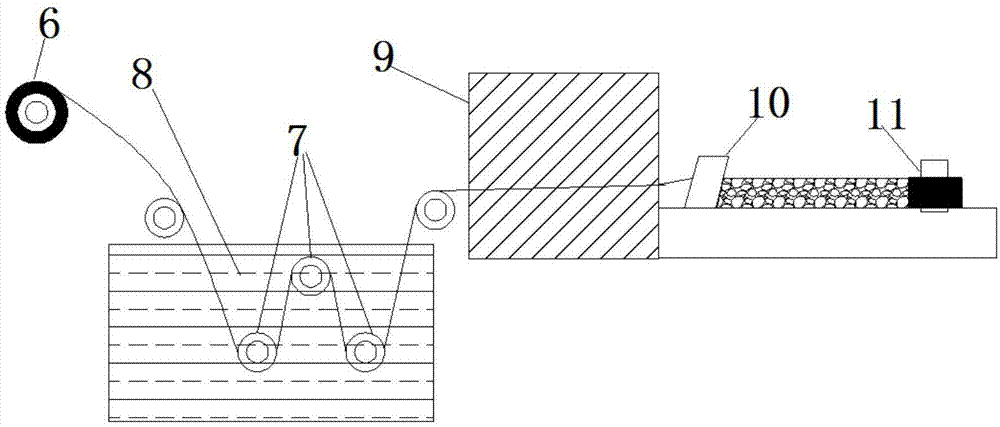
本实用新型涉及无线充电
技术领域:
,特别涉及一种低损耗隔磁片制备装置及隔磁片。
背景技术:
:无线充电过程中会产生交变电磁场,而当交变电磁场遇到金属,会产生电子涡流,在金属上产生热能,造成传输效率较低,电能浪费,如果充电电池内部金属板受到该磁场的影响,产生的涡流损耗会引起电池发烫,引起爆炸或火灾不安全,而且该磁场会干扰周围器件,影响整个充电器的正常工作。因此在技术层面上必须采用屏蔽材料或者吸波材料,来阻挡磁力线外泄,来保障整个充电系统的安全高效的工作!在实际应用中发射端和接收端线圈都放置在屏蔽上,以达到提高效率,降低干扰的目的。常规的技术是使用一个高导磁率的铁氧体和常规制作的非晶纳米晶来做屏蔽材料。Qi充电标准中的充电频率范围在100-200KHz之间,在小功率使用铁基或者钴基非晶、纳米晶材料制做低损耗隔磁片的效果与常规非晶纳米晶,铁氧体差别不是很大,在10-20W功率下铁基或者钴基非晶、纳米晶材料制做低损耗隔磁片的效果明显优于铁氧体,常规制作非晶纳米晶。市面带有无线充电手机,基本都采用非晶或者纳米晶屏蔽片。随着充电需求功率的增加和充电新技术的产生,效率提高、工作温升较低一直以来都是无线充电行业追求的目标。许多专利均提到了非晶叠片、滚压破碎、蚀刻工艺,等压合时使胶填满碎片的间隙,从而增加磁阻、降低涡流损耗,以提高充电效率。目前的屏蔽材料生产工艺方法具有很大的弊端,如传统滚压破碎后的碎片杂乱无章形状缝隙大小不一致(胶体填充大小不一的缝隙,造成材料层间磁性材料在一定频率下介电常性能不一),造成性能不稳定(磁导率差值过大)。蚀刻工艺,虽然可以控制其形状和缝隙宽度,但是对贴合胶层的带材蚀刻,蚀刻工艺(同FPC蚀刻法):非晶、纳米晶合金带材→除油→水洗→干燥→贴膜→曝光→显影→水洗→蚀刻图案→水洗→去膜→水洗→酸洗→水洗→干燥→检验。以上工艺过程复杂制程较长,胶层带材又经过强酸碱溶液和蚀刻溶液,而胶层性能变化且缝隙处不容易干燥带材易氧化。成本造价高,且都是经过化学药品处理和加温,性能一致性差,充电效率较低。技术实现要素:本实用新型的目的就在于为了解决上述问题而提供一种低损耗隔磁片制备装置及隔磁片,使得涡流损耗进一步降低,充电效率进一步提高、温升较低且工艺简单、成本较低绿色环保。为了解决上述问题,本实用新型提供了一种技术方案:一种低损耗隔磁片制备装置,包括放料轴、缓冲辊轮、容器、烘干器、导向轮、张力轴、泡棉辊轮和注液器;所述放料轴位于容器左侧上端;所述容器中设有数个缓冲辊轮;所述缓冲辊轮的外表面上均固定包覆有一个泡棉辊轮;所述泡棉辊轮上均固定连通有一个注液器;所述容器的右侧上端设有一个烘干器;所述烘干器的右侧设有一个张力轴;所述张力轴与烘干器之间设有一个导向轮。作为优选,还包括热处理炉,所述热处理炉位于张力轴的右侧。一种低损耗隔磁片制备装置生产的隔磁片的具体结构为:包括PET塑料、软磁带材图形化细块、双面胶和离型膜;所述软磁带材图形化细块为3个,以相互间隔的方式排列;上端所述软磁带材图形化细块的上表面上设有一个PET塑料;下端所述软磁带材图形化细块的下方设有一个离型膜;上端所述软磁带材图形化细块与中端所述软磁带材图形化细块之间设有双面胶;中端所述软磁带材图形化细块与下端所述软磁带材图形化细块之间设有双面胶;下端所述软磁带材图形化细块与离型膜之间设有双面胶。作为优选,所述隔磁片的外表面上进行图形化处理。作为优选,所述容器的溶液为氧化锌、氧化镁、三氧化二铝、二氧化硅等粉体中的至少一种与酒精偶联剂混合形成的混合物溶液,其粉体重量含量为3%-50%,偶联剂重量含量为0.5%-3%。本实用新型的有益效果:本实用新型具有结构合理简单、生产成本低、安装方便,功能齐全,通过本实用新型表面处理工艺,粉体表面绝缘、表面磷化法和表面氧化法再通过图形网筒与带材接触形成均匀有序的形状和一定尺寸的缝隙,使得隔磁片的电磁性能磁导率相对平均,磁损较小,品质因数较高,形状真正大小均匀,缝隙大小一致性好,胶体填充性较佳,表面阻抗变大涡流损耗小,再加上带材表面处理后使得涡流损耗进一步降低,使得充电效率得提高,且隔磁片稳定性好,自动化程易于实现。附图说明为了易于说明,本实用新型由下述的具体实施及附图作以详细描述。图1为本实用新型的结构示意图。图2为本实用新型的俯视结构示意图。图3为本实用新型隔磁片的结构示意图。图4为本实用新型隔磁片表面图形化示意图。图5为本实用新型隔磁片表面图形化示意图。图6为本实用新型隔磁片表面图形化示意图。具体实施方式如图1至图3所示,本具体实施方式采用以下技术方案:一种低损耗隔磁片制备装置,包括放料轴6、缓冲辊轮7、容器8、烘干器9、导向轮10、张力轴11、泡棉辊轮12和注液器13;所述放料轴6位于容器8左侧上端;所述容器8中设有数个缓冲辊轮7;所述缓冲辊轮7的外表面上均固定包覆有一个泡棉辊轮12;所述泡棉辊轮12上均固定连通有一个注液器13;所述容器8的右侧上端设有一个烘干器9;所述烘干器9的右侧设有一个张力轴11;所述张力轴11与烘干器9之间设有一个导向轮10。其中,还包括热处理炉,所述热处理炉位于张力轴11的右侧。如图1至图3所示,一种低损耗隔磁片制备装置生产的隔磁片的具体结构为:包括PET塑料2、软磁带材图形化细块3、双面胶4和离型膜5;所述软磁带材图形化细块3为3个,以相互间隔的方式排列;上端所述软磁带材图形化细块3的上表面上设有一个PET塑料2;下端所述软磁带材图形化细块3的下方设有一个离型膜5;上端所述软磁带材图形化细块3与中端所述软磁带材图形化细块3之间设有双面胶4;中端所述软磁带材图形化细块3与下端所述软磁带材图形化细块3之间设有双面胶4;下端所述软磁带材图形化细块3与离型膜5之间设有双面胶4。其中,如图4到图6,所述隔磁片的外表面上进行图形化处理;所述容器8的溶液为氧化锌、氧化镁、三氧化二铝、二氧化硅等粉体中的至少一种与酒精偶联剂混合形成的混合物溶液,其粉体重量含量为3%-50%,偶联剂重量含量为0.5%-3%。一种低损耗隔磁片制备装置及隔磁片,可以获得一种隔磁片,其结构为权利要求3所述叠层形状化,为单层或多层软磁材料叠加形成的隔磁片,具有优良的电磁波屏蔽功能。叠层,胶体会进入和填满缝隙,这样可以保证磁片间的绝缘度,复合材料的介电性能和避免带材磁性能的老化,并保证结构性能的稳定。如表1所示,本实用新型通过粉体表面绝缘、表面磷化法表面处理,缝隙尺寸和形状大小的相同,得到两种磁片样品。通过对比未表面处理的隔磁片,分别为实例1、实例2、实例3、和传统滚压制作的隔磁片对比:表1案例图形尺寸(mm)叠层磁片厚度(mm)电感(uH)组件RS(mΩ)实例110.16.25180实例210.16.21181实例310.16.25190传统辊压10.16.26210通过表1可以看出,相同图形缝隙尺寸,电感几乎一致,组件的阻抗值从小变大。表2通过本实用新型通过粉体表面绝缘、表面磷化法表面处理,缝隙尺寸和形状大小的相同,得到2种磁片样品,测试其充电效率得到表2的结果,降低表面涡流损耗才能更近一步提高充电效率。从与辊压破碎工艺对比,充电效率最低的实例3都比辊压制作的效率高。说明辊压制作的表面碎片纹路杂乱无章造成磁导率差别过大,表面电阻率不均匀涡流损耗增加导致充电效率偏低,表面绝缘、表面磷化法表面处理制备的隔磁片充电效率最高。表3表3为实例1、实例2、实例3、和传统滚压制作的隔磁片温升对比,通过本实用新型粉体表面绝缘、表面磷化法制备的隔磁片随着时间推移温升最低,未表面处理的也要优于传统辊压制备的隔磁片。综上所述纵横比较可得出,表面绝缘、表面磷化法表面处理制备的隔磁片充电效率最高、温升最低。通过本实用新型工艺再对比传统辊压无规则破碎工艺相比充电效率,本实用新型艺均较一般工艺优异。本实用新型的使用状态为:首先通过放料轴6带动带材,使带材通过缓冲辊轮7置于盛有氧化锌、氧化镁、三氧化二铝、二氧化硅等粉体中的至少一种与酒精偶联剂混合形成的混合物溶液其粉体含量为3%-50%偶联剂含量为0.5%-3%的容器8中,使带材上附着粉体再通过烘干器9烘干,再通过导向轮10到张力轴11上收卷,将绕制好的软磁材料带材放置在加磁场或者未加磁场热处理炉内进行热处理(非晶为380~520℃,纳米晶为480~650℃),通过卷式贴合将双面胶粘贴在热处理后的软磁材料的一面,另一面裸露形成单层;表面图形化处理,通过对上述形成的单层或者由上述单层层叠成多层的软磁材料进行图形化处理;通过复合叠层形成低涡流损耗隔磁片。以上显示和描述了本实用新型的基本原理和主要特征和本实用新型的优点,本行业的技术人员应该了解,本实用新型不受上述实施例的限制,上述实施例和说明书中描述的只是说明本实用新型的原理,在不脱离本实用新型精神和范围的前提下,本实用新型还会有各种变化和改进,这些变化和改进都落入要求保护的本实用新型范围内,本实用新型要求保护范围由所附的权利要求书及其等效物界定。当前第1页1 2 3