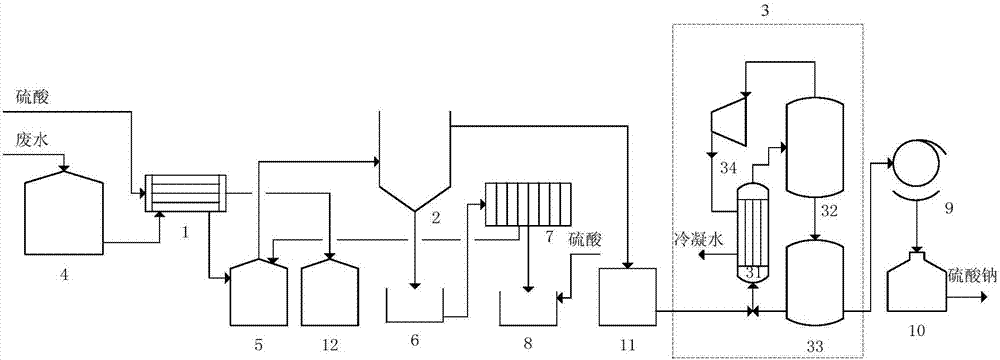
本发明属于废水深度处理
技术领域:
,特别是涉及一种三元正极材料生产废水的处理方法及处理系统。
背景技术:
:随着石油资源的逐渐减少及传统能源带来的巨大环境污染,开发可再生绿色能源及储能材料成为全球发展的重要方向。锂离子二次电池具有高能量密度、工作性能稳定、质量轻等优势,是大功率动力电池开发的重点。目前,成功商业化的锂离子电池正极材料有钴酸锂、锰酸锂和磷酸铁锂。钴酸锂和锰酸锂放电比容量小,化学稳定性较差,难以作为大功率动力锂电池的正极材料。磷酸铁锂热稳定性好但是存在理论和实际比容量小以及导电性能差等缺点。镍钴锰三元正极材料作为新型锂离子电池正极材料,具有放电容量高,循环寿命好,安全性高,成本低廉等优点,是最具潜力的正极材料。三元材正极材料的制备方法主要有高温固相法,溶胶凝胶法,化学共沉淀法,水热合成法,喷雾干燥法等,其中化学共沉淀法合成产物组分均匀性好,条件容易控制,操作简单,工业上已经大规模生产。化学共沉淀法一般是把化学原料以溶液状态混合,并向溶液中加入适当沉淀剂,使溶液中已混合均匀的各个组分按照计量比共沉淀出来,或者在溶液中先反应沉淀出一种中间产物,再把它煅烧分解制备出微细粉料。化学共沉淀法在洗涤和分离过程会产生大量碱性废水(ph>9),氨氮含量高达数十克每升而且与重金属形成络合物。另外,由于含有大量的硫酸钠盐,除氨后仍不能达标排放,而且会对资源造成浪费。因此,为了实现该类废水的达标排放以及资源化回收,急需一种针对三元正极材料生产废水的零排处理方法及处理系统。技术实现要素:本发明针对以上所述现有技术存在的技术缺陷,提供了一种三元正极材料生产废水的处理方法及处理系统。所述处理方法首次采用膜分离、固液分离和蒸发结晶相结合的工艺流程:首先,以硫酸溶液为吸收剂,采用膜分离将废水中氨氮转化为硫酸铵,实现脱氨;由于前期的ph为碱性,废水脱氨后废水中大量金属破络并与碱形成沉淀,过滤去除溶液中的重金属沉淀;过滤后上清液通过蒸发结晶,得到硫酸钠。本发明的处理方法对三元正极材料生产废水进行深度处理回用,有效解决三元正极材料生产废水的处理问题,回收废水中氨,重金属和硫酸钠资源,水回收率高达99%以上,实现零排放。本发明是通过以下技术方案实现的:本发明第一方面提供一种三元正极材料生产废水的处理方法,包括以下步骤:1)将三元正极材料生产废水通入膜分离的壳程,吸收液通入膜分离的管程,所述吸收液为硫酸,得到硫酸铵溶液和脱氨废水;三元正极材料生产废水中气态氨可以透过膜表面的微孔从壳程的废水相进入管程的酸吸收相,被酸液吸收变成硫酸铵溶液2)将步骤1)得到的脱氨废水过滤,得到上清液和沉淀;脱氨废水中重金属离子络合破坏形成沉淀;3)将步骤2)得到的上清液经蒸发结晶,得到硫酸钠。优选地,步骤1)中,三元正极材料生产废水中na2so4浓度为50-150g/l,nh3-n浓度为500-10000mg/l,m2+浓度为50-500mg/l,m2+浓度为ni2+、co2+和mn2+的总浓度,ph为10~14。优选地,步骤1)中,还包括如下特征中的一项或多项:1)所述膜分离使用疏水性中空纤维膜;2)膜分离工艺条件为:温度30~45℃,运行相对压力为0.1~0.25mpa;3)吸收液的ph值为0~5;4)三元正极材料生产废水与吸收液的体积流量比为1:2.5~5;5)步骤1)得到的硫酸铵溶液浓度为15-30wt%;6)步骤1)得到的硫酸铵溶液回用于三元正极材料生产工艺中。优选地,还包括如下特征中的一项或多项:1)步骤2)得到的沉淀压滤后用硫酸溶解,用于三元正极材料生产工艺中;2)步骤2)得到的沉淀排入浓缩液槽,浓缩液槽底部浓浆经板框压滤后用硫酸溶解,用于三元正极材料生产工艺中;3)步骤2)中,所述过滤为通过液体过滤器分离。优选地,步骤3)中,将步骤2)得到的上清液进入加热室加热到溶液沸点以上,如70~125℃,然后进入蒸发室内进行蒸发至过饱和,最后在结晶罐内析出硫酸钠,经离心干燥,得到硫酸钠。更优选地,蒸发室产生的二次蒸汽进行压缩后返回至加热室继续加热步骤2)得到的上清液,无需新鲜蒸汽加入。优选地,所述二次蒸汽返回至加热室后得到蒸发冷凝水,所述冷凝水用于分离吸收液配制或者三元正极材料生产工艺中。本发明第二方面提供一种三元正极材料生产废水的处理系统,包括:膜分离装置,用于将三元正极材料生产废水进行膜分离得到脱氨废水;固液分离装置,用于将脱氨废水过滤得到上清液和沉淀,所述固液分离装置与膜分离装置连通;蒸发结晶装置,用于将上清液蒸发结晶得到硫酸钠,所述蒸发结晶装置与固液分离装置连通。所述膜分离装置可使用疏水性中空纤维膜。所述固液分离装置为液体过滤器,可以为西恩过滤器,如西恩cnii2200过滤器。优选地,还包括如下特征中的一项或多项:1)所述膜分离装置设有用于将三元正极材料生产废水输入膜分离装置的壳程入口、用于将脱氨废水排出膜分离装置的壳程出口、用于将硫酸输入膜分离装置的管程入口和用于将硫酸铵溶液排出膜分离装置的管程出口,膜分离装置的管程出口与所述固液分离装置连通;从管程出口排出的硫酸铵溶液可回用于三元正极材料生产工艺中;2)所述处理系统还包括用于储存三元正极材料生产废水的废水槽,所述废水槽与膜分离装置连通;3)所述处理系统还包括用于储存脱氨废水的脱氨后液罐,所述脱氨后液罐与固液分离装置连通;4)所述处理系统还包括浓缩液槽和板框压滤机,所述固液分离装置包括上清液出口和沉淀出口,所述沉淀出口与浓缩液槽连通,所述浓缩液槽与板框压滤机连通,所述板框压滤机设有滤液出口和滤渣出口,所述板框压滤机的滤液出口与固液分离装置连通或者所述板框压滤机的滤液出口与脱氨后液罐连通;5)所述蒸发结晶装置包括依次连通的加热室、蒸发室和结晶罐;6)所述处理系统还包括蒸发前液罐,所述固液分离装置与蒸发前液罐连通;7)所述处理系统还包括用于储存硫酸铵溶液的溶液罐,所述溶液罐与膜分离装置连通。更优选地,还包括如下特征中的一项或多项:1)特征4)中,所述处理系统还包括用于将板框压滤机得到的滤渣进行酸溶解的酸溶槽,所述酸溶槽与板框压滤机的滤渣出口连通;2)特征5)中,所述蒸发结晶装置还包括蒸汽压缩机,蒸发室设有蒸汽出口和过饱和溶液出口,所述蒸发室的蒸汽出口与蒸汽压缩机连通,所述蒸汽压缩机再与加热室连通,所述蒸发室的过饱和溶液出口与结晶罐连通;蒸发室产生的蒸汽进行压缩返回至加热室继续加热,无需新鲜蒸汽加入,得到的蒸发冷凝水可用于分离吸收液配制或者三元正极材料生产工艺中;3)特征5)中,所述处理系统还包括依次连通的离心机和干燥器,所述结晶罐设有硫酸钠固体出口和溶液出口,结晶罐的硫酸钠固体出口与离心机连通,结晶罐的液体出口与加热室连通。与现有技术相比,本发明的处理方法具有以下技术效果:(1)本发明通过采用膜分离、固液分离和蒸发结晶相结合的工艺流程,对三元正极材料生产废水进行深度处理回用,回收废水中氨,重金属和硫酸钠资源,水回收率高,实现零排放;(2)本发明中膜分离过程方法简单易行,能耗低;mvr蒸发结晶仅需要极少量蒸汽,极大地降运行成本,减少环境污染;没有废热蒸汽排放,节能效果十分显著;(3)本发明投资小,运行成本低,设备简单,易于维护;(4)本发明无有害的副产品产生,无二次污染。附图说明图1是本发明三元正极材料生产废水的处理方法;图2为本发明三元正极材料生产废水的处理系统。附图标记:1-膜分离装置;2-固液分离装置;3-蒸发结晶装置;31-加热室;32-蒸发室;33-结晶罐;34-蒸汽压缩机;4-废水槽;5-脱氨后液罐;6-浓缩液槽;7-板框压滤机;8-酸溶槽;9-离心机;10-干燥器;11-蒸发前液罐;12-溶液罐。具体实施方式以下通过特定的具体实例说明本发明的技术方案。应理解,本发明提到的一个或多个方法步骤并不排斥在所述组合步骤前后还存在其他方法步骤或在这些明确提到的步骤之间还可以插入其他方法步骤;还应理解,这些实施例仅用于说明本发明而不用于限制本发明的范围。而且,除非另有说明,各方法步骤的编号仅为鉴别各方法步骤的便利工具,而非为限制各方法步骤的排列次序或限定本发明可实施的范围,其相对关系的改变或调整,在无实质变更技术内容的情况下,当亦视为本发明可实施的范畴。下面结合具体实施例对本发明做进一步说明:实施例1以国内某年产6000吨三元前驱体生产厂家为例,废水水量350m3/d。废水排放污染物浓度测试如下:污染物phna2so4nh3-nm2+浓度(g/l)12.9510010.20.243一种三元正极材料生产废水的处理系统,如图2所示,包括:膜分离装置1,用于将三元正极材料生产废水进行膜分离得到脱氨废水;所述膜分离装置1设有用于将三元正极材料生产废水输入膜分离装置的壳程入口、用于将脱氨废水排出膜分离装置的壳程出口、用于将硫酸输入膜分离装置的管程入口和用于将硫酸铵溶液排出膜分离装置的管程出口,膜分离装置1的管程出口与所述固液分离装置2连通;从管程出口排出的硫酸铵溶液可回用于三元正极材料生产工艺中;所述膜分离装置可使用疏水性中空纤维膜,如聚丙烯(pp)疏水中空纤维膜;固液分离装置2,用于将脱氨废水过滤得到上清液和沉淀,所述固液分离装置2与膜分离装置1连通;所述固液分离装置为液体过滤器,可以为西恩过滤器,如西恩cnii2200过滤器;蒸发结晶装置3,用于将上清液蒸发结晶得到硫酸钠,所述蒸发结晶装置3与固液分离装置2连通;所述蒸发结晶装置3包括依次连通的加热室31、蒸发室32和结晶罐33;所述蒸发结晶装置3还包括蒸汽压缩机34,蒸发室32设有蒸汽出口和过饱和溶液出口,所述蒸发室32的蒸汽出口与蒸汽压缩机34连通,所述蒸汽压缩机34再与加热室31连通,所述蒸发室32的过饱和溶液出口与结晶罐33连通;蒸发室产生的蒸汽进行压缩返回至加热室继续加热,无需新鲜蒸汽加入,得到的蒸发冷凝水可用于分离吸收液配制或者三元正极材料生产工艺中;所述处理系统还包括用于储存三元正极材料生产废水的废水槽4,所述废水槽4与膜分离装置1连通;还包括用于储存脱氨废水的脱氨后液罐5,所述脱氨后液罐5与固液分离装置2连通;还包括浓缩液槽6和板框压滤机7,所述固液分离装置2包括上清液出口和沉淀出口,所述沉淀出口与浓缩液槽6连通,所述浓缩液槽6与板框压滤机7连通,所述板框压滤机7的滤液出口与脱氨后液罐5连通;还包括蒸发前液罐11,所述固液分离装置2与蒸发前液罐11连通;还包括用于储存硫酸铵溶液的溶液罐12,所述溶液罐12与膜分离装置1连通。还包括用于将板框压滤机7得到的滤渣进行酸溶解的酸溶槽8,所述酸溶槽8与板框压滤机7的滤渣出口连通;还包括依次连通的离心机9和干燥器10,所述结晶罐33设有硫酸钠固体出口和溶液出口,结晶罐33的硫酸钠固体出口与离心机9连通,结晶罐的液体出口与加热室31连通。一种三元正极材料生产废水的处理方法,工艺流程图见图1。图中膜分离为聚丙烯(pp)疏水中空纤维膜,运行相对压力为0.1mpa,温度为30℃;液体过滤器为cnii2200过滤器,单台处理能力15m3/h;蒸发结晶装置设计蒸发量为13.5t/h,蒸汽压缩机设计温差15℃,设计温度从90℃升至105℃。工艺步骤如下:1.膜分离:将废水罐中三元废水泵入膜分离的壳程,在膜分离的管程泵入ph=1的稀硫酸进行循环流动,稀硫酸的流量为1320m3/d。废水中气态氨可以透过膜表面的微孔从壳程的废水相进入管程的酸吸收相,被酸液吸收变成硫酸铵溶液,通过不断地补充稀硫酸使硫酸铵浓度升高,当达到20wt%的浓度就回用于三元正极材料生产工艺中。其中稀酸的配制可以蒸发冷凝水配制。2.固液分离:脱氨后的废水重金属离子络合形态被破坏从而形成沉淀,进入cnii3300过滤器进行分离。经过过滤器分离后上清液悬浮物小于5mg/l,金属离子小于1mg/l,可以溢流排入蒸发前液罐。过滤器底部的沉淀定期排入浓缩液槽,然后打入板框压滤机进行脱水,沉淀物采用稀硫酸溶解后,可回用于三元正极材料生产系统,板框滤液则返回到过滤器继续固液分离。3.蒸发结晶:蒸发结晶装置包括蒸发室,结晶罐,加热室和蒸汽压缩机。脱氨后废水先进入加热室与蒸汽压缩机出来的饱和水蒸气换热,废水被加热到溶液沸点以上,然后进入蒸发室内进行蒸发至过饱和。接着在结晶罐内冷却析出无水硫酸钠,经离心干燥后集中处置。蒸发室内二次蒸汽经过蒸汽压缩机压缩后,返回加热室加热脱氨后废水。蒸发冷凝水可以回用于膜分离吸收液的配制和三元正极材料生产系统。经过整个处理系统,得到20wt%的硫酸铵138.6t/d,重金属85.05kg/d和无水硫酸钠35t/d,资源都回收,水也几乎100%回用。实施例2以国内某年产10000吨三元前驱体生产厂家为例,废水水量1000m3/d。废水排放污染物浓度测试如下:污染物phna2so4nh3-nm2+浓度(g/l)11.5754.50.07工艺流程示意图见图2。图中膜分离为聚四氟乙烯(ptfe)疏水中空纤维膜,运行相对压力为0.25mpa,温度为45℃,ph=5的稀硫酸流量为3600m3/h;液体过滤器为cnii3300过滤器,单台处理能力30m3/h,共2台;蒸发结晶装置设计蒸发量为42t/h,设计2套,单套21t/h,蒸汽压缩机设计温差18℃,设计温度从95℃升至113℃。工艺步骤如实施例1,经过整个处理系统,得到25wt%的硫酸铵139.8t/d,重金属70kg/d和无水硫酸钠75t/d,资源都回收,水也几乎100%回用。当前第1页12