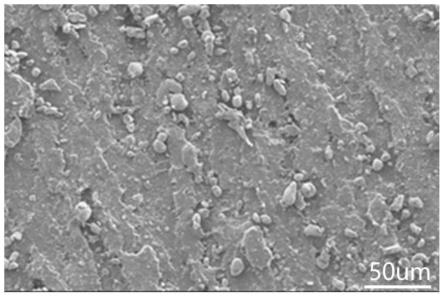
1.本发明涉及一种力学性能优异的不发泡聚氨酯弹性体的制备方法,属于聚氨酯弹性体技术领域。
背景技术:2.聚氨酯弹性体是一种应用广泛的弹性体材料,因其原料的可选择性广泛及特殊的微相分离结构,具有优异的力学强度、韧性、耐磨、耐油性等特点,可应用到鞋材、管材、薄膜和片材、线缆、汽车、建筑、医药卫生、国防等许多领域。
3.在聚氨酯弹性体的制备过程中,若加入水等发泡剂可制得发泡聚氨酯弹性体,制品中存在大量的泡孔结构,因此力学性能相对较差,主要用来减振降噪、保温隔热等;若不添加发泡剂,则得到不发泡聚氨酯弹性体,由于没有泡孔、结构致密,具有优异的力学性能,主要用于汽车部件、管材、建筑等领域。然而,在不发泡聚氨酯弹性体的制备过程中难免会引入气泡等缺陷,而且由于凝胶化速度快,没有足够的时间进行固化前的脱泡处理,从而不能达到理论的力学性能。
技术实现要素:4.针对现有技术存在的问题,本发明提供一种力学性能优异的不发泡聚氨酯弹性体的制备方法,通过调控各组分的含量,尤其是严格控制催化剂的含量,同时优化真空脱泡处理的工艺条件,来控制凝胶化反应程度,以有足够的时间进行成型前的脱泡处理,从而有效除去制备过程中引入气泡,进而能够在不影响其他性能的情况下进一步提高不发泡聚氨酯弹性体的强度和韧性。
5.本发明的目的是通过以下技术方案实现的。
6.一种力学性能优异的不发泡聚氨酯弹性体的制备方法,所述方法包括以下步骤:
7.将预热至(30
±
2)℃的a组分以及b组分在1900rpm~2200rpm的转速下搅拌混合(25
±
5)s,然后置于真空度≤0.09mpa的条件下真空脱泡8min~10min,再装入预热至(75
±
5)℃的模具中,之后先放入(75
±
5)℃烘箱中固化1h~1.5h,再在(25
±
5)℃下固化(48
±
5)h,得到力学性能优异的不发泡聚氨酯弹性体。
8.所述a组分由分子量为2000的聚四氢呋喃醚二醇(ptmeg2000)、分子量为4950的聚氧化丙烯三醇(330n)、1,4-丁二醇(bdo)、广州德田新材料公司型号为x-313的消泡剂以及二月桂酸二丁基锡(t-12)混合配制而成;其中,a组分中各成分的质量份数如下:ptmeg2000 70~71份,330n 19~20份,bdo 7.3~7.5份,x-313 1.8~2.0份以及t-12 0.0003~0.002份;
9.所述b组分是由含有-nco基团的异氰酸酯与ptmeg2000反应形成的nco含量在12%~13%之间的预聚体;
10.另外,a组分中-oh基团与b组分中-nco基团的摩尔比为(1.03~1.07):1;ptmeg2000、330n以及bdo的含水量均小于等于500ppm。
11.进一步地,所述b组分是由含有-nco基团的异氰酸酯与ptmeg2000在(80~85)℃下搅拌反应(3.8~4.2)h形成的nco含量在12%~13%之间的预聚体。
12.进一步地,含有-nco基团的异氰酸酯为4,4
’‑
二苯基甲烷二异氰酸酯(mdi);此时,b组分中各成分的质量份数如下:ptmeg2000 54~57份以及mdi 44~47份。
13.进一步地,先将t-12溶解到330n中,再与ptmeg2000、bdo以及x-313混合。
14.进一步地,a组分中t-12的质量份数为0.0003~0.0005。
15.有益效果:
16.(1)本发明通过调控各组分的含量,尤其是催化剂的含量,以调控体系的凝胶化反应速率,同时优化制备过程中工艺参数,尽量避免制备过程中引入气泡,而且还有足够的时间进行成型前的脱泡处理以除去引入的气泡,降低制品缺陷,从而得到几乎无泡孔且具有高强度以及良好韧性的聚氨酯弹性体。
17.(2)由于催化剂的含量对于反应体系凝胶化的速率影响非常大,所以本发明尽量降低催化剂的含量,而催化剂含量太低不易于精确控制,所以本发明先将低含量的催化剂加入与其不反应的高含量330n中进行稀释,然后再将含有催化剂的330n与ptmeg2000、bdo以及x-313混合,从而实现对低含量催化剂的精确控制,操作简便。
18.(3)本发明所述方法操作简单,有效降低了不发泡聚氨酯弹性体中的泡孔缺陷,使制备的聚氨酯弹性体的拉伸强度≥18mpa以及断裂伸长率>700%,具有很好的应用前景。
附图说明
19.图1为实施例1制备的不发泡聚氨酯弹性体的拉伸断面的扫描电子显微镜(sem)图。
20.图2为对比例1制备的不发泡聚氨酯弹性体的表面扫描电子显微镜图。
21.图3为对比例2制备的不发泡聚氨酯弹性体的表面扫描电子显微镜图。
具体实施方式
22.下面结合具体实施方式对本发明作进一步阐述,其中,所述方法如无特别说明均为常规方法,所述原材料如无特别说明均能从公开商业途径获得。
23.实施例1
24.(1)分别采用水泵、油泵对ptmeg2000、330n以及bdo进行真空脱水处理,直至含水量小于等于500ppm;
25.(2)将0.005份的t-12溶解到250份脱水后的330n中进行稀释并混合均匀,得到含有t-12的330n;将70.9份脱水后的ptmeg2000、19.7份含有t-12的330n、7.4份脱水后的bdo以及1.9份x-313(广州德田新材料公司型号为x-313的消泡剂)混合均匀,得到组分a;
26.将45份mdi和55份ptmeg在氮气保护气氛下混合均匀,并于80℃~85℃下搅拌反应4h,得到以-nco封端的预聚体,简记为b组分且其nco含量为12.5%;
27.(3)将a组分以及b组分分别预热至30℃,然后按照a组分中-oh基团与b组分中-nco基团1.05的摩尔比将预热后的a组分与b组分混合(即将53.4份a组分与46.6份b组分混合),并在2000rpm的转速下搅拌混合30s,然后置于真空度≤0.09mpa的条件下真空脱泡10min,再装入预热至70℃的模具中,之后先放入70℃烘箱中固化1.5h,再在25℃下固化48h,得到
力学性能优异的不发泡聚氨酯弹性体。
28.对所制备的不发泡聚氨酯弹性体进行微观形貌表征,从图1中的sem图片可以看出,该聚氨酯弹性体拉伸断面无明显气泡,说明制备过程中脱泡完全。参照标准gb/t1040.3-2006对所制备的不发泡聚氨酯弹性体的拉伸强度以及断裂伸长率进行测试,测得该聚氨酯弹性体的拉伸强度为19.18mpa以及断裂伸长率为782%。
29.实施例2
30.(1)分别采用水泵、油泵对ptmeg2000、330n以及bdo进行真空脱水处理,直至含水量小于等于500ppm;
31.(2)将0.0045份的t-12溶解到250份脱水后的330n中进行稀释并混合均匀,得到含有t-12的330n;将70.8份脱水后的ptmeg2000、19.5份含有t-12的330n、7.5份脱水后的bdo以及1.8份x-313(广州德田新材料公司型号为x-313的消泡剂)混合均匀,得到组分a;
32.将44份mdi和56份ptmeg在氮气保护气氛下混合均匀,并于80℃~85℃下搅拌反应4.2h,得到以-nco封端的预聚体,简记为b组分且其nco含量为12.6%;
33.(3)将a组分以及b组分分别预热至28℃,然后按照a组分中-oh基团与b组分中-nco基团1.07的摩尔比将预热后的a组分与b组分混合(即将53份a组分与47份b组分混合),并在2200rpm的转速下搅拌混合30s,然后置于真空度≤0.09mpa的条件下真空脱泡8min,再装入预热至75℃的模具中,之后先放入75℃烘箱中固化1h,再在28℃下固化50h,得到力学性能优异的不发泡聚氨酯弹性体。
34.对所制备的不发泡聚氨酯弹性体进行微观形貌表征,可以观察到所制备聚氨酯弹性体中无明显的泡孔缺陷,说明制备过程中脱泡完全。参照标准gb/t1040.3-2006对所制备的不发泡聚氨酯弹性体的拉伸强度以及断裂伸长率进行测试,测得该聚氨酯弹性体的拉伸强度为18.68mpa以及断裂伸长率为745%。
35.对比例1
36.(1)分别采用水泵、油泵对ptmeg2000、330n以及bdo进行真空脱水处理,直至含水量小于等于500ppm;
37.(2)将70.9份脱水后的ptmeg2000、19.7份330n、0.1份t-12、7.4份脱水后的bdo以及1.9份x-313(广州德田新材料公司型号为x-313的消泡剂)混合均匀,得到组分a;
38.将45份mdi和55份ptmeg在氮气保护气氛下混合均匀,并于80℃~85℃下搅拌反应4h,得到以-nco封端的预聚体,简记为b组分且其nco含量为12.9%;
39.(3)将a组分以及b组分分别预热至30℃,然后按照a组分中-oh基团与b组分中-nco基团1.05的摩尔比将预热后的a组分与b组分混合(即将53.7份a组分与46.3份b组分混合),并在2000rpm的转速下搅拌混合30s,然后置于真空度≤0.09mpa的条件下真空脱泡10min,再装入预热至70℃的模具中,之后先放入70℃烘箱中固化1.5h,再在25℃下固化48h,得到不发泡聚氨酯弹性体。
40.对所制备的不发泡聚氨酯弹性体进行微观形貌表征,从图2中的sem图片可以看出,该聚氨酯弹性体中存在明显的泡孔,说明制备过程中脱泡不完全。参照标准gb/t1040.3-2006对所制备的不发泡聚氨酯弹性体的拉伸强度以及断裂伸长率进行测试,测得该聚氨酯弹性体的拉伸强度为11.76mpa以及断裂伸长率为484%。
41.对比例2
42.(1)分别采用水泵、油泵对ptmeg2000、330n以及bdo进行真空脱水处理,直至含水量小于等于500ppm;
43.(2)将0.02份的t-12溶解到250份脱水后的330n中进行稀释并混合均匀,得到含有t-12的330n;将70.9份脱水后的ptmeg2000、19.7份含有t-12的330n、7.4份脱水后的bdo以及1.9份x-313(广州德田新材料公司型号为x-313的消泡剂)混合均匀,得到组分a;
44.将45份mdi和55份ptmeg在氮气保护气氛下混合均匀,并于80℃~85℃下搅拌反应4h,得到以-nco封端的预聚体,简记为b组分且其nco含量12.6%;
45.(3)将a组分以及b组分分别预热至30℃,然后按照a组分中-oh基团与b组分中-nco基团1.05的摩尔比将预热后的a组分与b组分混合(即将53份a组分与47份b组分混合),并在1700rpm的转速下搅拌混合16s,然后置于真空度≤0.09mpa的条件下真空脱泡7min,再装入预热至65℃的模具中,之后先放入70℃烘箱中固化1.5h,再在18℃下固化48h,得到不发泡聚氨酯弹性体。
46.对所制备的不发泡聚氨酯弹性体进行微观形貌表征,从图3中的sem图片可以看出,该聚氨酯弹性体中存在明显的泡孔,说明制备过程中脱泡不完全。参照标准gb/t1040.3-2006对所制备的不发泡聚氨酯弹性体的拉伸强度以及断裂伸长率进行测试,测得该聚氨酯弹性体的拉伸强度为15.25mpa以及断裂伸长率为602%。
47.根据实施例1~2以及对比例1~2所制备的聚氨酯弹性体的力学性能可知,本发明通过对催化剂含量进行调控以及优化制备过程的工艺参数,能够通过脱泡有效除去制备过程中引入的气泡,降低制品中的泡孔缺陷,从而明显提高聚氨酯弹性体的拉伸强度以及断裂伸长率。
48.综上所述,以上仅为本发明的较佳实施例而已,并非用于限定本发明的保护范围。凡在本发明的精神和原则之内,所作的任何修改、等同替换、改进等,均应包含在本发明的保护范围之内。