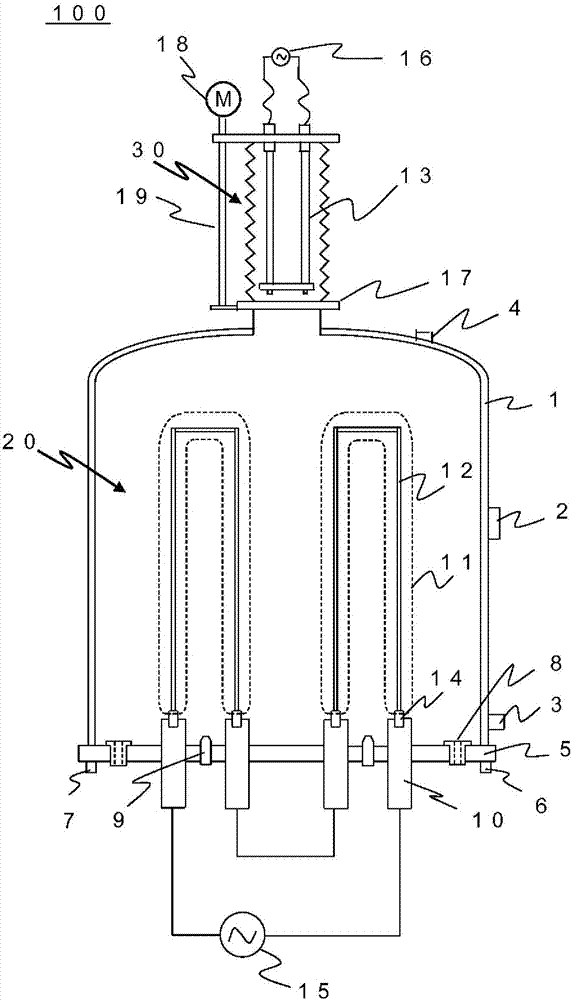
本发明涉及多晶硅的制造技术,更详细而言,涉及为了降低通过西门子法制造的多晶硅中含有的碳浓度而优选的技术。
背景技术:
:多晶硅是半导体器件制造用单晶硅基板、太阳能电池制造用硅基板的原料。通常,多晶硅的制造通过使含有氯硅烷的原料气体与加热后的硅芯线接触而使多晶硅在该硅芯线的表面进行气相生长(cvd:chemicalvapordeposition)的西门子法进行。在通过西门子法使多晶硅气相生长的情况下,沿铅垂方向将2根硅芯线、沿水平方向将1根硅芯线在反应炉内组装成神社大门型(倒u字型),将该组装成神社大门型的硅芯线的两端分别经由碳制的芯线支架而固定于在底板上设置的金属电极。并且,通过从这些金属电极向上述神社大门型硅芯线通电而进行加热。需要说明的是,通常多个神社大门型硅芯线配置在底板上。这样的芯线支架虽然可以直接固定于电极,但是从防止电极的损伤的目的出发,有时也在电极与芯线支架之间设置碳制的适配器(参照专利文献1:日本特开2006-206387号公报,专利文献2:日本特开2013-71856号公报等)。在反应炉(反应器)内,由上述的底板和半球型的容器(钟罩)形成的密闭空间成为用于使多晶硅气相生长的反应空间。金属电极隔着绝缘物而贯通底板,通过配线而与其他的金属电极连接,或者与配置于反应炉外的电源连接。在反应空间内使多晶硅气相生长时,为了防止在神社大门型硅芯线以外的部分也析出多晶硅,而且为了防止装置材料的高温引起的损伤,金属电极、底板及钟罩使用水、油等冷却介质来冷却。芯线支架经由金属电极而被冷却。使反应炉内为氢气氛,使电流从上述金属电极导通而将硅芯线加热成900℃以上且1200℃以下的温度范围并将原料气体从气体喷嘴向反应炉内供给时,硅在硅芯线上进行气相生长,所希望的直径的多晶硅形成为倒u字状。作为上述原料气体,使用例如三氯硅烷与氢的混合气体。需要说明的是,多晶硅的析出工序时的反应炉内的反应压力通常选定0.1mpa~0.9mpa。在多晶硅的析出工序结束后,将反应炉内冷却之后进行大气开放,从反应炉取出多晶硅。另外,硅芯线由多晶或单晶的硅等制作,但是为了高纯度多晶硅制造而使用的硅芯线需要不纯物浓度低的高纯度的硅芯线,具体而言,要求比电阻为500ωcm以上的高电阻的硅芯线。这样的高电阻的硅芯线的通电通常在常温下比电阻高(导电性低),因此通电需要非常高的电压。因此,通常使用比电阻低的芯进行通电,或者预先将硅芯线初始加热成200~400℃而降低比电阻(提高导电性)之后开始通电。为了这样的初始加热,进行如下情况:在反应炉的中央或内周面预先设置初始加热用的碳加热器,在反应开始时,首先通过通电使该碳加热器发热,通过此时产生的辐射热而将配置于碳加热器周边的硅芯线加热至所希望的温度(例如,参照专利文献3)。如果一旦开始向硅芯线的通电,则即使之后不继续进行使用了碳加热器的加热,通过硅芯线自身的发热也能维持表面温度,因此析出反应持续进展。因此,上述的向硅芯线的通电开始后,将碳加热器的电源切断。然后,向反应工序转移而多晶硅向硅芯线上的析出继续,但是加热用碳加热器在初始加热这样的作用结束之后也以原封不动的状态保持在反应炉内。因此,加热用碳加热器尽管不再用于反应,但是曝露于反应炉内的严苛(高温且高速气体流)的环境中,其劣化激烈。在较多的情况下,在1次的使用(一个批次的析出反应)中发生劣化,难以进行多次的使用,成为多晶硅制造的成本上升的主要原因之一。而且,由于是加热用碳加热器在多晶硅的析出空间内放任不管的状态,因此也会成为向析出的多晶硅的碳污染源。尤其是在谋求了析出反应的高效率化的设计的反应炉内,由于高压且高温的析出反应进展,因此存在容易产生来自加热用碳加热器的碳污染的问题。鉴于这样的问题,作为加热用碳加热器的代替,也考虑了通过红外线照射手段对硅芯线进行加热的方法等,但是该方法是来自反应炉外部的加热方法,因此存在需要使用特殊且高价的装置(专利文献4:日本特开平9-241099号公报)、需要通过强度比钢弱的透明石英来制作反应炉壁的一部分(专利文献5:日本特开2001-278611号公报)等难点,作为进行高压下的反应的炉,存在有在安全方面不优选的问题。在先技术文献专利文献专利文献1:日本特开2006-206387号公报专利文献2:日本特开2013-71856号公报专利文献3:日本特开2011-37699号公报专利文献4:日本特开平9-241099号公报专利文献5:日本特开2001-278611号公报专利文献6:美国专利第4179530号说明书技术实现要素:发明要解决的课题本发明鉴于这样的课题而作出,其目的在于提供一种在通过西门子法来制造多晶硅时为了抑制来自碳加热器的碳污染并降低多晶硅中含有的碳浓度而优选的技术。用于解决课题的方案为了解决上述的课题,本发明的多晶硅制造用反应炉是用于通过西门子法来制造多晶硅的反应炉,所述多晶硅制造用反应炉的特征在于,具备:作为使多晶硅析出到硅芯线上的空间部的析出反应部;及作为能够收容所述硅芯线的初始加热用的碳加热器的空间部的加热器收纳部。优选的是,所述多晶硅制造用反应炉具备加热器驱动部,所述加热器驱动部对所述碳加热器的、从所述加热器收容部向所述析出反应部的载入和从所述析出反应部向所述加热器收容部的卸载进行控制。另外,优选的是,所述多晶硅制造用反应炉具备将所述析出反应部与所述加热器收纳部在空间上隔断的能够开闭的开闭器。例如,所述加热器收纳部由波纹管构成。另外,本发明的多晶硅的制造方法是基于西门子法的多晶硅的制造方法,所述多晶硅的制造方法的特征在于,在多晶硅的析出反应工序之前,利用碳加热器对硅芯线进行初始加热,在该硅芯线达到预定的温度之后使所述碳加热器从析出反应空间退避,然后开始所述析出反应工序。发明效果根据本发明,能够降低通过西门子法制造的多晶硅中的碳污染水平,能够高效率地制造高品质的多晶硅。附图说明图1是表示以往的多晶硅制造用反应炉的结构的一例的概略剖视图。图2a是表示本发明的多晶硅制造用反应炉的结构的一例的概略剖视图,是用于说明将碳加热器从析出反应部向加热器收容部卸载的状态的图。图2b是表示本发明的多晶硅制造用反应炉的结构的一例的概略剖视图,是用于说明将碳加热器从加热器收容部向析出反应部载入的状态的图。图3是表示废气中的ch4浓度的析出反应时间依赖性的坐标图。具体实施方式以下,参照附图,说明用于实施本发明的方式。图1是表示以往的多晶硅制造用反应炉200的结构的一例的概略剖视图。反应炉200是通过西门子法使多晶硅在硅芯线12的表面进行气相生长而用于得到多晶硅棒11的装置,具备底板5和钟罩1。在底板5配置有:用于向固定于适配器14的硅芯线12供给电流的硅芯线用电极10;供给氮气、氢气、三氯硅烷气体等工艺气体的原料气体供给喷嘴9;及将废气向外部排出的反应废气出口8。图中的附图标记13所示的结构是硅芯线初始加热用的碳加热器,在初始加热时从碳加热器用电源16被供给电流而进行通电加热,由此将硅芯线12的表面初始加热至所希望的温度。钟罩1具有冷却用冷却介质的入口3和出口4,且具有用于通过目视来确认钟罩内部的状态的窥视窗2。底板5也具有冷却用冷却介质的入口6和出口7。在实际的多晶硅的制造过程中,反应炉进行批次运转。因此,在一个批次结束之后,将钟罩1与底板5分离,从反应炉内部取出多晶硅棒11,进行用于除去钟罩1和底板5的表面附着的副反应物的清扫,安设下一批次的反应用的硅芯线12。此时,在加热用碳加热器13的劣化激烈而处于无法耐受下一反应批次的状况时,更换为新的物品。在该硅芯线12的安设后,在底板5上再次安设钟罩1,首先,进行反应炉内部的氮气置换。氮气从原料气体供给喷嘴9被供给到反应炉内,空气成分从反应废气出口8向外部排出。在该氮气置换完成之后,将供给气体切换为氢气而利用氢气对反应炉内部进行置换。在氢气置换完成后,进行反应炉内的气密测试。该气密测试时的炉内压力大致等于多晶硅的析出反应工序时的炉内压力(0.4~0.9mpa),通过向钟罩1的底面与底板5接触的面浇洒发泡液或者使用氢气检测器等的手法来确认气体有无漏泄。在上述的氢气气密测试完成之后,开始向硅芯线12的加热用的碳加热器13的通电。由此,硅芯线12被加热,由于硅芯线12的温度上升而硅芯线12的比电阻下降,通过从硅芯线用电源15向硅芯线12施加电压而使电流流动。成为通电加热状态的硅芯线12即使没有加热用碳加热器13的热辐射,通过硅芯线12自身的发热也能维持其表面温度。因此,在上述的初始加热工序的完成后,停止向碳加热器13的通电。在初始加热工序完成之后,以氢气为运载气体而从喷嘴9供给作为反应原料气体的氯硅烷气体,由此开始多晶硅的析出反应工序。在图1所示那样的构造的以往的装置中,在该析出反应工序中,硅芯线初始加热用的碳加热器13也与初始加热工序同样地留置在反应炉内。即,尽管碳加热器13不再用于多晶硅的析出反应,但是曝露于在反应炉内持续接受来自多晶硅的辐射热等的严苛(高温且高速气体流)的环境中。反应炉内由于反应气体的热对流引起的循环流和来自气体供给喷嘴9的气体流而产生反应炉内的高速的循环流,因此碳加热器13处于在高温状态下受到气体流的阻力而且受到氢气的攻击的状态。其结果是,劣化激列,在较多的情况下在一个批次的析出反应中发生劣化,难以进行多次的使用。而且,已知有曝露于这样的高温的碳加热器13在炉内与氢气反应而成为甲烷(ch4)的产生源的情况。并且,该甲烷气体进入到析出中的多晶硅,成为碳污染的原因。而且,不仅是硅芯线12,而且在碳加热器13上也局部性地析出多晶硅,因此即便假设劣化不显著而能够再使用,也必须在下一批次的使用之前进行除去多晶硅的作业。因此,在本发明中,采用的是仅在需要硅芯线12的初始加热时将碳加热器13向析出反应空间载入、而在硅芯线12的初始加热结束后将碳加热器13从析出反应空间卸载的结构。通过设为这样的结构,碳加热器13在反应炉内不会受到必要以上的损害,能够抑制其劣化,而且能抑制与炉内的氢气的反应,因此能抑制甲烷(ch4)的产生,也能抑制向通过析出反应而生成的多晶硅的碳污染。此外,由于未产生多晶硅向碳加热器13上的析出,因此在下一批次的使用之前也不需要除去多晶硅。图2a~图2b是表示本发明的多晶硅制造用反应炉的结构的一例的概略剖视图,图2a是用于说明将碳加热器从析出反应部向加热器收容部卸载的状态的图,图2b是用于说明将碳加热器从加热器收容部向析出反应部载入的状态的图。该反应炉100具备作为能够收容硅芯线的初始加热用的碳加热器的空间部的加热器收纳部,在这一点上与图1所示的构造的反应炉200不同。在这样的构造的反应炉中,仅在需要硅芯线12的初始加热时将碳加热器13向析出反应空间20载入,在硅芯线12的初始加热结束后将碳加热器13从析出反应空间向加热器收纳部30卸载。需要说明的是,在上述的图中,附图标记17所示的结构是能将析出反应部20与加热器收纳部30在空间上隔断的能够开闭的开闭器,附图标记18所示的结构是加热器驱动用电动机,附图标记19所示的结构是加热器驱动用滚珠丝杠。在该图所示的例子中,加热器收纳部由波纹管构成,通过加热器驱动用电动机18而旋转的加热器驱动用滚珠丝杠19构成加热器驱动部。即,本发明的多晶硅制造用反应炉是用于通过西门子法来制造多晶硅的反应炉,具备作为使多晶硅析出到硅芯线上的空间部的析出反应部和作为能够收容所述硅芯线的初始加热用的碳加热器的空间部的加热器收纳部。并且,该反应炉具备对所述碳加热器的从所述加热器收容部向所述析出反应部的载入和从所述析出反应部向所述加热器收容部的卸载进行控制的加热器驱动部,还具备将所述析出反应部与所述加热器收纳部在空间上隔断的能够开闭的开闭器。上述加热器收纳部例如由波纹管构成。使用了这样的构造的反应炉的多晶硅的制造方法的特征在于,在多晶硅的析出反应工序之前,利用碳加热器对硅芯线进行初始加热,在该硅芯线到达预定的温度之后使所述碳加热器从析出反应空间退避,然后开始所述析出反应工序。作为用于解决上述的以往构造的反应炉具有的问题的方法,也已知有在开始多晶硅的析出工序时的点火完成后将反应炉的上部开放而将碳加热器13向炉外拔出的手法(专利文献6:美国专利第4179530号说明书)。然而,在该方法中,无法在氢气氛下进行上述点火。因此,需要利用惰性气体对析出反应空间进行净化,花费工序上的劳力和时间。相对于此,在本发明中,不需要利用惰性气体对析出反应空间进行净化。实施例在本实施例中,测定了使用图2a~图2b所示的构造的反应炉使多晶硅析出时的、(a)反应中的废气含有的甲烷的浓度及(b)生成的多晶硅中含有的碳浓度(实施例:批次1)。而且,为了进行比较,也测定了使用图1所示那样的以往构造的反应炉生成时的、(a)反应中的废气含有的甲烷的浓度及(b)生成的多晶硅中含有的碳浓度(比较例:批次2)。图3是表示废气中的ch4浓度的析出反应时间依赖性的坐标图。在实施例的情况下,ch4浓度经过析出反应工序(72小时)而废气甲烷浓度为检测下限以下(小于0.100volppm)。相对于此,在比较例的情况下,随着析出反应工序进展而ch4浓度升高,最大废气甲烷浓度成为0.213volppm。将两者的比较结果汇总在表1中。【表1】实施例:批次1比较例:批次n2反应温度1,160℃1,160℃反应压力0.5mpa0.5mpa硅烷源三氯硅烷三氯硅烷最终直径121mmφ120mmφ反应时间72小时72小时废气最大甲烷浓度小于0.100volppm0.213volppm多晶中碳浓度10ppba以下80ppba根据表1所示的结果,在实施例中,废气最大甲烷浓度小于0.100volppm(检测下限以下),多晶中碳浓度为10ppba以下,相对于此,在比较例中,废气最大甲烷浓度为0.213volppm,多晶中碳浓度成为80ppba。即,废气最大甲烷浓度被抑制成一半以下,其结果是,多晶中碳浓度减少一位数程度。工业实用性本发明提供一种在通过西门子法制造多晶硅时为了抑制来自碳加热器的碳污染并降低多晶硅中含有的碳浓度而优选的技术。附图标记说明1钟罩2窥视窗3冷却介质入口(钟罩)4冷却介质出口(钟罩)5底板6冷却介质入口(底板)7冷却介质出口(底板)8反应废气出口9原料气体供给喷嘴10硅芯线用电极11多晶硅棒12硅芯线13碳加热器14硅芯线用适配器15硅芯线用电源16碳加热器用电源17开闭式开闭器18加热器驱动用电动机19加热器驱动用滚珠丝杠20析出反应空间30加热器收纳部100、200反应炉当前第1页12