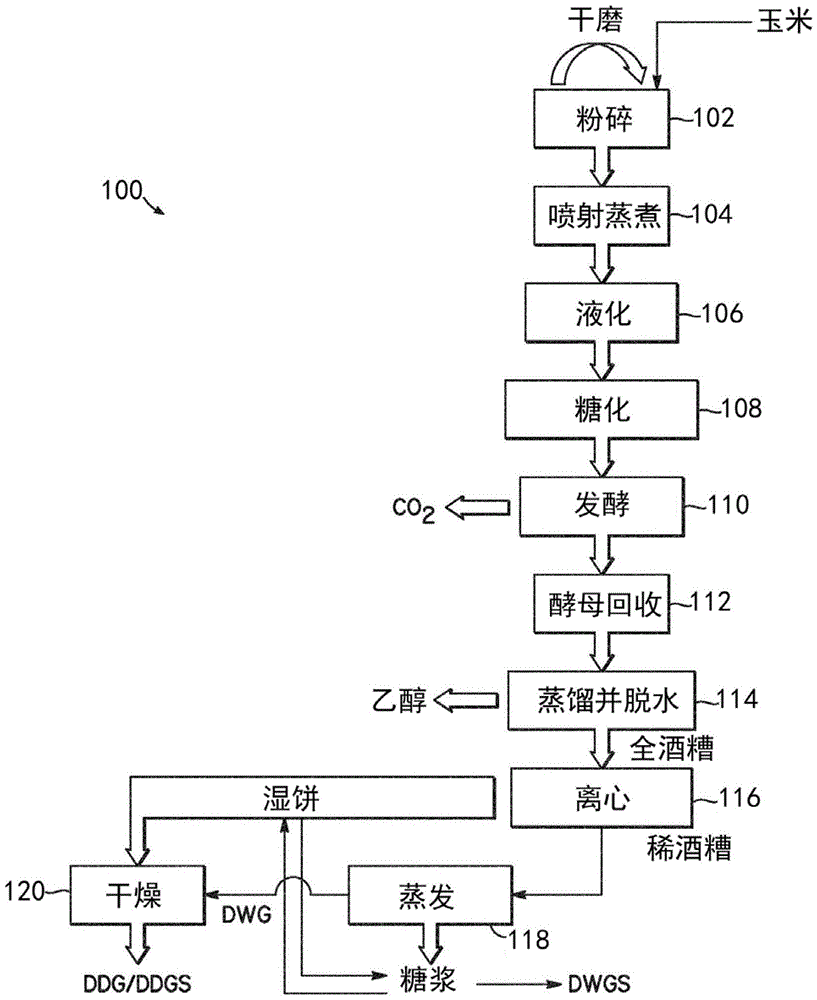
从用于生产醇的谷物中分离高价值副产品的系统和方法相关申请的交叉引用本申请要求2010年12月3日递交的美国临时申请No.61/419,426的优先权,并将该申请公开的全部内容通过引用合并于此。技术领域本发明普遍地涉及一种从用于生产醇的谷物中分离副产品的系统和方法。
背景技术:现今,令人非常感兴趣的一种醇为乙醇,它能够由任何类型的谷物生产得到,但最常见的是由玉米制得。美国大多数的燃料乙醇由湿磨工艺或干磨乙醇工艺生产得到。事实上,尽管任何类型和品质的谷物都能够用来生产乙醇,但用于这些工艺的原料通常是被称为“黄马牙种玉米2号(No.2YellowDentCorn)”的玉米。“2号”是指本领域公知的由国家粮食检验协会(NationalGrainInspectionAssociation)所定义的具有某些特性的品质的玉米。“黄马牙种”是指本领域公知的一种特定类型的玉米。用于从谷物中生产各种类型的醇的传统方法一般按照类似的工艺进行,这取决于所述工艺是湿法操作还是干法操作。湿磨玉米加工厂将玉米谷粒(corngrain)转换成几种不同的副产品,例如,胚芽(用于榨油)、麸质饲料(高纤维动物饲料),谷蛋白粉(glutenmeal,高蛋白动物饲料),以及淀粉基产品(例如,乙醇、高果糖玉米糖浆或食用和工业用淀粉)。干磨乙醇工厂将玉米转换为两种产品,即乙醇和含有可溶物的酒糟(distiller'sgrains)。如果作为湿的动物饲料出售,具有可溶物的湿酒糟被称为DWGS。如果作为干的动物饲料出售,具有可溶物的干酒糟被称为DDGS。在标准的干磨乙醇工艺中,一蒲式耳玉米除产生约10.5升(约2.8gal)的乙醇,还产生约8.2kg(约17lbs)的DDGS。这种副产品提供了重要的二次收益流,能够弥补部分生产乙醇的总成本。对于湿磨工艺,图1为典型的湿磨乙醇生产工艺10的流程图。所述工艺10起始于浸泡步骤12,其中,玉米在水和二氧化硫的溶液中浸泡24-48小时,以软化用于研磨的谷粒,使可溶性组分进入到浸渍水中,并使具有胚乳的蛋白基质松弛。玉米粒主要含有淀粉、纤维、蛋白质和油(oil)。然后将浸泡的玉米和水的混合物输送到去胚芽研磨步骤(第一次研磨)14,其中,将玉米以粉碎的方式进行研磨,并释放胚芽以制备研磨组分的高密度(8.5-9.5Be)浆液,主要是淀粉浆液。然后进行胚芽分离步骤16,通过浮选并使用水力旋流器从剩余的浆液中分离胚芽。胚芽为谷粒的一部分,并含有存在于玉米中的油。将含有部分淀粉、蛋白质和纤维的分离的胚芽流进行胚芽洗涤,以去除淀粉和蛋白质,然后进入烘干机以制得约2.7-3.2Lb(干基)的胚芽/蒲式耳玉米。以干基计,干胚芽具有约50%的油含量。现在将不含胚芽但含有纤维、谷蛋白(即蛋白质)和淀粉的剩余浆液进行精磨步骤(第二次研磨)20,其中,胚乳将被完全破坏并从纤维中释放胚乳成分,即谷蛋白和淀粉。然后进行纤维分离步骤22,其中,浆液通过一系列的筛选以从淀粉和谷蛋白中分离纤维,并将谷蛋白和淀粉从纤维中清洗除掉。纤维分离阶段22通常利用压力筛选机(pressurescreens)或安装在筛筒中的旋转叶片(搅拌筛选机,PaddleScreens)。即使洗涤后,来自常规湿磨的纤维仍含有15-20%的淀粉。淀粉与纤维一起作为动物饲料出售。现在,使不含有纤维的剩余浆液进入谷蛋白分离步骤24,其中,通过离心分离或水力旋流器从谷蛋白中分离淀粉。谷蛋白流进入真空过滤机和烘干机而得到谷蛋白(蛋白质)粉。然后,将得到的纯化的淀粉副产品进行喷射蒸煮步骤26,以开始将淀粉转换为糖的工艺。喷射蒸煮是指在高温和高压下进行的蒸煮工艺,尽管具体的温度和压力可以在很宽的范围内变化。通常情况下,喷射蒸煮在约120-150℃的温度下(约248-302°F)和约8.4-10.5kg/cm2(约120-150lbs/in2)的压力下进行,尽管当采用的压力约为8.4kg/cm2(约120lbs/in2)时,温度可以低至约104-107℃(约220-225°F)。随后是液化28、糖化30、发酵32、酵母回收34以及蒸馏/脱水36。随着混合物或“糊状物(mash)”在90-95℃下维持,α-淀粉酶将糊化的淀粉水解为麦芽糊精和低聚糖(葡萄糖糖分子的链)而发生液化,以产生液化醪液(liquefiedmash)或浆液。在糖化步骤30中,将液化醪液冷却至约50℃,并添加被称为糖化酶的商业酶。所述糖化酶将麦芽糊精和短链低聚糖水解成单个的葡萄糖糖分子而获得了液化醪液。在发酵步骤32中,添加常规的酵母菌株(酿酒酵母)以将葡萄糖代谢为乙醇和CO2。完成后,发酵醪液(“啤酒”)将含有约17%-18%的乙醇(以体积/体积为基准),和来自所有剩余谷物成分的可溶性和不溶性固体。发酵后剩余的固体和一些液体进入酵母可以作为副产品回收的蒸发阶段。在酵母回收步骤34中,酵母可以选择性地回收。在某些情况下,回收CO2并将其作为商品出售。发酵步骤32之后是蒸馏和脱水步骤36,其中,啤酒被泵入将其煮沸以蒸发乙醇的蒸馏塔(distillationcolumns)中。乙醇蒸汽在蒸馏塔中冷凝,液态醇(在此情况下为乙醇)从蒸馏塔顶部排出,纯度约为95%(190酒精纯度)。然后,190酒精纯度的乙醇经过分子筛脱水塔(molecularsievedehydrationcolumn),从乙醇中除去剩余的残留水,以获得基本上为100%的乙醇(199.5酒精纯度)的最终产品。现在,这种无水乙醇可以备用于汽车燃料。由于胚芽、纤维和谷蛋白在之前的分离步骤16、22和24中已经被除去,因此,在湿磨乙醇生产工艺10的最后不需要离心的步骤。在湿磨工艺10中,蒸馏和脱水36后产生的“酒糟(stillage)”通常被称为“全酒糟”,尽管在技术上与下图2中所述的干磨工艺产生的全酒糟是不同的类型,因为干磨工艺产生的全酒糟不含有不可溶性固体。其他湿磨生产商可能会将这种类型的酒糟称为“稀”酒糟。湿磨工艺10能够产生转换为醇的高质量的淀粉产物,以及能够产生作为副产品出售以产生额外的收益流的胚芽、纤维和蛋白质的分离流。然而,各种副产物的总产量不太理想,而且湿磨工艺复杂,成本高,需要投入大量资金且运作消耗的能量高。由于湿磨工艺如此高昂的资金成本,一些醇厂更愿意使用较简单的干磨工艺。图2为典型的干磨乙醇生产工艺100的流程图。工艺100开始于研磨步骤102,其中,干燥的整个玉米粒通过锤式粉碎机以将它们研磨成粉(meal)或细粉(finepowder)。将研磨的粉与水混合以制备浆液,然后加入被称为α-淀粉酶的商业酶(未示出)。然后,在加压的喷射蒸煮工艺104中,将所述浆液加热至约120℃维持约0.5至三(3)分钟,以糊化(溶解)研磨的粉中的淀粉。值得注意的是,除喷射蒸煮外的一些工艺,需要在约50-95℃的温度下将浆液在浆料槽中维持较长的时间。然后进行可以添加额外的α-淀粉酶的液化步骤106。液化步骤后的液流含有约30%的干固体(DS)含量,干固体具有玉米粒中涵盖的所有成分,包括糖、蛋白质、纤维、淀粉、胚芽、油和盐。随后分别进行单独的糖化和发酵步骤,108和110,尽管在大多数商业干磨乙醇工艺中,糖化和发酵是同时发生的。在工业上,此步骤被称为“同时糖化和发酵”(SSF)。糖化和SSF都可以进行长达约50-60小时,发酵将糖转化为醇。在酵母回收步骤112中,可以选择性地回收酵母。发酵步骤110之后为蒸馏和脱水步骤114,与湿磨工艺类似,该步骤旨在回收醇。最后,离心分离步骤116涉及将蒸馏和脱水步骤114产生的残留物,即“全酒糟”进行离心,以从液体(“稀酒糟”)中分离不溶性固体(“湿饼”)。离心分离的液体含有约8%-10%的DS。在蒸发步骤118中,稀酒糟进入蒸发器以蒸发水分,留下含有来自发酵的可溶性(溶解的)固体(25-35%的干固体)的稠糖浆。可以将浓缩的浆液送去离心以从糖浆中分离油。所述油可以作为独立的高价值产品出售。油的产量通常约为0.5Lb/Bu的玉米,具有高含量的游离脂肪酸。当油在发酵中维持约50小时时产生的游离脂肪酸。游离脂肪酸含量降低了油的价值。由于蛋白质和油形成了乳剂(emulsion),脱油离心仅能脱除50%以下的油,分离效果不理想。可以将具有高于10%的油的糖浆与离心的湿饼混合,混合物可以作为具有可溶物的湿酒糟(DWGS)出售给肉牛和奶牛饲养场。可替代地,可以在干燥步骤120干燥湿饼和浓缩的糖浆的混合物,并作为具有可溶物的干酒糟(DDGS)出售给奶牛和肉牛饲养场。该DDGS具有玉米中所有的蛋白质和75%的油。但是由于高百分比的纤维,并且在某些情况下,油有碍于动物的消化,DDGS的价值较低。因为干磨工艺100仅产生乙醇和低价值的DDGS,许多公司已经开始研究干法分馏工艺(dryfractionprocess)。在该工艺中,玉米经过例如蒸汽处理的预处理步骤,然后利用各种类型的机械分离设备分离玉米的干组分,包括纤维、淀粉和油/胚芽部分。虽然这些分离工艺实现了一些组分的分离,但通常分离得不完全。例如,纤维部分通常含有以干基计30%以上的淀粉,胚芽含有以干基计25%以上的淀粉和35%以上的油。此外,在这些工艺中,回收的玉米粒中的总油不到30%;并且,胚芽和纤维部分必须经过纯化步骤才能够以合理的价格出售。干法分馏后,淀粉(含有蛋白质)经另外的研磨步骤,然后液化、发酵、蒸馏并蒸发,以产生醇和糖浆,与干磨工艺100大致相同。但由于淀粉在胚芽和纤维部分的损失,醇的产量通常低至2.3gal/Bu的玉米。此外,上述用于胚芽和纤维的纯化步骤复杂且成本较高。值得注意的是,干法分馏工艺不能进行精细分离(sharpseparation),且产生低纯度的副产品,这使下游的纯化步骤变得复杂。由于成本高且产量低,这些干法分馏工艺还没有在工业上被普遍接受。在干磨工业中已经进行了其它的尝试,以希望回收高价值的副产品,如油。然而,由于高浓度的固体以及由于油未从固体颗粒中释放,从“锤式粉碎”浆液中分离油的尝试失败了。从干磨工艺的蒸发阶段中回收油的工艺取得了一些成功。然而,产量相对较低,并且油必须经过整个工艺,包括蒸发前的发酵。工艺的这些步骤中油的存在可能会降低工艺其余部分的效率。已经尝试了在发酵后直接回收油。然而,混合的工艺和发酵过程中油的乳化使得其非常难以脱除。进行了其它的尝试以通过溶剂萃取直接从玉米中回收油,但对于商业用途,例如成本太高。因此,提供一种改进的从用于生产醇的谷物中分离副产品的系统和方法,以克服上述各种缺点,例如,生产具有理想产量的高价值的副产品,这将是有利的。
技术实现要素:本发明涉及一种从用于生产醇的谷物中分离副产品的系统和方法。所述系统和方法能够在油、蛋白质、纤维,和/或淀粉之间提供更精细地分离,并且,由于醇生产路线的各种改变,能够生产更纯的副产品。在一种实施方式中,从用于生产醇的谷物中分离副产物的方法包括:将用于生产醇的粉碎的谷物进行液化,以提供含有纤维、蛋白质和胚芽的液化淀粉溶液。从液化淀粉溶液中分离胚芽,然后研磨,例如,研磨至颗粒尺寸小于150微米(或小于50微米)以释放油,从而提供胚芽/油混合物。在发酵前,从胚芽/油混合物中分离油以获得油副产品。所述胚芽/油混合物的pH可以调节到约8至约10.5,和/或向其中添加酶以促进油的释放。也可以将所述胚芽/油混合物置于约180°F至约200°F的温度下。在一种实例中,油的产量大于1.0lb/Bu。在另一种实施方式中,从用于生产醇的谷物中分离副产品的方法包括:将用于生产醇的粉碎的谷物进行液化,以提供含有纤维、蛋白质、胚芽和油的液化淀粉溶液。从液化淀粉溶液中分别分离胚芽和油以获得油副产品。然后,研磨分离的胚芽以释放油,从而提供胚芽/油混合物。在发酵前,从胚芽/油混合物中分离油以获得油副产品。在另一种实施方式中,从用于生产醇的谷物中分离副产品的方法包括:将用于生产醇的粉碎的谷物进行液化,以提供含有纤维、蛋白质、胚芽和油的液化淀粉溶液。从液化淀粉溶液中分离含有纤维和胚芽的固体。然后,在发酵之前,从液化淀粉溶液中分离油以获得油副产品。在另一种实施方式中,从用于生产醇的谷物中分离副产品的连续系统包括:破碎用于生产醇的谷物的研磨设备,以及辅助将破碎的谷物的淀粉转化为糖以提供含有纤维、蛋白质和胚芽的液化淀粉溶液的液化装置。所述系统还包括从液化淀粉溶液中分离胚芽的胚芽分离器,以及研磨分离的胚芽以释放油,从而提供胚芽/油混合物的胚芽研磨机。从胚芽/油混合物中分离油以产生油副产品的胚芽/油分离器。然后,将所述液化淀粉溶液分别进行发酵和蒸馏以生产醇的发酵罐和蒸馏器。在又一种实施方式中,从用于生产醇的谷物中分离副产物品的连续系统包括:破碎用于生产醇的谷物的研磨设备,以及辅助将破碎的谷物的淀粉转化为糖以提供含有纤维、蛋白质、胚芽和油的液化淀粉溶液的液化装置。所述系统还包括从液化淀粉溶液中分别分离胚芽和油以获得油副产品的分离器,以及研磨分离的胚芽以释放油,从而提供胚芽/油混合物的胚芽研磨机。从胚芽中分离油以获得油副产品的胚芽/油分离器。然后,将含有分离的胚芽和液化淀粉溶液的混合物分别进行发酵和蒸馏以生产醇的发酵罐和蒸馏器。在另外一种实施方式中,从用于生产醇的谷物中分离副产物的连续系统包括:破碎用于生产醇的谷物的研磨设备,以及辅助将破碎的谷物的淀粉转化为糖以提供含有纤维、蛋白质、胚芽和油的液化淀粉溶液的液化装置。所述系统还包括从液化淀粉溶液中分离含有纤维和胚芽的固体的固体/液体分离器。然后,从液化淀粉溶液中分离油以获得油副产品的油分离器。以及然后,将含有液化淀粉溶液和固体的混合物分别进行发酵和蒸馏以生产醇的发酵罐和蒸馏器,所述液化淀粉溶液含有蛋白质且所述固体含有纤维和胚芽。根据上述特点,本发明提供了一种改进的从用于生产醇的谷物中分离副产品的系统和方法,该系统和方法能够生产具有理想产量的高价值的副产品。附图说明附图被合并入说明书中并构成本说明书的一部分,用来说明本发明的实施方式,并结合下面给出的详细描述的实施方式一起解释本发明的原理。图1是典型的湿磨乙醇生产工艺的流程图;图2是典型的干磨乙醇生产工艺的流程图;图3是根据本发明的实施方式的从用于生产醇的谷物中分离高价值的副产品的系统和方法的流程图;图3A是图3的系统和方法的变体的流程图;图4是根据本发明的另一种实施方式的从用于生产醇的谷物中分离高价值的副产品的系统和方法的流程图;图4A是图4的系统和方法的变体的流程图;图5是根据本发明的另一种实施方式的从用于生产醇的谷物中分离高价值的副产品的系统和方法的流程图;图5A是图5的系统和方法的变体的流程图;以及图5B是图5的系统和方法的另一种变体的流程图。具体实施方式上文已经讨论了图1和图2,分别代表典型的湿磨和干磨乙醇生产工艺的流程图。图3-5B说明了从用于生产醇的谷物中分离高价值的副产品(例如油、白纤维(whitefiber)和蛋白粉)的系统和方法的各种实施方式,它们是在典型的工艺和其它工艺上的改进。下文将详细讨论这些系统和方法。作为图3-5B中所示的实施方式的总括,各个系统和工艺包括:在研磨玉米后以及发酵前,利用液化淀粉溶液中不同组分之间的密度差异从液化淀粉溶液中分离胚芽。液化后的液化淀粉溶液中含有油、胚芽、砂砾(grit)、蛋白质和颗粒尺寸在小于50微米至大于2毫米范围内变化的纤维颗粒。油的密度通常约为0.9克/立方厘米,胚芽颗粒约为1克/立方厘米,砂砾、蛋白质和纤维约为1.1-1.15克/立方厘米。在浸泡/蒸煮和液化期间液体溶液具有约1.05-1.12克/立方厘米的密度(例如,约15-28白利糖度(Brix)的糖溶液)。可以利用液化淀粉溶液的高密度从砂砾、蛋白质和纤维中分离胚芽和油。此外,液化的浆液的pH值约为5-6。将胚芽从液化淀粉溶液中分离之前制备胚芽的方法通常有两种。第一种方法如图3和3A所示,涉及浸泡和蒸煮玉米,然后利用研磨或滚压将玉米粒破碎,然后进行液化。可替代地,如图4-5B中所示,省略浸泡和蒸煮步骤,与现有的干磨工艺大体相同,例如,可以将玉米直接进行锤式粉碎,然后进行液化。研磨步骤意在不将纤维切割得太细的情况下破碎胚芽和砂砾颗粒,并破坏淀粉和蛋白质之间的连接。存在三种类型的纤维:(1)果皮,平均颗粒尺寸通常约为1mm-5mm;(2)胚芽根(tipcap),平均颗粒尺寸约为500微米;(3)以及细纤维,平均颗粒尺寸约为250微米。可以使用过滤设备(filtrationdevice)例如纤维离心机,根据具有不同尺寸的孔的筛子以分离不同类型的纤维。果皮和胚芽根维持在大于300微米的尺寸下,而胚芽和砂砾小于该尺寸。此外,细纤维能够引发下游纤维/蛋白质的分离问题,并能够产生非常湿的干燥成本非常高的纤维(DDG)饼。在研磨/冲击式粉碎步骤中也可以选择性的加入酶,例如包括淀粉酶、蛋白酶或它们的组合的细胞壁降解酶,例如,以帮助破坏蛋白质、淀粉和纤维之间的连接。在浸泡/蒸煮或液化期间或之后,液化淀粉溶液可以通过几种可能的分离设备,如三相滗析器(decanter)或旋风分离器(cyclone),由此分离例如胚芽和油,胚芽和油可以按照如下详述地进一步被加工,例如,生产满足需要的油和/或纤维副产品。现参见图3,图3示出了一般对应湿式系统和工艺的系统和方法200,其中,从用于生产醇的谷物中分离副产品(例如,高价值的胚芽和蛋白质)以生产例如满足需要的用于工业用途的白纤维(例如,果皮)和高价值的油。在这种特定的系统和方法200中,将玉米进行浸泡/蒸煮步骤202,此处,玉米在充满了温度约为55-95℃的水的浸泡罐中浸泡4-12小时。所述浸泡罐可选择性的含有酶(例如α-淀粉酶),以及约50-100ppm的亚硫酸钠、二氧化硫等。然后可以使用一个或多个研磨式粉碎机和/或滚压粉碎机将浸泡后的玉米进行研磨步骤204,以破碎玉米粒并释放胚芽。在研磨步骤204中或之前可以选择性地添加酶,例如α-淀粉酶。然后,将含有淀粉的浆液进行液化步骤206,以提供具有约1.05-1.15克/立方厘米的密度的液化淀粉溶液。在液化步骤206中,淀粉开始转换为液化淀粉溶液。此处可以利用本领域公知的任何合适的液化装置。接下来,在胚芽分离步骤208中,使用例如两级胚芽旋风分离器或因此设计的串联的盘式或滗析式离心机,利用液化淀粉溶液中不同组分之间的密度差异将胚芽,以及纤维、蛋白质和砂砾从液化淀粉溶液中分离。具体地,将液化淀粉溶液用作重介质液体以使胚芽漂浮,随后将胚芽从中分离。然后,将胚芽输送到研磨步骤209中的研磨装置,在不产生细纤维的情况下,将胚芽颗粒精细研磨至颗粒尺寸小于150微米(或者,在另一实例中,小于50微米),以从胚芽中释放油,从而提供油/胚芽混合物。将研磨的胚芽(或油/胚芽混合物)输送到胚芽维持罐210中,此处,例如,可以通过加入化学试剂(例如,氢氧化钠、石灰(lime)、碳酸钠、磷酸三钠等)将罐中胚芽的pH值调节至约8至约10.5(或约8至约9.5),以促进油从胚芽中释放。此外,也可以加入细胞破壁酶(例如,蛋白酶等),和/或化学试剂(例如,亚硫酸钠等),以促进油从胚芽中释放。在一种实例中,胚芽可以在温度为约140°F至约200°F(或者,约180°F至约200°F)的罐中保持约1小时。接下来,将油和细胚芽的混合物进行油/胚芽分离步骤211,此处,使用例如三相滗析器或三相盘式离心机,利用残留的液化淀粉溶液中不同组分之间的密度差异从细胚芽中分离油。相对于在下游回收的油,特别是发酵后回收的油,在本工艺中的此阶段回收的油在颜色和游离脂肪酸含量(从约2%至约5%)方面具有更理想的质量。具体地,在发酵前回收的油的颜色较淡,游离脂肪酸含量较低。油的产量可以包括1.0lb/Bu以上。在一种实例中,油的产量为约1.0至约1.2lb/Bu。除此之外,或者作为发酵前油回收工作的一种替代,应理解的是,类似的油回收方法可以在发酵后进行。利用研磨式粉碎机、销棒粉碎机(pinmill)或高压力锅,将来自胚芽分离步骤208的含有纤维、蛋白质和砂砾的下层液化淀粉溶液进行粉碎步骤212,例如,以进一步破坏纤维、淀粉和蛋白质之间的连接。虽然没有具体示出,在粉碎步骤212或其后,包括发酵过程中,可以选择性地添加各种酶(以及它们的类型),如葡糖淀粉酶、真菌酶(fungal)、纤维素酶(cellulose)、纤维二糖酶、蛋白酶等,以促进组分的分离。在发酵步骤213中,将含有分离的细胚芽(脱油的)的固体和来自油/胚芽分离步骤211的残留的液化淀粉溶液返回至来自粉碎步骤212的液化淀粉溶液。在下游可以从纤维和蛋白质组分中分离出细胚芽作为高价值的细胚芽颗粒。在一种可替代的实例中,可以将输送至研磨步骤209的分离的胚芽研磨至颗粒尺寸小于500微米,但不能小至油从胚芽中释放,且不产生细纤维。在一种实例中,所述胚芽的颗粒尺寸为50-500微米,平均颗粒尺寸为250微米。此后,在粉碎细步骤212后以及发酵步骤213前,可以将细胚芽颗粒返回到液化淀粉溶液中,用于在下游作为高价值的细胚芽颗粒被分离出来。在这种可替代的实例中,省去了胚芽维持罐210和油/胚芽分离步骤211。作为替代,所述油/胚芽分离步骤211可以选择性地替换为溶剂萃取步骤214、醇/胚芽分离步骤215,以及醇蒸发步骤216,以在维持罐210中从油和细胚芽的混合物中回收油。具体地,可以将油和细胚芽的混合物从维持罐210输送至溶剂萃取步骤214,此处,将来自蒸馏步骤217的回收的醇添加到油和细胚芽的混合物中,以从中提取油。然后将醇/油/胚芽的混合物输送到醇/胚芽分离步骤215,通过利用例如滗析式或盘式离心机从细胚芽中分离含有萃取的油的醇。在发酵步骤213中,将含有分离的细胚芽(脱油的)的固体(或重相)和来自醇/胚芽分离步骤213的残留的液化淀粉溶液返回至来自粉碎步骤212的液化淀粉溶液。将分离的醇/油溶液(或轻相)输送至醇蒸发步骤214,此处,使用蒸发器分离油和醇用于它们的回收。作为蒸馏塔的一部分可以包括小的蒸发器。脱油的胚芽通常含有约10%-20%的油。但是,由于溶剂萃取步骤214,脱油的胚芽含有约4%-10%的油。油的产量能达到1.0lb/Bu以上。在一种实例中,油的产量为约1.0至约1.4lb/Bu(或1.2至约1.4lb/Bu)。在发酵步骤213中,将含有纤维、蛋白质、砂砾以及现在的细胚芽颗粒的液化淀粉溶液进行发酵,然后在蒸馏步骤217中进行蒸馏。在发酵过程中细胚芽将被部分脱油,这有助于后续具有降低的或没有胚芽蛋白的高价值的油的分离和生产。在蒸馏塔中,液化淀粉溶液中的糖从酒糟(含有纤维、蛋白质和细胚芽颗粒)中分离出来,以获得醇。在纤维/蛋白质分离步骤218中,可以使用筛选设备(例如搅拌筛选机/过滤离心机),利用颗粒尺寸的差异从细胚芽颗粒、细纤维和蛋白质(谷蛋白)中分离纤维,以从中去除白纤维,即果皮。此处,筛孔的尺寸通常约为1mm,但可以从约0.3mm至1.5mm的范围内变动。另外,关于颗粒尺寸,蛋白质的平均颗粒尺寸约为1-5微米,细胚芽的约为10-500微米,且各种纤维从约50微米至3mm的尺寸范围内变动。洗涤并干燥分离出的纤维以获得高价值的用于工业用途的白纤维,产量约为2lb/Bu。分离出的纤维还可以用作生产仲醇的原料,产量约为3lb/Bu。白纤维主要来自果皮,且含有低于10%的蛋白质,低于2%的油,和低于2%的淀粉。在一种实例中,白纤维包括85%以上的果皮,在另一种实例中,90%以上的果皮,在另一种实例中,95%以上的果皮。继续参见图3,将来自过滤离心的滤液(含有残留的具有约30微米至300微米以及约300微米至500微米尺寸的细纤维和胚芽根),以及细胚芽和谷蛋白(蛋白质)移至细胚芽和纤维分离步骤219,此处,通过精细筛选设备例如具有筛孔尺寸为45微米左右的搅拌筛选机或压力筛选机,将细胚芽和细纤维从谷蛋白溶液中去除。将细胚芽和细纤维输送到细胚芽/纤维维持罐220,此处,例如,可以通过加入化学试剂(例如,氢氧化钠、石灰、碳酸钠、磷酸三钠等)将罐中的细胚芽/纤维的pH值调节至约8至约10.5(或约8至约9.5),以促进额外的油从胚芽中释放。此外,也可以加入细胞破壁酶(例如,蛋白酶等),和/或化学试剂(例如,亚硫酸钠等),以促进额外的油从胚芽中释放。接下来,将细胚芽和纤维的混合物进行细纤维分离步骤221,此处,通过例如滗析器将细纤维从细胚芽中分离,然后干燥以获得DDG。在一种实例中,细纤维含有低于15%的蛋白和4%的油。将来自细胚芽和纤维分离步骤219的分离液(centrate)和来自细纤维分离步骤221的分离液返回,并进入蛋白质回收/脱水步骤222,该步骤中使用例如,滗析器、喷嘴离心机或盘式滗析器以回收细胚芽和蛋白质(以及使用的酵母)。可替代地,来自细纤维分离步骤221的分离液可以使用例如,滗析器、喷嘴离心机或盘式滗析器进行选择性地脱水,并返回胚芽研磨步骤209以提取更多的油。将来自回收/脱水步骤222的组分送至干燥机223以生产高价值的具有约60%的谷蛋白和约40%的胚芽/酵母的谷蛋白/胚芽/酵母混合物(蛋白粉)。来自蛋白质脱水步骤222的下层进入蒸发器226,以从中分离油,并生产糖浆,所述糖浆可以如标号228表示的与DDG混合并干燥,以获得供如牛或猪的低蛋白(约20%)/低油(约7%)的DDGS。在一种实例中,蛋白质不高于20%,油不高于7%。在另一种实例中,可以在此工艺中的浸泡/蒸煮步骤202和干燥步骤228之间的任何步骤中添加亚硫酸钠、二氧化硫等。值得注意的是,在该系统和方法200中,大部分的副产品在发酵后被回收。关于油的回收,每当回收油时,在收集罐中一般都会倾向于形成乳剂层。在储存油的罐中,油自然飘浮,且乳剂层与所有固体一起沉向底部。乳剂层中的叶黄素含量显著,这有利于鸡蛋蛋黄的形成和使皮肤变黄。在可选的离心步骤(未示出)中,可以回收乳剂层中含有的叶黄素,并在干燥蛋白质前与蛋白粉副产品混合以增加饲料的价值。例如,可以将亚硫酸钠、二氧化硫等添加到湿蛋白饼中,以在湿蛋白饼被输送至蛋白质干燥机223前将二氧化硫水平维持在20ppm以上。二氧化硫可以防止蛋白质干燥机223中的叶黄素分解。来自离心机的油(轻相)可以返回到油储存罐中。现在参见图3A,该图显示了图3的系统和方法200的变体的流程图。在该系统和方法200a中,谷蛋白(蛋白质)粉和白纤维(即,果皮)可以在发酵步骤213之前去除。简单地说,考虑到背景因素,需要注意的是,来自典型玉米湿磨工艺的谷蛋白粉中含有100-200mg/lb的叶黄素。在发酵步骤213之前回收谷蛋白粉能够减少叶黄素在发酵步骤213的过程中、以及随后的蒸馏和蛋白质回收步骤217、222中的损失。此外,需要注意的是,果皮的颗粒尺寸对于工业用途很重要,如在造纸工业中。较大尺寸的果皮颗粒,如从约1至约5mm,能堵塞发酵过程中使用的热交换器。因此,在发酵步骤213前去除果皮能避免这些堵塞问题,并且由于果皮的早期去除,可以增加约15%的发酵能力。如图3A所示,在胚芽分离和随后的粉碎步骤212之后,利用筛选设备例如过滤离心机将液化淀粉溶液与纤维、蛋白质和砂砾一起进行谷蛋白/纤维分离步骤230,以从中除去白纤维,即果皮。筛孔尺寸通常约为1.5mm,但可以从约1mm至约2mm的范围内变化。如标号232所示,洗涤并干燥分离出的纤维,以获得高价值的用于工业用途的白纤维,产量约为2lb/Bu。分离出的纤维还可以用作生产仲醇的原料。例如,对于用于造纸工业的原料的白纤维,纤维主要来自果皮,而用于生产仲醇的白纤维,纤维主要来自果皮、胚芽根和细纤维,产量为3-4lb/Bu,并含有低于14%的蛋白质和低于5%的油。在一种实例中,白纤维包括85%以上的果皮,在另一种实例中,90%以上的果皮,在另一种实例中,95%以上的果皮。可以利用本领域公知的方法选择性地分离来自谷蛋白/纤维分离步骤230的上层液化淀粉溶液中的蛋白质,其中,谷蛋白进入洗涤和干燥步骤234,以获得具有理想叶黄素百分率(即,约100mg/Lb至约200mg/Lb)的高价值谷蛋白粉。否则,在发酵步骤213中,将上层液化淀粉溶液部分与细胚芽颗粒混合。该工艺的其余部分通常与图3的相同,除了在该工艺的前面,在发酵步骤213之前回收谷蛋白粉和白纤维。具体地,在图3的系统和方法200中,之前便将白纤维从蛋白质、细纤维和细胚芽颗粒中进行了分离并回收,在细胚芽和纤维分离步骤219中,使用筛选设备例如具有约45微米筛孔尺寸的搅拌筛选机或压力筛选机,从残留的蛋白质(谷蛋白)中分离尺寸大于50微米的细纤维和细胚芽。然后,将细胚芽和细纤维输送到细胚芽/细纤维维持罐220中,此处,例如,可以通过加入化学试剂(例如,氢氧化钠、石灰、碳酸钠、磷酸三钠等)将罐中的细胚芽/纤维的pH值调节至约8至约10.5(或约8至约9.5),以促进油从胚芽中释放。此外,也可以加入细胞破壁酶(例如,蛋白酶等),和/或化学试剂(例如,亚硫酸钠等),以促进油从胚芽中释放。接下来,将胚芽和纤维的混合物进行细纤维分离步骤221,此处,通过例如滗析器从细胚芽中分离细纤维,然后干燥以获得DDG。在一种实例中,细纤维含有低于15%的蛋白质和4%的油以便生产DDG。将来自细胚芽和纤维分离步骤219的分离液和来自细纤维分离步骤221的分离液返回,并进入使用例如滗析器、喷嘴离心机或盘式滗析器的蛋白质回收/脱水步骤222,以回收细纤维和残留蛋白质以及使用的酵母。可替代地,可以使用例如,滗析器、喷嘴离心机或盘式滗析器,将来自细纤维分离步骤221的分离液选择性地脱水,并返回胚芽研磨步骤209以提取更多的油。将来自蛋白质回收/脱水步骤222的组分送至干燥机223以主要生产具有约60%的谷蛋白和约40%的胚芽/酵母的胚芽/酵母混合物。现参见图4,该图示出了从用于生产醇的谷物中分离高价值副产品的系统和方法300的另一种实施方式。该系统和方法300通常对应于干磨乙醇生产系统和工艺,分离各种副产品,以生产例如用于生产仲醇的纤维素材料和高价值油。为达到这个目的,在这种具体的工艺和方法300中,首先,将玉米进行例如锤式粉碎302,能够用于将玉米研磨至颗粒尺寸小于约7/64英寸,并促进油从中释放。在一种实例中,颗粒尺寸从约50微米到3mm。研磨有助于破坏纤维、蛋白质、淀粉和胚芽之间的连接。在另一种实例中,例如来自干法分馏工艺的胚芽部分可以取代此处起始的未研磨的玉米。将研磨的玉米与水混合,并输送至液化步骤304,提供具有约1.05-1.15克/立方厘米的密度的液化淀粉溶液。在液化步骤304,淀粉开始转化为液化淀粉溶液。可以在液化步骤304添加酶例如α-淀粉酶,此处可以使用本领域公知的任何合适的液化装置。来自液化步骤304的液流含有约1lb/Bu的游离油和约1.5lb/Bu的胚芽颗粒(尺寸在约小于50微米至约1mm的范围内变动)、1lb/Bu的砂砾(尺寸在约50微米至约1mm的范围内变动)以及5lb/Bu的纤维(颗粒尺寸在约50微米至约3mm的范围内变动)。该液流进入胚芽/油分离步骤306,利用三相分离装置(例如,三相滗析器、三相盘式离心机、水利旋流器等),根据液化淀粉溶液中不同组分的密度差异,从含有重纤维、蛋白质和砂砾的液化淀粉溶液中分别分离油和胚芽。具体地,将液化淀粉溶液用作重介质液体以漂浮胚芽和油(分别具有约1.0-1.05克/立方厘米和0.9-0.92克/立方厘米的密度)。此处需要注意的是,如果在胚芽/油分离步骤306中利用三相盘式离心机,可能需要例如进行预筛选步骤(未示出)以除去大尺寸的纤维颗粒,例如>750微米。如果利用该预筛选步骤,固体部分绕开胚芽/油分离步骤306并直接进入下面进一步讨论的研磨步骤310。相对于在下游回收的油,特别是发酵后回收的油,在本工艺中的此阶段(例如,在胚芽/油分离步骤306)回收的油在颜色和游离脂肪酸含量(从约2%至约5%)方面具有更理想的质量。具体地,在发酵前回收的油的颜色较淡,游离脂肪酸含量较低。油的产量可以包括1.0lb/Bu以上。在一种实例中,油的产量为约1.0至约1.2lb/Bu。然后,将分离的胚芽供给到研磨步骤307中的研磨装置,以将胚芽颗粒精细研磨至颗粒尺寸在10-300微米之间,以促进从中释放额外的油,从而提供油/胚芽混合物。在另一种实例中,颗粒尺寸小于50微米。将研磨的胚芽(或油/胚芽混合物)输送到胚芽维持罐308中,此处,例如,可以通过加入化学试剂(例如,氢氧化钠、石灰、碳酸钠、磷酸三钠等)将细胚芽的pH值调节至约8至约10.5(或约8至约9.5),以促进油从胚芽中释放。此外,也可以加入细胞破壁酶(例如,蛋白酶等),和/或化学试剂(例如,亚硫酸钠等),以促进油从胚芽中释放。在一种实例中,细胚芽可以于约140°F至约200°F(或者,约180°F至约200°F)的温度下在罐中保持约1小时。接下来,将油和胚芽的混合物进行油/胚芽分离步骤309,此处,使用例如三相滗析器或三相盘式离心机,利用残留的液化淀粉溶液中不同组分之间的密度差异从胚芽中分离油。相对于在下游回收的油,特别是发酵后回收的油,在本工艺中的此阶段回收的油在颜色和游离脂肪酸含量(从约2%至约5%)方面具有更理想的质量。除此之外,或者作为发酵前油回收工作的一种替代,应当理解的是,类似油的回收方法可以在发酵后进行。将来自胚芽分离步骤306的含有纤维、蛋白质和砂砾的下层液化淀粉溶液进行例如使用研磨式粉碎机的研磨步骤310,以进一步破坏纤维、淀粉和蛋白质之间的连接。虽然没有具体示出,在研磨步骤310过程中,包括随后的发酵过程中,可以选择性地添加各种酶(以及它们的类型)如葡糖淀粉酶、真菌酶、纤维素酶、纤维二糖酶、蛋白酶等,以促进组分间的分离。将含有分离的细胚芽的固体和来自油/胚芽分离步骤309的残留的液化淀粉溶液返回至来自粉碎步骤310的液化淀粉溶液,然后进行发酵步骤311。在下游可以将细胚芽颗粒从纤维和蛋白质组分中分离出来,并作为高价值的细胚芽颗粒(部分脱油的)。在一种可替代的实例中,将分离的胚芽输送至研磨步骤310,此后,在发酵阶段,在发酵步骤311的粉碎步骤310之后,可以将细胚芽颗粒返回到液化淀粉溶液中,用于在下游作为高价值的细胚芽颗粒被分离出来。在这种可替代的实例中,省去了方法中胚芽维持罐308和油/胚芽分离步骤309。作为替代,油/胚芽分离步骤309可以选择性地替换为溶剂萃取步骤312、醇/胚芽分离步骤313以及醇蒸发步骤314,以在维持罐308中从油和细胚芽的混合物中回收油。具体地,可以将油和细胚芽的混合物从维持罐308输送至溶剂萃取步骤312,此处,将来自蒸馏步骤315的回收的醇添加到油和细胚芽的混合物中,以从中提取油。然后将醇/油/胚芽混合物输送到醇/胚芽分离步骤313,以通过利用例如滗析式或盘式离心机从细胚芽中分离含有萃取的油的醇。在发酵步骤311中,将含有分离的细胚芽(脱油的)的固体(或重相)和来自醇/胚芽分离步骤313的残留的液化淀粉溶液返回至来自粉碎步骤310的液化淀粉溶液。将分离的醇/油溶液(或轻相)输送至醇蒸发步骤314,此处,使用蒸发器分离油和醇用于它们的回收。作为蒸馏塔的一部分可以包括小的蒸发器。脱油的胚芽通常含有约10%-20%的油。但是,由于溶剂萃取步骤312,所述脱油的胚芽含有约4%-10%的油。油的产量能达到1.0lb/Bu以上。在一种实例中,油的产量为约1.0至约1.4lb/Bu(或1.2至约1.4lb/Bu)。在发酵步骤311中,将含有纤维、蛋白质、砂砾以及现在的细胚芽颗粒的液化淀粉溶液进行发酵,然后在蒸馏步骤315中进行蒸馏。在蒸馏塔中,将发酵溶液(也称为啤酒)从酒糟(含有纤维、蛋白质和细胚芽颗粒)中分离,以获得醇。在纤维/蛋白质分离步骤316中,使用筛选设备例如搅拌筛选机、过滤离心机或滗析器,利用颗粒尺寸的差异从细胚芽颗粒和蛋白质(谷蛋白)中分离纤维,以从中去除纤维。筛孔尺寸通常约为50微米,以收集大量的胚芽根、果皮以及细纤维,但可以从约300微米至700微米的范围内变动。洗涤并选择性地干燥分离出的纤维以获得用于生产仲醇的纤维素,该纤维素为质量低于例如通过图3的工艺获得的白纤维的纤维。可以将得到的含有果皮和胚芽根(并可以含有细纤维),并具有低于15%的蛋白质,低于5%的油,以及低于4%的淀粉的纤维素材料在不进行进一步处理的情况下作为原料输送至本领域公知的仲醇系统。继续参考图4,将来自纤维/蛋白质分离步骤316的分离液(含有残留的具有30微米至300微米以及300微米至500微米大小的细纤维和胚芽根)以及细胚芽和谷蛋白移至细胚芽和纤维分离步骤317,此处,通过精细筛选设备例如具有筛孔尺寸为45微米左右的搅拌筛选机或压力筛选机将细胚芽和细纤维从谷蛋白溶液中去除。将细胚芽和细纤维输送到细胚芽/纤维维持罐318,此处,例如,可以通过加入化学试剂(例如,氢氧化钠、石灰、碳酸钠、磷酸三钠等)将罐中的细胚芽/纤维的pH值调节至约8至约10.5(或约8至约9.5),以促进额外的油从胚芽中释放。此外,也可以加入细胞破壁酶(例如,蛋白酶等),和/或化学试剂(例如,亚硫酸钠等),以促进额外的油从胚芽中释放。接下来,将胚芽和纤维的混合物进行细纤维分离步骤319,此处,通过例如滗析器将细纤维从细胚芽中分离。将细纤维和来自蒸馏的酒糟混合,以便可以再次进行纤维/蛋白质分离步骤316。将来自细胚芽和纤维分离步骤317的分离液和来自细纤维分离步骤319的上层返回,并进入蛋白质回收/脱水步骤320,该步骤中使用例如,滗析器、喷嘴离心机或盘式滗析器以回收细胚芽和蛋白质(以及使用的酵母)。可替代地,来自细纤维分离步骤319的上层可以使用例如,滗析器、喷嘴离心机或盘式滗析器选择性地脱水,并返回胚芽研磨步骤310以提取更多的油。将来自回收/脱水步骤320的组分送至干燥机321以生产高价值的具有约60%的谷蛋白和约40%的胚芽/酵母的谷蛋白/胚芽/酵母混合物(蛋白粉)。来自蛋白质脱水步骤的上层进入蒸发器324,以从中分离各种油,并获得高浓度的糖浆(大于65%的DS),其可以在其它物质中作为(a)用于生产仲醇的营养素,(b)动物饲料,(c)肥料,(d)和/或用于生产沼气的厌氧发酵物。另外,在发酵步骤311之前和之后,可以选择性的提供离心步骤(未示出)以在回收的油的乳剂层中回收叶黄素成分,并在干燥蛋白质前与蛋白粉副产品混合以增加饲料价值。可以将亚硫酸钠、二氧化硫等添加到湿蛋白饼中,例如,以在湿蛋白饼被输送至蛋白质干燥机321前将二氧化硫水平维持在20ppm以上。二氧化硫可以防止蛋白质干燥机321中的叶黄素分解。来自离心机的上层可以返回到油储存罐中。现参见图4A,该图显示了图4的系统和方法300的变体的流程图。在该系统和方法300a中,可以在发酵步骤311之前除去纤维素材料和谷蛋白(蛋白质)粉。在发酵步骤311之前回收谷蛋白粉能够减少叶黄素在发酵步骤311的过程中、以及随后的蒸馏和蛋白质回收步骤315、320中的损失。此外,较大尺寸的果皮颗粒,如从约1mm至约4mm,会堵塞发酵步骤311过程中使用的热交换器。因此,在发酵步骤311前去除果皮能避免这些堵塞问题,并且能够比传统工艺增加约15%的发酵能力。如图4A所示,在胚芽/油分离步骤306之后,利用筛选设备例如过滤离心机将含有砂砾、纤维和蛋白质的液化淀粉溶液进行研磨步骤310,然后进行谷蛋白/纤维分离步骤326,以从中除去纤维。筛孔通常约为500微米,以收集大量的胚芽根、果皮以及细纤维,但可以在约300微米至约700微米的范围内变化。如标号328所示,洗涤并选择性地干燥分离出的纤维,以获得用于生产仲醇的纤维素。在不进行任何进一步处理的情况下,可以将产生的含有果皮和胚芽根以及具有高达约15%的蛋白质、高达约5%的油,以及高达约4%的淀粉的纤维素材料输送至仲醇系统作为原料。如标号330所示,利用离心机例如盘式离心机,或喷嘴离心机/滗析器组合,可以选择性地将来自谷蛋白/纤维分离步骤326后的液化淀粉溶液分离液中的蛋白质部分分离出来。将分离的蛋白质进行进一步的洗涤步骤332,并能够产生具有理想叶黄素百分率(即,约100mg/Lb至约200mg/Lb)的高价值蛋白粉,其可以与后续进一步讨论的从下游分离出的残留蛋白质进一步混合。否则,在发酵步骤311中,将液化淀粉溶液分离液部分将与细胚芽颗粒混合。作为另一种选择,可以将来自油/胚芽分离步骤309的细胚芽颗粒进一步加工,以在发酵步骤311中与液化淀粉溶液混合前分离并获得胚芽蛋白质。该工艺的其余部分通常与图4的相同,除了在发酵步骤311前,于工艺的前端回收了谷蛋白粉和纤维。具体地,之前便将纤维从蛋白质、细胚芽颗粒和细纤维中进行了分离,现在不存在分离步骤316(图4)。替代的是,在细胚芽和纤维分离步骤317中,从残留蛋白质(谷蛋白)中分离尺寸大于50微米的细纤维和细胚芽。本文中,使用精细筛选设备例如具有约45微米筛孔尺寸的搅拌筛选机或压力筛选机分离细胚芽和细纤维。将细胚芽和细纤维输送到细胚芽/细纤维维持罐318中,此处,例如,可以通过加入化学试剂(例如,氢氧化钠、石灰、碳酸钠、磷酸三钠等)将罐中的细胚芽/纤维的pH值调节至约8至约10.5(或约8至约9.5),以促进额外的油从胚芽中释放。此外,也可以加入细胞破壁酶(例如,蛋白酶等),和/或化学试剂(例如,亚硫酸钠等),以促进额外的油从胚芽中释放。接下来,将胚芽和纤维的混合物进行细纤维分离步骤319,此处,通过例如滗析器从细胚芽中分离细纤维。然后,如标号328所示,可以将细纤维与分离的已经洗涤并选择性干燥的纤维混合,用于生产仲醇的纤维素。在一种实例中,细纤维含有低于15%的蛋白质和4%的油。在蛋白质回收/脱水步骤320中,将来自细胚芽和纤维分离步骤317的分离液、来自细纤维分离步骤319的上层,以及来自前端选择性谷蛋白洗涤步骤332的上层混合,并使用例如滗析器、喷嘴离心机或盘式滗析器回收细纤维和蛋白质(以及使用的酵母)。可替代地,可以使用例如滗析器、喷嘴离心机或盘式滗析器将来自细纤维分离步骤319的上层进行选择性地脱水,并返回胚芽研磨步骤307以提取更多的油。将来自回收/脱水步骤320的组分送至干燥机321,并与从前端选择性分离的谷蛋白混合以获得具有约60%的谷蛋白和约40%的胚芽/酵母的谷蛋白/胚芽/酵母混合物(蛋白粉)。来自蛋白质脱水步骤320的上层进入蒸发器324,以从中分离各种油,并获得高浓度的糖浆(大于65%的DS),其可以在其它物质中作为(a)用于生产仲醇的营养素,(b)动物饲料,(c)肥料,(d)和/或用于生产沼气的厌氧发酵物。现参见图5,该图示出了从用于生产醇的谷物中分离高价值副产品的系统和方法400的另一种实施方式。该系统和方法400通常对应于干磨乙醇生产系统和工艺,分离各种副产品,例如,以生产例如供牛或猪的低蛋白(低于20%)/低油(低于8%)的DDGS和高价值油。为此,在这种具体的工艺和方法400中,首先,将玉米进行例如锤式粉碎402,用于将玉米研磨至颗粒尺寸小于约7/64英寸,并促进油从中释放。在一种实例中,颗粒尺寸从约50微米到3mm。研磨有助于破坏纤维、蛋白质、淀粉和胚芽之间的连接。在另一种实例中,例如来自干法分馏工艺的胚芽部分可以取代此处起始的未研磨的玉米。将研磨的玉米与水混合,并输送至液化步骤404,提供具有约1.05-1.15克/立方厘米的密度的液化淀粉溶液。在液化步骤404,淀粉开始转化为液化淀粉溶液。可以在液化步骤404添加酶例如α-淀粉酶,此处可以使用本领域公知的任何合适的液化装置。来自液化步骤404的液流含有约1lb/Bu的游离油和约1.5lb/Bu的胚芽颗粒(尺寸在约小于50微米至约1mm的范围内变动)、1lb/Bu的砂砾(尺寸在约50微米至约1mm的范围内变动)以及5lb/Bu的纤维(颗粒尺寸在约小于50微米至约3mm的范围内变动)。该液流进入固体/液体分离步骤406,利用合适的筛选设备(例如,预浓缩器、搅拌筛选机、压力筛选机、纤维离心机等)从固体材料中分离液体。选择可以在约50微米至约500微米的范围内变动的筛孔,从主要含有液化淀粉溶液(含有少量的油、游离蛋白质(主要是谷蛋白)和淀粉)的液体中分离出满足需要的纤维、砂砾和胚芽颗粒。在一种实例中,筛孔约为50微米。液体部分可以进入油/液化淀粉溶液分离步骤408,此处,将液体部分置于离心机例如盘式离心机中,以在将液化淀粉溶液与发酵前处理的固体部分混合前分离出油,这将在下面进行讨论。在油/液化淀粉溶液分离步骤408中,将液化淀粉溶液用作重介质液体以漂浮油(密度约为1.05-1.15克/立方厘米)。相对于在下游回收的油,特别是发酵后回收的油,在本工艺中的此阶段回收的油在颜色和游离脂肪酸含量(从约2%至约5%)方面具有更理想的质量。具体地,在发酵前回收的油的颜色较淡,游离脂肪酸含量较低。油的产量可以包括0.8lb/Bu以上。在一种实例中,油的产量为约0.8至约1.0lb/Bu。利用例如研磨式粉碎机、销棒粉碎机或高压力锅步骤,将来自固体/液体分离步骤406的分离的固体进行粉碎步骤410,以进一步破坏纤维、淀粉和蛋白质之间的连接。可以选择性地添加各种酶(以及它们的类型),如葡糖淀粉酶、真菌酶、纤维素酶、纤维二糖酶、蛋白酶等,以促进分离。然后,将来自粉碎步骤410的处理的固体部分和来自油/液化淀粉分离步骤408的液化淀粉溶液混合。将现在含有纤维、砂砾、胚芽和蛋白质的液化淀粉溶液进行发酵步骤412,然后进行蒸馏步骤414。在蒸馏塔中,将发酵溶液从酒糟(含有纤维、蛋白质和胚芽颗粒)中分离,以获得醇。在纤维/蛋白质分离步骤416中,使用筛选设备例如过滤离心机,通过颗粒尺寸的差异从胚芽颗粒和蛋白质(谷蛋白)中分离纤维,以从中去除纤维。筛孔通常约为500微米,以收集大量的胚芽根、果皮以及细纤维,但可以在约300微米至700微米的范围内变动。分离的纤维用于生产低蛋白(低于20%)/低油(低于8%)的DDG。如果纤维中较低的蛋白质和油含量是需要的或理想的,可以将纤维输送至例如维持罐(未示出),此处,可以通过加入化学试剂(例如,氢氧化钠、石灰、碳酸钠、磷酸三钠等)将分离的纤维的pH值调节至约8至约10.5(或约8至约9.5),以促进额外的油从胚芽中释放。此外,也可以加入细胞破壁酶(例如,蛋白酶等),和/或化学试剂(例如,亚硫酸钠等),以促进额外的油从胚芽中释放。在一种实例中,纤维可以在温度为约140°F至约200°F(或者,约180°F至约200°F)的罐中保持约1小时。然后,可以将纤维进行研磨步骤以从纤维中释放更多的油和蛋白质。通过这些额外的处理步骤生产的纤维能够具有低得多的油(低于2%)和低得多的蛋白质(低于10%),并且可以用于生产仲醇。使用例如滗析器、喷嘴离心机或盘式滗析器,将来自纤维/蛋白质分离步骤416的分离液进行蛋白质回收/脱水步骤418,以回收细胚芽和蛋白质(以及使用的酵母)。将这些组分输送至干燥机420以获得高价值的具有约60%的谷蛋白和约40%胚芽/酵母的谷蛋白/胚芽/酵母混合物(蛋白粉)。该系统和方法400将生产5.5lb/Bu的蛋白质,蛋白质纯度约为45%。可替代地,在蛋白质回收/脱水步骤418前,来自纤维/蛋白质分离步骤416的分离液首先可以选择性的替换为输送至胚芽/谷蛋白分离步骤422,此处,使用例如搅拌筛选机或压力筛选机从谷蛋白中分离胚芽。将胚芽返回至胚芽研磨步骤410以提取更多的油。谷蛋白被输送至蛋白质回收/脱水步骤418,然后进入蛋白质干燥机420。来自蛋白质脱水步骤418的上层进入蒸发器424,以从中分离各种油,并获得糖浆,糖浆可以如标号426所示的与DDG混合并干燥,以获得供例如牛或猪的尤其是奶牛的低蛋白(低于20%)/低油(低于8%)的DDGS。DDGS含有低于约20%的蛋白质、低于约8%的油,以及低于约4%的淀粉。另外,在发酵步骤412之前和之后,可以提供选择性的离心步骤(未示出),以对回收的油的乳剂层中含有的叶黄素进行回收,并在干燥前与蛋白质副产品混合以增加饲料价值。例如,可以将亚硫酸钠、二氧化硫等添加到湿蛋白饼中,以在湿蛋白饼被输送至蛋白质干燥机420前将二氧化硫水平维持在20ppm以上。二氧化硫可以防止蛋白质干燥机420中的叶黄素分解。来自离心机的上层可以返回至油储存罐中。另外,尽管没有示出,应该理解的是,可以按照图3和图4的方法300、400的后端所阐明的方式处理来自蒸馏的酒糟的纤维、蛋白质、细胚芽和细纤维。现参见图5A,该图显示了图5的系统和方法400的变体的流程图。在该系统和方法400a中,在发酵步骤412之前除去谷蛋白粉。在发酵步骤412之前回收谷蛋白粉能够减少叶黄素在发酵步骤412的过程中、以及随后的蒸馏和蛋白质回收步骤414、418中的损失。如图5A所示,在固体/液体分离步骤406后,液体部分可以进入油/液化淀粉溶液/谷蛋白分离步骤428,此处,将液体部分置于盘式离心机或盘式滗析器离心机,以从在发酵步骤412前输送至与处理的固体部分混合的液化淀粉溶液中分别分离出油和谷蛋白。在油/液化淀粉溶液/谷蛋白分离步骤428中,液化淀粉溶液用作重介质液体以漂浮和分离具有约0.9-0.92克/立方厘米的密度的油。谷蛋白作为饼从分离步骤428中去除,并进入谷蛋白洗涤步骤430,然后进入谷蛋白干燥步骤432以获得具有理想叶黄素百分率(即,约100mg/Lb至约200mg/Lb)的高价值谷蛋白粉。该工艺的其余部分通常与图5的相同,除了在发酵步骤412前,于工艺的前端回收了谷蛋白粉。具体地,选择性的胚芽/谷蛋白分离步骤422(图5)现在为使用例如搅拌筛选机或压力筛选机的选择性的胚芽脱水步骤423,以回收细胚芽。将胚芽返回至胚芽研磨步骤410以提取更多油。将分离液输送至蛋白质回收/脱水步骤418,然后将回收的组分输送至蛋白质干燥机420。得到的谷蛋白/胚芽/酵母混合物(蛋白粉)含有较低百分比的谷蛋白。来自蛋白质回收/脱水步骤418的上层仍使其进入蒸发器424以从中分离各种油,并获得糖浆,糖浆可以与DDG混合并干燥以的得到低蛋白(低于20%)/低油(低于8%)的DDGS。现参见图5B,该图显示了图5的系统和方法400的变体的流程图。在该系统和方法400b中,在发酵步骤412中,与来自油/液化淀粉溶液分离步骤408的液化淀粉溶液混合前,先将来自碎粉步骤410的处理的固体部分输送至维持罐434,然后,进行固体/液体分离步骤436。具体地,如图5B所示,在维持罐434中将处理的固体部分与蒸煮水(cookwater)混合,此处,细胚芽和细纤维的纤维、淀粉、蛋白质和油之间的连接可以进一步被破坏。另外,例如,可以通过加入化学试剂(例如,氢氧化钠、石灰、碳酸钠、磷酸三钠等)将细胚芽的pH值调节至约8至约10.5(或约8至约9.5),以促进油从胚芽中释放。此外,也可以加入细胞破壁酶(例如,蛋白酶等),和/或化学试剂(例如,亚硫酸钠等),以促进油从胚芽中释放。在一种实例中,胚芽可以在温度为约140°F至约200°F(或者,约180°F至约200°F)的罐中保持约1小时。在维持罐434后,将浆液输送至固体/液体分离步骤436,此处,通过使用例如搅拌筛选机或压力筛选机分离固体和液体。筛子的孔的尺寸比在固体/液体分离步骤406中使用的筛子的孔的尺寸大。在一种实例中,孔可以在约100微米到400微米的范围内变动。在另一种实例中,筛子的孔约为250微米。在锤式粉碎402后和液化步骤404前,将含有小于筛孔尺寸的细胚芽颗粒和细纤维颗粒的液体分离液返回与研磨的谷物混合,以形成浆液并用于进一步加工,例如,回收额外的油副产品。然后,将来自固体/液体分离步骤436的固体部分和来自油/液化淀粉分离步骤408的液化淀粉溶液混合,并进行发酵步骤412,然后进行蒸馏步骤414。该工艺的其余部分通常与图5的相同,包括选择性地将来自谷蛋白/分离步骤422的细胚芽返回至胚芽研磨步骤410以提取更多的油,随后进一步置于维持罐434和进行固体/液体分离步骤436。使用该系统和方法400b,来自油/液化淀粉溶液分离步骤408的油的产量为1.0lb/Bu以上。在一种实例中,油的产量为约1.2到约1.4lb/Bu。另外,需要理解的是,这些额外的步骤434和436可以同样的用于图3-5A所示的工艺中。因此,本发明提供了一种在传统工艺和其它工艺上进行了改进的从用于生产醇的谷物中分离高价值副产品(例如,油、白纤维和蛋白粉)的系统和方法,从而克服了现有系统和方法的缺陷。尽管已经通过各种实施方式的描述阐明了本发明,且尽管已经相当详细的描述了这些实施方式,但申请人并不意在将随附的权利要求约束或以任何方式限制在这些细节上。例如,尽管本文中描述的各种系统和方法均集中在玉米上,事实上,可以使用任何类型的谷物,例如,但并不限于小麦、大麦、高粱、黑麦、水稻、燕麦等。还需要理解的是,可以使用任何副产品,例如,来自现有玉米湿磨工艺的纤维蛋白或来自现有干法分馏工艺的胚芽部分和纤维部分。其它的优势和变型对于本领域技术人来说是显而易见的。因此,本发明并不限于典型的装置和方法以及实施例所示和描述的具体细节,而具有更宽的范围。因此,在不背离本申请发明构思的精神或范围的情况下,可以根据这些具体描述对本发明进行修改。