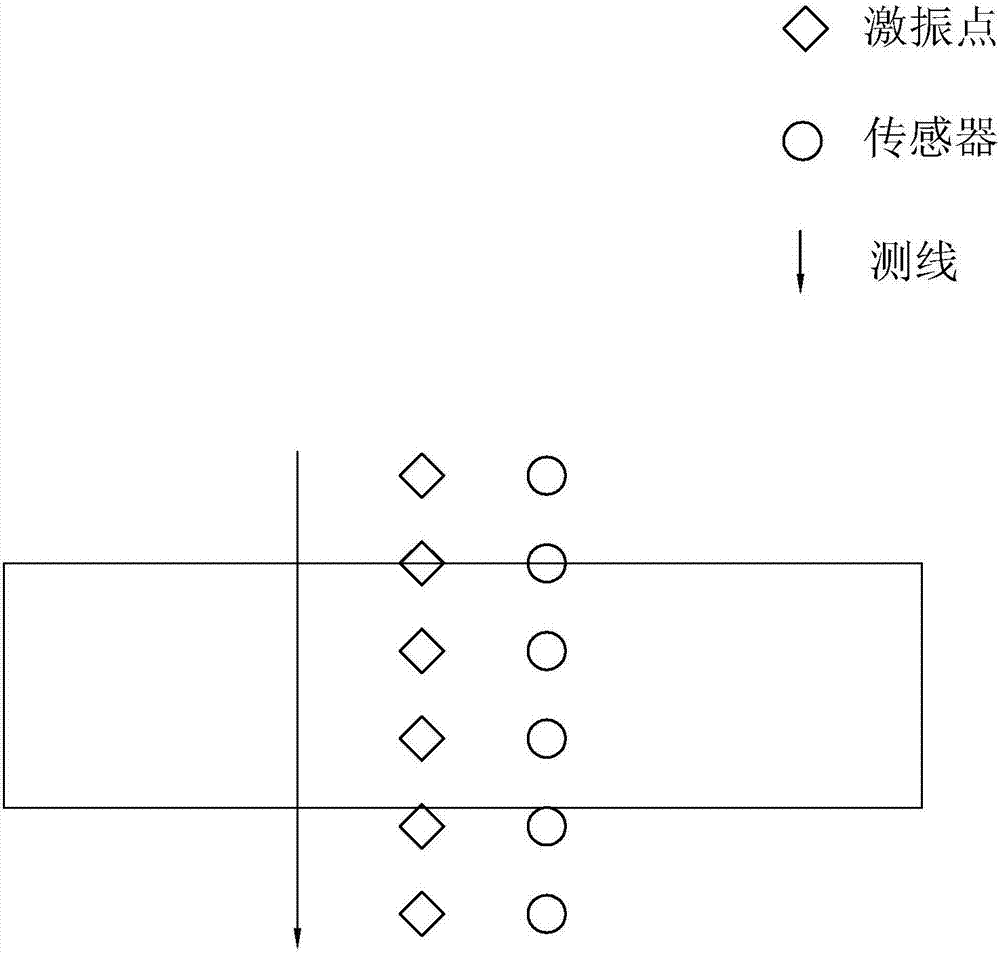
本发明涉及工程建设质量检测
技术领域:
,特别涉及一种灌浆密实度检测方法。
背景技术:
:近年来,随着公路桥梁工程建设的蓬勃发展,预应力混凝土梁被广泛运用到桥梁建设的项目中,而预应力孔道灌浆是后张法预应力混凝土结构的一道非常关键的工序,重要性显著。当预应力孔道中存在灌浆缺陷时,水和空气的进入使得处于高度张拉状态的钢绞线发生腐蚀,造成有效预应力降低,从而极大地影响桥梁的耐久性。严重时,钢绞线会发生断裂,有可能出现突发安全事故。此外,压浆质量缺陷还会导致混凝土应力集中,进而改变梁体的设计受力状态,从而影响桥梁的承载力和使用寿命。因此,对灌浆缺陷的检测成为保证预应力桥梁质量的重要环节.预应力孔道灌浆密实度检测技术的发展与应用也日益引起业内的关注。由于灌浆缺陷的危害性,长期以来,研究人员尝试了多种方法来检测灌浆缺陷。按测试所采用的媒介来分,大致可以分为:1)基于电磁波的检测方法:由于该方法受金属屏蔽,因此不适合于铁皮波纹管;即使是塑料波纹管或者无管状况,也不合适于钢筋密集状况;电磁雷达受钢筋影响大、适用范围窄;2)基于超声波的检测方法:从理论上,利用灌浆缺陷对波速的影响,采用对测的方法可以检测灌浆缺陷,但检测时需要从板的两侧面对测,而且需要耦合,因此作业性差,效率很低;3)基于放射线(x光、γ射线等)的检测方法:该方法的检测精度较高,但测试设备和操作较复杂,需要底片等费用,检测成本高;并且具有放射性,存在安全隐患;4)基于冲击弹性波的检测方法:该方法被认为是最有前途的方法。目前的检测方法中,还未有明确的标准来指导检测的进行,因此测试得到的结果准确度难以得到保证。技术实现要素:本发明的目的是提供一种灌浆密实度检测方法,具有测试结果准确性好的优点。本发明的上述技术目的是通过以下技术方案得以实现的:一种灌浆密实度检测方法,包括如下步骤:定性测试:s1:钢绞线端头的清理:将测试孔道锚头两端的露出钢绞线清理干净,使钢绞线上无覆浆;s2:传感器安装:将传感器分别固定安装在孔道最上的一根或两根钢绞线上,并使传感器的轴线平行于钢绞线方向;s3:激振及接收信号,包括:s3-1:调整放大器,使激振短端的放大倍率低于接收端的放大倍率;s3-2:将激振锤对准安装传感器钢绞线,撞击激振,撞击方向平行于钢绞线的轴向;s4:混凝土波速的测定:选取无孔道且与测试孔道相近高度的部位,将传感器固定在梁的断面上,采用激振锤激振;s5:灌浆密实度分析与评定:采用综合灌浆指数if作为定性检测的评定指标,当灌浆饱满时,if=1;完全未灌时,if=0;综合灌浆指数定义为:if=(iev*ipv*itf)1/3,其中,为根据flea法得到的分项灌浆指数:为根据flpv法得到的分项灌浆指数;为根据pftf法得到的分项灌浆指数;或/和定位测试:a1:孔道定位;a2:传感器安装,包括:a2-1:选择测试点:测试点设于孔道轴线与测试表面的垂直投影面上;在孔道全长等间隔设置测试点,且在如下位置加密测试点:a.进浆口;b.出浆口;c.弯曲孔道的起弯点;d.弯曲孔道的反弯点顶部;e.弯曲孔道的反弯点后部;a2-2:确定检测方向:对于竖向结构,采用水平检测方向;对马蹄形扩幅的t梁腹板孔道,从下部测试;对于其他可以采用上下方向检测的结构,采用上下方向检测;a2-3:传感器的固定方式:采用人工或机械方式将传感器压在测试部位表面;a3:激振及接收信号,包括:a3-1:放大器的选择:放大器档位可调;a3-2:激振锤的选择:所述激振锤的对应壁厚小于实际梁厚;a3-3:激振锤设于孔道轴线与测试表面的垂直投影面上,利用激振锤激振并采集信号;a4:混凝土波速的测定:在健全混凝土结构上选取1-3m的一段;按照a2-a3的方法激振及采集数据;a5:灌浆密实度分析与评定:采用β值来反映测点位置的灌浆质量:β=1-sv-sp;其中sv为板底部反射速度影响系数,有其中,vsd和vr分别为灌浆密实部位和测试部位反射波速,ηv=vv/vsd,其中,vv为缺陷处反射波速;sp=0.5ap/(ab*ηa),ap、ab分别为波纹管、梁底部的反射信号振幅;ηa为反射振幅基准比率;当β>0.5时,表示为密实;当0<β≦0.5时,表示为半空或小规模缺陷;当β≦0时,表示为全空或大规模缺陷;用灌浆密实度指数d来评定测试区间的灌浆质量,根据测试区间的灌浆质量来评定孔道灌浆质量;其中,n为定位测试的点数,nj代表健全测点数,nx代表小空洞点数,nd代表大空洞点数。用修正灌浆密实度指数来判定孔道的灌浆质量:其中,d为检测区段的灌浆密实度指数;ld为检测区段长度;l0为孔道全长;dk为当该孔道各检测区段中,灌浆质量较好的连续区段的灌浆密实度指数;对于现浇预应力混凝土连续梁,若孔道长度≦50m,可采用定性定位综合法或单独采用定位测试;若孔道长度≧50m,则单独采用定位检测;所述定性定位综合法包括如下步骤:1)定性测试;2)计算灌浆指数;3)若灌浆指数>0.8,结束测试,认为无灌浆事故;4)若灌浆指数≦0.8,进行定位测试,对孔道和灌浆质量评价,结束测试。进一步优选为:在步骤s1中,钢绞线端头长度为3-5cm。采用上述方法,钢绞线端头太短传感器比较难安装,钢绞线端头太长则会影响激励信号。进一步优选为:在步骤s2中,传感器对称安装且传感器与锚头的距离x满足,0<x≦2cm。进一步优选为:步骤s3-2重复至少5次。采用上述方法,通过重复测试提高测试的精确度,减少偶然因素带来的误差。进一步优选为:采用全长衰减法进行分析时,步骤s3中的激振方式为双方向激振,在步骤s3-2后还包括步骤s3-3:对调激振端和接收端放大器的放大倍率,在原接收端的钢绞线上激振,原激振端的传感器接收信号。采用上述方法,双方向激振有利于减少测试方向的不同所带来的测试误差,提高测试的精度。进一步优选为:步骤a1包括如下步骤,1)根据设计图纸和施工记录标出孔道的位置,若能标出,则定位;2)若1)中不能准确定位,则利用混凝土雷达或竖向扫描的方法确认孔道位置,若能确认,则定位;3)若2)中不能准确定位,则钻孔验证,定位;孔道位置的定位误差不超过波纹管管径的1/4。定位检测需要沿孔道进行激振和测试。显然,孔道定位的精度直接影响测试的精度和分辨力。采用上述方法,能够通过最优的方式获得孔道位置的信息,且尽可能地减少对待测试孔道和梁的破坏。进一步优选为:步骤a2-1中,在孔道全长设置测试点间距为0.15-0.4m,对a-e部位,测试点间距为0.05-0.2m。采用上述方法,由于泌水、气泡聚集是造成灌浆缺陷的直接原因。而无论是泌水还是气泡,均轻于固体化灌浆料。因此,泌水、气泡容易聚集于管道的拐点和上部,a-e的部位正是这些部位,容易产生灌浆缺陷,所以需要设置更加密集的测试点,以提高测试的准确性。进一步优选为:在步骤a2-3中,用人工压着的方式或固定传感器,压着力度最大为10kg,并使传感器的轴线垂直于结构表面并对向孔道轴线。采用上述方法,实验对比了专用支座套(st-s31sc-1)、手按(5kg)、手按(12kg)、热熔胶这几种固定方法,测试结果表明:手按力度较小时对测试信号影响较小,也可得到满意的测试效果;手按按压力度过大时频阶杂乱,说明手按力度对测试信号的影响较大;热熔胶固定有附加模态,测试结果与热熔胶的厚度、温度等有关;专用支座套(st-s31sc-1)能提供稳定可靠地耦合力度和阻尼,使得测试信号更为稳定;与专用支座套相比,采用人工压着的方式在测试点之间的移动更加方便。进一步优选为:步骤a3-3中激振锤距传感器间距0.05-0.1m;击打接触结构表面瞬间的速度在0.2-0.6m/s。采用上述方法,激振的自振信号相对衰减较快,此时,在较大范围内均可得到梁底的反射频谱。这样测试得到的测试结果更加准确可靠。进一步优选为:步骤a5中,还可同时采用sps值来反映测点位置的灌浆质量:第i点的psg值为其中vi和vi+1分别是第i点和i+1测点得到的反射波速;δs为第i和第i+1测点的间距,h为第i和第i+1测点间板的设计厚度;第n点的sps值为其前面各点psg值的累积。采用上述方法,考虑到对反射波速产生影响的混凝土材质、波纹管本身、壁厚、弹性波波长等参数,其变化均较为缓慢,vi和vi+1的变化不大,sps和psg较小。而存在空洞型缺陷时,在缺陷起始位置sps和psg均会发生突变。因此,采用sps和psg可以突出缺陷,减少其他因素的影响。结合β值,可以更准确地判定缺陷的位置和类型。综上所述,本发明申请具有以下有益效果:(1)提供一种无损检测技术对预应力梁孔道灌浆密实度情况进行了测试,采用以冲击弹性波为检测媒介,综合了多种检测方法对预应力梁孔道灌浆情况进行测定及综合评判,将其结果定量化,形成一套更加精确的孔道灌浆质量评判标准,使得检测结果更加精确,更加合理;(2)对测试方法、测试步骤、测点、测试方向、传感器的安装、激振锤的选择等进行优化,形成完整的灌浆质量检测步骤,使得检测结果更加精确,更加合理。附图说明图1是实施例的工作流程图;图2是实施例的竖向扫描法示意图;图3是实施例的易出现灌浆缺陷的部位的示意图;图4是实施例的采用专用支座套固定传感器得到的测试信号图;图5是实施例的采用手压(5kg)方式固定传感器得到的测试信号图;图6是实施例的采用手压(12kg)方式固定传感器得到的测试信号图;图7是实施例的采用热熔胶固定传感器得到的测试信号图;图8是梁厚大于对应壁厚时的频谱图。图中,a、进浆口;b、出浆口;c、弯曲孔道的起弯点;d、弯曲孔道的反弯点;e、弯曲孔道的;a、梁底反射时间;b、自振周期。具体实施方式以下结合附图对本发明作进一步详细说明。本具体实施例仅仅是对本发明的解释,其并不是对本发明的限制,本领域技术人员在阅读完本说明书后可以根据需要对本实施例做出没有创造性贡献的修改,但只要在本发明的保护范围内都受到专利法的保护。一种灌浆密实度检测方法,包括如下步骤:1.1检测方法的选择:对于现浇预应力混凝土连续梁,若孔道长度≦50m,可采用定性定位综合法或单独采用定位测试;若孔道长度≧50m,则单独采用定位检测。本实施例中孔道的长度为30m,采用定性定位综合法。测试流程包括如下步骤:1)定性测试;2)计算灌浆指数;3)若灌浆指数>0.8,结束测试,认为无灌浆事故;4)若灌浆指数≦0.8,进行定位测试,对孔道和灌浆质量评价,结束测试。测试流程如图1所示。1.2抽样方式:定性检测的抽样方式:可按梁体或孔道,原则上以随机的方式抽样。但在下述情况下,应优先检测:1)当灌浆料在灌浆过程中发生初凝(特别是夏季容易出现),以及灌浆压力机出现故障的灌浆孔道;2)对腹板中的孔道,一般应选择弯曲较大的孔道;定位检测的抽样方式:对于按梁检测,应采用随机抽取的方式,或者对施工质量有所怀疑的构件;对于按孔道检测,应选取具有代表性的孔道,具体为:曲率最大的孔道;曲率最小、平直孔道;对施工质量有所怀疑的孔道。1.3定性检测1.3.1钢绞线端头清理及传感器安装1)确定检测梁体和孔道,并记录;2)将测试孔道锚头两端的露出钢绞线清理干净,钢绞线端头长度为3-5cm,使之能够牢固地粘接传感器;3)利用磁性卡座或粘接剂将传感器分别安装在孔道最上的一根或两根钢绞线上,并使传感器的轴线平行于钢绞线方向;4)传感器的安装应对称,并尽量靠近锚头,传感器与锚头的距离最大不大于2cm;5)安装完成后,确认传感器安装牢固。1.3.2激振及数据采集1)调整放大器,使激振短端的放大倍率低而接收端的放大倍率高,并记录;2)设置检测设备,使激振端的信号接入ch0而接收端的信号接入ch1;3)标定检测仪,并采集环境噪声以作为数据降噪用;4)检测仪进入准备状态后,利用激振锤对准安装传感器钢绞线,撞击激振;撞击方向平行于钢绞线轴向;5)在屏幕上核实检测数据无误后保存;6)重复上述3)-4)的步骤5次以上,完成单方向的数据采集;7)对调激振端和接收端放大器的放大倍率;8)在原接收端的钢绞线上激振,原激振端的传感器接收信号;9)重复上述3)-5)的步骤以完成定性检测。1.3.3混凝土波速的测定1)选取无孔道且与测试孔道相近高度的部位,进行混凝土波速的测定;2)测试方法与钢绞线测试相似,所不同的是需要将传感器固定在梁的断面上,激振则采用激振锤激振。1.4定位检测1.4.1孔道定位1)确定检测梁体和孔道,并记录;2)根据设计图纸和施工记录标出孔道的位置;3)当对孔道位置不确定时,利用混凝土雷达或竖向扫描的方法确认孔道位置;仍然不能确定时,应钻孔验证;竖向扫描法如图2所示。4)管道位置的定位误差不应超过波纹管管径的1/4;1.4.2确定检测方向选择上下方向为检测方向;在另外的实施例中,检测对象为腹板等竖向结构,应采用水平检测方向;在另外的实施例中,检测对象为马蹄形扩幅的t梁腹板孔道,从下部测试;再另外的实施例中,无法采用上下方向检测,则采用其他方向检测;1.4.3激振及数据采集1)在孔道轴线与测试表面的垂直投影面上,对于全孔道长度检测,检测间距取0.2m;对于下述易出现灌浆缺陷的部位,间距取0.1m:a.进浆口;b.出浆口;c.弯曲孔道的起弯点;d.弯曲孔道的反弯点顶部;e.弯曲孔道的反弯点后部;易出现灌浆部位如图3所示。2)设置检测设备,适当设置放大器,使采集得到的电压信号在0.5~2v之间即可;3)标定检测仪,并采集环境噪声以作为数据降噪用;4)用人工压着等方式使传感器固定在测试结构的表面上,并使其轴线垂直于结构表面并对向孔道轴线;在固定传感器时应使传感器先端与结构表面密切接触,避免点接触或线接触;在另外的实施例中,采用机械压着的方式将传感器压在测试部位表面;5)检测仪进入准备状态后,利用激振锤激振并采集信号;激振锤参考表1选取;6)激振力度不应过大。击打接触结构表面瞬间的速度在0.4m/s;激振锤也应和传感器同样,在孔道轴线与测试表面的垂直投影面上,且距传感器间距0.05m;7)在屏幕上核实检测数据无误后保存;8)移动传感器到下一测点,开始下一测点的测试。表1激振锤选择准则对象壁厚<20cm20~40cm40~60cm>60cm首选激振锤d10d17d17d30次选激振锤d6、d17d10d30d501.4.4混凝土波速的标定1)在健全混凝土结构上选取2m的一段;2)按照定位检测同样的方法激振及采集数据。1.5测试结果分析1.5.1定性测试结果采用综合灌浆指数if作为定性检测的评定指标,当灌浆饱满时,if=1;完全未灌时,if=0;综合灌浆指数定义为:if=(iev*ipv*itf)1/3,其中,iev为根据flea法得到的分项灌浆指数:ipv为根据flpv法得到的分项灌浆指数;itf为根据pftf法得到的分项灌浆指数。根据综合灌浆指数if:0.80以上表明无灌浆事故或大范围灌浆缺陷;不足0.80(包含)表明有灌浆事故或大范围灌浆缺陷。1.5.2定位测试分析采用β值和sps值来反映测点位置的灌浆质量。其中,psg:phasesensitivitydetectionofgroutdensity,灌浆密实度相敏检测指标;sps:sumofpsg,相敏指标和。β=1-sv-sp;其中sv为板底部反射速度影响系数,有其中,vsd和vr分别为灌浆密实部位和测试部位反射波速,ηv=vv/vsd,其中,vv为缺陷处反射波速;sp=0.5ap/(ab*ηa),ap、ab分别为波纹管、梁底部的反射信号振幅;ηa为反射振幅基准比率,根据幅频计算的方式有所不同,参考表2。表2不同管道类型的ηv和ηa值评定标准:当β>0.5时,表示为密实;当0<β≦0.5时,表示为半空或小规模缺陷;当β≦0时,表示为全空或大规模缺陷。psg:第i点的psg值为其中vi和vi+1分别是第i点和i+1测点得到的反射波速;δs为第i和第i+1测点的间距,h为第i和第i+1测点间板的设计厚度;第n点的sps值为其前面各点psg值的累积。用灌浆密实度指数d来评定测试区间的灌浆质量,根据测试区间的灌浆质量来评定孔道灌浆质量。其中,n为定位测试的点数,nj代表健全测点数,nx代表小空洞点数,nd代表大空洞点数。用修正灌浆密实度指数来判定孔道的灌浆质量:其中,d为检测区段的灌浆密实度指数;ld为检测区段长度;l0为孔道全长;dk为当该孔道各检测区段中,灌浆质量较好的连续区段的灌浆密实度指数。表3孔道灌浆质量分类传感器固定方式试验:采用一标准试块,对如下几种传感器的固定方式的测试结果进行了比较,采用d6锤进行测试,分别是,a:专用支座套(st-s31sc-1);b:手按(5kg);c:手按(12kg);d:热熔胶。测试结果如图4-7所示。测试结果表明:手按力度较小时对测试信号影响较小,也可得到满意的测试效果;手按按压力度过大时频阶杂乱,说明手按力度对测试信号的影响较大;热熔胶固定有附加模态,测试结果与热熔胶的厚度、温度等有关。专用支座套(st-s31sc-1)能提供稳定可靠地耦合力度和阻尼,使得测试信号更为稳定。采用手动按压的方式,既能使传感器牢固地与梁体表面接触,又能够方便移动,实现快速又可靠地测试。激振方式对比试验:选取的激振锤对灌浆密实度检测精度和分辨力有很大的影响。激振锤激振得到的弹性波具有自振周期。该自振周期与弹性波速的乘积的一半,即为对应壁厚。采用c50的预应力混凝土梁进行了试验,各激振锤得到的弹性波自振周期及对应壁厚见表4:表4典型条件下对应壁厚激振锤d6d10d17d22d30d50自振周期(ms)0.0210.0340.0580.0760.1030.172对应壁厚(m)0.0430.0690.1180.1540.2100.351根据实际壁厚与对应壁厚的关系,可以分为以下3种情形:如图8所示,当实际梁厚大于上表中的对应壁厚时,理论上在频谱图上就会出现两条线。当实际梁厚接近表中的对应壁厚时,其自振信号与梁底反射信号会形成共振,此时在频谱上仅出现一个对应的峰值。该峰值可能偏向梁底反射时间,也可能偏向自振周期。当实际梁厚小于表中的对应壁厚时,其自振信号与梁底反射信号可能形成反向叠加,从而削弱梁底的反射。因此,选取激振锤使其对应壁厚小于实际梁厚是必要的。实施例1-12如表5所示。表5实施例1-12的各项参数表当前第1页12