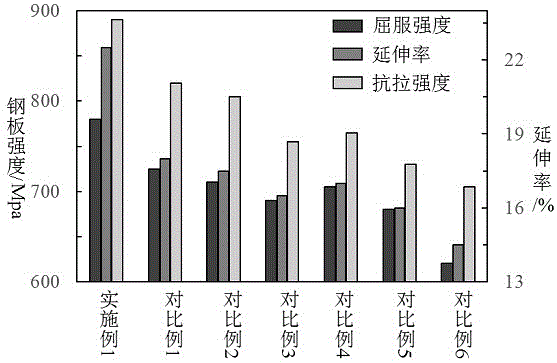
本发明涉及钢铁材料领域,尤其涉及一种高强韧海洋装备钢板。
背景技术:
:为了提高海洋经济的生产效益和海洋资源的应用能力,大量海洋工程装备被应用于海洋资源的勘探和采集。海洋工程装备在服役过程中要面对很多极端的自然环境,同时随着其结构规模越来越庞大,部件的维修以及更换费用很高,深海海工装备对海工钢的强韧性、抗疲劳性、耐腐蚀性、良好的焊接性、抗层状撕裂能力提出了更高的要求。因此,高强韧耐腐蚀钢成为大型海洋工程装备用钢的主要发展方向。目前,主要通过加入各类微合金元素来实现强韧性匹配。其中,ni、mn、c元素主要通过固溶强化的方式提高合金钢的抗拉强度,而mn、ni元素可以扩大奥氏体相区,提高钢中残余奥氏体体积分数,改善材料的低温韧性,但mn含量过高会使轧制和冶炼过程变得困难,过多的ni、mn元素还会导致材料的碳当量较高,恶化材料焊接性。ti、nb、v、cu等作为微量合金元素加入高强钢中,通过形成复杂碳氮化物或团簇,来改善基体的强韧性,tin以及ti的氧化物等形成弥散纳米相的碳氮化物在高温时仍能保持稳定,可抑制奥氏体晶粒长大,通过细晶强化提高强度和韧性。同时,nb、cu等元素能够形成大量直径小于50nm的团簇,通过析出强化作用可以提高合金钢的强度。然而,钢的强度越高环境断裂敏感性越大,特别是在潮湿空气、水介质、有机溶剂等环境中都表现出氢脆敏感性,由于氢脆断裂具有延迟性和突发性,难以通过正常检查程序发现合金构件是否会发生氢脆断裂,所以氢脆断裂带来的危害要比其他断裂造成的危害大得多,严重制约了高强钢在复杂海洋环境中的应用。因此,迫切需要对高强韧钢的组分及含量进行优化设计,并通过合理的合金化、热处理及轧制工艺,以达到最合适的强韧性匹配来满足钢铁材料实际服役环境的性能要求。技术实现要素:本发明的目的就是针对上述存在的缺陷,提供一种高强韧海洋装备用钢,通过常规加入c(碳)、si(硅)、mn(锰)元素,增加钢板强度,通过nb(铌)、v(钒)、ti(钛)微合金化细化晶粒,提高钢板强韧性和冲击韧性,加入ni(镍)元素改善低温冲击韧性和耐腐蚀性能。为了稳定nb、v、ti形成的碳化物,加入mo(钼)元素,同时加入该元素还起到改善点蚀的作用。在以上合金共同作用下,通过合理的化学成分设计以及轧制工艺,从而在保证高强度、高韧性及良好的耐腐蚀性能等要求下,大幅度降低材料氢脆敏感性,此外,还简化了生产工艺、缩短了生产流程,从而降低生产能耗。为实现上述目的,本发明采用的技术方案是:一种高强韧海洋装备用钢板,钢板化学成分按重量百分比包括:c:0.10~0.15%、si:0.31~0.45%、mn:1.35~1.65%、p≤0.02%、s≤0.005%、ni:0.21~0.41%、mo:0.10~0.30%、al:0.015~0.1%、v:0.02~0.08%、nb:0.02~0.10%、ti:0.005~0.05%,余量为fe和不可避免杂质,并满足0.110%≤nb+v+ti≤0.130%。进一步,所述钢板的化学成分按重量百分比包括:c:0.12~0.15%、si:0.31~0.36%、mn:1.25~1.45%、p≤0.01%、s≤0.005%、ni:0.34~0.41%、mo:0.10~0.25%、al:0.022~0.035%、v:0.05~0.08%、nb:0.02~0.05%、ti:0.01~0.03%,余量为fe和不可避免杂质,并满足0.110%≤nb+v+ti≤0.130%。作为优选方案,所述钢板化学成分质量百分比为:c:0.12%,si:0.35%,mn:1.45%,p:0.009%,s:0.003%,ni:0.36%,mo:0.15%,al:0.033%,v:0.062%,nb:0.043%,ti:0.015%,余量为fe及不可避免的杂质。进一步,所述钢板厚度为20-60mm。进一步,所述钢板制造方法包括以下工序:冶炼、铸造、加热、轧制、冷却和堆垛,具体工序条件如下:(1)冶炼、铸造:按所述成分及重量百分比混合均匀熔炼成铁水,将铁水经深脱s处理后,在转炉内加入铁水和废钢,利用转炉吹氧脱c,然后出钢转入钢包,经lf炉精炼及真空脱气处理后铸造成铸坯;(2)加热:将铸坯加热到1215~1245℃,加热速率8~12min/cm,保温段温度为1180~1240℃;(3)轧制:将加热保温后的坯料依次进行再结晶区轧制和未再结晶区轧制,再结晶区轧制开轧温度为1050~1120℃,未再结晶区开轧温度为850~900℃。(4)冷却:轧制后水冷,冷却速率控制在15~30℃/s,终冷温度控制在380~450℃。(5)堆垛:待钢板温度在300~350℃时进行堆垛缓冷,堆冷时间≥24h。进一步,所述钢板制造工序(1)中,铁水深脱s处理时,到站铁水必须扒前渣与扒后渣,保证液面渣层厚度≤20mm,铁水经搅拌脱s,脱s周期≤21min。进一步,所述钢板制造工序(1)中,出钢温度为1650~1710℃,出钢过程中加入含有v和nb元素的合金;出钢完成后吹入惰性气体,惰性气体为氩气或氮气,吹入惰性气体的时间为2-5min。进一步,所述钢板制造工序(1)中,lf炉精炼过程中,进行电加热,并通过前期大功率加热进行扩散脱氧处理,电加热温度控制范围为高于液相线温度60~90℃,达到要求温度后,加入含ti元素的合金。进一步,所述钢板经lf炉精炼后,[n]≤30ppm,[o]≤25ppm,[h]≤1.5ppm。进一步,所述钢板制造工序(1)中,真空脱气处理过程中,采用吹气搅拌或电磁搅拌,其中,吹起搅拌的气体为氩气或氮气;真空脱气处理后,[n]≤10ppm,[o]≤5ppm,[h]≤0.5ppm。有益效果与现有技术相比,本发明提供的一种高强韧海洋装备用钢板,具有如下有益效果:(1)本发明提供的钢板,主要采用nb、v、ti复合微合金化,通过第二相沉淀析出相细化晶粒,提高钢板强韧性和冲击韧性,添加少量的ni改善低温冲击韧性和耐腐蚀性能;加入少量mo,有助于稳定nb、v、ti形成的碳化物,同时还起到改善点蚀的作用。(2)本发明钢板成分及配比设计合理,尤其对nb、v、ti复合微合金含量进行了优化,通过合理的化学成分设计以及控轧控冷工艺,不仅保证了高强度、高韧性及良好的耐腐蚀性能能等要求,还大幅度降低了钢板中h含量,从而降低氢脆敏感性。(3)本发明对钢板的生产工艺进行了简化,缩短了生产流程,从而有助于降低生产能耗。附图说明图1为实施例1及对比例1-6力学性能测试结果;图2为实施例1及对比例1-6耐腐蚀速率测试结果;图3为实施例1及实施例14-17力学性能测试结果。具体实施方式以下将结合附图对本发明各实施例的技术方案进行清楚、完整的描述,显然,所描述的实施例仅仅是本发明的一部分实施例,而不是全部的实施例;基于本发明的实施例,本领域普通技术人员在没有做出创造性劳动的前提下所得到的所有其它实施例,都属于本发明所保护的范围。本发明涉及的一种高强韧海洋装备用钢板厚度范围在20-60mm,钢板化学成分质量百分比为:c:0.10~0.15%、si:0.31~0.45%、mn:1.25~1.65%、p≤0.02%、s≤0.005%、ni:0.21~0.41%、mo:0.10~0.30%、al:0.015~0.055%、v:0.03~0.08%、nb:0.02~0.08%、ti:0.005~0.03%,0.110%≤nb+v+ti≤0.130%,余量为fe和不可避免杂质,所述钢板制造方法包括以下工序:冶炼、铸造、加热、轧制、冷却和堆垛,具体工序条件如下:(1)冶炼、铸造:按所述成分及重量百分比混合均匀熔炼成铁水,将铁水经深脱s处理后,在转炉内加入铁水和废钢,利用转炉吹氧脱c,然后出钢转入钢包,经lf炉精炼及真空脱气处理后铸造成铸坯;(2)加热:将铸坯加热到1215~1245℃,加热速率8~12min/cm,保温段温度为1180~1240℃;(3)轧制:将加热保温后的坯料依次进行再结晶区轧制和未再结晶区轧制,再结晶区轧制开轧温度为1050~1120℃,未再结晶区开轧温度为850~900℃。(4)冷却:轧制后水冷,冷却速率控制在15~30℃/s,终冷温度控制在380~450℃。(5)堆垛:待钢板温度在300~350℃时进行堆垛缓冷,堆冷时间≥24h。本发明中各元素的作用:c是最基本最经济的强化元素,随着碳含量的增加,钢的抗拉强度和屈服强度随之提高,但延伸率和冲击韧性下降,当c含量高于0.19%时,延伸率、冲击韧性和耐腐蚀性能下降明显,在本发明中,为了确保钢的耐大气腐蚀和焊接性能,故将其范围严格控制在0.10%~0.15%范围内。p、s是钢中难以避免的有害杂质元素。高p会导致偏析,影响钢组织均匀性,降低钢的塑性;s易形成硫化物夹杂对低温韧性不利,且会造成性能的各向异性,同时严重影响钢的应变时效。因此,应严格限制钢中的p、s含量,本发明p控制在≤0.02%,s控制在≤0.005%。si的脱氧能力较强,是炼钢时常用的脱氧剂,硅还能够增大钢液的流动性,所以一般钢中都含硅;硅还能阻止渗碳体的形成,延缓钢中回火马氏体的脆性温度范围,使淬火钢能够在较高的温度下进行回火。si可以固溶强化形式提高钢的强度,当si含量低于0.31%时,钢强度性能偏低,当si含量高于0.45%时,钢的韧性下降。因此,本发明将硅含量控制在在0.31%~0.45%范围之内。al通常作为钢中的脱氧剂。但al含量低于0.015%时,脱氧不充分,当als含量高于0.055%时,氧化铝夹杂物增加,降低钢的洁净度。因此,本发明al选择在0.015~0.055%。mn是作为脱氧除硫的元素加入到碳钢中的,在冶炼过程中用强脱氧剂硅与铝来脱氧时,锰可以同时增强硅与铝的脱氧效果;锰也是碳化物的形成元素,锰的碳化物能够溶入渗碳体,从而间接地增强珠光体的强度;mn还是重要的强韧化元素,随着mn含量的增加,钢的强度明显增加。mn含量低于1.25%时,发明钢强度性能较低,当mn含量高于1.65%时,钢中偏析会较明显,影响耐蚀性能。因此,本发明mn选择在1.25~1.65%。mo是低合金钢中十分有用的元素,可固溶于铁素体、奥氏体和碳化物中,能够改善钢的淬透性,使较大断面的机件能够淬深、淬透,mo还可以增加钢的回火稳定性,使机件能够在较高的温度下进行回火,从而更加有效的降低或者消除残余应力,进而提高其塑性,同时增强其热硬性进而增加钢的强度。在本发明中,mo的加入是为了提高碳化物的稳定性,从而保证钢的强度,且加入mo还可以改善钢的耐点蚀性能。当mo含量低于于0.10时;钢板强度偏低,耐点蚀效果差;当mo含量高于0.30时,钢板低温韧性恶化明显。因此,本发明含量mo控制在0.10~0.30%ni是碳化物形成元素,能够显著提高钢的回火稳定性,使钢在回火过程中析出的碳化物更加均匀、细小和稳定进而提高钢的强度;ni能改变碳钢中位错的滑移特点,使位错容易绕过某些障碍,阻碍应力集中,使钢不易发生解理断裂;同时镍能够提高碳钢的基体层错能,使螺位错便于发生交叉滑移,进而提高钢的韧性。镍是一种只会进入铁素体相的合金元素,使a/p相变温度下降到较低的温度,致使珠光体中的渗碳体难以长大聚集,因此碳化物具备较高的弥散度,导致退火硬度不易降低,所以含镍量不宜过大。因此,本发明将ni含量限定在0.21%~41%的范围之内。nb具有细晶强化作用和沉淀强化作用,在热加工工艺过程中,铌的碳化物、氮化物或碳氮化物可在热轧过程中从奥氏体中析出,或在相变过程在相界析出,或在最终冷却过程中从过饱和铁素体中析出。但由于奥氏体中的析出相降低了微合金元素的固溶量,使得随后在铁素体中的析出相减少,所以也影响了屈服强度。考虑到合金强化效果,本发明将其含量控制在0.02%~0.08%。nb、v、ti具有晶粒细化作用,可提高钢板强度的同时改善钢板的延伸率、低温韧性等性能。钛的加入也更加容易形成v(c、n)质点、nb(c、n)质点和ti(c、n)质点,从而促进v、nb和ti的析出,能够更加充分的发挥钒和铌的沉淀强化和晶粒细化作用,以提高钢的综合力学性能,在同等力学性能的前提下,可减少钒和铌的使用量。当nb、v、ti低于相应的最低值时,细化晶粒效果较差;当nb、v、ti高于相应的最高值时,会使钢板韧性恶化;因此,本发明nb选择在0.02~0.08%,v选择在0.03~0.08%,ti选择在0.005~0.05%。优选地,钢板厚度规格为60mm,化学成分按重量百分比包括:c:0.12~0.15%、si:0.31~0.36%、mn:1.25~1.45%、p≤0.01%、s≤0.005%、ni:0.34~0.41%、mo:0.10~0.25%、al:0.022~0.035%、v:0.05~0.08%、nb:0.02~0.05%、ti:0.01~0.03%,余量为fe和不可避免杂质,并满足0.110%≤nb+v+ti≤0.130%。优选地,钢板厚度规格为60mm,钢板化学成分质量百分比为:c:0.12%,si:0.35%,mn:1.45%,p:0.009%,s:0.003%,ni:0.36%,mo:0.15%,al:0.033%,v:0.062%,nb:0.043%,ti:0.015%,余量为fe及不可避免的杂质。本发明对钢板进行常温拉伸试验,通过测试钢板屈服强度、抗拉强度及延伸率来表征钢板强度和韧性,通过周期浸润腐蚀试验表征钢板耐腐蚀性能。实施例1钢板厚度规格为60mm,钢板化学成分质量百分比为:c:0.12%,si:0.35%,mn:1.45%,p:0.009%,s:0.003%,ni:0.36%,mo:0.15%,al:0.033%,v:0.062%,nb:0.043%,ti:0.015%,余量为fe及不可避免的杂质,nb+v+ti=0.120%,制造工序如下:(1)冶炼、铸造:按所述成分及重量百分比混合均匀熔炼成铁水,将铁水经深脱s处理,并进行搅拌脱硫,脱硫周期为21min、脱硫温降20℃,脱硫后的铁水按质量百分比含s含量为0.003%;然后进行转炉冶炼铁水,在转炉内加入铁水和废钢,利用转炉吹氧脱c,然后出钢转入钢包,出钢温度1680℃,出钢过程中加入含有v和nb元素的合金;出钢完成后吹入惰性气体,吹入惰性气体的时间为2min;然后进行lf炉精炼,进行电加热,并通过前期大功率加热进行扩散脱氧处理,电加热温度为高于液相线温度60~90℃,达到要求温度后,加入含ti元素的合金;然后再进行真空脱气处理,真空脱气处理过程中,采用电磁搅拌搅拌,真空脱气处理后,[n]=8ppm,[o]=3ppm,[h]=0.3ppm,然后铸造成铸坯;(2)加热:将铸坯加热到1230℃,加热速率8min/cm,保温段温度为1200℃;(3)轧制:将加热保温后的坯料依次进行再结晶区轧制和未再结晶区轧制,再结晶区轧制开轧温度为1090℃,未再结晶区开轧温度为860℃。(4)冷却:轧制后水冷,冷却速率控制在18℃/s,终冷温度控制在400℃。(5)堆垛:待钢板温度在320℃时进行堆垛缓冷,堆冷时间为24h。实施例2-13实施例2-13提供一种高强韧海洋装备用钢板,与实施例1相比,不同之处在于,钢板化学成分按质量百分比如表1所示,其他均与实施例1相同。表1实施例2-13的化学成分质量百分比实施例14-17实施例14-17提供的一种高强韧海洋装备用钢板,与实施例1相比,不同之处在于,实施例14-17的钢板厚度依次为20mm、30mm、40mm和50mm。实施例18-29实施例13-18提供的一种高强韧海洋装备用钢板,与实施例1相比,不同之处在于,步骤(2)中,钢板制造工艺参数如表2所示,其他均与实施例1相同。表2实施例18-29主要工艺参数实施例30-38实施例30-38提供的一种高强韧海洋装备用钢板,与实施例1相比,不同之处在于,步骤(3)中,钢板制造工艺参数如表3所示,其他均与实施例1相同。表3实施例30-38主要工艺参数实施例再结晶区轧制温度(℃)未再结晶区轧制温度(℃)301030840311050850321070870331120900341140910351090850361090880371090890381090900实施例39-47实施例39-47提供的一种高强韧海洋装备用钢板,与实施例1相比,不同之处在于,步骤(4)中,钢板制造工艺参数如表4所示,其他均与实施例1相同。表4实施例39-47主要工艺参数实施例48-53实施例48-53提供的一种高强韧海洋装备用钢板,与实施例1相比,不同之处在于,步骤(5)中,钢板制造工艺参数如表5所示,其他均与实施例1相同。表5实施例48-53主要工艺参数实施例堆冷温度(℃)堆冷时间(h)482802449300245032020513302452350245336524对比例1-6对比例1-6提供的一种高强韧海洋装备用钢板,与实施例1相比,不同之处在于,钢板化学成分按质量百分比如表6所示,其他均与实施例1相同。表6对比例1-6主要工艺参数表7实施例1-13及对比例1-6力学性能和耐腐蚀性能表7为实施例1-13及对比例1-6力学性能和耐腐蚀性能测试结果,图1及图2分别为实施例1及对比例1-6的测试结果。可以看出,当钢板化学成分质量百分比在本发明限定范围内时,钢板屈服强度在760-790mpa之间,抗拉强度在870-890mp之间,延伸率≥20.0%,耐腐蚀速率低于1.33g/m2·h,说明钢板具有良好的强度和韧性以及耐腐蚀性;其中,实施例9~13钢板化学成分质量百分比在优选范围内,性能更优。对比例1和2的nb、v和ti及三者之和均在限定范围内,其他元素均在限定范围外,钢板屈服强度、抗拉强度及延伸率均有降低,腐蚀速率明显增大;对比例3和4所有元素含量都在限定范围外,但nb、v和ti之和在限定范围内,钢板屈服强度、抗拉强度及延伸率均有降低,且降低量比对比例1和2更多,腐蚀速率也更大;对比例5和6所有元素均在范围内,但nb、v和ti之和在限定范围外,钢板屈服强度、抗拉强度及延伸率降低最明显,尤其是当nb、v和ti之和明显低于限定值时,力学性能最差。由此说明,合理的成分配比,对钢板力学性的提高能至关重要。图3为实施例14-17钢板力学性能测试结果,可以看出,钢板力学性能随厚度增加而增加,考虑到加工工艺及钢板实际应用,本发明提供的钢板适合高强韧中厚板的制造,具体根据实际需求确定钢板厚度。表8实施例18-29力学性能和耐腐蚀性能实施例屈服强度/mpa抗拉强度/mpa延伸率/%腐蚀速率(g/m2·h)1873584018.51.661975586021.01.452076085521.51.322172083018.01.712276587019.51.292377588521.51.152478589022.00.922577087521.01.142677087520.01.052778088521.51.102878589023.00.932977587521.51.12表8为实施例18-29钢板力学性能及耐腐蚀性能测试结果,从实施例18-21测试结果可以看出,当铸坯温度低于或高于设定温度范围时,钢板力学性能及耐腐蚀性能均下降;从实施例18-29测试结果可以看出,加热速率对钢板性能和耐腐蚀性能影响不大,随着铸坯温度升高,钢板强度和韧性及耐腐蚀性先升高后降低,因此,适宜的铸坯温度有助于钢板力学性能和耐腐蚀性能的提高。表9实施例30-38力学性能和耐腐蚀性能表9为实施例30-38钢板力学性能和耐腐蚀性能测试结果,从实施例30-34测试结果可以看出,再结晶区轧制温度和未再结晶区轧制温度高于或低于限定范围时,钢板力学性能及耐腐蚀性均变差,从实施例30-38测试结果可以看出,钢板力学性能随轧制温度的升高先升高,后变化不大,超过温度设定范围就会降低,耐腐蚀性能具有相同变化趋势。表10实施例39-47力学性能和耐腐蚀性能实施例屈服强度/mpa抗拉强度/mpa延伸率/%腐蚀速率(g/m2·h)3973083516.51.734076086520.51.334177587521.01.254278088522.51.124377087021.51.274477088021.51.234577588522.01.184678589022.51.094778088521.51.12表10为实施例39-47钢板力学性能及耐腐蚀性能测试结果,从实施例39-43可以看出,冷却速率过低时,钢板力学性能及耐腐蚀性能明显较低,这是因为较高的冷却速率使得奥氏体/铁素体相变开始温度降低,因而析出相更加细小,而且,随着冷却速率的增加,晶粒尺寸会不断减小,有助于增强钢板强度及耐腐蚀性;从实施例44-47可以看出,终冷温度对钢板力学性能和耐腐蚀性能影响较小。表11实施例48-53力学性能和耐腐蚀性能实施例屈服强度/mpa抗拉强度/mpa延伸率/%腐蚀速率(g/m2·h)4873584016.51.684976586520.01.235076085519.01.355178088522.51.125277588022.01.155376587021.01.17表11为实施例48-53力学性能及耐腐蚀性能测试结果,通过对比实施例50及实施例1测试结果可以发现,堆冷时间低于24h时,钢板力学性能降低,腐蚀速率增快,因此需保证足够的堆冷时间。从实施例48-53测试结果可以看出,随着堆冷温度的升高,钢板力学性能先升高后降低,特别是温度低于设定温度范围时,力学性能明显变差,腐蚀速率明显加快。以上所述,仅为本发明较佳的具体实施方式,但本发明的保护范围并不局限于此,任何熟悉本
技术领域:
的技术人员在本发明揭露的技术范围内,根据本发明的技术方案及其发明构思加以等同替换或改变,都应涵盖在本发明的保护范围之内。当前第1页12