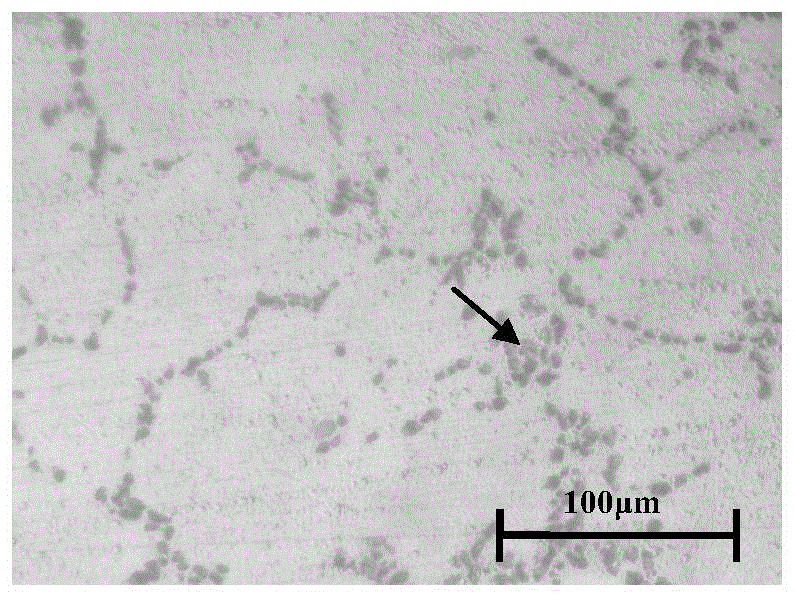
本发明涉及铝合金加工
技术领域:
,具体涉及一种航天卫星用管型热交换器的铝合金加工工艺。
背景技术:
:管型热交换器具有极高的导热性能,结构简单且传热功率大,温度均匀等特点,尤其在空间失重状态下仍具有此优异性能,因此在航天领域得到了广泛应用。目前,卫星上的单机和有效载荷大部分采用金属铝-氨热管型热交换器实现温度的均衡调节,管型热交换器内的工作介质为液氨。由于卫星使用的管型热交换器体积小,重量轻,尺寸精度要求高,公差要求范围为±0.05mm,远高于《gb/t14846-2014铝及铝合金挤压型材尺寸偏差》尺寸偏差为±0.35-0.45mm超高级标准的要求,因此对加工的材料要求非常严格。现有技术的3a21铝合金具有较好的拉伸强度,韧性好,耐腐蚀性能及焊接性能优良,适用于铝合金结构件的深加工,如焊接、弯折。由于航天管型热交换器的内部工作介质为液氨,采用现有技术的3a21铝合金加工为航天管型热交换器后,其铝合金中含有的cu、s与氨工质发生化学反应,使用较短的期限后因腐蚀反应出现裂痕,严重影响了卫星内部设施运行的稳定性。根据《gb/t6892-2015一般工业用铝及铝合金挤压型材》的标准,3a21铝合金的力学性能要求为抗拉强度≤185mpa,断后拉伸率a50mm>14%。因此,研发一种3a21系列的铝合金材料,既能满足《gb/t6892-2015一般工业用铝及铝合金挤压型材》有关力学性能的标准要求,又可以符合卫星用管型热交换器的特殊加工精度要求,且具有较高的液氨耐腐蚀性,以满足航天卫星的设施加工需求,对促进航天事业的发展具有重大意义。技术实现要素:本发明提出一种航天用铝合金管材的加工工艺,通过优化控制合金成分,采用特定的挤压加工工艺,具有稳定达标的力学性能,挤压加工需要的压力低易成型,外表光洁无振纹橘皮,且具有较高的液氨耐腐蚀性。为达此目的,本发明采用以下技术方案:一种航天用铝合金管材的加工工艺,依次包括成分优化步骤、浇铸制棒步骤、均质处理步骤和挤压成型步骤;所述成分优化步骤中,选取铝锭、金属硅、锰添加剂和铁添加剂作为铝合金原料,按照重量百分数计算,优化后的铝合金原料的成分为:si0.10-0.40wt%、fe0.30-0.60wt%、cu≤0.01wt%、mn1.15-1.40wt%、mg≤0.05wt%、zn≤0.1wt%、ti0.01-0.05wt%、s≤0.01wt%和余量为al。选取的原料铝锭包括工业铝锭、高纯度铝锭,通过检测工业铝锭、高纯度铝锭内相关金属成分含量,调整工业铝锭和高纯度铝锭配比,添加金属硅、锰添加剂和铁添加剂获得优化的目标成分比例。本发明所述的铝合金相较现有技术的3a21合金(成分见表1),进一步缩窄了所述铝合金其中的si、fe、mn和ti的含量,所述铝合金可以获得较好的晶粒,铸造时不产生热裂现象,所述铝合金管材具有良好的铸造加工性能,无加工或弯曲的橘皮和开裂等缺陷。高含量的si会增加所述铝合金的热裂倾向,降低所述铝合金的铸造加工性能。所述铝合金原料中mn含量在1.15-1.40wt%内时,能保证所述铝合金具有较高抗拉伸强度且加工时变形不易开裂。所述铝合金中含量为0.30-0.60wt%的fe,能使所述铝合金获得较细的晶粒,并中和所述铝合金中si元素的不利影响。考虑原材料中不可避免的含有铁杂质,铁添加剂的用量应减除原料中已有杂质铁含量,计算方法为:fe添加量=铝合金总投料重量×(fe成分目标控制含量(wt%)-fe杂质含量(wt%))。表13a21合金成分(wt%)化学元素sifecumnmgznti单个合计al含量(%)0-0.60-0.70-0.21-1.60-0.050-0.10-0.150.050.1余量进一步的,所述优化后的铝合金原料成分中s和cu的含量均≤0.005wt%。通过熔铸前洗炉的操作减少杂质,并通过添加高纯度铝锭进一步优化控制所述铝合金中s、cu含量在0.005wt%以内。所述航天用铝合金管材的内部工作介质是液氨,所述铝合金的原料成分中s、cu的含量均在0.005wt%以内,可以降低所述铝合金管材中s、cu元素与介质氨发生腐蚀反应的强度,以达到提升材料耐腐蚀性的目的,超出上述范围,将影响所述铝合金管材的使用寿命。控制所述铝合金中s、cu含量在0.005wt%以内,可以降低所述铝合金因腐蚀反应而出现裂痕的质量风险,提高了采用本发明所述铝合金材料的卫星内部设施运行的稳定性。进一步的,所述浇铸制棒步骤具体为:s1、对铝锭和金属硅原材料进行熔炼,熔炼温度为690℃~750℃,待所述铝锭、金属硅原材料彻底熔化后添加所述锰添加剂和铁添加剂,精炼4次,扒渣即得到熔体;s2、将熔体静置30分钟后,在720℃~740℃温度下,使用半连续铸造设备铸出的铸锭铝棒。所述铝合金采用常规恒温熔炼炉即可进行熔炼,操作简单,熔炼成本低。通过多次精炼更好的对所述铝合金起到除气、净化和细化所述铝合金晶粒的作用,扒渣去除熔炼产生的渣滓,避免所述铝合金的晶内留存有硬块或者杂质相。采用铸造铝棒进行挤压加工,根据常规的航天用铝合金热管管材的使用直径,设定铸锭铝棒的直径为φ100mm可满足常规各种直径的铝合金热管管材的挤压需求。进一步的,所述均质处理步骤的均质处理温度为590±20℃。通过dsc差热分析实验得知,本发明所述的铝合金在657.8℃出现吸热峰,如将均质温度设定过高,实际生产中有出现熔棒的风险,对设备、人身安全危害极大,如均质温度过低,则无法使所述铝合金中低熔点共晶相回溶基体,影响所述铝合金的性能,因此均质处理温度设定为590±20℃;进一步的,所述均质处理的保温时间4-10hr。均质处理又叫做均匀化退火,是将合金铸锭加热到接近不平衡固相线温度进行较长时间的保温,然后缓慢冷却到室温的过程,其目的在于通过合金元素原子的扩散来消除或减少合金的晶内化学成分和组织的不均匀性,改善铸锭的内部组织,消除铸锭残余应力,改善铸锭机械加工性能,同时提高塑性、降低变形抗力,使合金的热加工工艺性能得以改善。均质处理的保温时间少于4hr,所述铝合金的晶内化学成分和组织重新回溶不够完全,金相分布不均匀,没有达到均质的效果。所述铝合金挤压突破压力上升,难于挤出成型。均质处理的保温时间超过10hr以上,所述铝合金的晶内化学成分和组织已经基本回溶完全,金相分布均匀,随着时间的延长,对材料加工性能、表面质量的提升没有明显效果,增加了生产成本,也影响生产效率,没有积极的意义。故此,所述铝合金的均质处理的保温时间设置为4-10hr比较恰当。进一步的,所述挤压成型步骤采用正向挤压机,挤压速度为1.2-2mm/s。将获得的所述铝合金铸造铝棒通过正向挤压机进行挤压,如挤压速度过慢,由于挤压筒内所述铝合金的温度迅速降低,后期会出现堵模情况,如挤压速度过快,挤压筒内所述铝合金会出现流速不均的现象,造成挤出的所述铝合金管材出现振纹、尺寸不达标等不良的质量问题;进一步的,所述挤压成型步骤中铸棒温度为430℃-460℃,模具温度为410℃-430℃,挤压筒温度为400℃-420℃。挤压成型时的三温,铸棒温度、模具温度和挤压筒温度如过低,挤压杆很难挤动,如温度过高,挤出的所述铝合金管材尺寸容易出现不达标的状况。因此,在1.2-2mm/s的挤压速度下,铸棒温度、模具温度和挤压筒温度是获得尺寸合格和外观平滑的所述铝合金管材挤压成型的工艺关键控制点。进一步的,本发明还提出了一种航天用铝合金管材,通过以上所述的加工工艺制得。所述铝合金可以获得较好的晶粒,铸造时不产生热裂现象,具有良好的铸造加工性能。所述铝合金具有较高的抗拉伸强度,且加工变形时不易开裂。所述航天用铝合金管材采用的所述铝合金为3a21系合金。本发明优化了3a21合金的金属成分中的si、fe、mn和ti的含量,与现有技术相比,本发明还提出严控s、cu含量,并进一步将两种元素含量控制均在0.005%以内,提升了材料的耐腐蚀性。与现有技术相比,本发明所述铝合金的加工工艺可使材料更加顺利的挤压成型,不易出现堵模,不易产生振纹、橘皮等加工缺陷,且具有良好的耐腐蚀性。本发明的有益效果为:综上所述,本发明优化了适用于航天用的3a21合金的铝合金成分,本发明的所述铝合金所用材料严格控制s、cu含量,将两种元素含量均控制在0.005%以内,提升了所述铝合金对液氨的耐腐蚀性;本发明所述的铝合金相较现有技术的3a21合金(成分见表1),进一步缩窄了所述铝合金其中的si、fe、mn和ti的含量。所述铝合金获得较好的晶粒,铸造时不产生热裂现象,具有良好的铸造加工性能。而且,所述铝合金具有较高的抗拉伸强度,加工变形时不易开裂。本发明所述铝合金的加工工艺具有挤压成型顺利,不易出现堵模,不易产生振纹、橘皮等加工缺陷的优点。附图说明图1是本发明一个实施例4的金相组织示意图;图2是本发明一个对比例13的金相组织示意图;图3是本发明一个对比例12的金相组织示意图;图4是本发明一个对比例11的金相组织示意图;图5是本发明一个对比例10的金相组织示意图;图6是本发明一个对比例8的金相组织示意图。具体实施方式下面结合具体实施方式进一步说明本发明的技术方案。一种航天用铝合金管材,所述铝合金管材的生产加工工艺包括成分优化、浇铸制棒、均质处理和挤压成型等步骤,具体如下:1)成分优化,优化后的各实施例1-4和对比例5-13的所述铝合金管材原料成分和含量见表2。通过购买高纯度铝锭、熔铸前洗炉的操作减少杂质,并控制实施例1和4、对比例6、8、10、11、12和13的所述铝合金中s、cu含量均在0.005wt%以内。2)所述浇铸制棒步骤中所用原材料为高纯度铝锭、金属硅、锰添加剂和铁添加剂,所述浇铸制棒具体方法为:s1、熔炼温度为690℃~750℃,待所述高纯度铝锭、金属硅原材料熔化彻底后添加所述锰添加剂和铁添加剂,精炼4次,扒渣即得到熔体;s2、将熔体静置30分钟后,在720℃~740℃温度下,使用半连续铸造设备铸出直径为φ100mm的铝棒。3)将步骤2)所述铝合金铸件铝棒进行均质处理,均质处理的温度为590±20℃,保温时间4-10hr。4)将步骤3)得到的所述铝合金铸棒在合适的正向挤压机上进行挤压,挤压杆的挤压速度为1.2-2mm/s,挤压成型时铸棒温度为430℃-460℃,模具温度为410℃-430℃,挤压筒温度为400℃-420℃,测量挤压模具的模孔外圆直径为φ15±0.01mm,模孔内圆直径为φ9±0.01mm,挤出制得所述铝合金管材。5)将步骤4)得到的所述铝合金管材在弯管机上进行45°弯管加工,制成管件。表2实施例和对比例有关原料成分和含量(wt%)对以上实施例和对比例获得的所述铝合金管材,铸件铝棒有明显缺陷的除外,进行以下1~4的各项检测:1、参照《gb/t14846-2014铝及铝合金挤压型材尺寸偏差》的规定和要求,对各实施例取样进行成型尺寸的公差检测,各实施例测试结果表3第1行。2、参照《gbt6892-2015一般工业用铝及铝合金挤压型材》的规定和要求,对各实施例取样进行力学性能参数抗拉伸强度、屈服强度和断后拉伸率a50mm的检测,具体检测结果见表3第2、3和4行。3、将实施例和对比例获得的无外观明显缺陷的所述铝合金管件,浸泡于液氨中静置3年后,参照《gb/t6519-2000变形铝合金产品超声检验方法》,对各实施例取样进行浸泡前和浸泡后的有否腐蚀裂纹的检测,检测结果见表3第5、6行。4、以上实施例的制程中的外观检测结果,见表3第7行。另外,参照《gbt3246-2012变形铝及铝合金制品组织检验方法》使用金相显微镜对实施例4,以及铸造、挤压和弯管加工中有明显外管缺陷的对比例铸锭取样进行检测,获得的金相组织示意图见附图1~6,图号与实施例和对比例的对应记录见表3第8行。总体检测结论见表3第9行。表3实施例和对比例有关检测结果针对以上实施例和对比例的检测结果分析如下:1、根据以上表3第7行的制程中外观检验记录和表3第1行尺寸公差检测结果分析:1)实施例1~4和对比例5、7、9的整个制程中的外观合格无缺陷,图1为实施例4的有关金相组织示意图;分析表3第1行的公差检测数据可知,本发明的实施例1~4和对比例5、7、9制得的所述铝合金管材的加工公差在±0.03mm以内,可满足航天热交换器的加工精度为±0.05mm的要求;2)对比例6、8、10、11、12和13的制程中的外观不合格有明显缺陷,其中对比例13的铸件心部有明显缺陷,不适合制作所述铝合金管材,对比例6、8、10和11制得的所述铝合金管材的加工公差在±0.06~0.14mm之间,无法满足航天热交换器的加工精度为±0.05mm的要求,对比例12挤压时堵模,走水严重,挤出的管材拖料严重;3)与实施例4对比,对比例13的所述铝合金成分中fe的含量较低,只有0.2wt%,fe含量过低si含量不变时,合金中颗粒状al12(mn,fe)3si相较多,少量fe无法中和si的不利影响,影响了所述铝合金的铸造性能,具体表现为铸件心部、边部开裂,对比例13有关金相组织示意图见附图2;4)与实施例4对比,对比例12的所述铝合金成分中fe的含量较高,达到0.9wt%,fe含量过高si含量不变,所述铝合金的晶内形成多处鱼骨状al(mn,fe)硬质相,该硬质相无法回溶残留在基体内,影响材料性能,具体表现为影响管材表面质量出现划伤、拖烂现象,尺寸超限不稳定,力学性能抗拉强度、屈服强度、延伸率降低,对比例12有关金相组织示意图见附图3;5)对比例11的所述铝合金弯管加工时的管件弯曲部位有裂纹,与实施例4对比其成分中ti的含量较高,达到0.07wt%。微量ti可以细化所述铝合金的晶粒,ti含量超出0.05wt%以上时含ti相在基体与第二相界面边缘聚集析出,造成所述铝合金界面结合力差,对比例11有关的金相组织示意图见附图4。影响了所述铝合金的力学性能,具体表现为抗拉强度、延伸率降低,弯曲拉伸时发生变形而产生裂纹。因此,所述铝合金中ti的含量控制在0.05wt%以内,更有利于保障本发明的所述铝合金管材的弯曲和拉伸加工的品质;6)对比例10的所述铝合金进行加工时的管材和管件外表粗糙有橘皮,与实施例4比较对比例10的所述铝合金成分中mn的含量较低,达到0.8wt%,查看分析附图5对比例10所述铝合金的金相组织示意图,100nm尺度下看不到含mn相,第二相的弥散强化效果低,抑制再结晶能力弱,所述铝合金的抗拉强度明显降低,且表面出现橘皮。因此,所述铝合金中mn的含量控制在1.1wt%以上,更有利于保障所述铝合金的加工品质;7)对比例8的所述铝合金进行管材加工时发生堵模、走水现象,管件弯曲有裂纹,与实施例4比较对比例8的所述铝合金成分中mn的含量较高,达到1.6wt%。查看分析附图6对比例8所述铝合金的金相组织示意图,基体内形成了粗大al(mn,fe)相,降低了基体与第二相的结合力,具体表现为力学性能抗拉强度、屈服强度、延伸率在mn含量过量时反而降低,挤压成型的挤出压力上升,加工困难,表面质量变形严重,加工尺寸不稳定。因此,所述铝合金中mn的含量控制在1.4wt%以内更有利于保障所述铝合金管材的品质;8)对比例6的铸件铝棒外表面有细微裂纹,与实施例4比较对比例6的所述铝合金成分中si的含量较高,达到0.5wt%,过高含量的si虽然提高了对比例6所述铝合金的抗拉强度但降低了其流动性和加工性能,造成所述铝合金的铸件铝棒外表产生裂纹。因此,所述铝合金中si的含量控制在0.4wt%以内,确保所述铝合金铸件的具有更好的品质稳定性。2、分析表3第5、6行的内部缺陷检测数据,对比实施例1~4和对比例5、7、9的测试样在液氨中静置浸泡3年前后的结果可知,与氨工质无腐蚀反应合格的为实施例1-4,对比例5的cu含量为0.02wt%,对比例7和9的s含量分别为0.02wt%、0.015wt%,在液氨中静置浸泡3年后检测发现内部产生了不同程度裂纹缺陷,不符合耐腐蚀性测试要求,有较高的质量风险。含有0.01wt%的s或者cu的所述实施例2和实施例3的管件内部虽然没有明显缺陷但出现有缺陷阴影,存在质量隐患。因此,本发明所述铝合金成分中s、cu含量≤0.01wt%较为安全,为了更有效的减免所述铝合金中s、cu元素与氨工质的发生腐蚀性反应产生裂纹的不良现象,本发明所述铝合金成分中s、cu的含量降低为0.005wt%以内更加安全可靠。3、根据以上检测结果,获得的总体检测结论见表3第9行,实施1~4,检测合格,对比例5~13检测不合格。4、分析表3第2、3、4行的力学性能和各项检测合格的实施例数据可知,本发明的所述铝合金管材的抗拉强度为115~136mpa,断后拉伸率a50mm为24~32.7%,符合《gb/t6892-2015一般工业用铝及铝合金挤压型材》的标准,3a21铝合金的力学性能要求为的抗拉强度≤185mpa,断后拉伸率a50mm>14%的要求,屈服强度为72~98mpa,具有良好的加工性能。根据以上总体检测合格的实施例的数据,本发明所述铝合金原料成分优化后的范围值为:si0.10~0.40wt%,fe0.30~0.60wt%,cu≤0.01wt%,mn1.15~1.40wt%,mg≤0.05wt%,zn≤0.1wt%,ti0.01~0.05wt%,s≤0.01wt%,al余量。更进一步,降低本发明所述铝合金成分中s、cu的含量为0.005wt%以内,其耐腐蚀性能更加安全可靠。综上所述,本发明优化了适用于航天用的3a21合金的铝合金成分,本发明的所述铝合金所用材料严格控制s、cu含量,将两种元素含量均控制在0.005%以内,提升了所述铝合金对液氨的耐腐蚀性;本发明所述的铝合金相较现有技术的3a21合金(成分见表1),进一步缩窄了所述铝合金其中的si、fe、mn和ti的含量。所述铝合金获得较好的晶粒,铸造时不产生热裂现象,具有良好的铸造加工性能。而且,所述铝合金具有较高的抗拉伸强度,加工变形时不易开裂。本发明所述铝合金的加工工艺具有挤压成型顺利,不易出现堵模,不易产生振纹、橘皮等加工缺陷的优点。本发明提出的所述铝合金抗拉强度在115~136mpa之间比纯铝的抗拉强度60mpa更高,抗断裂的能力高于纯铝,屈服强度在72~98mpa之间,屈服强度低,有利于所述铝合金的冷加工成型和焊接;断后拉伸率在24%以上,具有良好的加工塑性,所述铝合金材料的拉伸和弯曲冷加工性能优良。以上结合具体实施例描述了本发明的技术原理。这些描述只是为了解释本发明的原理,而不能以任何方式解释为对本发明保护范围的限制。基于此处的解释,本领域的技术人员不需要付出创造性的劳动即可联想到本发明的其它具体实施方式,这些方式都将落入本发明的保护范围之内。当前第1页12