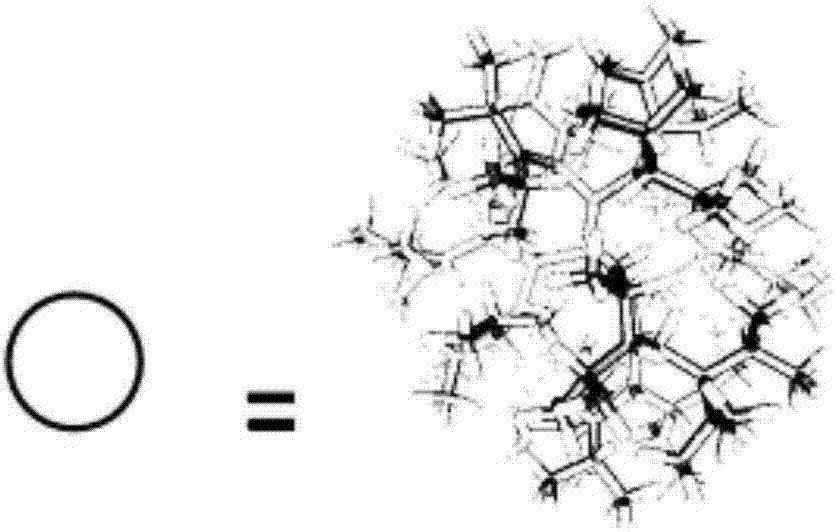
本发明公开一种具有良好耐刮擦性和耐溶剂腐蚀性的用于汽车面漆和其他类似应用的透明涂料。
背景技术:可用于汽车涂装和相关应用领域有多种多样的多组分的涂料组合物。已知包含酸酐或环氧组分的许多种涂料组合物。用于汽车和相关应用的现有涂料组合物的关注点在于耐刮擦性并不是希望中那么好。涂料组合物在干燥(耐擦伤性)或潮湿(耐汽车清洗性)条件下抵御暴露于意外划伤的能力是考察涂料组合物耐刮擦性的重要方面。现有技术描述了在涂料制备过程中将无机颗粒尤其是纳米二氧化硅作为添加剂添加来改性的涂料组合物,所述无机颗粒迁移到涂层表面(表面分层过程),提供了所需的耐刮擦性。但经常存在关于处理方面的问题以及随着时间的推移纳米二氧化硅颗粒从涂层表面逐渐磨损而导致涂料耐刮擦性能损耗的问题。一般的改进方法是使用表面处理过的纳米二氧化硅颗粒,使其能均匀分布在涂层干膜中;或者是将纳米二氧化硅颗粒接枝到聚合物骨架上使其损耗最小化。但这些改进方法都会大幅增加原材料成本,限制其应用范围。因此需要提供一种具有优越、持久的耐刮擦性(干法和湿法)的用于汽车面漆的透明涂料组合物。
技术实现要素:本发明要解决的第一个技术问题是需要提供一种汽车面漆透明涂料组合物,该透明涂料组合物具有优越、持久的耐刮擦性(干法和湿法)。为解决第一个技术问题,本发明采用如下技术方案:一种用于汽车面漆的透明涂料组合物,其包括成膜粘结剂,所述成膜粘结剂至少包含:a)一种高官能化的超支化树枝状聚合物;b)含半酯化羧酸基的共聚物,所述共聚物含有-COOH和-COOR两种官能基团;c)环氧官能化的共聚物。所述高官能化的超支化树枝状聚合物为环氧官能化的超支化树枝状聚合物和/或羧基官能化的超支化树枝状聚合物。其中所述环氧官能化的超支化树枝状聚合物为外围被环氧官能团改性的超支化树枝状聚合物,其具有式(Ⅰ)的结构:式中,HBP为超支化树枝状聚合物的骨架结构;为连接环氧基团和超支化树枝状聚合物骨架的连接基团,8≤(m+n)≤环氧官能化的超支化树枝状聚合物中有效官能团的总数目,m和n为正整数;优选地,式(Ⅰ)的环氧官能化的超支化树枝状聚合物中同一个超支化聚合物骨架HBP上连接有至少两个或以上的环氧基团,即n≥2。优选地,式(Ⅰ)的环氧官能化的超支化树枝状聚合物的环氧当量为1000-1300,OH当量为1000-1300,数均分子量Mn为5000-7000,重均分子量Mw为15000-20000。其中,所述羧基官能化的超支化树枝状聚合物为外围羧基基团被改性的超支化树枝状聚合物,其具有式(Ⅱ)的结构:式中,HBP为超支化树枝状聚合物的骨架结构;为连接羧基基团和超支化树枝状聚合物骨架的连接基团,8≤(m+n)≤羧基官能化的超支化树枝状聚合物中有效官能团的总数目,m和n为正整数。优选地,式(Ⅱ)的所述羧基官能化的超支化树枝状聚合物中一个超支化聚合物骨架HBP上连接有至少两个或以上羧酸基团,即n≥2。优选地,式(Ⅱ)的羧基官能化的超支化树枝状聚合物的酸值为75-120,羟值为1800-2000,数均分子量Mn为5500-6500,重均分子量Mw为16000-20000。优选地,所述组合物中包含2.5-25份,优选为5-20份的所述高官能化的超支化树枝状聚合物。所述组合物中包含质量份数为5-30份的所述半酯化羧酸基的共聚物。优选地,所述半酯化羧酸基的共聚物选自含半酯化羧酸基的丙烯酸共聚物。在一个实施方案中,上述提及的用于汽车面漆的透明涂料组合物中的所述半酯化羧酸基官能化的丙烯酸共聚物(ACS1218),可由立邦涂料(上海)有限公司获得,其酸当量为57-67mgKOH/g,数均分子量为1500-2500,重均分子量Mw为2500-3500,非挥发性物质含量为72±1%。所述组合物中包含质量分数为10-40份的所述环氧官能化的共聚物。优选地,所述环氧官能化的共聚物选自环氧官能化的丙烯酸共聚物。在一个实施方案中,用于汽车面漆的透明涂料组合物中所述环氧官能化的丙烯酸共聚物(ACS1211),可由立邦涂料(上海)有限公司获得,其环氧当量为350-450,数均分子量Mn为2500-3000,重均分子量Mw为5000-6000,非挥发性物质含量为55±1%。所述成膜粘结剂进一步包含羟基官能化的聚酯树脂,其质量分数为5-15份。在一个实施方案中,所述羟基官能化的聚酯共聚物(PRS-1014),可由立邦涂料(上海)有限公司获得,其羟值为430-480mgKOH/g,数均分子量Mn为2400-2600,重均分子量Mw为3000-3300,非挥发性物质含量为75±1%。优选地,所述超支化聚合物骨架为H20或H4001,所述环氧官能化的超支化聚合物如式(Ⅰa)和式(Ⅰb)所示;优选地,当所述超支化聚合物骨架为H40时,所述羧基官能化的超支化聚合物如式(Ⅱa)所示:当所述高官能化的超支化树枝状聚合物的质量份数少于的2.5份时,性能的增强无法达到预期水平,涂料膜的交联密度提高不足,因而固化的涂料干膜的耐刮擦性能没有得到改善。当所述高官能化的超支化树枝状聚合物的质量份数超过25份时,未反应的官能团可能存在,并可能削弱涂料干膜的硬度和耐化学性。此外,所述用于汽车面漆的透明涂料组合物进一步包括纳米颗粒,所述纳米颗粒选自由氧化铝纳米颗粒,氧化锌纳米颗粒,二氧化硅纳米颗粒以及其组合组成的组,优选纳米二氧化硅颗粒。纳米颗粒与超支化树枝状聚合物可以进一步的性能增强。用于汽车面漆的透明涂料配方中通常含有固化催化剂。固化催化剂的选择没有特别的限制,但可为酯化反应(酸与环氧之间)通常使用的任意催化剂,优选季铵盐类,例如苄基三乙基氯化铵、四丁基氯化铵、四丁基溴化铵及其类似物,或者更优选磷盐类的苄基三苯基氯化磷、四丁基磷氯及其类似物。所有这些催化剂类型可以单独或组合使用。所述固化催化剂的优选用量为相对于全部树脂固体总质量份数的0.01-5.0份。所述用于汽车面漆的透明涂料组合物中,进一步包括添加剂组,所述添加剂组包括表面改性剂、消泡剂、流变控制剂、紫外线吸收剂和受阻胺类光稳定剂。其中紫外线吸收剂和/或受阻胺类光稳定剂用于改善涂料膜耐候性,微凝胶用于流变控制,流变控制剂和/或表面改性剂,用于调节粘度的稀释剂,如此等等。所述紫外线吸收剂和光稳定剂没有特别的限制,但其中包括Tinuvin900,Tinuvin123(BASFChemicals的产品)及其类似物。所述稀释剂没有特别的限制,但其中包括醇类溶剂例如甲醇,乙醇,丙醇和丁醇;烃类,乙二醇酯类溶剂等溶剂。所述这些使用时优选两种或两种以上的组合。成膜粘结剂、固化催化剂和添加剂组等构成本发明的用于汽车面漆的透明涂料组合物的固含量或非挥发性物质,本发明的用于汽车面漆的透明涂料组合物具有较高的固含量或非挥发性物质含量,优选地,100份配方中固含量或非挥发性物质的质量分数为20-80份,更优选100份配方中固含量或非挥发性物质的质量分数为35-65份;100份配方中,所述有机溶剂或稀释剂质量分数为80-20份,优选地,100份配方中所述有机溶剂或稀释剂的质量份数为65-35。本发明组合物取决于储存条件,作为单组份体系使用具有3-6个月的货架期。作为汽车面漆的透明涂料组合物,其制备方法为将表1规定的树脂成分(以质量基础给出),与催化剂、添加剂和溶剂混合,借助实验室分散机搅拌。所述涂料的制备方法优选按照特定的步骤顺序以确保产品的一致性和质量,(i)第一步将全部涂料配方质量的10-20份的有机溶剂,优选极性溶剂,更优选酯类,醇类,乙二醇类溶剂,在连续搅拌下与高官能化的超支化树枝状聚合物混合15-20min,搅拌速度为250-350rpm。(ii)第二步在连续搅拌下依次加入丙烯酸共聚物,所选择的固化催化剂,添加剂组(表面改性剂,消泡剂,流变控制添加剂,紫外线吸收剂,受阻胺类光稳定剂),以及剩余有机溶剂来完成配方,搅拌速度为350-450rpm。优选地,所述制备方法进一步包括加入纳米颗粒;将纳米颗粒良好分散于溶剂中后,于第一步后,第二步前加入纳米颗粒,优选地,所述纳米颗粒为二氧化硅纳米颗粒。作为汽车面漆的透明涂料组合物施加时优选喷涂施加方法,特别是在自动OEM生产线上采用标准气动或电动喷涂技术;但是,涂膜方法并没有被限制,根据最终施加工艺的要求,可以采取浸涂、滚涂、刷涂、流涂及其他技术方法。对用作汽车面板的基底材料没有严格限制,但其中包括金属材料,例如铁、铜、铝、锡、锌及它们的合金及其铸件、玻璃、塑料和泡沫材料。上述汽车的透明涂料可有利地应用于塑料和金属,更优选应用于可用阳离子电沉积涂覆方式覆盖的金属产品。汽车面板没有特别限制,其中包括轿车的车身或部分、卡车、摩托车、公共汽车等。更优选这些金属预先经过用磷酸盐、铬酸盐等进行化学转化处理。对于底漆膜层没有特别限制,例如可以是由电沉积涂层膜形成或者由电沉积涂层和中间涂层膜形成。电沉积涂料膜可以是阳离子电沉积层或阴离子电沉积层,阳离子电沉积层能够赋予涂料膜更优越的耐腐蚀性。阳离子电沉积层是一种阴极沉积型的可热固化电沉积层,含有包含基本氨基基团的树脂作为基本树脂,可以轻易地通过与酸的中和反应溶解在水中,应用时施加于充当阴极的待涂覆物品上。包含基本氨基基团的树脂并没有特别限制,优选衍生自例如将仲胺加入环氧基团树脂中而形成的双酚基环氧树脂。所述仲胺没有特别限制,其中包括伯胺类例,如以氯胺酮形式封端的二亚乙基三胺。上述阳离子电沉积涂料中使用的交联剂没有特别限制,优选被封端剂如醇、苯酚、肟或内酰胺封端的封端型聚异氰酸酯。上述电沉积涂料中还可以含有一种或多种颜料,例如着色颜料、体质颜料、防锈颜料,亲水和/或疏水溶剂、添加剂等等。所述颜料添加量可以为每100份全部树脂固体中的5-150质量份数。通常并优选地,电沉积涂料膜在电沉积并烘焙/干燥后的薄膜厚度为10-40μm,更优选为15-25μm。在电沉积涂料之前,基底更优选进行普通的化学转化处理。所述中间涂料膜是通过在上述电沉积涂料膜上施加中间涂料形成。该中间涂料用来遮盖基底的缺陷,确保经过顶层涂覆后表层光滑以及提供耐崩裂性。中间涂料包含一种或多种不同的有机或无机的颜料以及体质颜料。在上述中间涂料中加入着色颜料并没有特别限制,其中包括有机颜料如含氮螯合颜料、不溶性偶氮颜料、浓缩的偶氮颜料、酞菁颜料、靛蓝颜料、紫环酮颜料、异吲哚啉酮类颜料、金属络合物颜料;无机颜料如铬黄、氧化铁黄、铁红、炭黑、二氧化钛、以及体质颜料如碳酸钙、硫酸钡、粘土和滑石。所述颜料可以单独使用,也可以两种或多种组合使用。通常,包含炭黑和二氧化钛的灰色中间涂料经常被使用作为主要颜料。但依照顶层涂料的遮盖力,经常使用其中各种着色颜料组合使用的所谓着色中间涂料。对于加入到上述中间涂料的热固化树脂没有特别限制,其中包括,例如涂料成膜树脂如丙烯酸树脂、聚酯树脂、醇酸树脂、环氧树脂和聚氨酯树脂。它们与固化剂如氨基树脂和/或封端异氰酸酯组合使用。在这些树脂中,从有利于颜料的分散性和可加工性的角度优选醇酸树脂和/或聚酯树脂与氨基树脂的组合。中间涂料可以是溶剂型和水性体系。中间涂料的固含量为全部配方的30-70wt%,优选35-55wt%。施加步骤中,中间涂料的固含量为全部配方的10-60wt%,优选20-50wt%。中间涂料通过静电涂覆、空气喷涂、真空喷涂或其他涂覆技术优选施加在热固化的或未固化的电沉积涂料膜上,通过施加上述中间涂料得到中间涂料膜。中间涂料膜本身在加热到约100-180℃条件下能够固化。通常,形成的中间涂料膜的干膜厚度优选为10-60μm,更优选为20-50μm。当膜厚度小于10μm时,基底不能被遮盖,而当膜厚度大于60μm时,施加步骤中可能会出现诸如发泡和流挂之类的问题。在底漆膜层(电沉积涂料膜层及必要时的中间涂料膜层)形成后,含有着色颜料的基础涂料可以施加于处于固化或未固化状态的底漆膜层上。对于要被加入到上述基础涂料中的着色颜料没有特别限制,其中包含,与要被加入到中间涂料中的着色颜料相同的着色颜料。对于光泽颜料也没有特别限制,其中包括,铝粉、铜粉、镍粉、不锈钢粉、云母粉,干扰云母粉(interferingmicapowders),彩色云母粉、铝片和石墨片。对于要被加入到上述基础涂料中的热固性树脂没有特别的限制,其中包括,与上述提及的要被加入到中间涂料中的热固性树脂相同的热固性树脂。其中,从有利于颜料的分散性、可加工性和耐候性的角度优选丙烯酸树脂和/或聚酯树脂与氨基树脂的组合。上述基础涂料的固含量为全部配方的15-60wt%,优选20-50wt%。在施加步骤,基础涂料的固含量为全部配方的10-50wt%,优选20-40wt%。上述中间涂料和基础涂料可以是有机溶剂型、水性类型(水溶性,水分散性,乳状液)或非水分散型。如果需要,可以引入固化催化剂、流变控制添加剂、表面改性剂等等。当上述的基础涂料是水性涂料时,从面漆和外观性能的角度考虑所述热固化树脂优选包括含有丙烯酰胺基、羟基和羧酸基的丙烯酸树脂与三聚氰胺树脂的组合;任选地,基础涂料树脂可以任选性包含聚丙烯酸/聚酯分散体与聚氨酯分散体的组合以表现出更好的性能例如耐碎石性和防水性。在任一情况下,在施加透明涂料膜前,所述基础涂料优选预先在60-100℃加热2-10分钟以便获得良好面漆的固化涂层。上述基础涂料优选以诸如静电喷涂或空气喷涂的方法施加到电沉积涂料膜或中间涂料膜上。施加基础涂料后,基础涂料膜本身在加热到100-180℃温度下固化。通常,形成的基础涂料膜优选具有10-30μm的干膜厚度。当干膜厚度小于10μm时,基底不容易被遮盖,当干膜厚度超过30μm时,在施加步骤中可能会出现诸如发泡和流挂之类的问题。当上述基础涂料是固态着色涂料时,本发明的作为汽车面漆的透明涂料可应用于在车体上形成多层涂料膜的工艺中,该工艺包括,在汽车面板上形成底漆膜层(固化)后,在其上施加含有着色颜料的固态着色涂料组合物,加热使其固化,然后用干碰湿(dry-on-wet)技术施加透明涂料作为顶层涂层,紧接着加热使其固化。在另一实例中,在底漆膜层形成后,在其已固化阶段,用含有着色颜料的基础涂料和/或含有光泽颜料的基础涂料来形成基础涂料膜,可以通过利用湿碰湿(wet-on-wet)技术施加透明涂料作为面漆然后通过加热固化施加多层涂料膜。这样就可以形成三次涂覆,两次烘焙(3C2B)的复合涂料膜-底漆(固化),基础涂料(含着色颜料和/或含光泽颜料),和透明涂料(湿碰湿)。在同样的工艺中,含着色颜料和/或含光泽颜料的基础涂料可以或者作为单独涂料施加,或者作为两种涂料施加,即含有着色颜料的基础涂料,随后含有光泽颜料的基础涂料,然后通过湿碰湿工艺施加透明涂料。...