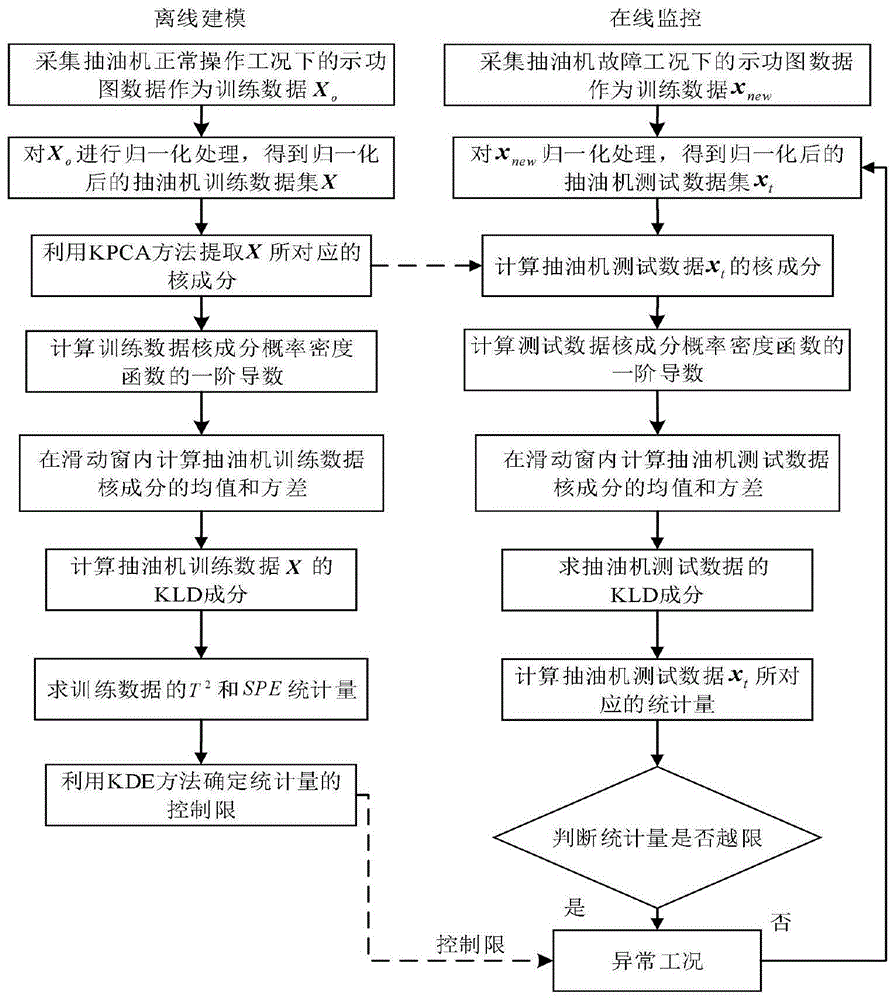
本发明属于工业系统工况监控
技术领域:
,具体地说,涉及一种抽油机异常工况监控方法。
背景技术:
:抽油机是石油开采的主要装置,在石油开采行业中发挥着重要的作用。由于大多数抽油机在恶劣环境中运行,通常存在不同的故障,这些故障会导致抽油机安全性的恶化和生产利润的降低。因此,有必要对抽油机进行实时监控,以保证石油开采过程的安全稳定运行。在抽油机故障诊断领域,示功图是最常用的工具,基于示功图已经开发出一些用于抽油机故障诊断的方法并取得了成功的应用,但这些方法本质上属于监督学习方法,需要正常和故障示功图来训练故障诊断模型。在实际应用中,抽油机的故障数据并不总是可用的,因此,需要研究无监督学习方法实现对抽油机异常工况的有效监控。核主元分析(简称:kpca)方法作为一种常见的非线性无监督方法,已经广泛应用于基于数据驱动的故障诊断领域。然而,在实际监控中,传统的kpca方法仅利用核成分构造监控模型,忽略了抽油机示功图数据所包含的概率信息,难以深入挖掘抽油机过程信息,进而影响对抽油机故障监控的效果,故障检测性能低。技术实现要素:本发明针对传统kpca方法存在的忽略过程信息中的概率信息导致故障检测性能低等问题,提供一种抽油机异常工况监控方法。该方法将kullbackleibler散度(英文:kullbackleiblerdivergence,简称:kld)引入到kpca方法中,利用kld挖掘抽油机过程数据所包含的概率信息,能够进一步挖掘抽油机过程数据信息,提高故障检测率,进而改善对抽油机异常工况的监控能力。为了达到上述目的,本发明提供了一种抽油机异常工况监控方法,含有以下步骤:(一)采集抽油机正常操作工况下的示功图数据作为训练数据x0,并利用训练数据x0的均值和标准差对训练数据xo进行归一化处理,得到归一化后的抽油机训练数据x;(二)利用kpca方法对所述归一化后的抽油机训练数据x进行处理,提取所述抽油机训练数据x的非线性特征作为核成分;(三)计算所述抽油机训练数据x核成分的概率密度函数以及该概率密度函数对应的一阶导数,利用滑动窗口得到所述抽油机训练数据x的训练kld成分;(四)由训练kld成分计算抽油机训练数据x的核主元空间统计量t2和核残差空间统计量spe,给定置信水平α,通过核密度估计方法计算核主元空间统计量t2所对应的控制限和核残差空间统计量spe所对应的控制限speα;(五)采集抽油机故障工况下的示功图数据作为测试数据xnew,利用训练数据xo的均值和标准差对测试数据xnew进行归一化处理,得到归一化后的抽油机测试数据xt;(六)利用kpca方法提取所述抽油机测试数据xt所对应的核成分;(七)计算所述抽油机测试数据xt核成分的概率密度函数以及该概率密度函数所对应的一阶导数,采用滑动窗口计算抽油机测试数据xt的在线kld成分;(八)由在线kld成分计算抽油机测试数据xt的核主元空间统计量和核残差空间统计量spenew;(九)依据核主元空间统计量是否超出控制限和核残差空间统计量spenew是否超出控制限speα,判断抽油机测试数据xt是否发生故障。进一步的,所述步骤(一)中,利用训练数据x0的均值和标准差通过公式(1)对训练数据xo进行归一化处理,得到归一化后的抽油机训练数据x,公式(1)的表达式为:训练数据集x0经上述公式(1)归一化处理后即可获得归一化后的抽油机训练数据x。进一步的,所述步骤(二)中,利用kpca方法提取所述抽油机训练数据x的非线性特征作为核成分的具体步骤为:对于归一化后的抽油机训练数据x=[x1,x2,...,xn]t∈rn×m,其中n表示样本个数,m变量个数,首先计算所述kpca方法中的核矩阵k,所述核矩阵k中的每个元素k(i,j)的计算公式表示为:式中,c为预设的核函数参数;对所述核矩阵k开展公式(3)中所示的特征值分解,公式(3)的表达式为:式中,为保留的特征空间维数;求解公式(3)得到个非零特征值以及与非零特征值对应的特征向量按照特征值的85%累计贡献率准则确定主元个数l,所述抽油机训练数据x的样本空间被划分为核主成分空间和核残差空间两部分;对于所述抽油机训练数据x中在第h个采样时刻的样本x(h),通过公式(4)提取对应的非线性特征ts=[ts(1),...,ts(h),...,ts(n)]t作为核成分,公式(4)的表达式为:式中,ts(h)为抽油机训练数据x中第h个采样时刻的样本x(h)对应的第s个核成分;ps为求解公式(3)所获得的第s个特征向量,kx=[k(h,1),...,k(h,n)]t∈rn为核向量。进一步的,步骤(三)中,计算所述抽油机训练数据x核成分的概率密度函数以及该概率密度函数对应的一阶导数的具体步骤为:由公式(5)计算所述抽油机训练数据x中第h个采样时刻的样本x(h)对应的第s个核成分ts(h)的概率密度函数g(ts(h)),公式(5)的表达式为:式中,us表示所述抽油机训练数据x核成分ts所对应的均值,λs表示所述抽油机训练数据x核成分ts所对应的方差,当数据满足高斯分布假设时,λs等于由公式(3)所分解得到特征值;由公式(6)计算所述概率密度函数g(ts(h))的一阶导数g′(ts(h)),公式(6)的表达式为:计算所述抽油机训练数据x的训练kld成分的具体步骤为:利用滑动窗口求取核成分ts(h)的均值和方差,由公式(7)计算所述抽油机训练数据x第h个采样时刻处的kldkls(h),公式(7)的表达式为:式中,表示利用滑动窗口所求的ts(h)均值,表示利用滑动窗口所求的ts(h)方差;进一步由公式(8)计算得到训练kld成分ys(h),公式(8)的表达式为:式中,ε表示调节参数,其取值由交叉验证法确定。进一步的,步骤(四)中,计算抽油机训练数据x的核主元空间统计量t2和核残差空间统计量spe的具体步骤为:基于kld成分ys,由公式(9)构造用于过程监控的核主元空间统计量t2,由(10)构造用于过程监控的核残差空间统计量spe,公式(9)、公式(10)的表达式为:式中,sl表示核主元空间所对应的协方差矩阵,sr表示核残差空间所对应的协方差矩阵,l为步骤(二)中所得到的主元个数。进一步的,步骤(五)中,利用训练数据x0的均值和标准差通过公式(11)对测试数据xnew进行归一化处理,得到归一化后的抽油机测试数据xt,公式(11)的表达式为:测试数据xnew经上述公式(11)归一化处理后即可获得归一化后的抽油机测试数据xt。进一步的,步骤(六)中,利用kpca方法提取所述抽油机测试数据xt所对应的核成分的具体步骤为:计算归一化后的抽油机测试数据xt对应的测试核向量kt,kt中每个元素kt(i)的计算公式为:式中,n表示样本数目,c为核参数;由公式(13)从所述测试核向量kt中提取非线性特征tt,s=[tt,s(1),...,tt,s(h),...]t,公式(13)的表达式为:式中,tt,s(h)为抽油机测试数据xt中第h个采样时刻的样本xt(h)对应的第s个核成分;ps为求解公式(4)获得的第s个特征向量。进一步的,步骤(七)中,计算所述抽油机测试数据xt核成分的概率密度函数以及该概率密度函数对应的一阶导数的具体步骤为:由公式(14)计算所述抽油机测试数据xt中第h个采样时刻的样本xt(h)对应的第s个核成分tt,s(h)的概率密度函数f(tt,s(h)),公式(14)的表达式为:式中,ut,s表示抽油机测试数据xt核成分tt,s所对应的均值,λt,s表示抽油机测试数据xt核成分tt,s所对应的方差;由公式(15)计算所述概率密度函数f(tt,s(h))的一阶导数f′(tt,s(h)),公式(15)的表达式为:计算所述抽油机测试数据xt的在线kld成分的具体步骤为:利用滑动窗口求取核成分tt,s(h)的均值和方差,由公式(16)计算在第h个采样时刻处的kldklt,s(h),公式(16)的表达式为:式中,表示利用滑动窗口所求的tt,s(h)均值,表示利用滑动窗口所求的tt,s(h)方差;进一步由公式(17)计算得到在线kld成分yt,s(h),公式(17)的表达式为:式中,ε表示步骤(三)中所得到的调节参数。进一步的,步骤(八)中,由在线kld成分计算抽油机测试数据xt的核主元空间统计量和核残差空间统计量spenew的具体步骤为:基于在线kld成分yt,s,由公式(18)构造用于过程监控的核主元空间统计量由公式(19)构造用于过程监控的核残差空间统计量spenew,公式(18)、公式(19)的表达式为:式中,sl表示核主元空间所对应的协方差矩阵,sr表示核残差空间所对应的协方差矩阵,l为步骤(二)中所得到的主元个数。进一步的,步骤(九)中,判断抽油机测试数据xt是否发生故障的步骤为:当且spenew≤speα时,认为抽油机处于正常工作状态,否则,认为抽油机出现故障。与现有技术相比,本发明的有益效果在于:本发明提供的抽油机异常工况监控方法,利用kullbackleibler散度度量核成分的概率分布变化,并考虑抽油机正常工况数据与故障数据核成分概率密度函数的一阶导数信息差异,实现了过程数据信息的进一步挖掘,使得统计量能够更为明显的反应抽油机过程数据所包含故障信息,进而改善故障检测结果,提高对抽油机异常工况的监控能力,有效克服传统kpca方法因忽略抽油机过程数据概率信息所造成的对抽油机异常工况监控性能不佳的问题。附图说明图1为本发明抽油机异常工况监控方法的流程图;图2为本发明实施例所述有杆抽油(英文:suckerrodpumping,简称:srp)系统的结构图;图3a为本发明实施例采用现有kpca方法对srp系统故障1的监控结果示意图;图3b为本发明实施例采用本发明抽油机异常工况监控方法对srp系统故障1的监控结果示意图;图4a为本发明实施例采用现有kpca方法对srp系统故障3的监控结果示意图;图4b为本发明实施例采用本发明抽油机异常工况监控方法对srp系统故障3的监控结果示意图。图中,1、电动机,2、连杆,3、游梁,4、悬绳,5、抽油杆,6、油管,7、游动阀,8、固定阀,9、套管,10、泵筒,11、配重,12、皮带,13、减速箱,14、电机控制箱,15、油层。具体实施方式下面,通过示例性的实施方式对本发明进行具体描述。然而应当理解,在没有进一步叙述的情况下,一个实施方式中的元件、结构和特征也可以有益地结合到其他实施方式中。参见图1,本发明揭示了一种抽油机异常工况监控方法,含有以下步骤:(一)采集抽油机正常操作工况下的示功图数据作为训练数据x0,利用训练数据x0的均值和标准差通过公式(1)对训练数据xo进行归一化处理,得到归一化后的抽油机训练数据x,公式(1)的表达式为:训练数据集x0经上述公式(1)归一化处理后即可获得归一化后的抽油机训练数据x。(二)利用kpca方法对所述归一化后的抽油机训练数据x进行处理,提取所述抽油机训练数据x的非线性特征作为核成分;其中,提取所述抽油机训练数据x的非线性特征作为核成分的具体步骤为:对于归一化后的抽油机训练数据x=[x1,x2,...,xn]t∈rn×m,其中n表示样本个数,m变量个数,首先计算所述kpca方法中的核矩阵k,所述核矩阵k中的每个元素k(i,j)的计算公式表示为:式中,c为预设的核函数参数。对所述核矩阵k开展公式(3)中所示的特征值分解,公式(3)的表达式为:式中,为保留的特征空间维数;求解公式(3)得到个非零特征值以及与非零特征值对应的特征向量按照特征值的85%累计贡献率准则确定主元个数l,所述抽油机训练数据x的样本空间被划分为核主成分空间和核残差空间两部分;对于所述抽油机训练数据x中在第h个采样时刻的样本x(h),通过公式(4)提取对应的非线性特征ts=[ts(1),...,ts(h),...,ts(n)]t作为核成分,公式(4)的表达式为:式中,ts(h)为抽油机训练数据x中第h个采样时刻的样本x(h)对应的第s个核成分;ps为求解公式(3)所获得的第s个特征向量,kx=[k(h,1),...,k(h,n)]t∈rn为核向量。(三)计算所述抽油机训练数据x核成分的概率密度函数以及该概率密度函数对应的一阶导数,利用滑动窗口得到所述抽油机训练数据x的训练kld成分;具体步骤为:由公式(5)计算所述抽油机训练数据x中第h个采样时刻的样本x(h)对应的第s个核成分ts(h)的概率密度函数g(ts(h)),公式(5)的表达式为:式中,us表示所述抽油机训练数据x核成分ts所对应的均值,λs表示所述抽油机训练数据x核成分ts所对应的方差,当数据满足高斯分布假设时,λs等于由公式(3)所分解得到特征值;由公式(6)计算所述概率密度函数g(ts(h))的一阶导数g′(ts(h)),公式(6)的表达式为:利用滑动窗口求取核成分ts(h)的均值和方差,由公式(7)计算所述抽油机训练数据x第h个采样时刻处的kldkls(h),公式(7)的表达式为:式中,表示利用滑动窗口所求的ts(h)均值,表示利用滑动窗口所求的ts(h)方差;进一步由公式(8)计算得到训练kld成分ys(h),公式(8)的表达式为:式中,ε表示调节参数,其取值由交叉验证法确定。(四)由训练kld成分计算抽油机训练数据x的核主元空间统计量t2和核残差空间统计量spe,具体步骤为:基于kld成分ys,由公式(9)构造用于过程监控的核主元空间统计量t2,由(10)构造用于过程监控的核残差空间统计量spe,公式(9)、公式(10)的表达式为:式中,sl表示核主元空间所对应的协方差矩阵,sr表示核残差空间所对应的协方差矩阵,l为步骤(二)中所得到的主元个数;给定置信水平α,通过核密度估计(简称:kde)方法计算核主元空间统计量t2所对应的控制限和核残差空间统计量spe所对应的控制限speα。(五)采集抽油机故障工况下的示功图数据作为测试数据xnew,利用训练数据x0的均值和标准差通过公式(11)对测试数据xnew进行归一化处理,得到归一化后的抽油机测试数据xt,公式(11)的表达式为:测试数据xnew经上述公式(11)归一化处理后即可获得归一化后的抽油机测试数据xt。(六)利用kpca方法提取所述抽油机测试数据xt所对应的核成分,具体步骤为:计算归一化后的抽油机测试数据xt对应的测试核向量kt,kt中每个元素kt(i)的计算公式为:式中,n表示样本数目,c为核参数;由公式(13)从所述测试核向量kt中提取非线性特征tt,s=[tt,s(1),...,tt,s(h),...]t,公式(13)的表达式为:式中,tt,s(h)为抽油机测试数据xt中第h个采样时刻的样本xt(h)对应的第s个核成分;ps为求解公式(4)获得的第s个特征向量。(七)计算所述抽油机测试数据xt核成分的概率密度函数以及该概率密度函数所对应的一阶导数,采用滑动窗口计算抽油机测试数据xt的在线kld成分,具体步骤为:由公式(14)计算所述抽油机测试数据xt中第h个采样时刻的样本xt(h)对应的第s个核成分tt,s(h)的概率密度函数f(tt,s(h)),公式(14)的表达式为:式中,ut,s表示抽油机测试数据xt核成分tt,s所对应的均值,λt,s表示抽油机测试数据xt核成分tt,s所对应的方差;由公式(15)计算所述概率密度函数f(tt,s(h))的一阶导数f′(tt,s(h)),公式(15)的表达式为:利用滑动窗口求取核成分tt,s(h)的均值和方差,由公式(16)计算在第h个采样时刻处的kldklt,s(h),公式(16)的表达式为:式中,表示利用滑动窗口所求的tt,s(h)均值,表示利用滑动窗口所求的tt,s(h)方差;进一步由公式(17)计算得到在线kld成分yt,s(h),公式(17)的表达式为:式中,ε表示步骤(三)中所得到的调节参数。(八)由在线kld成分计算抽油机测试数据xt的核主元空间统计量和核残差空间统计量spenew,具体步骤为:基于在线kld成分yt,s,由公式(18)构造用于过程监控的核主元空间统计量由公式(19)构造用于过程监控的核残差空间统计量spenew,公式(18)、公式(19)的表达式为:式中,sl表示核主元空间所对应的协方差矩阵,sr表示核残差空间所对应的协方差矩阵,l为步骤(二)中所得到的主元个数。(九)依据核主元空间统计量是否超出控制限和核残差空间统计量spenew是否超出控制限speα,判断抽油机测试数据xt是否发生故障。具体地,当且spenew≤speα时,认为抽油机处于正常工作状态,否则,认为抽油机出现故障。上述方法中,步骤(一)至(四)为离线建模阶段,步骤(五)至(九)为在线测试阶段。本发明上述故障检测方法,利用kullbackleibler散度挖掘抽油机过程数据所包含的概率信息,并考虑正常数据与故障数据核成分概率密度函数的导数信息差异,能够更加精准地衡量抽油机过程数据的故障特征信息,提高故障检测率,进而改善故障检测结果。为了能更清楚地说明本发明上述故障检测方法的有益效果,以下结合实施例对本发明上述故障检测方法做出进一步说明。实施例:有杆泵抽油(以下简称:srp)系统是石油开采的主要单元,广泛应用于石油开采行业。参见图2,srp系统由电动机1、连杆2、游梁3、抽油泵等部件构成。系统运行时,电动机1产生的动力通过连杆2、游梁3和悬绳4使得抽油杆5作上下往复运动,进而将动力传递给井下部分,随着固定阀8与游动阀7交替打开和关闭,井内液体不断进入泵筒10,从而上行进入油管6,最后达到地面。在抽油机运行过程中,示功图是最常见的状态数据采集手段。本实施实例中,根据重心分解法和阀门工作位置对示功图进行特征提取,采集7个示功图特征作为监控变量,参见表1,pall代表一次冲程内的流体生产率和泵的效率,p1、p2、p3和p4分别反映了不同阀门位置下柱塞的工作情况,d1、d2分别代表固定阀和游动阀的工作位移。通过机理模拟方式仿真正常工况数据,并同时仿真表2所示的3种故障工况数据。对于每种操作模式,均采集500个样本用于过程监测,其中测试数据集从第201个采样时刻开始引入故障并使故障一直持续到仿真结束为止。表1变量变量描述pall示功图的总面积p1示功图左下方区域的面积p2示功图左上方区域的面积p3示功图右上方区域的面积p4示功图右下方区域的面积d1固定阀的工作位移d2游动阀的工作位移表2故障描述f1供液不足f2泵上碰f3游动阀发生泄露采用本发明上述监控方法(以下简称:kld-kpca方法)对本实施例所述srp系统进行故障检测。检测到发生故障后,为评价不同故障检测方法的故障检测性能,通过故障检出率fdr指标对不同方法的故障检测结果对比。故障检出率fdr定义为检测出的故障数据与实际总的故障数据之比。很显然,fdr的数值越大,意味着故障检测方法的故障检测效果越好即对抽油机异常工况的监控性能越好;反之,对抽油机异常工况的监控性能越差。在本实施例的srp系统仿真中,采用kpca方法和本发明kld-kpca方法两种方法进行仿真对比。在本实施例中,两种方法均根据99.99%的方差累计贡献率保留特征空间的维数根据85%的方差贡献率确定主元个数l。本发明kld-kpca方法中利用交叉验证法选择滑动窗窗口宽度w为25。利用99%置信度计算两种方法统计量的控制限。故障1是由供液不足引起的,采用传统kpca方法和本发明kld-kpca方法对故障1的监控结果参见图3a-3b。图3a为传统kpca方法对故障1的监控结果,核主元空间统计量t2的检出率为54%,核残差空间统计量spe的检出率为60%,两个统计量的检出时间均为第303个采样时间。从图3b可以看出,与传统kpca方法相比,本发明kld-kpca方法对故障1的监控性能有了的明显提高,核主元空间t2统计量的检出率为71%,相应的检出时间为第304个采样点。核残差空间统计量spe的检出率为77.33%,相应的检出时间为第248个采样点。通过比较这两种方法的检测结果,初步证明了本发明所提的kld-kpca方法能够改善对srp系统故障1的检测性能。故障3为游动阀发生泄漏,采用传统kpca方法和本发明kld-kpca方法对故障3的监控效果参见图4a-4b所示。参见图4a,传统kpca方法对故障3的监测能力较差,大多数故障样本未被检测到。其中核残差空间统计量spe在第215个采样点出检测到故障的发生,相应的检出率为15.67%,核主元空间统计量t2的检出率为22.33%。本发明kld-kpca方法对故障3的监测结果如图4b所示,所提方法利用kullbackleibler散度挖掘过程数据中包含的概率信息,并进一步考虑正常数据与故障数据核成分概率密度函数的一阶导数信息差异,与传统kpca方法相比,检测能力得到了显著提高。在第214个采样时刻核主元空间统计量t2开始检测到故障3的发生,相应的检出率为94%。核残差空间统计量spe的检出率为92.67%,相应的检出时间为第218个采样点。对故障3的仿真结果表明,本发明kld-kpca方法能够更及时地检测到故障的发生,并具有更高的故障检出率。表3给出了传统kpca方法和本发明kld-kpca方法对于本实施例srp系统3种故障的故障检出率。表3由表3可知,传统的kpca方法对于本实施例srp系统的3种故障不能给出满意的监控效果,本发明kld-kpca方法通过利用kullbackleibler散度挖掘过程数据所包含的概率信息,并进一步考虑正常数据与故障数据核成分概率密度函数的一阶导数信息差异,本发明提供的kld-kpca方法对于这3种故障的检测效果能获得明显的改善。综合以上分析,本发明所提供抽油机异常工况监控方法,其故障检测效果明显优于传统kpca方法。以上所举实施例仅用为方便举例说明本发明,并非对本发明保护范围的限制,在本发明所述技术方案范畴,所属
技术领域:
的技术人员所作各种简单变形与修饰,均应包含在以上申请专利范围中。当前第1页12