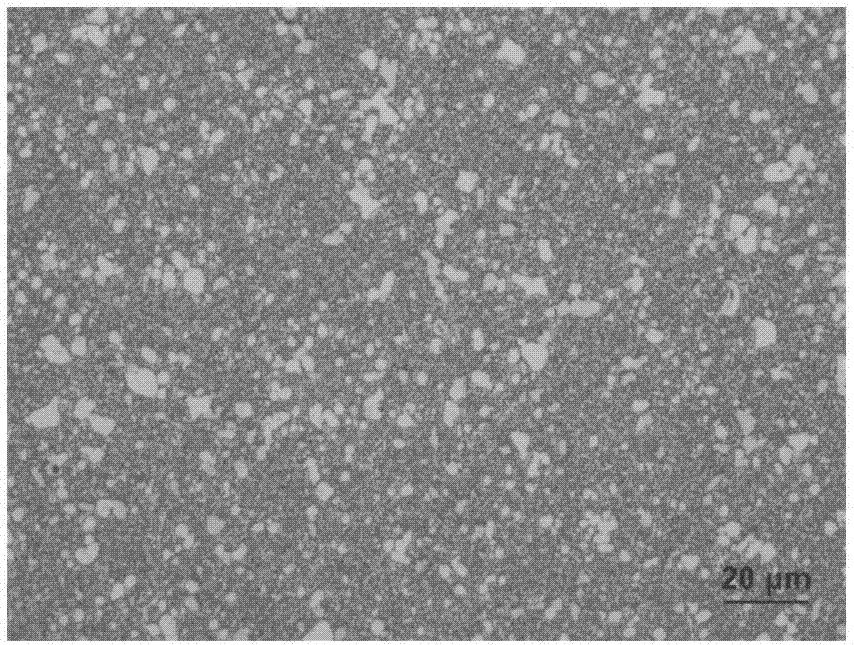
本发明属于模具钢制造
技术领域:
,更具体地说,是涉及一种冷热兼作模具钢及其制造工艺。
背景技术:
:模具钢传统上分为冷作模具钢和热作模具钢,两种模具钢的主要区别在于使用的温度不同,冷作模具钢是在低温下使用(100度以下),主要是用在冲压模具;热作模具钢是高温下使用,主要是用在压铸模具。使用环境及使用温度的不同,导致了冷作模具钢和热作模具钢分别侧重不同的性能,冷作模具钢侧重硬度、耐磨性,热作模具钢对硬度要求适当,侧重于红硬性,导热性,耐磨性。针对不同的使用需求,一般采用不同的模具钢原材料制备,无形中增加了生产成本。现有的一些研究提供了能够冷热兼作的钢材,但还是存在组织成分不均匀,使用过程中容易开裂,影响模具使用寿命的问题。技术实现要素:本发明的目的在于提供一种冷热兼作模具钢,以解决现有技术中存在的冷热兼作模具钢的组织成分不均匀的技术问题。为实现上述目的,本发明采用的技术方案是:提供一种冷热兼作模具钢的制造工艺,包括如下步骤:利用中频炉进行中频冶炼,冶炼后出钢,并在出钢后进行炉外精炼;喷射成形,获得钢锭;对所述钢锭进行初次退火,退火后出炉空冷;对经过初次退火后的所述钢锭进行热变形锻打,所述热变形锻打的加热温度为1140-1160℃,保温4-6小时,开锻温度1050℃,终锻温度为900℃;对经过热变形锻打的圆坯进行车皮,并在车皮后进行二次锻打;对经过二次锻打的棒材进行锻后余热退火,退火后出炉空冷;对经过锻后余热退火的棒材进行淬火及多次回火,其中,淬火为分级预热式淬火,一级预热温度为500-550℃,二级预热温度为850-900℃,奥氏体化温度为1050-1120℃;回火温度为540-560℃,回火时间为1小时,回火次数为3次,每次回火后工件冷却至室温。进一步地,所述炉外精炼包括:精炼时间为30-120分钟,精炼时采用氩气搅拌。进一步地,所述喷射成形包括:在炉外精炼温度达到1620-1650℃时开始喷射,喷射雾化气体为氮气,雾化压力为6-10bar,沉积距离为450-500mm,喷射温度为1620-1580℃,转速为40-60转/分。进一步地,所述初次退火包括:在880℃-920℃的温度下保温5-8小时;以20℃/h的降温速度降到550℃。进一步地,所述热变形锻打为自由锻造方式,在锻造时采用轻重轻的锻造方法。进一步地,所述二次锻打为自由锻造方式,在锻造时采用轻重轻的锻造方法,锻打的加热温度为1140-1160℃,保温4-6小时,开锻温度1050℃,终锻温度为900℃。进一步地,所述锻后余热退火具体为:在880℃-920℃的温度下保温5-8小时;以20℃/h的降温速度降到550℃。进一步地,对经过锻后余热退火的钢锭进行淬火及三次回火。本发明提供的冷热兼作模具钢的制造工艺的有益效果在于:与现有技术相比,本发明冷热兼作模具钢的制造工艺,通过喷射成形步骤,钢锭内组份的偏析被抑制在了很小的范围内,同时通过两次锻造,能够有效防止大颗粒碳化物的形成,提高钢材的冲击韧性及塑性,提高了钢材的品质。本发明还提供一种冷热兼作模具钢,基于上述的冷热兼作模具钢的制造工艺制造,化学组分按质量百分比计包括:c:0.55-0.65%,si:0.85-1.15%,cr:3.7-4.4%,mo:1.8-2.2%,v:1.3-1.7%,w:1.9-2.2%,余量为铁和杂质。进一步地,组分中c:0.57-0.63%,si:0.9-1.1%,cr:3.8-4.3%,mo:1.9-2.1%,v:1.4-1.6%,w:2.0-2.1%。本发明提供的冷热兼作模具钢的有益效果在于:与现有技术相比,本发明冷热兼作模具钢,组织均匀细小,避免大颗粒碳化物的存在,具备高硬度和高冲击韧性,可与粉末钢韧性相当,同时具有较好的塑性,易于进行机加工,有利于提高模具成品的使用寿命。附图说明为了更清楚地说明本发明实施例中的技术方案,下面将对实施例或现有技术描述中所需要使用的附图作简单地介绍,显而易见地,下面描述中的附图仅仅是本发明的一些实施例,对于本领域普通技术人员来讲,在不付出创造性劳动性的前提下,还可以根据这些附图获得其他的附图。图1为本发明实施例1在100微米尺度下的组织照片;图2为本发明实施例1在20微米尺度下的组织照片;图3为本发明实施例1与传统工艺制备的模具钢的硬度对比图;图4为本发明实施例1与传统工艺制备的模具钢的冲击值对比图;图5为本发明实施例1与传统工艺制备的模具钢的抗拉强度对比图;图6为本发明实施例1与传统工艺制备的模具钢的断面收缩比率对比图。具体实施方式为了使本发明所要解决的技术问题、技术方案及有益效果更加清楚明白,以下结合附图及实施例,对本发明进行进一步详细说明。应当理解,此处所描述的具体实施例仅仅用以解释本发明,并不用于限定本发明。现对本发明提供的冷热兼作模具钢的制造工艺进行说明,所述冷热兼作模具钢的制造工艺包括如下步骤:利用中频炉进行中频冶炼,冶炼后出钢,并在出钢后进行炉外精炼;喷射成形,获得钢锭,钢锭的直径为400-550mm,重量为2-4吨;对所述钢锭进行初次退火,退火后出炉空冷;对经过初次退火后的所述钢锭进行热变形锻打,所述热变形锻打的加热温度为1140-1160℃,保温4-6小时,开锻温度1050℃,终锻温度为900℃;对经过热变形锻打的圆坯进行车皮,中间圆坯表面有小裂纹,为了防止小裂纹在后续锻打过程中延伸,并在车皮后进行二次锻打;对经过二次锻打的钢锭进行锻后余热退火,退火后出炉空冷;对经过锻后余热退火的钢锭进行淬火及多次回火,其中,淬火为分级预热式淬火,一级预热温度为500-550℃,二级预热温度为850-900℃,奥氏体化温度为1050-1120℃;回火温度为540-560℃,回火时间为1小时,回火次数为3次,每次回火后工件冷却至室温。本发明提供的冷热兼作模具钢的制造工艺,通过喷射成形步骤,钢锭内组份的偏析及组织的粗化被抑制在了很小的范围内,同时通过两次锻造及多次的回火处理,能够有效防止大颗粒碳化物的形成,提高钢材的冲击韧性及塑性,提高了钢材的品质,有效延长钢材的使用寿命。分次锻造,能够环节加工变形量对加工硬化强度的影响,避免长时间锻造过程中产生心部断裂或表面裂纹。进一步地,炉外精炼包括:精炼时间为30-120分钟,精炼时采用氩气搅拌,有助于提高钢材的纯净度。进一步地,作为本发明提供的冷热兼作模具钢的制造工艺的一种具体实施方式,喷射成形包括:在炉外精炼温度达到1620-1650℃时开始喷射,喷射雾化气体为氮气,雾化压力为6-10bar,沉积距离为450-500mm,喷射温度为1620-1580℃,转速为40-60转/分。通过调整喷射的参数,能够获得组织均匀细小且致密度高的沉积坯,有利于提高成品的性能。进一步地,初次退火为了防止钢锭表面和心部温差大引起的应力裂包括:在880℃-920℃的温度下保温5-8小时;以20℃/h的降温速度降到550℃。进一步地,热变形锻打为自由锻造方式,在锻造时采用轻重轻的锻造方法。自由锻造是利用冲击力或压力使金属在上下砧面间各个方向自由变形,不受任何限制而获得所需形状及尺寸和一定机械性能的锻件的一种加工方法,所用工具和设备简单,通用性好,成本低,操作灵活,同铸造毛坯相比,自由锻消除了缩孔、缩松、气孔等缺陷,使毛坯具有更高的力学性能。采用轻重轻的锻造方法,避免了连续重锤,避免出现内裂等缺陷,提高钢材的品质。进一步地,二次锻打为自由锻造方式,在锻造时采用轻重轻的锻造方法,锻打的加热温度为1140-1160℃,保温4-6小时,开锻温度1050℃,终锻温度为900℃。进一步地,锻后余热退火具体为:在880℃-920℃的温度下保温5-8小时;以20℃/h的降温速度降到550℃。锻后余热退火一般为等温退火,可以获得均匀、稳定的硬度和组织,提高锻坯的加工切削性能,降低刀具损耗,也为最后的热处理做好组织上的准备,此工艺也有显著的节能效果。进一步地,对经过锻后余热退火的钢锭进行淬火及三次回火,让残余奥氏体更多的转变为回火马氏体,发挥其高硬度高韧性。本发明还提供一种冷热兼作模具钢。所述冷热兼作模具钢,基于上述的冷热兼作模具钢的制造工艺制造,化学组分按质量百分比计包括c:0.55-0.65%,si:0.85-1.15%,cr:3.7-4.4%,mo:1.8-2.2%,v:1.3-1.7%,w:1.9-2.2%,余量为铁和杂质。本发明提供的冷热兼作模具钢,与现有技术相比,组织均匀细小,避免大颗粒碳化物的存在,冲击韧性高,可与粉末钢韧性相当,同时具有较好的塑性,易于进行机加工,有利于提高模具成品的使用寿命。c元素不仅是碳化物的组成元素,而且固溶于基体,对基体起到强烈的强化作用,c元素的含量控制在0.55-0.65%,以保证合金元素能够充分析出,同时避免基体韧性及塑性下降的过低,进而能够获得最大的硬度、韧性与塑性的配合。si元素通常作为脱氧添加剂,主要用于控制钢的含氧量,对钢的二次硬化做出了贡献,si元素的含量控制在0.85-1.15%,使硬度略有降低,但是能显著提高冲击韧性。cr元素的作用在于保证钢的淬透性,特别对于截面较大的模具,淬透性尤为重要。cr元素的含量控制在3.7-4.4%,含量较低,在回火的过程中可同时析出mo、v、w的二次硬化合金碳化物,能够有效控制cr的一次碳化物的含量,配合cr较低的含量,能够有效降低cr的一次碳化物对冲击韧性的影响。mo、w主要在回火的过程中析出二次碳化物(m6c或m2c),是强二次硬化元素,提高钢的热强性和抗回火软化,还能提高硬度。mo对改善冲击韧性有利,w则能够有效提高耐热性,但当mo、w的含量较高的时候,二次硬化能力提高较少,韧性损失较多,因此将mo的含量控制在1.8-2.2%,将w的含量控制在1.9-2.2%,使二次硬化能力达到较高的水平,同时有利于改善冲击韧性。v元素主要参与mc碳化物的形成,特别是在多次回火的过程中形成的mc型碳化物对耐磨性贡献最大,v也有超晶粒细化作用,但v在凝固过程中也会形成共晶碳化物,当共晶碳化物含量过多的时候呈链状分布,热处理的时候也基本不发生变化,对韧性有不利的影响,因此在平衡耐磨性和对冲击韧性的不利影响的前提下,v的含量控制在1.3-1.7%。本发明提供的冷热兼作模具钢提供了合适的组份配比,充分考虑到了钢的耐磨性、硬度、冲击韧性、塑性等性能,提高了钢的力学性能。进一步地,组分中c:0.57-0.63%,si:0.9-1.1%,cr:3.8-4.3%,mo:1.9-2.1%,v:1.4-1.6%,w:2.0-2.1%。将各个组份的含量做出进一步精确的控制,进而有利于提高钢材的力学性能。表1不同实施例冷热兼作模具钢的化学组分表csicrmovw实施例10.57%0.90%3.80%1.90%1.40%2.00%实施例20.60%1.00%4.00%2.00%1.50%2.05%实施例30.63%1.10%4.30%2.10%1.60%2.10%实施例1采用表1中实施例1对应的组份,并且工艺参数为:精炼时间为30分钟;在炉外精炼温度达到1620℃时开始喷射,喷射雾化气体为氮气,雾化压力为6bar,沉积距离为450mm,喷射温度为1620℃,转速为40转/分;初次退火时在880℃的温度下保温5小时,随后以20℃/h的降温速度降到550℃;热变形锻打的加热温度为1140℃,保温4-6小时,开锻温度1050℃,终锻温度为900℃;二次锻打的加热温度为1140℃,保温4-6小时,开锻温度1050℃,终锻温度为900℃;锻后余热退火时在880℃的温度下保温5小时,随后以20℃/h的降温速度降到550℃;对经过锻后余热退火的钢材进行淬火及三次回火,淬火时采用分级预热:一级预热温度为500℃,二级预热温度为850℃,奥氏体化温度为1050℃,回火温度为540℃,回火时间为1小时,回火三次。实施例2采用表1中实施例2对应的组份,并且工艺参数为:精炼时间为90分钟;在炉外精炼温度达到1635℃时开始喷射,喷射雾化气体为氮气,雾化压力为8bar,沉积距离为475mm,喷射温度为1600℃,转速为50转/分;初次退火时在900℃的温度下保温5小时,随后以20℃/h的降温速度降到550℃;热变形锻打的加热温度为1150℃,保温4-6小时,开锻温度1050℃,终锻温度为900℃;二次锻打的加热温度为1150℃,保温4-6小时,开锻温度1050℃,终锻温度为900℃;锻后余热退火时在900℃的温度下保温5小时,随后以20℃/h的降温速度降到550℃;对经过锻后余热退火的钢材进行三次回火,淬火时采用分级预热:一级预热温度为525℃,二级预热温度为875℃,奥氏体化温度为1085℃,回火温度为550℃,回火时间为1小时,回火三次。实施例3采用表1中实施例3对应的组份,并且工艺参数为:精炼时间为120分钟;在炉外精炼温度达到1650℃时开始喷射,喷射雾化气体为氮气,雾化压力为10bar,沉积距离为500mm,喷射温度为1580℃,转速为60转/分;初次退火时在920℃的温度下保温5小时,随后以20℃/h的降温速度降到550℃;热变形锻打的加热温度为1160℃,保温4-6小时,开锻温度1050℃,终锻温度为900℃;二次锻打的加热温度为1160℃,保温4-6小时,开锻温度1050℃,终锻温度为900℃;锻后余热退火时在920℃的温度下保温5小时,随后以20℃/h的降温速度降到550℃;对经过锻后余热退火的钢材进行淬火及三次回火,淬火时一级预热温度为550℃,二级预热温度为900℃,奥氏体化温度为1120℃,回火温度为560℃,回火时间为1小时,回火三次。请参阅图1及图2,可见采用实施例1制备得到的模具钢组织均匀细小,没有大颗粒碳化物的存在。请参阅图3至图6,可见采用实施例1制备得到的模具钢(图中以hsf122表示)余传统工艺制备的模具钢(c2)相比,硬度、抗拉强度基本持平,冲击值(冲击韧性)比传统工艺高约3倍,断面收缩率高于传统工艺,其中的断面收缩率与塑性相关,断面收缩率越高,塑性越好。表2不同实施例冷热兼作模具钢的性能表实施例1实施例2实施例3硬度60.861.261.5冲击值262.5245138抗拉强度740745750断面收缩率55.30%53.90%53.00%可见,三个实施例的冲击值(冲击韧性)和断面收缩率均比传统工艺得到的产品高,硬度、抗拉强度基本持平。以上所述仅为本发明的较佳实施例而已,并不用以限制本发明,凡在本发明的精神和原则之内所作的任何修改、等同替换和改进等,均应包含在本发明的保护范围之内。当前第1页12