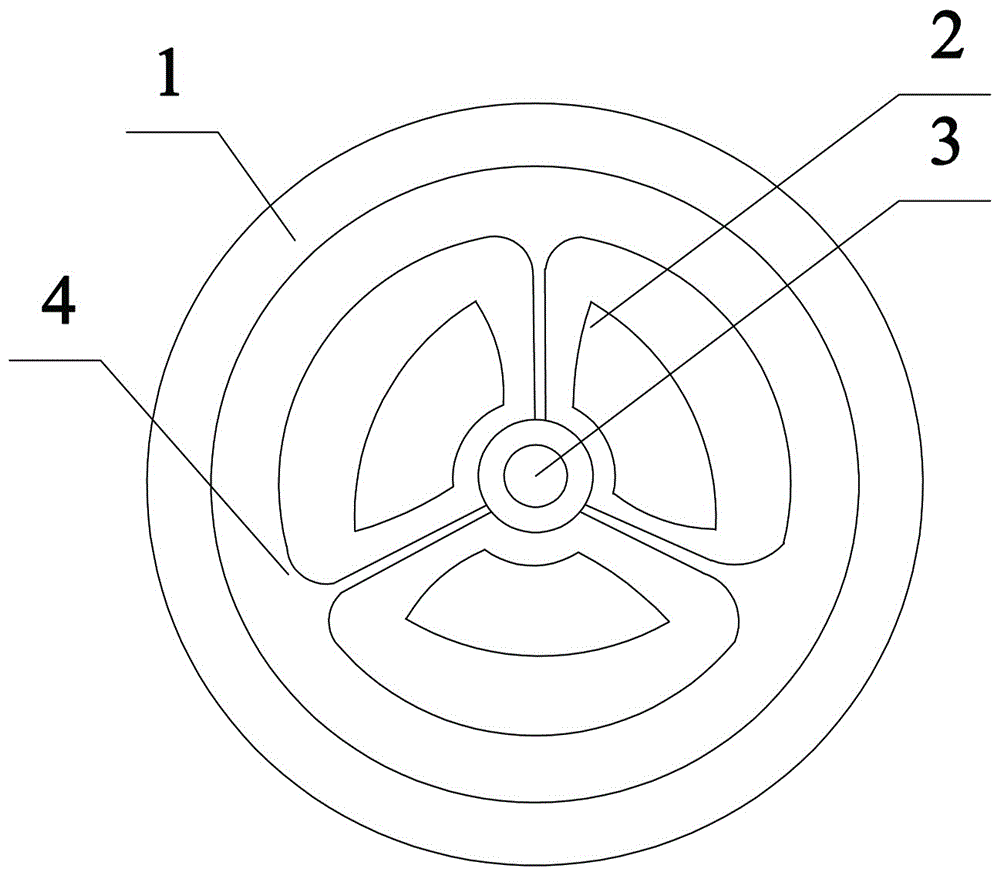
本发明涉及模具
技术领域:
,具体的说,涉及了一种铝管连续挤压模具。
背景技术:
:无缝金属管类产品通常采用挤压工艺来批量生成,而在挤压成型过程中,模具成型部件的形状稳定性及模具成型部件的表面光洁度会对金属管类产品的尺寸和光洁度产生较大影响。现有的成型部件通过因连续高温使用后尺寸或成型部件的表面光洁度降低导致模具要经常进行维修甚至直接报废,从而造成巨大的经济损失。如现有的铝管连续挤压模具,在生产管道外径为7.5mm、管道壁厚为0.7mm的铝管时,通常只能完成将10吨左右的铝液加工成铝管,该铝管连续挤压模具就因尺寸公差达到了报废程度,且在生产过程中每加工1~2吨的铝液,就需要对模具成型部件进行打磨处理。为了延长模具的使用寿命,通常采用热沉积法或电镀法在模具的成型部件表面沉积一层耐磨层,但由于耐磨层与基体两者粘接力不牢固,彼此之间润湿性差导致耐磨层与基体的结合力较弱,耐磨层很难与基体形成紧密结合界面涂层容易脱落;且在模具使用寿命上表面沉积有一般涂层的铝管连续挤压模具也仅仅只比没有涂层的模具多加工20%~30%左右的铝液,模具寿命依然不长。为了解决以上存在的问题,人们一直在寻求一种理想的技术解决方案。技术实现要素:本发明的目的是针对现有技术的不足,从而提供一种具有较强的层间结合力、较好的耐磨耐腐蚀性能及较好热稳定性的铝管连续挤压模具。为了实现上述目的,本发明所采用的技术方案是:一种铝管连续挤压模具,包括凸模、凹模,所述凸模上设置有成型芯棒,所述凹模包括内部开设有倒锥台形凹模成型型腔的凹模基体、设在所述倒锥台形凹模成型型腔中心的成型垫片和贯穿所述凹模基体和所述成型垫片的凹模成型通孔,所述成型芯棒包括硬质合金材质的成型芯棒基体和沉积在所述成型芯棒基体上的耐磨耐腐蚀涂层;所述成型垫片包括与所述成型芯棒基体材质相同的成型垫片基体和沉积在所述成型垫片基体上的所述耐磨耐腐蚀涂层;所述耐磨耐腐蚀涂层为纳米氮化钛层、纳米碳化钛层或纳米碳氮化钛层,所述硬质合金为碳化钛铌钼合金、氮化钛铌钼合金或钨钛类合金,且该钨钛类合金包括下述质量百分数的组分:WC78%~85%、TiC5%~15%、Co6%~10%;所述成型芯棒基体和所述成型垫片基体的表面粗糙度Ra值均为0.01~0.1。基于上述,所述钨钛类合金组分中还包括NbC或TaC,且含有NbC或TaC的钨钛类合金基体中WC的质量百分数为82%~85%、TiC的质量百分数为6%、Co的质量百分数为6%~8%,余量为NbC或TaC。基于上述,所述耐磨耐腐蚀涂层的厚度为5微米~10微米。基于上述,所述成型垫片的厚度为3毫米~8毫米。基于上述,所述凸模包括凸模基体、凸模成型凸台和贯穿所述凸模成型凸台和所述凸模基体的至少两个分流槽,所述凸模基体和所述凸模成型凸台一体设置,所述凸模成型凸台外端面开设有装配盲孔,所述凸模成型凸台与倒锥台形的所述凹模成型型腔配合形成铝液流通通道,所述成型芯棒基体包括安装柄和与所述凹模成型通孔配合的定型内芯,所述安装柄和所述定型内芯一体设置,所述安装柄设置在所述装配盲孔内,所述安装柄与所述装配盲孔过盈配合;具体安装方法采用热装法将所述安装柄装配在所述装配盲孔内。基于上述,所述定型内芯的横截面为圆形、三角形或多边形。基于上述,所述凹模成型通孔的横截面为与所述定型内芯配合的圆形、三角形或多边形。基上所述,所述定型内芯的成型端为长条形的齿状,所述凹模成型通孔的横截面为与所述定型内芯配合的长圆孔。基于上述,所述成型芯棒是通过以下方法制得的:首先选用含有上述质量百分数组分的硬质合金材料进行加工制得成型芯棒胚体,然后对所述成型芯棒胚体进行研磨、抛光处理,使得该成型芯棒胚体的表面粗糙度Ra值为0.04~0.1,得到抛光成型芯棒胚体;并对所述抛光成型芯棒胚体进行脱脂、除油处理得到具有洁净表面的所述成型芯棒基体;然后采用化学沉积法以纳米氮化钛、纳米碳化钛或纳米碳氮化钛为原料,在具有洁净表面的所述成型芯棒基体上沉积厚度为5微米~10微米的耐磨耐腐蚀涂层;最后采用流体抛光方法对耐磨耐腐蚀涂层进行精抛光,使得耐磨耐腐蚀涂层的表面粗糙度Ra值为0.01~0.04,制得所述成型芯棒。基于上述,所述成型垫片是通过以下方法制得的:首先选用含有上述质量百分数组分的硬质合金材料进行加工制得成型垫片胚体,然后对所述成型垫片胚体进行研磨、抛光处理,使得该成型垫片胚体的表面粗糙度Ra值为0.04~0.1,得到抛光成型垫片胚体;并对所述抛光成型垫片胚体进行脱脂、除油处理得到具有洁净表面的所述成型垫片基体;然后采用化学沉积法以纳米氮化钛、纳米碳化钛或纳米碳氮化钛为原料,在具有洁净表面的所述成型垫片基体上沉积厚度为5微米~10微米的所述耐磨耐腐蚀涂层;最后采用流体抛光方法对耐磨耐腐蚀涂层进行精抛光,使得耐磨耐腐蚀涂层的表面粗糙度Ra值为0.01~0.04,制得所述成型垫片。其中,为了在确保制得的所述成型芯棒和所述成型垫片加工尺寸稳定性的同时,提高研磨抛光效率,在对所述成型芯棒胚体和所述成型垫片胚体进行研磨、抛光处理时,首先选用目数为100目~500目的研磨设备对所述成型芯棒胚体和所述成型垫片胚体进行粗加工,然后再选用1000目~3000目的研磨设备进行精加工,最终使得该成型芯棒胚体和所述成型垫片胚体的表面粗糙度Ra值为0.04~0.1,对于耐磨耐腐蚀涂层的抛光采用斯漫克磨粒流体抛光机进行,将耐磨耐腐蚀涂层的表面粗糙度Ra值抛光到0.01~0.04。具体地,该耐磨耐腐蚀涂层成型模具装配状态时,倒锥台形的所述凹模成型型腔与所述凸模成型凸台配合形成液体流通通道,所述定型内芯与所述凹模成型通孔配合决定管壁的厚度。熔融态的铝液首先通过所述分流槽进入所述凹模成型型腔中,使得铝液混合均匀,然后在流入所述凹模成型通孔中,并通过所述定型内芯与所述凹模成型通孔之间的装配配合使得薄壁铝管得到定型,从而制得一定壁厚和一定管径的薄壁铝管。本发明选用碳化钛铌钼合金、氮化钛铌钼合金或钨钛类合金材料作为铝管连续挤压模具中的由成型垫片和成型垫片组成的成型部件的原材料,利用该类硬质合金自身具有的高耐腐蚀性、较高的高温尺寸稳定性和较好的红硬性,确保了铝管连续挤压模具的成型部件的尺寸稳定性和具有较好的高温耐腐蚀性,同时该类硬质合金材料具有较小的晶粒粒度,使得该铝管连续挤压模具的成型部件经研磨、抛光处理能够获得具有较低表面粗糙度的表面。进一步的,本发明在所述成型芯棒基体和所述成型垫片基体表面均沉积一层纳米氮化钛层、纳米碳化钛层或纳米碳氮化钛层,利用共同存在于该耐磨耐腐蚀涂层、所述成型芯棒基体和所述成型垫片基体中的钛元素所起到的同种元素扩散效应,提升了所述耐磨耐腐蚀涂层与所述成型芯棒基体和所述成型垫片基体之间的结合力,使得耐磨耐腐蚀涂层与上述两种基体之间形成紧密结合的界面涂层不易脱落。更重要的是,该耐磨耐腐蚀涂层是以纳米级的氮化钛、碳化钛或纳米碳氮化钛为原料,利用纳米颗粒的纳米效应,使制得的所述耐磨耐腐蚀涂层具有较高的光泽度和较低的摩擦系数,从而大幅降低了铝管连续挤压模具的成型部件与铝液之间的摩擦力,使得在铝管生产过程中铝液不易粘连和堆积在铝管连续挤压模具的成型部件,确保了制得的铝管表面光滑无划痕。更进一步的,所述耐磨耐腐蚀涂层以纳米氮化钛、纳米碳化钛或纳米碳氮化钛为原料,使得制得耐磨耐腐蚀涂层硬度比所述成型芯棒基体和所述成型垫片基体的硬度高,同时由于该耐磨耐腐蚀涂层具有高的抗氧化性、较好的抗粘结性、较高的耐磨性及较好的抗月牙洼磨损,从而显著提高了该铝管连续挤压模具中成型部件的尺寸稳定性、高温耐腐蚀性、高温耐磨性,从而显著提高了该铝管连续挤压模具的使用寿命。例如利用该铝管连续挤压模具在生产管道外径为7.5mm、管道壁厚为0.7mm的薄壁铝管时,可以连续加工40吨左右的铝液,所制得的薄壁铝管尺寸合格率达99%以上。附图说明图1是本发明实施例1提供的铝管挤压成型模具凸模外侧结构示意图。图2是本发明实施例1提供的铝管挤压成型模具凸模内侧结构示意图。图3和图4是本发明实施例1提供的铝管挤压成型模具的成型芯棒结构示意图。图5是本发明实施例1提供的铝管挤压成型模具凹模内侧结构示意图。图6是本发明实施例1提供的铝管挤压成型模具凹模外侧结构示意图。图7是本发明实施例1提供的铝管挤压成型模具凹模立体剖面结构示意图。图8是本发明实施例1提供的铝管挤压成型模具成型垫片结构示意图。图9是本发明实施例5提供的铝管挤压成型模具凸模内侧的结构示意图。图10是本发明实施例5提供的铝管挤压成型模具凹模内侧结构示意图。图中:1、凸模基体;2、分流槽;3、成型芯棒;31、定型内芯;32、安装柄;34、成型芯棒基体;35、耐磨耐腐蚀涂层;4、凸模成型凸台;5、凹模基体;6、凹模成型通孔;7、凹模成型型腔;8、成型垫片;9、成型垫片安装凹槽;81、成型垫片基体。具体实施方式下面通过具体实施方式,对本发明的技术方案做进一步的详细描述。实施例1本实施例提供一种铝管挤压成型模具,它具体包括凸模、凹模和设置在凸模上的成型芯棒3。如图1和图2所示,所述凸模包括圆柱形凸模基体1、凸模成型凸台4和三个贯穿所述凸模成型凸台4和所述凸模基体1的分流槽2。其中圆柱形的所述凸模基体1和所述凸模成型凸台4一体设置,所述凸模成型凸台4的外端面中心部位开设有装配盲孔。如图3和图4所示,所述成型芯棒3包括成型芯棒基体34和沉积在所述成型芯棒基体34表面的耐磨耐腐蚀涂层35。其中,所述耐磨耐腐蚀涂层35为纳米氮化钛涂层,所述纳米氮化钛涂层的厚度为5微米。所述成型芯棒基体34由包括下述质量百分数组分的合金材料加工而成:WC85%、TiC6%、Co6%、NbC3%。由于本方案中的涂层厚度极薄,为了保证涂层表面具有较高的表面光洁度,就要求所述成型芯棒基体34具有较低的表面粗糙度,优选地,所述成型芯棒基体的表面粗糙度Ra值为0.05。按照功能区分,所述成型芯棒基体34具体结构可分为一体设置的横截面为圆形的定型内芯31、安装柄32。所述安装柄32设置在所述装配盲孔内,所述安装柄32与所述装配盲孔过盈配合,具体安装方法采用热装将所述安装柄装配在所述装配盲孔内。其中,本实施例提供的所述成型芯棒3是通过以下方法制得的:首先选用含有上述质量百分数组分的硬质合金材料加工处理制得成型芯棒胚体,然后对所述成型芯棒胚体进行研磨、抛光处理使得该成型芯棒胚体的表面粗糙度Ra值为0.05,得到抛光成型芯棒胚体;并对所述抛光成型芯棒胚体进行脱脂、除油处理得到具有洁净表面的成型芯棒基体;其中,为了在确保制得的成型芯棒基体加工尺寸稳定性的同时提高研磨抛光效率,在对所述成型芯棒胚体进行研磨、抛光处理时,首先选用目数为100~500目的研磨设备对所述成型芯棒胚体进行粗加工,然后再选用1000~3000目的研磨设备对粗加工后的成型芯棒胚体进行精加工,最终使得该成型芯棒胚体的表面粗糙度Ra值为0.05;然后采用化学沉积法以纳米氮化钛为原料,在具有洁净表面的所述成型芯棒基体外表面沉积厚度为5微米的耐磨耐腐蚀涂层,最后采用流体抛光方法对耐磨耐腐蚀涂层进行精抛光,使得耐磨耐腐蚀涂层的表面粗糙度Ra值为0.03,制得所述成型芯棒。如图5和图6所示,所述凹模包括内部开设有倒锥台形凹模成型型腔7的凹模基体5、设在所述倒锥台形凹模成型型腔7中心的成型垫片8和贯穿所述凹模基体5和所述成型垫片8的凹模成型通孔6,所述成型垫片的厚度为5毫米。具体地,如图7和图8所示,所述倒锥台形凹模成型型腔7中心开设有成型垫片安装凹槽9,所述成型垫片8采用热装方法装配在所述成型垫片安装凹槽9内。所述成型垫片8包括与所述成型芯棒基体34材质相同的成型垫片基体81和沉积在所述成型垫片基体81上的所述耐磨耐腐蚀涂层35。其中,本实施例提供的所述成型垫片是通过以下方法制得的:首先选用含有上述质量百分数组分的硬质合金材料进行加工制得成型垫片胚体,然后对所述成型垫片胚体进行研磨、抛光处理,使得该成型垫片胚体的表面粗糙度Ra值为0.05,得到抛光成型垫片胚体;并对所述抛光成型垫片胚体进行脱脂、除油处理得到具有洁净表面的所述成型垫片基体;然后采用化学沉积法以纳米氮化钛、纳米碳化钛或纳米碳氮化钛为原料,在具有洁净表面的所述成型垫片基体上沉积厚度为5微米的所述耐磨耐腐蚀涂层;最后采用流体抛光方法对耐磨耐腐蚀涂层进行精抛光,使得耐磨耐腐蚀涂层的表面粗糙度Ra值为0.03,制得所述成型垫片。具体地,该耐磨耐腐蚀涂层成型模具装配状态时,倒锥台形的所述凹模成型型腔7与所述凸模成型凸台4配合形成液体流通通道,所述定型内芯31与所述凹模成型通孔6配合决定管壁的厚度。熔融态的铝液首先通过三个所述分流槽2进入所述凹模成型型腔7中,使得铝液混合均匀,然后在流入所述凹模成型通孔6中,并通过所述定型内芯31与所述凹模成型通孔6之间的装配配合使得薄壁铝管得到定型,从而制得一定壁厚和一定管径的薄壁铝管。本实施例选用含有WC85%、TiC6%、Co6%、NbC3%的硬质合金材料作为铝管连续挤压模具中的由成型垫片和成型垫片组成的成型部件,利用该类硬质合金自身具有的高耐腐蚀性、较高的高温尺寸稳定性和较好的红硬性,确保了铝管连续挤压模具的成型部件的尺寸稳定性和具有较好的高温耐腐蚀性,同时该类合金材料具有较小的晶粒粒度,使得该铝管连续挤压模具的成型部件经研磨、抛光处理能够获得具有较低表面粗糙度的表面。进一步的,本实施例在所述成型芯棒基体和所述成型垫片基体表面均沉积一层纳米氮化钛层,利用共同存在于该耐磨耐腐蚀涂层、所述成型芯棒基体和所述成型垫片基体中的钛元素所起到的同种元素扩散效应,提升了耐磨耐腐蚀涂层与所述成型芯棒基体和所述成型垫片基体之间的结合力,使得两者之间形成紧密结合的界面涂层不易脱落。更重要的是,该耐磨耐腐蚀涂层是以纳米级的氮化钛为原料,利用纳米颗粒的纳米效应使得制得的所述耐磨耐腐蚀涂层具有较高的光泽度和较低的摩擦系数,从而大幅降低了铝管连续挤压模具的成型部件与铝液之间的摩擦力,使得在铝管生产过程中铝液不易粘连和堆积在铝管连续挤压模具的成型部件,确保了制得的铝管表面光滑无划痕。更进一步的,所述耐磨耐腐蚀涂层以纳米氮化钛为原料,使得制得耐磨耐腐蚀涂层硬度比所述成型芯棒基体和所述成型垫片基体的硬度高,同时由于该耐磨耐腐蚀涂层具有高的抗氧化性、较好的抗粘结性、较高的耐磨性及较好的抗月牙洼磨损,从而显著提高了该铝管连续挤压模具中成型部件的尺寸稳定性、高温耐腐蚀性、高温耐磨性,从而显著提高了该铝管连续挤压模具的使用寿命。实施例2本实施例提供一种铝管连续挤压模具,具体结构与实施例1中的结构不同之处在于:所述耐磨耐腐蚀涂层的厚度为10微米,所述成型垫片8的厚度为3毫米;所述耐磨耐腐蚀涂层为纳米碳化钛层;所述成型芯棒基体和所述成型垫片基体由包括下述质量百分数组分的硬质合金材料加工而成:WC85%、TiC5%、Co10%。实施例3本实施例提供一种铝管连续挤压模具,具体结构与实施例1中的结构大致相同,不同之处在于:所述耐磨耐腐蚀涂层的厚度为8微米,所述成型垫片的厚度为8毫米,所述耐磨耐腐蚀涂层为纳米碳氮化钛层;所述成型芯棒基体和所述成型垫片基体由包括下述质量百分数组分的硬质合金材料加工而成:WC82%、TiC6%、Co8%、TaC4%。实施例4本实施例提供一种铝管连续挤压模具,具体结构与实施例1中的步骤大致相同,不同之处在于:所述定型内芯31的横截面为多边形,所述凹模成型通孔6的横截面为与所述定型内芯31配合的多边形。所述成型芯棒基体和所述成型垫片基体材质为碳化钛铌钼合金。实施例5本实施例提供一种铝管连续挤压模具,如图9和图10所示,本实施例与上述实施例的不同之处在于:所述定型内芯31的为齿状的多边形,所述凹模成型通孔6的横截面为与所述定型内芯31配合的长圆孔。且本实施例中所述分流槽2的数量为两个,所述定型内芯31基体和所述成型垫片基体材质为氮化钛铌钼合金。对比例1本对比例提供一种铝管连续挤压模具,与实施例1中的步骤大致相同,不同之处在于:该对比例所提供的铝管连续挤压模具的成型芯棒基体材质为YG8类硬质合金,且在该芯棒表面不沉积任何涂层,该YG8类硬质合金组分中包括质量百分数为92%的WC和质量百分数为8%的Co。对比例2本对比例提供一种用于铝管挤压成型的定型模具构件中的成型芯棒基体材质YG6类硬质合金,且在该成型芯棒基体表面通过化学沉积法沉积一层厚度为5微米的氮化钛涂层。该YG6类硬质合金组分中包括质量百分数为94%的WC和质量百分数为6%的Co。性能测试分别对实施例1~5和对比例1~2所提供的铝管连续挤压模具进行洛氏硬度、层间结合力及500℃温度下的洛硬度进行检测和统计,同时,分别将上述铝管连续挤压模具的成型部件尺寸设计成能同时生产规格为外径为7.5mm、管道壁厚为0.7mm的薄壁铝管,分别利用上述铝管连续挤压模具进行生产上述规格的薄壁铝管,统计当模具达到报废程度时所能完成加工的铝液吨数;上述各项检测和统计结果如表1所示。由表中可以看出,实施例1~5所提供的所述铝管连续挤压模具与对比例1~2相比均具有较高的维氏硬度和较强的层间结合力。从而验证了所述耐磨耐腐蚀涂层中含有的钛元素与硬质合金中的钛元素能显著改善所述耐磨耐腐蚀涂层与所述成型芯棒基体和所述成型垫片基体之间的结合力。同时,在所述成型芯棒基体和所述成型垫片基体上沉积耐磨耐腐蚀涂层,使得铝管连续挤压模具耐磨性能优异,具有较高的红硬性,并且该铝管连续挤压模具与铝液不易粘连,从而能延长所述铝管连续挤压模具的使用寿命。表1、实施例1~5及对比例1~2提供的铝管连续挤压模具性能检测洛氏硬度层间结合力500℃温度下的洛氏硬度铝液加工吨数实施例19470Mpa9040吨实施例29372Mpa8942吨实施例39071Mpa8745吨实施例49170Mpa9041吨实施例59270Mpa9040吨对比例182无718吨对比例28662Mpa7517吨最后应当说明的是:以上实施例仅用以说明本发明的技术方案而非对其限制;尽管参照较佳实施例对本发明进行了详细的说明,所属领域的普通技术人员应当理解:依然可以对本发明的具体实施方式进行修改或者对部分技术特征进行等同替换;而不脱离本发明技术方案的精神,其均应涵盖在本发明请求保护的技术方案范围当中。当前第1页1 2 3