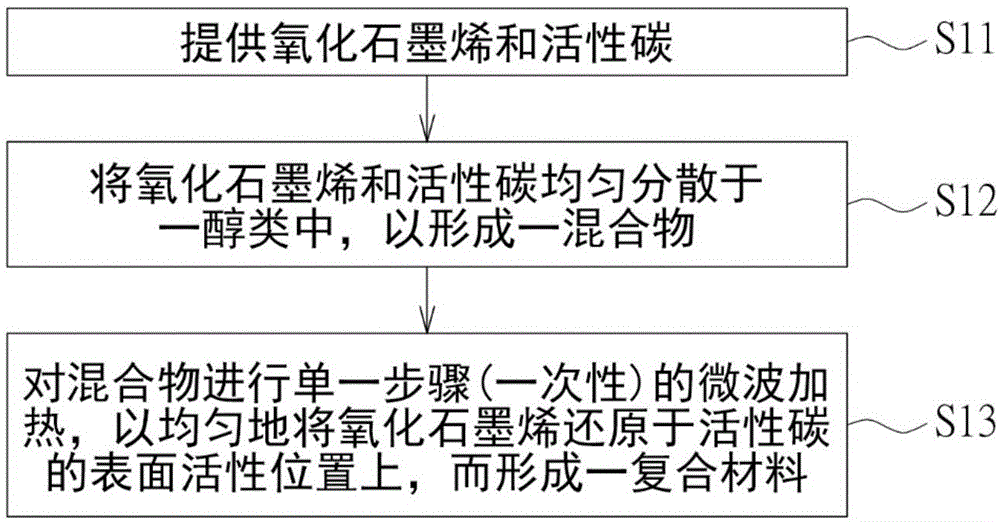
本发明是有关于一种复合材料与其制造方法及其应用,且特别是有关于一种石墨烯/活性炭复合材料及其制造方法与应用。
背景技术:
:电容脱盐技术(capacitivedeionization,cdi)及超级电容(supercapacitor)的关键材料为碳材料,需具备多孔性、高比表面积与高导电性等特性,目前主流以活性炭(activatedcarbon)为主,因为原料来源多,其量产成本很低是主要诱因外,同时具备高比面积与高脱盐量特性是其应用优势。许多研究针对活性炭改质使之具有高比表面积进而提升电极比电容值与高脱盐率。然而,由于活性炭的导电性普遍不佳,因此在制作电极的过程需要额外添加导电材(例如:石墨)。但石墨本身比表面积远低于活性炭材料,因此其吸附离子能力有限,然而额外添加导电材会降低活性炭在电极中的比重,影响其有效离子吸附位置,降低电极表现。因此,如何研发出具高导电性的活性炭复合材料为研发重要方向。由于石墨烯(graphene)具有优越的性质,例如超高导热系数(5300w/m·k)而有高散热性、高电子迁移率(200,000cm2/v·s)而有高导电性、透光性与优良的机械性能,而被认为是改质活性炭的极具潜力的材料。但是传统制备石墨烯的方法相当耗时,通常需要数天的时间,而还原氧化石墨烯的阶段使用的化学还原剂具有毒性,不具环境友善性以及需额外处置成本,因此限制石墨烯发展应用性。此外,传统制备石墨烯过程中结构容易发生堆叠现象,一旦发生堆叠,其电极效能便会大幅受影响。因此如何研发出石墨烯改质活性炭的高效能复合材料,以维持低成本又可迅速制备,而制得的复合材料的碳层结构又不易堆叠,以具有高导电性,实为研发人员的重要目标。技术实现要素:本发明的目的在于提供一种复合材料与其制造方法,以解决现有技术中复合材料制备耗时、成本高昂且碳层结构容易堆叠的缺陷。本发明的另一目的在于提供一种应用复合材料的电极及其制造方法。为实现上述目的,本发明提出一种复合材料制造方法,包括:提供氧化石墨烯和活性炭;将所述氧化石墨烯和所述活性炭均匀分散于一醇类中,以形成一混合物;以及对所述混合物进行单一步骤的微波加热,以均匀地将前述氧化石墨烯还原于所述活性炭的表面活性位置上,而形成一复合材料。本发明所述的制造方法,其中,所述氧化石墨烯及所述活性炭的添加量的重量比介于0.05~0.5范围之间。本发明所述的制造方法,其中,所述氧化石墨烯及所述活性炭的添加量的重量比介于0.1~0.25范围之间。本发明所述的制造方法,其中,所述醇类与所述氧化石墨烯的添加量的重量比介于0.01~0.2范围之间。本发明所述的制造方法,其中,所述醇类具有碳原子数c2~c4的碳链。本发明所述的制造方法,其中,在分散于所述醇类之前,所提供的所述活性炭的比表面积介于500m2/g至3000m2/g之间。本发明所述的制造方法,其中,在分散于所述醇类之前,所提供的所述活性炭的孔径介于1nm至1000nm范围之间。本发明所述的制造方法,其中,所述微波加热的时间短于30分钟。本发明所述的制造方法,其中,前述微波加热的时间在3分钟至小于30分钟的范围之间。本发明所述的制造方法,其中,所述微波加热的温度介于50℃~300℃范围之间。本发明所述的制造方法,其中,所述微波加热的功率介于400w~1600w范围之间。本发明所述的制造方法,其中,所述微波加热时所使用的微波频率介于0.3ghz至300ghz范围之间。为实现上述目的,本发明还提出一种复合材料,根据上述的制造方法而制得。为实现上述目的,本发明还提出一种电极,包括一导电基材,和一材料混合物,所述材料混合物涂布于导电基材上,材料混合物至少包括:根据上述的制造方法而制得的复合材料;以及至少一黏着剂。为实现上述目的,本发明还提出一种电极制造方法,包括:提供一导电基材;混合黏着剂与根据上述的制造方法而制得的复合材料,并以溶剂稀释和均匀搅拌,以形成一糊状浆料;涂布所述糊状浆料于所述导电基材上,于干燥后制得一复合碳电极。本发明所述的电极制造方法,其中,所述复合材料与所述黏着剂的重量比介于7:3至9:1的范围。本发明所述的电极制造方法,其中,所述溶剂包括n-甲基吡咯烷酮和二甲基乙酰胺中的一种或两种。本发明的有益效果:可利用单一步骤微波加热方式迅速地将氧化石墨烯均匀还原于活性炭材料上,进而使制得的复合材料具有改善的高导电性与高比电容值。复合材料也适合应用于电容脱盐(capacitivedeionization,cdi)及超级电容(supercapacitor)的电极制作。附图说明图1为本发明一实施例的复合材料制造方法的流程图。图2为本发明一实施例的电极制造方法的流程图。图3a为氧化石墨烯(grapheneoxide,go)和经由本发明一实施例的制程中以不同微波加热的功率(400w、800w、1200w)还原氧化石墨烯的温度分布曲线。图3b分别为氧化石墨烯和经由本发明一实施例的制程中以不同微波加热的功率(400w、800w、1200w)还原氧化石墨烯的xrd图谱。图4(a)~4(f)为活性炭、石墨和石墨烯的电子显微镜(sem)影像。图5(a)、5(b)是不同复合碳电极的表面形貌的电子显微镜影像。图6为氧化石墨烯(grapheneoxide,go)和经由不同热制程还原氧化石墨烯的xrd图谱。图7为尚未还原的活性炭、和经由不同热制程还原氧化石墨烯的复合碳电极的循环伏安图(电解液为0.5m氯化钠水溶液,扫描速率为0.01v/s)。图8为尚未还原的活性炭、和经由不同热制程还原氧化石墨烯的复合碳电极的电化学阻抗频谱图。图9为不同氧化石墨烯添加量制备而成的碳复合电极的循环伏安图的电化学分析(电解液为0.5m氯化钠水溶液,扫描速率为0.01v/s)。其中,附图标记:s11、s12、s13、s21、s22、s23:步骤具体实施方式在此
发明内容的实施例中,提出一种复合材料与其制造方法,以及应用此复合材料所制得的电极及其制造方法。根据本发明,可快速制备一种复合材料,此复合材料包括石墨烯和活性炭。实施例利用单一步骤微波加热方式将氧化石墨烯均匀地还原于活性炭材料上,可在低温和常压下进行,而且还原时间可大幅缩短(例如从传统制备方式的数十小时缩短至几分钟,还原速率大幅提升);再者,可选用环境无毒性的醇类做为化学还原剂(取代传统制备方式中具毒性的化学还原剂如联氨)来进行氧化石墨烯的还原。此外,根据实施例,氧化石墨烯可均匀地还原在活性炭表面,可避免石墨烯因为疏水性彼此间团聚再堆叠的情形,相较于传统制备方式所制得的石墨烯/活性炭的复合材料,实施例的复合材料因而可具有改善的高导电性与高比电容值。因此,实施例所提出的复合材料与其制造方法,不但在制造方法上具有无毒、容易进行(低温、常压、单一步骤微波加热)并大幅缩短制备时间,所制得的复合材料也兼具活性炭的高比表面积与石墨烯的高导电性的优点。此
发明内容的实施例其应用十分广泛,特别是适合应用于作为电容脱盐(capacitivedeionization,cdi)及超级电容(supercapacitor)的电极材料,例如在不需添加导电材的情形下,使用实施例的复合材料与黏着剂,以制备用于电容脱盐及超级电容的电极。当然,本发明并不仅于此些应用。以下提出相关实施例,配合附图以详细说明本发明所提出的复合材料的制造方法。然而本发明并不仅限于此。实施例中的叙述,如制程步骤、材料应用和结构细部等等,仅为举例说明之用,本发明欲保护的范围并非仅限于所述的态样。需注意的是,本发明并非显示出所有可能的实施例,相关领域者可在不脱离本发明的精神和范围内对实施例的结构和制程加以变化与修饰,以符合实际应用所需。因此,未于本发明提出的其他实施态样也可能可以应用。再者,实施例中所提出的实验与其结果仅为本发明的其中几组示例用的内容,以利清楚例示依实施例所制得的复合材料的特性,该些示例内容并非用以限制本发明的保护范围。因此,说明书和附图内容仅作叙述实施例之用,而非作为限缩本发明保护范围之用。图1为本发明一实施例的复合材料制造方法的流程图。如图1所示,于步骤s11,为提供氧化石墨烯和活性炭。接着,于步骤s12,将氧化石墨烯和活性炭均匀分散于一醇类中,以形成一混合物。之后,于步骤s13,对混合物进行单一步骤(一次性)的微波加热,以均匀地将氧化石墨烯还原于活性炭的表面活性位置上,而形成一复合材料。其中,醇类做为将氧化石墨烯还原于活性炭表面上的一还原剂。一实施例中,石墨烯/活性炭的复合材料由氧化石墨烯、活性炭、醇类于特定比例范围下进行混合,例如,一次性地在微波加热方式下完成。例如,一示例中,氧化石墨烯及所述活性炭的添加量的重量比介于0.05~0.5范围之间。再一示例中,氧化石墨烯及所述活性炭的添加量的重量比介于0.1-0.25范围之间。若氧化石墨烯与所述活性炭的添加量的重量比过低时,则无法有效增加复合材料的导电性;当氧化石墨烯与前述活性炭的添加量的重量比过高时,石墨烯易堆叠降低了复合材料的比表面积,两种情况下皆使石墨烯/活性炭复合材料的比电容值偏低。实施例中,可应用的活性炭种类并没有特别限制,例如可以是包括化学法活性炭、物理法活性炭、物理-化学法活性炭与化学-物理法活性炭等。于一示例中,活性炭例如是使用(但不限制是)acp(石油焦类)或acw(木质类,景明化工)。再者,于一实施例中,于分散于所述醇类之前,所提供的活性炭的比表面积例如是(但不限制地)介于500m2/g至3000m2/g,其孔径(poresize)例如是(但不限制地)介于1nm至1000nm范围之间。值得注意的是,根据本发明,与活性炭混合而形成待微波的混合物的另一原料是氧化石墨烯,而非石墨烯。可应用的氧化石墨烯的制备方式也没有特别限制,例如可以由brodie法、staudenmaier法和hummers法制备而成。另外,实施例中,用来分散氧化石墨烯和活性炭并做为还原剂的醇类,其与氧化石墨烯的添加量的重量比,例如是(但不限制是)介于0.01~0.4范围之间。例如于一实验中,80mg氧化石墨烯分散于30ml乙二醇中,添加量的重量比为30/80=0.4。当然本发明并不限制于前述范围,于另一实施例中醇类与氧化石墨烯之添加量的重量比,例如是介于0.01-0.2之间。另外,实施例中,醇类例如可选用具有碳原子数为c2~c4的碳链的醇类种类。于一示例中,醇类例如为(但不限制是)乙二醇,以做为还原剂,使氧化石墨烯还原分散于活性炭表面上。当碳数愈高时,醇类极性降低因而影响亲水性活性炭的分散性及微波加热效果。再者,一实施例中,对混合物进行微波加热的单一步骤(i.e.一次性步骤)中,微波加热之时间可短于30分钟。例如,微波加热的时间在3分钟至小于30分钟的范围之间。于一实施例中,微波加热的温度介于50℃~300℃范围之间;或是100℃~200℃范围之间。另外,于一实施例中,微波加热的功率介于400w~1600w范围之间。若上述微波加热的功率过低,则使氧化石墨烯还原不完全,若上述微波加热的功率过高,则会破坏碳材结构。例如,微波加热的功率在400w~1200w的范围之间。图3a和图3b分别为氧化石墨烯(grapheneoxide,go)和经由本发明一实施例的制程中以不同微波加热的功率(400w、800w、1200w)还原氧化石墨烯的温度分布曲线以及xrd图谱。如图3b所示,微波加热的功率为400w时在10.4度时尚有峰部,表示氧化石墨烯还原不完全。另外,于一示例中,微波加热的功率例如是(但不限制是)800w。于一实施例中,微波加热时所使用的微波频率例如是(但不限制是)介于0.3ghz至300ghz范围之间。值得注意的是,实施例中所提出的这些数值是做为举例说明之用,而非用以限制本发明范围之用。当然,实际应用时,微波加热的条件可视欲加热的材料内容(也即混合物的各成分份量与比例)而可做相应调整和搭配;例如微波加热的时间可和其余条件(例如微波温度、功率、频率等)相互配合,使氧化石墨烯可快速还原于活性炭表面上。于一示例中,对于包括80ml氧化石墨烯、0.4g活性炭和30ml乙二醇的一混合物,例如是可用功率800w微波进行加热3分钟,即可快速还原氧化石墨烯于活性炭表面上。根据实施例提出的方式可在低温和常压下使氧化石墨烯与高比表面积活性炭通过无毒性还原剂(例如乙二醇),利用单一步骤微波加热方式(局部高温加热特性),使氧化石墨烯均匀地还原在活性炭材表面活性位置上,而快速制得一种复合材料,大幅缩短制备时间(数十小时缩短至数分钟)。据此,实施例制得的复合材料(也可称为石墨烯/活性炭复合材料)包括:上述活性炭以及均匀地还原于活性炭的表面活性位置的石墨烯。另外,实施例制得的复合材料可改善传统混掺方式下石墨烯分散不佳的状况,也可避免石墨烯因苯环的π-π吸引力而发生层与层的结构再堆叠的情况。实施例所制得的复合材料,经实验证实,实具有高导电性与高比电容值。因此实施例适合用以进行复合碳电极制备,以应用于电容脱盐技术及超级电容。由于石墨烯的均匀分散(还原)于活性炭的表面活性位置,可使之充分展现电极特性。石墨烯/活性炭复合材料兼具高导电性与高比表面积,制作电极过程中无须添加导电材,活性炭材料比重增加,增加碳电极吸附能力。通过实施例提出的制备方法,可迅速、简易地制备出实施例的石墨烯/活性炭复合材料及其应用的电极。实施例所提出的低成本但高效能的石墨烯改质活性炭复合材料十分有利于业界量化生产的应用。在此也提出可应用该复合材料的其中一种电极制造方法,但仅为举例说明之用,并非用以限制本发明的应用与其细节。图2为本发明一实施例的电极制造方法的流程图。如图2所示,于步骤s21,提供一导电基材、一或多种黏着剂、实施例的复合材料与一或多种溶剂。接着,于步骤s22,混合一或多种黏着剂与实施例的复合材料,并以一或多种溶剂进行稀释和均匀搅拌,以形成一糊状浆料。之后,于步骤s33,涂布糊状浆料于导电基材上,于干燥后(例如烘箱干燥)制得一复合碳电极。据此,制得的复合碳电极包括一材料混合物,该材料混合物涂布于该导电基材上,且材料混合物至少包括实施例的复合材料以及至少一黏着剂。一实施例中,电极制作的糊状浆料干燥成膜(例如烘箱干燥)的温度条件例如是(但不限制是)70℃~140℃。一实施例中,实施例的复合材料与黏着剂的重量比例如是(但不限制是)介于7:3至9:1的范围。于实施例中所应用的溶剂可以是单一溶剂,或是两种或两种以上的溶剂所形成的混合物。本发明对应用溶剂所包含的化合物数量并没有特别限制。一实施例中,溶剂例如是(但不限制是)包括n-甲基吡咯烷酮(n-methyl-2-pyrrolidone,nmp)或二甲基乙酰胺(dimethylacetamide,dmac)或前述两者。以下提出部分相关实验为例示说明,包括如何制备实施例的复合材料、复合材料的特性(如电子显微镜影像、石墨烯结构分析)、如何应用实施例的复合材料制作电极、及电极特性(如以电化学分析量测比电容值、进行电容脱盐实验等)。当然,以下实验内容及测试结果仅为举例说明之用,并非用以限制本发明的复合材料及其应用的范围。实施例<微波加热制备石墨烯/活性炭复合材料>实施例提出以微波加热单一步骤制备石墨烯活性炭复合材料,可应用作为电容脱盐及超级电容的电极。复合材料制备方法如下。首先,参照hummers法制备氧化石墨烯,接着将80mg的氧化石墨烯和0.4g活性炭(氧化石墨烯:活性炭重量比为1:5)混合后加入30ml的乙二醇(做为还原剂)内,活性炭使用acp(石油焦类)或acw(木质类,景明化工),在回流条件下以功率800w进行微波加热3分钟,待反应结束并冷却至室温后,接着加入乙醇以转速5000rpm离心20分钟,并重复3次离心步骤后以清洗残留的乙二醇溶剂,干燥后便可以获得石墨烯/活性炭复合材料。<石墨烯/活性炭复合材料电子显微镜影像>图4(a)~4(f)为活性炭、石墨和石墨烯的电子显微镜(sem)影像。其中图4(a)及4(b)为活性炭影像,图4(c)及4(d)为石墨影像,影像图4(e)及4(f)为石墨烯影像。图4(e)及4(f)的电子显微镜影像显示出片状的石墨烯有较多的皱褶,这代表和其他的碳材料(活性炭、石墨)相比具有较高的比表面积。图5(a)、5(b)是不同复合碳电极的表面形貌的电子显微镜影像。图5(a)、5(b)是以sem影像分析经由不同的还原制程所制备出不同的复合碳电极的表面形貌图,其中图5(a)为高温还原的石墨烯和活性炭混掺的复合材料的sem影像(亦即传统制备方式);图5(b)为实施例利用微波加热单步骤制备石墨烯/活性炭复合材料的sem影像。由图5(a)可观察到,如其中一种传统制备方式,若是先将氧化石墨烯还原后再与活性炭混掺而制备出的复合材料,则石墨烯容易因团聚而产生再堆叠情形,进而影响了石墨烯在活性炭间的分布情形以及表面积。由图5(b)可观察到,实施例的微波加热法还原制程为单一步骤的快速制程,可以直接将氧化石墨烯还原并均匀分布在活性炭表面,避免了石墨烯彼此间团聚再堆叠情形发生。<石墨烯结构鉴定-x射线绕射分析>图6为氧化石墨烯(grapheneoxide,go)和经由不同热制程还原氧化石墨烯的xrd图谱。在此实验中,以x光绕射仪(x-raydiffractometer,xrd)分析氧化石墨烯经由一般热还原法(thermalreduction)以及经由实施例的微波加热的还原情形。其中曲线go代表未还原的氧化石墨烯,曲线tr代表经过传统热还原之后的石墨烯,曲线mr代表经过实施例的微波加热还原之后的石墨烯。其中y轴为信号强度(intensity),x轴为2倍绕射角(2θ)。对照未还原的氧化石墨烯(曲线go),可以发现在大约10.4°的六角形石墨(002)方位从经过微波加热还原3分钟后,几乎消失不见,此因石墨烯层与层之间的含氧官能基被移除后,层间距离有缩小的情形。而一般经过热还原之后的石墨烯(曲线hr),在大约24.5°产生一宽信号,代表石墨烯层与层之间的再堆叠情形。据此,根据实施例的微波加热还原后所形成的石墨烯(曲线mr),在xrd图谱中没有明显的绕射峰信号出现。<电极制作与电容测试>于一电极制作的示例中,将实施例的石墨烯/活性炭复合材料与聚偏二氟乙烯(pvdf)黏着剂以重量比9:1的比例混合后,添加n-甲基吡咯烷酮(nmp)溶剂,并均匀搅拌24小时使之成为糊状浆料。将糊状浆料以涂布间隙300μm刮刀使用涂布机均匀涂布在50μm钛箔上,送入140℃烘箱中烘干4小时,完成应用实施例的复合碳电极的制备。之后,可对制得的复合碳电极进行多种电化学分析。<复合碳电极的电化学分析>1.电极的电容测试电极的电容值测定以循环伏安法(cyclicvoltammetry,cv)分析得之。测试溶液为0.5m氯化钠(nacl)水溶液,工作电极面积1cmx1cm,对电极为白金线,参考电极为氯化银电极(agcl/ag),电位扫描范围为-0.5v~0.5v,扫描速率为10mv/s,电容值计算方法为对cv曲线积分得到的电荷变化量除以电位窗及电极活性材料重量。图7为尚未还原的活性炭、和经由不同热制程还原氧化石墨烯的复合碳电极的循环伏安图(电解液为0.5m氯化钠水溶液,扫描速率为0.01v/s)。其中曲线acp代表尚未还原的活性炭(acp),曲线acp/gtr(acp/graphenethermalreduction)代表包括了以传统热还原方式制得复合材料的复合碳电极,曲线acp/gmr(acp/graphenemicrowavereduction)代表包括了以实施例微波加热方式制得复合材料的复合碳电极。图7结果显示,尚未还原的活性炭(acp)以及用复合材料所制备的电极,其cv曲线皆呈现矩形形状,显示为理想的双电层电容(electricaldoublelayercapacitance,edlc)行为,其中又以实施例的包括单一制程微波加热还原石墨烯制备的复合碳(石墨烯/活性炭)电极图形呈现结果,显示有较高的电容特性,其比电容值最高可达到190.9f/g,平均则有170.5f/g的高比电容值,和原本使用石墨作为导电材的单纯acp活性炭电极的平均比电容值100.4f/g相比,大幅提升了约70%。因此,如图7结果显示,实施例的微波加热还原氧化石墨烯而制成的石墨烯/活性炭复合材料,实具有更高的比表面积,进而得到更佳的电容表现。2.电极的电化学阻抗分析图8为尚未还原的活性炭、和经由不同热制程还原氧化石墨烯的复合碳电极的电化学阻抗频谱图。其分析电化学反应中离子与电子的传导与扩散产生的阻抗。其中曲线acp代表尚未还原的活性炭(acp),曲线acp/gtr代表包括了以传统热还原方式制得复合材料的复合碳电极,曲线acp/gmr代表包括了以实施例微波加热方式制得复合材料的复合碳电极。图8的电化学阻抗频谱(electrochemicalimpedancespectrum,eis)结果显示,实施例的复合碳电极(包括了单一制程微波加热还原的石墨烯的复合材料)在高频区具有最小的半圆形,代表电极材料和集电板具有最低的内电阻(也即,阻抗频谱中的半圆越小,内电阻就越小),而即使在低频区间,也呈现了垂直的图形,这是因为氧化石墨烯可以均匀地被还原成高导电度的石墨烯在活性炭表面,有利于电子在电极之间传递,降低的阻抗而提升电容表现。根据上述的循环伏安电容测试以及电化学阻抗测试,实施例的微波加热还原氧化石墨烯而制成的石墨烯/活性炭复合材料,实具有更高的比表面积和更低的电化学阻抗,进而得到更佳的电容表现。而应用于超级电容时,比电容值很重要。比电容值越大,导电效果越好。<不同氧化石墨烯添加量制备而成的复合碳电极的特性分析>图9为不同氧化石墨烯添加量制备而成的碳复合电极的循环伏安图的电化学分析(电解液为0.5m氯化钠水溶液,扫描速率为0.01v/s)。此实验中,分析不同比例的氧化石墨烯加入活性炭后的电容值表现,此示例中氧化石墨烯的添加量分别为200mg、100mg、80mg、40mg以及20mg,也即氧化石墨烯(go):活性炭(acp)重量比分别为0.5、0.25、0.2、0.1及0.05。经过如前述实施例方法的单一步骤微波还原后所制得的复合材料,取其制得复合碳电极,并进行循环伏安的电化学分析。其结果如图9所示,平均比电容值分别为90.3、138.9、170.5、117.4以及96.2f/g。在相同go:acp添加重量比下,使用实施例的微波加热方式制得复合材料电极的比电容值较传统加热的高出38%(由123.5提高至170.5f/g),且相较于单纯活性炭(acp)电极,以go:acp添加重量比0.1~0.25条件制成的电极,其比电容值有明显提升。相关实验结果如表1所示。表1另外,由拉曼(raman)分析结果可以得知,当氧化石墨烯添加量太多时,石墨烯在还原过程中容易堆叠在一起,使得拉曼信号i2d/ig值下降,减少了复合碳电极的表面积,造成比电容值下降;但是当氧化石墨烯添加量太少时,还原后又会因为石墨烯在碳材间无法构成有效的导电网络,使得复合材料的电容表现也会较差。例如上述一示例中(i.e.100mg、80mg以及40mg的氧化石墨烯(氧化石墨烯:活性炭重量比分别为0.25、0.2及0.1),当氧化石墨烯添加量在大约80mg(重量比0.2)时,相较于其他两个氧化石墨烯添加量的重量比为0.25和0.1,有较好的平均比电容值170.5f/g。应用时选择实验结果较好的平均比电容值有利于之后的制程优化。虽然如图9所示的结果,不同的氧化石墨烯及活性炭的添加量的重量比所测得的比电容值不同,不过本发明并不因这些比电容值的大小而限制在氧化石墨烯及活性炭的添加量的重量比必须是0.2。于一应用中,氧化石墨烯及活性炭的添加量的重量比介于0.05~0.5为本发明实施例可应用的范围,相较于其他传统制法所得到的复合碳电极,皆具有提升的比电容值。<以不同活性炭材进行制备复合碳电极的电容分析与比较>关于实施例的复合材料,前述实验使用活性炭acp制备。而实验中也使用不同的活性炭材(acw)进行单一制程微波加热,并利用制得的复合材料制备复合碳电极,并量测其比电容值。如表2所示,以传统制备电极方式与实施例的微波加热方式制备电极,并进行电容比较,实施例的复合碳电极的比电容值最高可以达到68.6f/g,和用传统加入导电石墨制备而成的复合碳电极相比较,其比电容值52.1f/g提升了31.7%,显示实施例提出的制法适用于不同碳材的改质,都能大幅提升复合碳电极的比电容值。表2<石墨烯/活性炭复合碳电极之电容脱盐实验>实验中也进行纯碳电极(acw与acp)与石墨烯改质的复合碳电极(包括实施例的石墨烯/活性炭复合材料)的电容脱盐效能比较,实验结果整理于表3。表3的电容脱盐数据显示,纯acw碳电极与acp碳电极的脱盐量分别为5.4±0.9mg/g与10.3±0.6mg/g,主要差异为活性炭本身的特性不同,acp碳材比表面积高于acw碳材,因此提供更多的离子吸附位置。而如实施例的制备方式,经过微波加热制得改质的石墨烯复合碳电极后,电容脱盐量分别可提升至7.2±0.5mg/g与18.6±1.2mg/g,分别提升1.3与1.8倍,因此经石墨烯改质的碳材可提升导电性与活材利用率(且不用添加导电材),而在电容脱盐量上有显著增加。因此应用本发明实施例于电容脱盐技术时,电容脱盐量实具有显著的提升。表3电极材料脱盐量(mg/g)acw碳电极5.4±0.9acp碳电极10.3±0.6acw/石墨烯复合碳电极7.2±0.5acp/石墨烯复合碳电极18.6±1.2根据上述实施例提出的一种复合材料与其制造方法,以单一步骤微波加热方式将氧化石墨烯均匀地还原于活性炭材料上。除了可在低温和常压环境下进行还原,和传统热还原方式相比,实施例的还原速率大幅提升(还原时间可从传统制备方式的数十小时(例如48小时)大幅缩短至几分钟(例如3分钟))。再者,可选用环境无毒性的醇类做为化学还原剂(取代传统制备方式中具毒性的化学还原剂如联氨)来进行氧化石墨烯的还原,而且氧化石墨烯可均匀地还原在活性炭表面,可避免石墨烯因为疏水性彼此间团聚再堆叠的情形。因此,与其他制程相比,根据实施例的制程可迅速制备出高导电性与高比电容值的石墨烯/活性炭复合材料。因此实施例特别适合应用于制作电容脱盐及超级电容的电极。以实施例的石墨烯/活性炭复合材料制作电极时,无须添加其他导电材,且以复合材料的形式制作电极能大幅降低碳材料制备成本。综合而言,通过实施例提出的制备方法,可迅速简易地制备出实施例的石墨烯/活性炭复合材料及其应用的电极,作为电极应用于电容脱盐技术及超级电容可同时兼具活性炭高比表面积与石墨烯高导电性的优点。此实施例所提出的低成本但高效能的石墨烯/活性炭复合材料十分有利于业界量化生产的应用。如上述步骤或实验内容,是用以叙述本发明的部分实施例或应用例,本发明并不限制于上述步骤的范围与应用态样。再者,示例的步骤可根据实际应用的需求而调整。因此例示数值与实验结果图仅为举例说明之用,而非限制之用。本领域普通技术人员当知,应用本发明的相关步骤细节与制得结构等,都可能以依实际应用样态所需而可能有相应的调整和变化。当然,本发明还可有其它多种实施例,在不背离本发明精神及其实质的情况下,熟悉本领域的技术人员可根据本发明作出各种相应的改变和变形,但这些相应的改变和变形都应属于本发明权利要求的保护范围。当前第1页12