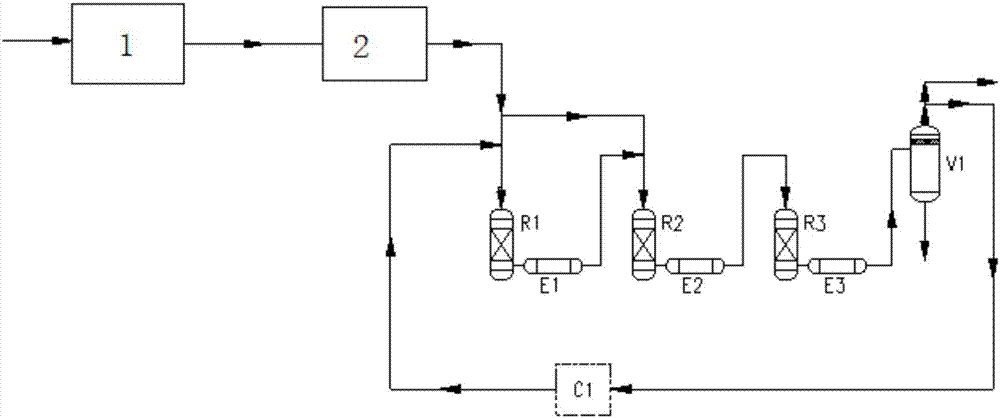
本实用新型涉及一种由焦炉煤气甲烷化生产液化天然气富裕氢气循环补碳的系统。
背景技术:
:目前,中国每年放散或点火炬的焦炉煤气约为350亿立方米,放散或点火炬不仅浪费大量能源,也造成环境污染。焦炉煤气主要成份为:CO5~8%、H255~60%、CH423~27%、N23~7%、CO21.5~3%、O20.3~0.8%、CmHn2~4%,目前焦炉煤气甲烷化生产LNG工艺已逐步趋于成熟,但焦炉煤气甲烷化反应富氢少碳,因此开发焦炉煤气生产LNG富裕氢气循环补碳方法,使焦炉煤气中的有效成份全部加以利用,提高焦炉煤气附加值。甲烷合成的主要反应式为:CO+3H2→CH4+H2OΔH0=-206.2kJ/molCO2+4H2→CH4+2H2OΔH0=-165.1kJ/mol由上式可以看出,甲烷化正常反应氢气和一氧化碳的摩尔比为3、氢气和二氧化碳的摩尔比为4,相对而言,焦炉煤气中富氢少碳。如果使焦炉煤气甲烷化后富裕的氢气最大程度得到利用,富裕的氢气需返回到甲烷化装置入口,但富氢会越积累越多。为了使富氢最大程度转化成甲烷,则需向甲烷化入口补入富碳气体,使氢气和碳发生甲烷化反应,以此得到甲烷。合成气中含有饱和水,采用等压变温脱水工艺,将合成气中的水脱到1pmm以下。脱水后的合成气进行液化分离处理,从而得到产品LNG。此外,焦炉煤气在进行甲烷合成装置前要进行加压、净化处理,以满足后续工艺要求。因此,亟需一种由焦炉煤气甲烷化生产液化天然气(LNG)富裕氢气循环补碳的系统来满足上述需求。技术实现要素:本实用新型意在提出一种由焦炉煤气甲烷化生产液化天然气(LNG)富裕氢气循环补碳的系统。在一个实施方式中,本实用新型的由焦炉煤气甲烷化生产液化天然气(LNG)富裕氢气循环补碳的系统包括:依次连接的气柜、第一压缩机、初净化系统、第二压缩机、精脱硫系统、甲烷合成反应系统、脱水装置、天然气液化系统,其中,天然气液化系统具有LNG产品出口管道、富氮尾气管道、富氢尾气管道,富氢尾气管道与除净化系统的出口管道汇合后连接第二压缩机的入口,其中气柜连接有补碳管道和焦炉煤气进料管。进一步地,第一压缩机为螺杆压缩机。进一步地,初净化系统包括脱油脱萘塔和粗脱硫塔。进一步地,第二压缩机为往复压缩机。进一步地,精脱硫系统包括依次连接的滤油槽、加氢转化器和中温氧化锌槽。进一步地,甲烷合成反应系统包括调温器、保护床、一段反应器、二段反应器、三段反应器、废热锅炉、气液分离器、循环压缩机,其中,净化煤气进料管依次连接调温器、保护床,出保护床之后分为两个支路,第一支路连接一段反应器进口,第二支路连接二段反应器进口,一段反应器的出口管道经由废热锅炉之后与第二支路汇合,再连接二段反应器进口,二段反应器出口经由废热锅炉后连接三段反应器进口,三段反应器出口经由废热锅炉后连接气液分离器,气液分离器的气相出口管道分为两路,一路送到下一工序,另一路经由循环压缩机返回一段反应器进口。进一步地,脱水装置为等压变温脱水塔。进一步地,天然气液化系统包括天然气液化、分离和制冷剂压缩循环。使用本实用新型系统的由焦炉煤气甲烷化生产液化天然气(LNG)富裕氢气循环补碳的方法包括以下工序:焦炉煤气加压,将焦炉煤气加压进行0.55MPa,送入煤气初净化工序;和0.55MPa的焦炉煤气进入吸附塔,将煤气中焦油、萘降到10mg/Nm3,无机硫降到20mg/Nm3以下;和初净化后的煤气进一步加压至2.5MPa,送入精脱硫工序;和2.5MPa的焦炉煤气采用加氢转化串氧化锌工艺,将煤气中总硫降到0.1ppm以下;和精脱硫后的焦炉煤气在三段甲烷化反应器中分别进行甲烷合成反应,得到合成气,合成气主要成份为:CH4、CO2、N2、H2O;和合成气脱水,将合成气中的饱和水脱除,然后进入液化装置;和合成气液化分离,采用混合制冷剂作冷媒,将甲烷液化得到LNG,分离尾气包括:富氢尾气和富氮尾气。富氢尾气含氢约90%、其余为氮气和少量甲烷,压力约1.2MPa。富氮尾气含氢约35%、其余为氮气和少量甲烷,压力约0.5MPa。在一个优先实施方式中,富氢尾气和富氮尾气混合后,氢含量约85%、其余为氮气和少量甲烷,进入压缩机入口,循环回甲烷化装置入口,这样,甲烷化装置入口混合气体的氢碳比会更高。在一个优选实施方式中,向系统补入富碳气体,如:二氧化碳、转炉煤气、电石炉尾气、气化炉煤气等,使系统富裕的氢气全部转化成甲烷。通过本实用新型的方法,向焦炉煤气中补入富碳气体,富裕氢气循环回甲烷化装置入口,使焦炉煤气中的氢气全部转化成甲烷,以提高LNG的产量,提高氢气的利用率。附图说明图1为根据本实用新型的由焦炉煤气甲烷化生产液化天然气(LNG)富裕氢气循环补碳的系统的示意图。图2为本实用新型的甲烷合成反应系统的示意图,其中,1:调温器;2:保护床;R1:一段反应器;R2:二段反应器;R3:三段反应器;E1:一级废热锅炉;E2:二级废热锅炉;E3:三级废热锅炉;C1:循环压缩机;V1:气液分离器。具体实施方式下面结合附图进一步说明本实用新型的由焦炉煤气甲烷化生产液化天然气(LNG)富裕氢气循环补碳的系统。以下仅为本实用新型的较佳的实例,不能以此限定本实用新型的范围。凡是依此实用新型申请专利范围所作的变化与修饰,皆应属于本实用新型专利涵盖的范围内。如图1所示,该系统包括:依次连接的气柜、第一压缩机、初净化系统、第二压缩机、精脱硫系统、甲烷合成反应系统、脱水装置、天然气液化系统,其中,天然气液化系统具有LNG产品出口管道、富氮尾气管道、富氢尾气管道,富氢尾气管道与除净化系统的出口管道汇合后连接第二压缩机的入口,其中气柜连接有补碳管道和焦炉煤气进料管。第一压缩机可以为螺杆压缩机。初净化系统可包括脱油脱萘塔和粗脱硫塔。第二压缩机可以为往复压缩机。精脱硫系统可包括依次连接的滤油槽、加氢转化器和中温氧化锌槽。如图2所示,甲烷合成反应系统可包括调温器1、保护床2、一段反应器R1、二段反应器R2、三段反应器R3、废热锅炉E1、E2、E3、气液分离器V1、循环压缩机C1,其中,净化煤气进料管依次连接调温器1、保护床2,出保护床之后分为两个支路,第一支路连接一段反应器R1进口,第二支路连接二段反应器R2进口,一段反应器R1的出口管道经由一级废热锅炉E1之后与第二支路汇合,再连接二段反应器R2进口,二段反应器R2出口经由二级废热锅炉E2后连接三段反应器R3进口,三段反应器R3出口经由三级废热锅炉E3后连接气液分离器V1,气液分离器V1的气相出口管道分为两路,一路送到下一工序,另一路经由循环压缩机C1返回一段反应器R1进口。脱水装置可为等压变温脱水塔。天然气液化系统包括天然气液化、分离和制冷剂压缩循环,可以采用本领域已知的天然气液化系统。本实用新型的由焦炉煤气甲烷化生产液化天然气(LNG)富裕氢气循环补碳的方法包括:焦炉煤气加压、净化、甲烷合成、深冷液化、富氢循环、补碳。所述焦炉煤气经过螺杆压缩机加压到0.55MPa,进入初净化工序。所述初净化采用物理吸附工艺方法,塔内分别装有不同的吸附剂,有选择性地将煤气中的杂质去除,将煤气中焦油、萘降到10mg/Nm3,无机硫降到20mg/Nm3以下。所述初净化后的焦炉煤气经往复压缩机加压至2.5MPa,进入精脱硫工序。所述2.5MPa的焦炉煤气先经过滤油槽,除去煤气中可能带有的油,然后升温到280℃进入加氢转化器,煤气中的有机硫与氢气在催化剂的作用下转化成硫化氢,而后进入中温氧化锌槽将硫化氢脱除,使精脱硫出口的气体中总硫含量降到0.1ppm以下;加氢反应热回收利用,出口气体温度约200℃。所述精脱硫后焦炉煤气进入保护床,进一步净化煤气,将煤气中的总硫含量降到0.02ppm以下。所述总硫含量低于0.02ppm的净化煤气在三段甲烷化反应器中分别进行甲烷合成反应,得到合成气。甲烷化反应:CO+3H2→CH4+H2OΔH0=-206.2kJ/molCO2+4H2→CH4+2H2OΔH0=-165.1kJ/mol合成气进入脱水装置进行深度脱水,使气体中水含量降至1ppm以下。这些知识在本领域是已知的。脱水后的合成气进入冷箱,由混合制冷剂提供冷量,使CH4液化,与H2、N2分离,得到LNG;分离尾气包括富氢尾气和富氮尾气。富氢尾气和富氮尾气混合后,氢含量约85%、其余为氮气和少量甲烷,进入压缩机入口,循环回甲烷化装置入口,这样,甲烷化装置入口混合气体的氢碳比会更高。在一个优选实施方式中,向系统补入富碳气体,如:二氧化碳、转炉煤气、电石炉尾气、气化炉煤气等,使系统富裕的氢气全部转化成甲烷。本实用新型特点是富裕氢气循环回甲烷化装置入口,同时向系统补入富碳气体,使焦炉煤气中的氢气全部转化成甲烷,从而开发一种焦炉煤气生产LNG、富裕氢气循环补碳的方法。实施例按图1所示的工艺流程示意图(以补CO2为例)处理量为1000kmol/h的焦炉煤气,压力为0.004MPa,常温,气体摩尔组成为:CO6.7%,H257.5%,CO22.25%,CH425%,N25%,O20.55%,CnHm3%;污染物含量为:H2S200mg/m3,NH3300mg/m3,焦油500mg/m3,萘200mg/m3,苯4000mg/m3,有机硫200mg/m3。焦炉煤气进入螺杆压缩机加压到0.55MPa进入初净化工序。初净化包括脱油脱萘塔、粗脱硫塔,塔内装有不同的吸附剂,脱油脱萘塔脱除气体中的焦油、萘及少量苯,粗脱硫脱除气体中硫化氢,初净化出口气体中焦油、萘降到10mg/Nm3,无机硫降到20mg/Nm3以下。初净化后的煤气经往复压缩机加压至2.5MPa进入精脱硫工序。所述2.5MPa的焦炉煤气先经过滤油槽,除去煤气中可能带有的油,然后升温到280℃进入加氢转化器,煤气中的有机硫与氢气在催化剂的作用下转化成硫化氢,而后进入中温氧化锌槽将硫化氢脱除,使精脱硫出口的气体中总硫含量降到0.1ppm以下;加氢反应热回收利用,出口气体温度约200℃。进入合成工段的净化煤气首先经过调温器调节温度到约200℃,进入保护床进一步使气体中的总硫降至0.02ppm,保护床出口气体预热到约280℃后分两股分别进入一段反应器和二段反应器,第一股气400kmol/h与三段反应器出口约650kmol/h的循环气混合后进入一段反应器,第二股气600kmol/h与一段反应器出口气体经废热锅炉回收热量后的气体混合进入二段反应器,二段反应器出口气体经废热锅炉回收热量进入三段反应器,三段反应器出口气体换热、降温后部分循环回一段反应器入口,部分送到下一工序。合成气主要成份为:CH459.19%、H233.04%、N27.41%、H2O0.36%,气量约675kmol/h。合成气进入等压变温脱水塔,脱除气体中饱和水。脱水塔内装分子筛,8小时完成一个吸附、卸压、加热、冷吹、卸压循环过程。脱水后的合成气进入天然气液化系统,此系统包括:天然气液化、分离,制冷剂压缩循环。得到纯度≥99%的LNG,产量约399kmol/h。分离尾气包括富氢尾气和富氮尾气两种,其中:富氢尾气主要成份为:CH41.02%、H288.33%、N210.65%,气量约235kmol/h;富氮尾气主要成份为:CH43.79%、H236.98%、N259.23%,气量约42kmol/h。富氢尾气、富氮尾气混合后,经加压循环回甲烷化装置入口,混合尾气主要成份为:CH41.44%、H280.51%、N218.05%,气量约277kmol/h。分离尾气混合后循环回系统,则甲烷化装置入口气体组成发生变化,主要成份为:CH419.89%、H262.49%、N27.83%、CO5.25%、CO21.76%、CnHm2.35%、O20.43%,气量约1277kmol/h。由上述甲烷化装置入口组成与焦炉煤气的组成比较,可以看出,富裕氢气循环回系统后,甲烷化装置入口的氢碳比更大。向甲烷化装置入口补入二氧化碳55~60kmol/h,调节甲烷化装置入口氢碳比约3.5,使甲烷化装置入口气体组成相对稳定,液化分离富氢尾气组成也相对稳定,富氮尾气含氮量达95%左右,整个工艺系统各节点组成和气量在较小范围内变化。主要节点组成及气量如下:组成合成入口合成出口富氢气富氮气LNGCO26.850.000.00000.000.0000CO5.850.000.00000.000.0000C2H60.870.000.00000.000.0000C2H41.750.000.00000.000.0000H256.6012.2386.49800.030.0000CH421.9376.841.66420.0299.6438N25.6710.9311.83790.960.3562O20.480.000.00000.000.0000H2O0.000.000.000000.0000气量kmol/h11465958256456本专利与富氢气无循环补碳工艺相比,1000kmol/h处理气量,LNG产量增加57kmol/h。CO2多消耗55~60kmol/h,水、电消耗相差无几,效益可观。以上已对本实用新型进行了详细描述,但本实用新型并不局限于本文所描述具体实施方式。本领域技术人员理解,在不背离本实用新型范围的情况下,可以作出其他更改和变形。本实用新型的范围由所附权利要求限定。当前第1页1 2 3