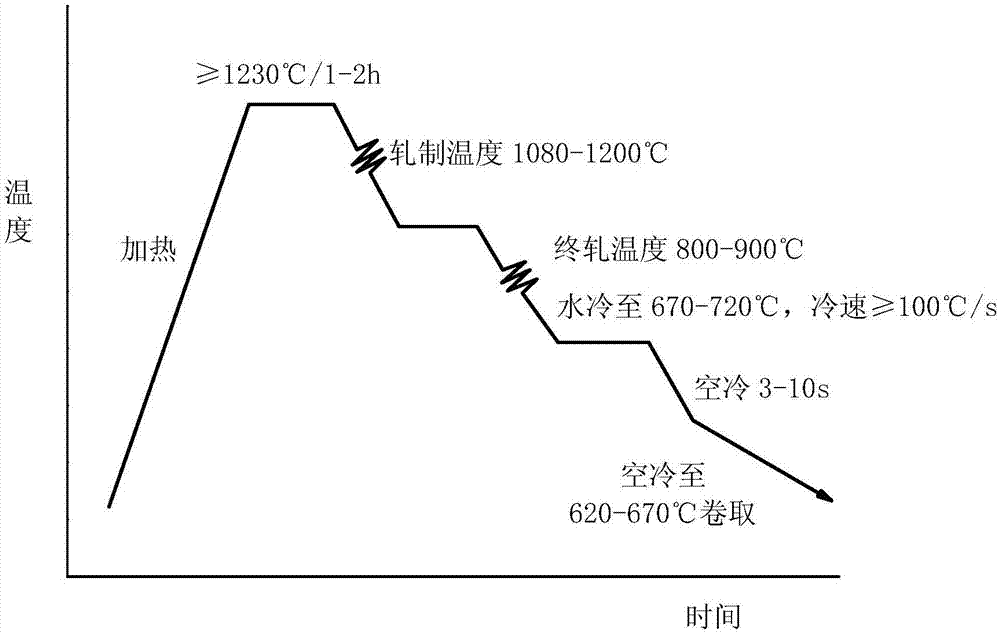
本发明属于热轧或酸洗高强钢领域,特别涉及一种600mpa级高疲劳高强钢及其制造方法。
背景技术:
在乘用车或轻卡商用车领域,采用高强钢进行高强减薄设计已经成为一种不可避免的趋势。尤其是在乘用车领域,无论国际还是国内,各种相关的法律法规都在更加严格,如燃油排放的标准愈发严格,乘用车的轻量化不仅是汽车行业的发展趋势,而且还是法律法规的要求。法律法规中规定了油耗,实际上是变相地要求降低车身重量,反映到材料上的要求是高强减薄轻量化。高强减重是后续新车型的必然要求,这势必造成用钢级别更高,从而使得底盘结构上也必然带来变化:如零件更复杂,造成在材料性能、表面等要求上以及成型技术上进步,如液压成形、热冲压、激光焊接等,进而转化材料的高强、冲压、翻边、回弹以及疲劳等各种特殊性能上。乘用车的一部分底盘结构件如扭力梁、摆臂、中型或轻型商用车桥壳等都是承受各种交变载荷的重要安全件,对疲劳性能要求很高。如有的用户要求桥壳在三倍载荷条件下的台架疲劳次数≥30万次,2.5倍载荷条件下的台架疲劳次数≥80万次。在目前的实际生产工艺条件下,为了满足这种疲劳性能的要求,扭力梁或桥壳的设计人员只能采用更厚和较低强度的钢板来满足这种台架疲劳性能的要求,但是这种设计不符合乘用车或轻型卡车轻量化的要求,采用这种落后的设计工艺制造出来的乘用车或轻型商用车甚至都不能对外销售。因此,如何在采用高强钢高强减薄之后仍具有优异的台架疲劳性能就显得尤为重要。扭力梁或桥壳的台架疲劳性能主要取决于以下几个方面:一是结构设计。合理的结构设计是保证台架疲劳性能的基础和关键因素,结构设计不合理很容易造成台架疲劳试验不合格;二是焊接质量的影响。如果该结构件包含焊接,则焊接接头的质量也会对台架疲劳性能造成很大影响,疲劳裂纹容易发生在焊接的薄弱环节;三是材料本身的疲劳性能。在前面两个因素确保良好的条件下,材料本身的疲劳性能就显得非常重要。不同材料的疲劳性能的影响因素众多,如温度、载荷条件、表面、内质、组织类型等。但是,材料本身具有优异的疲劳性能是获得良好的台架疲劳性能的基础。以上三个方面是相互影响相互依存的关系,本发明正是在这种行业背景下形成的。具体到轻卡桥壳,目前采用的多是屈服强度345mpa的低强度钢,厚度主要是6-7mm,而用户希望能够采用5mm的屈服强度550-650mpa的高强钢板进行高强减薄,但对台架疲劳试验要求则没有任何降低,仍然要求台架疲劳次数与6-7mm的低强度钢的台架疲劳具有同样的标准。因此,本发明正是从材料设计的角度来获得具有更加优异的疲劳性能的高强钢来满足这种要求。技术实现要素:本发明的目的在于提供一种600mpa级高疲劳高强钢及其制造方法,其屈服强度≥550mpa,抗拉强度≥600mpa,且厚度在3-6mm的热轧超高强钢,同时且具有良好的延伸率(≥25%)和低温冲击韧性(-40℃冲击功≥100j),表现出优异的强度、塑性和韧性匹配;可应用于汽车底盘、大梁、车轮、桥壳等需要高强减薄的地方,具有广阔的应用前景。为达到上述目的,本发明的技术方案是:本发明通过合理的成分设计和相匹配的工艺设计,采用热连轧工艺生产一种抗拉强度达到600mpa以上的热轧高疲劳型高强钢;通过加入较高的ti以保证在热轧卷取高温阶段在铁素体中析出大量弥散细小的相间析出纳米级碳化物,不仅起到强烈的弥散析出强化效果,而且还可以显著提高疲劳性能;添加适量的mo主要是为了保证在高温卷取后缓慢冷却的过程中提高纳米析出碳化物的热稳定性,抑制纳米析出相的粗化,同时也降低铁素体的长大速度,从而获得以细小的铁素体和纳米级相间析出为主要特征的高疲劳高强钢,可应用于桥壳、扭力梁等对疲劳性能有特殊要求的场合。具体的,本发明所述的600mpa级高疲劳高强钢,其成分重量百分比为:c0.03~0.07%,si≤0.1%,mn1.0~1.8%,p≤0.01%,s≤0.002%,al0.02~0.08%,n≤0.004%,ti0.05~0.10%,mo0.10~0.30%,o≤30ppm;其余为fe以及不可避免的杂质;所述钢的组织为全铁素体,晶粒呈近等轴形,平均晶粒尺寸约5-10μm;析出相的体积分数为0.104-0.209%,平均析出相尺寸为5-10nm。优选的,所述c的含量为0.04-0.06%。优选的,所述mn的含量为1.3-1.6%。优选的,所述al的含量为0.03-0.05%。本发明所述高强钢的屈服强度≥550mpa,抗拉强度≥600mpa,且厚度在3-6mm的热轧超高强钢,延伸率≥25%和低温冲击韧性-40℃冲击功≥100j。材料的疲劳性能与晶粒尺寸、夹杂物级别、偏析程度等密切相关。晶粒尺寸越细,疲劳性能越好;夹杂物等级越小,偏析越轻,则疲劳性能越好;钢中析出相的尺寸越大,则疲劳性能越低;反之,析出相尺寸越小,可显著提高疲劳性能。钢的疲劳性能与其抗拉强度有一定的相关性。通常,强度越高,疲劳极限增加,但达到一定强度级别时,疲劳极限不再继续增加,反而有降低的趋势。本发明为保证钢板的高疲劳性能,所述钢板不仅对组织类型和晶粒大小,而且对析出相的平均尺寸和体积分数均进行严格控制。钢板的组织为全铁素体,晶粒呈近等轴形,平均晶粒尺寸约5-10μm;析出相的体积分数为0.104-0.209%,平均析出相尺寸为5-10nm。在其他条件不变的情况下,钢板的疲劳性能主要取决于晶粒尺寸和析出相尺寸及其体积分数。晶粒尺寸和析出相尺寸越小,钢板的疲劳性能越好。这是因为疲劳裂纹通常在表面产生,钢板表面的局部区域发生小的塑性变形,变形产生滑移线。随着疲劳交变载荷的进行,滑移线的宽度和深度逐渐增加,形成滑移带,进而扩展成疲劳裂纹源。当晶粒尺寸和析出相尺寸很小时,由于变形引起的滑移线不容易在晶粒内部形成或者不容易穿过或越过硬的析出相,即难以造成位错塞积;或者,即使位错越过析出相也难以在后续的过程中继续扩展,使得疲劳裂纹不容易形成或者即使形成裂纹源,细小的晶粒和析出相也能够有效地阻止疲劳裂纹的扩展,从而提高了钢板的疲劳性能。在本发明钢的成分设计中:(1)碳是钢中的基本元素,也是本发明中的重要元素之一。碳作为钢中的间隙原子,对提高钢的强度起着非常重要的作用,对钢的屈服强度和抗拉强度影响最大。在本发明中,为了在高温卷取时获得抗拉强度达到600mpa的高强钢,同时又保证组织为全铁素体细晶组织,碳的含量既不能太低也不能太高,碳含量低于0.03%,形成的纳米析出相的数量少,析出强化效果弱,强度达不到600mpa;碳的含量高于0.07%,则高温卷取时组织中会出现少量珠光体,不能获得全铁素体组织。因此,碳含量要控制在合理的范围内,通常应控制在0.03-0.07%,优选范围为0.04-0.06%。(2)硅也是钢中的基本元素,但在本发明中,硅并非关键元素,其在炼钢过程起到部分脱氧的作用。硅在钢中可扩大铁素体形成范围,有利于扩大轧制工艺窗口;同时硅还有较强的固溶强化效果。但硅加入钢中后容易在轧制后的钢板表面形成不均匀分布的“红铁皮”,这些“红铁皮”在随后的酸洗过程中难以彻底去除。虽然带有“红铁皮”的钢板在后续的加工过程中对性能没有不良影响,但在构件的电泳、涂漆过程中,由于钢板表面“红铁皮”去除不彻底,涂漆之后构件表面容易产生色差,影响美观。大量的生产统计结果表明,当钢中硅的含量在0.10%以下时可完全消除“红铁皮”现象,故钢中si的含量控制在≤0.10%。(3)锰是钢中最基本的元素,同时也是本发明中最重要的元素之一。众所周知,mn是扩大奥氏体相区的重要元素,可以降低钢的临界淬火速度,稳定奥氏体,细化晶粒,推迟奥氏体向珠光体的转变。在本发明中,为保证钢板的强度,mn含量一般应控制在1.0%以上,mn含量过低,过冷奥氏体不够稳定,在分段冷却的空冷阶段容易转变为珠光体类型的组织;同时,mn的含量一般也不宜超过1.8%,超过该含量空冷阶段铁素体转变过程延缓,同时也影响析出相的形成。因此,钢中mn的含量一般控制在1.0-1.8%,优选范围在1.3-1.6%。(4)磷是钢中的杂质元素。p极易偏聚到晶界上,钢中p的含量较高(≥0.1%)时,形成fe2p在晶粒周围析出,降低钢的塑性和韧性,故其含量越低越好,为了获得具有高疲劳性能的高强钢,p的含量需要比一般钢种要求更严格。在本发明中,p含量需严格控制在0.01%以内。(5)硫是钢中的杂质元素。钢中的s通常与mn结合形成mns夹杂,尤其是当s和mn的含量均较高时,钢中将形成较多的mns,而mns本身具有一定的塑性,在后续轧制过程中mns沿轧向发生变形,降低钢板的横向拉伸性能。更主要的是,mns作为有一定塑性的大型夹杂物,对钢的疲劳性能影响较大。为了保证钢的疲劳性能,钢中s含量应控制得越低越好,实际生产时通常控制在0.002%以内。(6)铝是钢中除c,si,mn,p,s五大元素之外另一重要合金元素。al在本发明中的基本作用主要是在炼钢过程中脱氧。钢中铝的含量一般不低于0.02%;同时,若铝的含量若超过0.08%,其细化晶粒的作用反而减弱。根据实际生产过程中铝含量的控制水平,将钢中铝的含量控制在0.02-0.08%即可,优选范围为0.03-0.05%。(7)氮在本发明中属于杂质元素,其含量越低越好。n也是钢中不可避免的元素,通常情况下,若在炼钢过程中不进行特殊控制,钢中n的残余含量通常≤0.005%。这些固溶或游离的n元素必须通过形成某种氮化物加以固定,否则游离的氮原子对钢的冲击韧性非常不利,而且在带钢轧制的过程中很容易形成全长性的“锯齿裂”缺陷。由于本发明的目的是获得高疲劳性能的高强钢,而tin属于硬度很高的析出相,且尺寸大,形状为立方形,这种方形的tin与基体界面之间的结合力弱,在外力的作用下,界面处容易产生应力集中,对疲劳性能非常不利。因此,在含有较高ti含量的钢中,为了获得良好的疲劳性能,钢中n的含量必须严格控制,否则形成的大尺寸的tin会严重降低钢的疲劳性能。因此,钢中n含量要控制在0.004%以内,且越低越好。(8)钛是本发明中的重要元素之一。钛与钢中c、n原子有很强的结合力。本发明的成分设计思路主要是想获得细小弥散的纳米析出相而不是氮化物。钛与氮的结合力大于钛与碳之间的结合力,为了尽量减少钢中tin的形成量,钢中氮的含量应控制得越低越好。加入较高含量的钛主要目的是为了在层流冷却的空冷阶段获得细小弥散的相间析出纳米级碳化物,一方面起到析出强化效果,同时还可以显著提高钢的疲劳性能。为了保证钢的强度达到600mpa以上,ti的含量应至少达到0.05%以上,否则加入的ti一部分被n和s结合之后,可用来析出强化的有效ti就会数量不足,对强度贡献小;同时ti的含量也不宜超过0.10%,否则不仅提高了成本,而且还会使钢的强度幅提高,对钢的成形性和冲击韧性不利。因此,钢中ti的含量应控制在0.05-0.10%之间。(9)钼也是本发明中的关键元素之一。钼与碳之间也有较强的结合力,但钼与碳结合形成的碳化物在奥氏体中有很大的固溶度。因此,与钛相比,moc通常大部分在铁素体中析出。但钼与钛相比一个最大的优点是具有良好的高温热稳定性。理论和试验均已证实,单纯添加钛的高强钢中,tic在高温卷取过程中粗化现象比较严重,钢卷缓慢冷却至室温后tic的弥散强化效果会大大减弱。添加一定量的钼元素之后,降低了tic与基体之间的界面能,从而使得(ti,mo)c的粗化过程比单一的tic的粗化过程缓慢得多,因此,(ti,mo)c具有更高的热稳定性。根据试验结果,钼的含量控制在0.10-0.30%之间时,其与钛形成的(ti,mo)c均具有较强的高温热稳定性。(10)氧是炼钢过程中不可避免的元素,对本发明而言,钢中o的含量通过al脱氧之后一般都可以达到30ppm以下,对钢板的性能不会造成明显不利影响。因此,将钢中的o含量控制在30ppm以内即可。本发明所述的600mpa级高疲劳高强钢的制造方法,其包括:转炉或电炉冶炼、真空炉二次精炼、铸造成铸坯或铸锭、再加热、轧制、层流冷却、卷取成钢卷;其中,铸坯或铸锭的再加热温度≥1230℃,保温时间:1~2小时;轧制的开轧温度:1080~1200℃,在1000℃以上3-5道次压下且累计变形量≥50%;随后中间坯待温至900-950℃,然后进行最后3-5个道次轧制且累计变形量≥70%;在800-900℃之间终轧结束后;层流冷却采用以≥100℃/s的冷速将钢板水冷至670-720℃,然后经过3-10s的空冷,在620-670℃卷取后缓慢冷却至室温。本发明通过合理的成分设计,同时配合创新性的热轧工艺可获得强度、塑性、韧性以及疲劳性能优异的600mpa级纳米析出强化高疲劳高强钢。钢板的组织为全铁素体和铁素体晶内相间析出的纳米析出相。在抗拉强度达到600mpa高强度的同时,钢板仍具有≥25%的高延伸率,钢板的-40℃冲击功≥100j,同时还具有优异的疲劳性能。在工艺设计上,采用轧后层流冷却控制技术,即终轧结束后快速冷却至在670-720℃,在该温度区间空冷3-10s,形成铁素体以及铁素体晶内的相间析出,同时伴随着空冷过程,带钢的温度逐渐降低,最终在620-670℃的温度区间进行卷取。虽然在该温度下卷取时通常伴随着铁素体晶粒的长大以及析出相的粗化,但由于mo含量的加入,上述晶粒长大和析出相粗化的过程会大大抑制,从而可以获得这种600mpa级高疲劳高强钢。在卷取之后缓冷的过程中,在670-720℃空冷阶段尚未充分析出的ti和mo原子可以在相对较低的温度区间即620-670℃进一步随机析出。因此,最终铁素体晶内的析出以相间析出为主,同时含有部分随机析出。二者的析出尺寸均非常细小且对高强钢的疲劳性能有显著提高作用。在轧制工艺设计上,为了配合高ti的成分设计,钢坯的加热温度必须足够高(如≥1230℃)以保证有尽可能多的ti原子固溶在板坯中;在粗轧和精轧阶段按照正常轧制节奏完成,避免在粗轧和精轧阶段待温时间过长,防止过多ti的碳氮化物析出。在终轧结束后应以较高冷速(≥100℃/s)快速水冷至670-720℃,在随后的空冷过程中发生铁素体相变,同时伴随着铁素体晶内的相间析出。由于本发明设计思路为全铁素体和铁素体晶内纳米析出相。钢板的高强度来自两方面:一是纳米析出强化,根据经典的orowan机制,纳米析出相对强度的贡献大约在200-400mpa之间。因此,仅有纳米析出强化还不够;钢板的高强度还必须来自于具有一定尺寸的细小铁素体。总体而言,由于钢板的强度相对而言不是特别高,因此,只要铁素体晶粒控制在5-10μm,同时铁素体晶内的相间析出和随机析出的纳米析出相的尺寸控制在5-10nm之间,就可以获得这种强度、塑性、韧性以及疲劳性能优异的600mpa级高疲劳高强钢。对于高ti析出强化类型的高强钢而言,加热温度是一个很重要的工艺参数。与普通高强钢相比,高ti钢更高的加热温度(≥1230℃)主要目的是在加热的板坯中固溶尽可能多的ti原子。由于ti的碳氮化物固溶温度通常很高(≥1300℃),在炼钢或连铸以及轧制过程的不同阶段均会析出,这就使得最终可用来起到析出强化作用的ti含量就很低。因此,必须保证高的加热温度才有可能在最终的卷取过程中获得更多的纳米析出相,故本发明要求钢板的最低加热温度必须≥1230℃;加热温度的上限根据现场加热炉实际可达到的或可承受的温度为限,加热温度原则上不设定上限要求。板坯出炉开始轧制时应保持较快的节奏进行轧制,以尽量减少在粗轧和精轧阶段ti的析出。这是因为在粗轧尤其是精轧处于奥氏体区,在此温度区间析出的ti的碳化物或碳氮化物尺寸大多在几十微米,对最终的析出强化效果不大。因此,粗轧和精轧阶段应尽快完成以保留更多的ti原子在空冷和卷取过程中析出。对于高ti钢而言,板坯的加热时间相对于加热温度而言,其影响要小得多。理论上而言,只要加热温度达到ti的碳氮化物的平衡溶解温度,其溶解速度较快。故在这一阶段,加热时间主要是以保证板坯能够均匀的“烧透”为主要目标。当然,加热时间也不能太长,否则高温未溶解的ti的碳氮化物极有可能发生粗化和长大,这些粗大的ti的碳氮化物在奥氏体晶界处析出,降低了晶界的结合强度,容易在加热过程中板坯在加热炉中发生“断坯”现象。因此,根据板坯厚度不同,板坯到温之后的均热时间控制在1~2小时即可。本发明的有益效果:本发明方法可用于制造屈服强度≥550mpa,抗拉强度≥600mpa,且厚度在3-6mm的热轧超高强钢,同时且具有良好的延伸率(≥25%)和低温冲击韧性(-40℃冲击功≥100j),表现出优异的强度、塑性和韧性匹配,由此带来以下两个方面的有益效果:(1)采用相对经济的成分设计思路,同时配合现有的热连轧产线就可以生产出具有高强度、高韧性、高延伸率以及高疲劳的纳米析出强化先进高强钢;(2)钢板具有优异的高强度和塑性匹配。可应用于汽车底盘、大梁、车轮、桥壳等需要高强减薄的地方,具有广阔的应用前景。附图说明图1为本发明钢的制造工艺流程图。图2为本发明实施例1钢的典型金相照片。图3为本发明实施例3钢的典型金相照片。图4为本发明实施例5钢的典型金相照片。图5为本发明实施例实施例3钢典型tem照片(相间析出)。图6为本发明实施例实施例3钢典型tem照片(随机析出)。图7为本发明实施例3钢在拉-拉(应力比为0.1)条件下的s-n疲劳曲线。具体实施方式下面结合实施例和附图对本发明做进一步说明。参见图1,本发明所述的600mpa级高疲劳高强钢的制造方法,其包括:转炉或电炉冶炼、真空炉二次精炼、铸造成铸坯或铸锭、再加热、轧制、层流冷却、卷取成钢卷;其中,铸坯或铸锭的再加热温度≥1230℃,保温时间:1~2小时;轧制的开轧温度:1080~1200℃,在1000℃以上3-5道次压下且累计变形量≥50%;随后中间坯待温至900-950℃,然后进行最后3-5个道次轧制且累计变形量≥70%;在800-900℃之间终轧结束后;层流冷却采用以≥100℃/s的冷速将钢板水冷至670-720℃,然后经过3-10s的空冷,在620-670℃卷取后缓慢冷却至室温。本发明实施例成分件表1,表2为本发明钢轧制工艺,钢坯厚度120mm,表3为本发明实施例钢板的力学性能。图2-图4给出了本发明实施例1、3、5钢的典型金相照片。从金相照片上可以清楚地看出,钢板的显微组织为全铁素体,铁素体晶粒平均尺寸约为6-8μm。图5、图6给出了实施例3铁素体中存在的两种典型的纳米析出相,一种为高温空冷阶段形成的相间析出,另一种为卷取之后形成的随机析出。通过对两种析出相的尺寸进行粗略分析可知,析出相的平均尺寸大约为5-8nm,部分相对粗化的析出相可达到10nm。正是由于这种细小的铁素体组织和铁素体晶内析出的细小的纳米级碳化物赋予了钢板优异的强度、塑性、韧性以及高疲劳性能。图7给出了实施例3钢在拉-拉条件下的高周疲劳s-n曲线,从图中可以看出,本发明实施例钢具有非常优异的疲劳性能,其疲劳极限可达660mpa。表1单位:重量百分比实施例csimnpsalntimoo10.050.021.50.0090.00100.050.00350.070.150.002620.070.011.70.0080.00180.060.00260.050.120.002530.040.051.40.0080.00140.040.00240.080.170.002740.060.081.60.0090.00160.030.00310.100.200.002450.030.061.80.0070.00150.080.00280.090.190.0029表2表3当前第1页12