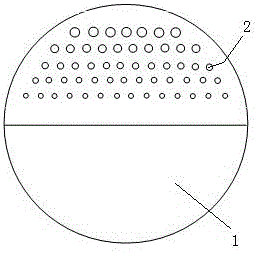
用于晶体硅扩散的匀流板及其晶体硅扩散工艺炉本发明涉及晶体硅扩散装置,具体是指用于晶体硅扩散的匀流板及其晶体硅扩散工艺炉。
背景技术:在晶体硅太阳能电池生产工艺中,目前所普遍采用的是POCL3液态源扩散制作PN结,其原理是,在一个炉体内放置晶体硅,通入工艺气体进行扩散。在扩散过程中,工艺气体通过一个罩杯从炉管尾进入炉内,尾气和未反应的气体通过尾气管从炉口抽出。利用该方法进行扩散,工艺简单,成本较低,因而成为目前晶体硅太阳能电池生产制作PN结的主要方法。由于从炉尾进入的工艺气体温度较低(室温),工艺气体在进入炉内(温度800度左右)后会先下沉,经加热后再上升分散进入硅片中心区域。这样使得炉尾及靠近炉尾区域的方阻均匀性受到一定的影响。为了使整个炉管的硅片有较好的方阻均匀性,通常采用的方法是在进气口添加一个匀流管。但是匀流管存在诸多维护和安全上,成本上的问题。为了进一步改善扩散方阻的均匀性。现有技术的技术方案:目前业内所采用的匀流管结构延伸进炉内,匀流管延伸进炉内的一端封闭,其侧壁处开有开口指向炉顶的出气口。其通过使用匀流管将温度低的工艺气体往上通入到炉体顶部中,这样使得低温的工艺气体在下沉的过程中加热进行扩散。现有技术的缺点:缺点1:由于炉尾进气管通道内的温度要远低于炉内。因此工艺气体在炉内反应生产的P2O5及容易在出气口和匀流管壁上沉积,实践证明,在用过一段时间之后,匀流管靠近进气端的外壁上都会沉积很厚的一层P2O5沉淀。在P2O5沉淀的长期腐蚀作用下,匀流管壁就会被腐蚀穿,最后导致匀流管断裂。现有设计匀流管的使用寿命一般只有1-2个月。这就变相地加大了匀流管的使用成本以及设备的维护时间。缺点2:工艺气体进入炉体内之后,仅仅通过匀流管的上扬作用,再依靠气体自身在管内均匀分布的方法不能很好的达到匀流的左右。上述炉尾区域是指工艺气体进入的区域。
技术实现要素:本发明的目的在于提供用于晶体硅扩散的匀流板及其晶体硅扩散工艺炉,本方案不在进气口增加匀流管,工艺气体通过匀流板再进入炉内,这样不但能解决炉尾区域气体流向问题导致的方阻均匀性问题,对扩散方块电阻的均匀性起到了很好的改善作用,P2O5不会造成匀流板损坏,还不存在多次维护和安全上的问题。本发明的目的主要通过以下技术方案实现:用于晶体硅扩散的匀流板,包括匀流板本体,匀流板本体按照区域划分为炉顶板区域和炉底板区域,炉顶板区域内开有若干匀流通孔,炉底板区域为密封板体。实现原理为:利用匀流板替代匀流管,在匀流板本体上设置分流的匀流通孔,且匀流通孔只位于炉顶板区域,即将匀流板本体安装进工艺炉炉体内后,匀流通孔位于工艺炉炉体上部区域,这样可以造成工艺气体经过匀流通孔后得到上扬,这样工艺气体可以像设置匀流管时一样先流通到多晶硅上方,工艺气体在多晶硅上方开设下沉,被加热后进行扩散,由于匀流板本体在安装时才有密封安装在工艺炉炉体的内壁上,因此P2O5不会对匀流板本体造成的腐蚀。其不存在多次维护的问题,维护成本大大降低。优选的,炉顶板区域和炉底板区域的面积相等。优选的,炉顶板区域和炉底板区域均为半圆形或矩形。优选的,炉顶板区域和炉底板区域以匀流板本体的轴线对称设置。优选的,匀流通孔的大小一致均匀的分布在炉顶板区域内。优选的,匀流通孔的大小从炉顶板区域指向炉底板区域方向由大变小、且同一高度的匀流通孔大小一致的均匀分布在炉顶板区域内。本发明的技术方案,还包括在上述匀流板本体的基础上建立的晶体硅扩散工艺炉,包括工艺炉炉体和上述匀流板本体,匀流板本体横挡在工艺炉炉体内,且匀流板本体的边缘与工艺炉炉体内壁密封连接,且炉顶板区域位于工艺炉炉体上部区域,炉底板区域位于工艺炉炉体下部区域,工艺炉炉体一端设置有进气管,工艺炉炉体内设置有硅片放置区域,匀流板本体位于进气管与有硅片放置区域之间。进气管的轴线与匀流板本体表面垂直。工艺炉炉体内还设置有尾气管,尾气管的进气端位于硅片放置区域远离匀流板本体的一侧,且尾气管沿着工艺炉炉体底部内壁敷设。优选的,尾气管的进气端位于工艺炉炉体内距离匀流通孔最远的点上。上述工艺炉炉体的工作过程为:工艺气体从进气管内进入到工艺炉炉体内,工艺气体在匀流板本体与进气管之间的区域内聚集后,通过匀流通孔上扬到工艺炉炉体内上部区域,在多晶硅上方聚集,由于工艺气体为室温气体,因此进入到工艺炉炉体后的工艺气体会产生下沉现象,因此工艺气体从多晶硅上方往多晶硅下方流动,最后到达工艺炉炉体内底部区域,由尾气管的进气端位于硅片放置区域远离匀流板本体的一侧、且尾气管沿着工艺炉炉体底部内壁敷设,因此可加剧工艺气体由多晶硅上方往多晶硅下方流动的趋势。这样可致使扩散均匀,得到的多晶硅的方阻均匀。本发明的有益效果为:1.在改善炉体内气流均匀性的同时,降低更换成本和维护时间,达到降本增效的效果。2.降低因匀流管被腐蚀断裂而造成的方块电阻异常等风险。3.进一步起到匀流气体的作用,改善扩散后方块电阻的均匀性。附图说明图1为实施例1匀流板本体的示意图。图2为实施例2匀流板本体的示意图。图3为工艺炉炉体的示意图。图4为选取5片多晶硅做实验的多晶硅位置示意图。图5为同一片多晶硅内风阻测试点的位置示意图。具体实施方式下面结合实施例及附图对本发明作进一步的详细说明,但本发明的实施方式不限于此。实施例1:如图1和图3所示。用于晶体硅扩散的匀流板,其特征在于:包括匀流板本体1,匀流板本体1按照区域划分为炉顶板区域和炉底板区域,炉顶板区域内开有若干匀流通孔2,炉底板区域为密封板体。实现原理为:利用匀流板替代匀流管,在匀流板本体1上设置分流的匀流通孔2,且匀流通孔2只位于炉顶板区域,即将匀流板本体1安装进工艺炉炉体3内后,匀流通孔2位于工艺炉炉体3上部区域,这样可以造成工艺气体经过匀流通孔2后得到上扬,这样工艺气体可以像设置匀流管时一样先流通到多晶硅上方,工艺气体在多晶硅上方开设下沉,被加热后进行扩散,由于匀流板本体1在安装时才有密封安装在工艺炉炉体3的内壁上,因此P2O5不会对匀流板本体1造成的腐蚀。其不存在多次维护的问题,维护成本大大降低。优选的,炉顶板区域和炉底板区域的面积相等。优选的,炉顶板区域和炉底板区域均为半圆形。优选的,炉顶板区域和炉底板区域以匀流板本体1的轴线对称设置。优选的,匀流通孔2的大小一致均匀的分布在炉顶板区域内。本发明的技术方案,还包括在上述匀流板本体1的基础上建立的晶体硅扩散工艺炉,包括工艺炉炉体3和上述匀流板本体1,匀流板本体1横挡在工艺炉炉体3内,且匀流板本体1的边缘与工艺炉炉体3内壁密封连接,且炉顶板区域位于工艺炉炉体3上部区域,炉底板区域位于工艺炉炉体3下部区域,工艺炉炉体3一端设置有进气管6,工艺炉炉体3内设置有硅片放置区域,匀流板本体1位于进气管6与有硅片放置区域之间。进气管6的轴线与匀流板本体1表面垂直。工艺炉炉体3内还设置有尾气管7,尾气管7的进气端位于硅片放置区域远离匀流板本体1的一侧,且尾气管7沿着工艺炉炉体3底部内壁敷设。优选的,尾气管7的进气端位于工艺炉炉体3内距离匀流通孔2最远的点上。上述工艺炉炉体3的工作过程为:工艺气体从进气管6内进入到工艺炉炉体3内,工艺气体在匀流板本体1与进气管6之间的区域内聚集后,通过匀流通孔2上扬到工艺炉炉体3内上部区域,在多晶硅上方聚集,由于工艺气体为室温气体,因此进入到工艺炉炉体3后的工艺气体会产生下沉现象,因此工艺气体从多晶硅上方往多晶硅4下方流动,最后到达工艺炉炉体3内底部区域,由尾气管7的进气端位于硅片放置区域远离匀流板本体1的一侧、且尾气管7沿着工艺炉炉体3底部内壁敷设,因此可加剧工艺气体由多晶硅上方往多晶硅下方流动的趋势。这样可致使扩散均匀,得到的多晶硅的方阻均匀。工艺炉炉体3的另一端设置有炉门5,炉门5可以开启或关闭。方便进行装料和卸料。实施例2如图2所示。本实施例与实施例1的区别在于:匀流通孔2的大小从炉顶板区域指向炉底板区域方向由大变小、且同一高度的匀流通孔2大小一致的均匀分布在炉顶板区域内。上述实施例中,匀流通孔2的大小不是均一的,越靠近工艺炉炉体3顶部的地方孔洞越大。优选以百分之十的比例变化,即从工艺炉炉体3顶部到工艺炉炉体3底部方向相邻的匀流通孔2之间的大小比为百分之十。实施例3本实施例在实施例1和实施例2的基础上:匀流通孔2的孔轴线与工艺炉炉体3的轴线呈30度-80度的夹角。匀流通孔2上扬指向工艺炉炉体3顶部。这样可进一步的造成气流上扬。优选80度和60度或80度至60度之间的数据做实验。图中的箭头表示为工艺气体的流向。数据说明:如图4和图5所示,图4中,在工艺炉炉体内部存在500片多晶硅4,500片多晶硅4中等间距的选取5片用于测定方阻数据,如图3所示,5片用于测定方阻数据的多晶硅4分别是:片1A、片2B、片3C、片4D、片5E;如图5,图5为同一个多晶硅4中选取5个测试点用于测试片内的方阻数据,这5个测试点分别是:点1A1、点2B1、点3C1、点4D1、点5E1;实施例3的数据是在实施例2的基础上完成的。点1A1、点2B1、点4D1、点5E1为边缘点;点3C1为中间点。根据上述3个实施例分别做出试验后,得到方阻参数为:片1方阻表:片2方阻表:片3方阻表:片4方阻表:片5方阻表:根据上述方阻表计算得出的不均匀性表:传统技术得到的片间不均匀性和片内不均匀性均在10%以上,本发明相比传统技术而言,具备显著的进步性。如上表,实施例3的数据效果最佳,优选实施例3作为技术实现手段。如上则可较好的实现本发明。