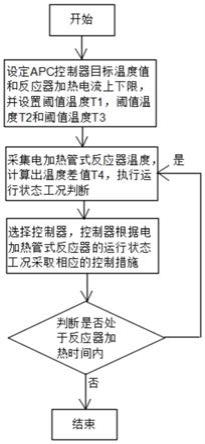
1.本发明涉及电加热管式反应器防飞温控制技术领域,尤其是指一种电加热管式反应器防飞温控制系统和方法。
背景技术:2.电加热管式反应器是化工生产过程中常见的设备,具有停留时间精确控制、反应温度分段控制等优势,但是在电加热管式反应器工作期间,由于管内反应物料组分及配比波动会导致某些副反应,而这些副反应会进行剧烈的放热,管内温度又很难通过人工进行控制,所以最后反应器会因为飞温被烧坏。因此,亟待开发一种防止反应器飞温烧坏的控制技术。
3.公开于2016年8月17日公开号为103922889b的中国专利提供了一种六氟丙烯裂解反应器防飞温控制方法,该专利的应用对象为六氟丙烯裂解反应器,该裂解反应以四氟乙烯为裂解原料,在电加热的作用下发生裂解生成六氟丙烯,其反应器飞温状态判断标准主要是通过反应器温度变化率来实现,具体控制手段是通过调节八氟环丁烷缓冲管路、氮气及压缩空气管路开启和关闭来达到防飞温的目的。但是该专利采用的利用反应器温度变化率来判断反应器运行状态的方法并不够准确,且反应温度变化率作为飞温判断依据存在一定的滞后性,变化率的值也不好选取,而且该专利采用的防飞温控制手段主要是增加八氟环丁烷稀释管路及压缩空气与氮气吹扫管路,根据不同的温度变化率开启不同的管路,因此需要对反应器进行较大的改造,仪表阀门等硬件投资较大,经济性差。在
技术实现要素:4.本发明的目的是克服现有技术中的缺点,提供一种电加热管式反应器防飞温控制系统和方法。
5.本发明的目的是通过下述技术方案予以实现:
6.一种电加热管式反应器防飞温控制系统,包括电加热管式反应器和防飞温控制设备,所述防飞温控制设备包括apc控制器和防飞温控制器,所述apc控制器与电加热管式反应器为通信连接,所述防飞温控制器与电加热管式反应器为通信连接,所述防飞温控制设备还包括反应器运行状态判断模块和逻辑控制模块,所述反应器运行状态判断模块用于获取电加热管式反应器的运行状态,所述逻辑控制模块用于根据反应器运行模块状态判断模块获取的电加热管式反应器运行状态输出相应的控制措施。
7.通过防飞温控制设备进行温度控制,解决了人工手动控制反应器温度难操作和温度数据反馈滞后的困难,且防飞温控制器和apc控制器之间可以进行无扰切换,反应器的温度控制更加平稳,且能保证最优的反应转化率,且做到了智能识别反应器的状态,更高效率的防止飞温现象的出现。
8.进一步的,一种电加热管式反应器防飞温控制方法,基于上述的电加热管式反应器防飞温系统,包括以下步骤:
9.步骤一:设定apc控制器目标温度值和反应器加热电流上下限,并设置电加热管式反应器温度和apc控制器目标温度差值的阈值温度t1、阈值温度t2和阈值温度t3,所述阈值温度t1、阈值温度t2和阈值温度t3用于判断电加热管式反应器所处运行状态工况;
10.步骤二:采集电加热管式反应器内若干个点的温度,筛选出一段时间后的温度与初始温度相差最大的点,将在该点采集到的温度作为电加热管式反应器温度,计算出电加热管式反应器温度和apc控制器目标温度的温度差值t4,并执行运行状态工况判断;
11.步骤三:根据运行状态工况判断的判断结果确定电加热管式反应器所处运行状态工况,根据电加热管反应器所处的运行状态工况选择控制器,控制器根据电加热管式反应器的运行状态工况采取相应的控制措施,并执行步骤四;
12.步骤四:在电加热管式反应器为反应物加热的时间内,持续执行步骤二和步骤三。
13.放弃使用温度变化率这一指标来判断反应器运行状态,以反应器当前温度与apc目标温度差值作为判断反应器运行状态的依据,有效消除温度变化率波动大引起误判带来的损失,更加有效解决了无法找到飞温临界点的难题,做到了提前捕捉和提前干预,进一步增加防飞温的成功率。在对反应物加热的过程中,持续监测管内运行状态工况,保证了电加热管式反应器在反应过程中一直处于安全工作状态。
14.进一步的,所述运行状态工况判断具体包括运行状态子步骤,所述运行状态工况判断子步骤具体为:将计算出的电加热管式反应器温度和apc控制器目标温度的温度差值t4与阈值温度t1、阈值温度t2和阈值温度t3进行比较,确定温度差值t4所处温度范围,并根据温度差值t4所处温度范围来确定电加热管式反应器所处的运行状态工况。
15.通过对比反应器温度和apc控制器目标温度差值和阈值温度来确定电加热管式反应器所处运行状态工况,不同工况所采取的控制措施不同,进一步细化反应器内温度控制,以达到最优的反应转化率。
16.进一步的,所述运行状态工况具体包括:计算出的电加热管式反应器温度和apc控制器目标温度的温度差值t4处在小于或等于t1的温度范围内,所述电加热管式反应器处于工况一,而当电加热管式反应器处于工况一时,apc控制器控制电加热管式反应器的加热输出电流变化,工况一运行状态下,加热电流输出值的输出步幅计算公式如下:
17.a(step)=a(step_apc)
18.其中:a(step)为电流输出步幅,a(step_apc)为apc控制器输出步幅;
19.计算出的电加热管式反应器温度和apc控制器目标温度的温度差值t4处在大于t1且小于或等于t2的温度范围内,所述电加热管式反应器处于工况二,而当电加热管式反应器处于工况二时,所述电加热管式反应器的加热输出电流由apc控制器切换至防飞温控制器控制,防飞温控制器控制电加热管式反应器的加热输出电流变化,工况二运行状态下,加热电流输出值的输出步幅计算公式如下:
20.a(step)=k1*(1+t4)
21.其中:k1为电加热管式反应器处于工况二时防飞温控制器降低电流的速度系数,t4为apc控制器目标温度和电加热管式反应器温度的差值;
22.电加热管式反应器温度和apc控制器目标温度的温度差值t4处在大于t2且小于或等于t3的温度范围内,所述电加热管式反应器处于工况三,而当电加热管式反应器处于工况三时,防飞温控制器进一步加快电流降低的速度,加热电流输出值的输出步幅计算公式
如下:
23.a(step)=k2*(1+t4)
24.其中:k2为电加热管式反应器处于工况三时防飞温控制器降低电流的速度系数;
25.计算出的电加热管式反应器温度和apc控制器目标温度的温度差值t4处在大于t3的温度范围内,所述电加热管式反应器处于工况四,而当电加热管式反应器处于工况四时,防飞温控制器直接输出最大电流,加热电流输出值的输出步幅计算公式如下:
[0026][0027]
其中:k3为电加热管式反应器处于工况四时防飞温控制器降低电流的速度系数,k为apc控制器模型增益,a(sp)为反应器加热电流设定值,a(l)为防飞温控制器电流下限值。
[0028]
通过调节加热电流输出步幅来达到调节管内温度的目的,直接由控制器进行输出电流控制,根据具体情况来调节步幅的大小,可以更加精确的调节管内温度。
[0029]
进一步的,步骤三中所述控制措施为先通过控制器改变电加热管式反应器的加热输出电流,再通过加热输出电流来改变电加热管式反应器内温度;控制器输出的加热输出电流随着运行状态工况的变化而变化。
[0030]
无需对反应器进行额外的技术改造,包括增加额外的管线及仪表阀门等,直接通过控制加热电流大小即可完成对反应器温度的平稳控制,实施难度小投资危险性小。
[0031]
进一步的,控制器通过控制电加热管式反应器的电流mv虚开关的开闭来改变电加热管式反应器的加热输出电流。
[0032]
无需对反应器进行额外的技术改造,节省了投资成本,并且实施难度较小。
[0033]
进一步的,步骤三中所述控制措施通过apc
‑
suite软件的图形化脚本模块进行编写或修改。
[0034]
可以通过脚本语言编写针对反应器不同工况下的不同控制措施,apc
‑
suite软件的操作画面直观整洁,操作员全程无需操作即可轻松应对反应器飞温
[0035]
进一步的,通过反应器运行状态判断模块执行步骤二中所述运行状态工况判断,所述反应器运行状态判断模块通过对采集到的电加热管式反应器防飞温控制系统底层dcs数据进行逻辑计算与判断来获取反应器运行状态。
[0036]
通过防飞温控制器来判断反应器的运行状态工况,不需要人工进行监视,减小了操作人员的工作量,也提高了对反应器运行状态工况的判断精度。
[0037]
进一步的,步骤三中所述控制措施通过opc协议写入电加热管式反应器防飞温控制系统底层dcs。
[0038]
通过opc协议进行数据通信,不需要对电加热管式反应器进行改造,控制措施直接通过无线传输的模式写入电加热管反应器内,反应速度快且可实施性高。
[0039]
本发明的有益效果是:
[0040]
采用了防飞温控制器对电加热管式反应器进行工况判断和控制,且支持与apc控制器之间的无扰切换,反应器的温度控制更加平稳,可以保证最优的反应转化率;对比于人工控制反应器温度,防飞温控制器更能智能识别反应器状态,防止飞温现象的产生。且反应
器状态的识别以反应器当前温度与apc控制器目标温度差值作为判断反应器运行状态的依据,有效消除温度变化率波动大引起误判带来的损失,更加有效解决了无法找到飞温临界点的难题,做到了提前捕捉并进行提前干预。且无需对反应器进行额外的技术改造,包括增加额外的管线及仪表阀门等,直接通过控制加热电流大小即可完成对反应器温度的平稳控制,实施难度小,投资成本也小。
附图说明
[0041]
图1是本发明的一种电加热管式反应器防飞温控制系统基本架构图;
[0042]
图2是本发明的一种流程示意图;
[0043]
图3是本发明实施例的一种电加热管式反应器飞温曲线图;
[0044]
图4是本发明实施例的一种异常工况下防飞温控制器控制效果图。
[0045]
其中:1、电加热管式反应器,2、防飞温设备,3、apc控制器,4、防飞温控制器,5、反应器运行状态判断模块,6、逻辑控制模块,7、图形化脚本模块。
具体实施方式
[0046]
下面结合附图和实施例对本发明进一步描述。
[0047]
实施例:
[0048]
一种电加热管式反应器防飞温控制系统,包括电加热管式反应器1和防飞温控制设备2,所述防飞温控制设备2包括apc控制器3和防飞温控制器4,所述apc控制器3与电加热管式反应器1为通信连接,所述防飞温控制器4与电加热管式反应器1为通信连接,所述防飞温控制设备2还包括反应器运行状态判断模块5和逻辑控制模块6,所述反应器运行状态判断模块5用于获取电加热管式反应器1的运行状态,所述逻辑控制模块6用于根据反应器运行状态判断模块5获取的电加热管式反应器1运行状态输出相应的控制措施。
[0049]
电加热管式反应器1防飞温控制系统基本架构如图1所示,输入端为反应器温度、apc目标温度值、反应器加热电流上下限和反应器电流,这些数据通过标准的opc协议与防飞温控制设备2进行通讯。整个防飞温控制设备2由两个子模块构成:首先是反应器运行状态判断模块5,该模块通过对采集到的底层dcs数据进行逻辑计算与判断,从而准确获得不同的反应器运行状态,并将该状态传递给逻辑控制模块6。逻辑控制模块6的主要功能是根据不同的反应器运行状态采取不同的控制措施。最后将控制输出通过opc协议写入到底层dcs完成对整个反应器防飞温专拣控制的过程。
[0050]
如图2所示,一种电加热管式反应器防飞温控制方法,基于上述的电加热管式反应器防飞温系统,包括以下步骤:
[0051]
步骤一:设定apc控制器3目标温度值和反应器加热电流上下限,并设置电加热管式反应器1温度和apc控制器3目标温度差值的阈值温度t1,阈值温度t2和阈值温度t3,所述阈值温度t1、阈值温度t2和阈值温度t3用于判断电加热管式反应器1所处运行状态工况;
[0052]
步骤二:采集电加热管式反应器1内若干个点的温度,筛选出一段时间后的温度与初始温度相差最大的点,将在该点采集到的温度作为电加热管式反应器1温度,计算出电加热管式反应器1温度和apc控制器3目标温度的温度差值t4,并执行运行状态工况判断;
[0053]
步骤三:根据运行状态工况判断的判断结果确定电加热管式反应器1所处运行状
态工况,根据电加热管反应器所处的运行状态工况选择控制器,控制器根据电加热管式反应器1的运行状态工况采取相应的控制措施,并执行步骤四;
[0054]
步骤四:在电加热管式反应器1为反应物加热的时间内,持续执行步骤二和步骤三。
[0055]
所述运行状态工况判断具体包括运行状态子步骤,所述运行状态工况判断子步骤具体为:将计算出的电加热管式反应器1温度和apc控制器3目标温度的温度差值t4与阈值温度t1、阈值温度t2和阈值温度t3进行比较,确定温度差值t4所处温度范围,并根据温度差值t4所处温度范围来确定电加热管式反应器1所处的运行状态工况。
[0056]
如图3所示,根据温度变化特性可以将整个飞温过程分成两个阶段:第一阶段称为过渡阶段,此时反应器温度已经开始超过设定值,可以看到这段时间内温度变化率较小但是温度在持续不断上升。第二阶段称为飞温阶段,反应器温度开始快速上升,直到烧穿反应器加热电流关闭反应器温度降低到保温温度,而反应器运行状态判断主要是在过渡阶段进行。
[0057]
步骤三中所述控制措施为先通过控制器改变电加热管式反应器1的加热输出电流,再通过加热输出电流来改变电加热管式反应器1内温度;控制器输出的加热输出电流随着运行状态工况的变化而变化。
[0058]
计算出的电加热管式反应器1温度和apc控制器3目标温度的温度差值t4处在小于或等于t1的温度范围内,所述电加热管式反应器处于工况一,而当电加热管式反应器1处于工况一时,apc控制器3控制电加热管式反应器1的加热输出电流变化,工况一运行状态下,加热电流输出值的输出步幅计算公式如下:
[0059]
a(step)=a(step_apc)
[0060]
其中:a(step)为电流输出步幅,a(step_apc)为apc控制器3输出步幅;
[0061]
计算出的电加热管式反应器1温度和apc控制器3目标温度的温度差值t4处在大于t1且小于或等于t2的温度范围内,所述电加热管式反应器1处于工况二,而当电加热管式反应器1处于工况二时,此时电加热管式反应器1温度在t1℃与t2℃之间,可能是某种干扰导致副反应增加放热较多,反应器存在飞温的可能,为了快速将该温度降到正常范围内,需要快速降低电流,所述电加热管式反应器1的加热输出电流由apc控制器3切换至防飞温控制器4控制,防飞温控制器4控制电加热管式反应器1的加热输出电流变化,工况二运行状态下,加热电流输出值的输出步幅计算公式如下:
[0062]
a(step)=k1*(1+t4)
[0063]
其中:k1为电加热管式反应器1处于工况二时防飞温控制器4降低电流的速度系数,t4为apc控制器3目标温度和电加热管式反应器1温度的差值;
[0064]
电加热管式反应器1温度和apc控制器3目标温度的温度差值t4处在大于t2且小于或等于t3的温度范围内,所述电加热管式反应器1处于工况三,而当电加热管式反应器1处于工况三时,此时说明在工况二采取的降电流措施下温度还在继续上升,反应器温度偏离apc目标值进一步增加,反应器飞温的可能性进一步扩大,为了快速将该温度降到正常范围内,防飞温控制器4进一步加快电流降低的速度,加热电流输出值的输出步幅计算公式如下:
[0065]
a(step)=k2*(1+t4)
[0066]
其中:k2为电加热管式反应器1处于工况三时防飞温控制器4降低电流的速度系数;
[0067]
计算出的电加热管式反应器1温度和apc控制器3目标温度的温度差值t4处在大于t3的温度范围内,所述电加热管式反应器1处于工况四,而当电加热管式反应器1处于工况四时,此时可以基本认为反应器运行状态马上会由过渡阶段转向飞温阶段,因此在这种工况下,防飞温控制器4直接输出最大电流,加热电流输出值的输出步幅计算公式如下:
[0068][0069]
其中:k3为电加热管式反应器1处于工况四时防飞温控制器4降低电流的速度系数,k为apc控制器3模型增益,a(sp)为反应器加热电流设定值,a(l)为防飞温控制器4电流下限值。
[0070]
如图4所示,在工况一状态下,apc控制器3进行正常控制,电加热管式反应器1加热输出电流保持在反应器加热电流设定值附近,电加热管式反应器1温度也保持在apc控制器3目标温度附近,但是一旦温度出现异常,工况一状态改变,apc控制器3无扰切换至防飞温控制器4控制,直至电流重新进入反应器加热电流设定值附近,但是由于温度存在一定滞后,会导致温度低于设定值较多,所以通过apc控制器3以最大步幅输出的方式将温度逐渐拉回到设定值附近。
[0071]
控制器通过控制电加热管式反应器1的电流mv虚开关的开闭来改变电加热管式反应器1的加热输出电流。
[0072]
步骤三中所述控制措施通过apc
‑
suite软件的图形化脚本模块7进行编写或修改。
[0073]
通过反应器运行状态判断模块5执行步骤二中所述运行状态工况判断,所述反应器运行状态判断模块5通过对采集到的电加热管式反应器1防飞温控制系统底层dcs数据进行逻辑计算与判断来获取反应器运行状态。
[0074]
步骤三中所述控制措施通过opc协议写入电加热管式反应器1防飞温控制系统底层dcs。
[0075]
以上所述的实施例只是本发明的一种较佳的方案,并非对本发明作任何形式上的限制,在不超出权利要求所记载的技术方案的前提下还有其它的变体及改型。