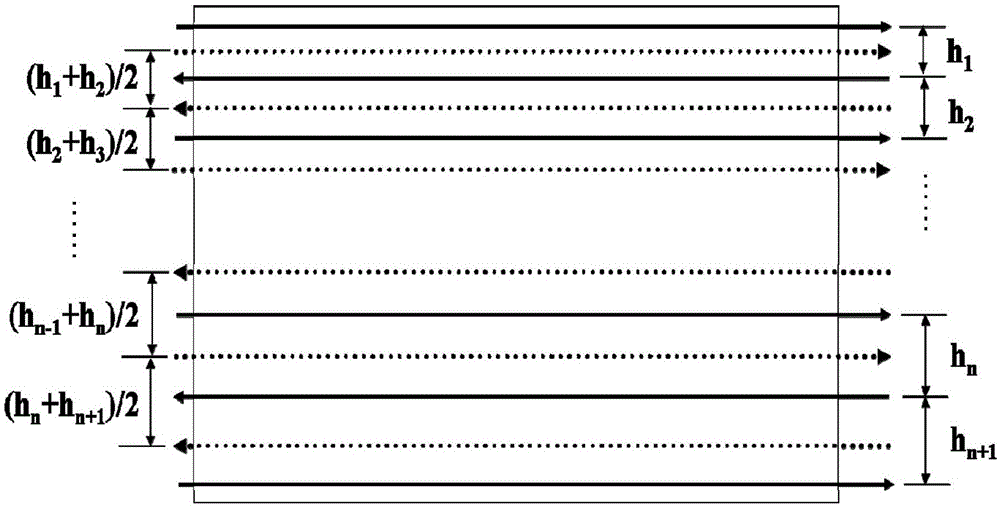
本发明属于材料表面处理
技术领域:
,且特别涉及一种微波吸收涂层及其制备方法。
背景技术:
:微波是指频率为300mhz-300ghz,波长在0.1mm-1m米之间的电磁波,其频率比一般的无线电波频率高。微波最重要应用是雷达和通信,还可广泛的应用于加热、遥感、工业生产、农业科学、生物学、医学等诸多领域。特别的,高功率高频率的微波有望应用于核聚变反应堆,如托卡马克装置(tokamak)的离子回旋加热系统或电子回旋加热系统内,用于制造并加热等离子体,这种等离子体受到超导磁体的挤压,进而发生聚变。然而,在高强度或长时间的微波辐射下,会严重危害人类的身体健康和其他生物体的生存环境,也会对附近的电子器件与电子设备的服役稳定性构成威胁。因此,必须减少微波引起的干扰和污染。微波吸收的基本原理是通过某种物理作用机制将微波能转化为其他形式运动的能量,并通过该运动的耗散作用而转化为热能。理想的微波吸收材料,必须具有强吸收、宽频、轻质和良好环境适应性等特点。微波吸收材料按工作原理可分为干涉型和吸收型微波吸收材料。干涉型微波吸收材料以电磁波的干涉为主,在中心频率点上入射电磁波和反射电磁波相位相反而相互抵消,但因有效频率范围较窄而限制了进一步的应用。吸收型微波吸收材料又可分为电损型和磁损型两类。通常,电损型材料吸收高频率的效果较好;而磁损型材料吸收低频更有效,且高功率高频率微波的服役环境温度容易快速升高,而绝大部分磁损型吸波材料居里温度较低,导致在高温下失去磁性,从而失去吸波性能。因此,高温服役环境中的吸波材料多采用陶瓷材料,并通过介电损耗来吸收微波。在核聚变反应堆内,吸波材料吸收微波后所产生的热量还可通过水冷结构去除,再将热量转移至热交换器,形成蒸气后进行回收利用。目前广泛研究和应用的微波吸收材料主要应用于军事装备领域,如飞机、导弹、舰船等,用于吸收和衰减雷达波,并通过与目标外形设计相结合,从而起到隐身作用。然而,微波吸收材料的研究依然主要面向传统吸波材料为主,其吸收频段范围一般是从0.72ghz到40ghz。对于新型吸波材料的研究开发仍存不足,特别是面向诸如核聚变反应堆内的高功率高频率的微波吸收材料及制备方法的关注较少。技术实现要素:本发明的目的之一包括提供一种微波吸收涂层,该微波吸收涂层中陶瓷工作层的结构致密,厚度呈梯度变化,耐环境性好。微波吸收涂层不仅对高功率和高频率(100-170ghz)的微波具有良好的吸收效果,而且还具有优异的抗高温氧化和耐腐蚀性能。本发明的目的之二包括提供一种上述微波吸收涂层的制备方法,该方法简单可靠,制备效率高,生产成本低,对环境污染小。本发明解决其技术问题是采用以下技术方案来实现的:本发明实施例提出了一种微波吸收涂层,微波吸收涂层包括金属粘结层和陶瓷工作层。陶瓷工作层覆盖于金属粘结层的一侧;金属粘结层的远离陶瓷工作层的一侧用于覆盖于基体的表面。金属粘结层的制备原料包括nial或nicr,和/或陶瓷工作层的制备原料包括cr2o3。优选地,金属粘结层的厚度为80-150μm,和/或陶瓷工作层的厚度为100-500μm。优选地,陶瓷工作层的厚度由陶瓷工作层的第一侧到与第一侧相对的第二侧逐渐增大或缩小。更优选地,增大或缩小均呈均匀梯度变化。本发明还提出了一种上述微波吸收涂层的制备方法,包括以下步骤:分别采用不同的超音速等离子喷涂条件喷涂金属粘结层和陶瓷工作层;金属粘结层用于喷涂于基体的表面,陶瓷工作层用于喷涂于金属粘结层的远离与基体接触的一侧的表面。本发明实施例中微波吸收涂层及其制备方法的有益效果包括:本发明较佳实施例提供的微波吸收涂层中陶瓷工作层的结构致密,厚度呈梯度分布,耐环境性好,不仅对高功率高频率的微波具有良好的吸收效果,还具有优异的抗高温氧化和耐腐蚀性能。其制备方法简单可靠,制备效率高,生产成本低,对环境污染小。附图说明为了更清楚地说明本发明实施例的技术方案,下面将对实施例中所需要使用的附图作简单地介绍,应当理解,以下附图仅示出了本发明的某些实施例,因此不应被看作是对范围的限定,对于本领域普通技术人员来讲,在不付出创造性劳动的前提下,还可以根据这些附图获得其他相关的附图。图1为本申请提供的超音速等离子喷涂的微波吸收涂层喷涂搭接距离变化示意图,其中,黑色实线为奇数次喷涂轨迹,hn+1>hn>……>h2>h1;黑色虚线为偶数次喷涂轨迹;图2为本申请提供的超音速等离子喷涂的微波吸收涂层喷枪移动速度变化示意图,其中:v2=v1+at,v1为初速度,a为加速度,t为时间;图3为本申请实施例1提供的微波吸收涂层的结构示意图;图4为实施例1制备所得的微波吸收涂层的陶瓷工作层的截面形貌图。图标:10-微波吸收涂层;11-基体;12-金属粘结层;13-陶瓷工作层。具体实施方式为使本发明实施例的目的、技术方案和优点更加清楚,下面将对本发明实施例中的技术方案进行清楚、完整地描述。实施例中未注明具体条件者,按照常规条件或制造商建议的条件进行。所用试剂或仪器未注明生产厂商者,均为可以通过市售购买获得的常规产品。以下对本申请技术方案进行详细说明。本申请涉及的微波吸收涂层包括金属粘结层和陶瓷工作层。陶瓷工作层覆盖于金属粘结层的一侧。金属粘结层的远离陶瓷工作层的一侧用于覆盖于基体的表面。作为可选地,金属粘结层覆盖的基体的材质可以为不锈钢或无氧铜,其中,不锈钢例如可以为304或316等不锈钢,无氧铜例如可以为tu1或tu2等无氧铜。本申请中,金属粘结层的制备原料可以包括nial或nicr,上述两种原料的热膨胀系数介于基体与陶瓷工作层之间,在喷涂陶瓷层之前先喷涂一层金属粘结层,有利于改善陶瓷工作层与基体之间的结合强度,避免由于陶瓷涂层的热物理性能和力学性能与金属基体存在着较大的差异而在喷涂过程中产生大的热应力。优选地,包覆型nial粉末在喷涂过程中的放热反应可显著增强涂层结合强度且具有较好的抗氧化性,适宜于在较高温度环境中长时稳定的工作;nicr合金粉末所制备粘结层则兼具优异的抗高温氧化性能及耐腐蚀性能。陶瓷工作层的制备原料例如可以包括cr2o3。将cr2o3作为陶瓷工作层的原料,能使微波能快速转化为热能,其原因可能在于cr2o3具备较高的介质损耗因数,且密度较小,其力学性能、高温稳定性和耐化学腐蚀性能优良,具有其他微波介质损耗材料(如铁氧体或复合金属粉末)无法相比的耐环境性,具有在较高服役温度下成为面向高功率高频率(100-170ghz)微波吸收涂层的应用前景。本申请中,金属粘结层的厚度可以为80-150μm,例如80μm、90μm、100μm、110μm、120μm、130μm、140μm或150μm,也可以为85μm、95μm、105μm、115μm、125μm、135μm或145μm。当然,也可以为80-150μm范围内的任一厚度值。陶瓷工作层的厚度可以为100-500μm。值得说明的是,本申请中陶瓷工作层的厚度并非为等厚,其厚度是由陶瓷工作层的第一侧到与第一侧相对的第二侧逐渐增大或缩小,也即陶瓷工作层远离金属粘结层的一侧的表面到金属粘结层的距离由陶瓷工作层的一侧到与其相对的另一侧逐渐增大或缩小;除此之外,也可以理解为陶瓷工作层的远离金属粘结层的一侧的表面是倾斜设置的。在一些优选的实施方式中,陶瓷工作层厚度的增大或缩小均呈均匀梯度变化。通过涂层厚度渐变(呈均匀梯度变化)可调节吸波层阻抗,以使空间入射来的微波尽可能多地进入吸波材料而被损耗吸收,大大提高涂层的微波吸收率。本申请中,陶瓷工作层的孔隙率小于2%。作为可选地,陶瓷工作层的孔隙率可以为0.8-1.8%,例如0.8%、0.95%、1.4%或1.8%。此外,陶瓷工作层的孔隙率也可以小于0.8%。值得说明的是,孔隙率可表征陶瓷工作层的致密度,涂层越致密,其微波吸收性能越强。本申请还提供了一种上述微波吸收涂层的制备方法,可包括如下步骤:分别采用不同的超音速等离子喷涂条件喷涂金属粘结层和陶瓷工作层。金属粘结层用于喷涂于基体的表面,陶瓷工作层用于喷涂于金属粘结层的远离与基体接触的一侧的表面。在将金属粘结层喷涂于基体前,还可将基体依次进行脱脂除油、喷砂及预热处理。脱油例如可以用汽油或丙酮进行脱脂除油,然后用酒精清洗,再进行喷砂处理,以使基体的粗糙度ra>3μm。将上述经喷砂的基体置于与喷枪垂直的位置,在未送粉条件下利用喷枪射流对基体进行预热处理。值得说明的是,本申请采用的脱脂除油、喷砂及预热处理均为本
技术领域:
的通用技术,具体的处理参数本发明对其不做限定。本申请采用超音速等离子喷涂以制备金属粘结层和陶瓷工作层,其主要是利用“非转移型”等离子弧与高速气流混合时出现的“扩展弧”得到稳定聚集的超音速等离子射流,该方法保留了常规大气等离子喷涂射流温度高、材料适应性广等优点,并且喷涂速度有显著提高,在大气环境下即可高效制备均匀致密的陶瓷涂层。同时,采用超音速等离子喷涂方法还能够避免采用以下方式所存在的问题:超音速火焰喷涂射流温度相对较低,陶瓷粉末在喷涂过程中不易发生熔化;低压等离子喷涂在真空室内进行,效率较低、成本较高,且难以喷涂大尺寸复杂工件;大气等离子喷涂制备的涂层孔隙率高而影响到涂层的致密度。在一些实施方式中,金属粘结层的超音速等离子喷涂条件可以包括:喷涂电流为160-220a,压缩空气压力为0.25-0.40mpa,送粉速率为20-40g/min,喷距为150-220mm,喷枪移动速度为800-1200mm/s,喷涂搭接距离为6-8mm。具体地,喷涂电流可以为160a、170a、180a、190a、200a、210a或220a等,也可以为165a、175a、185a、195a、205a或215a等,也可以为160-220a中的任一电流值。压缩空气压力可以为0.25mpa、0.28mpa、0.3mpa、0.32mpa、0.35mpa、0.38mpa或0.4mpa等,也可以为0.25-0.40mpa中的任一压力值。送粉速率可以为20g/min、22g/min、25g/min、28g/min、30g/min、32g/min、35g/min、38g/min或40g/min等,也可以为20-40g/min中的任一速率值。喷距可以为150mm、160mm、170mm、180mm、190mm、200mm、210mm或220mm等,也可以为155a、165a、175a、185a、195a、205mm或215mm等,也可以为150-220mm中的任一距离值。喷枪移动速度可以为800mm/s、900mm/s、1000mm/s、1100mm/s或1200mm/s等,也可以为850mm/s、950mm/s、1050mm/s或1150mm/s等,也可以为800-1200mm/s中的任一速度值。搭接距离可以为6mm、6.5mm、7mm、7.5mm或8mm等,也可以为6-8mm中任一距离值。在一些实施方式中,陶瓷工作层的超音速等离子喷涂条件可以包括:喷涂电流为250-350a,压缩空气压力为0.35-0.50mpa,丙烷流量为1-3l/min,送粉速率为30-60g/min,喷距为150-250mm,喷枪移动速度为300-1200mm/s,喷涂搭接距离为4-10mm。具体地,喷涂电流可以为250a、260a、270a、280a、290a、300a、310a、320a、330a、340a或350a等,也可以为255a、265a、275a、285a、295a、305a、315a、325a、335a或345a等,也可以为250-350a中的任一电流值。压缩空气压力可以为0.35mpa、0.38mpa、0.4mpa、0.42mpa、0.45mpa、0.48mpa或0.5mpa等,也可以为0.35-0.50mpa中的任一压力值。丙烷流量可以为1l/min、1.5l/min、2l/min、2.5l/min或3l/min等,也可以为1-3l/min中的任一流量值。送粉速率可以为30g/min、35g/min、40g/min、45g/min、50g/min、55g/min或60g/min等,也可以为30-60g/min中的任一速率值。喷距可以为150mm、160mm、170mm、180mm、190mm、200mm、210mm、220mm、230mm、240mm或250mm等,也可以为155a、165a、175a、185a、195a、205mm、215mm、225mm、235mm或245mm等,也可以为150-250mm中的任一距离值。喷枪移动速度可以为300mm/s、500mm/s、700mm/s、900mm/s或1100mm/s等,也可以为400mm/s、600mm/s、800mm/s、1000mm/s或1200mm/s等,也可以为300-1200mm/s中的任一速度值。搭接距离可以为4mm、4.5mm、5mm、5.5mm、6mm、6.5mm、7mm、7.5mm、8mm、8.5mm、9mm、9.5mm或10mm等,也可以为4-10mm中任一距离值。喷涂过程中,采用压缩空气作为等离子工作气体一方面可有效降低运行成本;另一方面,在喷涂陶瓷粉末时,丙烷作为等离子工作气体的加入可以进一步提高焰流温度和速度,保证粉末充分熔融。承上,金属粘结层和陶瓷工作层均采用同一设备进行超音速等离子喷涂制备,可提高喷涂效率;超音速等离子喷涂方法采用等离子体为热源,其功率比常规大气等离子喷涂更高,射流可达到超音速状态,且射流中心与边缘速度、温度梯度极低,在较大送粉量时仍可保证送入射流中的粉末充分熔融,并在碰撞到基体或已沉积涂层之前具备较高的飞行速度,以保证涂层具备致密的结构。超音速等离子喷涂采用压缩空气作为等离子工作气,且气体流量较低,可有效降低运行成本;工作过程中在射流中注入丙烷,可以进一步提高射流温度和速度,提高涂层质量。本申请中,实现陶瓷工作层的厚度梯度变化可采用以下两种方式。第一种方法是在喷枪移动速度及其它喷涂参数一致的前提下,逐渐线性的增加各喷涂搭接之间的距离,如图1所示,黑色实线表示奇数次走枪轨迹,喷涂搭接距离逐渐增加,其中hn+1>hn>……>h2>h1。黑色虚线表示偶数次走枪轨迹,由于喷涂射流有效沉积区间的局限,为保证涂层表面的粗糙度,在基体表面需喷涂部位完成一次喷涂后进行二次喷涂时,喷枪位置移动至上一次喷涂相邻两条轨迹的中心位置,即喷涂搭接距离依次变为(h1+h2)/2,(h2+h3)/2,……(hn+hn+1)/2。如此循环,可保证涂层表面不出现高低起伏不平的现象。另一种方法是,在喷涂搭接距离及其它喷涂参数均一致的前提下,喷涂过程中,同一喷涂道次(此处也即同一喷涂直线轨迹),喷枪移动速度以恒定的加速度由快减慢做匀减速运动或由慢加快做匀加速运动,并在下一喷涂道次时与上一喷涂道次保持相同的匀减速运动或匀加速运动规律。示意图如图2所示。比如,可将基体固定,喷枪从左到右水平移动过程中,速度以恒定的加速度a由速度v1匀加速到v2,喷枪向下移动搭接距离h,喷枪由右到做移动,其速度由v2匀减速到v1,如此循环,所制备涂层厚度由左向右均匀降低。类似的,喷枪移动方向也可以由上向下再由下而上返回,喷枪移动速度以恒定加速度进行匀变速运动,也可实现涂层在厚度方向上的梯度分布。在一些实施方式中,陶瓷工作层的喷涂过程中,喷涂搭接距离可由4mm线性增加至10mm或由10mm线性减少至4mm。本申请中,通过在喷涂过程中喷枪在同一喷涂方向上以恒定的加速度做匀加速或匀减速移动,或逐渐改变喷涂搭接距离的方式,可实现工作涂层厚度在平行于基体方向上呈均匀的梯度分布,可有效增强涂层的微波吸收效果。承上,本申请所采用超音速等离子喷涂方法于经除油清洗、喷砂及预热处理的不锈钢或无氧铜基体表面依次喷涂nicr/nial+cr2o3涂层,该方法简单可靠,制备效率高,生产成本低,对环境污染小。所得到的微波吸收涂层具有组织均匀致密、孔隙少、厚度可控和耐环境性好等特点,可满足面向高功率高频率的微波吸收涂层的使用要求。实施例1请参照图3,本实施例提供了一种微波吸收涂层10,该微波吸收涂层10包括金属粘结层12和陶瓷工作层13。陶瓷工作层13覆盖于金属粘结层12的一侧,金属粘结层12的远离陶瓷工作层13的一侧用于覆盖于基体11的表面。该微波吸收涂层10的制备方法包括:(1)将304不锈钢基体11用汽油除油清理,用酒精清洗后进行喷砂粗化,以使基体11的粗糙度大于3μm,将上述经喷砂的基体11置于与喷枪垂直的位置,在未送粉条件下利用喷枪射流对基体11进行预热处理。(2)采用超音速等离子喷涂nicr粘结层:喷涂电流为200a,压缩空气压力为0.30mpa,送粉速率为25g/min,喷距为160mm,喷枪移动速度为800mm/s,喷涂搭接距离为7mm,涂层厚度为95μm。(3)采用超音速等离子喷涂cr2o3工作层:喷涂电流为330a,压缩空气压力为0.40mpa,丙烷流量为1.5l/min,送粉速率为45g/min,喷距为200mm,同一喷涂道次时,喷枪移动速度由左到右以恒定的加速度由400mm/s增加到1000mm/s,喷枪下移搭接距离6mm,再由右到左以恒定的加速度由1000mm/s减少到400mm/s,如此循环,至涂层厚度在200-450μm内梯度变化。实施例2本实施例的微波吸收涂层结构与实施例1相同,其区别在于,制备方法不同,本实施例的制备方法包括:(1)将316不锈钢基体用丙酮除油清理,用酒精清洗后进行喷砂粗化,以使基体的粗糙度大于3μm,将上述经喷砂的基体置于与喷枪垂直的位置,在未送粉条件下利用喷枪射流对基体进行预热处理。(2)采用超音速等离子喷涂nial粘结层:喷涂电流为180a,压缩空气压力为0.35mpa,送粉速率为30g/min,喷距为200mm,喷枪移动速度为1000mm/s,喷涂搭接距离为8mm,涂层厚度为120μm。(3)采用超音速等离子喷涂cr2o3工作层:喷涂电流为335a,压缩空气压力为0.45mpa,丙烷流量为1l/min,送粉速率为50g/min,喷距为210mm,喷枪移动速度为800mm/s,喷涂搭接距离开始为4mm,喷枪每下移1道次,喷涂搭接增加0.2mm,至基体喷涂面完成1次喷涂。第2次喷涂时,喷枪移动轨迹为第1次喷涂时每相邻两条轨迹线的中心处,至基体喷涂面完成全覆盖。如此循环,至涂层厚度在150-300μm内梯度变化。实施例3本实施例的微波吸收涂层结构与实施例1相同,其区别在于,制备方法不同,本实施例的制备方法包括:(1)将tu1无氧铜基体用汽油除油清理,用酒精清洗后进行喷砂粗化,以使基体的粗糙度大于3μm,将上述经喷砂的基体置于与喷枪垂直的位置,在未送粉条件下利用喷枪射流对基体进行预热处理。(2)采用超音速等离子喷涂nial粘结层:喷涂电流为190a,压缩空气压力为0.28mpa,送粉速率为35g/min,喷距为210mm,喷枪移动速度为900mm/s,喷涂搭接距离为6mm,涂层厚度为110μm。(3)采用超音速等离子喷涂cr2o3工作层:喷涂电流为270a,压缩空气压力为0.48mpa,丙烷流量为1l/min,送粉速率为40g/min,喷距为170mm,同一喷涂道次时,喷枪移动速度由上到下以恒定的加速度由350mm/s增加到1050mm/s,喷枪下移搭接距离7mm,再由下到上以恒定的加速度由1050mm/s减少到350mm/s,如此循环,至涂层厚度在180-450μm内梯度变化。实施例4本实施例的微波吸收涂层结构与实施例1相同,其区别在于,制备方法不同,本实施例的制备方法包括:(1)将tu2无氧铜基体用丙酮除油清理,用酒精清洗后进行喷砂粗化,以使基体的粗糙度大于3μm,将上述经喷砂的基体置于与喷枪垂直的位置,在未送粉条件下利用喷枪射流对基体进行预热处理。(2)采用超音速等离子喷涂nicr粘结层:喷涂电流为210a,压缩空气压力为0.32mpa,送粉速率为28g/min,喷距为190mm,喷枪移动速度为1050mm/s,喷涂搭接距离为7mm,涂层厚度为125μm。(3)采用超音速等离子喷涂cr2o3工作层:喷涂电流为310a,压缩空气压力为0.38mpa,丙烷流量为2l/min,送粉速率为50g/min,喷距为230mm,喷枪移动速度为1000mm/s,喷涂搭接距离开始为6mm,喷枪每下移1道次,喷涂搭接增加0.15mm,至基体喷涂面完成1次喷涂。第2次喷涂时,喷枪移动轨迹为第1次喷涂时每相邻两条轨迹线的中心处,至基体喷涂面完成全覆盖。如此循环,至涂层厚度在220-350μm内梯度变化。实施例5本实施例的微波吸收涂层结构与实施例1相同,其区别在于,制备方法不同,本实施例的制备方法包括:(1)将tu1无氧铜基体用汽油除油清理,用酒精清洗后进行喷砂粗化,以使基体的粗糙度大于3μm,将上述经喷砂的基体置于与喷枪垂直的位置,在未送粉条件下利用喷枪射流对基体进行预热处理。(2)采用超音速等离子喷涂nial粘结层:喷涂电流为160a,压缩空气压力为0.25mpa,送粉速率为20g/min,喷距为150mm,喷枪移动速度为1000mm/s,喷涂搭接距离为8mm,涂层厚度为80μm。(3)采用超音速等离子喷涂cr2o3工作层:喷涂电流为250a,压缩空气压力为0.35mpa,丙烷流量为2l/min,送粉速率为30g/min,喷距为150mm,同一喷涂道次时,喷枪移动速度由上到下以恒定的加速度由300mm/s增加到1200mm/s,喷枪下移搭接距离10mm,再由下到上以恒定的加速度由1200mm/s减少到300mm/s,如此循环。实施例6本实施例的微波吸收涂层结构与实施例1相同,其区别在于,制备方法不同,本实施例的制备方法包括:(1)将tu2无氧铜基体用丙酮除油清理,用酒精清洗后进行喷砂粗化,以使基体的粗糙度大于3μm,将上述经喷砂的基体置于与喷枪垂直的位置,在未送粉条件下利用喷枪射流对基体进行预热处理。(2)采用超音速等离子喷涂nicr粘结层:喷涂电流为220a,压缩空气压力为0.4mpa,送粉速率为40g/min,喷距为220mm,喷枪移动速度为1200mm/s,喷涂搭接距离为6mm,涂层厚度为150μm。(3)采用超音速等离子喷涂cr2o3工作层:喷涂电流为350a,压缩空气压力为0.5mpa,丙烷流量为3l/min,送粉速率为60g/min,喷距为250mm,喷枪移动速度为1000mm/s,喷涂搭接距离开始为6mm,喷枪每下移1次,喷涂搭接增加0.15mm,至基体喷涂面完成1次喷涂。第2次喷涂时,喷枪移动轨迹为第1次喷涂时每相邻两条轨迹线的中心处,至基体喷涂面完成全覆盖,如此循环。试验例1以实施例1为例,对所得的微波吸收涂层的陶瓷工作层进行截面形貌分析,其结果如图4所示,由图4可以看出,制备所得的cr2o3涂层截面均匀,结构致密,孔隙率低。试验例2以实施例1-4为例,对所得的各涂层按按astme2109测试涂层的孔隙率。试验结果如表1所示:表1涂层性能表征结果孔隙率(%)实施例10.80实施例21.80实施例31.40实施例40.95此外,按照相同的方法对实施例5和实施例6的陶瓷工作层进行孔隙率测试,其结果显示陶瓷工作层孔隙率<2%。结合表1,可以看出,由本申请提供的制备方法制备而得的微波吸收涂层的陶瓷工作层的孔隙率均小于2%,表明本申请提供的制备方法制备而得的微波吸收涂层组织均匀致密。综上,本申请提供的微波吸收涂层的陶瓷工作层结构致密,厚度呈梯度变化,耐环境性好。微波吸收涂层不仅对高功率高频率的微波具有良好的吸收效果,而且还具有优异的抗高温氧化和耐腐蚀性能。其制备方法简单可靠,制备效率高,生产成本低,对环境污染小,能够保证陶瓷工作层具有致密的结构,可满足较高服役温度下对高功率高频率微波的损耗要求。以上仅为本发明的优选实施例而已,并不用于限制本发明,对于本领域的技术人员来说,本发明可以有各种更改和变化。凡在本发明的精神和原则之内,所作的任何修改、等同替换、改进等,均应包含在本发明的保护范围之内。当前第1页12