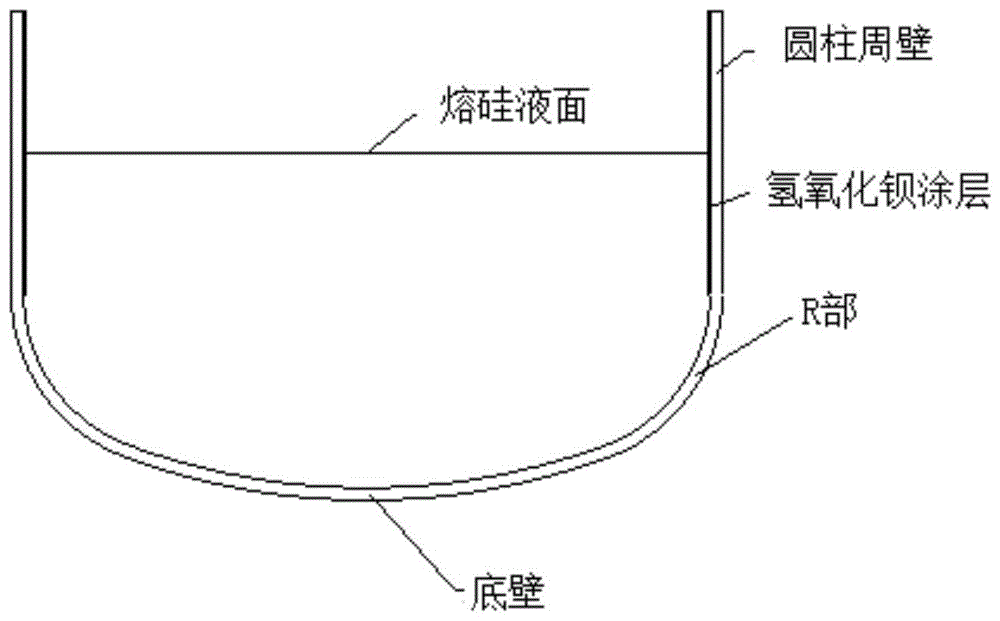
本发明涉及单晶硅生产
技术领域:
,尤其涉及一种减少直拉单晶硅内部气孔的方法。
背景技术:
:目前,在单晶炉中拉制硅棒的主要步骤包括装料、抽空、熔料、稳定化、引晶、放肩、等径、收尾环节。装料环节即将硅料(包括掺杂剂)装入单晶石英坩埚中,通过单晶炉内加热系统将硅料熔化,之后降低加热器功率将熔体稳定在适当温度,之后开始进行晶体生长。在整个工艺过程中,单晶炉内处于减压状态。为了能够及时带走拉晶过程中产生的杂质,单晶炉内需要不断通入氩气。然而,在熔料步骤中,硅料熔化后的熔硅中会夹杂大量的气泡,由于熔硅的粘度较高且受到其内部压力影响,气泡不容易排除;同时,单晶石英坩埚,尤其是涂层石英坩埚(涂层石英坩埚内表面覆盖氢氧化钡,所以表面更加粗糙,但由于拉晶过程中与二氧化硅反应可以形成致密保护层,提高成晶率)内壁相对粗糙的部分,比较容易吸附气泡。拉晶过程中,这些气泡可能会进入晶体内部,在晶棒内部形成气孔。切片环节有气孔的硅片为不合格品(残次品),只能作为回收硅料使用,造成合格率降低,成本升高。此外,熔硅与石英坩埚反应剧烈,会产生大量sio气体,若不能及时排出,也有可能会形成气孔,且sio气体冷却后会在炉内沉积,在晶体生长阶段容易掉落造成断棱(晶体失去单晶结构),同样也会造成成品率下降,成本增加。技术实现要素:针对现有直拉单晶硅生产过程中存在的上述技术问题,本发明提供一种减少直拉单晶硅内部气孔的方法。为达到上述发明目的,本发明实施例采用了如下的技术方案:一种减少直拉单晶硅内部气孔的方法,包括如下步骤:s1:将石英坩埚加热至预设温度后,将氢氧化钡溶液均匀喷涂于所述石英坩埚的圆柱周壁内侧形成氢氧化钡涂层;s2:向所述石英坩埚内装料,抽空至炉内压力为5~15torr,调节氩气流量为50~60l/min,将单晶炉的加热器功率调节至熔料功率,所述石英坩埚的转速保持在第一预设转速,直至单晶硅原料全部熔化;s3:将所述石英坩埚逐步上升,使熔硅液面处于单晶炉的导流筒下方的预设位置,将石英坩埚的转速升至第二预设转速,将加热器功率调节至引晶功率,调节炉内压力至15~20torr,调节氩气流量至30~40l/min,进行引晶、放肩生长、等径生长和收尾生长。其中,所述石英坩埚的坩埚壁包括底壁、弧度过渡区(r部)及圆柱周壁三个部分。相对于现有技术,本发明提供的减少直拉单晶硅内部气孔的方法,先对石英坩埚进行预处理,仅在石英坩埚的圆柱周壁内侧喷涂氢氧化钡溶液形成氢氧化钡涂层,而石英坩埚的底壁和r部均未涂覆氢氧化钡涂层,保证成品率的同时减少气泡在坩埚表面的附着;熔料阶段采用合适的压力和氩气流量,保证气泡排除同时减少sio沉积,保证后续晶体生长的稳定性;原料硅全部熔化后,稳定化阶段通过提升坩埚转速加强熔体对流,进一步带走气泡。本发明通过对石英坩埚预处理和工艺参数的调控,同时减少了石英坩埚附着和熔体中的气泡,抑制了晶棒内部气孔的产生,保证了单晶硅生长的稳定性,有利于提升成品率并降低成本。进一步地,所述氢氧化钡涂层的上边缘与熔硅液面之间的距离为30-150mm,所述氢氧化钡涂层的下边缘与熔硅液面之间的距离为30-150mm。使用无涂层石英坩埚,对熔硅液面液位线附近的石英坩埚的圆柱周壁内侧进行涂层处理,而石英坩埚的底壁和r部不进行喷涂(如图1所示),氢氧化钡涂层在石英坩埚的圆柱周壁内侧上形成致密保护层(硅酸钡),保证晶体生长稳定性,且上部熔硅压力相对较小,温度较高对流较强(靠近加热器),气泡相对更容易被带走排出;r部和底壁由于没有涂层,气泡附着相对较少,进一步降低晶体内部产生气泡的可能。进一步地,步骤s1中,所述预设温度为200~300℃,在坩埚圆柱周壁内侧表面形成氢氧化钡涂层,进而与空气中的二氧化碳反应形成碳酸钡涂层。进一步地,步骤s1中,所述氢氧化钡溶液的质量浓度为1%~3%,喷涂时间为1~3min。进一步地,步骤s2中,所述熔料功率为80~100kw,保证加热温度达到1412℃以上,保证熔料效果的同时减弱熔硅与石英坩埚的反应,减少sio的产生。进一步地,步骤s2中,所述第一预设转速为0.6~0.8rpm/min,加快原料硅的熔化,并有助于气泡的排出。进一步地,步骤s2中,所述预设位置距导流筒下沿20~30mm。进一步地,步骤s3中,所述引晶功率为60~80kw,保证熔硅稳定的同时,进一步地减少sio的产生,保证后续晶体生长的稳定性。进一步地,步骤s3中,所述第二预设转速为1~2rpm/min,通过与导流筒配合,保证熔硅液面的稳定同时增强熔体内部对流,通过对流作用将熔体内气泡进一步排除,保证后续晶体生长的稳定性,提高成品率。进一步地,步骤s3中,所述石英坩埚以1~2rpm/min运行1~1.2h,进行熔体稳定化。附图说明图1是本发明实施例中的石英坩埚示意图。具体实施方式为了使本发明的目的、技术方案及优点更加清楚明白,以下结合实施例,对本发明进行进一步详细说明。应当理解,此处所描述的具体实施例仅仅用以解释本发明,并不用于限定本发明。本发明实施例提供一种减少直拉单晶硅内部气孔的方法,包括如下步骤:s1:将石英坩埚加热至预设温度后,将氢氧化钡溶液均匀喷涂于所述石英坩埚的圆柱周壁内侧形成氢氧化钡涂层,而石英坩埚的底壁和r部不进行喷涂;s2:向所述石英坩埚内装料,抽空至炉内压力为5~15torr,调节氩气流量为50~60l/min,将单晶炉的加热器功率调节至熔料功率,所述石英坩埚的转速保持在第一预设转速,直至单晶硅原料全部熔化;s3:将所述石英坩埚逐步上升,使熔硅液面处于距单晶炉的导流筒下沿20~30mm的位置,将石英坩埚的转速升至第二预设转速,将加热器功率调节至引晶功率,调节炉内压力至15~20torr,调节氩气流量至30~40l/min,进行引晶,然后再按直拉单晶硅的常规方法进行放肩生长、等径生长和收尾生长。具体地,现有技术主要是依靠坩埚旋转变化,对熔体进行搅拌带走气泡。该方法对熔体中的存在气泡效果较好,但对吸附于石英坩埚壁的气泡作用不明显。主要是由于接近坩埚壁后熔体流动将由湍流变为层流,也是是流速减缓,所以熔体搅拌对带走坩埚壁附近气泡能力较弱。再加上现有技术中绝大部分使用的是涂层坩埚,而涂层坩埚由于表面比较粗糙,气泡更容易附着,尤其是坩埚的r部和底壁,这是由于底部受熔硅压力和对流的影响,造成气泡更不容易排出。本发明在步骤s1中,仅对石英坩埚圆柱周壁内侧进行涂层处理,而石英坩埚的底壁和r部不进行喷涂,保证成品率的同时减少气泡在坩埚表面的附着,有利于气泡的排出。同时,现有技术中熔料采用低压力(280~500pa)和低氩气流量(10~15l/min)。然而,由于熔料阶段加热器功率较高,熔硅与石英坩埚反应剧烈,会产生大量sio气体。如果采用低压力容易使sio挥发加剧;而采用低氩气流量则挥发出来的sio气体不容易被带走。大量的sio气体冷却后会在炉内沉积,在晶体生长阶段容易掉落造成断棱(晶体失去单晶结构),造成成品率下降,成本增加。本申请在步骤s2中,通过调节炉内压力及氩气流量保证气泡被排除的同时抑制了sio的大量产生,并能够保证sio被及时带走排出,防止sio沉积对晶体生长的影响。此外,本申请在步骤s3中,通过调节熔硅液面与导流筒的距离,以及提升石英坩埚的转速,保证熔硅液面的稳定同时增强熔体内部对流,通过对流作用将熔体内气泡进一步排除,实现稳定化,然后,再调节炉内压力及氩气流量,减少液面抖动,保证sio被及时带走的同时降低氩气消耗,保证后续晶体生长的稳定性,提高成品率并降低成本。为了更好的说明本发明实施例提供的减少直拉单晶硅内部气孔的方法,下面通过实施例做进一步的举例说明。实施例1一种减少直拉单晶硅内部气孔的方法,包括如下步骤:s1:采用22寸单晶热场,石英坩埚(外径22寸)高度385mm,单晶硅原料投料量120kg(全部熔化后熔硅液面液位线在石英坩埚上沿以下约130mm处),将石英坩埚加热至200℃后,将质量浓度为2%的氢氧化钡溶液均匀喷涂于石英坩埚的圆柱周壁内侧,喷涂时间为为2min,使形成的氢氧化钡涂层的上边缘和下边缘与熔硅液面之间的距离均为100mm(如图1所示);s2:向上述石英坩埚内装入单晶硅原料,抽空至炉内压力为10torr,调节氩气流量为50l/min,将单晶炉的加热器功率调节至85kw,将石英坩埚的转速保持在0.7rpm/min,直至单晶硅原料全部熔化;s3:将上述石英坩埚逐步上升,使熔硅液面处于距单晶炉的导流筒下沿30mm的位置,将石英坩埚的转速升至2rpm/min,将加热器功率调节至70kw,石英坩埚以2rpm/min运行1h后,完成稳定化,调节炉内压力至15torr,调节氩气流量至30l/min,进行引晶,然后再按直拉单晶硅的常规方法进行放肩生长、等径生长和收尾生长,得到单晶硅棒。实施例2一种减少直拉单晶硅内部气孔的方法,包括如下步骤:s1:采用22寸单晶热场,石英坩埚(外径22寸)高度385mm,单晶硅原料投料量120kg(全部熔化后熔硅液面液位线在石英坩埚上沿以下约130mm处),将石英坩埚加热至300℃后,将质量浓度为3%的氢氧化钡溶液均匀喷涂于石英坩埚的圆柱周壁内侧,喷涂时间为为1min,使形成的氢氧化钡涂层的上边缘和下边缘与熔硅液面之间的距离均为30mm;s2:向上述石英坩埚内装入单晶硅原料,抽空至炉内压力为15torr,调节氩气流量为60l/min,将单晶炉的加热器功率调节至100kw,将石英坩埚的转速保持在0.8rpm/min,直至单晶硅原料全部熔化;s3:将上述石英坩埚逐步上升,使熔硅液面处于距单晶炉的导流筒下沿25mm的位置,将石英坩埚的转速升至1.5rpm/min,将加热器功率调节至80kw,石英坩埚以1.5rpm/min运行1.2h后,完成稳定化,调节炉内压力至20torr,调节氩气流量至40l/min,进行引晶,然后再按直拉单晶硅的常规方法进行放肩生长、等径生长和收尾生长,得到单晶硅棒。实施例3一种减少直拉单晶硅内部气孔的方法,包括如下步骤:s1:采用22寸单晶热场,石英坩埚(外径22寸)高度385mm,单晶硅原料投料量120kg(全部熔化后熔硅液面液位线在石英坩埚上沿以下约130mm处),将石英坩埚加热至250℃后,将质量浓度为1%的氢氧化钡溶液均匀喷涂于石英坩埚的圆柱周壁内侧,喷涂时间为为3min,使形成的氢氧化钡涂层的上边缘和下边缘与熔硅液面之间的距离均为80mm;s2:向上述石英坩埚内装入单晶硅原料,抽空至炉内压力为5torr,调节氩气流量为55l/min,将单晶炉的加热器功率调节至80kw,将石英坩埚的转速保持在0.6rpm/min,直至单晶硅原料全部熔化;s3:将上述石英坩埚逐步上升,使熔硅液面处于距单晶炉的导流筒下沿20mm的位置,将石英坩埚的转速升至1rpm/min,将加热器功率调节至60kw,石英坩埚以1rpm/min运行1.2h后,完成稳定化,调节炉内压力至18torr,调节氩气流量至35l/min,进行引晶,然后再按直拉单晶硅的常规方法进行放肩生长、等径生长和收尾生长,得到单晶硅棒。为了更好的说明本发明的技术方案,下面还通过对比例和本发明的实施例做进一步的对比。对比例1采用涂层石英坩埚一种减少直拉单晶硅内部气孔的方法,在实施例1的基础上将石英坩埚替换为全涂层石英坩埚,具体包括如下步骤:s1:采用22寸单晶热场,石英坩埚(外径22寸)高度385mm,单晶硅原料投料量120kg(全部熔化后熔硅液面液位线在石英坩埚上沿以下约130mm处),将石英坩埚加热至200℃后,将质量浓度为2%的氢氧化钡溶液均匀喷涂于石英坩埚的内表面(圆柱周壁内侧、底壁及r部),形成氢氧化钡涂层;s2:向上述石英坩埚内装入单晶硅原料,抽空至炉内压力为10torr,调节氩气流量为50l/min,将单晶炉的加热器功率调节至85kw,将石英坩埚的转速保持在0.7rpm/min,直至单晶硅原料全部熔化;s3:将上述石英坩埚逐步上升,使熔硅液面处于距单晶炉的导流筒下沿30mm的位置,将石英坩埚的转速升至2rpm/min,将加热器功率调节至70kw,石英坩埚以2rpm/min运行1h后,完成稳定化,调节炉内压力至15torr,调节氩气流量至30l/min,进行引晶,然后再按直拉单晶硅的常规方法进行放肩生长、等径生长和收尾生长,得到单晶硅棒。对比例2一种减少直拉单晶硅内部气孔的方法,在实施例1的基础上,并采用低压力和低氩气流量,具体包括如下步骤:s1:采用22寸单晶热场,石英坩埚(外径22寸)高度385mm,单晶硅原料投料量120kg(全部熔化后熔硅液面液位线在石英坩埚上沿以下约130mm处),将石英坩埚加热至200℃后,将质量浓度为2%的氢氧化钡溶液均匀喷涂于石英坩埚的圆柱周壁内侧,喷涂时间为为2min,使形成的氢氧化钡涂层的上边缘和下边缘与熔硅液面之间的距离均为100mm;s2:向上述石英坩埚内装入单晶硅原料,抽空至炉内压力为500pa(3.75torr),调节氩气流量为15l/min,将单晶炉的加热器功率调节至85kw,将石英坩埚的转速保持在0.7rpm/min,直至单晶硅原料全部熔化;s3:将上述石英坩埚逐步上升,使熔硅液面处于距单晶炉的导流筒下沿30mm的位置,将石英坩埚的转速升至2rpm/min,将加热器功率调节至70kw,石英坩埚以2rpm/min运行1h后,完成稳定化,调节炉内压力至900pa(6.75torr),调节氩气流量至30l/min,进行引晶,然后再按直拉单晶硅的常规方法进行放肩生长、等径生长和收尾生长,得到单晶硅棒。对比例3一种减少直拉单晶硅内部气孔的方法,在实施例1的基础上将石英坩埚替换为全涂层石英坩埚,并采用低压力和低氩气流量,具体包括如下步骤:s1:采用22寸单晶热场,石英坩埚(外径22寸)高度385mm,单晶硅原料投料量120kg(全部熔化后熔硅液面液位线在石英坩埚上沿以下约130mm处),将石英坩埚加热至200℃后,将质量浓度为2%的氢氧化钡溶液均匀喷涂于石英坩埚的内表面(圆柱周壁内侧、底壁及r部),形成氢氧化钡涂层;s2:向上述石英坩埚内装入单晶硅原料,抽空至炉内压力为500pa(3.75torr),调节氩气流量为15l/min,将单晶炉的加热器功率调节至85kw,将石英坩埚的转速保持在0.7rpm/min,直至单晶硅原料全部熔化;s3:将上述石英坩埚逐步上升,使熔硅液面处于距单晶炉的导流筒下沿30mm的位置,将石英坩埚的转速升至2rpm/min,将加热器功率调节至70kw,石英坩埚以2rpm/min运行1h后,完成稳定化,调节炉内压力至900pa(6.75torr),调节氩气流量至30l/min,进行引晶,然后再按直拉单晶硅的常规方法进行放肩生长、等径生长和收尾生长,得到单晶硅棒。为了更好的说明本发明实施例提供的减少直拉单晶硅内部气孔的方法的特性,下面将实施例1、2、3及对比例1、2、3制备的单晶硅棒进行超声波检测,与对比例相比本发明实施例提供的单晶硅棒内部缺陷明显减少。同时,将实施例1、2、3及对比例1、2、3制备的单晶硅棒进行切片得到硅片,统计所得硅片中的气孔片(残次品)数量,结果如表1所示。表1序号硅片总数/片气孔片数/片次品率实施例1600060.1%实施例2600090.15%实施例3600060.1%对比例16000130.22%对比例26000120.2%对比例36000150.25%由以上数据可知,本发明实施例提供的减少直拉单晶硅内部气孔的方法,能够同时减少石英坩埚表面附着和熔体中的气泡,抑制晶体内部气孔的产生,保证了单晶硅生长的稳定性,使次品率降低25%以上,有利于提升良品率并降低成本。以上所述仅为本发明的较佳实施例而已,并不用以限制本发明,凡在本发明的精神和原则之内所作的任何修改、等同替换或改进等,均应包含在本发明的保护范围之内。当前第1页12