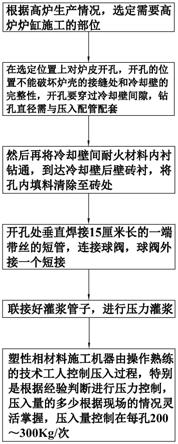
1.本技术涉及高炉炉缸密封领域,具体涉及高炉冷却壁与炉缸碳砖密封用塑性相材料。
背景技术:2.在高炉炼铁生铁过程中,往往伴随着大量的冷却作业,其中,高炉的炉腰、炉腹处于高炉渣铁和热流严重冲击的高热负荷区域,故而此区域碳砖外侧一般设置有冷却壁和水冷管,水冷管位于冷却壁和碳砖之间,水冷管和冷却壁实现高炉的冷却换热,此时冷却壁和炉缸碳砖之间的温度约为30~150℃。
3.在实际生产操作中,由于高炉炉衬受到高温冲刷、冷热往复循环以及各种侵蚀等,使得炉缸周围碳砖逐渐侵蚀减少,导致冷却壁与炉缸碳砖间出现气隙,降低冷却效果,倒置局部温度过高,影响高炉安全运行。
技术实现要素:4.为了增强冷却壁和炉缸碳砖之间的密封和导热性能,本技术提供高炉冷却壁与炉缸碳砖密封用塑性相材料。
5.本技术提供的高炉冷却壁与炉缸碳砖密封用塑性相材料,采用如下的技术方案:高炉冷却壁与炉缸碳砖密封用塑性相材料,其特征在于,以重量份数计,包括碳素材料30~50份、碳化硅20~40份、金属粉末5~15份、添加剂2~5份、含碳结合剂20~30份。
6.通过选用碳素材料、碳化硅、金属粉末等材料作为塑性相材料的主要成分,使得本技术塑性相材料导热性能高,从而使得塑性相材料能够将炉内的热量传递给水冷管排出高炉;添加剂能够使得塑形相材料能够在100℃便具有一定的耐压和抗折强度,从而提升塑性相材料的密封性能;而含碳结合剂能够使得塑性相材料在20~100℃之间有一定塑性,使得塑性相材料在施工时间内具有一定的流动性,便于将塑性相材料压入冷却壁与碳砖之间,填充冷却壁与碳砖之间的微小缝隙,从而增强冷却壁和碳砖之间的密封和导热性能。
7.优选的,以重量份数计,包括碳素材料35~45份、碳化硅25~35份、金属粉末10~15份。
8.优选的,以重量份数计,包括碳素材料40份、碳化硅30份、金属粉末10份。
9.通过采用上述技术方案,碳素材料能够增加塑性相材料中的碳素,使得塑性相材料接近高炉的原始材料,增加塑性相材料使用时的质量稳定性。金属粉末和碳化硅能够增加塑性相材料的导热性。
10.优选的,所述碳素材料包括石油焦粉和石墨通过采用上述技术方案,石油焦粉导热性好,荷重变形温度高,抗渣、抗热震性稳定;石墨起到润滑剂的作用,可改善塑性相材料的塑性;同时石油焦粉和石墨能够在塑性碳材料中形成网状结构,增强导热性。
11.优选的,所述石油焦粉和石墨的重量比为7~9:1~3。
12.通过采用上述技术方案,采用上述配比的石油焦粉和石墨能够有效的增强塑性相材料的塑性和导热性。
13.优选的,所述含碳结合剂包括沥青和含碳热塑性酚醛树脂,且所述沥青和热塑性酚醛树脂的重量比为1~3:7~9。
14.通过采用上述技术方案,沥青自身具有一定的热塑性,在50~150℃之间呈现一定的流动性,从而使得塑性相材料方便压入冷却壁与碳砖之间缝隙,而在大于400℃之后,沥青碳化,提高了塑性相材料的残碳量,提升高炉炉衬的耐高温冲刷性能。而热塑性酚醛树脂同样具有热塑性,便于塑性相材料的施工操作,同时还可使得塑性相材料具有良好的体积稳定性,在高温下体积变化小。
15.优选的,所述金属粉末为金属铜粉末。
16.通过采用上述技术方案,金属铜粉末性能较为稳定,同时其热传导系数为401w/mk,金属铜粉末可有效提升塑性相材料的导热性能。
17.优选的,所述碳化硅为碳化硅微粉,其sic含量≥98wt%,粒度≤0.005mm。
18.通过采用上述技术方案,碳化硅微粉在塑性相材料基质中呈网状结构,能够有效提升塑性相材料的耐压强度和导热性能。
19.优选的,所述添加剂基本组成为二茂铁4~6份、六亚甲基四胺3~5份、二氧化钛1~5份、金属铝粉1~5份、羧甲基纤维素8~12份。
20.通过采用上述技术方案,二茂铁、六亚甲基四胺和二氧化钛能够与热塑性酚醛树脂相互配合,使得塑性相材料在150~200℃之间发生固化,从而使得塑性相材料在密封缝隙之后具有一定强度,提升塑性相材料的密封性能;金属铝粉一方面可很好地防止碳化硅微粉和碳的氧化,另一方面一部分可以与热塑性酚醛树脂反应生成碳化铝,且二氧化钛也可与热塑性酚醛树脂反应生成碳化钛,提高塑性相材料的强度;羧甲基纤维素可作为悬浮剂,使得塑性相材料在施工时料浆稳定性好,分散性好,流动性佳,利于施工。
21.综上所述,本技术具有以下有益效果:1、本技术塑性相材料导热性能高,且塑性相材料在施工时间内具有一定的流动性,便于将塑性相材料压入冷却壁与碳砖之间,填充冷却壁与碳砖之间的微小缝隙,从而增强冷却壁和碳砖之间的密封和导热性能。
22.2、碳素材料的加入,能够增加塑性相材料中的碳素,使得塑性相材料接近高炉的原始材料,使得本技术塑性相材料与高炉冷却壁和碳砖能够紧密结合。
23.3、本技术的塑性相材料在20~100℃之下具有良好的塑性,利于施工;而在150~200℃之间时逐渐发生固化,且此时塑性相材料体积稳定不收缩,从而使得塑性相材料在密封缝隙之后具有一定强度,提升塑性相材料的密封性能;在大于400℃之后,沥青碳化,提高了塑性相材料的残碳量,提升高炉炉衬的耐高温冲刷性能。
附图说明
24.图1是本技术提供的塑性相材料的施工方法流程图。
具体实施方式
25.以下结合实施例对本技术作进一步详细说明。
26.本技术所用原料皆可通过商购获得。
27.原料的制备例制备例1添加剂的制备,按重量份数取二茂铁4份、六亚甲基四胺3份、二氧化钛1份、金属铝粉1份、羧甲基纤维素8份加入到搅拌机中进行搅拌,搅拌速度为800r/min。其中,tio2含量≥98wt%,粒度≤0.074mm。金属铝粉为球形雾化金属铝,其al含量≥99wt%,粒度0.045mm~0.074mm。
28.制备例2-10制备例2-10分别提供了添加剂,与制备1的不同之处在于,各添加剂中组分和含量不同,具体如表1所示。
29.表1制备例1-10中各添加剂的组分和含量10中各添加剂的组分和含量其中,“/”表示没有添加。
30.实施例实施例1高炉炉缸冷却壁与碳砖密封用塑性相材料,采用以下制备方法制备而成:在碳素材料30份、碳化硅20份、金属粉末5份及添加剂2份的混合料中加入含碳结合剂20份,之后进行混练形成所述一种塑性相材料。
31.其中碳素材料包括重量比为7:3的石油焦粉和石墨混合而成,且石油焦粉和石墨的粒度为100目以下,碳含量在99%以上。碳化硅为碳化硅微粉,其sic含量≥98wt%,粒度≤0.005mm。金属粉末为金属铜粉末,其细度为2μm。添加剂选自制备例1的添加剂。含碳结合剂包括沥青和含碳热塑性酚醛树脂,所述沥青和热塑性酚醛树脂的重量比为3:7;其中沥青为软化点为100~120℃的改性煤沥青。
32.实施例2-8实施例2-8分别提供了高炉炉缸冷却壁与碳砖密封用塑性相材料,与实施例1的不同之处在于,各实施例中原料的重量份数不同,具体如表2所示。
33.表2实施例1-8提供的塑性相材料中各原料的重量份数实施例碳素材料碳化硅金属粉末添加剂含碳结合剂1302052202352510220340301022044540152205403010325640301042574030105258403010430实施例9本实施例与实施例6的不同之处在于,碳素材料中石油焦粉和石墨的重量比为8:2。
34.实施例10本实施例与实施例6的不同之处在于,碳素材料中石油焦粉和石墨的重量比为9:1。
35.实施例11本实施例与实施例9的不同之处在于,含碳结合剂中沥青和热塑性酚醛树脂的重量比为2:8。
36.实施例12本实施例与实施例9的不同之处在于,含碳结合剂中沥青和热塑性酚醛树脂的重量比为1:9。
37.实施例13-21实施例13-21分别提供了高炉炉缸冷却壁与碳砖密封用塑性相材料,与实施例11的不同之处在于,各实施例中选用的添加剂不同,具体如表3所示。
38.表3实施例13-21提供的塑性相材料中所选用的添加剂实施例添加剂13制备例214制备例315制备例416制备例517制备例618制备例719制备例820制备例921制备例10对比例对比例1对比例1提供塑性相材料,按重量份数计,其中粉料部分:一级焦宝石粉30份;活性
二氧化硅微粉2份;石墨5份;活性α-al2o3微粉2份;结合剂部分:焦油15份;脱晶蒽油15份;热塑性酚醛树脂10份;改质石油沥青5份;改性煤沥青5份。
39.对比例2本对比例与实施例1的区别在于,碳素材料的加入量为10份。
40.对比例3本对比例与实施例1的区别在于,碳素材料的加入量为60份。
41.对比例4本对比例与实施例1的区别在于,碳化硅的加入量为10份。
42.对比例5本对比例与实施例1的区别在于,碳化硅的加入量为50份。
43.对比例6本对比例与实施例1的区别在于,金属铜粉的加入量为1份。
44.对比例7本对比例与实施例1的区别在于,金属铜粉的加入量为30份。
45.性能检测试验分别按照国家标准gb/t 3001、gb/t 5072-2008、gb/t 5988-2007检测上述实施例和对比例中塑性相材料的冷态抗折强度、耐压强度、线变化率,检测结果见表4。
46.表4实施例1-21与对比例1-7提供的塑性相材料性能测试结果
结合实施例1-21和对比例1-7并结合表4可以看出,本技术提供的塑性相材料具有良好的施工流动性,本技术的塑性相材料在20~100℃之下具有良好的塑性,利于施工;而在150~200℃之间时逐渐发生固化,且此时塑性相材料体积稳定不收缩,从而使得塑性相材料在密封缝隙之后具有一定强度,提升塑性相材料的密封性能;在大于400℃之后,塑性相材料中的沥青和热塑性酚醛树脂发生碳化,提高了塑性相材料的残碳量,提升高炉炉衬的耐高温冲刷性能。
47.结合实施例1-8和对比例1-7并结合表4可以看出,碳素材料、碳化硅和金属粉末的加入量分别为40、30、10份时,塑性相材料的冷态抗折强度和耐压强度较高。实施例6中,塑性相材料在500℃
×
24h时的冷态抗折强度为4.4mpa、耐压强度为10.4mpa。
48.结合实施例9-12并结合表4可以看出,当碳素材料中石油焦粉和石墨的重量比为8:2、含碳结合剂中沥青和热塑性酚醛树脂的重量比为2:8时,可进一步提升塑性相材料的抗折强度和耐压强度。实施例11中,塑性相材料在500℃
×
24h时的冷态抗折强度为4.6mpa、耐压强度为11.4mpa。
49.结合实施例13-21并结合表4可以看出,本技术塑性相材料中所用添加剂中的组分
中,二茂铁、六亚甲基四胺、二氧化钛、金属铝粉、羧甲基纤维素的加入与否以及加入比例皆能够影响塑性相材料的冷态抗折强度和耐压强度,其中羧甲基纤维素的添加与否对塑性相材料的施工流动性有较大的影响。其中,实施例14制备的塑性相材料各项性能较佳,实施例14提供的塑性相材料在500℃
×
24h时的冷态抗折强度为4.8mpa、耐压强度为12.2mpa。
50.应用例采用实施例14提供的塑性相材料对高炉炉缸冷却壁与炉缸碳砖之间的缝隙进行填充施工,具体施工方法如下:s1、根据高炉生产情况,选定需要高炉炉缸施工的部位,修复之前,高炉冷却壁与炉缸碳砖间热电偶温度检测温度高于200℃,说明此处高炉炉缸冷却壁与碳砖之间具有空隙;s2、在选定位置上对炉皮开孔,开孔的位置不能破坏炉壳的接缝处和冷却壁的完整性,开孔要穿过冷却壁间隙,钻孔直径需与压入配管配套;s3、然后再将冷却壁间耐火材料内衬钻通,到达冷却壁后壁砖衬,将孔内填料清除至砖处;s4、开孔处垂直焊接15厘米长的一端带丝的短管,连接球阀,球阀外接一个短接;s5、联接好灌浆管子,进行压力灌浆;s6、塑性相材料施工机器由操作熟练的技术工人控制压入过程,特别是根据经验判断进行压力控制,压入量的多少根据现场的情况灵活掌握,压入量控制在每孔200~300kg/次。
51.施工完成后高炉冷却壁与炉缸碳砖间热电偶温度降至正常范围内,说明此处高炉炉缸冷却壁与碳砖之间的空隙被塑性相材料所填充,且得益于塑性相材料良好的导热性能,从而使得塑性相材料能够将炉内的热量传递给水冷管排出高炉。
52.可以理解的是,以上实施方式仅仅是为了说明本发明的原理而采用的示例性实施方式,然而本发明并不局限于此。对于本领域内的普通技术人员而言,在不脱离本发明的精神和实质的情况下,可以做出各种变型和改进,这些变型和改进也视为本发明的保护范围。