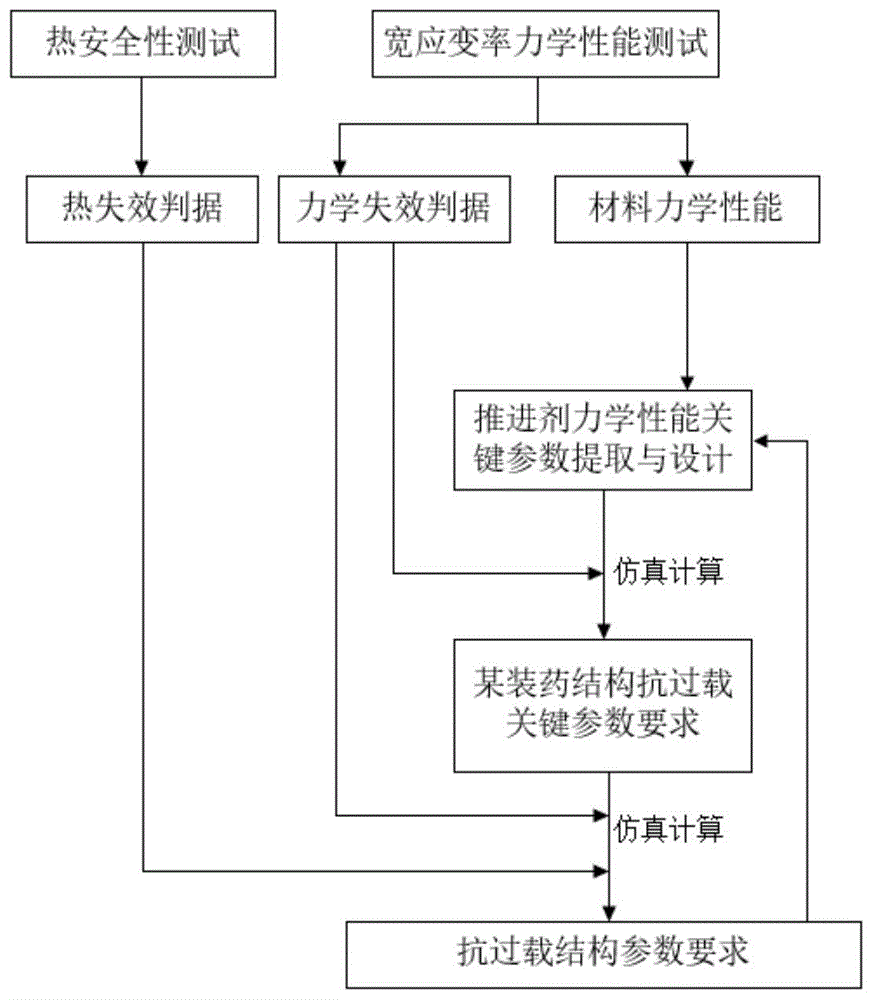
本发明涉及一种固体火箭推进剂装药耐炮射过质量评价方法,特别涉及一种固体推进剂装药耐炮射过载条件的测试评估方法,属于固体推进剂装药领域。
背景技术:
:固体推进剂装药在炮射环境下承受上万g的轴向过载,对发动机装药的结构产生较大影响,容易造成装药结构完整性破坏等恶劣现象。同时,炮射过载条件下装药发生较大变形且存在振荡,与发动机壳体之间的摩擦作用可能造成热点形成,进而导致意外点火的危险情况。推进剂装药的抗过载质量评估,可以通过试验获得推进剂的材料性能,建立本构方程和失效判据,再通过有限元计算得到装药的抗过载响应,结合失效判据分析装药的抗过载能力。炮射过载条件下,推进剂装药发生宽应变率力学响应,传统方法中通过准静态推进剂性能和失效判据进行装药抗过载评估可靠性较低,并且在热安全性方面缺乏定量的失效判据。同时,对影响推进剂力学性能的关键参数不明确,对影响装药抗过载能力的结构参数不明确,造成推进剂力学性能抗过载设计及装药结构抗过载安全性设计的盲目性,增加产品研发中的工作量和成本。技术实现要素:本发明公开的推进剂装药耐炮射过载测试评估方法要解决的技术问题是:提供一种推进剂装药耐炮射过载测试评估方法,所述评估方法建立影响推进剂力学性能的三个关键参数(应力应变率对数曲线的转折前曲线斜率、转折点及转折后曲线斜率)与推进剂装药抗过载能力的对应关系,建立基于力学失效的装药长径比与抗过载能力的对应关系、基于热失效的装药壁面间隙与抗过载能力的对应关系,根据所述对应关系能够评估推进剂装药耐炮射过载能力,根据评估结果明确推进剂力学性能参数改进方向,明确推进剂装药结构参数的改进方向,进而提高满足工程要求的炮射抗过载推进剂装药研发效率,解决抗过载推进剂装药领域相关工程问题。本发明的目的是通过下述技术方案实现的。本发明公开的推进剂装药耐炮射过载测试评估方法,实现方法如下:通过对待评估的推进剂进行宽应变率力学测试得到应力应变曲线,通过应力应变曲线获得待评估的推进剂在不同应变率下的屈服强度,通过屈服强度建立待评估的推进剂率相关的屈服失效判据。对待评估的推进剂进行摩擦感度试验,基于摩擦功定量评价摩擦感度对应的产热量,建立热失效判据。将应力应变曲线变换为应力应变率对数曲线,所述应力应变率对数曲线为带有转折点的双线性曲线,转折前曲线的斜率、转折点及转折后曲线斜率为影响推进剂力学性能的三个关键参数,通过所述三个关键参数能够反演出应力应变曲线。根据反演的应力应变曲线,建立描述待评估推进剂宽应变率力学性能的prony级数本构方程。通过该本构方程进行抗过载数值计算,结合计算结果和建立的屈服失效判据评估出待评估推挤装药的抗过载能力。调整上述关键参数,获得新的推进剂,通过反演新推进剂应力应变曲线,进一步建立描述新推进剂力学性能的本构方程,再次进行抗过载计算,获得新推进剂的抗过载能力。重复上述过程可以获得在待评估装药结构条件下,影响推进剂力学性能的三个关键参数与抗过载能力之间的关系。基于上述建立的不同推进剂的本构方程,调整装药结构的长径比,通过数值计算并结合力学失效判据,得到装药长径比与抗过载能力之间的关系;调整装药与发动机壳体之间的缝隙,通过数值计算并结合热失效判据,得到装药壁面间隙与抗过载能力之间的关系。本发明公开的推进剂装药耐炮射过载测试评估方法,包括以下步骤:步骤一,对初始方案给定的推进剂进行宽应变率力学性能测试和推进剂摩擦感度测试。所述的初始方案包括待评估的推进剂和装药结构。步骤二,通过步骤一所述的宽应变率力学测试得到待评估推进剂的应力应变曲线,通过应力应变曲线获得待评估的推进剂在不同应变率下的屈服强度,通过屈服强度建立待评估的推进剂率相关的屈服失效判据。通过步骤一所述的摩擦感度试验获得待评估推进剂的摩擦感度试验数据,通过式计算选定摩擦感度对应的摩擦功产热阈值,建立基于摩擦功的热安全性判据。步骤三,将步骤二获得的待评估推进剂应力应变曲线变换为应力应变率对数曲线,所述应力应变率对数曲线为带有转折点的双线性曲线,转折前曲线斜率、转折点及转折后曲线斜率为影响推进剂力学性能的关键参数,并且通过影响推进剂力学性能的三个关键参数能够反演出对应的待评估推进剂应力应变曲线。根据反演的待评估的推进剂的应力应变曲线建立描述待评估的推进剂宽应变率力学性能的prony级数本构方程。所述推进剂力学性能的三个关键参数包括转折前曲线斜率、转折点及转折后曲线斜率。步骤三实现方法为:根据步骤二建立的待评估推进剂率相关的屈服失效判据,得到不同应变率对应的屈服应变为εy,截取宽应变率应力应变曲线中应变值为预设截取范围内的数据点,所述预设截取范围为屈服前靠近屈服点的一个小范围。在截取的应变范围内均布取若干个应变值,将试验数据插值后提取相应若干个应变值对应的应力及应变率数据,绘制应力-应变率对数坐标曲线,在宽应变率范围内应力随应变率对数变化近似呈现双线性规律,即存在一个转折应变率,在转折应变率前、后应力随应变率对数线性变化。根据曲线变化选取转折应变率,对该曲线按式(1)进行双线性拟合,选取的转折应变率应使得拟合后的数据相对原始数据方差最小。拟合结果中每个εi对应一个参数系列,所述一个参数系列包括第一段斜率k1,i,第二段斜率k2,i,转折应变率式中:σi——第i个应变对应的应力,i=1~n,单位mpa;εi——截取范围内均布选取的应变值,i=1~n;——应变率,单位s-1;k1,i,b1,i——第i个应变对应的第一段直线系数,i=1~n;k2,i,b2,i——第i个应变对应的第二段直线系数,i=1~n;——某一应变率下第i个应变对应的转折应变率,i=1~n,单位s-1。对拟合得到的对应若干个双线性参数系列按照式(2)取均值,得到描述该待评估推进剂力学性能的三个关键参数k1,k2,所述转折前曲线的斜率k1、转折点及转折后曲线斜率k2即为影响推进剂力学性能的关键参数。通过通过影响推进剂力学性能的三个关键参数k1,k2,能够反演出对应的待评估推进剂应力应变曲线。根据反演的待评估推进剂的应力应变曲线建立描述待评估的推进剂宽应变率力学性能的prony级数本构方程。步骤四,将步骤一中所述初始方案待评估的推进剂和装药结构作为数值仿真的输入条件,基于步骤三建立的描述待评估推进剂宽应变率力学性能的prony级数本构方程进行抗过载数值仿真计算,结合上述数值计算结果和步骤二建立的屈服失效判据评估出待评估推挤装药的抗过载能力。步骤五,通过调整影响推进剂力学性能的三个关键参数转折前曲线的斜率k1、转折点及转折后曲线斜率k2能够反演出调整后待评估推进剂应力应变曲线。根据调整后三个关键参数反演的调整后推进剂应力应变曲线建立描述调整后待评估推进剂宽应变率的学性能的prony级数本构方程。步骤六,按照步骤五更新的prony级数本构方程进行抗过载数值仿真计算,结合数值仿真计算结果和建立的屈服失效判据评估出调整后待评估推挤装药的抗过载能力。步骤七,重复步骤五和步骤六,得到在步骤一所述初始方案装药结构条件下,抗过载需求对应三个关键参数转折前曲线的斜率k1、转折点及转折后曲线斜率k2的范围,根据抗过载需求对应三个关键参数的范围明确推进剂力学性能参数改进方向,进而提高炮射抗过载推进剂研发效率,进而解决抗过载推进剂领域相关工程问题。步骤七实现方法为:步骤7.1:重复步骤五、步骤六,能够得到在步骤一所述初始方案装药结构条件下,抗过载需求对应三个关键参数转折前曲线的斜率k1、转折点及转折后曲线斜率k2的范围。所述三个关键参数的范围具体为:当装药抗过载应变率响应小于转折应变率时,转折前曲线斜率k1对装药力学性能起主导作用,存在一个最小值k1,min使装药能够满足某抗过载需求;当装药抗过载应变率响应大于转折应变率时,转折后曲线斜率k2对装药力学性能起主导作用,存在一个最小值k2,min使装药能够满足某抗过载需求。步骤7.2:将入步骤7.1得到的数据填入制表格式满足表1和表2的参数对照表,得到在步骤一所述初始方案装药结构条件下,抗过载需求对应影响推进剂力学性能的关键参数的范围。表1抗过载需求与推进剂关键参数k1,min对照表(当)过载load关键参数k1,minload1k1,min,1load2k1,min,2……表2抗过载需求与推进剂关键参数k2,min对照表(当且给定k1)过载load关键参数k2,minload1k2,min,1load2k2,min,2……步骤7.3:根据抗过载需求查取步骤7.2得到的表1和表2,得出抗过载需求对应影响推进剂力学性能的关键参数的范围,根据该范围明确推进剂力学性能参数改进方向,进而提高炮射抗过载推进剂研发效率,解决抗过载推进剂领域相关工程问题。步骤八,在步骤一所述的初始方案装药结构的基础上调整装药长径比、壁面间隙等结构参数,通过步骤三、步骤七建立的本构方程进行抗过载需求条件的数值计算,结合建立的力学失效判据、热失效判据,得到抗过载需求对应的装药结构参数范围,根据抗过载需求对应结构参数的范围明确装药结构改进方向,进而提高炮射抗过载装药结构研发效率,解决抗过载推进剂装药领域相关工程问题。步骤八实现方法为:步骤8.1:装药长度l、外径d,定义长径比为l/d。步骤一所述初始方案装药结构尺寸外径d0,长度l0,长径比(l/d)0为。根据装药设计需求,将保持装药量或装药外径不变作为约束条件,给定一系列装药长径比(l/d)i,可以计算出对应的一系列装药尺寸di、li。步骤8.2:通过步骤三、步骤七建立的本构方程和步骤8.1计算得到的装药结构尺寸进行抗过载需求的数值计算,结合建立的力学失效判据,得到抗过载需求对应的装药长径比范围,所述装药长径比范围具体为:对于某抗过载需求,存在一个最大长径比(l/d)max,使装药能够满足某抗过载需求。步骤8.3:将入步骤8.2得到的数据填入制表格式满足表3的参数对照表,得到抗过载需求对应装药长径比l/d的范围,根据该范围明确装药长径比的改进方向进而提高炮射抗过载推进剂装药研发效率,解决抗过载推进剂装药领域相关工程问题。表3抗过载需求与装药长径比(l/d)max对照表过载load长径比(l/d)maxload1(l/d)max,1load2(l/d)max,2……步骤8.4:装药与壳体之间存在的缝隙为壁面间隙ds,通过步骤8.1-8.3确定待评估装药尺寸,设置一系列壁面间隙ds,i,通过步骤三、步骤七建立的本构方程进行抗过载需求数值计算,通过该数值计算得到装药抗过载响应过程中与壁面的接触应力p和相对速度v,通过式(3)得到待评估装药抗过载响应过程中沿装药侧面的产热量qc。式中:qc——产热量;p——接触应力;v——相对速度;步骤8.5:取装药侧面上产热量qc最大值qc,max,该产热量最大值与壁面间隙之间存在式(4)所示的规律。所述规律具体为:存在一个转折间隙dt,当ds<dt时,ds与qc,max呈线性关系;当ds≥dt时,ds与qc,max呈指数关系。式中:qc,max——最大产热量;ds——壁面间隙;l1,k1,l2,k2——拟合得到的系数。步骤8.6:结合热安全性判据qμ,min,令qc,max=qμ,min,通过式(4),得到能够满足热安全性的最小壁面间隙ds,min。有益效果:1、本发明公开的一种推进剂装药耐炮射过载测试评估方法,通过试验获得待评估推进剂力学性能并建立力学失效判据、获得待评估推进剂热安全性能并建立热失效判据,通过对待评估装药结构抗过载需求数值计算并结合建立的待评估推进剂的力学失效判据、热失效判据,实现对待评估推进剂装药在炮射过载条件下的质量评估。2、本发明公开的一种推进剂装药耐炮射过载测试评估方法,根据推进剂宽应变率压缩力学响应中应力-应变率对数呈双线性变化的规律,提出影响推进剂力学性能的关键参数,所述关键参数具体为转折前曲线的斜率k1、转折点及转折后曲线斜率k2,并结合建立的失效判据与数值计算得到与抗过载需求对应的关键参数范围。所述关键参数范围具体指:在抗过载需求条件下,根据装药应变率响应与转折应变率的大小关系,折前曲线斜率k1或转折后曲线斜率k2,分别存在最小值,使待评估推进剂装药能够满足对应抗过载需求。根据该范围明确推进剂力学性能参数改进方向,进而提高炮射抗过载推进剂研发效率,解决抗过载推进剂领域相关工程问题。3、本发明公开的一种推进剂装药耐炮射过载测试评估方法,综合力学失效和热失效两方面。力学失效考虑炮射过载条件下推进剂装药的宽应变率响应,建立率相关的力学失效判据;热失效方面,通过摩擦功定量描述推进剂摩擦感度试验和装药的抗过载响应过程中的产热量,建立摩擦感度与抗过载响应过程中壁面摩擦效应之间的数值联系,进而建立热失效判据。通过建立的力学失效判据和热失效判据,实现装药抗过载过程中力学结构完整性和热安全性两方面的定量评估。4、本发明公开的一种推进剂装药耐炮射过载测试评估方法,明确影响推进剂装药抗过载能力的主要结构参数为长径比和装药壁面间隙。在装药量或装药外径不变的约束条件下通过调整装药长径比获得一系列装药尺寸,通过抗过载数值计算结合建立的力学失效判据得到抗过载需求与装药长径比的对应关系;在装药长径比一定的情况下,调整装药与发动机壳体之间的壁面间隙,通过抗过载数值计算结合建立的热失效判据得到抗过载需求与壁面间隙之间的对应关系。根据上述抗过载需求与装药结构参数的对应关系,明确装药结构参数的改进方向,进而提高炮射抗过载推进剂装药的研发效率,解决抗过载推进剂装药领域相关工程问题。附图说明图1为本发明公开的一种推进剂装药耐炮射过载测试评估方法的流程图;图2为宽应变率条件压缩试验应力应变响应曲线;图3为截取的应力应变数据;图4为50个均布应变对应的应力-应变率对数曲线;图5为部分应变的双线性拟合曲线;图6为平行假设下应力-应变率对数曲线;图7为prony级数拟合结果与计算值对比,其中散点为计算值,实线为拟合值;图8为二维轴对称数值计算模型;图9为抗过载数值计算的过载作用形式;图10为过载6000g和8000g条件下装药应力集中位置的应力响应曲线;图11为装药抗过载过程中沿装药侧面的qc值变化曲线;图12为不同壁面间隙下的qc值变化曲线;图13为不同壁面间隙下的qc,max变化曲线;具体实施方式图1为本发明测试评估方法的基本流程图,下面将结合附图对本发明的优选实施方案进行详细说明。按照图1的基本流程,本发明推进剂装药耐炮射过载测试评估方法,具体实现步骤如下:步骤一,某配方cmdb推进剂及其典型管装药结构(外径d=62mm、内径d=13mm、长度l=140mm)为给定的初始方案,对改配方推进剂进行宽应变率力学性能测试和摩擦感度测试。采用同批推进剂方坯加工试验所用的试件。低应变率和中应变率试验圆柱试件尺寸为高应变率试验的圆柱试件尺寸为摩擦感度试验的圆片试件尺寸为表1和表2给出宽应变率试验设备及条件要求,试验测得推进剂试件压缩过程的时间-位移-力数据,通过数据处理获得图2给出的宽应变率条件压缩试验应力应变响应曲线。表1低应变率和中应变率试验条件试验类型低应变率压缩试验中应变率压缩试验设备材料万能试验机高速液压伺服测试系统平均加载速度0.2,2,20,200[mm/min]20,200,800,3000[mm/s]工程应变率[s-1]1.7×(10-4,10-3,10-2,10-1)1,10,40,150表2高应变率试验条件摩擦感度试验参考gjb700b-1997进行,该cmdb推进剂在20℃下摩擦感度为20%,即在给定的测试条件下,有20%的概率发生爆发现象。步骤二,通过步骤一所述的宽应变率力学测试得到待评估推进剂的应力应变曲线,通过应力应变曲线获得待评估的推进剂在不同应变率下的屈服强度,通过屈服强度建立待评估的推进剂率相关的屈服失效判据。通过步骤一所述的摩擦感度试验获得待评估推进剂的摩擦感度试验数据,通过式计算选定摩擦感度对应的摩擦功产热阈值,建立基于摩擦功的热安全性判据。从图2中可以看到,在各个应变率条件压缩响应中,cmdb推进剂存在明显的屈服行为。屈服前和屈服后的应力应变曲线的切线存在交点,切线交点处的角平分线与应力应变曲线的交点判定为屈服点。屈服应力和屈服应变存在率相关性,但屈服应变的率相关性明显低于屈服应力,可以认为屈服应变不随应变率的变化发生明显变化。从上述配方宽应变率压缩试验得到的结果,可以得到不同应变率下的屈服应变,对应的屈服应力作为该配方宽应变率条件下的力学失效判据。对应不同应变率下的应力失效判据如表3所示。根据试验得到的十二个应变率条件下的失效应力值,可以绘制应力-应变率对数曲线,并采用相邻平均法进行处理,则可以读出任意应变率下的失效应力。表3推进剂率相关的力失效判据摩擦感度试验过程中,推进剂试样放置于上下滑柱之间,固定摆锤的摆角,调整表压,释放摆锤,打击击杆,击杆使上滑柱高速移动,上下滑柱端面产生滑动摩擦,使试样受到激烈的摩擦作用。该过程中,击杆的移动距离约1.5mm~2.0mm。在该过程中,假设垂直方向装药受力处于平衡状态且滑柱对装药的正压力不随时间发生变化。基于摩擦功的产热量评价可以表示为则qμ∈[19.53mpa·mm,26.04mpa·mm],作为热安全性判据应取其最小值qμ,min=19.53mpa·mm。步骤三,将步骤二获得的待评估推进剂应力应变曲线变换为应力应变率对数曲线,所述应力应变率对数曲线为带有转折点的双线性曲线,转折前曲线斜率、转折点及转折后曲线斜率为影响推进剂力学性能的关键参数,并且通过影响推进剂力学性能的三个关键参数(转折前曲线斜率、转折点及转折后曲线斜率)能够反演出对应的待评估推进剂应力应变曲线。根据反演的待评估的推进剂的应力应变曲线建立描述待评估的推进剂宽应变率力学性能的prony级数本构方程。按照步骤一判定的不同应变率对应的屈服应变εy,取宽应变率条件应力应变响应曲线中应变值为0.75εy~εy范围内的数据点,如图3所示。在截取的应变范围内均布取50个应变值,将试验数据插值后提取50个应变值对应的应力及应变率数据,绘制应力-应变率对数坐标曲线,如图4所示。在宽应变率范围内可以认为应力随应变率对数变化近似呈现双线性规律,即存在一个转折应变率,在转折应变率前、后应力随应变率对数线性变化。根据曲线变化选取适当转折应变率,对该曲线按式(1)进行双线性拟合,选取的转折应变率应使得拟合后的数据相对原始数据方差最小。部分拟合结果如图5所示,每个εi对应一个参数系列(第一段斜率k1,i,第二段斜率k2,i,转折应变率)。式中:σi——第i个应变对应的应力,i=1~50,单位mpa;εi——截取范围内均布选取的应变值,i=1~50;——应变率,单位s-1;k1,i,b1,i——第i个应变对应的第一段直线系数,i=1~50;k2,i,b2,i——第i个应变对应的第二段直线系数,i=1~50;——某一应变率下第i个应变对应的转折应变率,i=1~50,单位s-1。上述得到的参数系列k1,i,k2,i,i=1~50能够描述该配方推进剂在承受轴向载荷时的率相关的力学性能。从拟合参数的结果看,应力-应变率对数曲线呈现微小的发散状态,假定各个应变下的曲线平行,即对拟合得到的双线性参数系列取均值(式(2)),得到描述该配方推进剂力学性能的三个关键参数k1=98.34,k2=577.41,以图3中提取的应力数据中最低应变率对应的应力数据作为起点,按照关键参数参数k1=98.34,k2=577.41,即在平行假设条件下可以计算不同应变下的数据,绘制成应变率对数坐标曲线如图6所示。通过prony级数对图6曲线进行力学性能表征。由于上述计算得到的应力应变数据仅限于应变值在ε=0.75εy~εy范围内的数据点,为提高prony级数本构方程的拟合精度,将ε=0.75εy的数据点与原点用直线连接,形成用于拟合prony级数本构方程的完整数据。在图2的试验数据中,可以发现在变形初始阶段推进剂更多表现出弹性状态,此处采用直线连接原点的方法是与实际相符合的。prony级数本构的拟合结果与计算得到的数据对比如图7所示,其中散点为计算得到的应力应变数据,实线为拟合的prony级数本构方程对应的应力应变数据。获得推进剂本构方程系数e∞,ei,τi,i=1~4。获得该配方推进剂prony级数本构方程:通过以上方式构造应力应变数据和对应的本构模型,表示不同的关键参数系列k1,k2,能够表征具有不同力学性能的推进剂配方,对关键参数的设计就可以在推进剂配方力学性能设计中产生指导作用。步骤四,按照给定的典型管装药结构尺寸(外径d=62mm、内径d=13mm、长度l=140mm),结合发动机抗高轴向过载的实际情况,建立图8所示的二维轴对称数值计算模型,其中壁面间隙给定为ds=1mm,由于主要考虑发射过载下的力学响应,发动机外壳简化为厚度为4mm的侧壁面和底面。参考炮射试验测得的实际发射过载,给定图9所示的轴向过载。其上升段经历7.5ms、最大过载平台段持续6.5ms、下降段经历3.5ms,在各阶段持续时间一定的条件下,平台阶段的过载最大值loadmax可根据计算需要进行调整。模型在6000g和8000g过载作用过程中,应力分布规律几乎不发生改变,在管装药底面内孔边缘位置产生较大应力。提取过载作用过程中底面内孔边缘位置的应力响应数据如图10所示,存在应力最大值13.72mpa和16.84mpa。发生最大应力时,6000g过载下该位置的应变率约为2.47s-1,且8000g过载下应变率响应几乎相同。查找图6所示的数据,可以得到在该应变率下的失效应力为14.5mpa,即具有关键参数为k1=98.34,k2=577.41,的该配方推进剂能够承受6000g的过载,不能承受8000g过载。步骤五,步骤四的结果表示该典型管装药在推进剂具有关键参数值为k1=98.34,k2=577.41,时,恰好可以承受6000g过载。步骤三中,构造的应力-应变率对数曲线起点一定时,率敏感性参数k1越大,意味着失效应力约大。因此寻找能够抗住更高过载的推进剂时,应当使其具有更大的关键参数k1。尝试取一个极大值k1=k2=577.41,按照新的双线性参数k1=k2=577.41,重复步骤三,得到本构方程:步骤六,按照新的本构方程重复步骤四的计算过程,过载最大值设置为9000g时,应力响应分布规律不变,应力响应数值明显提高。最大应力仍发生在底面靠近内孔位置,应力响应峰值约20.94mpa,对应的应变率响应约4.24s-1。查找构造的应力应变数据,具有力学关键参数k1=k2=577.41,的推进剂,在该应变率条件下失效应力为76.30mpa,远大于9000g过载下的应力响应。即该配方抗过载能力远大于9000g。步骤七,上述计算过程中的应变率响应水平明显小于推进剂关键参数中的转折应变率即推进剂抗过载能力仅受到k1影响;对特定的过载值,应存在一个最小值k1,min使得对应的推进剂配方能够保证不发生力学失效。但当某类型配方推进剂的转折应变率较小时,推进剂的抗过载应变率响应大于转折应变率关键参数k2将对推进剂的抗过载能力产生主要影响;对特定的过载值,在给定和一个较小的k1值时,应存在一个最小值k2,min使得对应的推进剂配方能够保证不发生力学失效。经过反复调整关键参数的数值,重复步骤五、步骤六,可以得到不同过载条件下壁面装药力学失效对关键参数的要求如表4、表5所示。表4实现不同抗过载能力推进剂的关键参数最小值k1,min过载g=9.8m/s2k1,min应力峰值/mpa失效应力/mpa6000g98.3413.7214.509000g158.2320.6221.0012000g218.1127.4928.0215000g277.9934.3736.16注:适用于在给出的过载作用下,转折应变率大于应变率响应的情况。表5实现不同抗过载能力推进剂的关键参数最小值k2,min过载g=9.8m/s2k2,min应力峰值/mpa失效应力/mpa6000g461.9313.7815.559000g866.1220.5622.0412000g981.6025.0325.1815000g1097.0833.1935.38注:即转折应变率小于抗过载应变率响应。即对给定的装药结构(d0=62mm,d0=13mm,l0=140mm),为获得6000~15000g的抗过载能力,推进剂力学性能的设计应满足其关键参数复合表4、表5的要求,给出推进剂配方设计中力学性能设计的指导。步骤八,根据步骤四的计算结果,初始方案的推进剂装药(即长径比l/d=2.26)具有6000g抗过载能力,要提高装药的抗过载能力,需要减小装药长径比。当长径比l/d=1.5,保证装药量和装药m数不变,计算得到装药结构尺寸d=71mm,d=15mm,l=106mm,重复步骤四,将过载最大值提高到9000g。计算得到应力响应峰值约26.11mpa,应变率响应约43.30s-1,对应失效应力为21.27mpa,即无法承受9000g过载。在实际使用中,长径比通常不会过小,因此为提高抗过载能力而继续减小长径比的设计是没有意义的。为承受更高的炮射过载条件,需要采用步骤五、步骤六中设计的具有更高抗过载力学性能的推进剂。此处采用某具有更高抗过载能力推进剂,其prony级数形式的本构方程为:调整装药模型的长径比,重复步骤六,可以得到不同过载条件要求的最大长径比如表6所示。表6不同过载条件的最大长径比设计要求当装药长径比较大时,径向变形相对明显,装药侧面与发动机壳体发生相对明显的摩擦作用,此处对装药壁面间隙的设计采用长径比l/d=4.3的装药进行6000g过载条件的有限元计算。根据装药抗过载应力响应结果,按照摩擦做功计算装药外侧面上的qc值,其沿装药侧面的变化趋势如图11所示。由图可得到三条结论:(1)过载作用期间,装药与壳体接触的最大长度约157mm,占装药总长的73%;(2)qc-t曲线呈钟形,其较大值出现在装药与壳体接触区域的中间部位,并非装药的底部或顶部;(3)qc的最大值约18.39mpa·mm,接近qμ,可以判断此装药在炮射过程中存在着自燃并引发发动机失效的危险。装药与壳体摩擦过程中产生并积累的热量可能导致热点的生成,并进一步威胁装药的热安全性。在这一过程中,对于给定的过载条件,显然装药与壳体间缝隙的宽度ds将对二者间的接触应力和相对运动速度的大小和历程产生决定性影响。图12给出不同缝隙宽度下的qc值,可见仅仅将缝隙宽度增大1mm,就可使qc值降至一个比较安全的范围。提取图12中不同缝隙宽度下qc的最大值,记为qmax,分析其与缝隙宽度ds的关系如图13所示。可见,存在一个关键的缝隙宽度dk,将qmax与缝隙宽度的关系分为两部分,在缝隙宽度小于dk时,二者呈线性关系,在缝隙宽度大于dk时,二者呈指数关系,即对于确定的装药结构尺寸,qmax与缝隙宽度ds间存在上述关系,当完成装药长径比设计后,再通过上述方法得到壁面间隙设计准则,以保障壁面摩擦的热安全性。对于本节所采用配方,有qμ,min=19.53mpa·mm,代入式(3)得到最小间隙要求约1mm。通过上述步骤一到步骤八,实现对给定某cmdb推进剂装药(结构尺寸为d0=62mm,d0=13mm,l0=140mm)耐炮射过载能力的测试与评估,得出该推进剂装药6000g最大抗过载能力的结论。同时,通过表4、表5明确提高推进剂抗过载能力的关键参数改进方向,表6、式(3)明确提高装药结构抗过载能力的装药结构参数。以上所述描述对本发明的目的、技术方案和有益性进行进一步说明,所应理解的是,以上所述仅为本发明的优选具体实施例,用于解释本发明,并不用于限定本发明的保护范围,实际操作中可以对实施过程中的各技术方案进行修改。凡在本发明的精神和原则之内,所做的任何修改、等同替换、改进等,均应包含在本发明的保护范围之内。当前第1页12