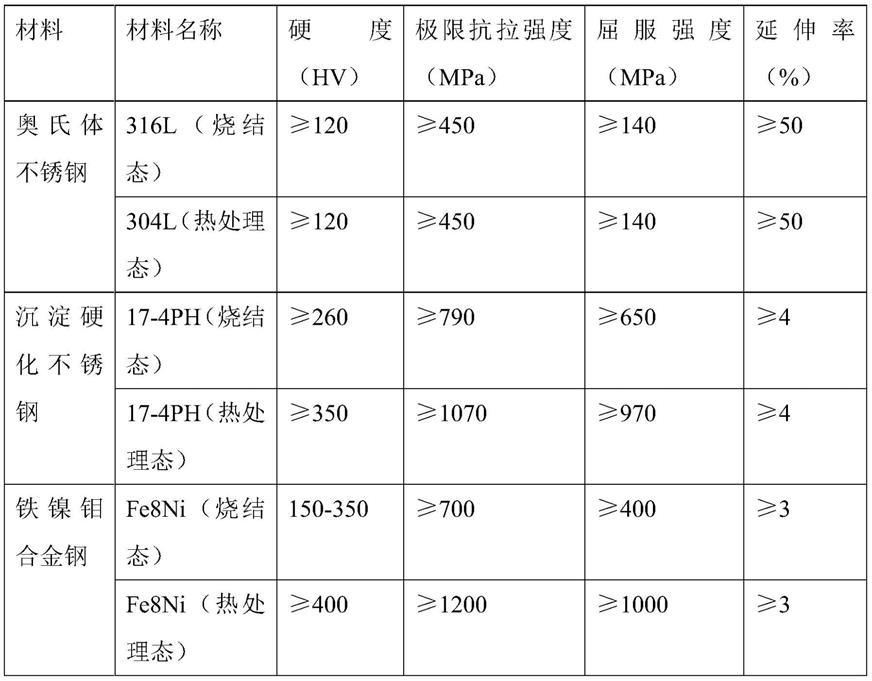
1.本发明涉及金属注射成型材料技术领域,特别是涉及一种金属注射用热脱脂型粘结剂及喂料、马氏体时效不锈钢及其制备方法。
背景技术:2.金属注射成型(metal injection molding,mim)材料已广泛应用于许多领域。现最常见的mim材料主要有奥氏体不锈钢(例如316l、304l)、沉淀硬化不锈钢(17
‑
4ph)、铁镍钼合金钢(例如fe8ni)等,这些常见的mim材料力学性能见如下表1:
[0003][0004]
随着mim产品在许多领域更广泛和深入的应用,经常会遇到要求材料既要有很高的强度(例如屈服强度≥1500mpa、极限抗拉强度≥1700mpa),又要有良好的韧性(例如延伸率≥5%)的情况,比较常见的例子有通讯设备转轴、某些军工枪械零件、高压传感器等,以上常见的mim材料的已无法同时满足这种高强度和高韧性的要求。
技术实现要素:[0005]
为了弥补上述现有技术的不足,本发明提出一种热脱脂型粘结剂及喂料、马氏体时效不锈钢及其制备方法。
[0006]
本发明的技术问题通过以下的技术方案予以解决:
[0007]
一种马氏体时效不锈钢的制备方法,包括如下步骤:
[0008]
s1、混粉:将cu粉、ni粉、mo粉、co粉和fe粉称量后混合成金属粉末;其中,所述金属粉末包括如下质量分数的各组分:cu 0.2
‑
0.45%,ni 13
‑
17%,mo 4.5
‑
7%,co 5
‑
8.5%,c≤0.01%,o≤0.35%,s≤0.03%,p≤0.03%,以及fe为余量;
[0009]
s2、混炼造粒:将粘结剂和所述金属粉末进行混炼造粒,得到喂料;其中,所述粘结剂与所述金属粉末的质量比为8
‑
10%,所述粘结剂包括如下质量分数的各组分:pom 15
‑
20%,甘油25
‑
30%,油酸35
‑
40%,pe和/或pp 5
‑
15%,润滑剂4.5
‑
9%,以及耦合剂0.5
‑
1%;
[0010]
s3、制件:对喂料进行注射得到生坯;
[0011]
s4、脱脂烧结:将生坯进行热脱脂后烧结;
[0012]
s5、热处理:将烧结后的产品做固溶处理和时效处理,得到所述马氏体时效不锈钢。
[0013]
优选地,所述步骤s4具体为:在保护气氛下,将生坯进行热脱脂后烧结,其中,在热脱脂段,以升温速率1
‑
3℃/min升温到600
‑
800℃,保温1
‑
2h,通过热脱将粘接剂全部脱除,然后进入烧结阶段,以升温速率2
‑
5℃/min升温到1360
‑
1400℃进行烧结,保温时间3
‑
6小时,分压压力10
‑
60kpa。
[0014]
优选地,所述步骤s5中的固溶处理的温度为1000
‑
1100℃,保温时间1
‑
2小时,淬火处理采用油淬;所述时效处理的温度为450
‑
600℃,保温3
‑
6小时。
[0015]
优选地,所述步骤s3的制件条件为:注射压力150
‑
180mpa,注射温度170
‑
190℃,模具温度60
‑
90℃,注射速度为15
‑
45cm3/s。
[0016]
优选地,所述步骤s2中,所述润滑剂为pw、cw和花生油中的任意一种,优选地,所述润滑剂为pw;所述耦合剂为硬脂酸钙、硬脂酸锌和硬脂酸中的至少一种,优选地,所述耦合剂为硬脂酸钙;优选地,所述粘结剂由如下质量分数的各组分组成:pom 15
‑
20%,甘油25
‑
30%,油酸35
‑
40%,pe 5
‑
15%,pw 4.5
‑
9%,以及硬脂酸钙0.5
‑
1%,更优选地,所述粘结剂由如下质量分数的各组分组成:pom 15
‑
20%,甘油25
‑
30%,油酸35
‑
40%,pe 5
‑
15%,pw 4.5
‑
9%,以及硬脂酸钙0.5
‑
1%。
[0017]
优选地,所述步骤s1的混粉是在v型混合机中进行干混,混合时间为1
‑
2小时,转速为8
‑
12r/min;所述步骤s2的混炼造粒中,混炼时间为1
‑
2小时,混炼温度为180
‑
200℃。
[0018]
一种马氏体时效不锈钢,由所述的制备方法制得。
[0019]
一种金属注射成型用热脱脂型粘结剂,包括如下质量分数的各组分:pom 15
‑
20%,甘油25
‑
30%,油酸35
‑
40%,pe和/或pp 5
‑
15%,润滑剂4.5
‑
9%,以及耦合剂0.5
‑
1%。
[0020]
优选地,所述润滑剂为pw、cw和花生油中的任意一种,优选地,所述润滑剂为pw;所述耦合剂为硬脂酸钙、硬脂酸锌和硬脂酸中的至少一种,优选地,所述耦合剂为硬脂酸钙;优选地,所述粘结剂由如下质量分数的各组分组成:pom 15
‑
20%,甘油25
‑
30%,油酸35
‑
40%,pe 5
‑
15%,pw 4.5
‑
9%,以及硬脂酸钙0.5
‑
1%,更优选地,所述粘结剂由如下质量分数的各组分组成:pom 15
‑
20%,甘油25
‑
30%,油酸35
‑
40%,pe 5
‑
15%,pw 4.5
‑
9%,以及硬脂酸钙0.5
‑
1%。
[0021]
一种用于制作马氏体时效不锈钢的喂料,所述喂料由所述的粘结剂和金属粉末组成;其中,所述粘结剂与所述金属粉末的质量比为8
‑
10%;所述金属粉末包括如下质量分数
的各组分:cu 0.2
‑
0.45%,ni 13
‑
17%,mo 4.5
‑
7%,co 5
‑
8.5%,c≤0.01%,o≤0.35%,s≤0.03%,p≤0.03%,以及fe为余量。
[0022]
本发明与现有技术对比的有益效果包括:通过本发明的制备方法最终可获得一种屈服强度≥1500mpa、极限抗拉强度≥1700mpa、延伸率≥5%、硬度≥450hv(450
‑
550hv之间)的合金材料,与常用的mim材料相比,在极限抗拉强度和屈服强度两个方面获得了显著提高,同时具有良好的韧性,扩大了mim材料的应用范围。
具体实施方式
[0023]
下面结合优选的实施方式对本发明作进一步说明。需要说明的是,在不冲突的情况下,本技术中的实施例及实施例中的特征可以相互组合。
[0024]
本发明实施例提供一种马氏体时效不锈钢的制备方法,其包括如下步骤:
[0025]
s1、混粉:将cu粉、ni粉、mo粉、co粉和fe粉称量后混合成金属粉末;其中,所述金属粉末包括如下质量分数的各组分:cu 0.2
‑
0.45%,ni 13
‑
17%,mo 4.5
‑
7%,co 5
‑
8.5%,c≤0.01%,o≤0.35%,s≤0.03%,p≤0.03%,以及fe为余量;其中,c,o,s和p是所用cu粉、ni粉、mo粉、co粉和fe粉中不可避免的杂质。
[0026]
s2、混炼造粒:将粘结剂和所述金属粉末进行混炼造粒,得到喂料;其中,所述粘结剂与所述金属粉末的质量比为8
‑
10%,所述粘结剂包括如下质量分数的各组分:pom(聚甲醛)15
‑
20%,甘油25
‑
30%,油酸35
‑
40%,pe(聚乙烯)和/或pp(聚丙烯)5
‑
15%,润滑剂4.5
‑
9%,以及耦合剂0.5
‑
1%;
[0027]
s3、制件:对喂料进行注射得到生坯;
[0028]
s4、脱脂烧结:将生坯进行热脱脂后烧结;
[0029]
s5、热处理:将烧结后的产品做固溶处理和时效处理,得到所述马氏体时效不锈钢。
[0030]
在上述技术方案中,金属粉末中的fe是主体成分,cu、ni、mo、co作为合金元素加入,起到沉淀强化作用,四种元素共同协同,使得对材料产生的强化作用足以使材料到达屈服强度≥1500mpa、极限抗拉强度≥1700mpa的性能要求,从而大幅提高材料的综合力学性能。其中,cu、ni、mo、co各自的含量如果低于所给的最小值,则可能出现对材料的强化效果不足的问题,而如果高于所给的最大值,会对材料的韧性将带来不良影响;cu、co的沉淀强化作用的强化的机理均是固溶处理时通过油淬控制冷却速度得到过饱和体,然后时效处理时让过饱和体中的过饱和原子析出,得到极细的第二相均匀第弥散分布在材料当中,产生第二相强化,而ni、mo的沉淀强化作用是通过形成金属间化合物,对材料产生强化作用。
[0031]
在上述技术方案中,采用的粘接剂为热脱脂型,粘结剂中的各个组分在烧结过程中的热脱脂段脱除,不会残留在最终的材料中,避免了催化脱脂过程中硝酸对钴的腐蚀,也避免了溶剂脱脂溶胀现象给产品带来的变形。该粘接剂与催化脱脂型粘结剂和溶剂脱脂型粘结剂相比,注射形成的生坯不需要任何额外的脱脂处理,可直接进入烧结炉利用烧结过程中的热脱脂段直接将粘接剂脱除干净,简化了工序。粘接剂的作用在于赋予金属粉末流动性以完成注射,在烧结的热脱脂阶段会从产品内部完全脱除,不会对材料性能产生影响,具体来说,在注射过程中粘接剂处于熔融状态,均匀地包覆在金属粉末颗粒的表面,在注射压力的作用下,粘接剂带动金属粉末充满模腔,其中,pom以及pe和/或pp在金属粉末颗粒间
起粘接的作用,耦合剂中的官能团在金属粉末颗粒和pom、pe和/或pp之间起桥接作用,加强了pom、pe和/或pp对粉末颗粒的抓附力,润滑剂起降低整个体系的粘度的作用,甘油和油酸协同作为填充剂。
[0032]
在优选的实施例中,所述步骤s4具体为:在保护气氛下,将生坯进行热脱脂后烧结,其中,在热脱脂段,以升温速率1
‑
3℃/min升温到600
‑
800℃,保温1
‑
2h,通过热脱将粘接剂全部脱除,然后进入烧结阶段,以升温速率2
‑
5℃/min升温到1360
‑
1400℃进行烧结,保温时间3
‑
6小时,分压压力10
‑
60kpa。其中,保护气氛为氮气和氩气中的至少一种。粘接剂的脱除过程如下:生坯直接放入烧结炉进行烧结,随着温度升高,pom会裂解脱除,油酸和甘油会挥发脱除,在产品内部形成均匀分布的流通孔隙作为剩余粘接剂组分热脱的排出通道,pom脱除后pe和/或pp起骨架支撑作用以保证产品仍有一定强度。在烧结阶段,若烧结温度低于1360℃时,材料的屈服强度和极限抗拉强度会显著降低,而若高于1400℃时,材料有烧熔风险。
[0033]
在优选的实施例中,所述步骤s5中的固溶处理的温度为1000
‑
1100℃,保温时间1
‑
2小时,淬火处理采用油淬;所述时效处理的温度为450
‑
600℃,保温3
‑
6小时。
[0034]
在优选的实施例中,所述步骤s3的制件条件为:注射压力150
‑
180mpa,注射温度170
‑
190℃,模具温度60
‑
90℃,注射速度为15
‑
45cm3/s。在该步骤中,注射压力如果低于150mpa则可能出现模腔填充不满,如果大于180mpa则可能出现披锋;注射温度若低于170℃则在会出现因塑化不充分而注射困难,若大于190℃则会造成喂料中的pom剧烈分解;模具温度若低于60℃,则生坯表面会出现熔接痕和黑纹,若高于90℃则生坯表面会出现银纹;注射速度若低于15cm3/s则会导致模具填充不满,而若高于45cm3/s则会发生金属粉末和粘接剂的分离,在浇口附件出现严重的黑纹。
[0035]
在优选的实施例中,所述步骤s2中的所述润滑剂为pw(石蜡)、cw(carnauba wax,棕榈蜡)和花生油中的任意一种。
[0036]
在优选的实施例中,所述润滑剂为pw。
[0037]
在优选的实施例中,所述耦合剂为硬脂酸钙、硬脂酸锌和硬脂酸中的至少一种。
[0038]
在优选的实施例中,所述耦合剂为硬脂酸钙。
[0039]
在优选的实施例中,所述粘结剂由如下质量分数的各组分组成:pom15
‑
20%,甘油25
‑
30%,油酸35
‑
40%,pe 5
‑
15%,pw 4.5
‑
9%,以及硬脂酸钙0.5
‑
1%。
[0040]
在优选的实施例中,所述粘结剂由如下质量分数的各组分组成:pom15
‑
20%,甘油25
‑
30%,油酸35
‑
40%,pe 5
‑
15%,pw 4.5
‑
9%,以及硬脂酸钙0.5
‑
1%。
[0041]
在优选的实施例中,所述步骤s2的混炼造粒中,混炼时间为1
‑
2小时,混炼温度为180
‑
200℃。
[0042]
在优选的实施例中,所述步骤s1的混粉是在v型混合机中进行干混,混合时间为1
‑
2小时,转速为8
‑
12r/min。
[0043]
一种马氏体时效不锈钢,由所述的制备方法制得。
[0044]
本发明实施例还提供一种金属注射成型用热脱脂型粘结剂,包括如下质量分数的各组分:pom(聚甲醛)15
‑
20%,甘油25
‑
30%,油酸35
‑
40%,pe(聚乙烯)和/或pp(聚丙烯)5
‑
15%,润滑剂4.5
‑
9%,以及耦合剂0.5
‑
1%。
[0045]
在优选的实施例中,所述润滑剂为pw(石蜡)、cw(carnauba wax,棕榈蜡)和花生油
中的任意一种。
[0046]
在优选的实施例中,所述润滑剂为pw。
[0047]
在优选的实施例中,所述耦合剂为硬脂酸钙、硬脂酸锌和硬脂酸中的至少一种。
[0048]
在优选的实施例中,所述耦合剂为硬脂酸钙。
[0049]
在优选的实施例中,所述粘结剂由如下质量分数的各组分组成:pom 15
‑
20%,甘油25
‑
30%,油酸35
‑
40%,pe 5
‑
15%,pw 4.5
‑
9%,以及硬脂酸钙0.5
‑
1%。
[0050]
在优选的实施例中,所述粘结剂由如下质量分数的各组分组成:pom 15
‑
20%,甘油25
‑
30%,油酸35
‑
40%,pe 5
‑
15%,pw 4.5
‑
9%,以及硬脂酸钙0.5
‑
1%。
[0051]
本发明实施例又提供一种用于制作马氏体时效不锈钢的喂料,所述喂料由粘结剂和金属粉末组成;其中,所述粘结剂与所述金属粉末的质量比为8
‑
10%;所述金属粉末包括如下质量分数的各组分:cu 0.2
‑
0.45%,ni 13
‑
17%,mo 4.5
‑
7%,co 5
‑
8.5%,c≤0.01%,o≤0.35%,s≤0.03%,p≤0.03%,以及fe为余量。
[0052]
本发明的一个示例中,马氏体时效不锈钢的制备方法包括如下步骤:
[0053]
1、混粉:将cu粉、ni粉、mo粉、co粉和fe粉称量后加入v型混合机进行干混成金属粉末;其中,所述金属粉末包括如下质量分数的各组分:cu 0.2
‑
0.45%,ni 13
‑
17%,mo 4.5
‑
7%,co 5
‑
8.5%,c≤0.01%,o≤0.35%,s≤0.03%,p≤0.03%,以及fe为余量;混合时间1
‑
2小时,转速8
‑
12r/min。
[0054]
2、混炼造粒:按照粘接剂与金属粉末质量比8
‑
10%,将金属粉末和粘接剂加入混炼造粒一体机进行混炼造粒得到喂料,其中,所述粘结剂与所述金属粉末的质量比为8
‑
10%,所述粘结剂包括如下质量分数的各组分:pom 15
‑
20%,甘油25
‑
30%,油酸35
‑
40%,pe和/或pp 5
‑
15%,润滑剂4.5
‑
9%,以及耦合剂0.5
‑
1%;混炼时间1
‑
2小时,混炼温度180
‑
200℃。
[0055]
3、制件:对喂料进行注射得到生坯,其中,注射压力150
‑
180mpa,注射温度170
‑
190℃,模具温度60
‑
90℃,注射速度为15
‑
45cm3/s。为进行力学测试,本实施例的步骤3中,采用力学标准件模具对喂料进行注射得到力学标准件生坯。
[0056]
4、脱脂烧结:生坯直接放入烧结炉进行烧结,烧结过程设一个热脱脂段,即以升温速率1
‑
3℃/min升温到600
‑
800℃,通过热脱将粘接剂全部脱除,然后进入烧结阶段,即以升温速率2
‑
5℃/min升温到1360
‑
1400℃进行,保温时间3
‑
6小时,分压压力10
‑
60kpa。
[0057]
5、热处理:热处理包括固溶处理和时效处理,即将烧结后的产品做固溶处理和时效处理得到最终产品,其中,固溶温度1000
‑
1100℃,保温时间1
‑
2小时,淬火处理采用油淬;时效温度450
‑
600℃,保温3
‑
6小时。为进行力学测试,本实施例的步骤5中,得到的是力学标准件。6、测试:用万能力学试验机对所得的力学标准件进行力学性能检测,检测项目为极限抗拉强度、屈服强度和延伸率,用维氏硬度计测硬度。
[0058]
实施例1
[0059]
1、混粉:按质量分数cu 0.4%、ni 13.8%、mo 5.5%、co 7.6%、余量为fe,分别称好cu、ni、mo、co和fe粉末,加入v型混合机进行干混得到金属粉末,混合时间1小时,转速10r/min。金属粉末中还不可避免地含有c、o、s和p等杂质元素,其中c≤0.01%,o≤0.35%,s≤0.03%,p≤0.03%
[0060]
2、混炼造粒:按照粘接剂与金属粉末质量比9.83%,将金属粉末和粘接剂加入混
炼造粒一体机进行混炼造粒得到喂料,其中,粘结剂由pom 16%、甘油26%、油酸38%、pe 14.4%、pw 5%和硬脂酸钙0.6%组成,混炼时间为1.5小时,混炼温度为185℃。
[0061]
3、制件:采用力学标准件模具对喂料进行注射得到力学标准件生坯。注射压力170mpa,注射温度185℃,模具温度75℃,注射速度25cm3/s。
[0062]
4、脱脂烧结:将所得生坯直接放入烧结炉进行烧结,烧结过程设一个热脱脂段,热脱脂温度600℃,升温速率1.5℃/min,通过热脱将粘接剂全部脱除后进入烧结段,烧结温度1400℃,保温时间3小时,气氛为氩气,分压压力30kpa。
[0063]
5、热处理:将烧结后的产品做固溶处理和时效处理,其中,固溶处理的温度为1050℃,保温1小时,淬火处理采用油淬,时效处理的温度为550℃,保温4小时。
[0064]
6、测试:用万能力学试验机对力学标准件进行力学性能检测,检测项目为极限抗拉强度、屈服强度和延伸率,用维氏硬度计测硬度,测试结果见表2。
[0065]
对比例1
[0066]
与实施例1的区别在于,该对比例中,步骤1中的金属粉末含cu 0.4%、ni 12%、mo 4%、co 7.6%、余量为fe。其他步骤(步骤2
‑
6)同与实施例1。力学性能检测结果见表2。
[0067]
对比例2
[0068]
与实施例1的区别在于,该对比例中,步骤1中的金属粉末含cu 0.4%、ni 13.8%、mo 5.5%、co 4.5%、余量为fe。其他步骤(步骤2
‑
6)同与实施例1。力学性能检测结果见表2。
[0069]
表2:
[0070][0071]
通过表2可以看出,本技术实施例1中的喂料在烧结态下(即步骤4处理后的产品)与现有常用mim材料并无显著优势,但是在热处理后材料(即步骤5处理后的产品)的性能得到显著提升,其中合金元素在热处理过程中产生的沉淀强化作用是主要原因。普通的碳素钢c含量均在0.02%以上,可以通过碳化物对材料进行强化,但本发明的材料由于碳含量很低(≤0.01%),因此不能通过碳化物进行强化,但本发明实施例的材料中含有较大量的ni、mo、co、cu等元素,这些元素在奥氏体温度下能大量固溶于γfe中,当温度下降到马氏体温度时,这些元素在αfe中的溶解度比在γfe中的溶解度低得多,因此得到这些元素的过饱和马氏体组织,该组织本身具有高的强度和硬度,使材料得到一定程度的强化,时效处理过程中,溶解在基体组织中的过饱和元素(ni、mo、co、cu)析出,且相互之间形成ni3mo等一系列
复杂的金属间化合物,这些化合物弥散地分布在基体组织内,极大地提高了材料的强度,且这些金属间化合物尺寸比碳素钢中析出的碳化物小得多,保证了该材料既具有很高的强度又具备良好的韧性。
[0072]
以上内容是结合具体的优选实施方式对本发明所作的进一步详细说明,不能认定本发明的具体实施只局限于这些说明。对于本发明所属技术领域的技术人员来说,在不脱离本发明构思的前提下,还可以做出若干等同替代或明显变型,而且性能或用途相同,都应当视为属于本发明的保护范围。