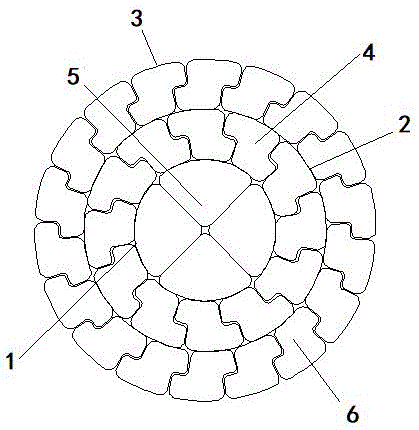
本发明涉及一种可用于高速轨道交通的异形股线的高精度小直径电缆生产方法,属于电缆制造
技术领域:
。
背景技术:
:高速轨道交通用电缆用于列车运行的电力传输。沿线路的供电电缆用于对牵引电机的长定子供电。每条单线铁路有两组相互独立的三相电缆分别对高速铁路的两侧电机长定子供电。每一相都由多股导线组成,以降低电缆电抗。由于设计特殊,电缆在轨道中呈现“s”型布线,需满足弯曲半径小,防紫外线、耐腐蚀、抗震动、抗老化、阻燃、质量轻等特点。由于电缆要求外径小,可敷设在定子槽并不脱落,电缆的整体结构较为固定,很难采用对电缆附加功能/性能层来提高电缆的适用性能。所以,要在生产过程中通过工艺方法来提高产品的精度。如公告号为cn210667842u的“一种交通用电缆”,在为了保证使用,需要控制成品电缆外径尺寸尽可能小,以确保电缆能敷设在定子槽中不脱落。技术实现要素:为了解决上述技术问题,本发明提出一种高精度异形股线小直径电缆生产方法,本方法通过生产工艺的控制,基于现有的设备以及模具,可实现电缆产品的高精度生产。具体来说:一种高精度异形股线小直径电缆生产方法,包括步骤:1)制造电缆导体;2)挤包半导电氯丁橡胶制成导体屏蔽层;3)挤包乙丙橡胶制成绝缘层;4)挤包半导电氯丁橡胶制成绝缘屏蔽层;5)挤包半导电氯丁橡胶制成半导电护套层;6)涂覆纳米级半导电胶水制成半导电纳米涂层。所述步骤1)包括:1.1)预制单丝:拉丝:将铝合金杆采用相应拉丝模具分别拉制成扇形单丝、z形单丝和s形单丝;拉丝工艺:将铝杆按道次依次穿入11个拉丝模,将单丝弧面与模孔弧槽相对应,确保铝丝受力稳定,单丝截面无偏差;1.2)取步骤1.1)制得的三种单丝绞合构成导体,扇形单丝制成导体内层;z形单丝和s形单丝依次包裹在导体内层外;设导体自内而外有n层,导体内层为第1层,n为自然数;相邻层导体的绞合方向相反;从第2层起,相邻层导体的单丝的断面是成镜像对称的,最终制成第n层导体,得到电缆导体;该工艺要求的技术原理以及效果为:将铝杆拉制成异型单丝,然后通过绞合工艺使异型单丝按序绞合成圆形,效果是导体弯曲时,单丝由于互相嵌合,不会出现炸开现象,确保了导体的紧密性。在具体实施时候,导体共三层,导体内层是由4根扇形单丝制成,导体中间层是由多根z形单丝构成,导体外层是由多根s形单丝构成;所述步骤1.1)中,扇形单丝、z形单丝和s形单丝都是将铝杆按道次依次穿入11个对应的拉丝模,将单丝弧面与模孔弧槽相对应,拉丝机的参数包括:扇形单丝:定速轮的速比为1.19,成品模直径4.20mm,排线节距0.1mm,拉丝速度8m/s;z形单丝:定速轮的速比为1.16,成品模直径3.30mm,排线节距0.1mm,拉丝速度10m/s;s形单丝:定速轮的速比为1.16,成品模直径3.29mm,排线节距0.1mm,拉丝速度12m/s;所述步骤1.2)中,把三种单丝在绞线机上绞合,绞线机的参数包括:绞合导体内层的转速是40~45r/min;绞合导体中间层的转速是30~35r/min;绞合导体外层的转速是30~33r/min;成品的线速度是7~8m/min;1.3)在金属线材连续退火生产线上,对步骤1.2)制得的电缆导体进行退火处理,其中:加热阶段温度为500℃,加热时间为30~40min;保温阶段温度为500℃,保温时间为3h;降温阶段的降温速度为40℃/h,降温时间为12h。所述步骤2)~4)是三层共挤工艺实现:挤包半导电氯丁橡胶的第一挤橡机温区控制为:一区50~60℃、二区55~65℃、三区65~70℃、四区80~90℃、五区90~100℃;一区为入料段,二区和三区为塑化段,四区和五区为均化段;挤包乙丙橡胶的第二挤橡机温区控制为:一区50~60℃、二区55~65℃、三区65~70℃、四区65~75℃、五区75~80℃;一区为入料段,二区和三区为塑化段,四区和五区为均化段;挤包半导电氯丁橡胶的第三挤橡机温区控制为:一区50~60℃、二区55~65℃、三区65~70℃、四区80~90℃、五区90~100℃;一区为入料段,二区和三区为塑化段,四区和五区为均化段;机头温度设定:110℃;上述挤包过程中,生产时蒸汽压力8~12bar,生产速度5~6m/min,第一挤橡机螺杆转速15~20r/min,第二挤橡机螺杆转速8~12r/min,第三挤橡机螺杆转速8~12r/min。上述步骤完成后,在冷水槽中水冷,冷却时间为15min;冷水槽的水温控制为5~10℃。所述步骤5)挤包半导电氯丁橡胶制成半导电护套层:对步骤4)制得线缆,在第四挤橡机中挤包半导电氯丁橡胶,第四挤橡机的温区控制为:一区50~60℃、二区55~65℃、三区65~70℃、四区65~75℃、五区75~80℃;一区为入料段,二区和三区为塑化段,四区和五区为均化段;生产时蒸汽压力7~8bar,生产速度5~6m/min,第四挤橡机螺杆转速18~20r/min;在冷水槽中水冷,冷却时间为20min;冷水槽的水温控制为5~10℃。所述步骤6)在步骤5)制得线缆外,在线涂覆纳米级半导电胶水,涂覆步骤为:电缆在涂覆机上走线,半导电胶进行喷涂,红外加热管进行加热烘干固化。传统的电缆半导电层多是采用覆有纳米级半导电层的薄膜或带制品(如聚酯薄膜、半导电无纺布),这类薄膜是采用绕包方式包裹在线缆外。对于本电缆来说,这种方式增加了线缆外径。为了进一步减少线缆外径,特采用直接涂覆纳米级半导电胶水的方式。现有技术中,这类胶水产品是用于制造纳米级半导电薄膜,主要是包含有纳米碳黑或碳管道的油性丙烯酸乳液和乙脂等混合物。涂胶时,线缆的线速度是4~5m/min,胶水固化时间为5min,本工艺制得的半导电纳米涂层的厚度范围可达5~50μm,非常薄,并且牢固程度好。半导电胶水的粘度控制在15~18秒(恩氏粘度),采用电压力筒匀速搅拌均匀;涂层厚度的调节:电缆输送速度与喷涂压力同步,电缆输送速度是4~5m/min,喷涂压力是0.8~1mpa,确保电缆每个面的胶水厚度均匀;烘干温度的控制:红外加热管加热烘干,固化加热温度是200℃,电缆横截面表面温度均匀一致。电缆输送:电缆在喷涂过程中,始终位于喷涂机中央,防止涂层被刮伤,并且厚度均匀。所述步骤1)中,导体采用的铝合金是aa8000系列铝合金。用来提高机械强度及抗蠕变性能。通过本生产工艺,在产品精度上,电缆导体外径控制偏差±0.1mm,绝缘线芯外径控制偏差±0.2mm,成品电缆外径控制偏差±0.2mm,确保了电缆能敷设在定子槽中不脱落。通过对导体的退火工艺控制,使导体具有柔软度高,曲折应力小,敷设后不变形、不松散、抗蠕变等优点。而且,经检测,中心导体的断裂伸长率在25%~35%。本高精度异形股线小直径电缆生产方法制得电缆是用于高速轨道交通的牵引电机的长定子供电。本方法制得的电缆适用于高速轨道交通的电力传输,其不仅严格控制外径,具有可靠的电气性能(如耐压等绝缘性能),同时还具有优异的弯曲性能、耐候性能、阻燃等特点。通过生产控制,绝缘屏蔽层、半导电护套层、半导电纳米涂层为一体式结构,成品电缆表面电阻不大于200ω。可以有效降低电缆运行时的感应电流、电容电流和泄漏电流,确保电缆长期运行时的使用安全。本技术方案的原理以及有益效果说明如下:1、为了满足高速轨道交通线路轨道敷设的特种应用环境,则需要电缆满足优异的电气性能、耐候性能、易弯曲性能等要求。本特种电缆采用异型退火铝导体,中心层由4根90°扇形单丝绞合构成;次内层采用z字形单丝绞合构成;外层采用s字形单丝绞合构成;再进行导体整体退火,导体柔软度高,曲折应力小,敷设后不变形、不松散、抗蠕变等优点;乙丙橡胶作为绝缘料,采用三层共挤工艺加工绝缘层。由于该材料在满足高电压性能的要求下能够满足耐-40℃低温性能、耐105℃高温性能。高强度橡皮作为护套材料,采用单层结构,在满足高机械性能的情况下能够满足耐气候、半导电要求。2、特种应用环境对电缆的外径有很高要求,同时为了电缆嵌在定子铁芯上的嵌入部的要求,则需要电缆外径偏差极小的要求。本方法及其制得电缆具有优秀的外径一致性,通过本生产工艺,在产品精度上,电缆导体外径控制偏差±0.1mm,绝缘线芯外径控制偏差±0.2mm,成品电缆外径控制偏差±0.2mm,确保了电缆能敷设在定子槽中不脱落。附图说明图1是本实施例电缆的导体径向截面示意图。图2为本实施例电缆截面结构示意图。图中:导体内层1、导体中间层2、导体外层3、z形单丝4、扇形单丝5、s形单丝6、导体7、导体屏蔽层8、绝缘层9、绝缘屏蔽层10、半导电护套层11、半导电纳米涂层12。具体实施方式下面结合附图和具体实施例,对本技术方案进一步说明:参考附图1和2,本制造方法制得的高精度异形股线小直径电缆,其结构为:导体7以及导体7外包裹的导体屏蔽层8、绝缘层9、绝缘屏蔽层10、半导电护套层11和半导电纳米涂层12构成的电缆。该电缆是用于高速轨道交通的牵引电机的长定子供电。所述导体7的直径范围是19.5-20.5mm;所述绝缘层9的厚度范围是5.2-5.8mm;所述半导电护套层11的厚度范围是1.8-2.4mm;所述半导电纳米涂层12的厚度范围是5-50μm;所述导体7的材质是铝合金材质;所述导体屏蔽层8是由半导电氯丁橡胶构成;所述绝缘层9是由乙丙橡胶构成;所述绝缘屏蔽层10是由半导电氯丁橡胶构成;所述半导电护套层11的护套料是半导电氯丁橡胶经挤橡构成;导体7由内而外分为第1~n层,n为自然数(本例为3层);——对于第1层导体:它由多根成轴对称的扇形单丝绞合构成,绞合的节径比是20~25倍;——对于第2~n层导体7:它们分别由多个相同的、截面是“z”字形或“s”字形的单丝相互拼接绞合构成;相邻层导体的单丝绞合方向相反;相邻层导体的单丝是成镜像对称的;任一异形单丝是由铝合金单丝挤压成型。构成各层导体的单丝绞合的节径比是10~18倍,(最外层节径比最小,确保导体紧密、不松散)。所述导体7是由铝合金杆经拉制、绞合及退火工艺制得的导体。所述导体屏蔽层8是由半导电料(半导电氯丁橡胶)经挤橡连硫工艺制得的屏蔽层。所述绝缘层9是由绝缘料(乙丙橡胶)经挤橡连硫工艺制得的绝缘层。所述绝缘屏蔽层10是由半导电料(半导电氯丁橡胶)经挤橡连硫工艺制得的绝缘屏蔽层。所述半导电护套层11是由护套料(半导电氯丁橡胶)经挤橡连硫工艺制得的护套层。所述半导电纳米涂层12是由半导电胶经喷涂工艺制得的纳米级涂层。本高精度异形股线小直径电缆生产方法制得电缆是用于高速轨道交通的牵引电机的长定子供电。本高精度异形股线小直径电缆生产方法,包括步骤:1)制造电缆的导体7;2)挤包半导电氯丁橡胶制成导体屏蔽层8;3)挤包乙丙橡胶制成绝缘层9;4)挤包半导电氯丁橡胶制成绝缘屏蔽层10;5)挤包半导电氯丁橡胶制成半导电护套层11;6)涂覆纳米级半导电胶水制成半导电纳米涂层12。所述步骤1)包括:1.1)预制单丝:拉丝:将铝合金杆采用相应拉丝模具分别拉制成扇形单丝5、z形单丝4和s形单丝6;拉丝工艺:将铝杆按道次依次穿入11个拉丝模,将单丝弧面与模孔弧槽相对应,确保铝丝受力稳定,单丝截面无偏差;1.2)取步骤1.1)制得的三种单丝绞合构成导体7,扇形单丝5制成导体内层1;z形单丝4和s形单丝6依次包裹在导体内层1外;设导体7自内而外有n层,导体内层1为第1层,n为自然数;相邻层导体的单丝的绞合方向相反;从第2层起,相邻层导体的单丝的断面是成镜像对称的,最终制成第n层导体,得到电缆的导体7;1.3)在金属线材连续退火生产线上,对步骤1.2)制得的电缆导体进行退火处理,其中:加热阶段温度为500℃,加热时间为30~40min;保温阶段温度为500℃,保温时间为3h;降温阶段的降温速度为40℃/h,降温时间为12h;所述步骤2)~4)是三层共挤工艺实现:挤包半导电氯丁橡胶的第一挤橡机温区控制为:一区50~60℃、二区55~65℃、三区65~70℃、四区80~90℃、五区90~100℃;一区为入料段,二区和三区为塑化段,四区和五区为均化段;挤包乙丙橡胶的第二挤橡机温区控制为:一区50~60℃、二区55~65℃、三区65~70℃、四区65~75℃、五区75~80℃;一区为入料段,二区和三区为塑化段,四区和五区为均化段;挤包半导电氯丁橡胶的第三挤橡机温区控制为:一区50~60℃、二区55~65℃、三区65~70℃、四区80~90℃、五区90~100℃;一区为入料段,二区和三区为塑化段,四区和五区为均化段;机头温度设定:110℃;挤包过程中,生产时蒸汽压力8~12bar,生产速度5~6m/min,第一挤橡机螺杆转速15~20r/min,第二挤橡机螺杆转速8~12r/min,第三挤橡机螺杆转速8~12r/min;在冷水槽中水冷,冷却时间为15min;冷水槽的水温控制为5~10℃。所述步骤5)挤包半导电氯丁橡胶制成半导电护套层11;对步骤4)制得线缆,在第四挤橡机中挤包半导电氯丁橡胶,第四挤橡机的温区控制为:一区50~60℃、二区55~65℃、三区65~70℃、四区65~75℃、五区75~80℃;一区为入料段,二区和三区为塑化段,四区和五区为均化段;生产时蒸汽压力7~8bar,生产速度5~6m/min,第四挤橡机螺杆转速18~20r/min;在冷水槽中水冷,冷却时间为20min;冷水槽的水温控制为5~10℃。所述步骤6)在步骤5)制得线缆外,在线涂覆纳米级半导电胶水,涂覆步骤为:电缆在涂覆机上走线,半导电胶进行喷涂,红外加热管进行加热烘干;涂胶时,线缆的线速度是4~5m/min;胶水固化时间为5min。半导电纳米涂层12的厚度范围是5~50μm,采用红外加热管200摄氏度加热烘干;1)涂料的配置:采用双组分体系,在涂料中加入固化剂及稀释剂,涂料的粘度控制在15~18秒,采用电压力筒匀速搅拌均匀;2)涂层厚度的调节:电缆输送速度与喷涂压力同步(电缆输送速度为4~5m/min,喷涂压力为0.8~1mpa),确保电缆每个面的胶水厚度均匀;3)烘干温度的控制:红外加热管加热烘干,电缆横截面表面温度均匀一致;4)电缆输送:电缆在喷涂过程中,始终位于喷涂机中央,防止涂层被刮伤,并且厚度均匀。本例中,导体7共三层(即n=3),导体内层1是由4根扇形单丝5制成,导体中间层2是由多根z形单丝4构成,导体外层3是由多根s形单丝6构成;所述步骤1.1)中,扇形单丝5、z形单丝4和s形单丝6都是将铝杆按道次依次穿入11个对应的拉丝模,将单丝弧面与模孔弧槽相对应,拉丝机的参数包括:扇形单丝5:定速轮的速比为1.19,成品模直径4.20mm,排线节距0.1mm,拉丝速度8m/s;z形单丝4:定速轮的速比为1.16,成品模直径3.30mm,排线节距0.1mm,拉丝速度10m/s;s形单丝6:定速轮的速比为1.16,成品模直径3.29mm,排线节距0.1mm,拉丝速度12m/s。所述步骤1.2)中,把三种单丝在绞线机上绞合,绞线机的参数包括:绞合导体内层1的转速是40~45r/min;绞合导体中间层2的转速是30~35r/min;绞合导体外层3的转速是30~33r/min;成品的线速度是7~8m/min。挤包工艺对电缆的成品率有一定影响,经比对,本例制得电缆良品率最高的最优挤包工艺是例2工艺:例1一区二区三区四区五区螺杆转速第一挤橡机50℃55℃65℃80℃90℃15r/min第二挤橡机50℃55℃65℃65℃75℃8r/min第三挤橡机50℃55℃65℃80℃90℃8r/min第四挤橡机50℃55℃65℃65℃75℃18r/min例2一区二区三区四区五区螺杆转速第一挤橡机56℃60℃68℃86℃96℃18r/min第二挤橡机55℃59℃67℃70℃77℃10r/min第三挤橡机53℃58℃66℃83℃94℃9r/min第四挤橡机55℃60℃68℃70℃78℃18r/min例3一区二区三区四区五区螺杆转速第一挤橡机60℃65℃70℃90℃100℃20r/min第二挤橡机60℃65℃70℃75℃80℃12r/min第三挤橡机60℃65℃70℃90℃100℃12r/min第四挤橡机60℃65℃70℃75℃80℃20r/min经破坏性解剖实验检测:电缆导体外径控制偏差±0.1mm,绝缘线芯外径控制偏差±0.2mm,成品电缆外径控制偏差±0.2mm,确保了电缆能敷设在定子槽中不脱落。柔软度控制:材料的硬度进行控制,其中绝缘、护套料硬度≤70a。经检测,本电缆的电性能、机械性能的检测全要求如下表,在下表的检测项目中,结果均为合格:本发明不限于上述实施例,凡采用等同或等效替换形成的技术方案均落入本发明要求的保护范围。当前第1页12