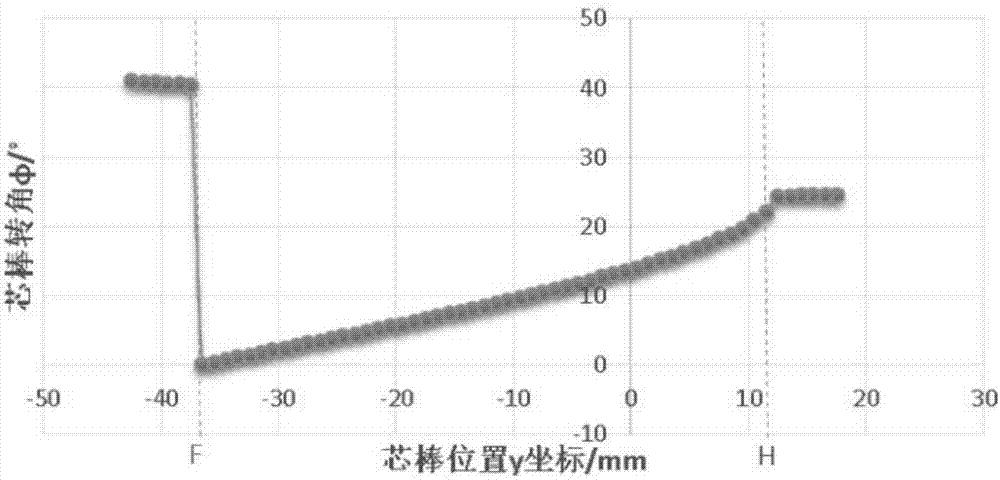
本发明属于大型齿轮测量的
技术领域:
,具体说是一种采用精密芯棒测头在位测量大型直齿轮廓形偏差的方法。
背景技术:
:齿轮测量技术在齿轮制造中占有很重要的地位,没有先进的检测技术和仪器,不可能制造出性能优良、高质量、高精度的齿轮。由于大型齿轮的大模数、大尺寸和大重量的特点,要准确测量其加工精度是非常困难的。另外,测量装置的重量和体积很大,不仅造成制造、安装、调整的困难,而且测量中的惯性问题也非常突出。多年来,国内外诸多学者在大型齿轮测量领域进行研究,丰富和发展了大型齿轮精密测量的理论和方法。大型齿轮的测量方式通常有两种,一是在专用齿轮测量仪上进行测量,二是在位测量。按测量的形式,在位测量方式还可分为上置式量仪和旁置式量仪。其中,基于在位测量方法的旁置式量仪和上置式量仪不仅克服了台式量仪测量大型齿轮的局限性,而且能显著降低测量仪器的成本,可操作性强,符合我国的国情,成为大型齿轮尤其是超大型齿轮测量技术的重要研究方向。常规在位测量仪受加工机床的限制,如机床的原始误差影响测量精度、测量条件与测量环境等问题的影响,测量精度、实施措施仍有待于进一步提高。在位测量大齿轮的齿廓偏差中,由于齿轮的重量大而产生的惯性大,致使测量过程中产生相应的麻烦,如完成一个轮齿廓面的齿廓偏差的测量后,想要测量其相邻廓面的偏差时就很困难。因为测量过程是从齿轮开始转动到测头划出齿顶,或测头从轮齿的一端走到另一端。由于齿轮惯性大,完成一个轮齿的测量后,即使停止工作台的回转,其位置已经不在测头的正确位置,需重新调整正确位置,才能开始下一个齿轮廓面的测量,且由于齿轮模数大,点测头沿基圆切线展开时行程长,致使测量仪结构大。2008年,金嘉琦、李文龙等人研制出了刃边齿条测头与被测齿轮单面啮合测量大齿轮偏差的在机测量仪,其测量原理主要为利用刃边齿条测头测量齿廓上不同位置,获得直母线偏差,进而分离出齿廓偏差和螺旋线偏差。技术实现要素:为了解决大型齿轮测量中遇到的测量基准选择困难,齿轮惯性大,测量效率低,测量条件差等问题,本发明提供了一种采用精密芯棒测头在位测量大型直齿轮廓形偏差的方法。为实现上述目的,本申请采用的技术方案是:采用精密芯棒测头在位测量大型直齿轮廓形偏差的方法芯棒测头与渐开线齿廓时刻保持相切接触,与被测齿轮轴线有一定距离且交叉的直线方向为y轴方向,绕齿顶圆逆时针切向为正方向,以过被测齿轮中心垂直于y轴的方向为x轴方向,远离齿轮中心的方向为正方向,建立坐标系,建立芯棒测头理论转角变化与芯棒测头位置坐标变化的关系;沿y轴方向平移芯棒测头,在位测量芯棒测头的线位移和微小转角变化,获得被测齿廓各位置点沿齿廓法线方向的偏差,通过对齿轮廓面上点集的误差分析获得齿轮的齿廓总偏差。进一步的,在所建立的坐标系下,设芯棒测头理论转角变化为δφ,芯棒测头位置坐标变化为δy,两者关系为:其中芯棒测头测点位移:式中:y—滑块的位移;—展开角;a—被测齿轮中心到测量坐标系y轴的距离;rb—被测齿轮的基圆半径;δ—被测齿廓初始位置与测量坐标系x轴夹角,即渐开线转角。进一步的,沿y轴方向平移芯棒测头,在位测量芯棒测头的线位移和微小转角变化,在位测量齿轮廓面的多个点形成的点集,需完成两个运动,获取两路测量信号,即芯棒测头沿与被测齿轮轴线有一定距离且交叉的直线方向的线位移y以及为获取廓面上不同位置的点所需的芯棒微小转角变化δφ′。进一步的,利用芯棒测头测量齿轮廓面上不同位置测得的芯棒测头转角变化、芯棒测头理论转角变化和芯棒测头测点位移得到被测廓面上各位置点沿齿廓法线方向的偏差,δfαi=νi(δφ′i-δφi)i=1,2···n通过对齿轮廓面上点集的误差分析获得齿轮的齿廓总偏差fα=max(δfα)-min(δfα)其中,y—滑块的位移;—展开角;a—被测齿轮中心到测量坐标系y轴的距离;rb—被测齿轮的基圆半径;δ—被测齿廓初始位置与测量坐标系x轴夹角,即渐开线转角。本发明由于采用以上技术方案,能够取得如下的技术效果:(1)芯棒测头直母线加工易获得高精度;(2)测量时,芯棒测头不需要偏置距离,可显著减小芯棒测头导轨的长度;(3)通过适当的初始位置调整,只改变滑块的位移方向和芯棒测头的旋转方向,即可完成齿轮左、右齿面的测量,提高测量效率;(4)被测齿轮不动,没有因大齿轮转动引起的惯性问题和芯棒测头跟踪问题;(5)测量过程是芯棒测头直母线与被测齿轮廓面的啮合过程,所测量的廓形偏差是在传动状态下的廓形偏差,更接近于齿轮的传动品质,测量属于带有某些综合测量特征的单项测量。附图说明本发明共有附图4幅:图1是本发明的测量系统原理图;图2芯棒测头转角随芯棒测头位置坐标的变化曲线图;图3转角变化与芯棒测头位置变化的规律曲线图;图4芯棒测头测点位移的变化曲线图。具体实施方式为了使本发明的目的、技术方案和优点更加清楚,下面结合附图和具体实施例对本发明进行详细描述。本实施例公开了一种采用精密芯棒测头在位测量大型直齿轮廓形偏差的方法,具体为:(1)确定被测齿轮的测量齿廓,任选被测齿轮的某一齿廓作为测量齿廓;(2)以大型齿轮的齿圈端面和基圆柱面为基准,定位并安装精密芯棒测头,被测齿轮固定不动,移动滑块,芯棒测头进入测量齿槽内,芯棒测头未与齿廓接触,此位置称为齿廓测量零位,芯棒测头可沿与被测齿轮轴线有一定距离且交叉的直线方向移动,可绕滑块中心转动。继续移动滑块,芯棒测头到达齿廓根部位置,滑块沿导轨移动的同时,芯棒测头转动且始终保持与被测齿轮廓面相切接触,芯棒测头与被测齿轮齿廓根部相接触,芯棒测头在上方,被测齿轮在下方;芯棒测头与被测齿轮轴线有一定距离且交叉的直线方向为y轴方向,绕齿顶圆逆时针切向为正方向,以过被测齿轮中心垂直于y轴的方向为x轴方向,远离齿轮中心的方向为正方向,建立坐标系;(3)芯棒测头刚好接触到被测齿廓根部时,此位置称为齿廓测量的开始位;继续移动滑块,芯棒测头与被测齿廓顶部接触时,此位置称为齿廓测量的结束位;在此范围内,均布测量n次,其中n为测量总次数,即每隔δy=y/n测量一次芯棒测头转角,其中δy为每次测量芯棒测头位置坐标变化量;在齿廓测量中,第i次测量时,芯棒测头在y轴方向上的位移值记为yi,其中i=1,2···n,第i次测量时,芯棒测头微小转角变化记为φ′i,其中i=1,2···n,这样共获取n组测量值记为(yi,φi′),其中i=1,2···n;从测量开始位到测量结束位,这中间的过程即为齿廓测量的数据采集过程,芯棒测头在y轴方向的位移和绕滑块中心的转角即为测量数据;完成上述测量后,移动滑块到齿廓测量零位,然后将芯棒测头退出被测齿轮的测量齿槽,完成齿廓的测量。芯棒测头理论转角变化记δφ,芯棒测头位置坐标变化记δy,芯棒测头理论转角变化与芯棒测头位置坐标变化关系为:芯棒测头测点位移:式中:y—滑块的位移;—展开角;a—被测齿轮中心到测量坐标系y轴的距离;rb—被测齿轮的基圆半径;δ—被测齿廓初始位置与测量坐标系x轴夹角(可视为渐开线转角)。(4)将这组偏差值代入下面的公式,即可求得被测齿廓的廓形偏差值齿轮廓形偏差值:δfαi=νi(δφ′i-δφi)i=1,2···n齿轮廓形总偏差:fα=max(δfα)-min(δfα)其中,y—滑块的位移;—展开角;a—被测齿轮中心到测量坐标系y轴的距离;rb—被测齿轮的基圆半径;δ—被测齿廓初始位置与测量坐标系x轴夹角(可视为渐开线转角)。已知被测齿轮的基本参数如表1所示,测量装置的初始位置如表2所示:表1渐开线齿轮基本参数参数名称符号数值单位模数m20mm齿数z192-压力角α20°分度圆直径d3840mm基圆直径db3608.419664mm齿根圆直径df3790mm表2测量装置初始位置根据测量原理,模拟分析出芯棒测头转角φ与芯棒测头位置y坐标的对应关系如表3所示,芯棒测头转角φ随芯棒测头位置y坐标的变化规律如图2所示,从图中可以看出,当芯棒测头位置达到f时,芯棒测头转角突变为φ=0,即为被测齿轮的初始位置,说明芯棒测头在到达f之前,没有与被测齿轮齿廓相接触,该段数据不是测量的有效数据,故将其滤去。芯棒测头位置达到h后,芯棒测头转角基本保持恒定,说明此时芯棒测头到达被测齿轮齿顶位置,该段数据与廓形误差的分析无关,故将此段数据滤去。基于上述原因,将芯棒测头到达初始位置之前的计算数据和芯棒测头到达齿顶点后的计算数据滤去,芯棒测头理论转角变化为δφ与芯棒测头位置坐标变化为δy的对应关系见表3,芯棒测头理论转角变化δφ与芯棒测头位置坐标变化δy的规律曲线如图3所示,从图中可以看出,芯棒测头理论转角变化δφ与芯棒测头位置坐标变化δy近似成线性分布。通过计算得到芯棒测头测点位移ν的值见表3,ν随转角的变化曲线如图4所示。表3芯棒测头转角φ、芯棒测头位置y坐标、芯棒测头理论转角变化为δφ,芯棒测头位置坐标变化为δy,以上所述,仅为本发明较佳的具体实施方式,但本发明的保护范围并不局限于此,任何熟悉本
技术领域:
的技术人员在本发明披露的技术范围内,根据本发明的技术方案及其发明构思加以等同替换或改变,都应涵盖在本发明的保护范围之内。当前第1页12