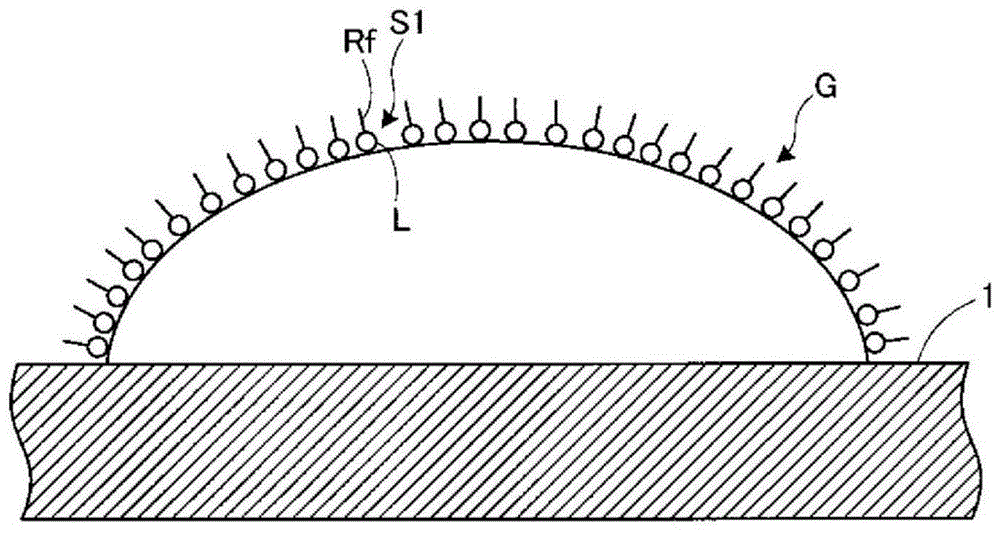
本发明涉及一种润滑剂表面处理剂、异物去除润滑组合物、异物去除润滑组合物的制造方法、异物去除润滑组合物的涂覆构件、以及异物去除润滑组合物的使用方法。
背景技术:
:可在门锁机构、车窗玻璃调节器(windowregulator)、座椅导轨(seatrail)及天窗(sunroof)等汽车部件、以及各种设备中的具备滑动部的构件上使用润滑油或润滑脂。但是,当润滑油或润滑脂中混入粉尘、沙等异物时,存在如下问题点,即,促进了滑动构件的磨损,并且根据情况还会产生异常噪音。现有技术文献专利文献专利文献1:日本特开2008-38047号公报技术实现要素:发明所要解决的课题作为现有技术,例如,已知由添加高交联树脂的润滑脂组合物实现的润滑性的提升(参照专利文献1)。但是,上述添加高交联树脂的添加润滑脂组合物没有去除粉尘、砂等异物的作用,因此无法抑制磨损、异常噪音。在此,本发明是鉴于上述问题而完成的,其目的在于提供一种可提高润滑剂的异物去除效果,并且与现有技术相比可提高润滑性的润滑剂表面处理剂、以及使用了该润滑剂表面处理剂的异物去除润滑组合物、异物去除润滑组合物的制造方法、异物去除润滑组合物的涂覆构件、以及异物去除润滑组合物的使用方法。用于解决课题的手段本发明中的润滑剂表面处理剂的特征在于,含有:具有全氟烷基的含全氟烷基化合物、或者含氟聚醚化合物中的至少1个。本发明的润滑剂表面处理剂中,优选为,含有由下述通式(1)表示的含全氟烷基化合物。rf-x-y(1)式中,rf为碳原子数c2~c6的全氟烷基,x为氧化乙烯基(c2h4o)、羰基(coo)、以及磺酰基(so3)中的至少1种以作为结合基,y为亲水基或亲油基。此外,本发明的润滑剂表面处理剂中可含有由下述通式(2)表示的甲基丙烯酸、或者由下述通式(3)表示的丙烯酸,以及由其共聚物的基本骨架构成的含全氟烷基低聚物化合物,。[化学式1][化学式2]本发明的润滑剂表面处理剂中可含有由下述通式(4)表示的含全氟烷基化合物。[化学式3]本发明的润滑剂表面处理剂中可含有由下述通式(5)或(6)表示的所述含氟聚醚化合物。[化学式4]x-cf2o-(cf2cf2o)m-(cf2o)n-cf2-x…(5)[化学式5]x-cf2o-(cf2cf(cf3)o)m-(cf2o)n-cf2-x…(6)在此,m+n=3~500、m∶n=10~90∶90~10、x中的一个或两个为官能基团,一个末端连接官能基团x的情况下,相反侧的x为氟(f),官能基团为羧酸酯基、烷基酰胺基、羧酸酯基三乙醇胺基、二硝基苯、醇、甲酯、乙氧基化醇、烷基酰胺基、聚酰胺、烷氧基硅烷、磷酸酯、聚氨酯甲基丙烯酸酯、聚氨酯烷基酯基中的至少1种。本发明的异物去除润滑组合物,其特征在于,润滑剂的表面通过上述所记载的润滑剂表面处理剂而得到表面处理。此外,本发明的异物去除润滑组合物的特征在于,具有润滑剂和覆盖所述润滑剂的表面的覆盖层,所述覆盖层上含有:具有全氟烷基的含全氟烷基化合物、或者含氟聚醚化合物中的至少一个。本发明的异物去除润滑组合物中,优选为,所述润滑剂含有润滑油或者润滑脂的润滑成分。此外,向含有所述具有全氟烷基的含全氟烷基化合物或者所述含氟聚醚化合物中的至少一个、以及润滑脂的润滑成分的所述异物去除润滑组合物中,加入具备jisz8901所规定的至少1种或2种异物后而测定出的摩擦系数优选为,小于在不含有所述具有全氟烷基的含全氟烷基化合物以及所述含氟聚醚化合物的所述异物去除润滑组合物中加入所述异物后而测定出的摩擦系数。此外,将向所述异物去除润滑组合物中加入具备jisz8901所规定的至少1种或2种异物后而测定出的初始时的摩擦系数设为μ1,将所述异物去除润滑组合物中未添加所述异物而测定出的初始时的摩擦系数设为μ0时,由{(μ1-μ0)/μ0}×100表示的所述摩擦系数的变化率(%)优选为小于45%,所述异物去除润滑组合物含有所述具有全氟烷基的含全氟烷基化合物或者所述含氟聚醚化合物中的至少一个、以及所述润滑脂的润滑成分。此外,本发明的异物去除润滑组合物中,优选为,在所述润滑剂设为100重量份时,所述含全氟烷基化合物的含量,或者,所述含氟聚醚化合物的含量,或者,含全氟烷基化合物以及所述含氟聚醚化合物的合计含量为0.01重量份以上10重量份以下的范围。此外,本发明的异物去除润滑组合物的特征在于,上述所记载的异物去除润滑组合物被置于含有尘埃的环境下。此时,所述尘埃的体积比率优选为所述异物去除润滑组合物的50%以下。此外,所述尘埃中优选含有作为主要成分的sio2。此外,本发明的异物去除润滑组合物的制造方法的特征在于,在润滑剂的表面上,涂覆上述所记载的润滑剂表面处理剂,或者以喷雾的方式喷出上述所记载润滑剂表面处理剂。此外,本发明的异物去除润滑组合物的涂覆构件的特征在于,涂覆了上述所记载的异物去除润滑组合物的构件被置于含有尘埃的环境下。此外,本发明的上述所记载的异物去除润滑组合物的涂覆构件的特征在于,在含有尘埃的环境下使用。发明效果因本发明的润滑剂表面处理剂含有具有全氟烷基的含全氟烷基化合物,或者含氟聚醚化合物的至少任意一个,能够提高润滑剂的异物去除效果,与以往相比能够提高润滑性。附图说明图1为表示涂覆在润滑脂表面上的含全氟烷基化合物的状态的示意图。图2为表示混入了异物时的含全氟烷基化合物的举动的示意图。图3为表示在润滑脂表面所涂覆的含氟聚醚化合物的状态的示意图。图4为表示混入了异物时的含氟聚醚化合物的举动的示意图。图5为表示涂覆在润滑脂表面上的含全氟烷基化合物的油膜的示意图。图6为表示用于说明往返滑动试验方法的示意图。图7为表示实施例1的相对于滑动速度在含有异物状态下的往返滑动次数与摩擦系数的关系的曲线图。图8为表示比较例2的相对于滑动速度在含有异物状态下的往返滑动次数与摩擦系数的关系的曲线图。具体实施方式以下,对本发明的一实施方式(以下,简称为“实施方式”)进行详细说明。另外,本发明并不限于以下实施方式,可以在其要点范围内进行各种变形来实施。本实施方式中的润滑剂表面处理剂的特征在于,含有:具有全氟烷基的含全氟烷基化合物或者含氟聚醚化合物中的至少一个。本实施方式中的“润滑剂表面处理剂”被用于处理润滑剂的表面,并且对于所应用的润滑剂的种类或表面处理方法等无特殊限制。即,本实施方式中的润滑剂表面处理剂可单独流通贩卖,购买该润滑剂表面处理剂的使用者不用问应用于什么样种类或组成的润滑剂,也不用问采用什么样的方法或条件下进行表面处理。此外,作为本实施方式的润滑剂表面处理剂的形态,可提示出溶剂型、油型等,但只要可以进行润滑剂的表面处理,则不限其形态。关于使用本实施方式中的润滑剂表面处理剂对润滑剂的表面进行处理后的组合物,通过对其表面部分进行组成分析,可确认出含有:具有全氟烷基的含全氟烷基化合物或者含氟聚醚化合物中的至少一个,或者,通过获得下述所记载的摩擦系数,可推测出应用了本实施方式中的润滑剂表面处理剂。以下,对于本实施方式的润滑剂表面处理剂中所包含的具有全氟烷基的含全氟烷基化合物及含氟聚醚化合物进行说明。(含全氟烷基化合物)本实施方式中,例如,可提示出以下含全氟烷基化合物。即,本实施方式中,可含有由下述通式(1)表示的含全氟烷基化合物。rf-x-y(1)式中,rf为碳原子数c2~c6的全氟烷基,x为氧化乙烯基(c2h4o),羰基(coo)及磺酰基(so3)中的至少1种基团以作为结合基,y为亲水基或亲油基。作为亲油基,例如,可列举出直链烷基c8~c18、支链烷基c8~c18、烷基苯c6~c16、烷基萘、全氟烷基c4~c9、聚氧化丙烯h-[och(ch3)ch2]n-oh、聚硅氧烷h-[osi(ch3)2]n-oh等。此外,亲水基有离子型、非离子型、两性离子型,作为离子型,例如,可列举出羧基-co2-、硫酸酯基-oso3-、磺酸基-so3-、吡啶鎓基-n+r、季铵基r4n+等。此外,作为非离子型,例如,可列举出脂肪酸基-co2h、伯醇基-ch2oh、仲醇基-crhoh、叔醇基-cr2oh、醚基-coc-、聚氧化乙烯基-[och2ch2]n-oh等。此外,作为两性离子型,例如,可列举出氧化胺基-nhco、氨基酸残基-n+(r′)2rco2等。作为亲水基或亲油基,可单独使用或者组合2种以上来使用,其使用量无特殊限定,可根据涂覆适合性来选定其量。或者,可含有由下述通式(2)表示的甲基丙烯酸、或者由下述通式(3)表示的丙烯酸,以及由其共聚物的基本骨架构成的含全氟烷基低聚物化合物。[化学式6][化学式7]或者,可含有由下述通式(4)表示的含全氟烷基化合物。[化学式8]上述列举的含全氟烷基化合物,可单独使用或者组合2种以上来使用。此时,不限定混合比率、使用量,可根据涂覆适应性来进行适当调整。另外,作为含全氟烷基化合物,一般在制造阶段可使用作为原料或中间体的全氟辛酸及全氟辛烷磺酸。此外,上述的全氟辛酸及全氟辛烷磺酸也在所述含全氟烷基化合物热分解时产生。由于上述的全氟辛烷磺酸及全氟辛酸极其稳定地存在于环境中,因而从环保的观点来看,相关企业会进行禁止制造、使用的自主限制。因此,优选为,在其制造阶段中,原料及中间体、以及其分解物中不含有作为限制对象的全氟辛酸及全氟辛烷磺酸的含全氟烷基化合物。具体优选为,全氟烷基的碳原子数为6以下。(含氟聚醚化合物)本实施方式中,例如,可提出以下含氟聚醚化合物。即,本实施方式中,可含有由下述通式(5)或(6)表示的含氟聚醚化合物。[化学式9]x-cf2o-(cf2cf2o)m-(cf2o)n-cf2-x…(5)[化学式10]x-cf2o-(cf2cf(cf3)o)m-(cf2o)n-cf2-x…(6)在此,m+n=3~500、m∶n=10~90∶90~10、x中的一个或两个为官能基团,一个末端连接官能基团x的情况下,相反侧的x为氟(f),官能基团为羧酸酯基、烷基酰胺基、羧酸酯基三乙醇胺基、二硝基苯、醇、甲酯、乙氧基化醇、烷基酰胺基、聚酰胺、烷氧基硅烷、磷酸酯、聚氨酯甲基丙烯酸酯、聚氨酯烷基酯基中的至少1种。另外,x两方均为官能基团的情况下,官能基团x既可相同也可不同,但通常相同。上述列举的含氟聚醚化合物,可单独使用或者组合2种以上来使用。此时,不限定混合比率、使用量,可根据涂覆适应性来进行适当调整。此外,含氟聚醚化合物的粘度(20℃)为,50cst~30000cst左右。对本实施方式的表面处理剂的应用例进行说明。但并不局限于以下的应用例。(1)在润滑脂或者润滑油的表面上,涂覆表面处理剂的原液或者以喷雾的方式喷出表面处理剂的原液的形态。(2)在润滑脂或者润滑油的表面上,涂覆溶剂型的表面处理剂或者以喷雾的方式喷出溶剂型的表面处理剂的形态。(3)在润滑脂或者润滑油的表面上,涂覆油型的表面处理剂或者以喷雾的方式喷出油型的表面处理剂的形态。作为润滑脂或润滑油,例如,适用于门锁机构、车窗玻璃调节器、座椅导轨、天窗等的汽车部件、以及各种设备中的具备滑动部构件,优选应用以往所使用的组合物。关于上述(1),在润滑剂的表面上形成具有全氟烷基的含全氟烷基化合物、含氟聚醚化合物的表面膜(参照图1、图3)。关于上述(2),以蒸镀的方式去除作为稀释材料的溶剂,从而在润滑剂的表面上残留了具有全氟烷基的含全氟烷基化合物、含氟聚醚化合物,从而形成表面膜(参照图1、图3)。此外,关于上述(3),在润滑剂的表面上形成含有具有全氟烷基的含全氟烷基化合物、含氟聚醚化合物的油膜(参照图5的油膜o)。作为利用本实施方式中的润滑剂表面处理剂进行了表面处理后的润滑组合物(以下称为异物去除润滑组合物),根据以下所说明的机制发现:与以往相比,可提高异物去除效果,并且能有效地提高润滑性。以下,对润滑脂的表面上涂覆了溶剂型的润滑剂表面处理剂的状态下的异物去除的机制进行说明,所述溶剂型的润滑剂表面处理剂含有具有全氟烷基的含全氟烷基化合物。图1为表示涂覆在润滑脂表面上的含全氟烷基化合物的状态的示意图。如图1所示,当润滑剂表面处理剂被涂覆在润滑脂g的表面时,溶剂蒸发后消失,进而在润滑脂g的表面上残留了含全氟烷基化合物s1,从而形成表面膜。如图1所示,作为含全氟烷基化合物s1,例如,具有全氟烷基rf和亲油基l。亲油基l比全氟烷基rf对油的亲和性更高。亲油基l带正电δ+,全氟烷基rf带负电δ-。这是由于全氟烷基rf含有氟元素,电负性极化至δ-所致。由于全氟烷基rf对润滑脂g的亲和性比亲油基l小,因此如图1所示,全氟烷基rf容易从润滑脂表面朝向外方排列。此时,含全氟烷基化合物的至少一部分也可埋没到润滑脂g内。另外,图3所示含氟聚醚化合物也是同样。图2表示混入了异物时的含全氟烷基化合物的举动的示意图。图2图示出异物c混入到润滑脂g内的样态。作为异物c,例如,以sio2为主要成分,异物c的表面极化为δ-。因此,如图2所示,在异物c上,以电中和的方式吸附有亲油基(δ+)l。由此,全氟烷基rf成为在异物c的外侧(吸附侧的相反侧)排列的状态。在外侧排列有全氟烷基rf的异物c与润滑脂g的亲和性小。其结果为,异物c成为悬浮在润滑脂g中的状态,并且产生朝润滑脂g表面方向转移的作用(图2箭头所示)。由此,异物c被置于可轻易地被去除到润滑脂g的外部的状态。而且,从润滑脂g被去除的异物c成为外周面被与润滑脂g的亲和性低的全氟烷基rf所覆盖的状态,因此不易混入到润滑脂g中(参照图2的“×”符号)。接下来,对润滑脂的表面上涂覆了含有含氟聚醚化合物的溶剂型的润滑剂表面处理剂的状态下的异物去除的机制进行说明。图3为表示涂覆在润滑脂表面上的含氟聚醚化合物的状态的示意图。如图3所示,当润滑剂表面处理剂被涂覆在润滑脂g的表面时,溶剂蒸发后消失,进而在润滑脂g的表面上残留了含氟聚醚化合物s2,从而形成表面膜。如图3所示,由于残留在润滑脂g的表面上的含氟聚醚化合物s2因氟原子f的电负性最高,因而带负电δ-,官能基团r带正电δ+。由于氟原子f对润滑脂g的亲和性比官能基r小,因此如图3所示,氟原子f容易从润滑脂表面朝向外方排列。图4表示混入了异物时的含氟聚醚化合物的举动的示意图。图4图示出异物c混入到润滑脂g内的样态。作为异物c,例如,以sio2为主要成分,异物c的表面极化为δ-。因此,如图4所示,在异物c上,以电中和的方式吸附有官能基团(δ+)r。由此,氟原子f成为在异物c的外侧(吸附侧的相反侧)排列的状态。在外侧排列有氟原子f的异物c与润滑脂g的亲和性小。其结果为,异物c成为悬浮在润滑脂g中的状态,并且产生朝润滑脂g表面方向转移的作用(图4的箭头所示)。由此,异物c被置于可轻易地被去除到润滑脂g的外部的状态。而且,从润滑脂g被去除的异物c成为外周面被与润滑脂g的亲和性低的全氟烷基rf所覆盖的状态,因此不易混入到润滑脂g中(参照图4的“×”符号)。上述异物去除作用例如在构件彼此处于大幅度地移动的、像轨道与滑块那样的滑动关系的情况下,特别有效。即,即使是半固态的润滑脂,也可通过使用本实施方式的润滑剂表面处理剂,容易地使通过滑动而流动化、且被全氟烷基覆盖的异物(参照图2)、被氟原子覆盖的异物(参照图4),迅速地朝润滑脂的表面移动,并向外部排出。此外,由于含全氟烷基化合物、含氟聚醚化合物本身也会在与滑动面接触的表面形成被膜,因此可以更加有效地赋予异物去除润滑组合物润滑性。另外,在上文中利用如下方式对异物去除的机制进行了说明,即,涂覆在润滑脂g的表面上的润滑剂表面处理剂的溶剂蒸发,从而在表面上形成含全氟烷基化合物及含氟聚醚化合物的表面膜的方式,而图5的油膜o也是根据同样的机制来促进异物去除。在本实施方式中,将异物去除润滑组合物设定为100重量份时,含全氟烷基化合物、含氟聚醚化合物优选含有0.01重量份以上10重量份以下的范围。在同时含有含全氟烷基化合物、含氟聚醚化合物这两方的情况下,含全氟烷基化合物与含氟聚醚化合物的合计含量可在0.01重量份以上10重量份以下的范围内进行调整。当含全氟烷基化合物、含氟聚醚化合物的含量小于0.01重量份时,异物去除效果降低,润滑性提高的效果不足。此外,当含全氟烷基化合物、含氟聚醚化合物的含量超过10重量份时,异物去除润滑组合物中所占的含全氟烷基化合物、含氟聚醚化合物的含量过多,从而导致润滑组合物原本所具有的润滑性能下降。此外,即使含有更多的含全氟烷基化合物、含氟聚醚化合物,也无法获得与含有量对应的目的的效果进一步地提高,且价格也会变得高昂,因而并不实用。此外,含全氟烷基化合物、含氟聚醚化合物优选含有0.05重量份以上10重量份以下的范围。虽然在图1~图5中润滑剂以润滑脂g为例进行了说明,但即使润滑剂是润滑油,也会产生同样的机制,可获得高的异物去除效果。在通过本实施方式的润滑剂表面处理剂而得到表面处理的润滑剂为润滑油的情况下,含有作为润滑成分的润滑油。此外,在通过本实施方式的润滑剂表面处理剂而得到表面处理的润滑剂为润滑脂的情况下,含有作为润滑成分的基础油及增稠剂。作为润滑成分,优选为选自矿物油、合成烃油、二酯油、多元醇酯油、醚油、二醇油、硅油及氟油中的至少1种。此润滑成分可单独使用或者组合2种以上来使用,其使用量无特殊限定,可根据涂覆适应性来选定其量。润滑成分可在较宽温度范围内使用,在这一点上,从与橡胶、树脂的适合性、与添加剂的相溶性方面考虑,尤其优选为聚α烯烃及乙烯α烯烃低聚物。本实施方式的润滑脂中所包含的增稠剂优选为,选自锂皂、钙皂、钠皂、铝皂、锂复合皂、钙复合皂、铝复合皂、脲化合物、有机化膨润土、聚四氟乙烯、硅胶、甲酰苯甲酸钠中的至少1种。从剪切稳定性方面考虑,增稠剂优选为硬脂酸锂和/或12-羟基硬脂酸锂。锂皂为,脂肪酸或其衍生物与氢氧化锂的皂化反应物。所使用的脂肪酸为,选自碳原子数2~22的饱和或不饱和的脂肪酸以及它们的衍生物中的至少1种。此外,使所述的脂肪酸或其衍生物与氢氧化锂反应的“皂”在市面上有售,也可使用。此外,根据需要,可向润滑剂中添加抗氧化剂、防锈剂、金属防腐剂、油性、耐磨损剂、极压剂、固体润滑剂等。这些添加物的含量可控制在0.01重量份~30重量份左右的范围内。作为抗氧化剂,可选自受阻酚、烷基化二苯胺、苯-α-萘胺等。作为防锈剂,可选自硬脂酸等羧酸、二羧酸、金属皂、羧酸胺盐、重质磺酸的金属盐、或多元醇的羧酸部分酯等。作为金属防腐剂,可选自苯并三唑或苯并咪唑等。作为油性剂,可选自月桂胺等胺类、肉豆蔻酯醇等高级醇类、棕榈酸等高级脂肪酸类、硬脂酸甲酯等脂肪酸酯类、或油酰胺等的酰胺类。作为耐磨损剂,可选自锌系、硫系、磷系、胺系、或酯系等。作为极压剂,可选自二烷基二硫磷酸锌、二烷基二硫磷酸钼、硫化烯烃、硫化油脂、三氯硬脂酸甲酯、氯化萘、碘化苄基、氟烷基聚硅氧烷、或环烷酸铅等。此外,作为固体润滑剂,可选自石墨、氟化石墨、聚四氟乙烯、氰尿酸三聚氰胺、二硫化钼、硫化锑等。(异物去除效果)本实施方式中,异物无特别限定,例如异物以sio2为主要成分(二氧化硅)。sio2构成由sio4四面体连结而成的结晶结构,所述sio4在中心有si4+、且在其周围包围有4个o2。si的电负性为1.8,o的电负性为3.5,两者电负性之差为1.7。因此,sio2极化为阴性(δ-)。此外,如后述的实验中详细描述那样,向通过本实施方式的润滑剂表面处理剂而得到表面处理的异物去除润滑组合物(润滑脂)中,加入具备jisz8901所规定的至少1种或者2种异物,并对摩擦系数进行测定。其结果可知,本实施方式的润滑脂不含含氟聚醚化合物,与加入了异物的现有润滑组合物相比,摩擦系数小。jisz8901所规定的1种、2种、7种、及8种均含有sio2作为主要成分的。此外,如后述的实验中详细描述那样,向通过本实施方式的润滑剂表面处理剂而得到表面处理的异物去除润滑组合物(润滑脂)中,加入具备jisz8901所规定的异物,并对初始摩擦系数μ1进行测定。此外,也对未加入异物的状态下的初始时的摩擦系数μ0进行测定。而且,在求出由{(μ1-μ0)/μ0}×100表示的摩擦系数的变化率(%)时,可知本实施方式的润滑脂在初始时的摩擦系数的变化率低于45%。在此,“初始时”是指,往返滑动次数在5次以上50次以下的滑动条件。通过使用本实施方式的异物去除润滑组合物,从而在润滑面上涂覆异物去除润滑组合物并让滑动构件滑动时,根据异物去除效果,可让摩擦系数稳定地保持为较低的状态。因此,通过使用本实施方式的异物去除润滑组合物,从而与以往相比,可稳定地获得高润滑性。另外,如后述的实验所示,可使用以预定的比例来混合jisz8901所规定的1种、2种、7种及8种之中的至少2种以上的异物,来进行上述摩擦系数的实验。此时的混合比例并无特殊限定。例如,如后述的实验所示,可以以1∶1∶1∶1的比例来混合jisz8901所规定的1种、2种、7种及8种。本实施方式的异物去除润滑组合物即使被放置于含有尘埃的环境下,根据异物去除效果,也可保持稳定的高润滑性。“含有尘埃的环境下”是指,例如,以异物去除润滑组合物的50%以下的体积比率含有尘埃的环境下。即,若是本实施方式的异物去除润滑组合物,即使尘埃在异物去除润滑组合物的体积比率中达到50%左右,也可适当地发挥异物去除效果。本实施方式中,在异物去除润滑组合物的体积比率中含有0.01%左右以上尘埃的环境下,与以往的润滑组合物相比,摩擦系数明显变低等,从而呈现出显著的异物去除效果。此外,对于门锁机构、车窗玻璃调节器、座椅导轨、及天窗等汽车部件、以及各种设备中的具备滑动部的构件,本实施方式的异物去除润滑组合物可作为润滑油或润滑脂来使用。即使具备这样的汽车部件及滑动部的构件放置于上述含有尘埃的环境下,也可通过使用本实施方式的异物去除润滑组合物,来适当地发挥异物去除效果,从而与以往相比,可稳定地获得高润滑性。本实施方式中,可通过以下方法制备异物去除润滑组合物。即,在润滑脂、润滑油等润滑剂的表面上涂覆本实施方式的润滑剂表面处理剂,或者以喷雾的方式喷出本实施方式的润滑剂表面处理剂。由此,可在润滑剂的表面上形成含有具有全氟烷基的含全氟烷基化合物或者含氟聚醚化合物中的至少一个,基于利用图1~图5来进行说明的机制,可获得高异物去除效果。可通过现有方法来进行涂覆或喷雾。例如,涂覆包括涂刷、滴落,浸渍等。此外,由喷雾器进行喷雾较为简单,因而优选。这样一来,根据本实施方式,若对已知的润滑脂、润滑油等润滑剂,涂覆本实施方式的润滑剂表面处理剂,可简单地获得具有高异物去除效果的异物去除润滑组合物。实施例以下,利用为了明确本发明的效果而实施的实施例来详细说明本发明。另外,本发明并不限于以下实施例。根据以下的表1及表2所示比例,来制备实施例1~实施例8、比较例1~比较例2。使用的原料如下。(实施例1)基础油聚α烯烃(运动粘度(40℃):30mm2/s):77.8重量份增稠剂锂皂(12-羟基硬脂酸锂):7.0重量份抗氧化剂受阻酚系抗氧化剂:0.2重量份固体润滑剂a聚四氟乙烯(平均粒径6.5μm):5.0重量份固体润滑剂b氰尿酸三聚氰胺(平均粒径3.1μm):5.0重量份固体润滑剂c超高分子量聚乙烯(平均粒径30μm):5.0重量份粉尘(以1∶1∶1∶1的方式混合jisz8901所规定的1种、2种、7种、8种):2.0重量份另外,粉尘在润滑脂制备后混合。在构件表面涂覆粉尘混合润滑脂后,将以下氟系表面活性剂a滴在润滑脂表面,并进行评价。氟系表面活性剂a平均分子量4480:0.5重量份(实施例2)基础油聚α烯烃(运动粘度(40℃):30mm2/s):77.8重量份增稠剂锂皂(12-羟基硬脂酸锂):7.0重量份抗氧化剂受阻酚系抗氧化剂:0.2重量份固体润滑剂a聚四氟乙烯(平均粒径6.5μm):5.0重量份固体润滑剂b氰尿酸三聚氰胺(平均粒径3.1μm):5.0重量份固体润滑剂c超高分子量聚乙烯(平均粒径30μm):5.0重量份粉尘(以1∶1∶1∶1的方式混合jisz8901所规定的1种、2种、7种、8种):15.0重量份另外,粉尘在润滑脂制备后混合。在构件表面涂覆粉尘混合润滑脂后,将以下氟系表面活性剂a滴在润滑脂表面,并进行评价。氟系表面活性剂a平均分子量4480:1.0重量份(实施例3)基础油聚α烯烃(运动粘度(40℃):30mm2/s):77.8重量份增稠剂锂皂(12-羟基硬脂酸锂):7.0重量份抗氧化剂受阻酚系抗氧化剂:0.2重量份固体润滑剂a聚四氟乙烯(平均粒径6.5μm):5.0重量份固体润滑剂b氰尿酸三聚氰胺(平均粒径3.1μm):5.0重量份固体润滑剂c超高分子量聚乙烯(平均粒径30μm):5.0重量份粉尘(以1∶1∶1∶1的方式混合jisz8901所规定的1种、2种、7种、8种):2.0重量份另外,粉尘在润滑脂制备后混合。在构件表面涂覆粉尘混合润滑脂后,将以下氟系表面活性剂a滴在润滑脂表面,并进行评价。氟系表面活性剂a平均分子量4480:0.01重量份(实施例4)基础油聚α烯烃(运动粘度(40℃):30mm2/s):77.8重量份增稠剂锂皂(12-羟基硬脂酸锂):7.0重量份抗氧化剂受阻酚系抗氧化剂:0.2重量份固体润滑剂a聚四氟乙烯(平均粒径6.5μm):5.0重量份固体润滑剂b氰尿酸三聚氰胺(平均粒径3.1μm):5.0重量份固体润滑剂c超高分子量聚乙烯(平均粒径30μm):5.0重量份粉尘(以1∶1的方式混合jisz8901所规定的2种、8种):2.0重量份另外,粉尘在润滑脂制备后混合。在构件表面涂覆粉尘混合润滑脂后,将以下氟系表面活性剂c滴在润滑脂表面,并进行评价。氟系表面活性剂c部分氟化醇取代二醇:10.0重量份(实施例5)基础油聚α烯烃(运动粘度(40℃):30mm2/s):77.8重量份增稠剂锂皂(12-羟基硬脂酸锂):7.0重量份抗氧化剂受阻酚系抗氧化剂:0.2重量份固体润滑剂a聚四氟乙烯(平均粒径6.5μm):5.0重量份固体润滑剂b氰尿酸三聚氰胺(平均粒径3.1μm):5.0重量份固体润滑剂c超高分子量聚乙烯(平均粒径30μm):5.0重量份粉尘(以1∶1∶1∶1的方式混合jisz8901所规定的1种、2种、7种、8种):2.0重量份另外,粉尘在润滑脂制备后混合。在构件表面涂覆粉尘混合润滑脂后,将以下含氟聚醚化合物a滴在润滑脂表面,并进行评价。含氟聚醚化合物a(商品名:fomblinda306vac):1.0重量份(实施例6)基础油聚α烯烃(运动粘度(40℃):30mm2/s):79.8重量份增稠剂锂皂(12-羟基硬脂酸锂):10.0重量份抗氧化剂受阻酚系抗氧化剂:0.2重量份固体润滑剂d超高分子量聚乙烯(平均粒径10μm):10.0重量份粉尘(以1∶1∶1∶1的方式混合jisz8901所规定的1种、2种、7种、8种):2.0重量份另外,粉尘在润滑脂制备后混合。在构件表面涂覆粉尘混合润滑脂后,将以下氟系表面活性剂a滴在润滑脂表面,并进行评价。氟系表面活性剂a平均分子量4480:1.0重量份(实施例7)基础油聚α烯烃(运动粘度(40℃):30mm2/s):77.8重量份增稠剂锂皂(12-羟基硬脂酸锂):7.0重量份抗氧化剂受阻酚系抗氧化剂:0.2重量份固体润滑剂a聚四氟乙烯(平均粒径6.5μm):5.0重量份固体润滑剂b氰尿酸三聚氰胺(平均粒径3.1μm):5.0重量份固体润滑剂c超高分子量聚乙烯(平均粒径30μm):5.0重量份粉尘(以1∶1∶1∶1的方式混合jisz8901所规定的1种、2种、7种、8种):2.0重量份另外,粉尘在润滑脂制备后混合。在构件表面涂覆粉尘混合润滑脂后,将以下润滑油稀释液滴在润滑脂表面,并进行评价。润滑油稀释液:5.0重量份润滑油稀释液的原料如下。氟系表面活性剂a平均分子量4480:10.0重量份聚α烯烃(运动粘度(40℃):30mm2/s):90.0重量份(实施例8)基础油聚α烯烃(运动粘度(40℃):30mm2/s):77.8重量份增稠剂锂皂(12-羟基硬脂酸锂):7.0重量份抗氧化剂受阻酚系抗氧化剂:0.2重量份固体润滑剂a聚四氟乙烯(平均粒径6.5μm):5.0重量份固体润滑剂b氰尿酸三聚氰胺(平均粒径3.1μm):5.0重量份固体润滑剂c超高分子量聚乙烯(平均粒径30μm):5.0重量份粉尘(以1∶1∶1∶1的方式混合jisz8901所规定的1种、2种、7种、8种):2.0重量份另外,粉尘在润滑脂制备后混合。在构件表面涂覆粉尘混合润滑脂后,将以下润滑油稀释液滴在润滑脂表面,并进行评价。溶剂稀释液:5.0重量份溶剂稀释液的原料如下。氟系表面活性剂c部分氟化醇取代二醇:10.0重量份正己烷(沸点69℃):90.0重量份(比较例1)基础油聚α烯烃(运动粘度(40℃):30mm2/s):77.8重量份增稠剂锂皂(12-羟基硬脂酸锂):7.0重量份抗氧化剂受阻酚系抗氧化剂:0.2重量份固体润滑剂a聚四氟乙烯(平均粒径6.5μm):5.0重量份固体润滑剂b氰尿酸三聚氰胺(平均粒径3.1μm):5.0重量份固体润滑剂c超高分子量聚乙烯(平均粒径30μm):5.0重量份粉尘(以1∶1∶1∶1的方式混合jisz8901所规定的1种、2种、7种、8种):2.0重量份另外,粉尘在润滑脂制备后混合。(比较例2)基础油聚α烯烃(运动粘度(40℃):30mm2/s):79.8重量份增稠剂锂皂(12-羟基硬脂酸锂):10.0重量份抗氧化剂受阻酚系抗氧化剂:0.2重量份固体润滑剂d超高分子量聚乙烯(平均粒径10μm):10.0重量份粉尘(以1∶1∶1∶1的方式混合jisz8901所规定的1种、2种、7种、8种):2.0重量份另外,粉尘在润滑脂制备后混合。在此,氟系表面活性剂a含有本申请的原权利要求书中的权利要求4所记载的含全氟烷基化合物。此外,氟系表面活性剂c含有本申请的原权利要求书中的权利要求2所记载的含全氟烷基化合物。各试料中,在基础油的存在下,合成锂皂,并进行搅拌的同时使温度上升。接下来,在冷却到80℃以下后,处置各种添加剂,并且可通过使用三辊研磨机、分散式研磨机、胶体磨等来获得均匀的润滑脂组合物。混和稠度可在280~310之间进行调整。另外,试验方法基于jisk2220。在混和稠度调整后,将规定量的粉尘混合到润滑脂中。<润滑脂的评价方法>因润滑脂为粘稠状物质,因而无法像润滑油那样通过粉尘的沉降来进行异物去除效果的评价。因此,通过摩擦系数来评价异物去除效果。<摩擦系数的实验条件>试验片:pa66gf30销/铝板载重:1000gf润滑脂涂覆膜厚:0.2mm试验温度:室温滑动速度:10mm/sec滑动幅:20mm/单程滑动次数:10往返图6为用于说明往返滑动试验方法的示意图。图6所示的符号3表示固定销,符号4表示铝板。而且,让铝板4朝a方向往返滑动。各试料中,测定了粉尘添加前与粉尘添加后的各动摩擦系数,根据下述的计算式算出了摩擦系数的变化率。即,将10次往返滑动后的粉尘混合后动摩擦系数设为μ1,将10次往返滑动后的粉尘混合前动摩擦系数设为μ0。并且,通过{(μ1-μ0)/μ0}×100来求出摩擦系数变化率(%)。其实验结果如以下的表1、表2所示。[表1][表2]比较例1比较例2基础油77.879.8锂皂7.010.0抗氧化剂0.20.2固体润滑剂a5.0固体润滑剂b5.0固体润滑剂c5.0固体润滑剂d10.0粉尘2.02.0变化率××表1及表2所示的“变化率”栏的○表示变化率小于45%,×表示变化率为45%以上。如此可知,在实施例中,初始时的摩擦系数的变化率可控制在45%以下。在此,在使滑动次数往返10次的状态下测定摩擦系数,即,这是由于在初始状态下稍微滑动的状态为最初的几次中,滑动构件与润滑脂的磨合低,摩擦系数的偏差大。接下来,使用了实施例1及比较例2的各试料,来调查滑动速度设为10mm/s时的、往返滑动次数与摩擦系数的关系。另外,除去上述的滑动次数,与摩擦系数的实验条件相同。图7为表示实施例1中的往返滑动次数与摩擦系数的关系的曲线图。图8为表示比较例2中的往返滑动次数与摩擦系数的关系的曲线图。接下来,如图7、图8所示,可知在含有异物的状态下,实施例1与比较例2相比,摩擦系数可控制得很小。本申请基于2016年10月21日在日本提出的专利申请2016-206845。所述内容全部包含在此。当前第1页12