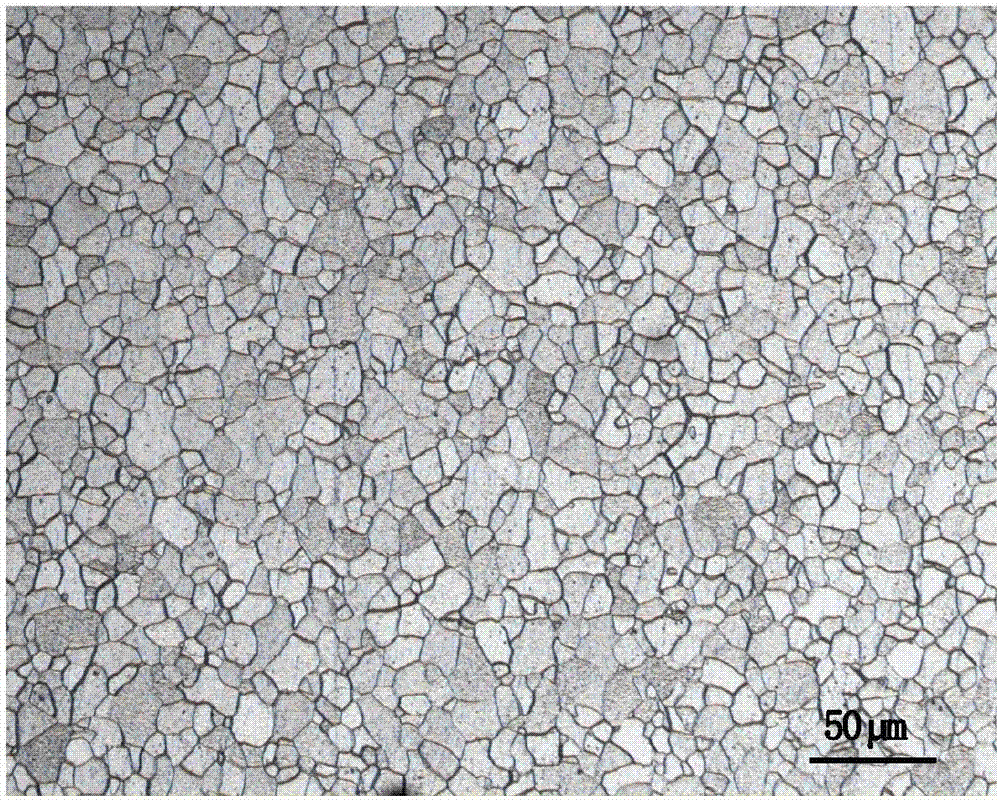
本发明属于超低碳钢板生产
技术领域:
,具体涉及一种极低屈服强度钢板及其生产方法。
背景技术:
:众所周知,冷轧碳素结构钢板是重要的工程结构材料之一,其成形后主要用于汽车工业、建筑结构、压力容器、桥梁结构及机械制造之中。影响工程结构安全的因素主要包括两方面,一方面是结构设计,另一方面是材料性能。工程结构在遭受震动、撞击或者其他意外工况时,如果结构设计连接强度不能承载变形,那么就需要材料强度的协同承载力。提高结构设计承载强度的最有效方法就是增加结构件尺寸,然而这会增加成本。因此增加材料的使用性能成为了现行工程结构材料最大的发展趋势,这就对其的强度、塑性提出了更高的要求。目前,在冷轧汽车用钢市场上,客户为了保证成形性能节约成本,逐步将多步成形工艺简化,力求一步成形。屈强比是衡量金属材料成型性的关键指标,金属材料塑性变形时,屈强比越低,材料从开始塑性变形到断裂所需要的形变能就越大,从而其协调变形的能力越强。因此客户对屈强比提出了更高的要求,随着钢材的品质改进和市场需求,低屈强比成为一些工程材料的重要技术指标之一。为了保证较低的屈强比,生产上对钢的化学成分和生产工艺做了多方面的改进,主要途径通常有两方面:一方面是提高碳含量,但是这样会使碳当量增加,影响焊接性能;另一方面是提高终轧温度或者卷取温度,这会使晶粒尺寸增大,但是会同时降低抗拉强度。因此,优化成分和生产工艺,生产出在保证强度和焊接性能的前提下,极低屈强比的产品具有实际而重要的意义。日本是首先研发低屈服强度钢的国家,国内的研发企业主要有宝钢、首钢、鞍钢、武钢等等,具体专利如下:公开号为“jp55104429a”和“jp2004339548”等专利,公开的都是屈服强度较低、延伸率较高的低合金结构钢。在成分设计上以c-si-mn为基础添加了cr、mo、ni、cu、b等合金中的一种或者多种,屈服强度范围在180-260mpa。公开号为“jp05214442a”和“jp06235042a”等专利,公开的低屈服点钢板屈服强度在130mpa以下。就成分设计而言,都采用在低c-si-mn的基础上添加微合金元素设计,同时还加入了b、nb等成分,就生产工艺而言,均较复杂。公开号为“cn104233061”的专利公开了一种屈服强度在225mpa的低屈服钢及其制造方法,该发明采用c-si-mn的成分设计,无其他合金元素的添加。该发明将成分设计和工艺控制较好的结合起来,生产经济型的低屈服钢板。但是该种方法容易出现混晶、轧制温度窗口窄等问题,并且其屈强比为60%,较高。公开号为“cn101845589”和“jp10324918a”的专利,均公布了一种极低屈服点钢板及其制造方法,其屈服强度在140mpa左右。发明均在低c-si-mn的基础上添加n、ti、nb中的一种或者多种,并含有b元素。然而b的添加不仅提高了钢板的制造成本、增加了冶炼难度,并且不利于钢板的焊接和冲击性能。公开号为“101514426a”的专利公开了一种屈服强度100mpa级的低屈服钢及其制造方法,该发明采用c-si-mn的成分设计,添加微量ti元素合金化。有本发明相比,专利101514426a”的碳当量较高,焊接性能较差。。技术实现要素:本发明提供一种极低屈服强度钢板及其生产方法,该钢板极低屈服强度钢板具有优良的综合力学性能,本发明方法生产成本低、工艺简单、产品成形性能好,能够带来可观的经济效益。为解决上述技术问题,本发明采用如下技术方案:一种极低屈服强度钢板,其特征在于,所述钢板的化学质量百分比为:c≤0.0050%,si≤0.03%,mn:0.10~0.20%,p≤0.013%,s≤0.012%,als:0.020~0.050%,ti:0.055~0.070%,n≤0.0050%,余量为fe及不可避免杂质。本发明所述钢板的冷轧卷显微组织为单一的等轴铁素体,晶粒尺寸为8~10级。本发明所述钢板屈服强度≤110mpa;抗拉强度≥280mpa;断后伸长率a80≥55%。本发明所述的成品钢板的厚度1.5~12mm。本发明的钢板化学成分设计思路如下:c通过固溶强化会使屈服强度升高、延伸率降低,并且过多的c会影响焊接性能,控制其含量≤0.005%。si为脱氧元素,也是固溶强化元素,使屈服强度升高、延伸率降低,控制其含量在0.02%以下。mn是钢中常见的强化元素,通过固溶强化提高屈服强度、使延伸率降低,控制其含量在0.1-0.2%。p、s能够提高强度,并使得钢板变脆、影响韧性,作为杂质元素控制其含量在0.012%以下。al是脱氧必需的元素,但也会提高钢的强度,控制其含量在0.01-0.05%。n的固溶能够显著提高钢的强度,控制其含量在0.005%以下。ti是强烈的铁素体形成元素,也是强脱氧剂,使钢中生成较多的ti的氮化物或碳化物。该ti的碳、氮化物的存在,可以在后期的轧制和热处理过程中阻止奥氏体晶粒的长大,从而改善钢的强度和冲击韧性。并且ti的氮化物或碳化物的存在还可以通过阻止热影响区的晶粒长大,进而有效提高焊接性能。控制其含量0.055-0.070%。本发明的另一目的在于提供上述一种极低屈服强度钢板的生产方法,所述生产方法包括冶炼工序、连铸工序、热轧工序和退火工序。本发明所述冶炼工序采用转炉冶炼,通过顶底复吹,充分脱碳,使用lf精炼进行脱氧脱硫合金化,采用rh精炼降低有害气体n、h含量,最后上板坯连铸。本发明所述热轧工序,粗轧轧制道次5道次,中间坯厚度40~48mm;精轧轧制道次7道次,道次压下率≥10%,总压下率≥75%。本发明所述热轧工序,在完全再结晶温度范围内连续轧制,轧前连铸坯加热温度1230~1270℃,驻炉时间120~160min,出炉温度1130~1150℃;精轧进口温度1030~1070℃,终轧温度885~915℃,卷取温度705~735℃。本发明所述热轧工序,卷取温度层冷过程开启u形卷取模式,带钢头尾30米处高出卷取温度20℃;轧后采用前段快冷,冷速10~20℃/s,上下水比控制在1:1。本发明所述退火工序,采用罩式退火炉,热点/冷点温度为680±20℃/620±20℃,延伸率控制1.0%。采用上述技术方案所产生的有益效果在于:1、本发明提供的极低屈服强度钢板具有优良的综合力学性能,钢板的晶粒尺寸达到8~10级,屈服强度≤110mpa,抗拉强度≥280mpa,断后伸长率a80≥55%,具有优良的塑性变形能力;2、本发明提供的极低屈服强度钢板具有良好的焊接性能,其低碳当量成分设计保证了钢板具有良好的焊接性能;3、本发明方法以低c+mn的基本成分、单加微合金ti元素,采用控轧控冷轧制工艺和罩式退火工艺,生产工艺简单投入小,适用于企业大规模低成本生产。附图说明图1实施例1钢带的边部200倍显微金相组织图;图2实施例1钢带的心部200倍显微金相组织图;图3实施例2钢带的边部200倍显微金相组织图;图4实施例2钢带的心部200倍显微金相组织图;图5实施例3钢带的边部200倍显微金相组织图;图6实施例3钢带的心部200倍显微金相组织图;图7实施例4钢带的边部200倍显微金相组织图;图8实施例4钢带的心部200倍显微金相组织图。具体实施方式下面结合附图和具体实施例对本发明作进一步的详细描述。实施例1一种极低屈服强度钢板,厚度3mm,化学成分组成见表1,余量为fe和不可避免杂质元素。上述极低屈服强度钢板生产方法包括:冶炼工序、连铸工序、热轧工序和退火工序。具体过程如下:1)冶炼及连铸工序:按预定成分冶炼钢水,冶炼工序采用转炉冶炼,通过顶底复吹,充分脱碳,使用lf精炼进行脱氧脱硫合金化,采用rh精炼降低有害气体n、h含量,最后上板坯连铸。连铸获得210mm厚度规格连铸坯。2)热轧工序:冷却后的连铸坯进行加热,均热温度1250℃,驻炉时间120min,出炉温度1150℃;粗轧轧制道次5道次,中间坯厚度40mm;精轧轧制道次7道次,道次压下率10%,总压下率92%;精轧进口温度1070℃,终轧温度900℃;卷取温度730℃,卷取温度层冷过程开启u形卷取模式,带钢头尾30米处高出卷取温度20℃;轧后采用前段快冷,冷速10℃/s,上下水比控制在1:1。3)退火工序:热点/冷点温度690/630℃,拉矫机延伸率控制1.0%。获得钢板力学性能见表2。钢板的冷轧卷显微组织为等轴铁素体,晶粒尺寸为8级。实施例2一种极低屈服强度钢板,厚度9mm,化学成分组成见表1,余量为fe和不可避免杂质元素。上述极低屈服强度钢板生产方法包括:冶炼工序、连铸工序、热轧工序和退火工序。具体过程如下:1)冶炼及连铸工序:按预定成分冶炼钢水,冶炼工序采用转炉冶炼,通过顶底复吹,充分脱碳,使用lf精炼进行脱氧脱硫合金化,采用rh精炼降低有害气体n、h含量,最后上板坯连铸。连铸获得210mm厚度规格连铸坯。2)热轧工序:冷却后的连铸坯进行加热,均热温度1250℃,驻炉时间140min,出炉温度1140℃。粗轧轧制道次5道次,中间坯厚度46mm;精轧轧制道次7道次,道次压下率12%,总压下率80%;控轧控冷轧制工序:精轧进口温度1040℃,终轧温度885℃;卷取温度705℃,卷取温度层冷过程开启u形卷取模式,带钢头尾30米处高出卷取温度20℃。轧后采用前段快冷,冷速12℃/s,上下水比控制在1:1。3)退火工序:罩退工序中,热点/冷点温度670/610℃,拉矫机延伸率控制0.7%。获得钢板力学性能见表2。钢板的冷轧卷显微组织为等轴铁素体,晶粒尺寸为9级。实施例3一种极低屈服强度钢板,厚度1.5mm,化学成分组成见表1,余量为fe和不可避免杂质元素。上述极低屈服强度钢板生产方法包括:冶炼工序、连铸工序、热轧工序和退火工序。具体过程如下:1)冶炼及连铸工序:按预定成分冶炼钢水,冶炼工序采用转炉冶炼,通过顶底复吹,充分脱碳,使用lf精炼进行脱氧脱硫合金化,采用rh精炼降低有害气体n、h含量,最后上板坯连铸。连铸获得210mm厚度规格连铸坯。2)热轧工序:冷却后的连铸坯进行加热,均热温度1270℃,驻炉时间120min,出炉温度1150℃;粗轧轧制道次5道次,中间坯厚度40mm;精轧轧制道次7道次,轧制道次压下率11%,总压下率96%;精轧进口温度1070℃,终轧温度890℃;卷取温度735℃,卷取温度层冷过程开启u形卷取模式,带钢头尾30米处高出卷取温度20℃。轧后采用前段快冷,冷速20℃/s,上下水比控制在1:1。3)退火工序:罩退工序中,热点/冷点温度660/600℃,拉矫机延伸率控制0.6%。获得钢板力学性能见表2。钢板的冷轧卷显微组织为等轴铁素体,晶粒尺寸为8级。实施例4一种极低屈服强度钢板,厚度12mm,化学成分组成见表1,余量为fe和不可避免杂质元素。上述极低屈服强度钢板生产方法包括:冶炼工序、连铸工序、热轧工序和退火工序。具体过程如下:1)冶炼及连铸工序:按预定成分冶炼钢水,冶炼工序采用转炉冶炼,通过顶底复吹,充分脱碳,使用lf精炼进行脱氧脱硫合金化,采用rh精炼降低有害气体n、h含量,最后上板坯连铸。连铸获得210mm厚度规格连铸坯。2)热轧工序:冷却后的连铸坯进行加热,均热温度1230℃,驻炉时间160min,出炉温度1130℃;粗轧轧制道次5道次,中间坯厚度48mm;精轧轧制道次7道次,道次压下率10%,总压下率75%;控轧控冷轧制工序:精轧进口温度1030℃,终轧温度915℃;卷取温度705℃,卷取温度层冷过程开启u形卷取模式,带钢头尾30米处高出卷取温度20℃。轧后采用前段快冷,冷速10℃/s,上下水比控制在1:1。3)退火工序:罩退工序中,热点/冷点温度700/640℃,拉矫机延伸率控制1.0%。获得钢板力学性能见表2。钢板的冷轧卷显微组织为等轴铁素体,晶粒尺寸为10级。表1实施例1-4钢的化学成分(wt%)序号csimnpsalstin实施例10.0040.0150.160.0100.0100.0360.0600.002实施例20.0030.0200.130.0090.0100.0330.0580.003实施例30.0050.0300.100.0080.0120.0500.0700.005实施例40.00450.0250.200.0130.0080.0200.0550.004表2实施例1-4钢板的综合力学性能序号位置屈服强度/mpa抗拉强度/mpa屈强比延伸率a80/%实施例11/41062980.3658实施例21/41002860.3561实施例31/41083030.3659实施例41/41102800.3955从上表可以看出,本发明提供的极低屈服强度钢板具有稳定的屈服强度,在不同的轧制工艺下,各种厚度钢板的屈服强度均≤110mpa。本发明提供的极低屈服强度钢板还具有很高的延伸率及良好的韧性。以上实施例仅用以说明而非限制本发明的技术方案,尽管参照上述实施例对本发明进行了详细说明,本领域的普通技术人员应当理解:依然可以对本发明进行修改或者等同替换,而不脱离本发明的精神和范围的任何修改或局部替换,其均应涵盖在本发明的权利要求范围当中。当前第1页12