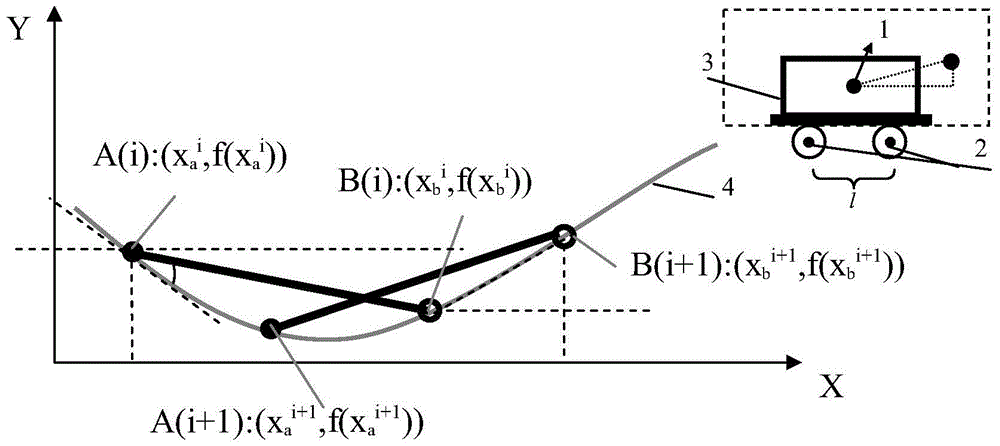
本发明涉及道路交通领域中各类公路、铁路、桥梁和隧道等工程结构表面线形检测方法,具体涉及一种基于刚性载体运行轨迹解析算法的线形检测方法及装置。
背景技术:公路、铁路路基的变形监测,桥梁和隧道的变形监测对于保证交通工程的结构安全至关重要。公路、铁路中软土地路基很容易发生沉降、错差等变形问题。普通的检测手段无法满足高精度的长距离引测。桥梁结构在外力作用下会产生变形,而各种病害如裂缝、预应力损失等最终也导致桥梁线形发生变化,线形位移是判断桥梁安全的最重要而且直观的参考指标。隧道在长期的运营及使用过程中,最关心的安全问题就是防止隧道坍塌,及时快速把握隧道沿线走向及围岩条件较差区域的环向变形是确保隧道运营安全的重要工作。道路交通领域的变形监测对精度要求必须符合相应的国家评定标准。例如对于目前常见的斜拉索桥中,如果主跨分别为钢箱架加劲梁,预应力混凝土梁和钢桁架加劲梁,跨中挠度最大允许变形为跨径的1/400,1/500和1/800。如果跨径为500m,则上述桥梁跨中挠度最大允许值分别为1.25m,1m和0.625m。然而每年观测数据显示,对于有下挠变形趋势的大型桥梁主跨跨中下挠每年只有2-3毫米,中小型桥梁跨中下挠甚至只有1-2毫米。据此,对线形测量系统的精度要求在毫米量级。公路、铁路、桥梁和隧道线形检测常规方法主要采用光学仪器通过建立水准控制网进行测量,长期监测主要采用连通管测试系统、激光测量系统、光电图像式测量系统以及GPS法等新型测试方法。水准控制网的建立工程复杂,耗时长,受环境影响较大。连通管测试系统通过测量各测点与基准点的液面压力差来得到各测点的挠度值。不仅需要预铺水管,而且在使用过程中存在着响应时间慢,施工及维护成本高等缺点。激光测量系统和光电图像式测量系统主要是通过光学系统捕捉光斑或成像的位置变化得出光源的相对位置变化。这两种测量系统都必须在桥上安装固定设备作为参考点,当设备移动后无法获得最初的测量基准状态,无法满足长期测量要求,而且不同气候条件对测量有影响。GPS技术接收导航卫星的载波相位差分数据实时测定站点的三维坐标,是一种新型的实时测量技术。GPS受外界大气影响小,可以在暴风雨中进行监测,可以实现三维坐标的自动监测。然而该技术存在着垂直高程精度较差、无法达到毫米精度的缺点,且成本高,无法大规模开展应用。此外进行多点精确测量方式时,要求每点静止测试时间较长,测试慢。上述技术除了存在各自不同的应用局限外,还由于通过为数不多的测点来拟合检测对象的挠度线形,因此均存在线形不连续的问题。既有专利(公开号:CN201210116750.6)中,提出了采用光纤陀螺线形测量系统测量桥梁的线形和刚性曲线的方法,并且提到了多种减小误差的方法,但是该专利仅采用对数据的分析达到减小误差的目的。既有专利(申请号:CN201210455343.8)中,提出了一种动态校正方法,该方法对测试系统中的光纤陀螺施加预先定义的角速度交变调制信号,通过将包含调制信号的角速度数据与预先定义的角速度调制信号数据进行对比,得到修正系数,并未考虑载体运动的方向与实际待测工程结构表面之间的关系。既有专利(申请号:CN201210455270.2)中,提出了一种静态校正方法,该方法在被测路段放置静态标定桥,通过系统测得标定桥的桥高与实际桥高进行对比,得到纵坐标修正系数,利用该系数修正整体线形曲线,并未提到载体本身结构尺寸大小对待测工程结构表面曲线测量是有影响的,当载体不能视为质点时,此方法会带来较大误差。
技术实现要素:本发明要解决的技术问题是:提供一种基于刚性载体运行轨迹解析算法的线形检测方法及装置,能够提高整体线形检测精度。本发明为解决上述技术问题所采取的技术方案为:一种基于刚性载体运行轨迹解析算法的线形检测方法,其特征在于:它包括以下步骤:S1、将一个刚性轮式检测车沿着待测工程结构表面运行,实时检测刚性轮式检测车的倾斜角度θi、前轮运行路程Δsb和后轮运行路程Δsa;S2、定义前轮和后轮与待测工程结构表面的接触点分别为B点和A点,B点和A点之间的距离为l,视刚性轮式检测车的运动方向与B、A两点的连线成割线关系,定义γi为刚性轮式检测车的倾斜角度从开始到i-1时刻夹角的积分;B点和A点的运行轨迹解析算法如下:①,②,③,④,其中C1、C2为中间变量,⑤,⑥,⑦,式中为i时刻A、B两点坐标;为i+1时刻A、B两点坐标;θi为i时刻的AB连线和i+1时刻的AB连线之间的夹角;S3、视刚性轮式检测车与待测工程结构表面的接触点的运动轨迹无限逼近待测工程结构表面线形,即得到待测工程结构表面线形。一种用于实现上述基于刚性载体运行轨迹解析算法的线形检测方法的检测装置,其特征在于:它包括一个刚性轮式检测车,刚性轮式检测车下方设置前轮和后轮,前轮与后轮之间的距离为定值,在刚性轮式检测车上设有角度传感器,前轮和后轮分别设有里程仪。按上述装置,所述的里程仪为光电编码器。按上述装置,所述的角度传感器为光纤陀螺。本发明的有益效果为:以前轮和后轮与待测工程结构表面的接触点的运动来无限逼近待测工程结构表面线形,更好地把握了刚性轮式检测车与待测曲线的位置关系;客观采用了割线AB倾斜角的变化决定角度传感器的输出,无需考虑割线AB是否能近似为切线的问题,更能够真实的反映待测工程结构表面的二维曲线,尤其是在测量小尺寸的待测工程结构时,与待测工程结构尺寸相比,刚性轮式检测车前后轮的间距不可忽略,刚性轮式检测车不可被近似为质点,本发明方法更能准确地描述待测工程结构表面线形。附图说明图1是本发明一实施例的方法流程图;图2是本发明涉及到的刚性轮式检测车的线形检测图;图3是用于检验运动轨迹解析算法的一个梯形钢制模型线形曲线;图4是采用通用算法所测得的结构表面线形曲线与基准线形的比较;图5是采用本发明方法推演出的结构表面线形曲线与基准线形的比较;图中:1-角度传感器,2-前、后轮里程仪,3-刚性轮式检测车,4-待测工程结构表面线形曲线。具体实施方式下面结合具体实例对本发明做进一步说明。一种基于刚性载体运行轨迹解析算法的线形检测方法,如图1所示,包括以下步骤:S1、将一个刚性轮式检测车沿着待测工程结构表面运行,实时检测刚性轮式检测车的倾斜角度θi、前轮运行路程Δsb和后轮运行路程Δsa;S2、定义前轮和后轮与待测工程结构表面的接触点分别为B点和A点,B点和A点之间的距离为l,视刚性轮式检测车的运动方向与B、A两点的连线分别成割线关系,定义γi为刚性轮式检测车的倾斜角度从开始到i-1时刻夹角的积分;B点和A点的运行轨迹解析算法如下:①,②,③,④,其中C1、C2为中间变量,⑤,⑥,⑦,式中为i时刻A、B两点坐标;为i+1时刻A、B两点坐标;θi为i时刻的AB连线和i+1时刻的AB连线之间的夹角;S3、视刚性轮式检测车与待测工程结构表面的接触点的运动轨迹无限逼近待测工程结构表面线形,即得到待测工程结构表面线形。用于实现上述线形检测方法的检测装置,如图2所示,包括一个刚性轮式检测车3,刚性轮式检测车3下方设置前轮和后轮,前轮与后轮之间的距离为定值,在刚性轮式检测车上设有角度传感器1(本实施例中为光纤陀螺),前轮和后轮分别设有里程仪2(本实施例中为光电编码器)。为了对比本发明的优点,选取一个梯形钢制模型,采用传统水准测量方法测得的线形曲线为f(x),如图3所示;将刚性轮式检测车近似为一个质点,采用通用算法测得的线形曲线与基准线形f(x)进行对比,如图4所示;采用本发明方法,视刚性轮式检测车运动方向与工程结构表面接触点间成割线关系,所推演的线形曲线与基准线形f(x)的比较如图5所示。综合比较图4和图5,可见本发明方法拥有更高的准确度。以上实施例仅用于说明本发明的计算思想和特点,其目的在于使本领域内的技术人员能够了解本发明的内容并据以实施,本发明的保护范围不限于上述实施例。所以,凡依据本发明所揭示的原理、设计思路所作的等同变化或修饰,均在本发明的保护范围之内。