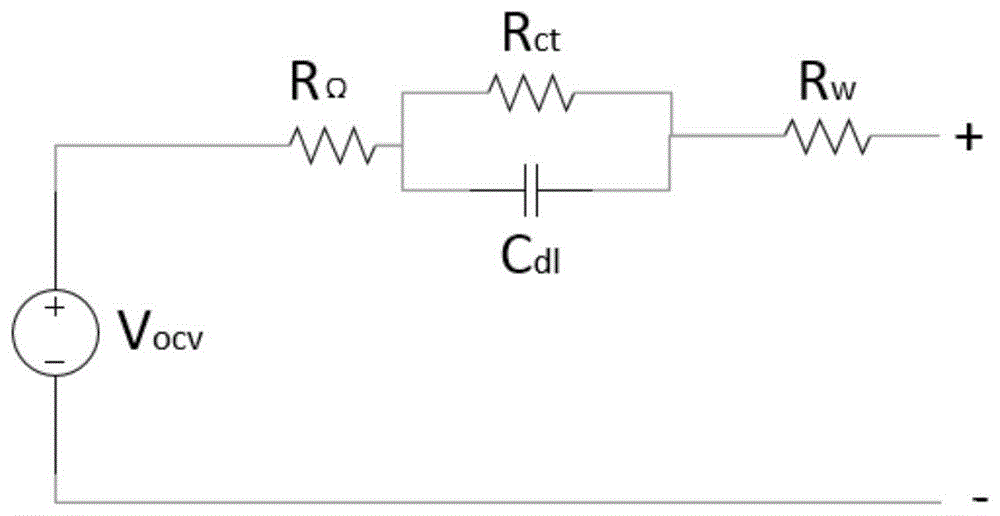
本发明属于锂电池
技术领域:
,具体涉及一种电池配组方法。
背景技术:
:在一些应用场合,需要将多个单体电池以串并联方式进行连接后组成电池组来使用。电池组中如果单体电池的一致性不稳定会影响整个电池组的性能及使用寿命,进而影响用户的使用体验。因此在电池配组之前,需要根据电池的性能参数对电池进行分档。目前锂电池分档配组时参考的性能参数主要有电压、内阻和容量,其中,电池内阻一般采用内阻测试仪进行测试,主要参考的是电池的交流内阻。图1为一阶锂电池的等效电路图,图1中的vocv表示电池开路电压,rω为欧姆电阻,rct为电荷转移电阻,cdl为双电层电容,rw为扩散电阻。当在电池的正、负极之间施加高频正弦波电流信号时,cdl相当于导通短路状态,高频正弦波电流不会造成电极表面物质的消耗,因此rct、cdl和rw都可以忽略,此时测试得到的是欧姆电阻;将正弦波电流信号的频率降低到不会造成电极表面物质大量消耗的时候,扩散电阻仍可忽略,测试得到的是电荷转移电阻和双电层电容;如果正弦波电流信号的频率继续降低,例如到0.1hz,此时电池表面物质被大量消耗,需要扩散来补充消耗的物质,测试得到的是扩散电阻。图2为锂电池的奈奎斯特图,是一种电化学阻抗谱。图2中实轴的截距代表欧姆阻抗,是由电子与离子迁移阻力产生的;半圆是由电解质与电极材料界面上的电荷转移产生的;低频部分是由锂离子在电解质中的扩散和在正负极材料中的扩散产生的。从图2可以看出,信号频率在1khz左右测得的电阻一般认为是电池的欧姆电阻,1khz~1hz左右的半圆弧代表的是电池的电荷转移电阻和双电层电容,1hz~mhz代表的是电池的扩散电阻。目前电阻测试仪的信号频率多为1000hz±100hz,测得的结果是电池的交流内阻,也就是只反映了锂电池的欧姆阻抗,没有反映出sei膜阻抗和电化学阻抗。而锂电池随着放电时间的增加,sei膜阻抗、电化学及扩散阻抗会显现出来,如果只以电池的欧姆电阻作为性能参数进行筛选配组,不能完全体现电池的阻抗性能,容易出现串压差不良的问题。技术实现要素:本发明的目的在于提供一种可以解决电池配组后出现串压差不良问题的电池配组方法。为了实现上述目的,本发明采取如下的技术解决方案:一种电池配组方法,对电池进行分档配组前,根据电池的直流内阻进行筛选,筛选步骤如下:s1、将电池与恒流负载相连,对电池进行恒流放电,测试电池的直流内阻;s2、测试一个批次电池的直流内阻,获取该批次电池的直流内阻平均值及直流内阻标准差,根据直流内阻平均值及直流内阻标准差计算该批次电池的直流内阻上限值及直流电阻下限值;s3、根据测得的直流内阻上限值及直流电阻下限值对该批次电池进行筛选,将该批次中直流内阻在直流内阻上限值和直流电阻下限值以外的电池剔除,直流内阻在直流内阻上限值和直流电阻下限值之间的电池为合格电池。更具体的,步骤s2中,直流内阻上限值式中的表示该批次电池的直流内阻平均值,m为调节系数,σ为该批次电池的直流内阻标准差。作为本发明电池配组方法的一种优选实施方式,步骤s1中,测试电池的直流内阻时,将电池通过pcb板与恒流负载相连,所述pcb板用于延长电池的放电时间。更具体的,步骤s1中,直流内阻r=(vt-v0)/(i1+i2),式中的vt为放电前的电池电压,v0为放电后的电池电压,i1为放电电流,i2为负载漏电流。更具体的,所述负载漏电流等于恒流负载设置的放电电流与放电时测得的恒流负载的放电电流之间的差值。更具体的,所述pcb板为锂电池pcb保护板。作为本发明电池配组方法的一种优选实施方式,步骤s1中,电池的放电时间为1000ms。作为本发明电池配组方法的一种优选实施方式,步骤s1中,电池的放电电流为0.5c或1.0c。进一步的,将筛选为合格的电池,根据电池的电压、交流内阻、容量进行分档配组,为每一个电池分配一个唯一的配组码,具有相同组号的电池组装成一个电池组。由以上技术方案可知,本发明在对电池进行分档配组前,先对电池的直流内阻进行测量,根据电池的直流内阻对同批次电池进行筛选,筛选合格的电池再进一步进行分档配组。电池的直流内阻除了可以反映电池的欧姆阻抗外,还可以反映出电池的sei膜阻抗和电化学阻抗,能够全面体现出电池的阻抗性能,相较于现有的基于电池交流电阻进行分选配组的方法,本发明方法避免了只以电池的欧姆电阻(交流内阻)作为性能参数进行筛选配组容易出现串压差不良的问题。附图说明为了更清楚地说明本发明实施例,下面将对实施例或现有技术描述中所需要使用的附图做简单介绍,显而易见地,下面描述中的附图仅仅是本发明的一些实施例,对于本领域普通技术人员来讲,在不付出创造性劳动的前提下,还可以根据这些附图获得其他的附图。图1为一阶电池等效电路图;图2为锂电池的奈奎斯特图;图3为本发明方法测试电池内阻时的连接示意图;图4为本发明方法测试电池内阻时一种优选实施方式的连接示意图;图5为不同放电电流及放电时间的dcir分布图;图6为本发明实施例1的dcir测试曲线图;图7为本发明实施例2的dcir测试曲线图;图8为本发明实施例3的dcir测试曲线图。图9为交流内阻和直流内阻对比图;以下结合附图对本发明的具体实施方式作进一步详细地说明。具体实施方式为了让本发明的上述和其它目的、特征及优点能更明显,下文特举本发明实施例,并配合所附图示,做详细说明如下。本发明的电池配组方法除了参考电池的电压、内阻和容量等性能参数外,还包括了按照电池(芯)的直流内阻对电池进行筛选的步骤,对电池根据直流内阻进行筛选的步骤如下:s1、如图3所示,将电池100与恒流负载200相连,对电池100进行恒流放电,放电过程中测试电池100的直流内阻;s2、对某一批次的电池的直流内阻进行测试,获取该批次电池的直流内阻平均值及直流内阻标准差,根据平均值及标准差计算该批次电池的直流内阻上限值rusl及直流电阻下限值rlsl,电池批次可以是天或周次,以实际生产情况为准;直流内阻上限值式中的表示该批次电池的直流内阻平均值,m为调节系数,σ为该批次电池的直流内阻标准差;调节系数m为正整数,例如可以是1、2、3、4或5,其取值为经验值,根据电池直流内阻的测量结果相应设置,通过调节系数可以使直流内阻的上、下限值涵盖绝大部分电池的测量值,从而可将异常电池剔除,后面实施例的说明中,m=3;s3、根据电池的直流内阻上限值及直流电阻下限值对该批次的电池进行筛选,将在直流内阻上限值和直流电阻下限值以外的电池剔除,直流内阻在直流内阻上限值和直流电阻下限值之间的电池为合格电池。将筛选出来的合格电池按照常规的方法进行电压、交流内阻、容量测试,根据电压、交流内阻和容量三个性能参数将电芯进行分组(档),根据电池的电压、交流内阻、容量进行分组为常规方法,不是本发明的创新之处,此处不再赘述。每一个电池分组后会分配到一个配组码,配组码由喷码机喷在电池表面,在对电池进行配组时,将配组码相同的电池组装成一个电池组。在对电池进行恒流放电测试直流内阻时,如果将电池直接与恒流负载相连,产线为了达成uph(单位小时产能)指标,以及避免放电电流过大造成压降大、易误判为不良品,放电时间一般比较短、放电电流比较小,如20ms,0.2c,从而测得的直流内阻不能很好地反映出真实的电池阻值状态,因此,作为本发明的一种优选的实施方式,在对电池进行恒流放电时,将电池100通过pcb板300与恒流负载200相连,对进行电池小电流放电(如图4),pcb板300用于延长电池的放电时间,使电池可以更进一步的深度放电。具体操作如下:在恒流负载200对电池100进行放电前,电阻测试仪的测试头先将电芯正、负极耳压在pcb板300的测试点上,然后启动恒流负载200进行放电。在测试头压合后测量放电前的电池电压vt,此时电池100与pcb板300导通,记录电压数据,如将电压数据上传至mes系统;恒流负载200接收到vt数据上传成功的信息后,执行放电指令放电,此时pcb板300导通时间在几十毫秒至几百毫秒之间,也就是电池100已经持续放电了一段时间,当恒流负载200放电结束后,mes系统抓取此时的放电后的电池电压v0。本发明所用的pcb板为锂电池中使用的常规的pcb保护板。电池100通过pcb板300连接恒流负载200时,直流内阻r通过以下公式计算:r=(vt-v0)/(i1+i2),式中的vt为放电前的电池电压,v0为放电后的电池电压(即电池与负载连接后,负载输出端电压),i1为放电电流,i2为负载漏电流;一般可在室温下测试电池的直流内阻,如25±5℃,放电电流以电池的标称容量为基准,电池容量为1c时,放电电流i1=n*c,c为电池容量,n为放电倍数,放电倍数n的取值为经验值,一般根据电池容量相应设置,如电池容量为3000mah时,n可为0.2,则放电电流i1为600ma。放电前的电池电压根据电池的荷电状态(soc)不同而不同,具体如下表所示:荷电状态(soc)电压标准(v)50%3.8~3.930%3.7~3.810%3.6~3.7可采用以下方法测试负载漏电流的大小:使用恒流负载对电池进行放电时,设置好恒流负载的放电电流后,用电流表测试负载的实际放电电流,设置的放电电流值与测得的实际放电电流值之间的差即为负载漏电流的大小。计算电池的直流内阻时,引入负载漏电流,可以使测量结果更为准确,有利于精确筛选不良品。在优选实施例中,通过使用pcb板,先进行小电流放电,有效控制了直接大电流放电导致的电压波动大,可以避免压降过大造成误判的问题,而且可以对电芯进行更进一步的深度放电,更能体现实际电芯内阻性能,对不良品进行筛选。而且,在不影响产线uph的前提下增加了放电时间(几十毫秒至几百毫秒),能够有效测量出电池实际的直流内阻值。对电池周次直流电阻进行动态管控,根据每个周次的实际分布状态定义不同的上下限值,可以有效识别出不良品。下面通过具体实施例对本发明的方法作进一步的说明。实施例1将容量为2720mah的电池通过pcb板与恒流负载仪相连,设置恒流负载仪的放电时间为20ms,放电电流为0.2c,进行直流内阻测试;连续测试同一批次中500pcs电池的直流内阻,mes系统自动抓取测试数据的均值、标准差进行计算,得出该批次电池的直流内阻上限值和下限值;根据该批次电池的直流内阻上限值和下限值对电池进行筛选,将超出直流内阻上限值和下限值的电池判定为ng品,并打上标记,将ng品剔除,电池的筛选步骤完成。对于筛选为合格的电池,再按照电压、交流内阻、容量三个标准进行筛选后配组,为每一个电池生成一个配组码,喷码机将配组码喷在电池表面,组号相同的电池可以pack成一组。打包入包装箱时,外箱条码将会和电池条码绑定,同一组别的电池才会入同一包装箱内,不是同一组别的电池不能入同一箱内。实施例2本实施例和实施例1不同的地方在于:将电池通过pcb板与恒流负载相连后,设置恒流负载仪的放电时间为1000ms,放电电流0.5c。实施例3本实施例与实施例1不同的地方在于:将电池通过pcb板与恒流负载相连后,设置恒流负载仪的放电时间为1000ms,放电电流1.0c。图5为实施例1至实施例3的测得的直流电阻分布图,从图5可以看出,以0.5c和1.0c的电流进行放电时,直流内阻分布更集中。图6至图8分别为实施例1至实施例3的dcir测试曲线图,从图6至图8可以看出,当以0.5c,20ms的条件测试电池的直流内阻时,cpk为1.19,均值为77.02,分布较分散且偏小,不能反映出真实的电池直流内阻。当以0.5c,1000ms的条件以及以1.0c,1000ms的条件测试电池的直流内阻时,均值分别为94.72和90.47,更能反馈真实的直流内阻值,可结合放电需求可以进行选择放电电流为0.5c或1.0c。图9为对同批次电池进行交流内阻和直流内阻测试的对比图,电池容量均为2720mah,测试直流内阻时,以0.5c20ms的条件进行测试,测试交流内阻时,内阻测试仪的放电频率为1khz。从图9可以看出来,同样电池的直流内阻较交流内阻均值大44mω,交流阻抗分布较分散,使用直流内阻测试,更能反映电芯内阻的真实状况(包括欧姆阻抗、电化学阻抗、sei膜阻抗)。对所公开的实施例的上述说明,使本领域专业技术人员能够实现或使用本发明。对这些实施例的多种修改对本领域的专业技术人员来说将是显而易见的,本文中所定义的一般原理可以在不脱离本发明的精神或范围的情况下,在其它实施例中实现。因此,本发明将不会被限制于本文所示的实施例,而是要符合与本文所公开的原理和新颖特点相一致的最宽范围。当前第1页12