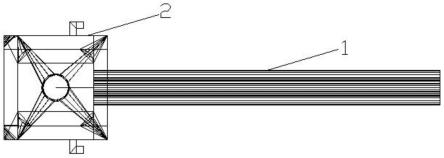
1.本发明属于无损检测技术领域,具体涉及一种发动机压气机叶片无损检测装置。
背景技术:2.涡流检测技术基本原理的建立和发展起源于早期电磁学的发现。1824年,加贝就发现,铜板会阻碍悬挂磁铁的摆动。1828年傅科指出,在强烈不均匀磁场中运动的铜盘内有涡流存在并伴随热效应发生。但其中仍有许多疑惑,直至1831年,法拉第发现了电磁感应现象,既变化的磁场能产生电场,并总结出电磁感应定律。直至现在,电磁感应现象都是用来阐述涡流实验基本原理所依据的重要的客观规律。在电磁感应现象发现以后由于人们广泛努力,对电磁现象的实验研究和对电磁基本理论问题的数学分析都获得了巨大进展。1873年,麦克斯韦系统总结了前人有关电磁学说的成就并加以发展,修正了描写电磁基本原理的方程得到了麦克斯韦方程组。麦克斯韦方程组严整描述了一切宏观的电磁现象,是解决大多数电磁学问题的基本理论工具对有适当边界条件的特定问题的麦克斯韦方程进行解析,原则上能够对不同形状,不同材料的内部和外表的电流或场的分布做出计算。
3.相关技术中,发动机叶片是非磁性金属材料叶片,叶缘处及叶盆、叶背1/3~1/2叶高处为应力集中处,容易发生疲劳,产生疲劳裂纹,裂纹方向为叶片径向。而叶片缺陷检测在一个特殊环境中,日常飞机维护过程中,一般由机械师进入进气道内对发动机叶片进行检查,故操作空间十分有限。因为检测对象为发动机压气机叶片,维护过程中一般并不做拆卸检测,故可供选择的检测方法受到限制。在航空维修中,常用的无损检测方法有超声、磁粉、涡流、射线和渗透。对于这类表面疲劳裂纹,主要以磁粉、涡流、渗透检测方法为主;然而,磁粉检测需要利用缺陷处的漏磁场吸附磁粉形成磁痕显示来判断工件表面及近表面有无缺陷,在不拆卸叶片的情况下根本难以实施,且磁粉检测只能检测铁磁性材料的零件;渗透检测对被测物表面要求较高,要满足相对光滑且无污染的条件,且必须对被测物表面进行预处理方可进行检测。该方法仅限于针对表面开口的不连续性进行检测,容易受到温度的影响,程序复杂,可重复性差,也不宜使用。
技术实现要素:4.有鉴于此,本发明的目的在于克服现有技术的不足,提供一种发动机压气机叶片无损检测装置,以解决现有技术中对发动机压气机叶片进行检测的检测装置在不拆卸叶片的情况下对叶片的正面和背面检测使用不便的问题。
5.为实现以上目的,本发明采用如下技术方案:一种发动机压气机叶片无损检测装置,包括:连杆,所述连杆一端连接探头且连杆的杆身部位设有握柄,所述握柄能够在杆身上滑动,且探头能够阻止握柄滑出;
6.所述探头包括检测线圈,用于检测线圈中的电流信号是否发生变化;
7.所述探头上设有检测面;
8.所述检测面设有斜槽部和斜角部,所述斜槽部和斜角部卡接且所述斜槽和斜角之
间通过弹簧形成活动约束。
9.进一步的,所述检测线圈包括导线和线圈;
10.所述检测线圈采用绝对式检测线圈或变压器式线圈。
11.进一步的,所述绝对式检测线圈,包括:
12.并联连接的激励线圈和感应线圈。
13.进一步的,所述检测线圈内部设有
14.磁芯,用于增强检测区域的磁场强度。
15.进一步的,所述探头的检测频率为400khz~1800khz;
16.当给定频率下只考虑趋肤效应时导线的交流电阻与邻近效应引起的电阻相等时,所述激励线圈导线的直径为0.08mm;
17.所述线圈的直径约为磁芯直径的1.2倍;
18.所述激励线圈的线圈匝数为28~35匝,感应线圈的线圈匝数为14~20匝;
19.所述激励线圈和感应线圈之间的最小距离为3.32mm。
20.进一步的,所述探头的检测频率为1200khz;
21.所述激励线圈的线圈匝数为32匝,感应线圈的线圈匝数为16匝。
22.进一步的,所述连杆的长度为300mm;
23.所述握柄的长度为130mm;
24.所述探头的体积为15*15*20mm3。
25.本发明采用以上技术方案,能够达到的有益效果包括:
26.本发明提供一种发动机压气机叶片无损检测装置,包括连杆,所述连杆一端连接探头且连杆的杆身部位设有握柄,所述握柄能够在杆身上滑动,且探头能够阻止握柄滑出;所述探头包括检测线圈,用于检测线圈中的电流信号是否发生变化。本发明提供的发动机压气机叶片无损检测装置通过设置连杆、探头及握柄,不需要对所检测物体进行任何的表面预处理,不需要施加耦合剂,实现非接触的快速检测,且斜槽部和斜角部通过弹簧连接能够在不拆卸的情况下进行方便快捷的检测,成功检出裂纹,本技术提供的发动机压气机叶片无损检测装置反应灵敏,检测效果良好。
附图说明
27.为了更清楚地说明本发明实施例或现有技术中的技术方案,下面将对实施例或现有技术描述中所需要使用的附图作简单地介绍,显而易见地,下面描述中的附图仅仅是本发明的一些实施例,对于本领域普通技术人员来讲,在不付出创造性劳动的前提下,还可以根据这些附图获得其他的附图。
28.图1为本发明提供的连杆与探头的结构示意图;
29.图2为本发明提供的握柄的结构示意图;
30.图3为本发明提供的导线电阻和直径的关系示意图。
具体实施方式
31.为使本发明的目的、技术方案和优点更加清楚,下面将对本发明的技术方案进行详细的描述。显然,所描述的实施例仅仅是本发明一部分实施例,而不是全部的实施例。基
于本发明中的实施例,本领域普通技术人员在没有做出创造性劳动的前提下所得到的所有其它实施方式,都属于本发明所保护的范围。
32.本技术提供的一种发动机压气机叶片无损检测装置主要用于检测材料表面裂纹,为不连续缺陷,是采用涡流检测方法的应用。涡流检测的原理是,电场能够在空间激发磁场,而变化的磁场又能激发电场,在该电场中放置闭合回路能够产生电流,那么在该电场中放置整块的导体是不是会产生跟闭合回路中电流方向一致的电流呢,答案是肯定的,该导体表面将相当于自发组成的无数条极细的闭合回路,其中有电流流过,这就是涡流。涡流的电流方向,根据电磁感应原理,将是能产生阻碍磁通量变化的磁场的方向,同时,根据前文对互感现象的描述,该涡流产生的磁场将在激励线圈内产生感生电动势,从而对激励线圈中的电流产生影响。故,监测线圈中的电流信号,就能对涡流进行监测,当产生涡流的导体发生变化时(如材质、表面缺陷等)涡流就会发生变化,激励线圈的感生电动势也会改变,其电流信号也会随之改变。因此,只需检测线圈中的电信号变化,就能发现材料的表面缺陷,达到无损检测目的。交变电流是方向和大小按一定周期规律变化的电流,日常生活中所用电流既为交变电流,根据电磁感应原理,它无疑能产生一个周期变化的磁场,该磁场就能在空间激发电场,如前所述,就能达到检测目的。
33.本技术中检测对象为发动机压气机叶片,维护过程中一般并不做拆卸检测,故可供选择的检测方法受到限制。在航空维修中,常用的无损检测方法有超声、磁粉、涡流、射线和渗透。对于这类表面疲劳裂纹,主要以磁粉、涡流、渗透检测方法为主。
34.然而,磁粉检测需要利用缺陷处的漏磁场吸附磁粉形成磁痕显示来判断工件表面及近表面有无缺陷,在不拆卸叶片的情况下根本难以实施;渗透检测对被测物表面要求较高,要满足相对光滑且无污染的条件,且必须对被测物表面进行预处理方可进行检测。该方法仅限于针对表面开口的不连续性进行检测,容易受到温度的影响,程序复杂,可重复性差,也不宜使用;涡流检测是一种基于电磁感应原理的无损检测方法,该方法不需要对所检测物体进行任何的表面预处理,不需要施加耦合剂,还可以实现非接触的快速检测,因此可以在不拆卸的情况下进行方便快捷的检测。并且涡流检测方法特别适合金属构件的表面和近表面缺的不连续性检测。因此从检测可靠性和可执行性性方面考虑,选择涡流检测法最佳。
35.下面结合附图介绍本技术实施例中提供的一个具体的发动机压气机叶片无损检测装置。
36.如图1和图2所示,本技术实施例中提供的发动机压气机叶片无损检测装置,包括:连杆1,所述连杆1一端连接探头2且连杆1的杆身部位设有握柄3,所述握柄3能够在杆身上滑动,且探头2能够阻止握柄3滑出;
37.所述探头2包括检测线圈,用于检测线圈中的电流信号是否发生变化。
38.发动机压气机叶片无损检测装置的工作原理为:因为在外场对压气机进行检测时,只能通过发动机机匣上的检查孔对叶片进行检测,所以将发动机压气机叶片无损检测装置设计为探头2+细长连杆1+握柄3的结构。且同级各叶片间距离有限,这就要求探头2尺寸足够小,以便能进入检查孔并灵活操作。经过实验测算,本技术设计发动机压气机叶片无损检测装置整体尺寸如下:连杆1长为300mm,握柄3为130mm,探头2为15*15*20mm3。本技术中连杆1及握柄3从实际需求出发,结合使用方便,拿握舒适等因素。分别设计为300*5尺寸
和130*10尺寸管状结构。连杆1与握柄3连接处设计为底径10mm顶径7mm高度20mm的锥台。
39.一些实施例中,所述探头2上设有检测面;
40.所述检测面设有斜槽部和斜角部,所述斜槽部和斜角部卡接且所述斜槽和斜角之间通过弹簧形成活动约束。
41.可以理解的是,待测叶片形状不规则,对待测叶片进行全面检测需面临的一个主要问题是:叶缘、叶尖为线接触式待测区域(下文称a区),叶盆、叶背为面接触式待测区域(下文称b区)。即在检测叶缘与叶尖时,检测装置沿曲线运动与待测区为线接触,而在检测叶盆与叶背时,检测装置与待测区域为面接触,检测装置需在叶片表面运动。
42.根据机械原理相关知识可知,面接触自由度小于线接触的自由度。为使探头2能够在手的操纵下按一定轨迹移动,其结构的自由度应该是一定的,多余的自由度应该由约束来对其进行抵消。故检测a、b两区的检测装置探头2约束度应当不同,即检测a区的探头2结构上应该较检测b区的探头2多一个约束。
43.因此,本技术在探头2的检测面上装有一个可活动的约束,该约束利用斜槽与斜角配合,由弹簧提供拉紧力使其可牢固固定在探头2的检测面上,又可方便卸下放置于探头2后侧的放置卡槽中。当利用探头2对待测区a进行检测时,将活动约束装上,当利用探头2对待测区b进行检测时则只需将活动约束卸下放置于放置卡槽即可。
44.为验证检测装置检测效果,将实验室中的叶片作为检测对象,用检测装置对其进行测试,叶片上有模拟裂纹缺陷,实验证明检测装置能成功检出裂纹,检测装置反应灵敏,检测效果良好,符合设计要求。
45.一些实施例中,所述检测线圈包括导线和线圈;
46.所述检测线圈采用绝对式检测线圈或变压器式线圈。
47.涡流检测装置的设计参数包括接线方式、线圈直径、线圈匝数、导线线径、线圈间距和检测频率等,这些参数决定了检测装置的线性度、灵敏度和测量范围。
48.优选的,所述绝对式检测线圈,包括:
49.并联连接的激励线圈和感应线圈。
50.优选的,所述检测线圈内部设有
51.磁芯,用于增强检测区域的磁场强度。
52.优选的,所述探头2的检测频率为400khz~1800khz;
53.当给定频率下只考虑趋肤效应时导线的交流电阻与邻近效应引起的电阻相等时,所述激励线圈导线的直径为0.08mm;
54.所述线圈的直径约为磁芯直径的1.2倍;
55.所述激励线圈的线圈匝数为28~35匝,感应线圈的线圈匝数为14~20匝;
56.所述激励线圈和感应线圈之间的最小距离为3.32mm。
57.所述探头2的检测频率为1200khz;
58.所述激励线圈的线圈匝数为32匝,感应线圈的线圈匝数为16匝。
59.其中,接线方式的确定为:因为叶片表面光滑,无其他干扰因素,目前使用的检测装置主要采用绝对式线圈设计,这类检测线圈适用于检测光滑平整可贴近检测的表面。因此,检测装置可以采用绝对式检测线圈,但是为了提高检测精度,采用激励线圈与响应线圈分开的结构形式,这种结构形式亦称为变压器式,变压器式线圈适用于检测表面平整光滑,
易于贴近检查的待测件。但是变压器式检测线圈对提离效应反应比较敏感,检测时需确保检测装置紧贴待测件,而不能提离待测件表面。在此基础上,变压器式检测线圈因收、发线圈分离,接受线圈受到的干扰小、信号稳定,能够对比较微小的差别作出反应,因此对表面缺陷反应灵敏,能够比较精确可靠的检测出待测表面的裂纹缺陷。并且因为只需贴紧待测面滑动,有检测效率高、检测机动灵活等优点。
60.此外,根据叶片结构和缺陷的检测特点以及便于原位检测的需要,将检测装置设计为放置式结构类型,并在检测线圈内部安装磁芯,增强检测区域的磁场强度,提高检测灵敏度高。
61.检测频率的选择为:根据涡流环理论,计算出放置式线圈检测试件的特征频率
[0062][0063]
式中:μ表示磁导率;σ表示电导率,其中,电导率为97.6%iacs,即σ=56.8ms/m,相对磁导率为1,故确定工作频率:f1=(10~50)fg=(10~50)
×
99739。
[0064]
叶片由于应力集中,叶缘处及叶盆、叶背1/3~1/2叶高处在长期交变载荷的作用下,容易产生疲劳裂纹,且裂纹缺陷一般都贯穿叶片叶片厚度即有效渗透深度d=0.5~1.5mm=2.6y(y为标准渗透深度,工程中通常定义2.6倍标准渗透深度为有效渗透深度)。由
[0065][0066]
式中:y表示裂纹深度;f表示试验频率。确定工作频率f2=1338.220446khz,由f1、f2综合分析确定检测频率f。计算可得,检测频率f=400k~1800khz。经实验选取检测频率1200khz。
[0067]
导线线径的选择为:对于一定的激励频率,存在着一个最佳导线线径。只考虑趋肤效应时,线圈损耗随着导线直径d0的增加而减小。然而,当导线直径d0增加时,由邻近效应而产生的交流电阻也越大。导线交流电阻和导线直径的关系见图3。其中,rf为给定频率下只考虑趋肤效应时导线的交流电阻,rg为邻近效应引起的电阻。当rf=rg时,导线交流电阻最小。计算得出,激励线圈导线的最佳直径为0.08mm。
[0068]
线圈直径的确定为:线圈直径的确定主要考虑以下几个因素:(1)线圈的直径越大,敏感范围越大,线性范围越大,线性范围一般为线圈外径的1/3~1/5;(2)线圈的直径越大,灵敏度越低;(3)线圈越薄,灵敏度越高;(4)线圈的直径越大,有效作用范围越大,一般为磁芯直径的三倍。
[0069]
根据以上分析因素,依据检测灵敏度要求和线性范围的要求,选取磁芯(材料为锰锌)的直径为1mm,即线圈内径为1mm、外径r约为1.16mm。
[0070]
线圈匝数的确定为根据航空维修中所使用的涡流仪,其阻抗的取值范围为(1~2)kω,根据x
l
=2πfl,可求得电感量l。线圈的匝数可由下式估算:
[0071][0072]
其中:l—电感量;цs—磁芯有效磁导率;n—线圈匝数;l—线圈长度;d0—线圈平
均直径。经计算,n取值范围为激励线圈28~35匝,接收线圈为14~20匝。经实验选取激励线圈32匝,接收线圈16匝。
[0073]
线圈间距的确定为:检测线圈主要采用两个相邻线圈同时对同一试件相邻部位进行检测,由于发动机压气机叶片结构特殊且在变截面附近易出现裂纹,因此两个线圈之间的间距对检测结果有很大的影响,间距大,变截面影响大;间距小,两个线圈之间的磁场会出现干扰。因此,在两个线圈的磁场互不干扰的情况下,两线圈的间距以小为宜。线圈的外径r=1.16mm,则单个线圈磁场的有效作用范围直径为3.32mm,半径为1.66mm,则两个线圈互不干扰的最小距离为3.32mm。
[0074]
综上所述,本发明提供一种发动机压气机叶片无损检测装置,包括连杆,所述连杆一端连接探头且连杆的杆身部位设有握柄,所述握柄能够在杆身上滑动,且探头能够阻止握柄滑出;所述探头包括检测线圈,用于检测线圈中的电流信号是否发生变化。本发明提供的发动机压气机叶片无损检测装置通过设置连杆、探头及握柄,不需要对所检测物体进行任何的表面预处理,不需要施加耦合剂,实现非接触的快速检测,且能够在不拆卸的情况下进行方便快捷的检测,成功检出裂纹,本技术提供的发动机压气机叶片无损检测装置反应灵敏,检测效果良好。
[0075]
可以理解的是,上述提供的装置实施例与上述的装置实施例对应,相应的具体内容可以相互参考,在此不再赘述。
[0076]
本领域内的技术人员应明白,本技术的实施例可提供为装置、系统、或计算机程序产品。因此,本技术可采用完全硬件实施例、完全软件实施例、或结合软件和硬件方面的实施例的形式。而且,本技术可采用在一个或多个其中包含有计算机可用程序代码的计算机可用存储介质(包括但不限于磁盘存储器和光学存储器等)上实施的计算机程序产品的形式。
[0077]
本技术是参照根据本技术实施例的装置、设备(系统)、和计算机程序产品的流程图和/或方框图来描述的。应理解可由计算机程序指令实现流程图和/或方框图中的每一流程和/或方框、以及流程图和/或方框图中的流程和/或方框的结合。可提供这些计算机程序指令到通用计算机、专用计算机、嵌入式处理机或其他可编程数据处理设备的处理器以产生一个机器,使得通过计算机或其他可编程数据处理设备的处理器执行的指令产生用于实现在流程图一个流程或多个流程和/或方框图一个方框或多个方框中指定的功能的装置。
[0078]
这些计算机程序指令也可存储在能引导计算机或其他可编程数据处理设备以特定方式工作的计算机可读存储器中,使得存储在该计算机可读存储器中的指令产生包括指令装置的制造品,该指令装置实现在流程图一个流程或多个流程和/或方框图一个方框或多个方框中指定的功能。
[0079]
这些计算机程序指令也可装载到计算机或其他可编程数据处理设备上,使得在计算机或其他可编程设备上执行一系列操作步骤以产生计算机实现的处理,从而在计算机或其他可编程设备上执行的指令提供用于实现在流程图一个流程或多个流程和/或方框图一个方框或多个方框中指定的功能的步骤。
[0080]
以上所述,仅为本发明的具体实施方式,但本发明的保护范围并不局限于此,任何熟悉本技术领域的技术人员在本发明揭露的技术范围内,可轻易想到变化或替换,都应涵盖在本发明的保护范围之内。因此,本发明的保护范围应以所述权利要求的保护范围为准。