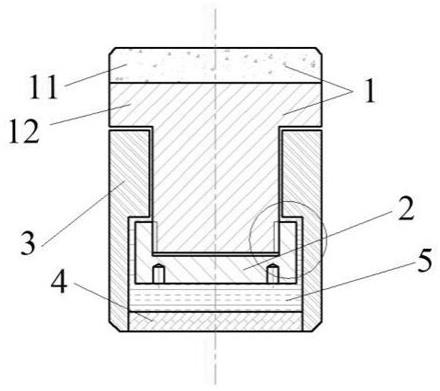
一种全刃口pdc钻齿及其制备方法
技术领域
1.本发明涉及油气钻探用钻齿技术领域,具体为一种全刃口pdc钻齿及其制备方法。
背景技术:2.pdc(金刚石复合片)具有耐磨性极高、抗冲击性优异、热稳定性好、导热系数高、便于加工、使用方便等一系列的优点。pdc最重要的用途之一是作为主要受力耐磨部件——钻齿,制备地质勘探及煤田、油气开采用钻头。现在pdc钻头在世界范围内己经占据了钻井总进尺的90%以上。
3.目前市面上传统的pdc钻齿通常被焊接在钻头本体上,在其使用过程中始终固定在同一个位置,被包覆部分往往占其总体积的60%以上。从目前的实际使用结果来看,刃口仅占到整个圆周的1/3左右。导致产品失效时,仍有较大部分处于未使用的状态,这是对材料的极大浪费,无形中提高了pdc钻头的使用成本。
4.同时使用区域过小也造成了产品使用寿命的相对缩短,在实际钻进过程中易出现频繁提钻的情况。目前的钻进现场特别是超深井的钻进使用环境中,起下钻本身的成本已经占到了单井钻进总成本的30~50%,而传统pdc钻头造成频繁起下钻的情况,将会造成钻进速度会大大降低,延长了钻井周期,这对钻头使用方来说是一种较大的成本损失。同时考虑到目前国内外油气资源分布,深井及超深井占比已经在50%以上,这一制约钻进的现状亟待解决。
技术实现要素:5.本发明的目的是提供一种全刃口pdc钻齿,能够针对目前传统产品刃口使用效率低,产品使用寿命短,起下钻频繁的特点,提供一种能够全刃口使用,耐磨性、抗冲击性明显提高,寿命大大延长,能够显著提高钻进效率、降低钻进成本的pdc钻齿。本发明还提供了上述pdc钻齿的制备方法。
6.为实现以上目的,本发明通过以下技术方案予以实现:一种全刃口pdc钻齿,包括旋转体和固定腔,旋转体安装在固定腔内,所述旋转体包括齿头和定位块,所述齿头和定位块采用螺纹相连接,所述定位块的底部开设有安装盲孔,所述齿头为t形圆柱结构,上部分材质为金刚石层,下部分材质为硬质合金,且两段结合面为平面或非平面,所述固定腔由外套环和封底件组成,所述外套环的内径分为两段,且两段内径差为2~5mm,所述旋转体与固定腔之间填充有润滑剂。
7.具体的,所述金刚石层分为圆台状芯部和外部的耐磨环,所述耐磨环的宽度d为1~5mm,厚度h为1~3mm,所述耐磨环与芯部结合面包含但不限于弧面、垂直面。
8.具体的,所述耐磨环所用1号粉料组成包括w3.5金刚石微粉10~15wt.%,w5金刚石微粉20~30wt.%,w28金刚石微粉45~60wt.%,w40金刚石微粉0~5wt.%,3~5μmco粉1~3wt.%,10~20μmfe粉0.5~1wt.%,20~30μmsic粉2~4wt.%;所述芯部1102所用2号粉料组成包括w28金刚石微粉45~60wt.%,w40金刚石微粉35~45wt.%,3~5μmco粉1~3wt.%,10~
20μmti3sic2粉2~5wt.%。
9.具体的,所述硬质合金部分为多段非均质合金,其中靠近金刚石层位置一端为低co含量合金co的含量为5~8wt.%,另一端为高co含量合金co的含量为13~16wt.%。
10.一种全刃口pdc钻齿的制备方法,其制作具体步骤如下:1)将1号粉料放入金属杯模具中,并压制成环状,而后将2号粉料放入,并将粉体表面匀平;2)将低co含量合金与金刚石接触的一面放入配置好的酸液中进行减钴处理,处理后将另一侧平磨抛光,与之接触的高co含量合金一侧也进行抛光加工;3)将低co含量合金、高co含量合金依次放入金属杯模具中,而后在外侧套装盐管、碳管、叶腊石等辅材,在高温高压下合成为毛坯;4)毛坯经机械加工,分别对复合层表面、外圆、底部及上下尖锐边缘进行磨削加工至半成品;5)对半成品金刚石层进行脱钴处理后,将其下端合金车削至所需形状并加工出螺纹,制成齿头;6)将齿头与固定块分别在两端装入外套环并拧紧;7)自大孔径一侧向外套环中注满润滑剂;8)采用过盈配合工艺将封底件装入外套环大孔径一侧,并对外套环底部外圆边缘进行倒角,制得成品pdc钻齿。
11.具体的,两种金刚石层粉料均采用三维混料机干混+滚筒球磨机湿混的复合混料工艺,其中干混转速为60~90r/min,时间为1~3h;湿混转速为100~150r/min,时间为2~10h,介质包含但不限于丙酮、无水乙醇、纯净水。
12.具体的,低co含量合金在使用前,靠近金刚石层的一侧须进行减钴处理,低co含量合金和高co含量合金使用前需进行抛光处理具体的,采用酸浸法对硬质合金进行处理,所用酸液为浓盐酸、浓硝酸、浓硫酸按体积比1:0.5~0.8:1.5~2.5配置而成,酸浸温度为10~30℃,酸浸时间为1~3h。
13.具体的,先在模具中放入1号粉料,干压至所需环形后,再放入2号粉料,匀平后依次放入低co含量合金和高co含量合金两段基体。
14.具体的,齿头自小孔径一端装入外套环后,将定位块自另一端装入,并使用专用工具将二者拧紧。
15.具体的,封底件与外套环之间采用过盈配合,使用冷装工艺进行组装。
16.与现有技术相比,该一种全刃口pdc钻齿具备如下有益效果:1、该一种全刃口pdc钻齿采用旋转体设计,使pdc钻齿金刚石层能够实现全刃口工作,在材料总量不变的基础上,能够大大提高产品的使用寿命,进而提高单次钻进深度,大大提高钻进效率,降低钻进成本。
17.2、该一种全刃口pdc钻齿在金刚石层中设置耐磨性、抗崩损性能更好的耐磨环结构,能够保证产品在使用过程前期不出现较大刀口,进而避免因刀口卡顿造成刀口处快速磨损进而使产品失效的情况发生;采用多段合金配合减钴工艺,既避免了合金中co元素大量向金刚石层中扩散而导致性能劣化,同时也保证了下端合金中co含量便于后续机械加工要求,而将两段基体抛光后,在高温合成阶段的类扩散焊接原理下,能够自行拼接在一起,
同时具有较高的拼接强度3、该一种全刃口pdc钻齿采用不同孔径的外套环作为固定腔腔壁,减小了固定腔的制作难度,可通过现有正常工艺进行生产;采用冷装工艺进行固定腔封底,避免了高温加热对金刚石层的不利影响,能够更大程度上发挥金刚石层原有的优良性能;采用复合混料工艺,避免了不同粒径的粉料再混料中出现不匀或离析现象,从而大大提高了金刚石层中的物质均匀性,进而为性能均匀、刃口磨削均匀提供了保障。
18.4、该一种全刃口pdc钻齿的齿头转动能够在钻进受力过程中,将部分冲击力转化为转动力,从而提高了产品的抗冲击强度,使用寿命进一步增加,同时在同等钻速下所需钻压也大大降低,能够节约能源的消耗。
附图说明
19.图1是本发明所述钻齿剖面图。
20.图2是图1的局部放大图。
21.图3是硬质合金组合示意图。
22.图4是半成品钻齿剖面图。
23.图5是另一种半成品钻齿剖面示意图。
24.图6是旋转体剖面示意图。
25.图7是外套环俯视图。
26.其中: 1、齿头;11、金刚石层;12、硬质合金;1101、耐磨环;1102、芯部;1201、低co含量合金;1202、高co含量合金;2、定位快;3、外套环;4、封底件;5、润滑剂。
具体实施方式
27.下面将结合本发明实施例中的附图,对本发明实施例中的技术方案进行清楚、完整地描述,显然,所描述的实施例仅仅是本发明一部分实施例,而不是全部的实施例。基于本发明中的实施例,本领域普通技术人员在没有做出创造性劳动前提下所获得的所有其他实施例,都属于本发明保护的范围。需要说明的是,在本发明的描述中,术语“中心”、“上”、“下”、“左”、“右”、“竖直”、“水平”、“内”、“外”等指示方向或位置关系的术语是基于附图所示的方向或位置关系,这仅仅是为了便于描述,而不是指示或暗示装置或元件必须具有特定的方位、以特定的方位构造和操作,因此不能理解为对本发明的限制。此外,术语“第一”、“第二”、“第三”、“第四”仅用于描述目的,而不能理解为指示或暗示相对重要性。
28.此外,还需要说明的是,在本发明的描述中,除非另有明确的规定和限定,术语“安装”、“相连”、“连接”应做广义理解,例如,可以是固定连接,也可以是可拆卸连接,或一体地连接;可以是机械连接,也可以是电连接;可以是直接相连,也可以通过中间媒介间接相连,可以是两个元件内部的连通。对于本领域技术人员而言,可根据具体情况理解上述术语在本发明中的具体含义。
29.如图1-7所示,本发明提供一种全刃口pdc钻齿,包括旋转体和固定腔,旋转体安装在固定腔内,旋转体包括齿头1和定位块2,齿头1和定位块2采用螺纹相连接,定位块2的底部开设有安装盲孔,齿头1为t形圆柱结构,上部分材质为金刚石层11,下部分材质为硬质合金12,且两段结合面为平面或非平面,固定腔由外套环3和封底件4组成,外套环3的内径分
为两段,且两段内径差为2~5mm,采用不同孔径的外套环作为固定腔腔壁,减小了固定腔的制作难度,可通过现有正常工艺进行生产,旋转体与固定腔之间填充有润滑剂5,润滑剂5的材质包含但不限于石墨、六方氮化硼、二硫化钼等,能够使用多种润滑材质,提高刀具的适用性,采用旋转体设计,使pdc钻齿金刚石层能够实现全刃口工作,在材料总量不变的基础上,能够大大提高产品的使用寿命,进而提高单次钻进深度,大大提高钻进效率,降低钻进成本。
30.进一步地,金刚石层11分为圆台状芯部1102和外部的耐磨环1101,耐磨环1101的宽度d为1~5mm,厚度h为1~3mm,耐磨环1101与芯部结合面包含但不限于弧面、垂直面等,设置耐磨性、抗崩损性能更好的耐磨环结构,能够保证产品在使用过程前期不出现较大刀口,进而避免因刀口卡顿造成刀口处快速磨损进而使产品失效的情况发生。
31.进一步地,耐磨环1101所用1号粉料组成包括w3.5金刚石微粉10~15wt.%,w5金刚石微粉20~30wt.%,w28金刚石微粉45~60wt.%,w40金刚石微粉0~5wt.%,3~5μmco粉1~3wt.%,10~20μmfe粉0.5~1wt.%,20~30μmsic粉2~4wt.%;芯部1102所用2号粉料组成包括w28金刚石微粉45~60wt.%,w40金刚石微粉35~45wt.%,3~5μmco粉1~3wt.%,10~20μmti3sic2粉2~5wt.%。
32.进一步地,硬质合金12部分为多段非均质合金,其中靠近金刚石层11位置一端为低co含量合金1201co的含量为5~8wt.%,另一端为高co含量合金1202co的含量为13~16wt.%,采用多段合金配合减钴工艺,既避免了合金中co元素大量向金刚石层中扩散而导致性能劣化,同时也保证了下端合金中co含量便于后续机械加工要求。
33.本发明提供一种全刃口pdc钻齿制备方法,其制作具体步骤如下:1)将1号粉料放入金属杯模具中,并压制成环状,而后将2号粉料放入,并将粉体表面匀平;2)将低co含量合金与金刚石接触的一面放入配置好的酸液中进行减钴处理,处理后将另一侧平磨抛光,与之接触的高co含量合金1202一侧也进行抛光加工;3)将低co含量合金、高co含量合金依次放入金属杯模具中,而后在外侧套装盐管、碳管、叶腊石等辅材,在高温高压下合成为毛坯;4)毛坯经机械加工,分别对复合层表面、外圆、底部及上下尖锐边缘进行磨削加工至半成品;5)对半成品金刚石层进行脱钴处理后,将其下端合金车削至所需形状并加工出螺纹,制成齿头;6)将齿头与固定块分别在两端装入外套环并拧紧;7)自大孔径一侧向外套环中注满润滑剂;8)采用过盈配合工艺将封底件装入外套环大孔径一侧,并对外套环底部外圆边缘进行倒角,制得成品pdc钻齿。
34.进一步地,两种金刚石层粉料均采用三维混料机干混+滚筒球磨机湿混的复合混料工艺,其中干混转速为60~90r/min,时间为1~3h;湿混转速为100~150r/min,时间为2~10h,介质包含但不限于丙酮、无水乙醇、纯净水等,采用复合混料工艺,避免了不同粒径的粉料再混料中出现不匀或离析现象,从而大大提高了金刚石层中的物质均匀性,进而为性能均匀、刃口磨削均匀提供了保障。
35.进一步地,低co含量合金在使用前,靠近金刚石层的一侧须进行减钴处理,低co含量合金和高co含量合金使用前需进行抛光处理,将两段基体抛光后,在高温合成阶段的类扩散焊接原理下,能够自行拼接在一起,同时具有较高的拼接强度。
36.进一步地,采用酸浸法对硬质合金进行处理,所用酸液为浓盐酸、浓硝酸、浓硫酸按体积比1:0.5~0.8:1.5~2.5配置而成,酸浸温度为10~30℃,酸浸时间为1~3h。
37.进一步地,先在模具中放入1号粉料,干压至所需环形后,再放入2号粉料,匀平后依次放入低co含量合金和高co含量合金两段基体。
38.进一步地,齿头自小孔径一端装入外套环后,将定位块自另一端装。入,并使用专用工具将二者拧紧,封底件与外套环之间采用过盈配合,使用冷装工艺进行组装,采用冷装工艺进行固定腔封底,避免了高温加热对金刚石层的不利影响,能够更大程度上发挥金刚石层原有的优良性能。
39.实施例1:本实施例的pdc钻齿,由下述步骤制备获得:1)按w3.5金刚石微粉10wt.%,w5金刚石微粉30wt.%,w28金刚石微粉45wt.%,3~5μmco粉2.5wt.%,10~20μmfe粉0.5wt.%,20~30μmsic粉2wt.%配置1号粉料;按w28金刚石微粉52wt.%,w40金刚石微粉45wt.%,3~5μmco粉1wt.%,10~20μmti3sic2粉2wt.%配置2号粉料;2)将上述两种粉料采用三维混料机干混+滚筒球磨机湿混的复合混料工艺,其中干混转速为70r/min,时间为1h;湿混转速为120r/min,时间为6h,介质为纯净水;3)将混合好的1号粉料放入模具并压制成环形,而后放入2号粉料并将表面匀平;4)按浓盐酸、浓硝酸、浓硫酸体积比1:0.6:1.9配置酸液,将co含量为8%的硬质合金与金刚石层接触的一侧放入15℃酸液中浸泡1h。
40.5)依次放入co含量为8%的硬质合金和13%的硬质合金,其中合金与金刚石层接触面为非平面;6)将上述组合体外套盐管、碳管、叶腊石后,进行高温高压合成得到毛坯pdc;7)毛坯pdc经机械加工,分别对复合层表面、外圆、底部及上下尖锐边缘磨削加工后形成半成品,之后对复合层进行脱钴处理;8)将脱钴后的pdc半成品加工成齿头,与定位块在外套环中进行组装,其中外套环两端内径差值为3mm;9)在外套环中注满石墨润滑剂,而后采用冷装过盈配合工艺将封底件装入外套环中,制得成品pdc钻齿。
41.利用本方法制得一批pdc钻齿,随机抽取5粒对其进行性能检测,分别采用用车削石材和模拟微钻的方法来检测金刚石复合片的耐磨性、使用寿命和钻进效率。并与目前传统pdc钻齿在同等条件下对比,对比结果如下:
实施例2:本实施例的pdc钻齿,由下述步骤制备获得:1)按w3.5金刚石微粉12wt.%,w5金刚石微粉23wt.%,w28金刚石微粉55wt.%,w40金刚石微粉5wt.%,3~5μmco粉1.5wt.%,10~20μmfe粉0.5wt.%,20~30μmsic粉3wt.%配置1号粉料;按w28金刚石微粉57wt.%,w40金刚石微粉37wt.%,3~5μmco粉2wt.%,10~20μmti3sic2粉5wt.%配置2号粉料;2)将上述两种粉料采用三维混料机干混+滚筒球磨机湿混的复合混料工艺,其中干混转速为60r/min,时间为2h;湿混转速为140r/min,时间为8h;3)将混合好的1号粉料放入模具并压制成环形,而后放入2号粉料并将表面匀平;4)按浓盐酸、浓硝酸、浓硫酸体积比1:0.5:2.5配置酸液,将co含量为8%的硬质合金与金刚石层接触的一侧放入25℃酸液中浸泡1h。
42.5)依次放入co含量为8%的硬质合金和16%的硬质合金,其中合金与金刚石层接触面为非平面;6)将上述组合体外套盐管、碳管、叶腊石后,进行高温高压合成得到毛坯pdc;7)毛坯pdc经机械加工,分别对复合层表面、外圆、底部及上下尖锐边缘磨削加工后形成半成品,之后对复合层进行脱钴处理;8)将脱钴后的pdc半成品加工成齿头,与定位块在外套环中进行组装,其中外套环两端内径差值为2mm;9)在外套环中注满六方氮化硼润滑剂,而后采用冷装过盈配合工艺将封底件装入外套环中,制得成品pdc钻齿。
43.利用本方法制得一批pdc钻齿,随机抽取5粒对其进行性能检测,分别采用用车削石材和模拟微钻的方法来检测金刚石复合片的耐磨性、使用寿命和钻进效率。并与目前传统pdc钻齿在同等条件下对比,对比结果如下:
实施例3:本实施例的pdc钻齿,由下述步骤制备获得:1)按w3.5金刚石微粉15wt.%,w5金刚石微粉30wt.%,w28金刚石微粉45wt.%,w40金刚石微粉5wt.%,3~5μmco粉1wt.%,10~20μmfe粉 1wt.%,20~30μmsic粉3wt.%配置1号粉料;按w28金刚石微粉57wt.%,w40金刚石微粉40wt.%,3~5μmco粉1wt.%,10~20μmti3sic2粉2wt.%配置2号粉料;2)将上述两种粉料采用三维混料机干混+滚筒球磨机湿混的复合混料工艺,其中干混转速为90r/min,时间为2h;湿混转速为120~150r/min,时间为8h;3)将混合好的1号粉料放入模具并压制成环形,而后放入2号粉料并将表面匀平;4)按浓盐酸、浓硝酸、浓硫酸体积比1:0.6:1.5配置酸液,将co含量为5%的硬质合金与金刚石层接触的一侧放入10~30℃酸液中浸泡1~3h。
44.5)依次放入co含量为5%的硬质合金和16%的硬质合金,其中合金与金刚石层接触面为非平面;6)将上述组合体外套盐管、碳管、叶腊石后,进行高温高压合成得到毛坯pdc;7)毛坯pdc经机械加工,分别对复合层表面、外圆、底部及上下尖锐边缘磨削加工后形成半成品,之后对复合层进行脱钴处理;8)将脱钴后的pdc半成品加工成齿头,与定位块在外套环中进行组装,其中外套环两端内径差值为5mm;9)在外套环中注满二硫化钼润滑剂,而后采用冷装过盈配合工艺将封底件装入外套环中,制得成品pdc钻齿。
45.利用本方法制得一批pdc钻齿,随机抽取5粒对其进行性能检测,分别采用用车削石材和模拟微钻的方法来检测金刚石复合片的耐磨性、使用寿命和钻进效率。并与目前传统pdc钻齿在同等条件下对比,对比结果如下:
实施例4:本实施例的pdc钻齿,由下述步骤制备获得:1)按w3.5金刚石微粉10wt.%,w5金刚石微粉20wt.%,w28金刚石微粉60wt.%,w40金刚石微粉5wt.%,3~5μmco粉1.5wt.%,10~20μmfe粉0.5wt.%,20~30μmsic粉3wt.%配置1号粉料;按w28金刚石微粉60wt.%,w40金刚石微粉45wt.%,3~5μmco粉3wt.%,10~20μmti3sic2粉2wt.%配置2号粉料;2)将上述两种粉料采用三维混料机干混+滚筒球磨机湿混的复合混料工艺,其中干混转速为60r/min,时间为3h;湿混转速为150r/min,时间为9h;3)将混合好的1号粉料放入模具并压制成环形,而后放入2号粉料并将表面匀平;4)按浓盐酸、浓硝酸、浓硫酸体积比1:0.8:2.5配置酸液,将co含量为8%的硬质合金与金刚石层接触的一侧放入20℃酸液中浸泡3h。
46.5)依次放入co含量为8%的硬质合金和16%的硬质合金,其中合金与金刚石层接触面为非平面;6)将上述组合体外套盐管、碳管、叶腊石后,进行高温高压合成得到毛坯pdc;7)毛坯pdc经机械加工,分别对复合层表面、外圆、底部及上下尖锐边缘磨削加工后形成半成品,之后对复合层进行脱钴处理;8)将脱钴后的pdc半成品加工成齿头,与定位块在外套环中进行组装,其中外套环两端内径差值为5mm;9)在外套环中注满六方氮化硼润滑剂,而后采用冷装过盈配合工艺将封底件装入外套环中,制得成品pdc钻齿。
47.利用本方法制得一批pdc钻齿,随机抽取5粒对其进行性能检测,分别采用用车削石材和模拟微钻的方法来检测金刚石复合片的耐磨性、使用寿命和钻进效率。并与目前传统pdc钻齿在同等条件下对比,对比结果如下:
尽管已经示出和描述了本发明的实施例,对于本领域的普通技术人员而言,可以理解在不脱离本发明的原理和精神的情况下可以对这些实施例进行多种变化、修改、替换和变型,本发明的范围由所附权利要求及其等同物限定。