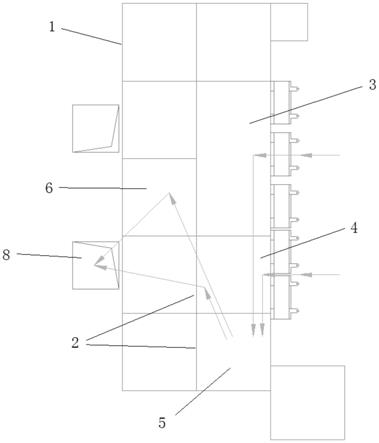
1.本发明属于生活垃圾焚烧发电行业垃圾贮存技术领域,涉及一种垃圾贮存库。
背景技术:2.现代城乡每天产生的垃圾不计其数,成为重要的环境问题和社会问题。在垃圾再生化、减量化、资源化以及生活垃圾焚烧发电成为新时代环境保护和经济发展的高速阶段,如何提升生活垃圾的经济效率,成为一个重要课题。
3.按有关研究文献介绍,生活垃圾经一定时长(5~6天)的厌氧发酵后,生活垃圾中的有机物经发酵(含水解)之后,能分离出一部分水份,大分子长链的有机物分解为较小分子的有机物,小分子的有机物燃烧时间更短、热值更高、燃烧温度更高。经多个地区和相关文献的介绍,生活垃圾的组成和热值变化幅度很大,含水率也有一定的变化范围,可以达到45~55%。按有关内部资料介绍,一般垃圾水分每降低1%,其热值增加160kj/kg(即40kcal/kg)。目前较大比例的含水率使降低含水率的技术创新存在很大的空间和发展前途。
4.降低入炉垃圾的含水率具有很大的经济价值。除了增加热值,降低入炉垃圾的含水率,还具有减少一二次空气量、减少热风量、减少脱酸脱硝气量、减少除尘气量、减少总排空烟气量等以及永久降低相应的炉排设备负荷、各种大功率风机(一二次空气、脱酸脱硝、除尘、废气)设备负荷和其他设备负荷,进而减少设备投资,降低运行费用,实现较好的经济效率。
5.按照目前许多生活垃圾焚烧发电厂的设计布置,焚烧炉炉前的垃圾库都是一个完整的整体空间,内部没有任何分割。整体空间的优点是一览无余,便于垃圾吊的起吊移动和操作,但是很不利于垃圾物料的新旧分区和顺序分割操作。大空间范围的垃圾斜坡裸露表面和大流量气流的负压空间也不利于局部厌氧发酵空间的大量形成和长时间保持。高料位垃圾物料堆积时极易滑落垮塌,大范围的库底空间垃圾物料会滞留很长时间而周转不畅或存在很低的周转效率。较少区域的高料位物料和大范围斜坡区域的垃圾物料导致垃圾物料承载的渗沥压力更小更少,渗沥水液也会更少;频繁的垃圾抓取和撒落会导致垃圾物料经常的相互挤压移位运动进而导致垃圾静置的时间更短,渗沥水液因静置而流动的时间也会更少,到达库底的渗沥水液总量也会更少。
6.由于生活垃圾物料堆积角包括湿润滑落垮塌的存在,其在加强充分混料的同时也导致垃圾库内垃圾吊及抓斗存在许多无效的起吊操作和起吊操作时间浪费;在计算有效库容的时候,由于垃圾物料堆积角和湿润滑落垮塌的存在,一般设计上也是按照垃圾卸料门地坪以上的空间按堆积角度计取,或按靠入炉料斗侧墙高度形成的三角形而对半计取,因而存在很多的无效库容,而这降低了垃圾库的总有效库容,降低了垃圾库承载因维修、季节、节日等峰值时刻原因可能产生的更多生活垃圾的收储量。
技术实现要素:7.本发明的目的就是为了提供一种垃圾贮存库,以提高生活垃圾发酵特别是厌氧发酵的效率与垃圾贮存库内的有效库容等。具体可为形成更多的发酵空间和维持发酵空间的更长时间、增加高料位压滤压力和静置渗沥时间、减少垃圾吊无效操作、降低垃圾含水率、提升垃圾热值、降低各种风量和设备负荷、减少运行费用和/或增加有效生活垃圾库容等原因,本发明旨在提出一种新的生活垃圾焚烧发电厂焚烧炉前的垃圾贮存库。
8.本发明的目的可以通过以下技术方案来实现:
9.一种垃圾贮存库,包括贮存库仓,在贮存库仓内设置有若干隔板,并将所述贮存库仓分隔为若干上部敞口的隔舱,所述隔舱分为卸料舱、周转舱、发酵舱和上料舱,其中,所述上料舱、周转舱均与卸料舱邻接。
10.进一步的,所述的贮存库仓沿纵向(与卸料门垃圾车车尾卸料方向相同)被隔板分割为等分的两列,每列再等分成5行或n行,其中,n为大于等于4并小于等于6的正整数,以形成2n等份的储存空间,其中,靠近垃圾车卸料侧的一列的中间部分的两份储存空间合并成所述卸料舱,隔舱总数为2n-1。其余各份储存空间形成分别形成单独的一个隔舱,且与卸料舱邻接的隔舱即为周转舱。
11.更进一步的,远离垃圾车卸料侧的一侧中的最中间部分的一个隔舱即为上料舱。
12.进一步的,围成所述发酵舱的隔板等高,并与位于垃圾贮存库旁的垃圾焚烧炉的入炉上料斗的顶口齐平。
13.进一步的,位于卸料舱与周转舱之间的隔板的高度与垃圾车所在卸料大厅的地坪齐平。
14.进一步的,位于卸料舱与上料舱之间的隔板的高度介于围成所述发酵舱的隔板和卸料舱与周转舱之间的隔板的高度之间。
15.更进一步的,位于卸料舱与上料舱之间的隔板的高度为围成所述发酵舱的隔板的高度的65-75%。更优选的,位于卸料舱与上料舱之间的隔板的高度为围成所述发酵舱的隔板的高度的70%。
16.进一步的,所述的隔舱底部放坡,并设置有直通渗沥液收集池的渗沥水液沟槽。
17.进一步的,所述的贮存库仓的上部还设有可自由移动并用于转移垃圾物料的垃圾吊车抓斗。
18.与现有技术相比,本发明提高了垃圾库的有效存贮量,对比同等总体尺寸的垃圾库可以增加一成以上或半天以上的贮存量,延长垃圾的可发酵(特别是厌氧发酵)的时间,平均延长时长三成,提高了垃圾的渗沥水液时的压滤压力,延长了静置沥水时间,产生了更多的渗沥液,从而降低炉前垃圾的含水率,减少垃圾中不必要的水分的蒸发(水分蒸发吸热且水分被库内负压抽至炉膛,降低整体能量利用效率和水分未整体移除)、升温和降温及排空余热的散失,提高入炉垃圾的干燥程度和单位质量的发热量,降低了焚烧炉一次风和二次风的风量以及随后的热风风量、脱硝脱酸除尘风量以及排空烟气总量,降低了炉排和大量风机的总负荷强度,充分的发酵(特别是厌氧发酵)导致更多物料以小分子的方式参加燃烧,实现更短的燃烧时间和更高的燃烧温度。
附图说明
19.图1为本发明的垃圾贮存库的平面布置示意图;
20.图2为垃圾贮存库的立面布置示意图;
21.图中标记说明:
22.1-贮存库仓,2-隔板,21-第一隔板,22-第二隔板,23-第三隔板,3-卸料舱,4-周转舱,5-发酵舱,6-上料舱,7-垃圾车,8-入炉上料斗,9-垃圾吊车抓斗。
具体实施方式
23.下面结合附图和具体实施例对本发明进行详细说明。本实施例以本发明技术方案为前提进行实施,给出了详细的实施方式和具体的操作过程,但本发明的保护范围不限于下述的实施例。
24.以下各实施方式或实施例中,如无特别说明的功能部件或结构,则表明其均为本领域为实现对应功能而采用的常规部件或结构。
25.为提高生活垃圾发酵特别是厌氧发酵的效率与垃圾贮存库内的有效库容等,本发明提供了一种垃圾贮存库,请再参见图1和图2所示,包括贮存库仓1,在贮存库仓1内设置有若干隔板2,并将所述贮存库仓1分隔为若干上部敞口的隔舱,所述隔舱分为卸料舱3、周转舱4、发酵舱5和上料舱6,其中,所述上料舱6、周转舱4均与卸料舱3邻接。
26.在一种具体的实施方式中,请再参见图1和图2所示,所述的贮存库仓1沿纵向被隔板2分割为等分的两列,每列再等分成5行或n行,其中,n为大于等于4并小于等于6的正整数,以形成2n等份的储存空间,其中,靠近垃圾车7卸料侧的一列的中间部分的两份储存空间合并成所述卸料舱3,总舱数为2n-1。其余各份储存空间形成分别形成单独的一个隔舱,且与卸料舱3邻接的隔舱即为周转舱4。
27.更具体的实施方式中,远离垃圾车7卸料侧的一侧中的最中间的隔舱即为上料舱6。
28.在一种具体的实施方式中,请再参见图1等所示,围成所述发酵舱5的隔板2(即第一隔板21)等高,并与位于垃圾贮存库旁的垃圾焚烧炉的入炉上料斗8的顶口齐平,最大限度地充分利用了垃圾库的有效容积比大开间无隔墙板的垃圾库的有效库容增加10%以上,或者增加了额定量半天以上的生活垃圾存贮量。
29.在一种具体的实施方式中,请再参见图2等所示,位于卸料舱3与周转舱4之间的隔板2(即第二隔板22)的高度与垃圾车7所在卸料大厅的地坪齐平。
30.在一种具体的实施方式中,请再参见图2等所示,位于卸料舱3与上料舱6之间的隔板2(即第三隔板23)的高度介于围成所述发酵舱5的隔板2和卸料舱3与周转舱4之间的隔板2的高度之间。
31.更具体的实施方式中,请再参见图2等所示,位于卸料舱3与上料舱6之间的隔板2的高度为围成所述发酵舱5的隔板2的高度的65-75%,而上料舱6由其最低隔板2的高度决定的有效容积是发酵舱5容积的65-75%左右,由此,周转舱4用于发酵后垃圾混料上料的有效容积仅需是发酵舱5容积的25-35%左右即可,而由上可知,卸料舱3与周转舱4的容积比是2:1,即周转舱4的容积是整个入厂接卸料舱3体总容积的三分之一,这样,既保证整个垃圾贮存库的有效容积尽可能大,也不会由于垃圾转移过程中,垃圾吊车抓斗9由于行程过大
而导致周转效率降低。更优选的,位于卸料舱3与上料舱6之间的隔板2的高度为围成所述发酵舱5的隔板2的高度的70%。
32.在一种具体的实施方式中,请再参见图2等所示,所述的隔舱底部放坡,并设置有直通渗沥液收集池的渗沥水液沟槽。
33.在一种具体的实施方式中,请再参见图2等所示,所述的贮存库仓1的上部还设有可自由移动并用于转移垃圾物料的垃圾吊车抓斗9。
34.以上各实施方式可以任一单独实施,也可以任意两两组合或更多的组合实施。
35.下面结合具体实施例来对上述实施方式进行更详细的说明。
36.实施例1:
37.为提高生活垃圾发酵特别是厌氧发酵的效率与垃圾贮存库内的有效库容等,本实施例提供了一种垃圾贮存库,请再参见图1和图2所示,包括贮存库仓1,在贮存库仓1内设置有若干隔板2,并将贮存库仓1分隔为若干上部敞口的隔舱,隔舱分为卸料舱3、周转舱4、发酵舱5和上料舱6,其中,上料舱6、周转舱4均与卸料舱3邻接。
38.请再参见图1和图2所示,贮存库仓1沿纵向被隔板2分割为等分的两列,每列再等分成5行,以形成10等份的储存空间,其中,靠近垃圾车7卸料侧的一列的中间部分的两份储存空间合并成卸料舱3,其余各份储存空间形成分别形成单独的一个隔舱,且与卸料舱3邻接的隔舱即为周转舱4。远离垃圾车7卸料侧的一侧中的最中间的隔舱即为上料舱6。
39.请再参见图1等所示,围成发酵舱5的隔板2(即第一隔板21)等高,并与位于垃圾贮存库旁的垃圾焚烧炉的入炉上料斗8的顶口齐平,最大限度地充分利用了垃圾库的有效容积比大开间无隔墙板的垃圾库的有效库容增加10%以上,或者增加了额定量半天以上的生活垃圾存贮量。
40.请再参见图2等所示,位于卸料舱3与周转舱4之间的隔板2(即第二隔板22)的高度与垃圾车7所在卸料大厅的地坪齐平。
41.请再参见图2等所示,位于卸料舱3与上料舱6之间的隔板2(即第三隔板23)的高度介于围成发酵舱5的隔板2和卸料舱3与周转舱4之间的隔板2的高度之间。
42.请再参见图2等所示,位于卸料舱3与上料舱6之间的隔板2的高度为围成发酵舱5的隔板2的高度的65-75%,而上料舱6由其最低隔板2的高度决定的有效容积是发酵舱5容积的65-75%左右,由此,周转舱4用于发酵后垃圾混料上料的有效容积仅需是发酵舱5容积的25-35%左右即可,而由上可知,卸料舱3与周转舱4的容积比是2:1,即周转舱4的容积是整个入厂接卸料舱3体总容积的三分之一,这样,既保证整个垃圾贮存库的有效容积尽可能大,也不会由于垃圾转移过程中,垃圾吊车抓斗9由于行程过大而导致周转效率降低。更优选的,位于卸料舱3与上料舱6之间的隔板2的高度为围成发酵舱5的隔板2的高度的70%。
43.请再参见图2等所示,隔舱底部放坡,并设置有直通渗沥液收集池的渗沥水液沟槽。
44.请再参见图2等所示,贮存库仓1的上部还设有可自由移动并用于转移垃圾物料的垃圾吊车抓斗9。
45.本实施例在具体使用过程中,贮存库仓1被隔板2分割为九个隔舱,单个发酵仓的容积为额定24小时入厂接卸料的垃圾总容积另加一定比例的设计余量,卸料舱3和周转舱4的总容积为额定24小时入厂接卸料的垃圾总容积另加一定比例的设计余量。总体上,额定
24小时入厂垃圾接卸量另加一定比例的余量,可贮存在任一个发酵舱5内。
46.正常操作运行时,发酵舱5按顺序编号,如从3号到8号。每日或每24小时,经卸料舱3和周转舱4先后分别接卸料混料后,装满一个发酵舱5,同时另一个静置发酵5-6天后的发酵舱5出料,先后分别经上料舱6和周转舱4混料后入焚烧炉进料斗口。多个发酵舱5间隔5-6天顺序轮流装料和出料。
47.参见图1右上侧箭头方向,卸料舱3专门接卸料,在每日24小时中的固定15小时内连续接卸料和混料;在其后发酵舱5总计约10小时装(满)料时间的62.5%的时间内即6.25小时内,卸料舱3内的料被垃圾吊起吊并均匀地一层层装入发酵舱5。发酵舱5总计约10小时装(满)料时间的另外37.5%的时间内即3.75小时内均匀装入来自周转舱4内经9小时(每日24小时中的前15小时外的另外后9小时)时间接卸料和混料后的垃圾物料。
48.参见图1右下侧箭头方向,周转舱4在完成前述总计约9+3.75=12.75小时的新鲜垃圾物料9小时接卸料混料和3.75小时出料后,开始持续3小时接受来自发酵舱5的30%的发酵料,这30%的发酵料经混料后即开始持续7.2小时的给焚烧炉进料斗上料。与此同时,同一发酵舱5另70%的发酵料,开始连续7小时出料给上料舱6,这70%的发酵料在上料舱6经混料后即开始持续16.8小时(即前述7.2小时外的每日一昼夜24小时外的另外16.8小时)的给焚烧炉进料斗上料。
49.确保周转舱4在24小时内依次完成9小时新鲜料接卸料和混料、3.75小时出料给被清空的发酵舱5,随后3小时接受来自另一发酵舱5的30%的发酵料,以及后续持续7.2小时给焚烧炉进料斗上料。
50.确保上料舱6在24小时内依次完成7小时接受来自同一发酵舱5剩余的70%发酵料,以及后续16.8小时给焚烧炉进料斗上料。
51.确保卸料舱3在24小时内依次完成15小时新鲜料接卸料和混料,以及后续6.25小时出料被清空的发酵舱5。
52.确保发酵舱5在6.25小时和3.75小时内依次分别完成接受来自卸料舱3和周转舱4混料后的新鲜料,之后,发酵舱5垃圾物料整体静置、充分发酵、充分压缩、充分沥水持续5~6天后,进入下一轮发酵料出料混料阶段,即开始连续3小时出料30%发酵料给周转舱4,以及随后7小时出料70%发酵料给上料舱6。发酵舱5清空后,进入下一轮新鲜料进料阶段,如此周而复始。
53.为确保均匀混合垃圾物料,每间隔4~6米高程料位,垃圾吊车抓斗9取料时尽量先从舱内中心取料,尽量产生足够多的垃圾物料的滑落塌陷以促进混料;垃圾吊车抓斗9落料时尽量按回字型一圈圈一层层在舱内料位较高处均匀移位落料。之后,另一个4~6米高程料位,垃圾吊车抓斗9取料时再尽量按回字型一圈圈一层层在舱内均匀移位取料。垃圾吊车抓斗9落料时尽量先自从舱内中心料位较高处落料,尽量产生足够多的垃圾物料的滑落塌陷以促进混料。即,中心取料和周圈取料每个4-6米高程交替进行,而落料则反之。
54.为确保均匀混合垃圾物料,经调度,发酵舱5向两个舱分别进料,并向两个舱分别出料;可以在合理调度后,特别发酵舱5存在5~6天的发酵时间前后,可以实现交叉进料和交叉出料,实现生活垃圾物料充分混料的目标。(此等交叉进出料需要较高的吊车抓斗负荷能力)
55.本实施例的垃圾贮存库中,如库顶的垃圾吊车抓斗9等设备均为本领域的常规设
备,另外,隔板2与贮存库仓1的墙体所用材料可以是钢筋混凝土或不锈钢板或镀锌钢板或其他材料,而隔舱底部设置的沟槽和放坡均是为了便于渗沥水液流向渗沥液收集池,贮存库仓1顶部还设有排风母管和支管等,确保库内负压,臭气不外溢外泄。
56.实施例2:
57.与实施例1相比,绝大部分都相同,除了本实施例中的贮存库仓1被隔板2分割为七个隔舱,其中,四个为发酵舱5,其余三个分别为卸料舱3、周转舱4和上料舱6。
58.上述的对实施例的描述是为便于该技术领域的普通技术人员能理解和使用发明。熟悉本领域技术的人员显然可以容易地对这些实施例做出各种修改,并把在此说明的一般原理应用到其他实施例中而不必经过创造性的劳动。因此,本发明不限于上述实施例,本领域技术人员根据本发明的揭示,不脱离本发明范畴所做出的改进和修改都应该在本发明的保护范围之内。