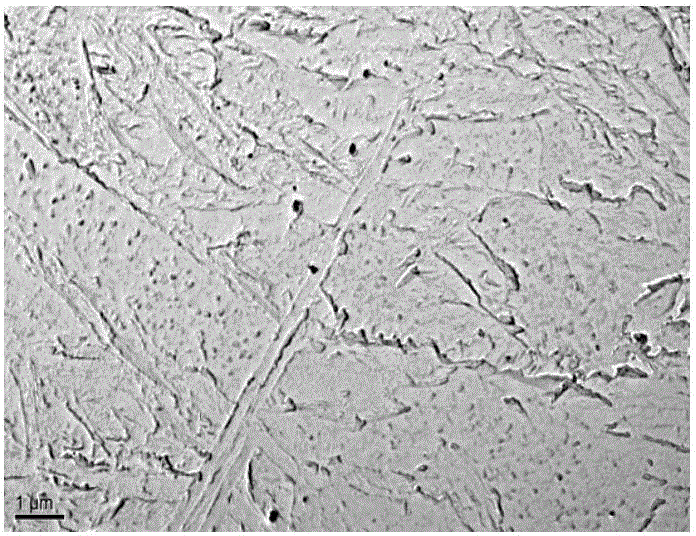
本发明涉及高韧钢板领域,特别提供了一种低成本可大线能量焊接高强高韧钢板的制造方法。
背景技术:
:随着我国的经济发展,需要大量的低温钢板制造液化石油液氨、液氧、液氮等生产储存容器以及在寒冷地区服役的船舶。在低温环境下,材料的韧性急剧降低,极易发生脆性断裂事故,因此对于低温服役环境下用材料的低温韧性和安全性提出了更高的要求,以保证储罐和船舶在使用过程中的可靠性和安全性。并且,随着储罐结构、船舶和工程结构的大型化,钢板尺寸规格的不断增加,焊接占制造成本的比重越来越大,要求这类钢板能够采用大线能量焊接的方法进行焊接,从而降低制造成本。改善钢板的低温韧性的方法很多,其中之一是添加一定含量的Ni元素。Ni为非碳化物形成元素,可以扩大奥氏体相区,在不降低强度的情况下能够提高材料的低温韧性。例如,瑞典专利SE442642“低合金高强度焊接钢”,其主要化学成分为0.07~0.11%C、0.5~0.9%Ni,还必须有Cr、Cu、Mo、V、Ti等合计元素,该钢板能够在-50℃的海水腐蚀环境下使用。又如,日本专利“一种低温高强度钢板的生产方法”,通过对含1.0-4.0%Ni、0.005-0.05%C的低合金钢进行轧制、快速冷却、回火热处理,获得优异的-40℃的低温韧性。然而,Ni是非常昂贵的元素,Ni的添加使材料的成本大幅度的上升;另一方面Ni会使碳当量增加,降低焊接性。而且大幅度添加Ni,在连铸坯和钢板表面产生粘着的氧化皮,如采取的措施不得力,轧制过程中钢板表面将产生氧化皮缺陷,需要考虑钢板表面修正工序的问题。在C、Mn为基础,同时在钢中添加少量的Nb、V和Ti等微合金元素,并利用控制轧制和控制冷却工艺(TMCP+ACC),同样可以提高钢板的低温韧性。采用此方法,专利CN103667915“一种具有良好低温韧性的热机械控制钢板及其制造方法”,其主要化学成分为0.01~0.08%Mo,0.01~0.02%Ti,0.02~0.04%Nb,0.03~0.07%V,其控制轧制工艺要点:再加热温度为1100~1180℃,精轧温度为830~900℃,终轧温度790~859℃,采用轧后水冷,生产了一种满足-40℃冲击功大于200J使用要求的优异低温韧性钢板;新日铁住金株式会社申请的专利CN103328669A“变形性能和低温韧性优良的高强度钢板、高强度钢管及它们的制造方法”中钢板的主要成分为0.01~0.05Nb%,0.005~0.030%Ti,制备了一种由铁素体和马氏体/贝氏体的复相组织,与钢板轧制方向成45°的兰克福特值和板宽度方向的兰克福特值大于1.0的钢板。但Nb、V和Ti合金元素的添加将导致碳当量的增加,在大线能量焊接条件下(焊接热输入≥50kJ/cm)形成粗大的晶界铁素体和粒状贝氏体组织,热影响区的低温韧性降低;另一方面,合金元素的添加导致制造成本增加。钢板经过特殊的热处理工艺,可以提高钢板的低温韧性。例如,舞阳钢铁有限公司申请的CN101876033“一种低温高韧性船板钢及其生产方法”,其主要化学成分为0.2~0.4%Ni,0.04~0.15%Cr,0.015~0.03%Nb,0.002~0.015%Ti,钢板经控制轧制后,采用920~940℃淬水,并进行900~920℃正火处理,其生产的钢板屈服强度≥350MPa,抗拉强度≥480MPa,-60℃冲击功≥250J。又如,南京钢铁股份有限公司申请的专利CN101643887A“一种特厚高等级船板钢及其生产工艺”,其钢板的化学成分为0.03~0.3%Ni,0.03~0.2%Cr,0.01~0.04%Nb,0.003~0.06%V,所用的正火温度为880~940℃。由于添加了Ni、Cr、Nb、V等合金元素导致碳当量增加,这类钢的只能采用小线能量(焊接热输入<50kJ/cm)进行焊接,并且制造成本较大。对于钢板改善钢板大线能量焊接后低温韧性的方法主要为第二相粒子阻碍奥氏体晶粒长大和晶内铁素体形核。例如,宝钢申请的专利“可大线能量焊接的超高强度厚板”(CN1676656A)和“可超大线能量焊接低温用厚钢板及其制造方法”(CN101045976)、杰富意钢铁株式会申请的专利“大线能量焊接埋弧焊焊接接头、该接头的制造方法及所用的焊丝和焊剂”(CN1616183),均是利用Mg、Ti、Ca的氧化物达到改善焊接热影响区低温韧性,该专利的不足之处还在于Mg、Ti和Ca的氧化物在液态析出时,析出氧化物粒子生长不受限制,形成的大颗粒夹杂物不仅起不到抑制焊接热影响区晶粒长大的作用,反而会使母材和热影响区韧性下降。因此,这种方法在工业生产中很难控制。综上所述,相关专利所涉及的提高钢板低温韧性、大线能量焊接热影响区低温韧性的技术均有各自的缺陷,为了解决上述缺陷,本发明提出一种低成本可大线能量焊接高强高韧钢的制备方法,控制N/Al比,发挥Al的作用,大大改善了钢的韧性,降低成本。技术实现要素:本发明的目的在于提供了一种低成本可大线能量焊接高强高韧性钢板及其制造方法,通过控制钢板中N/Al的含量,满足低温条件下大线能量焊接的要求。本发明的技术方案是:一种低成本可大线能量焊接高强高韧性钢板及其制造方法,包括以下步骤:将连铸坯加热到950~1100℃;第一阶段轧制累积变形量≥60%,轧制速度<1m/s,终轧温度≥900℃;二阶段轧制变形温度≤830℃,道次间隔时间≤10s,累积变形量≥30%;三阶段开轧温度为Ar3+20℃,终轧温度为Ar3-40℃,其中Ar3=910-273C-74Mn-56Ni-16Cr-9Mo-5Cu;钢板的冷却速度为5~15℃/s。本发明控制连铸坯的加热温度在950℃~1100℃的主要原因是:当再加热温度≤1100℃时,钢中的析出粒子未发生溶解,其能够钉扎连铸坯的奥氏体晶粒尺寸;当再加热温度>1100℃时,钢中的析出粒子发生大量的溶解,连铸坯的奥氏体晶粒尺寸发生迅速长大,因此连铸坯的再加热温度的上限为1100℃。此外,如果加热温度低于950℃时,钢板的变形抗力较大,不能进行完全的动态再结晶过程,奥氏体晶粒不能细化;同时连铸坯轧制阶段时间较短不利于精确的控制轧制工艺、钢板的除磷和矫直工艺等。可见,连铸坯的再加热温度应控制在950℃-1100℃。本发明控制连铸坯在第一阶段奥氏体动态再结晶区进行累积变形量变形≥60%,以获得均匀细小的奥氏体晶粒。主要原因是:随着连铸坯的再加热温度的降低,奥氏体再结晶区的温度区间减小,在高轧制速度、约70%的临界变形量的条件下奥氏体才能发生完全的动态再结晶,这实际轧制过程中不能实现,然而当采用低速轧制时发生完全动态再结晶所要求的变形量显著降低,因此本发明控制轧制速度<1m/s、累积变形量≥60%,终轧温度≥900℃。本发明控制连铸坯在第二阶段轧制变形温度≤830℃,道次间隔时间≤10s,累积变形量≥30%。主要原因如下:首先,由于钢板合金元素含量较低,因此容易发生完全的静态再结晶、道次间隔时间短,因此控制第二阶段变形温度设计≤830℃,道次间隔时间≤10s。本发明控制连铸坯在第三阶段轧制时变形温度为Ar3+20℃,终轧温度为Ar3-40℃,主要原因如下:首先,第三阶段轧制在Ar3+20℃变形时能够发生形变诱导铁素体相变,细化铁素体晶粒尺寸;终轧温度为Ar3-40℃时,能够在铁素体中形成大量的位错和亚晶界,强化铁素体相;未相变的奥氏体中形成大量的变形带。进一步的,钢板的组织特征为铁素体和珠光体,其中带有亚晶结构的铁素体含量5%~10%,小角度晶界含量≤5%,-80℃冲击功≥200J,所述小角度晶界为2°~15°。通过以上的工艺生产的钢板的组织特征为铁素体和珠光体,其中带有亚晶结构的铁素体含量5%~10%,小角度晶界(2°~15°)含量≤5%,-80℃冲击功≥200J;主要原因如下:亚晶界将一个先共析铁素体晶粒细化为多个晶粒取向差角≥2°的亚晶粒,可以有效提高细晶强化对屈服强度的贡献。同时,利用相变后的形成的细小等轴铁素体组织提高材料的低温韧性。当带有亚晶粒的铁素体和等轴细小的铁素体保持一定比例时,钢板既能够保证一定的强度,同时具有良好的低温韧性。进一步的,钢板中的Al≥0.04%,N/Al<0.1,焊接热影响区中M-A组元含量≤2.5%,在50~100kJ/cm的热输入下热影响区的-60℃冲击功≥60J。焊接热影响区中M-A组元含量≤2.5%,在50~100kJ/cm的热输入下热影响区的-60℃冲击功≥60J。具体原因如下:M-A组元是一种硬脆相,其往往分布在板条贝氏体和粒状贝氏体基体上,当收到冲击载荷的作用时,M-A组元产生解理裂纹导致热影响区低温韧性降低,因此降低M-A组元含量可以有效的提高低温韧性。进一步的,连铸坯加热时采用Al脱氧,Al脱氧过程在浸渍罩无渣吹氩精炼工位进行,并控制钢板中Al≥0.04%,N/Al<0.1。采用Al脱氧,并限制连铸坯Al≥0.04%,N/Al<0.1,其主要的原因如下:如果当Al<0.04%,N/Al≥0.1时,一方面不利于钢中形成AlN析出粒子,焊接热影响区中的固溶氮含量增加热影响区韧性降低;另一方面,较低的Al含量不能降低富碳区的形成M-A组元的含量增加,热影响区的韧性降低。进一步的,连铸坯以质量百分比计含有:C:0.05%~0.12%、Mn:1.3%~2.0%、Si:0.1%~0.4%、Ti:0.01%~0.05%、N:0.001%~0.006%、Al:0.02%~0.1%,余量:铁及不可避免的杂质。进一步的,第一阶段的终轧温度为912℃,累计变形量为60%;第二阶段的轧制开始温度为823℃,结束温度为768℃,累计变形量为34%。进一步的,钢板的冷却速度为7.6℃/s。本发明的优点和有益效果在于:本发明中钢板的制备工艺简单、钢材成本低廉,可广泛的应用于低温容器储罐、低温船板和高寒地区使用的高强度钢。本发明所生产的钢板可以同时满足360MPa级以上高强度以及F级以上高低温韧性,同时还能适应50~100kJ/cm可大线能量焊接要求;本发明制造成本较低,生产工艺简单,可以适用于20~40mm规格钢板制造要求。附图说明图1-1为对比例1连铸坯加热温度为1250℃时原始奥氏体晶粒形貌图;图1-2为对比例1连铸坯加热温度为1250℃时析出粒子透射观察图;图2-1为本发明中连铸坯在再加热温度为1100℃时原始奥氏体晶粒形貌图;图2-2为本发明中连铸坯在再加热温度为1100℃时析出粒子透射观察图;图3为本发明中连铸坯再加热温度与原始奥氏体晶粒尺寸关系图;图4为钢板终轧制温度与晶粒取向差角≥2°的有效晶粒尺寸、晶粒取向差角≥15°的有效晶粒尺寸的关系图;图5-1为对比例1连铸坯经过820℃终轧时金相组织形貌图;图5-2为对比例1连铸坯经过700℃终轧时晶粒取向差角分布图;图5-3为对比例1连铸坯经过700℃终轧时透射形貌;图6-1为对比例1连铸坯经过700℃终轧时金相组织形貌图;图6-2为对比例1连铸坯经过700℃终轧时晶粒取向差角分布图;图6-3为对比例1连铸坯经过700℃终轧时透射形貌;图7-1为本发明采用三阶段轧制情况下带有亚结构的铁素体金相组织形貌图;图7-2为本发明采用三阶段轧制情况下带有亚结构的铁素体晶粒取向差角分布图;图7-3为本发明采用三阶段轧制情况下带有亚结构的铁素体透射形貌图;图8-1为本发明高韧性钢板焊接热影响区显微组织图;图8-2为本发明高韧性钢板焊接热影响区M-A组元着色腐蚀示意图。图中,1-等轴铁素体,2-亚晶界,3-位错。具体实施方式下面结合附图来具体描述本发明的优选实施例,其中,附图构成本申请一部分,并与本发明的实施例一起用于阐释本发明的原理。本发明所述的高强度钢板实施例1~3和对比例钢板1~5的组成成分列于表1,这些实施例与对比例钢板采用130吨的转炉冶炼,实施例在浸渍罩无渣吹氩精炼工位进行Al脱氧,并控制Al≥0.04%,N/Al<0.1。经连铸及轧制工艺流程,制备成板厚为20mm~40mm的钢板,其具体的连铸坯再加热温度、轧制工艺参数列于表2。表1钢的化学成分Wt.%CMnSiTiNAlVNbAr3实施例10.081.50.20.0100.00240.045--777实施例20.091.50.30.0200.00400.087--774实施例30.081.50.30.0200.00400065--777对比例10.11.50.20.0100.00400.05--771对比例20.081.30.20.0120.00300.045--792对比例30.081.30.20.0130.00350.05--792对比例40.091.20.20.0140.00450.03--797对比例50.081.20.20.0120.00400.03-0.015799表2实施例钢板制备工艺从表1~2可以看出,实施例钢板的化学成分和制备工艺满足要求,对比例1~3生产的钢板化学成分满足要求,但制备工艺不满足要求,对比例4和5的化学成分和工艺均不满足要求。对实施例钢板和对比例钢板进行取样,按照GB/T13239-2006标准,采用MTSNEW810拉伸试验机,以3mm/min恒定的夹头移动速率进行拉伸,测试纵向拉伸性能,取样位置为钢板1/2处,试验结果取两个试样的平均值。按照GB/T229-2007标准,采用NCS系列500J仪器化摆锤式冲击试验机,测试-80℃时V型缺口冲击功,取样位置为1/2处,试样结果为3个试样的平均值。钢板力学性能见表3。表3钢板力学性能力学性能可见,按照本发明制备的试验钢,钢板的屈服强度达到355MPa以上,和对比例基本相当。实施例钢板-80℃的V型夏比冲击功均在200J以上,均显著高于对比例。将上述钢板分别开展50kJ/cm、75kJ/cm、100kJ/cm的埋弧焊焊接试验。然后根据GB/T229-1994标准,采用NCS系列500J仪器化摆锤式冲击试验机,测试了焊接接头-60℃时V型缺口冲击功,其结果如表4所示。从表4中可以看出,实施例钢板的焊接热影响区的-60℃冲击功均高于60J。从表5的数据中可以看出,实施例1~3的M-A组元含量组元含量均小于2.5%,对比例1~3的M-A含量复合要求但其母材缺口冲击功显著低于实施例1~3,对比例4和5焊接热影响区的M-A含量不符合专利要求。表4焊接热影响区冲击功表5:焊接热影响区M-A组元含量%实施例1实施例2实施例3对比例1对比例2对比例3对比例4对比例5含量2.01.81.72.31.81.93.53.7以上所述,仅为本发明较佳的具体实施方式,但本发明的保护范围并不局限于此,任何熟悉本
技术领域:
的技术人员在本发明揭露的技术范围内,可轻易想到的变化或替换,都应涵盖在本发明的保护范围之内。当前第1页1 2 3