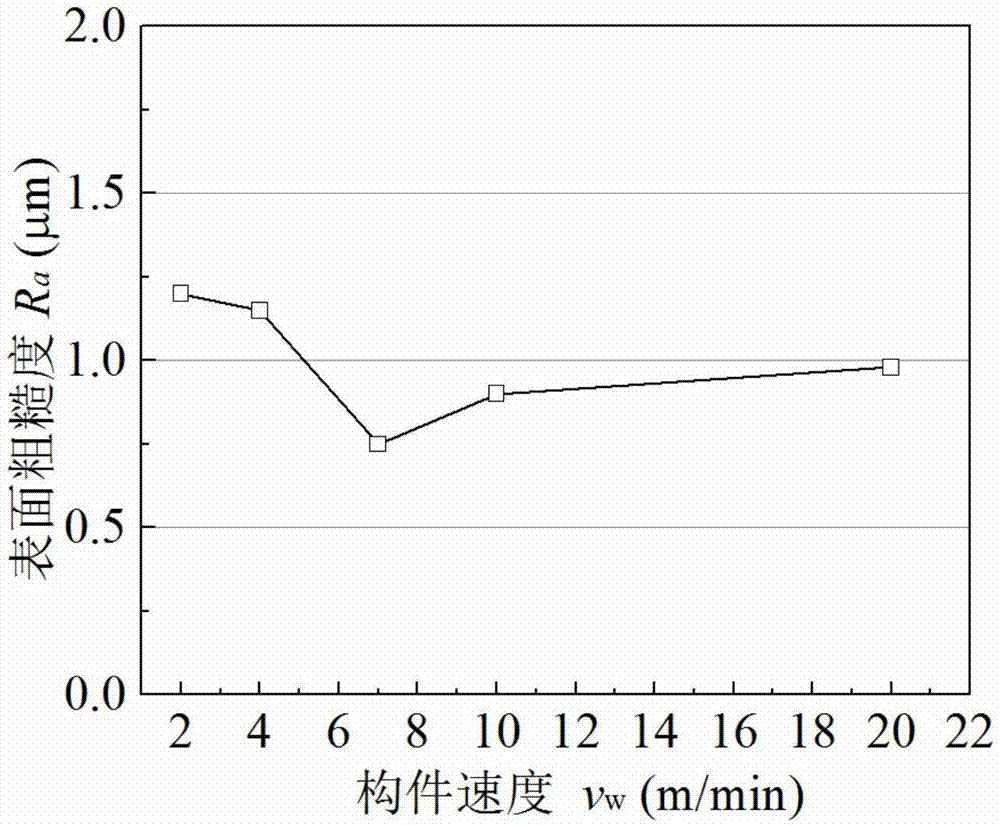
本发明属于金属材料机械加工
技术领域:
,具体涉及到一种超高强度钢构件抗疲劳磨削工艺参数域的获得方法。
背景技术:
:超高强度钢具有超细化、超洁净、超均质的组织和成分的特征,以及超高强度和超高韧性的特点。Aermet100作为一种二次硬化超高强度钢,具有突出的综合性能:高强度、高硬度、高断裂韧性和延展性、优良的抗疲劳性能和抗应力腐蚀性能,因其优良的综合性能受到国内外研究学者的关注。目前已被用做美国F-22战斗机的起落架材料以及RAH-66上的一些要求防弹性好的结构材料。由于具有良好的综合性能,所以Aeremt100钢在航空航天领域应用广泛,例如飞机起落架、气体涡轮发动机主轴和涡轮轴、火箭发动机壳体、高压容器、手机框架、齿轮和抗疲劳螺栓等强力结构件。磨削是一种应用非常广泛的切削加工方法,常被用作精加工工艺。航空工业产品大多对加工精度、疲劳寿命、服役性能有较高要求,尤其是核心承力部件。加工表面完整性对构件的疲劳寿命和服役性能具有重要的影响。然而Aermet100具有高强度和高硬度的特性,在磨削过程中的滑擦、耕犁以及切削中的变形抗力更大,磨削温度更高,磨削时易出现裂纹且磨削后表面残余拉应力较大,裂纹是引起构件疲劳断裂的致命缺陷,而较大的残余拉应力会降低构件的使用寿命。表面完整性是构件加工中很重要的评价指标,主要包括表面粗糙度、表面形貌、表面应力集中系数、表面显微硬度和表面残余应力等,对构件的耐磨性能、疲劳性能、应力腐蚀性能等具有重要的决定作用。因此在超高强度钢Aermet100磨削过程中,必须重视对表面完整性的控制。针对现有超高强度钢Aermet100的磨削特点,在金属材料机械加工
技术领域:
,提出一种超高强度钢Aermet100构件抗疲劳磨削工艺参数域的获得方法,实现对超高强度钢Aermet100构件磨削表面完整性的控制,提高构件的疲劳性能,以满足航空构件高可靠和长寿命的要求。技术实现要素:本发明的目的是提供一种超高强度钢构件抗疲劳磨削工艺参数域的获得方法,以解决现有技术中超高强度钢构件磨削过程存在表面完整性差和疲劳性能低的问题。本发明采用以下技术方案,一种超高强度钢构件抗疲劳磨削工艺参数域的获得方法,包括以下步骤:步骤一、建立超高强度钢构件磨削工艺参数域C1,根据C1加工出多个第一试验构件,建立磨削工艺参数与表面粗糙度关系曲线,得出超高强度钢构件磨削工艺参数域C2;步骤二、根据步骤一中的C2进行正交试验,加工出多个第二试验构件,并建立第一关系式:其中,Ra为表面粗糙度,HV为表面显微硬度,σr为表面残余应力,vs为砂轮速度,vw为构件速度,af为纵向进给,ap为径向进给,a0、a1、a2、a3、a4、b0、b1、b2、b3、b4、c0、c1、c2、c3、c4均为常数;步骤三、根据步骤一中C2加工得出多组第三试验构件,测量出多组表面粗糙度值、表面显微硬度值、表面残余应力值和疲劳寿命值,并建立第二关系式;步骤四、根据步骤二中的第一关系式和步骤三中的第二关系式,获得超高强度钢构件抗疲劳磨削工艺参数域C3。进一步地,第二关系式具体为:其中,Nf为疲劳寿命值,d0、d1、d2、d3均为常数。进一步地,步骤一中得出磨削工艺参数与表面粗糙度关系曲线的具体方法如下:步骤1.1、通过单因素试验法,根据C1设置多组参数值,并采用外圆磨床对初始构件进行加工,获得对应多个第一试验构件;步骤1.2、采用表面粗糙度测试仪对每个第一试验构件进行表面粗糙度测试,测试方向为沿第一试验构件的轴向,并记录测试结果;步骤1.3、根据步骤1.2记录的测试结果,绘制磨削工艺参数与表面粗糙度关系曲线。进一步地,步骤一中得出超高强度钢构件磨削工艺参数域C2的具体方法为:以低表面粗糙度为约束,设置表面粗糙度约束值,并在每个参数与表面粗糙度关系曲线中,选取小于表面粗糙度约束值对应的参数范围,得出超高强度钢构件磨削工艺参数域C2。进一步地,步骤二的具体方法为:步骤2.1、根据参数域C2采用正交试验方法,选取多组参数,在外圆磨床上加工出与每组参数对应第二试验构件;步骤2.2、通过表面粗糙度仪测量每个第二试验构件的表面粗糙度值;步骤2.3、通过数字显微硬度计测量每个第二试验构件的表面显微硬度值;步骤2.4、通过残余应力测试分析系统测试每个第二试验构件的表面残余应力值;步骤2.5、采用多元线性回归方法对步骤2.1中的多组参数和步骤2.2、步骤2.3、步骤2.4中表面粗糙度值、表面显微硬度值、表面残余应力值进行拟合,并建立第一关系式。进一步地,步骤三具体方法为:步骤3.1、根据C2,设计多组参数,并根据每组参数加工出第三疲劳构件;步骤3.2、根据步骤2.2、步骤2.3和步骤2.4中的方法,分别测量步骤3.1中每个第三疲劳构件的表面粗糙度值、表面显微硬度值和表面残余应力值,测量位置位于第三疲劳构件的中间圆弧段;步骤3.3、分别计算步骤3.2中每组疲劳构件表面粗糙度、表面显微硬度和表面残余应力的平均值;步骤3.4、采用旋转弯曲疲劳试验机对步骤3.1中的每个第三疲劳构件进行旋转弯曲疲劳寿命试验,并计算出每一组第三疲劳构件疲劳寿命值的平均值;步骤3.5、采用多元线性回归方法对步骤3.3中的表面粗糙度值平均值、表面显微硬度值平均值和表面残余应力值平均值,以及步骤3.4中的多组第三疲劳构件的疲劳寿命值平均值,进行拟合,并建立第二关系式。进一步地,步骤3.1中疲劳构件加工的具体方法为:步骤3.1.1、采用慢走丝电火花线切割切出圆棒试样,直径余量为3mm,轴向余量3mm;步骤3.1.2、采用数控车削加工外形尺寸,直径方向余量大于或等于0.5mm;步骤3.1.3、根据C2,设计多组参数,加工出多组第三疲劳构件。进一步地,步骤四的具体方法为:步骤4.1、根据第二关系式确定构件疲劳寿命值增大时,表面粗糙度值、表面显微硬度值和表面残余应力值的变化方向和范围;步骤4.2、在C2范围内,根据第一关系式和步骤4.1中得出的变化方向和范围,获得超高强度钢构件抗疲劳磨削工艺参数域C3。本发明的有益效果是:通过建立磨削工艺参数与表面完整性特征的关系,以及表面完整性特征与疲劳寿命的关系,以高疲劳寿命为目标,获得了保证一定疲劳寿命条件下的抗疲劳磨削工艺参数域;该发明采用单因素法和正交法进行试验设计,采用多元线性回归分析进行模型求解,设计和分析方法可靠,建立的关系模型较为精确,本发明获得的磨削工艺参数与现有磨削工艺参数相比,构件的表面粗糙度由Ra2.0μm提高到Ra0.45μm,表面显微硬度>500HV,表面残余压应力<350MPa,疲劳极限由905MPa提高到952MPa。【附图说明】图1为本发明中砂轮速度对超高强度钢Aermet100构件表面粗糙度的影响曲线图;图2为本发明中构件速度对超高强度钢Aermet100构件表面粗糙度的影响曲线图;图3为本发明中径向进给对超高强度钢Aermet100构件表面粗糙度的影响曲线图;图4为本发明中纵向进给对超高强度钢Aermet100构件表面粗糙度的影响曲线图;图5为本发明中的超高强度钢Aermet100疲劳构件结构示意图;图6为本发明中超高强度钢Aermet100抗疲劳磨削工艺参数与现有磨削工艺参数获得的S-N曲线对比图。【具体实施方式】下面结合附图和具体实施方式对本发明进行详细说明。本发明公开了一种超高强度钢构件抗疲劳磨削工艺参数域的获得方法,包括以下步骤:步骤一、根据航空制造工程手册、经验或文献资料,建立超高强度钢Aermet100构件的磨削工艺参数域C1,其中超高强度钢Aermet100磨削工艺参数域C1包括砂轮速度vs(单位为m/s)、构件速度vw(单位为m/min)、纵向进给af(单位为mm/r)、径向进给ap(单位为mm),即C1[vs,vw,af,ap],其具体参数参见表1:表1步骤1.1、通过单因素试验法,根据超高强度钢Aermet100构件的磨削工艺参数域C1设置多组参数值,参数值的选择参见表2,并采用外圆磨床对初始构件进行加工,初始构件尺寸优选为Φ30mm×100mm,加工并获得对应多个第一试验构件,外圆磨床优选的采用MMB1420型号;试验中,砂轮采用表1中的单晶刚玉砂轮,在试验中采用乳化液进行冷却;每组参数加工一个第一试验构件,表2中对应有20组参数,即加工20个第一试验构件;序号vs(m/s)vw(m/min)af(mm/r)ap(mm)11071.30.01521571.30.01532071.30.01542571.30.01553071.30.01562021.30.01572041.30.01582071.30.015920101.30.0151020201.30.015112070.50.015122071.00.015132071.30.015142071.80.015152073.60.015162071.30.005172071.30.010182071.30.015192071.30.020202071.30.025表2步骤1.2、采用表面粗糙度测试仪对每个第一试验构件进行表面粗糙度测试,优选采用TR240表面粗糙度测试仪,测试方向为沿第一试验构件的轴向,取样长度为0.8mm,评定长度为5.6mm,并记录测试结果;步骤1.3、根据步骤1.2记录的测试结果,绘制各个磨削工艺参数与表面粗糙度Ra关系曲线;如图1所示,即为砂轮速度对表面粗糙度的影响曲线图,如图2所示,即为构件速度对表面粗糙度的影响曲线图,如图3所示,即为纵向进给对表面粗糙度的影响曲线图,如图4所示,即为径向进给对表面粗糙度的影响曲线图;步骤1.4、根据磨削工艺参数与表面粗糙度关系曲线,以低表面粗糙度为约束,设置表面粗糙度约束值,在每个参数与表面粗糙度关系曲线中,选取小于表面粗糙度约束值所对应的参数范围,进一步优选磨削工艺参数域,得出超高强度钢Aermet100构件的磨削工艺参数域C2,如表3所示:工艺参数工艺参数域表面粗糙度约束值变化方向砂轮速度vs(m/s)[20,30]<0.5μm中间趋近构件速度vw(m/min)[5,20.2]<1.0μm中间趋近纵向进给af(mm/r)[0.5,1.5]<0.5μm增大趋势径向进给ap(mm)[0.005,0.020]<1.5μm增大趋势表3步骤二、根据步骤一中的超高强度钢Aermet100构件的磨削工艺参数域C2加工出多个与每组参数对应的第二试验构件,测量出每个第二试验构件的表面粗糙度值、表面显微硬度值和表面残余应力值,并建立第一关系式;其具体方法为:步骤2.1、采用正交试验方法,根据参数域C2选取多组参数,具体参数见表4,序号vs(m/s)vw(m/min)af(mm/r)ap(mm)1205.50.50.00522010.11.00.01032020.21.50.0154255.51.00.01552510.11.50.00562520.20.50.0107305.51.50.01083010.10.50.01593020.21.00.005表4在MMB1420外圆磨床上,加工出对应多个第二试验构件,其中,初始构件尺寸为Φ30mm×100mm,砂轮采用表1所示的砂轮,在试验中采用乳化液进行冷却,每组参数对应加工一个第二试验构件,即共9个第二试验构件;步骤2.2、通过表面粗糙度仪测量每个第二试验构件的表面粗糙度值,优选采用TR240表面粗糙度测试仪,测试方向沿构件的轴向,取样长度为0.8mm,评定长度为5.6mm;步骤2.3、通过数字显微硬度计测量每个第二试验构件的表面显微硬度值,优选采用430SVD数字显微硬度计,试验力0.5kgf,保载时间10s;步骤2.4、通过残余应力测试分析系统测试每个第二试验构件的表面残余应力值,优选采用ProtoLXRDMG2000残余应力测试分析系统,测试方向沿构件的轴向,测试靶材Cr靶,衍射角156.41°,测试电流25mA,测试电压30kV;表面完整性测试结果如表5所示。序号表面粗糙度(μm)表面显微硬度(HV)表面残余应力(MPa)11.18314-541.2021.42248-517.1931.62221-487.9041.35219-520.2751.54217-519.3861.71307-550.6571.34213-565.4081.554284-612.5191.83241-574.91表5步骤2.5、采用多元线性回归方法对步骤2.1,即表4中的多组参数和表5中测量出的表面粗糙度值、表面显微硬度、表面残余应力值进行拟合,并建立第一关系式,即超高强度钢Aermet100构件磨削工艺参数与表面完整性特征的关系式:本实施例中,根据上述具体值可得出具体关系式:其中,Ra为表面粗糙度,HV为表面显微硬度,σr为表面残余应力,vs为砂轮速度,vw为第二构件速度,af为纵向进给,ap为径向进给,a0、a1、a2、a3、a4、b0、b1、b2、b3、b4、c0、c1、c2、c3、c4均为常数。步骤三、根据步骤一中超高强度钢Aermet100构件磨削工艺参数域C2加工得出多组第三试验构件,测量出多组表面粗糙度值、表面显微硬度值、表面残余应力值和疲劳寿命值,并建立第二关系式;其具体方法为:步骤3.1、根据超高强度钢Aermet100构件磨削工艺参数域C2,设计多组参数,并根据每组参数加工出多组第三疲劳构件;步骤3.1.1、采用慢走丝电火花线切割切出圆棒试样,直径余量为3mm,轴向余量3mm;步骤3.1.2、采用数控车削加工外形尺寸,直径方向余量大于或等于0.5mm;步骤3.1.3、根据超高强度钢Aermet100构件磨削工艺参数域C2,设计多组参数,具体参数参见表6,在MMB1420外圆磨床上加工出多组第三疲劳构件,在试验中采用乳化液进行冷却,其中,砂轮采用表1中所示砂轮,以表6中超高强度钢Aermet100构件磨削工艺参数加工剩余尺寸,直至达到如图5所示的疲劳构件图纸要求,每组参数加工构件6件。序号vs(m/s)vw(m/min)af(mm/r)ap(mm)1205.51.00.00522010.11.00.01032020.21.00.0154255.51.00.01052510.11.00.01562520.21.00.0057305.51.00.01583010.11.00.00593020.21.00.010表6步骤3.2、从步骤3.1加工的每一组第三疲劳构件中选出若干个第三疲劳构件,在9组参数,每组6件的疲劳构件中,每组选取3件疲劳构件,根据步骤2.2、步骤2.3和步骤2.4的方法分别测量所选出的第三疲劳构件的表面粗糙度值、表面显微硬度值和表面残余应力值,测量位置位于构件中间圆弧段;步骤3.3、计算出步骤3.2中测量出的每组参数下第三疲劳构件表面粗糙度值、表面显微硬度值和表面残余应力值的平均值,测试结果参见表7;步骤3.4、在室温下,采用旋转弯曲疲劳试验机对步骤3.1中每一组的第三疲劳构件进行旋转弯曲疲劳寿命试验,试验载荷800MPa,频率5000r/min,记录试验结果,并计算出每一组第三疲劳构件疲劳寿命值的平均值,测试结果参见表7;表7步骤3.5、采用多元线性回归方法对表7中的多组表面粗糙度值平均值、表面显微硬度值平均值和表面残余应力值平均值,以及第三疲劳构件疲劳寿命值平均值,进行拟合,并建立第二关系式,即超高强度钢Aermet100构件表面完整性特征与疲劳寿命的关系式:本申请中由上述具体数值可得出:其中,Nf为疲劳寿命,d0、d1、d2、d3均为常数。步骤四、根据步骤二中的第一关系式和步骤三中的第二关系式,获得超高强度钢Aermet100构件抗疲劳磨削工艺参数域C3。其具体方法为:步骤4.1、根据第二关系式确定构件疲劳寿命值增大时,表面粗糙度值、表面显微硬度值和表面残余应力值的变化方向和范围;对比第二关系式中各表面完整性特征的指数大小可知,疲劳寿命对表面粗糙度的变化最为敏感,对表面显微硬度的变化敏感次之,对表面残余应力的变化不敏感,随着表面粗糙度的减小、表面显微硬度和表面残余应力的增大,疲劳寿命呈增大趋势;步骤4.2、在超高强度钢Aermet100构件磨削工艺参数域C2范围内,根据第一关系式和步骤4.1中得出的变化方向和范围,确定超高强度钢Aermet100构件磨削工艺参数的变化方向,即根据Nf增大的方向确定σr、HV、Ra的变化方向及范围,超高强度钢Aermet100构件抗疲劳磨削工艺参数域C3;根据步骤4.1可知首先保证表面粗糙度越小越好,其次保证表面显微硬度越大越好,最后保证表面残余压应力越大越好,结合图1至图4和第一关系式,可知,相对稳定的高疲劳寿命对应的磨削工艺参数变化方向为:砂轮速度vs→30m/s,构件速度vw→8~12m/min,纵向进给af→1.0mm/r,径向进给ap→0.005mm。超高强度钢Aermet100构件抗疲劳磨削工艺参数域C3,如表8所示:工艺参数工艺参数域表面粗糙度表面显微硬度表面残余压应力砂轮速度vs(m/s)[25,30]<0.45μm>550HV<350MPa构件速度vw(m/min)[10.1,20.2]<0.40μm>550HV<250MPa纵向进给af(mm/r)[0.5,1.0]<0.45μm>550HV<250MPa径向进给量ap(mm)[0.005,0.010]<0.42μm>500HV<350MPa表8步骤4.3、采用超高强度钢Aermet100构件抗疲劳磨削工艺参数域C3范围内的参数(vs=30m/s,vw=12m/min,af=1.0mm/r,ap=0.005mm)和现有磨削工艺参数(vs=30m/s,vw=10.1m/min,af=1.8mm/r,ap=0.020mm)分别加工旋转弯曲疲劳构件30件,然后进行疲劳试验,获得对应的S-N曲线,如图6所示。采用抗疲劳磨削工艺参数加工出疲劳构件的疲劳极限(952MPa)比现有磨削工艺参数获得的疲劳极限(905MPa)提高了5.2%,对比疲劳极限结果,验证抗疲劳磨削工艺参数域的准确性。本实施例超高强度钢Aermet100构件抗疲劳磨削工艺参数域的获得方法,其特点为,通过建立磨削工艺参数与表面完整性特征关系式,以及表面完整性特征与疲劳寿命的关系式,以疲劳寿命为判据,在保证低表面粗糙度、高表面显微硬度和高表面残余压应力的条件下,获得了抗疲劳磨削工艺参数域。本发明可用于指导超高强度钢构件抗疲劳磨削工艺参数域的确定,显著提高构件的磨削表面完整性,同时保证了构件的疲劳寿命。当前第1页1 2 3