沉积涂层26的上表面34的粗糙度得以保持,从而提供良好的不滑表面。屏蔽涂层能够通过刷子、辊筒、喷枪(hvlp,高速低压)或用于较小面积的浸渍进行施加。屏蔽涂层36能够包括颜料,以提供所需的基底涂层颜色。一旦施加屏蔽涂层,在步骤35进行最后的检验步骤,并且在步骤37确定通过或未通过。如果需要,可以在屏蔽涂层的表面施加包含其他颜料以产生其他颜色的另一种屏蔽涂层,以给出标识线或其他所需的分界线。能够手动操作上述类型的喷枪,以施加金属沉积涂层。然而,当对很大的表面区域进行作业时,优选使用图7和图8示出类型的机器人装置。该装置包括框架50,其设置在板材料12上,并且经轮子52可移动。喷枪54形式的施加器设置为以连续施加的方式施加第一金属沉积涂层和第二金属沉积涂层。然而,施加器能够可选地包括两个或更多个喷枪,以施加不同的金属沉积涂层,并且最优选地包括三个喷枪。第一喷枪施加第一金属沉积涂层,第二喷枪施加第二金属沉积涂层的第一阶段,以及第三喷枪施加第二金属沉积涂层的第二阶段。使用机器臂56形式的是施加器移动装置,使施加器相对于框架50移动。对该领域技术人员明显地是,可使用其他施加器移动装置诸如平板扫描仪等,以控制施加器相对于框架的移动。由处理器(未示出)控制机器臂56的移动和喷枪54的使用。处理器能够使涂层平均施加,并且通过控制臂的移动速度和/或金属涂层的沉积速率,能够确保小块涂层10(参见图8)的边缘被羽化(feathered)】,从而使一块块涂层10能够单独形成并且连续涂层可施加于板状钢材12的整个表面。该板材适于使用在任意下述应用中,仅以实例给出并不作为限定性清单,直升机着陆平台、潜艇、石油钻机、化学加工厂、能源生产厂、集装箱和弹药箱等。一般是这样的情况,在施加涂层时已经建好应用,在该应用中将涂层施加至钢板。例如,如果将涂层施加至航空母舰的甲板,在轮船建好之后便施加涂层。该领域技术人员可以理解,仅以实例而不构成任意限制的描述了上述实施方式,并且在不偏离由所附权利要求限定的保护范围的情况下进行各种变化和变形。当前第1页12