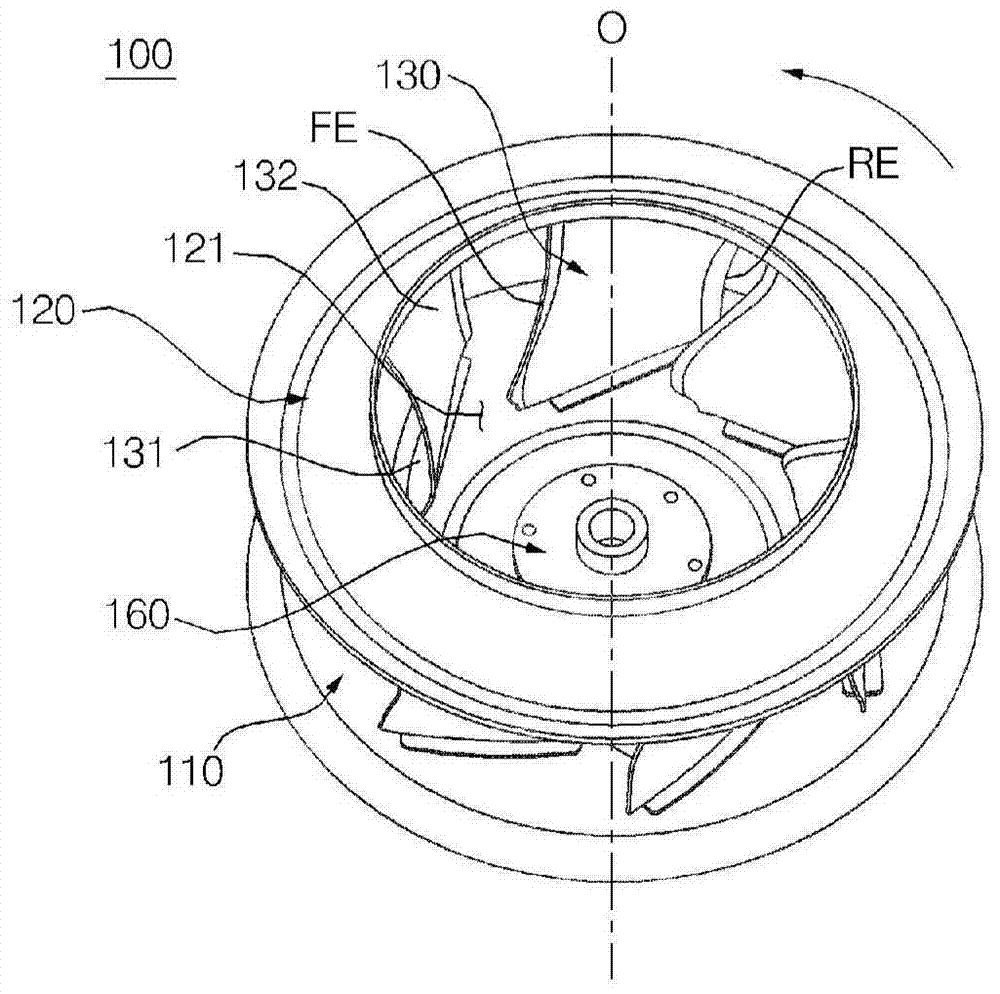
本发明涉及一种离心风扇的制造方法。
背景技术:离心风扇是将通过护罩(shroud)以轴向流入的空气进行加速,并使其通过叶片(blade)之间以径向吐出的风机。这样的离心风扇可由合成树脂或金属材质所构成,在树脂材质的情况下,具有可通过模塑成型制造出多种形态的叶片的优点,但具有硬度脆弱的缺点。因此,采用于大型产品的离心风扇适合使用金属材质。在这样的金属材质的离心风扇中,特别是叶片在现有技术中以一定的形状切割金属板材,然后将其折叠以形成正压面和负压面,然后将上述正压面和负压面相互接合而形成。例如,日本公开专利2000-45997中揭示有将金属材质的一个板材折叠而形成的叶片。上述专利中通过弯折加工一个板材,以形成截面为翼型(airfoil)的叶片。特别是,上述叶片构成其前缘(1af)对于离心风扇的转轴构成既定的倾斜,后缘(1ab)平行于上述转轴的立体形态,但是如上述专利的图6b所示,上述叶片的与转轴垂直的任意的层(layer)上所取的各翼型具有共同的弧面曲线(camberline)。例如,上述叶片在与主板3接合的下端部的弧面曲线的长度最长,在与护罩接合的上端部的弧面曲线的长度最短,但是,在上述上端部的弧面曲线与在上述下端部的弧面曲线将完全重叠。如上述专利的图7a所示,在将一个金属板材对准用于定义一条弧面曲线的框架5c2并进行弯折加工的情况下,将必然形成这种形态的叶片。如上所述,虽然日本公开专利2000-45997的叶片由金属材质所构成,但是在叶片的形状上存在有一定的限制,使在构成复杂的立体形状,例如,在叶片的上部截面所取的翼型的弧面曲线和在下部截面所取的翼型的弧面曲线处于相互交叉的关系,即,在叶片沿着转轴方向构成扭曲的形状的情况下,存在有很难呈现该形状的问题。
技术实现要素:发明要解决的问题本发明的目的在于提供一种用于制造离心风扇的方法,其能够更加多样地呈现正压面或负压面的形状。并且,本发明的目的在于提供一种用于制造离心风扇的方法,其具有由金属材质的两个构件所构成的叶片。并且,本发明的目的在于提供一种离心风扇的制造方法,其具有以往在金属材质的情况下较难呈现的复杂的立体形状叶片。并且,本发明的目的在于提供一种用于制造离心风扇的方法,其可减少材料费的同时提高硬度。并且,本发明的目的在于提供一种用于制造离心风扇的方法,其与现有技术相比可适用于大型产品。并且,本发明的目的在于提供一种用于制造离心风扇的方法,其具有正压面和负压面由具有相互不同倾向的曲面所构成的叶片。并且,本发明的目的在于提供一种用于制造离心风扇的方法,其通过改善叶片的形状以减小流动阻力,特别是改善风机的效率。并且,本发明的目的在于提供一种能够将立体形状的叶片容易地结合于护罩或主板的方法。并且,本发明的目的在于提供一种用于制造离心风扇的方法,其使构件之间的焊接痕最小化以抑制流动阻力的增大,并使焊接痕所致的对风机的平衡构成的影响最小化。用于解决问题的手段本发明的离心风扇的制造方法,其包括:步骤(a),通过裁剪金属板材,来形成分别构成正压面和负压面的正压面形成构件及负压面形成构件;步骤(b),通过分别加压所述正压面形成构件和负压面形成构件,来形成构成所述正压面的第一曲面部和构成所述负压面的第二曲面部;步骤(c),通过修剪形成有所述第一曲面部的正压面形成构件和形成有所述第二曲面部的负压面形成构件,来形成护罩接合面部及主板接合面部;步骤(d),挠曲所述护罩接合面部和所述主板接合面部;步骤(e),将所述正压面形成构件和负压面形成构件接合;步骤(f),在所述正压面形成构件和负压面形成构件接合的状态下,接合所述护罩接合面部和所述护罩,接合所述主板接合面部和所述主板。所述第一曲面部和所述第二曲面部构成相互不同形状的曲面。在所述步骤(c)中,通过对所述正压面形成构件的上端部和下端部以及所述负压面形成构件的上端部和下端部分别进行修剪,来使修剪后的所述正压面形成构件的上端部和下端部在所述步骤(d)中相对于所述正压面形成构件而能够独立地挠曲,并且使修剪后的所述负压面形成构件的上端部和下端部在所述步骤(d)中相对于所述负压面形成构件而能够独立地挠曲。所述步骤(e)包括:将所述正压面形成构件和所述负压面形成构件的前端部相互接合的步骤;以及将所述正压面形成构件和所述负压面形成构件的后端部相互接合的步骤。通过电阻焊接来进行所述各形成构件的前端部之间的接合及后端部之间的接合中的至少一个。在所述各形成构件的前端部或后端部相互对接的状态下,在从所述护罩侧到所述主板侧形成一列的多个点上进行所述电阻焊接。所述电阻焊接是点焊接。所述电阻焊接是凸焊接,本发明的方法还可包括形成突起的步骤,在该步骤中,在所述正压面形成构件及所述负压面形成构件中的一个面上,形成朝向另一个面突出的突起的步骤。所述形成突起的步骤包括:在所述正压面形成构件及所述负压面形成构件中的一个构件中,在所述前端部及所述后端部中的至少一个端部的从所述护罩侧到所述主板侧形成一列的多个点上形成所述突起的步骤。所述步骤(e)包括:将所有的所述多个突起同时一起进行熔融的步骤。本发明的方法还可包括:在所述护罩接合部及所述主板接合部中的至少一个加工出铆钉槽的步骤;所述步骤(f)包括:通过将铆钉耦接于所述铆钉槽,来使所述护罩接合部及所述主板接合部中的至少一个与所述护罩或主板进行结合的步骤。所述步骤(f)包括:在耦接了所述铆钉的状态下,将所述护罩接合部或所述主板接合部分别与所述护罩或所述主板进行接合的步骤。所述护罩接合部和所述护罩之间的接合或者所述主板接合部和所述主板间的接合通过电阻焊接来实现。所述电阻焊接是在从所述各形成构件的前端侧到后端侧形成一列的多个点上进行的点焊接。本发明的方法还可包括:在所述步骤(d)之后再实施所述步骤(b)的步骤。发明效果本发明的离心风扇的制造方法,其与由树脂材所构成的现有技术的离心风扇相比具有更高的硬度,并通过立体的叶片形状能够提高风机的性能。并且,将金属材质的薄的两张板材分别进行加工并接合,从而能够制造出以往较难实现的复杂的形状的叶片。并且,由两张板材所构成的叶片与现有的方式相比,其所需的材料费要少,并且重量轻而增大风机的效率,从而能够节省消耗电力。并且,由于将两个构件分别加工成曲面后进行接合而形成叶片,由各个构件所呈现的曲面的形状对于彼此相互独立,因而能够形成复杂的立体形状的叶片(例如,正压面和负压面由具有相互不同的倾向的形态的曲面所构成)。并且,由于利用金属材料可形成复杂的形状的叶片,能够减小流动阻力,并改善风机的性能特别是效率。并且,能够将具有立体的表面的叶片容易地结合于护罩或主板。并且,能够使构件间的焊接痕最小化,从而能够抑制流动阻力的增大,并使焊接痕所致的对风机的平衡构成的不良影响最小化。并且,由于构成叶片的构件间的接合部或结合部不存在于正压面或负压面上,能够减小流动阻力。并且,在塑性加工的特性上,能够增大叶片的强度并减小韧性。附图说明图1是示出了作为可采用离心风扇的一个例子的无蜗壳风机模块的图。图2是示出了本发明的一实施例的离心风扇的立体图。图3是示出了图2的离心风扇的分解立体图。图4的(a)部分是在叶片上标示出层的位置,图4的(b)部分是在叶片上标示出由层所取的截面。图5是示出了将图4所示的截面以转轴方向投影到一个平面上的图。图6是示出了横向剖开叶片的图。图7是示出了本发明的一实施例的离心风扇的制造方法的流程图。图8是示出了本发明的另一实施例的离心风扇的制造方法的流程图。图9a至图9i是依次示出了通过本发明的实施例制造离心风扇的过程的图。具体实施方式通过参照与所附的附图一起详细进行后述的实施例,将能够明确本发明的优点、特征及用于实现其的方法。但是,本发明并不限定于以下所揭示的实施例,而是可由相互不同的多种形态来实施,本实施例仅是为了更加完整地揭示本发明,以向本发明所属的技术领域的一般技术人员完整地提示出本发明的范围而提供,本发明仅由权利要求书的范围而进行限定。在整个说明书中,相同的附图标记表示相同的结构要素。图1是作为采用离心风扇的一个例子所示出的无蜗壳风机模块。以下说明的实施例的离心风扇可主要适用于冰箱、空调机、吸尘器等。由于空气自然地流入到风机的内部并向外部吐出,在没有风道的情况下也可进行设置,特别是,可适用于图1所示的无蜗壳(plug)型风机模块,其适用于设置于室外且将从室内流入的空气进行冷却或加热并再向室内供给的空调机。这样的风机模块1包括:具有转轴的电机2;用于支撑电机2的支撑框架3;结合于电机2的转轴的离心风扇4。并且,在支撑框架3的前面设置的前面板5形成有开口部,以使空气可流入到离心风扇4,通过上述开口部沿着转轴方向所流入的空气,其随着离心风扇4进行旋转,在前面板5背面的区域以放射状进行吐出。图2是示出了本发明的一实施例的离心风扇的立体图。图3是示出了图2的离心风扇的分解立体图。图4的(a)部分是在叶片上标示出层的位置,图4的(b)部分是在叶片上标示出由层所取的截面。图5是示出了将图4所示的截面以转轴方向投影到一个平面上的图。图6是示出了以横向剖开叶片的图。参照图2至图6,本发明的一实施例的离心风扇100包括主板110、护罩120、多个叶片130。主板110、护罩120及叶片130的材质由具有可塑性的金属材构成,优选地由钢(steel)所形成。主板110借助电机4(参照图1)来以转轴O(rotatingaxis)为中心进行旋转。根据不同的实施例,主板110也可与电机的转轴直接结合,并且,离心风扇100还可包括套节(hub)160,其用于将主板110与电机的转轴(rotatingshaft)结合。护罩120与主板110被隔开地进行配置,并形成有使空气以转轴O方向流入的吸入口121。护罩120以在中央形成有吸入口121的环形状所构成,从形成有吸入口121的内周以径向逐渐地扩展,并在由叶片130所压送的气流吐出的外周具有最大直径。护罩120的用于导向空气的内侧面可构成朝向主板110突出地弯曲的曲面。叶片130在主板110和护罩120之间沿着圆周方向配置有多个。通过护罩120的吸入口121吸入的空气从叶片130的前端部流动到后端部并吐出。离心风扇100可具有七个叶片130,但是并不限定于此。主板110可包括:叶片支撑板部111,其用于支撑叶片130的下端部;套节安装部112,其在中央从叶片支撑板部111朝向护罩120隆起。套节安装部112从叶片支撑板部111以具有既定的曲率而延伸。在套节安装部112的中央形成有开口的安装孔110a,以可安装与电机的转轴结合的套节(未图示),在套节安装部112沿着安装孔110a的外围形成有多个第一耦接孔110b,其沿着圆周方向以一定的间隔形成。通过第一耦接孔110b耦接螺丝、螺栓或螺钉等耦接构件,从而可固定上述套节。参照图3至图4,以下,在叶片130中,将与精油护罩120吸入的气流开始接触的部分定义为是前端FE(FrontEdge),将气流从叶片130分离的部分定义为是后端RE(RearEdge)。当采取与转轴O垂直的任意的层(或平面)时,在上述层上呈现的叶片130的截面中,前端FE位于既定的共同的内周上,后端RE位于具有比上述内周大的直径的既定的共同的外周上。在将叶片130中朝向离心风扇100的外侧的面称为正压面131,将位于正压面131的相反侧的朝向离心风扇100的内侧的面称为负压面132的情况下,与后端RE相比,叶片130的前端FE位于正压面131所面向的方向(或是离心风扇100的先转方向)侧。叶片130包括:用于形成正压面131(参照图2)的正压面形成构件140;用于形成负压面132(参照图2)的负压面形成构件150。正压面形成构件140和负压面形成构件150可在两者之间构成空间S而结合。优选地,正压面131的全部区域由正压面形成构件140所规定,负压面132的全部区域由负压面形成构件150所规定。正压面形成构件140和负压面形成构件150可通过加工金属板材而形成。优选地,正压面形成构件140(或是负压面形成构件150)通过加工具有均匀的厚度的金属板材而形成。特别是,正压面形成构件140或负压面形成构件150只要其厚度达到大约1mm左右即可具有充分的硬度,这与利用现有技术的金属板材而形成的叶片的厚度达到2mm以上的情况相比,其厚度减小了1/2以上。更详细说,正压面形成构件140和负压面形成构件150可通过将可塑性的金属板材进行加压成型(冲压成型:press)而形成。特别是,钢板材的可塑性较佳而可容易地实现多种形态的成型,同时根据碳C、铬Cr、镍Ni等的含量比而可确保充分的耐蚀性、耐热性、硬度等。特别是,由钢材质所构成的离心风扇具有得到提高的硬度,因此与现有技术的树脂材质相比可以更快的速度进行旋转。现有技术的由树脂材质所构成的离心风扇虽然容易地实现复杂的形状的叶片,但是其硬度较弱,特别是,在大型产品中采用的风机的情况下,叶片受到强机外正压而损坏的危险较高,因此在稳定性方面存在有问题。与此相比,本发明利用由金属材质所构成的两个构件140、150来形成叶片,从而可确保充分的硬度,同时可实现用于改善风机的性能的复杂的形状的叶片。在叶片130的前端部和后端部上,正压面形成构件140和负压面形成构件150可相互进行接合。正压面形成构件140和负压面形成构件150之间的接合可通过各构件的背面间来实现。以下,将在叶片130的前端部实现正压面形成构件140和负压面形成构件150之间的接合的部分称为前端接合部133,在叶片130的后端部实现正压面形成构件140和负压面形成构件150之间的接合的部分称为后端接合部134。并且,叶片130在前端接合部133和后端接合部134之间形成有本体部135,本体部135在内侧具有空间S。特别地,本体部135的截面可构成将空间S包覆的封闭结构。正压面形成构件140在前端部形成有第一前端接合面部141,在后端部形成有第一后端接合面部142,并在第一前端接合面部141和第二后端接合面部142之间形成有第一曲面部145。与之类似地,负压面形成构件150在前端部形成有第二前端接合面部151,在后端部形成有第二后端接合面部152,并在第二前端接合面部151和第二后端接合面部152之间形成有第二曲面部155。在叶片130的前端接合部133实现第一前端接合面部141和第二前端接合面部151之间的接合,在后端接合部134实现第一后端接合面部142和第二后端接合面部152间的接合。优选地,第一前端接合面部141的背面(以下,称为第一前端接合面)和第二前端接合面部151的背面(以下,称为第二前端接合面)可相互进行面接触。第一前端接合面部141和第二前端接合面部151可具有相互对应的形状的接合面。即,通过第一前端接合面和第二前端接合面由实质上相同的形状所构成,能够以相互贴紧的状态进行接合。同样地,第一后端接合面部142的背面(以下,称为第一后端接合面)和第二后端接合面部152的背面(以下,称为第二后端接合面)可相互进行面接触。第一后端接合面部142和第二后端接合面部152可具有相互对应的形状的接合面。即,通过第一后端接合面和第二后端接合面由实质上相同的形状所构成,能够以相互贴紧的状态进行接合。本体部135包括第一曲面部145和第二曲面部155,在第一曲面部145和第二曲面部155之间形成有空间S。空间S的横截面的形状由第一曲面部145的背面和第二曲面部155的背面决定,其上侧由护罩120所限定,其下侧由主板110所限定。在进行接合之前,由于正压面形成构件140和负压面形成构件150彼此相互独立,因而可任意以相互不同的形态自由地进行加工。因此,第一曲面部145和第二曲面部155的形状也可被构成为其曲率以相互不同的倾向进行变化。特别是,由于第一曲面部145和第二曲面部155的形状将分别决定正压面131的形状和负压面132的形状,因而可自由地构成曲面部145、155的形状,其对于提高风机的性能方面将非常有利。特别是,与通过将一个板材折叠而形成正压面和负压面的情况(参照日本公开专利2000-45997)相比,将可形成由更加复杂的曲面所构成的正压面或负压面。在前端接合部133或后端接合部134上,正压面形成构件140和负压面形成构件150之间的接合可由焊接来实现,具体的方式有电阻焊接和激光(raser)焊接。电阻焊接是在母材的焊接位置进行加压后导通电流,以使电阻热的产生被局限于比较小的特定部位的电阻焊接。例如,可以有点焊接(spotwelding)或凸焊接(projectionwelding)。利用焊接棒的焊接将产生因母材和焊接棒熔化所生成的带模样的波形的熔接痕(焊缝:bead),而凸焊接或点焊接较少形成焊缝,因而对风机的平衡(balancing)所构成的影响甚微。激光焊接虽然相对地费用较高,但是其焊接热输入非常少,热影响范围窄,几乎不留有焊接的痕迹,因此可实现构件间的非常精细的接合。在利用激光焊接来形成叶片130的情况下,可极大地缩减前端接合部133和后端接合部134的面积。叶片130可包括与护罩120连接的护罩连接部136。护罩连接部136可在正压面形成构件140及负压面形成构件150中至少一个的上端部包括弯折的护罩接合面部143、153。优选地,在正压面形成构件140和负压面形成构件150分别形成有第一护罩接合面部143和第二护罩接合面部153,并在正压面形成构件140和负压面形成构件150相互接合的状态下,第一护罩接合面部143和第二护罩接合面部153处于以相互相反方向弯折的形态。第一护罩接合面部143和第二护罩接合面部153可通过焊接与护罩120的内周面进行接合。第一护罩接合面部143和第二护罩接合面部153的与护罩120接合的各个接合面(以下,称为第一护罩接合面、第二护罩接合面)优选地被构成为与上述内周面的形状对应的曲面,以可与护罩120的内周面贴紧。叶片130可包括与主板110连接的主板连接部137。主板连接部137可在正压面形成构件140及负压面形成构件150中至少一个的下端部包括弯折的主板接合面部144、154。优选地,在正压面形成构件140和负压面形成构件150分别形成有第一主板接合面部144和第二主板接合面部154,并在正压面形成构件140和负压面形成构件150相互接合的状态下,第一主板接合面部144和第二主板接合面部154处于以相互相反方向弯折的形态。第一主板接合面部144和第二主板接合面部154可通过焊接与主板110进行接合。第一主板接合面部144和第二主板接合面部154的与主板110接合的各个接合面(以下,称为第一主板接合面、第二主板接合面)与主板110贴紧。护罩接合面部143、153和护罩120间的接合或主板接合面部144、154和主板110的接合可通过焊接来实现,具体的方式可举出电阻焊接和激光焊接。对于电阻焊接和激光焊接已进行了说明,在此将省略进一步的说明。参照图4至图6,叶片130可具有3D形状。以下定义为:在3D形状的叶片中,当将由与转轴O垂直的既定的平面所构成的既定的层(layer)上的叶片的截面以转轴O方向投影于既定的投影面上时,在上述投影面上连接上述各截面的前端FE和后端RE的线中两个以上不位于同线上(或是不重叠)。其中,连接上述前端和后端的线按照一定的规则进行定义,例如,可以是用直线连接前端FE和后端RE,与之不同地,可以是连接离正压面131和负压面132位于等距离的点。叶片130的形成有空间S的部分的截面可构成翼型。这样的翼型由本体部135所规定。构成空间S的内周面的截面在整体上为翼型,但是,上述截面的前端可能会具有正压面形成构件140和负压面形成构件150间的接合所致的尖点,因此,将以叶片130的外周面的形状为基准定义“翼型”,并定义前缘LE位于连接正压面形成构件140的外周面和负压面形成构件150的外周面之间的虚拟的曲线上。在附图中,r表示前缘LE的曲率半径,翼型的上部面或下部面的曲率半径在前缘LE具有最小值。以下,对本体部135进行更加详细的说明。本体部135的截面可以是在内侧设有空间S的翼型(airfoil)或流线型。根据NACA(NationalAdvisoryCommitteeforAeronautics,国家航空咨询委员会)所提示出的定义,翼型由前缘LE(leadingedge)、后缘TE(trailingedge)、用于连接上述前缘和后缘的上表面145a(uppersurface)、下表面155a(lowersurface)所构成,并由多种因子来定出其形状。这些因子有作为连接前缘和后缘的直线的弦线(chordline)、连接前缘和后缘之间的离上面和下面位于等距离的点的弧面曲线(camberline)等。图4中示出有与转轴O垂直的四个层。叶片130的截面S(L1)、S(L2)、S(L3)、S(L4)分别是在第一层(Layer1)、第二层(Layer2)、第三层(Layer3)、第四层(Layer4)上所看到的。定义叶片130的形状所需的第一层(Layer1)、第二层(Layer2)、第三层(Layer3)、第四层(Layer4)只需沿着转轴O以从上到下的顺序采取即可。叶片130由第一截面S(L1)和第四截面S(L4)间的相关关系而在整体上构成沿着上下方向扭曲的形状。在日本公开专利2000-45997等中揭示的现有技术的离心风扇的叶片,其截面在护罩侧和主板侧实质上构成相同的形状,从而未能有效地应对从护罩到主板侧的流动的变化倾向。与此相比,本发明的离心风扇100将第一层(Layer1)上的第一截面S(L1)设计为适合于护罩120侧的流动特性,将第四层(Layer4)上的第四截面S(L4)设计为对于第一截面(S(L1))独立地适合于主板110侧的流动特性,从而使风机的性能,特别是效率与现有技术相比极大地得到改善。靠近护罩120的第一截面S(L1)的前端FE(L1)与靠近主板110的第四截面S(L4)相比更远离转轴O,第一截面S(L1)的后端RE(L1)与第四截面S(L4)的后端RE(L4)相比更靠近转轴O。在此情况下,如图9所示,第一截面S(L1)和第四截面S(L4)的弦线将相互交叉。优选地,第一截面S(L1)的弦线除了与第四截面S(L4)以外,还与第二截面S(L2)和第三截面S(L3)的弦线交叉。另外,如图4的(a)部分所示,当从侧面观察叶片130时,叶片130的前端FE或后端RE构成与转轴O具有既定的角度的倾斜,特别地,构成为靠近护罩120的上端部与靠近主板110的下端部相比更远离转轴O的形态。由于越靠近护罩120流速越大,叶片130中越靠近护罩120的部分需要做的功越大。因此,叶片130在其至少一部分上,越是靠近护罩120的层,在该层上的叶片130的截面构成从转轴O远离的形态,这样的形态在靠近护罩120的层上将增大叶片130的线速度,从而使叶片130在该部分做更大的功。并且,一般来说在靠近护罩120的部分(以下,以第一层(Layer1)为例)上流速较快,因此,流动的惯性(特别是转轴O方向成分)较大,从而在第一层(Layer1)上的叶片截面的后端将产生流动剥离。但是,本实施例的叶片130与现有技术相比,由于第一截面S(L1)的前端FE(L1)的位置变得从转轴O远离,从护罩120的吸入口121到第一截面S(L1)的后端RE(L4)的流动的路径与现有技术相比变得更长,从而能够使流动克服惯性并柔和地导向到后端RE(L4),由此,能够相应地抑制叶片130的后端RE上的流动剥离。并且,叶片130的第一截面S(L1)与第四截面S(L4)相比可更靠近主板110的旋转方向的相反侧。特别是,叶片130的后端RE的至少一部分上,靠近护罩120的上端部与靠近主板110的下端部相比,构成为更偏向于主板110的旋转方向的相反侧。如前所述,即使是叶片130的形态被构成为,越是靠近护罩120的部分(例如,第一截面S(L1)),其与其它部分(例如,第四截面S(L4)相比从转轴O远离的形态,但是在相同的例中,由于第一截面S(L1)的后端RE(L1)与第四截面S(L4)后端RE(L4)相比更远离转轴O,因而与第一截面S(L1)的前端FE(L1)从转轴O远离的距离相比,后端RE(L1)相对地较少远离转轴O,这将实质上产生抑制叶片130的送风直径(从转轴O到叶片130的后端LE最大距离)增大的效果。优选地,第一截面的后端RE(L1)与第四截面的后端RE(L4)相比位于主板110的旋转方向的相反侧,在各截面的后端RE(L1)、RE(L2)、RE(L3)、RE(L4)中,第一截面的后端RE(L1)最位于主板110的旋转方向的相反方向侧,这样的倾向可在叶片130的前端FE也同样如此,特别是,在叶片130的各截面的前端FE(L1)、FE(L2)、FE(L3)、FE(L4)中,上述第一截面的前端FE(L1)最位于主板110的旋转方向的相反侧。另外,第三截面的前端FE(L3)可与第四截面的前端FE(L4)相比位于主板110的旋转方向侧。这样的倾向可在后端RE也同样如此,在此情况下,叶片130的第三截面的后端RE(L3)与第四截面的后端RE(L4)相比位于主板110的旋转方向侧。图7是示出本发明的一实施例的离心风扇的制造方法的流程图。图8是示出本发明的另一实施例的离心风扇的制造方法的流程图。图9a至图9i是依次地示出通过本发明的实施例制造离心风扇的过程。本发明的离心风扇的制造方法包括:步骤(a),通过裁剪金属板材,来形成分别构成正压面和负压面的正压面形成构件及负压面形成构件;步骤(b),通过分别加压上述正压面形成构件和负压面形成构件,来形成构成上述正压面的第一曲面部和构成上述负压面的第二曲面部;步骤(c),通过修剪(trimming)形成有上述第一曲面部的正压面形成构件和形成有上述第二曲面部的负压面形成构件,来形成护罩接合面部及主板接合面部;步骤(d),挠曲(bending)上述护罩接合面部和上述主板接合面部;步骤(f),在上述正压面形成构件和负压面形成构件接合的状态下,接合上述护罩接合面部和上述护罩,接合上述主板接合面部和上述主板。参照图7至图9,离心风扇100可通过如下的步骤进行制造。(1)预裁剪金属板材的步骤S10:通过裁剪金属板材210来形成构成正压面131的正压面形成构件140和构成负压面132的负压面形成构件150。上述金属板材是除了切割加工以外,还可适合于加压加工的具有可塑性的材质,其优选为是钢。在此步骤中,与最终的形态相比,以有若干余量的大小进行预裁剪正压面形成构件140和负压面形成构件150。例如,金属板材210可以以图9a中附图标记211所示的一定的形态进行裁剪,被裁剪的形态211在正压面形成构件140的情况下和负压面形成构件150的情况下可相互不同。(2)加压成型曲面部的步骤S20:将步骤S10中预裁剪的金属板材211进行加压,以形成曲面部145、155。曲面部145、155可通过加压成型而形成。在按照所要制作的叶片的形状而设计的上部模具220和下部模具230之间放置金属板材211,并将上部模具220进行加压(参照图9b)。曲面部145、155可形成于金属板材211的一部分区域,在曲面部145、155的前、后分别形成前端接合面部141、151和后端接合面部142、152,虽未图示,还可一同形成护罩接合面部143、153和主板接合面部144、154。特别是,在该步骤中,根据所利用的模具的形态,正压面形成构件140的第一曲面部145和负压面形成构件150的第二曲面部155可构成相互不同形状的曲面。通过加压加工可增强材质的强度并减小韧性。(3)修剪的步骤S30:对于形成有曲面部145、155的金属板材211实施修剪(trimming)作业,以对准最终形状的设计尺寸而在正压面形成构件140和负压面形成构件150分别去除不必要的部分。特别是,在该步骤中在金属板材211的前端部和后端部分别加工出前端接合面部141、151、后端接合面部142、152,在金属板材211的上端部和下端部分别加工出护罩接合面部143、153及/或主板接合面部144、155(步骤S31)。如图9c所示,为了在步骤S40中使接合面部143、153、144、154不与前端接合面部141、151或后端接合面部142、152发生干涉而独立地进行挠曲,可将金属板材211的四个边角切开。并且,步骤S30还可包括步骤S32,其中在护罩接合面部143、153的前端和后端、主板接合面部144、154的前端和后端分别加工出切口185(notch)。由于可以切口185为基准顺畅地挠曲护罩接合面部143、153或主板接合面部144、154,可以正确的形状加工出接合面部143、153、144、154,并由于在挠曲上述接合面部时应力将集中于切口185,相对地可防止曲面部145、155发生变形。(4)挠曲接合面部的步骤S40:在步骤S30中进行修剪的状态下,在正压面形成构件140及负压面形成构件150中的至少一个中,挠曲金属板材211的上端部上形成的护罩接合面部143、153和下端部上形成的主板接合面部144、154(参照图9d)。(5)补偿回弹(springback)的步骤S50:回弹(springback)指的是在塑性材料的挠曲加工中,当挠曲材料后去除压力时,基于要恢复至原状的弹力作用而挠曲量减少的现象。在步骤S40中挠曲护罩接合面部143、153或主板接合面部144、154的过程中,在回弹现象的作用下,包括上述接合面部143、153、144、154在内,特别是在之前步骤中加工出的曲面部145、155或前、后端接合面部141、151、142、152具有要恢复至原状的倾向。作为参考,图9e所示的步骤S50示出了需要加工成如虚线所示的金属板材211,其因回弹而变形为如实线所示。步骤S50是用于补偿因回弹而减少的挠曲量,其中利用模具220、230再次实施定型。步骤S50是以使材质屈服(yield)而在去除外力的情况下也可保持原先加工的形状为目的,其根据材质的变形程度而可反复实施多次。(6)接合正压面形成构件140和负压面形成构件150的步骤S60:将通过之前步骤来完成加工的正压面形成构件140和负压面形成构件150相互进行接合。在正压面形成构件140和负压面形成构件150的各个前端部相互接合前端接合面部141、151,同样地在各个后端部相互接合后端接合面部142、152。在两个构件140、150的前端接合面部141、151间相互对接,后端接合面部142、152间相互对接的状态下,可进行基于焊接的接合。作为前端接合面部141、151间的接合或后端接合面部142、152间的接合方法,在步骤S61中举例出凸焊接,但是并不限定于此,如前所述,还可使用点焊接等其它电阻焊接或是激光焊接。但是,在如步骤S61进行凸焊接的情况下,还可包括在正压面形成构件140或负压面形成构件150上形成用于焊接的突起的步骤A1。在前端接合面部141、151或后端接合面部142、152上,在从护罩120侧到主板110侧形成一列的多个点可形成有突起141a。图9f图示出沿着正压面形成构件140的前端接合面部141以上下方向形成有突起141a,但是并不限定于此,步骤A1只需在步骤S60之前的适当的时点实施即可。另外,步骤S61(参照图9g)的凸焊接可包括将多个突起141a同时一起地进行熔融的步骤。根据实施例,可利用一个电极向多个突起141a接通电流,或是利用多个电极在各突起141a同时一起地接通电流。其具有可缩短接合工艺的效果。在步骤S60中,作为电阻焊接的另一个例子可实施点焊接,在此情况下,与凸焊接同样地可在从护罩120侧到主板110侧形成一列的多个点上实施点焊接。点焊接或凸焊接等电阻焊接,其如图6所示的因母材局限于与电极接触的部位而被熔融,在接合部133、134按一定的间隔形成有由熔融的母材被凝固而形成的痕迹,即熔核133a(Nugget)。这样的熔核133a可在接合部133、134上沿着上下方向进行排列。(7)设置叶片的步骤S70:将通过步骤S60的接合而构成一体的叶片130与主板110和护罩120进行结合。叶片130和主板110间的结合或叶片130和护罩120间的结合可通过电阻焊接或激光焊接来进行。对此的焊接方法将基于前述的说明,在此将被省去。根据实施例,步骤S70可包括叶片定位步骤S71、叶片预组装步骤S72及电阻焊接步骤S73。在叶片定位步骤S71中,叶片130在主板110上定位于预设定的组装位置。在叶片预组装步骤S72中,利用螺栓、螺钉、铆钉等耦接构件预组装叶片130。以下,以利用铆钉171预组装为例进行说明。在步骤S72之前,还可包括在正压面形成构件140及负压面形成构件150中的至少一个中加工出用于设置铆钉的槽172的步骤A2。将铆钉对准槽172而耦接护罩120和护罩接合面部143、153,同样地,可耦接主板110和主板接合面部144、154。如图9h所示,槽172的加工位置在主板接合面部144、154上可以是前端部和后端部的至少两处,在护罩接合面部143、153可以是后端部的至少一处。但是,根据离心风扇100的大小,在护罩接合面部143、153的前端部也可加工出用于铆钉171耦接的槽172。接合面部143、153、144、154和相对物(护罩120或主板110)可在耦接有铆钉171的位置以外的部分上从前端部到后端部隔开既定的间隔而进行点焊接。图9i中图示出铆钉171,护罩接合面部143、153在后端部的两处耦接有铆钉171,在主板接合面部144、154的前端部和后端部分别耦接有铆钉171。但是,铆钉171的设置位置并不限定于此,其位置可根据风机100的大小或护罩120的形状而任意地改变。在步骤S71之后,可实施将叶片130与护罩120或主板110接合的步骤,可举出的接合方法有电阻焊接或激光焊接。在步骤S72中,作为电阻焊接的一个例子,通过点焊接将叶片130与护罩120及主板110进行接合。点焊接可在护罩接合面部143、153或主板接合面部144、154上,从前端部到后端部的多个地点进行。点焊接在母材上留有从表面凹陷的形态的焊接痕,在点焊接的特性上,这样的焊接痕形成于非常局限的范围内,其对流动的阻力少,并且也不会增大母材的重量,因此,几乎不会对风机的平衡构成不良影响。(8)后处理步骤S80:对主板110、护罩120及叶片130的组装完成的离心风扇100的表面进行后处理。可在表面涂覆涂料,在此情况下,通过涂料层可提高耐蚀性,并使构件间的结合部位得以密封。