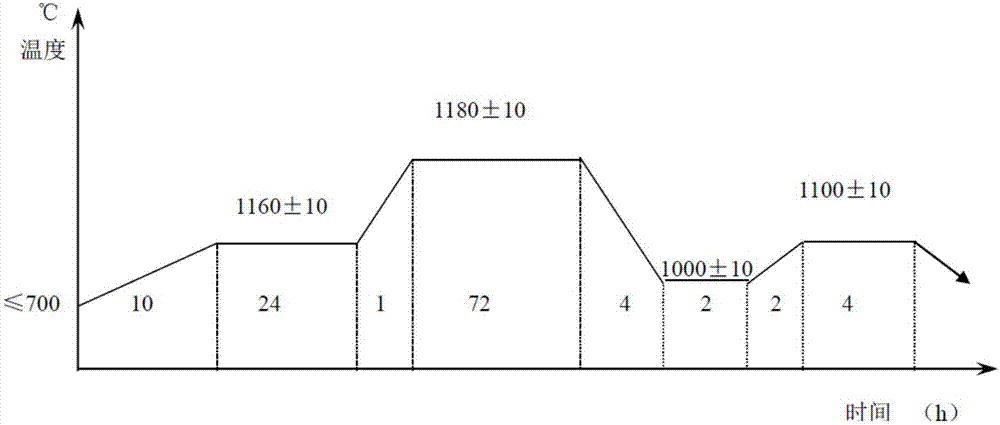
本发明涉及金属材料加工
技术领域:
,具体而言,涉及一种冷轧薄板的制备方法。
背景技术:
:钢铁工业的发展关系着一个国家的综合国力和国家整体的经济水平,是国民经济建设中的基础产业之一。钢铁材料在国防工业、机械工业、建筑、汽车、造船和家电等行业中都有重要的应用,是国家制造业中不可或缺的原材料。近年来,中国升级了其产业结构,为钢铁行业的发展提供了继续发展的空间,国民经济建设需要越来越多的高品质钢铁产品。冷轧薄板带是生产许多重要设备的基本原料,在钢铁工业生产中占有重要地位。冷轧的生产方式能够使带钢的厚度更薄,还能提高轧制的精度。冷轧薄板的平直度很高,具备清洁光亮的表面,容易进行涂镀加工,具有较高的冲压性能,不时效并且屈服点很低,因此冷轧薄板在汽车、建筑、自行车、建材、印制铁桶和涂镀钢板等行业受到了广泛的应用。冷轧薄板逐渐成为一些行业必不可缺的原料产品,反过来,相关行业的蓬勃发展也促进了冷轧薄板的生产,同时由于轻量化、高强度产品概念的普及,市场对冷轧薄板的质量要求不断提高。目前,冷轧薄板带的生产工艺比较复杂,工序较多,其质量很容易受到影响。经过热轧的板带作为生产冷轧板的原料,要经过冷轧产生变形,最后对其进行高温退火处理并进行精整。每道工序都可能改变薄板带的表面质量,加大了分析造成产品缺陷原因的难度。现有技术中,冷轧薄板的膨胀系数还不够理想,这限制了其在低膨胀结构件中的使用。有鉴于此,特提出本发明。技术实现要素:本发明的目的在于提供一种冷轧薄板的制备方法,以生产不含cr、al的低膨胀高温合金冷轧薄板。为了实现本发明的上述目的,特采用以下技术方案:本发明涉及一种冷轧薄板的制备方法,其包括将种化学成分质量百分比为:c≤0.06、ni为35.0~40.0、co为12.0~16.0、nb为4.3~5.2、ti为1.3~1.8、si为0.25~0.50、b≤0.012、mo≤0.20、mn≤1.00、al≤0.20、cr≤1.00、cu≤0.50、s≤0.015、p≤0.015,余量为fe的钢种制成的钢坯依次经过热轧、一次冷轧、一次退火、二次冷轧、二次退火后即得;其中,所述一次退火的条件为:加热温度:970±10℃;加热时间按1.5min/mm+3~5min计算,空冷;所述二次退火的条件为:加热温度:960±10℃;加热时间按1.5min/mm+3~5min计算,空冷。通过调整、优化和改进冷轧薄板制备工艺,本发明使一种低膨胀高温合金冷轧薄板的表面、尺寸、性能满足标准和用户使用要求,生产出合格的一种低膨胀高温合金冷轧薄板产品,提高产品质量,为企业创造更多的经济效益。与现有技术相比,本发明在保持非常薄的厚度的(≤0.6mm)的前提下具有优秀的低膨胀性和力学性能。附图说明为了更清楚地说明本发明具体实施方式或现有技术中的技术方案,下面将对具体实施方式或现有技术描述中所需要使用的附图作简单地介绍,显而易见地,下面描述中的附图是本发明的一些实施方式,对于本领域普通技术人员来讲,在不付出创造性劳动的前提下,还可以根据这些附图获得其他的附图。图1为gh2909合金6吨感应炉熔炼功率曲线;图2为钢锭均匀化处理及锻造工艺曲线;图3为锻造成品中间坯料加热曲线。具体实施方式本发明涉及一种冷轧薄板的制备方法,其包括将种化学成分质量百分比为:c≤0.06、ni为35.0~40.0、co为12.0~16.0、nb为4.3~5.2、ti为1.3~1.8、si为0.25~0.50、b≤0.012、mo≤0.20、mn≤1.00、al≤0.20、cr≤1.00、cu≤0.50、s≤0.015、p≤0.015,余量为fe的钢种制成的钢坯依次经过热轧、一次冷轧、一次退火、二次冷轧、二次退火后即得;其中,所述一次退火的条件为:加热温度:970±10℃;加热时间按1.5min/mm+3~5min计算,空冷;所述二次退火的条件为:加热温度:960±10℃;加热时间按1.5min/mm+3~5min计算,空冷。优选的,如上所述的冷轧薄板的制备方法,所述一次冷轧控制冷轧总变形量在30%~35%;所述二次冷轧控制冷轧总变形量在30~35%。优选的,如上所述的冷轧薄板的制备方法,所述热轧的参数为:荒轧温度1000±10℃,精轧温度970±10℃,荒轧终轧温度>800℃,精轧终轧温度>800℃;加热时间按1.5min/mm+3-5min计算。最大道次变形量<25%,最后一次变形量20~25%。优选的,如上所述的冷轧薄板的制备方法,在经过二次退火后还包括酸碱洗及白化步骤。优选的,如上所述的冷轧薄板的制备方法,所述钢坯由所述钢种经过真空感应熔炼及真空自耗重熔冶炼工艺路线获得钢锭,将所述钢锭锻造开坯、轧制开坯后得到钢坯。优选的,如上所述的冷轧薄板的制备方法,所述锻造开坯包括:电液锤或快锻机或精锻机末火锻造:加热温度980℃~1020℃,变形温度控制在955℃~980℃,变形量≥40%;更优选的,加热温度为990℃~1010℃,变形温度控制在960℃~975℃,变形量≥43%。优选的,如上所述的冷轧薄板的制备方法,所述轧制开坯包括:将锻造开坯后的坯料在轧机的连续炉中加热开坯后进行板坯轧制。优选的,如上所述的冷轧薄板的制备方法,所述加热开坯的条件为:装炉温度≤700℃,加热温度1110±10℃,加热时间≥4h,保温时间2h。优选的,如上所述的冷轧薄板的制备方法,所述板坯轧制包括:将板坯经轧机一火多道次轧成所需尺寸的板坯,停轧温度≥950℃,道次最大变形量≤25%。优选的,如上所述的冷轧薄板的制备方法,所述钢种的化学成分质量百分比为:c≤0.012、ni为37.8~38.8、co为12.8~13.8、nb为4.6~5.0、ti为1.4~1.7、si为0.35~0.47、b≤0.01、mo≤0.20、mn<0.5、al<0.06、cr<0.2、cu<0.1、s≤0.015、p≤0.015;更优选的,如上所述的冷轧薄板的制备方法,所述钢种的化学成分质量百分比为:c≤0.012、ni为38.2~38.7、co为12.8~13.8、nb为4.6~5.0、ti为1.4~1.7、si为0.35~0.47、b≤0.01、mo≤0.20、mn<0.5、al<0.06、cr<0.2、cu<0.1、s≤0.015、p≤0.015。下面将结合实施例对本发明的实施方案进行详细描述,但是本领域技术人员将会理解,下列实施例仅用于说明本发明,而不应视为限制本发明的范围。实施例中未注明具体条件者,按照常规条件或制造商建议的条件进行。所用试剂或仪器未注明生产厂商者,均为可以通过市购获得的常规产品。实施例1适用范围gh909合金是在gh907合金基础上发展起来的一种fe-ni-co基时效硬化型低膨胀高温合金,与gh907合金相比,合金的应力促进晶界氧化脆性(sagbo)抗力和持久寿命得到进一步提高,但热膨胀系数与gh903、gh907基本相同,其性能已基本可满足三代以下涡轮发动机的需求,它具有低的热膨胀系数、几乎恒定的弹性模量及良好的综合力学性能,广泛应用于转动部件与静止部件之间的间隙构件,实现间隙控制技术,节约能源,降低消耗,提高发动机推力,但由于合金不含cr,其缺点是氧化抗力和腐蚀抗力很低,特别是抗氧化问题,在650℃以上gh909合金不能完全抗氧化。gh2909合金熔点约为1336~1384℃,比重约为8.26g/cm3。2技术条件q/s15.2206-2011等3工艺路线真空感应+真空自耗4技术要求4.1真空感应熔炼工艺4.1.16吨真空感应炉熔炼工艺4.1.1.1设备要求:风、水、电、真空系统及各机械设备运转正常。4.1.1.2熔炼条件:新坩埚冶炼需fe洗2炉,第二炉铁洗用精钢材(纯00),中间冶炼需铁洗(纯00)1炉。4.1.1.3原材料炉料由本钢返回(≤50%)、精钢材(ct1-1)、1#ni、j-co、单晶硅、石墨电极、j-nb、海绵ti和fe-b组成。合金料进厂后必须按原材料进厂检验规程进行验收,原材料的表面、尺寸、块度要求符合6吨真空感应炉基本规程。4.1.1.4装入量及电极规格装入量:3200kg或6400kg;电极:支或支。4.1.1.5gh2909合金化学成分,见表1。gh2909合金化学成分▲(wt%)表14.1.1.6装料4.1.1.6.1前炉fe洗保证ct1-1全部化完,并翻净钢水,避免炉中撤料。4.1.1.6.2所有入炉原材料经生产工人、专责检查人员按配料单检查、称重,确认品种、数量无误并签字后方可入炉。4.1.1.6.3ni、co及精钢材(ct1-1)一次装入坩埚。c、ti、nb、fe-b、si按冶炼工艺曲线加入。4.1.1.7冶炼工艺曲线,如图1。4.1.1.8冶炼要点:精炼温度要求控制准确,保证脱n效果,勤测温和搅拌。加ti后十分钟取样分析,加料和取样时加强搅拌,控制好出钢温度。4.1.1.9浇注4.1.1.9.1浇注在真空下进行,控制浇注速度及充填质量。4.1.1.9.2钢锭模必须用钢水烫过,清洁无锈。4.1.1.9.3中间罐必须加热4个小时以上,表面温度必须达到1000℃。4.1.1.9.4浇注后炉冷时间大于1.5h方可破空,模冷2h后脱锭。4.2真空自耗重熔4.2.1熔炼条件熔炼前必须对设备进行检查,确认设备良好,冷态真空度<0.67pa,漏气度<0.67pa/min方可冶炼。4.2.2自耗电极头尾切净,表面须经砂轮研磨干净,若表面不好需扒皮清理后,缩孔朝向下自耗重熔。4.2.3自耗工艺4.2.3.1真空度<0.67pa方可给电起弧。4.2.3.2结晶器:4.2.3.3电力制度锭,电流7000a左右,电压22~24v左右。电流以熔池到边的最小电流为准。熔炼按电力曲线进行。重熔过程中进行冲氦气冷却,其压强为600pa±。4.2.3.4一定要注意充填质量,逐渐降低电流。每一阶段保持一定时间,不可一下降到低电流,使熔池尽可能收缩,缩孔上提,提高成材率。4.2.4充填工艺:在电极剩余200±10kg时开始填充,填充参考工艺及步骤如下:步骤电流(a)电压(v)保持时间(min)160002332550022.853450022.684400022.5105350022.05-106200021.75-107200020.05-104.3.均匀化处理对钢锭进行均匀化处理。注意钢锭在均匀化处理时严格控制温度,不能出现温度波动过大和跑温现象!均匀化处理制度见图2,钢锭在罩式炉中加热。4.4.锻造工艺4.4.1钢锭开坯锻造在2000t或4500t快锻上进行。4.4.2加热制度加热制度曲线,如图2:4.4.3锻造工艺开坯锻造:通常采用多次镦拔工艺,具体变形方案视成品规格确定;4.4.3.1精锻机组加热工艺以下为中间坯加热曲线,生产时可根据中间坯大小适当调整保温时间,以坯料温度均匀到温为准。锻造成材:电液锤或快锻机或精锻机末火锻造:加热温度980~1020℃,见图3,变形温度控制在955~980℃,变形量≥40%,不可回炉空烧。4.4.4供轧制坯料,可在电液锤进行开坯。4.5.轧制工艺4.5.1加热制度坯料在轧机的连续炉中加热。装炉温度≤700℃,加热温度1110±10℃,加热时间≥4h,保温时间2h。4.5.2板坯轧制板坯经轧机一火多道次轧成所需尺寸的板坯,停轧温度≥950℃,道次最大变形量≤25%。坯料表面全扒皮后下流,并按要求取头尾低倍。4.5.3方坯轧制方坯经轧机一火多道次轧成所需尺寸的棒材或坯料。4.6.薄板工艺4.6.1热轧荒轧温度1000±10℃,精轧温度970±10℃,荒轧终轧温度>800℃,精轧终轧温度>800℃。加热时间按1.5min/mm+3-5min计算。最大道次变形量<25%,最后一次变形量20~25%。4.6.2冷轧半成品总变形量30~35%,成品总变形量25~30%。4.6.3退火退火在辊底炉中进行。4.6.3.1半成品加热温度:970±10℃。加热时间按1.5min/mm+3~5min计算,空冷。4.6.3.2成品加热温度960±10℃。成品退火温度940±10℃。加热时间按1.5min/mm+3~5min计算,空冷。4.6.4酸碱洗、白化按铁基高温合金工艺执行。4.6.5精整、检验、探伤、包装、入库。4.7.未尽事宜按基本操作规程执行。实验例按照gb/t4339-2008金属材料热膨胀特性参数测量方法检测本发明所制备的冷轧薄板的室温~600℃平均线膨胀系数。试样规格为检测使用设备为(德)netzschdil203se膨胀仪。检测结果如下表所示:同时对0.6mm厚冷轧板材成品性能进行检测,结果如下表所示:最后应说明的是:以上各实施例仅用以说明本发明的技术方案,而非对其限制;尽管参照前述各实施例对本发明进行了详细的说明,但本领域的普通技术人员应当理解:其依然可以对前述各实施例所记载的技术方案进行修改,或者对其中部分或者全部技术特征进行等同替换;而这些修改或者替换,并不使相应技术方案的本质脱离本发明各实施例技术方案的范围。当前第1页12