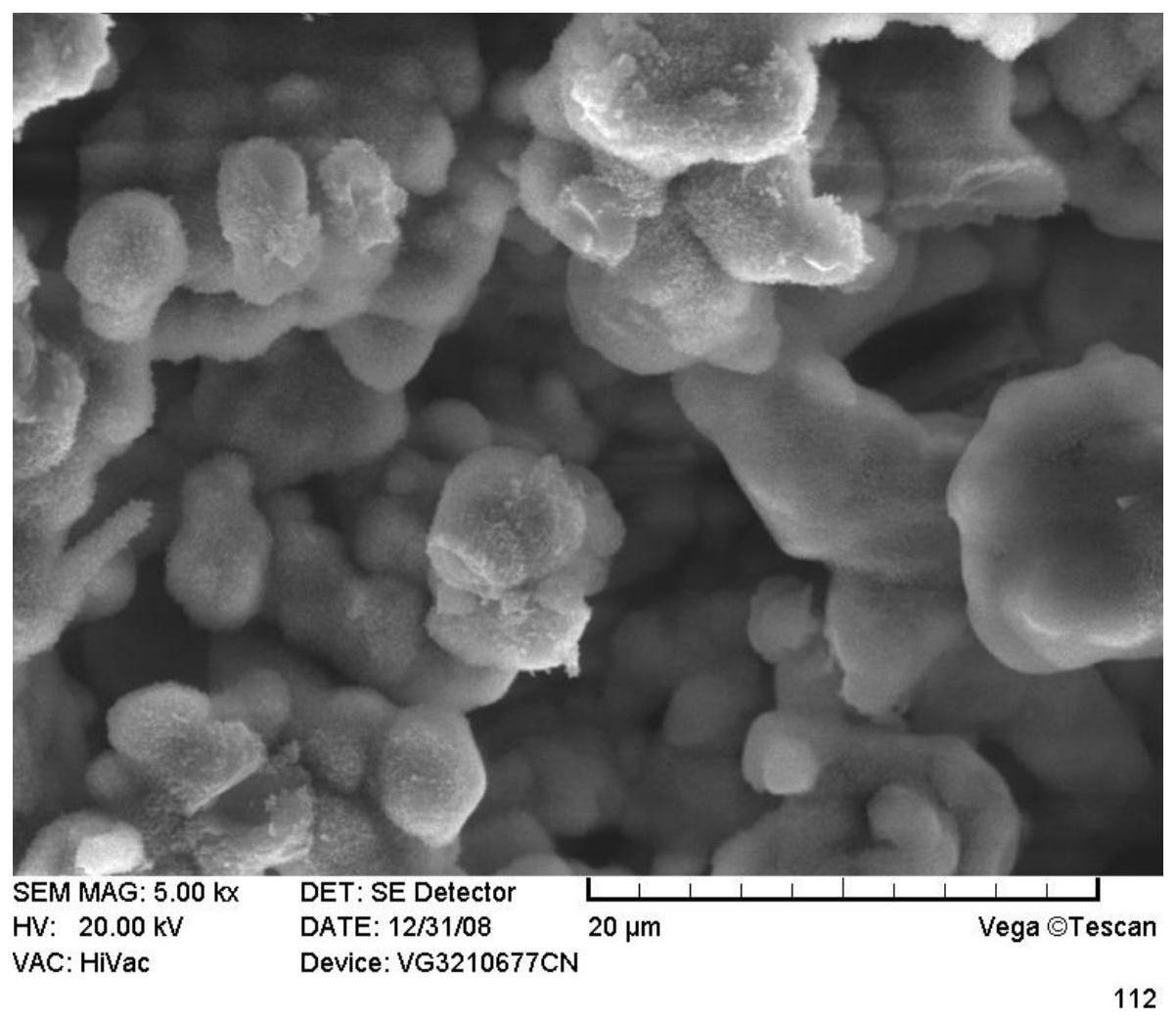
[0001]
本发明属于热喷涂处理技术领域,具体涉及一种起重机车轮耐磨自润滑梯度涂层的制备方法。
背景技术:[0002]
起重机运行过程中出现的车轮磨损问题,多是由于起重机车轮啃轨问题或者是现象导致的,起重机车轮啃轨问题不仅会导致起重机车轮受到磨损伤害,而且车轮啃轨产生的磨损阻力,还会在起重机运行过程中产生一定的噪声,甚至导致起重机运行中发生脱轨等不安全问题。导致起重机生产运行过程中,车轮啃轨故障问题发生的原因主要有,起重机设备的车轮安装不合理,或者是起重机设备运行轨道安装质量不合格、起重机设备的车架发生变形、起重机设备小车轮发生啃轨故障等原因,导致起重机设备生产运行过程中,发生车轮啃轨故障问题,从而导致起重机运行中车轮出现磨损,影响起重机正常运行以及运行安全。如果在起重机生产运行过程中,发生或者是出现车轮啃轨故障现象,不仅会对于起重机设备的正常生产运行造成一定的影响,而且车轮啃轨严重时,还会造成起重机车轮出现较大的摩擦与磨损,使起重机运行过程中出现不平稳的运行状态,并且伴有噪音产生,甚至会导致起重机车轮发生运行脱轨故障,对于起重机的生产运行安全也会造成一定的影响。
[0003]
起重机的大车行走轮的早期磨损的现象经常发生,车轮与轨道磨损发出刺耳的噪音,严重时会发生车轮轮缘断裂,车体跑出轨道的恶劣事故。
[0004]
对磨损不平衡导致超载车轮跑偏和啃轨进而损坏和报废,损坏的部位形式和原因一般有四种:(1)轮缘磨损断裂:是由于轮缘未经淬火,硬度偏低在水平分力作用下轮缘产生变形,使得接触表面因冷作硬化呈现鳞屑状剥落。如果车轮或轨道安装调整不好就会加剧运行中的啃轨和磨损,如果铸态车轮磨损值超过轮缘厚度的35%时即触发断裂。(2)踏面磨损层状脱皮:是由于车轮硬化程度过浅,尽管进行了表面淬火处理,但车轮所承受的最大剪应力已经超过淬火硬层深度与次表层强度构成极大的梯度位差,车轮踏面出现大片的层状疲劳剥落。(3)踏面局部压碎凹陷:是由于个别铸态车轮在铸造时内部存在着疏松、缩孔或砂眼等缺陷,单位压力增大时就会出现表面凹坑、压陷而导致轮体报废。(4)轮缘早期脆性断裂:是由于个别车轮在模铸制造时,长时间处于高温,且脱氧不充分,奥化体晶粒极易粗大,加之在正火状态中冷却速度缓慢导致铁素体晶粒也明显粗大化,这种材料的车轮韧性极差,经受很小的冲击就容易发生脆性断裂。如果在铸造时混入非金属夹杂后形成破断力的应力集中,就会加速车轮的早期脆断后报废。
[0005]
解决这一问题的关键是提高现有车轮轮缘的硬度,实现车轮组耐磨性抗朔变能力和抗剥离强度。随着热喷涂技术的不断发展和完善,以及应用领域的扩展,热喷涂涂层所表现的耐磨优越性在机器防护上应用越来越广泛,采用热喷涂金属涂层,陶瓷涂层,金属陶瓷复合涂层及金属间化合物涂层等工艺,能够有效的控制起重机车轮轮缘使用过程中的磨损问题,是人们所接收的一项经济,可靠的表面处理方法,有效的解决了起重机车轮轮缘防护问题。
[0006]
碳化钼具有较高熔点和硬度、良好热稳定性和机械稳定性和极好抗腐蚀性等特点。钼是一种银白色的难熔金属,熔点为2615℃,膨胀系数小,几乎与电子管的特殊玻璃的膨胀系数相同。钼在常温下稳定,高于600℃时会迅速氧化。与碳、碳氢化合物或一氧化碳在高于800℃时反应生成碳化钼。碳化钼,为深灰色金属状粉末,其结晶为密排六方晶格,熔点2690℃。作为一类具有很高熔点和硬度、良好热稳定性和机械稳定性、极好抗腐蚀特性的新型功能材料,已广泛用于各种耐高温、耐磨擦和耐化学腐蚀等领域。具有类似贵金属的电子结构和催化特性,可广泛用于有氢参与的反应如烷烃异构化、不饱和烃加氢、加氢脱硫和脱氮等反应的催化剂。硬度高,耐磨损,抗擦伤,是钼-碳化钼硬质涂层和其它金属陶瓷涂层的重要组分,亦可单独用作耐磨损、抗擦伤涂层。
[0007]
热喷涂碳化钼涂层具有较高的显微硬度,较好的耐磨性、氧化物含量低,涂层结合强度高等优势,是常用的耐磨涂层,已广泛应用于航空、航天、核能、机械等工业领域的装备关键摩擦运动副零部件表面耐磨防护。但在实际工作环境中,由于碳化钼涂层较高的硬度,摩擦体系的摩擦系数较大,会对与其配合的摩擦副产生较严重的磨损,甚至影响耐磨防护涂层的使用寿命。因为碳化钼涂层硬度较高,会对与起重机车轮轮缘磨损的轨道表面产生较严重的磨损,因此有必要制备具有自润滑特性的碳化钼涂层,以满足在起重机车轮轮缘和轨道表面摩擦条件下的服役要求。
技术实现要素:[0008]
本发明所要解决的技术问题在于针对上述现有技术的不足,提供一种起重机车轮耐磨自润滑梯度涂层的制备方法。该方法通过在涂层中添加碳化钼陶瓷增强相,碳化钼陶瓷具有极高的硬度以及优异的耐磨损性能,可以有效的提高涂层的耐磨损性能和涂层强度,对涂层形成有效的机械保护;通过将石墨烯作为自润滑耐磨添加剂应用于耐磨涂层中,一方面可以提高涂层的强度和韧性,另外石墨烯片层间的剪切力极小,在摩擦过程中石墨烯片层之间发生相对滑动,可以代替摩擦副表面金属件的相对滑动,实现磨屑与摩擦副表面的分离,大大降低了摩擦系数,减少了磨损;并利用钼酸铵作为钼的前驱体,通过碳热还原反应生成纳米碳化钼附着在石墨烯表面对石墨烯进行改性,改性石墨烯很大程度上提高了石墨烯的重量,在喷涂过程中不会被高速、高温的喷涂气流吹飞而损失,有效的保留了改性石墨烯在涂层中的成分含量和均匀分布,表面附着的纳米碳化钼提高了改性石墨烯与碳化钼喷涂粉末的相容性和均匀混合。
[0009]
为解决上述技术问题,本发明采用的技术方案是:一种起重机车轮耐磨自润滑梯度涂层的制备方法,其特征在于,包括以下步骤:
[0010]
步骤一、将三氧化钼粉末烘干,得到干燥粉末;将所述干燥粉末置于烧结炉内,向所述烧结炉内持续通入一氧化碳和氩气的混合气体进行烧结,得到碳化钼粉末;
[0011]
步骤二、将石墨烯粉末和无水乙醇混合均匀,然后加入去离子水混合后超声分散,得到石墨烯分散液;
[0012]
步骤三、将钼的前驱体加入步骤二中所述石墨烯分散液中,搅拌均匀后将沉淀抽滤,将抽滤后的沉淀烘干,得到干燥粉体;
[0013]
步骤四、将步骤三中所述干燥粉体在氩气环境下烧结,得到表面附着纳米碳化钼颗粒的改性石墨烯粉末;
[0014]
步骤五、将步骤一中所述碳化钼粉末和步骤四中所述表面附着纳米碳化钼颗粒的改性石墨烯粉末混合,得到混合喷涂粉末;将所述混合喷涂粉末置于无水乙醇中搅拌均匀,然后加入去离子水,超声分散,得到混合分散液;将所述混合分散液在桨叶式搅拌器下搅拌至干燥,搅拌过程中保持混合分散液恒温60℃~80℃,将干燥后的物料烘干后筛分,得到碳化钼/改性石墨烯混合喷涂粉末;所述碳化钼/改性石墨烯混合喷涂粉末中碳化钼的质量百分含量为20%~80%,余量为纳米碳化钼颗粒的改性石墨烯粉末;
[0015]
步骤六、对起重机车轮外缘表面进行表面除锈、除氧化皮和除油清洁处理;根据涂层梯度要求,采用步骤五中所述碳化钼/改性石墨烯混合喷涂粉末对处理后的起重机车轮外缘表面进行超音速火焰喷涂,在起重机车轮外缘表面得到起重机车轮耐磨自润滑梯度涂层。
[0016]
上述的一种起重机车轮耐磨自润滑梯度涂层的制备方法,其特征在于,步骤一中所述三氧化钼粉末中moo
3
质量含量大于99%,平均粒径<10μm;步骤一中所述烘干的温度为80℃~120℃,时间为1h~2h;步骤一中所述一氧化碳和氩气的混合气体中一氧化碳的体积百分比为20%~40%,余量为氩气;步骤一中所述烧结的升温速率为6℃/min~8℃/min,烧结温度为900℃~1100℃,保温时间为10min~20min,一氧化碳和氩气混合气体气氛压力为0.2mpa~0.4mpa。
[0017]
上述的一种起重机车轮耐磨自润滑梯度涂层的制备方法,其特征在于,步骤二中所述石墨烯粉末和无水乙醇的质量比为1:(200~400);石墨烯粉末和去离子水的质量比为1:(50~150);超声分散的频率为20hz~60hz,时间为4h~8h;所述石墨烯粉末为商用增强性石墨烯,比表面积为180m
2
/g~280m
2
/g,c含量为70%~80%,平均粒径<10μm。
[0018]
上述的一种起重机车轮耐磨自润滑梯度涂层的制备方法,其特征在于,步骤三中所述钼的前驱体为钼酸铵;步骤三中所述烘干的温度为100℃~120℃,烘干的时间为40min~60min。
[0019]
上述的一种起重机车轮耐磨自润滑梯度涂层的制备方法,其特征在于,步骤四中所述烧结的温度为900℃~1100℃,升温速率为6℃/min~8℃/min,保温时间10min~20min,氩气气氛压力为0.2mpa~0.4mpa。
[0020]
上述的一种起重机车轮耐磨自润滑梯度涂层的制备方法,其特征在于,步骤五中所述超声分散的频率为30hz~90hz,时间为2h~6h。
[0021]
上述的一种起重机车轮耐磨自润滑梯度涂层的制备方法,其特征在于,还包括步骤六中超音速火焰喷涂之前将所述碳化钼/改性石墨烯混合喷涂粉末在120℃~160℃条件下烘干30min~90min。
[0022]
上述的一种起重机车轮耐磨自润滑梯度涂层的制备方法,其特征在于,步骤六中所述超音速火焰喷涂的工艺条件为:助燃剂氧气流量为80l/min~120l/min,燃气丙烷流量为30l/min~90l/min,送粉气体氮气流量为20l/min~40l/min,喷枪移动速度为10mm/s~30mm/s,喷涂距离为200mm~400mm,梯度涂层的总厚度为600μm~900μm。
[0023]
上述的一种起重机车轮耐磨自润滑梯度涂层的制备方法,其特征在于,步骤六中所述超音速火焰喷涂为多道喷涂,其中第一道喷涂所用碳化钼/改性石墨烯混合喷涂粉末中碳化钼的质量百分含量为60%~80%,余量为纳米碳化钼颗粒的改性石墨烯粉末,第二道喷涂所用碳化钼/改性石墨烯混合喷涂粉末中碳化钼的质量百分含量为40%~60%,余
量为纳米碳化钼颗粒的改性石墨烯粉末,第三道喷涂所用碳化钼/改性石墨烯混合喷涂粉末中碳化钼的质量百分含量为20%~40%,余量为纳米碳化钼颗粒的改性石墨烯粉末。
[0024]
上述的一种起重机车轮耐磨自润滑梯度涂层的制备方法,其特征在于,所述第一道喷涂的工艺条件为:助燃剂氧气流量为100l/min~120l/min,燃气丙烷流量为60l/min~90l/min,送粉气体氮气流量为30l/min~40l/min,喷枪移动速度为10mm/s~20mm/s,喷涂距离为200mm~300mm,第一道喷涂涂层厚度为200~300μm;
[0025]
所述第二道喷涂的工艺条件为:助燃剂氧气流量为90l/min~110l/min,燃气丙烷流量为40l/min~80l/min,送粉气体氮气流量为25l/min~35l/min,喷枪移动速度为15mm/s~25mm/s,喷涂距离为250mm~350mm,第二道喷涂涂层厚度为200μm~300μm;
[0026]
所述第三道喷涂的工艺条件为:助燃剂氧气流量为80l/min~100l/min,燃气丙烷流量为30l/min~60l/min,送粉气体氮气流量为20l/min~30l/min,喷枪移动速度为20mm/s~30mm/s,喷涂距离为300mm~400mm,第三道喷涂涂层厚度为200μm~300μm。
[0027]
本发明与现有技术相比具有以下优点:
[0028]
1、本发明通过在涂层中添加碳化钼陶瓷增强相,碳化钼陶瓷具有极高的硬度以及优异的耐磨损性能,可以有效的提高涂层的耐磨损性能和涂层强度,对涂层形成有效的机械保护。本发明利用廉价的三氧化钼粉末作为主要原料通过碳热还原反应制备碳化钼粉末。
[0029]
2、本发明将石墨烯作为自润滑耐磨添加剂应用于耐磨涂层中,一方面可以提高涂层的强度和韧性,另外石墨烯片层间的剪切力极小,在摩擦过程中石墨烯片层之间发生相对滑动,可以代替摩擦副表面金属件的相对滑动,实现磨屑与摩擦副表面的分离,大大降低了摩擦系数,减少了磨损。
[0030]
3、石墨烯质量较轻,碳化钼粉末质量大,如果将石墨烯直接添加到喷涂粉末中,石墨烯在喷涂过程中会被高速气流吹飞而损失。另外,石墨烯比表面积较大,活性高,在与碳化钼粉末复合时容易团聚,很难保证在喷涂粉末中均匀混合,从而难以保证制备涂层具有自润滑耐磨特性。本发明利用钼酸铵为钼的前驱体,通过碳热还原反应生成纳米碳化钼附着在石墨烯表面对石墨烯进行改性,改性石墨烯很大程度上提高了石墨烯的重量,在喷涂过程中不会被高速、高温的喷涂气流吹飞而损失,有效的保留了改性石墨烯在涂层中的成分含量和均匀分布。表面附着的纳米碳化钼提高了改性石墨烯与碳化钼喷涂粉末的相容性和均匀混合。
[0031]
4、本发明优选采用三道喷涂,三道喷涂的混合喷涂粉末成分呈梯度分布,随着与基体的距离增大,单道涂层中的改性石墨烯含量增大。根据国内外梯度涂层相关研究结果,参考起重机车轮轮缘磨损的工作环境以及起重机车轮轮缘工作面的耐磨损性能和自润滑性能实验结果证明,喷涂粉末成分呈梯度分布的多道涂层的耐磨损性能和自润滑性能明显优于单道涂层。所以三道涂层喷涂粉末成分呈梯度分布,可以使整体涂层的耐磨损性能和自润滑性能得到最佳配合,使碳化钼/改性石墨烯梯度涂层保护起重机车轮外缘的作用充分发挥。
[0032]
5、本发明制备的自润滑梯度涂层具有极高的耐磨损和自润滑性能,用于起重机车轮轮缘防护时,涂层材料显示出优异的耐磨性能和自润滑性能,能够满足起重机车轮轮缘工作环境的要求,在该领域有着良好的应用前景。
[0033]
下面结合附图和实施例,对本发明的技术方案做进一步的详细描述。
附图说明
[0034]
图1为本发明实施例1制备的碳化钼粉末的sem照片。
[0035]
图2为本发明实施例1制备的自润滑梯度涂层表面的金相照片。
具体实施方式
[0036]
实施例1
[0037]
本实施例的起重机车轮耐磨自润滑梯度涂层的制备方法,包括以下步骤:
[0038]
步骤一、将三氧化钼粉末(moo
3
质量含量大于99%,平均粒径<10μm)烘干,烘干的温度为80℃,时间为1h,得到干燥粉末;将所述干燥粉末置于烧结炉内,向所述烧结炉内持续通入一氧化碳和氩气的混合气体进行烧结,烧结的升温速率为6℃/min,烧结温度为900℃,保温时间为10min,得到碳化钼粉末;所述一氧化碳和氩气的混合气体中一氧化碳的体积百分比为20%,余量为氩气;所述一氧化碳和氩气混合气体气氛压力为0.2mpa;
[0039]
步骤二、将石墨烯粉末(商用增强性石墨烯,比表面积为180m
2
/g~280m
2
/g,c含量为70%~80%,平均粒径<10μm)和无水乙醇混合均匀,然后加入去离子水混合后超声分散,得到石墨烯分散液;所述石墨烯粉末和无水乙醇的质量比为1:300;石墨烯粉末和去离子水的质量比为1:100;超声分散的频率为20hz,时间为4h;
[0040]
步骤三、将钼酸铵加入步骤二中所述石墨烯分散液中,搅拌均匀后将沉淀抽滤,将抽滤后的沉淀烘干,得到干燥粉体;所述烘干的温度为100℃,烘干的时间为40min;
[0041]
步骤四、将步骤三中所述干燥粉体在氩气环境下烧结,得到表面附着纳米碳化钼颗粒的改性石墨烯粉末;所述烧结的温度为900℃,升温速率为6℃/min,保温时间10min,氩气气氛压力为0.2mpa;
[0042]
步骤五、根据涂层梯度要求,将步骤一中所述碳化钼粉末和步骤四中所述表面附着纳米碳化钼颗粒的改性石墨烯粉末混合,得到混合喷涂粉末;将所述混合喷涂粉末置于无水乙醇中搅拌均匀,然后加入去离子水,超声分散,得到混合分散液;将所述混合分散液在桨叶式搅拌器下搅拌至干燥,搅拌过程中保持混合分散液恒温60℃,将干燥后的物料烘干后筛分,得到碳化钼/改性石墨烯混合喷涂粉末;所述超声分散的频率为30hz,时间为2h;
[0043]
第一道喷涂所用碳化钼/改性石墨烯混合喷涂粉末中碳化钼的质量百分含量为60%,余量为纳米碳化钼颗粒的改性石墨烯粉末;
[0044]
第二道喷涂所用碳化钼/改性石墨烯混合喷涂粉末中碳化钼的质量百分含量为40%,余量为纳米碳化钼颗粒的改性石墨烯粉末;
[0045]
第三道喷涂所用碳化钼/改性石墨烯混合喷涂粉末中碳化钼的质量百分含量为20%,余量为纳米碳化钼颗粒的改性石墨烯粉末;
[0046]
步骤六、对起重机车轮外缘(zg340-640)表面进行表面除锈、除氧化皮和除油清洁处理;将步骤五中三道喷涂所用碳化钼/改性石墨烯混合喷涂粉末均在120℃条件下烘干30min,然后根据涂层梯度要求,先采用烘干后的第一道喷涂所用碳化钼/改性石墨烯混合喷涂粉末对处理后的起重机车轮外缘表面进行第一道超音速火焰喷涂,然后采用烘干后的第二道喷涂所用碳化钼/改性石墨烯混合喷涂粉末进行第二道超音速火焰喷涂,再采用烘
干后的第三道喷涂所用碳化钼/改性石墨烯混合喷涂粉末进行第三道超音速火焰喷涂,在起重机车轮外缘表面得到总厚度为600μm的起重机车轮耐磨自润滑梯度涂层;
[0047]
第一道喷涂的工艺条件为:助燃剂氧气流量为100l/min,燃气丙烷流量为60l/min,送粉气体氮气流量为30l/min,喷枪移动速度为10mm/s,喷涂距离为200mm,第一道喷涂涂层厚度为200μm;
[0048]
第二道喷涂的工艺条件为:助燃剂氧气流量为90l/min,燃气丙烷流量为40l/min,送粉气体氮气流量为25l/min,喷枪移动速度为15mm/s,喷涂距离为250mm,第二道喷涂涂层厚度为200μm;
[0049]
第三道喷涂的工艺条件为:助燃剂氧气流量为80l/min,燃气丙烷流量为30l/min,送粉气体氮气流量为20l/min,喷枪移动速度为20mm/s,喷涂距离为300mm,第三道喷涂涂层厚度为200μm。
[0050]
图1为本实施例制备的碳化钼粉末的sem照片,从图1中可看出碳化钼颗粒近似球形,这能够保证在喷涂时粉末具有良好的流动性,有利于喷涂的持续进行。图2为本实施例制备的自润滑梯度涂层表面的金相照片,从图2中可明显的观察到基体与涂层的结合状况良好,涂层的微观组织均匀,结构致密,没有大的孔隙和裂纹出现,碳化钼/改性石墨烯作为喷涂材料能够形成致密的涂层,进一步保证涂层结构紧密。
[0051]
本实施例制备的自润滑梯度涂层具有极高的耐磨损和自润滑性能,用于起重机车轮轮缘防护时,涂层材料显示出优异的耐磨性能和自润滑性能,能够满足起重机车轮轮缘工作环境的要求,在该领域有着良好的应用前景。
[0052]
实施例2
[0053]
本实施例的起重机车轮耐磨自润滑梯度涂层的制备方法,包括以下步骤:
[0054]
步骤一、将三氧化钼粉末(moo
3
质量含量大于99%,平均粒径<10μm)烘干,烘干的温度为100℃,时间为1.5h,得到干燥粉末;将所述干燥粉末置于烧结炉内,向所述烧结炉内持续通入一氧化碳和氩气的混合气体进行烧结,烧结的升温速率为7℃/min,烧结温度为1000℃,保温时间为15min,得到碳化钼粉末;所述一氧化碳和氩气的混合气体中一氧化碳的体积百分比为30%,余量为氩气;所述一氧化碳和氩气混合气体气氛压力为0.3mpa;
[0055]
步骤二、将石墨烯粉末(商用增强性石墨烯,比表面积为180m
2
/g~280m
2
/g,c含量为70%~80%,平均粒径<10μm)和无水乙醇混合均匀,然后加入去离子水混合后超声分散,得到石墨烯分散液;所述石墨烯粉末和无水乙醇的质量比为1:200;石墨烯粉末和去离子水的质量比为1:150;超声分散的频率为40hz,时间为6h;
[0056]
步骤三、将钼酸铵加入步骤二中所述石墨烯分散液中,搅拌均匀后将沉淀抽滤,将抽滤后的沉淀烘干,得到干燥粉体;所述烘干的温度为110℃,烘干的时间为50min;
[0057]
步骤四、将步骤三中所述干燥粉体在氩气环境下烧结,得到表面附着纳米碳化钼颗粒的改性石墨烯粉末;所述烧结的温度为1000℃,升温速率为7℃/min,保温时间15min,氩气气氛压力为0.3mpa;
[0058]
步骤五、根据涂层梯度要求,将步骤一中所述碳化钼粉末和步骤四中所述表面附着纳米碳化钼颗粒的改性石墨烯粉末混合,得到混合喷涂粉末;将所述混合喷涂粉末置于无水乙醇中搅拌均匀,然后加入去离子水,超声分散,得到混合分散液;将所述混合分散液在桨叶式搅拌器下搅拌至干燥,搅拌过程中保持混合分散液恒温70℃,将干燥后的物料烘
干后筛分,得到碳化钼/改性石墨烯混合喷涂粉末;所述超声分散的频率为60hz,时间为4h;
[0059]
第一道喷涂所用碳化钼/改性石墨烯混合喷涂粉末中碳化钼的质量百分含量为70%,余量为纳米碳化钼颗粒的改性石墨烯粉末;
[0060]
第二道喷涂所用碳化钼/改性石墨烯混合喷涂粉末中碳化钼的质量百分含量为50%,余量为纳米碳化钼颗粒的改性石墨烯粉末;
[0061]
第三道喷涂所用碳化钼/改性石墨烯混合喷涂粉末中碳化钼的质量百分含量为30%,余量为纳米碳化钼颗粒的改性石墨烯粉末;
[0062]
步骤六、对起重机车轮外缘(zg-50simn)表面进行表面除锈、除氧化皮和除油清洁处理;将步骤五中三道喷涂所用碳化钼/改性石墨烯混合喷涂粉末均在140℃条件下烘干60min,然后根据涂层梯度要求,先采用烘干后的第一道喷涂所用碳化钼/改性石墨烯混合喷涂粉末对处理后的起重机车轮外缘表面进行第一道超音速火焰喷涂,然后采用烘干后的第二道喷涂所用碳化钼/改性石墨烯混合喷涂粉末进行第二道超音速火焰喷涂,再采用烘干后的第三道喷涂所用碳化钼/改性石墨烯混合喷涂粉末进行第三道超音速火焰喷涂,在起重机车轮外缘表面得到总厚度为750μm的起重机车轮耐磨自润滑梯度涂层;
[0063]
第一道喷涂的工艺条件为:助燃剂氧气流量为110l/min,燃气丙烷流量为70l/min,送粉气体氮气流量为35l/min,喷枪移动速度为15mm/s,喷涂距离为250mm,第一道喷涂涂层厚度为250μm;
[0064]
第二道喷涂的工艺条件为:助燃剂氧气流量为100l/min,燃气丙烷流量为60l/min,送粉气体氮气流量为30l/min,喷枪移动速度为20mm/s,喷涂距离为300mm,第二道喷涂涂层厚度为250μm;
[0065]
第三道喷涂的工艺条件为:助燃剂氧气流量为90l/min,燃气丙烷流量为40l/min,送粉气体氮气流量为25l/min,喷枪移动速度为25mm/s,喷涂距离为350mm,第三道喷涂涂层厚度为250μm。
[0066]
本实施例制备的自润滑梯度涂层具有极高的耐磨损和自润滑性能,用于起重机车轮轮缘防护时,涂层材料显示出优异的耐磨性能和自润滑性能,能够满足起重机车轮轮缘工作环境的要求,在该领域有着良好的应用前景。
[0067]
实施例3
[0068]
本实施例的起重机车轮耐磨自润滑梯度涂层的制备方法,包括以下步骤:
[0069]
步骤一、将三氧化钼粉末(moo
3
质量含量大于99%,平均粒径<10μm)烘干,烘干的温度为120℃,时间为2h,得到干燥粉末;将所述干燥粉末置于烧结炉内,向所述烧结炉内持续通入一氧化碳和氩气的混合气体进行烧结,烧结的升温速率为8℃/min,烧结温度为1100℃,保温时间为20min,得到碳化钼粉末;所述一氧化碳和氩气的混合气体中一氧化碳的体积百分比为40%,余量为氩气;所述一氧化碳和氩气混合气体气氛压力为0.4mpa;
[0070]
步骤二、将石墨烯粉末(商用增强性石墨烯,比表面积为180m
2
/g~280m
2
/g,c含量为70%~80%,平均粒径<10μm)和无水乙醇混合均匀,然后加入去离子水混合后超声分散,得到石墨烯分散液;所述石墨烯粉末和无水乙醇的质量比为1:400;石墨烯粉末和去离子水的质量比为1:50;超声分散的频率为60hz,时间为8h;
[0071]
步骤三、将钼酸铵加入步骤二中所述石墨烯分散液中,搅拌均匀后将沉淀抽滤,将抽滤后的沉淀烘干,得到干燥粉体;所述烘干的温度为120℃,烘干的时间为60min;
[0072]
步骤四、将步骤三中所述干燥粉体在氩气环境下烧结,得到表面附着纳米碳化钼颗粒的改性石墨烯粉末;所述烧结的温度为900℃~1100℃,升温速率为8℃/min,保温时间20min,氩气气氛压力为0.4mpa;
[0073]
步骤五、根据涂层梯度要求,将步骤一中所述碳化钼粉末和步骤四中所述表面附着纳米碳化钼颗粒的改性石墨烯粉末混合,得到混合喷涂粉末;将所述混合喷涂粉末置于无水乙醇中搅拌均匀,然后加入去离子水,超声分散,得到混合分散液;将所述混合分散液在桨叶式搅拌器下搅拌至干燥,搅拌过程中保持混合分散液恒温80℃,将干燥后的物料烘干后筛分,得到碳化钼/改性石墨烯混合喷涂粉末;所述超声分散的频率为90hz,时间为6h;
[0074]
第一道喷涂所用碳化钼/改性石墨烯混合喷涂粉末中碳化钼的质量百分含量为80%,余量为纳米碳化钼颗粒的改性石墨烯粉末;
[0075]
第二道喷涂所用碳化钼/改性石墨烯混合喷涂粉末中碳化钼的质量百分含量为60%,余量为纳米碳化钼颗粒的改性石墨烯粉末;
[0076]
第三道喷涂所用碳化钼/改性石墨烯混合喷涂粉末中碳化钼的质量百分含量为20%,余量为纳米碳化钼颗粒的改性石墨烯粉末;
[0077]
步骤六、对起重机车轮外缘(zg-50simn)表面进行表面除锈、除氧化皮和除油清洁处理;将步骤五中三道喷涂所用碳化钼/改性石墨烯混合喷涂粉末均在160℃条件下烘干90min,然后根据涂层梯度要求,先采用烘干后的第一道喷涂所用碳化钼/改性石墨烯混合喷涂粉末对处理后的起重机车轮外缘表面进行第一道超音速火焰喷涂,然后采用烘干后的第二道喷涂所用碳化钼/改性石墨烯混合喷涂粉末进行第二道超音速火焰喷涂,再采用烘干后的第三道喷涂所用碳化钼/改性石墨烯混合喷涂粉末进行第三道超音速火焰喷涂,在起重机车轮外缘表面得到总厚度为900μm的起重机车轮耐磨自润滑梯度涂层;
[0078]
第一道喷涂的工艺条件为:助燃剂氧气流量为120l/min,燃气丙烷流量为90l/min,送粉气体氮气流量为40l/min,喷枪移动速度为20mm/s,喷涂距离为300mm,第一道喷涂涂层厚度为300μm;
[0079]
第二道喷涂的工艺条件为:助燃剂氧气流量为110l/min,燃气丙烷流量为80l/min,送粉气体氮气流量为35l/min,喷枪移动速度为25mm/s,喷涂距离为350mm,第二道喷涂涂层厚度为300μm;
[0080]
第三道喷涂的工艺条件为:助燃剂氧气流量为100l/min,燃气丙烷流量为60l/min,送粉气体氮气流量为30l/min,喷枪移动速度为30mm/s,喷涂距离为400mm,第三道喷涂涂层厚度为300μm。
[0081]
本实施例制备的自润滑梯度涂层具有极高的耐磨损和自润滑性能,用于起重机车轮轮缘防护时,涂层材料显示出优异的耐磨性能和自润滑性能,能够满足起重机车轮轮缘工作环境的要求,在该领域有着良好的应用前景。
[0082]
对实施例1、2、3中的起重机车轮轮缘在有无本发明自润滑梯度涂层的条件下,施加载荷为50n,转速为1500r/min,利用摩擦磨损试验机进行摩擦磨损实验,表1为实施例1、2、3中的起重机车轮轮缘在有无碳化钼/改性石墨烯梯度涂层的条件下分别磨损30h、60h和90h后的磨损量。
[0083]
表1本发明有涂层防护的起重机车轮轮缘的耐磨损性能
[0084][0085]
注:(1)zg340-640(单道涂层-1)工艺条件为:助燃剂氧气流量为90l/min,燃气丙烷流量为40l/min,送粉气体氮气流量为25l/min,喷枪移动速度为15mm/s,喷涂距离为250mm,喷涂涂层厚度为600μm;
[0086]
(2)zg-50simn(单道涂层-2)工艺条件为:助燃剂氧气流量为100l/min,燃气丙烷流量为60l/min,送粉气体氮气流量为30l/min,喷枪移动速度为20mm/s,喷涂距离为300mm,喷涂涂层厚度为750μm;
[0087]
(3)zg-50simn(单道涂层-3)工艺条件为:助燃剂氧气流量为110l/min,燃气丙烷流量为80l/min,送粉气体氮气流量为35l/min,喷枪移动速度为25mm/s,喷涂距离为350mm,喷涂涂层厚度为900μm;
[0088]
从表1的试验数据可以观察到,在相同摩擦磨损测试条件下,有涂层防护的起重机车轮轮缘的磨损量和摩擦系数大大小于没有涂层防护的起重机车轮轮缘的磨损量和摩擦系数,喷涂粉末成分呈梯度分布的多道涂层的磨损量和摩擦系数小于相同喷涂工艺单道涂层防护的起重机车轮轮缘工作面的磨损量和摩擦系数。因此碳化钼/改性石墨烯梯度涂层能有效提高起重机车轮轮缘的耐磨损和自润滑性能。
[0089]
以上所述,仅是本发明的较佳实施例,并非对本发明做任何限制,凡是根据发明技术实质对以上实施例所作的任何简单修改、变更以及等效结构变化,均仍属于本发明技术方案的保护范围内。