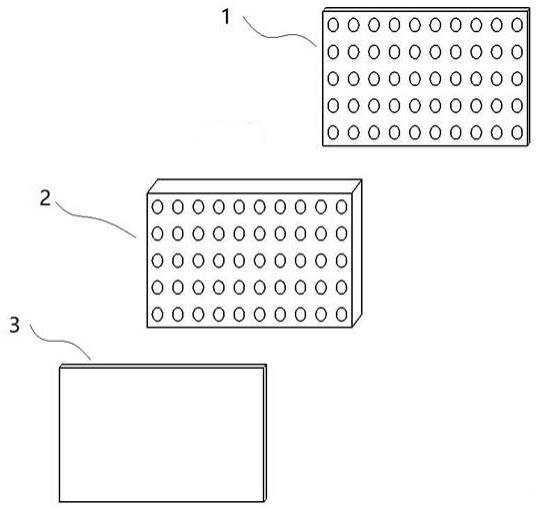
1.本发明属于半导体制冷器件领域,具体涉及一种半导体热电器件及其制备方法。
背景技术:2.现有半导体制冷器件一般包括陶瓷基板和半导体晶粒,其中,n对(n为自然数)半导体晶粒夹在两块陶瓷基板之间,并通过焊料焊接在陶瓷基板上。其制作工艺实现通常包括以下步骤:步骤一:将半导体晶棒切割成片,经过打磨及镀层工序后,再切割成要求大小的半导体晶粒。
3.步骤二:手动或排片机等方式将半导体晶粒子摆放到下陶瓷片上,再将上陶瓷通过定位针或目测等方式与贴在下陶瓷上面的半导体粒子进行对位,然后进行焊接。
4.以上半导体晶粒的制作方式,由于多次线切割和打磨,会造成材料利用率不高。同时,切出粒子的外形尺寸不规则,尺寸一致性差,会增加后面焊接工序的难度。随着半导体制冷进入超微型阶段,物理切割的方式,限于切割工艺,不利于小型化。同时超微型半导体制冷器件对上下陶瓷和晶粒的对位精度要求高,现有半导体制冷器件的制作工艺无法达到超微型半导体制冷器件制作的要求。
技术实现要素:5.针对现有技术中存在的上述问题,本发明提供一种半导体热电器件,该半导体热电器件的热电材料是封装在耐高温基板里面,不直接与空气接触,材料的可靠性和寿命大大增加。
6.本发明的另一目的在于提供一种半导体热电器件的制备方法。
7.为实现上述目的,本发明解决其技术问题所采用的技术方案是:一种半导体热电器件,所述半导体热电器件包括上陶瓷基板、下陶瓷基板和半导体热电模块,所述半导体热电模块主体为一块耐高温基板,所述耐高温基板上设有m*n个贯穿的通孔,所述m,n为自然数;所述通孔内填充有半导体热电材料,在耐高温基板的上表面和下表面的通孔处分别形成m*n个金属焊盘,所述金属焊盘表面镀有镀层,所述耐高温基板的上表面和下表面的金属焊盘通过焊料分别与上陶瓷基板和下陶瓷基板贴装。
8.进一步的,金属焊盘大小与通孔一致。
9.进一步的,所述通孔的形状为圆形、三角形、四边形、其它多边形中的一种。
10.进一步的,所述半导体热电材料为碲化铋,碲化铅,硅锗合金等,优选为碲化铋,具体为n型碲化铋材料和p型碲化铋材料。
11.进一步的,所述镀层为镍/金、银、锡中的一种。其中,镍/金表示为先镀一层镍层,再在镍层表面镀金层,进一步的,所述上陶瓷基板和下陶瓷基板与半导体热电模块上表面、下表面的金属焊盘分别相对的位置设有相适配的金属焊盘。
12.进一步的,所述上陶瓷基板的金属焊盘之间设有电路,所述下陶瓷基板上的金属焊盘之间设有电路,所述半导体热电材料连通所述上陶瓷基板与下陶瓷基板的电路,形成电流通路。
13.本发明还公开了一种半导体热电器件的制作工艺,具体包括以下步骤:s1.准备上陶瓷基板、下陶瓷基板和耐高温基板,在耐高温基板上按一定间距钻m*n个贯穿孔;s2.将半导体热电材料粉末填入步骤s1所得贯穿孔内并压实,置于在高温真空炉中,升温使半导体热电材料为熔融状态后,冷却到常温,在孔内形成m*n个预定形状半导体热电晶粒,磨平耐高温基板的上、下表面,在耐高温基板的上表面和下表面分别形成m*n个金属焊盘;s3.在步骤s2中金属焊盘的表面镀上镀层,形成含有镀层的m*n个晶粒的半导体热电模块;s4.将步骤s3所得半导体热电模块焊接在上陶瓷基板和下陶瓷基板之间。
14.进一步的,步骤s1中,所述上陶瓷基板、下陶瓷基板的制备过程为:将含有双面铜箔的陶瓷板,通过菲林、显影、蚀刻、表面处理等工序,制成专用的印制线路陶瓷基板,所述陶瓷基板表面包含金属焊盘以及连接金属焊盘之间的金属印制线路。进一步优选所述上陶瓷基板的金属印制线路和下陶瓷基板的金属印制线路交错对应。
15.进一步的,步骤s1中,在耐高温基板上等间距钻m*n个贯穿孔。
16.进一步的,步骤s3中,金属焊盘表面镀层的厚度为3~12um。
17.进一步的,步骤s4中,所述焊接工艺具体包括:(1)将半导体热电模块的下表面m*n金属焊盘对准下陶瓷基板上相应的m*n个金属焊盘贴装在一起,(2)将下陶瓷基板上相应的m*n个金属焊盘对准半导体热电模块的上表面m*n金属焊盘后贴装在一起;(3)采用回焊炉焊接或加热台焊接。
18.进一步的,在下陶瓷基板和上陶瓷基板上相应的m*n个金属焊盘处均预上焊料,进一步优选所述焊料为锡膏,所述锡膏包括不限于金锡,锡银,铟锡合金等。
19.本发明所产生的有益效果为:(1)本发明所述半导体热电器件的热电材料是封装在耐高温基板里面,不直接与空气接触,增加材料的可靠性和寿命。
20.(2)本发明设计了一种半导体热电模块,将半导体热电材料粉末在高真空环境下熔融,直接嵌入到耐高温基板的m*n个孔里,形成了带有m*n个热电粒子的模块,使得带有热电粒子的半导体热电模块可作为一个整体一次性贴装到陶瓷基板上,相较现行机械切割的方式,会大大提高半导体热电材料利用率;相较于现有的将半导体晶粒用排布机或人工夹取一个个贴到陶瓷板的方式,大大的提高了效率,降低了工艺难度。
21.(3)受限于现有技术的切割工艺和贴装工艺,晶粒很难做小,晶粒之间的间距较大,故很难达到超微型化;本发明所述半导体热电器件的制备方法通过调整钻孔的大小及孔间距即可,实现方法简单,且可以实现超微型化。
22.(4)本发明可以根据需要,通过钻不同形状的孔,使嵌入到半导体热电模块里的晶粒形成不同形状的柱状体,如圆柱,立方柱,多变形柱等,相应的,在发明的半导体热电模块上表面和下表面,形成m*n个和通孔一样大小的金属焊盘,如圆形,正方形,多边形等。
附图说明
23.图1为本发明半导体热电器件爆炸图;其中:1
‑
上陶瓷基板、2
‑
半导体热电模块、3
‑
下陶瓷基板。
24.图2为本发明半导体热电器件的部件结构图一;其中:2
‑
1为半导体热电模块背面结构图,2
‑
2为下陶瓷基板正面结构图,2
‑
3为下陶瓷基板背面结构图。
25.图3为本发明半导体热电器件的部件结构图二;其中:3
‑
1为半导体热电模块正面结构图,3
‑
2为上陶瓷基板正面结构图,3
‑
3为上陶瓷基板背面结构图。
具体实施方式
26.以下结合说明书附图和具体优选的实施例对本发明作进一步描述,但并不因此而限制本发明的保护范围。
27.实施例1参见图1~3所示,本实施例公开了一种半导体热电器件及其制备方法,所述半导体热电器件由上陶瓷基板1、下陶瓷基板3和一块半导体热电模块2组成,其中半导体热电模块2由一块耐高温基板和位于耐高温基板内部的m*n个(m,n为自然数)半导体热电材料组成。
28.本实施例中,半导体热电器件的长*宽尺寸为:2.2mm*2.2mm,陶瓷基板和半导体热电模块的厚度可根据不同需要进行设定,本实施例不限定陶瓷基板的厚度,对于半导体热电模块预设厚度为0.5mm,耐高温基板的材质为玻纤棉,m取3,n取4,所述半导体热电材料选用碲化铋,具体为n型碲化铋粉末和p型碲化铋粉末。
29.本实施例所述其一种半导体热电器件的制备方法包括以下步骤:s1.取一块玻纤棉材质的耐高温基板,在耐高温基板上以0.5mm中心间距钻3行4列的贯穿孔,贯穿孔的形状为圆柱形,孔直径为0.3mm;取两块含有双面铜箔的陶瓷板分别作为上陶瓷基板和下陶瓷基板,通过菲林、显影、蚀刻、表面处理等工序,制成专用的印制线路陶瓷基板,所述陶瓷基板表面包含金属焊盘以及连接金属焊盘之间的金属印制线路,所述上陶瓷基板的金属印制线路和下陶瓷基板的金属印制线路交错对应。
30.s2.将n型碲化铋粉末和p型碲化铋粉末分别填入相邻的贯穿孔内并压实,在高温真空炉中让半导体热电材料完全到熔融状态后,冷却到常温,在贯穿孔内形成3*4个直径为0.3mm圆柱形的半导体热电晶粒,此时在耐高温基板的上、下表面存在有凝固的半导体热电材料溢出,需要将耐高温基板的厚度调整至预设厚度,本实施例的半导体热电模块的预设厚度为0.5mm,采用磨平工艺将耐高温基板的上、下表面磨平,至预设厚度,从而在高温基板的上表面和下表面分别形成3*4个金属焊盘;s3.在步骤s2所得金属焊盘表面镀上3~12um厚的金属锡镀层,形成含有金属锡镀层的3*4个晶粒的半导体热电模块;s4.在上陶瓷基板和下陶瓷基板与半导体热电模块上下表面金属焊盘分别相对的位置上设有相适配的金属焊盘,焊盘间通过印制线路进行连接,形成含印刷线路的陶瓷基板,在上陶瓷基板和下陶瓷基板的金属焊盘上预上焊料,本实施例中采用锡膏作为焊料,将半导体热电模块下表面的3*4金属焊盘对准下陶瓷基板上相应的3*4个金属焊盘贴装在一起;将下陶瓷板上相应的3*4个金属焊盘对准半导体热电模块的上表面3*4金属焊盘后贴装在一起;整体过回焊炉焊接或加热台焊接,得半导体热电器件。
31.实施例2参见图1~3所示,本实施例公开了一种半导体热电器件及其制备方法,所述半导体热电器件由上陶瓷基板1、下陶瓷基板3和一块半导体热电模块2组成,其中半导体热电模块2由一块耐高温基板和位于耐高温基板内部的m*n个(m,n为自然数)半导体热电材料组成。
32.本实施例中,半导体热电器件的长*宽尺寸为:2.2mm*1.7mm,陶瓷基板和半导体热电模块的厚度可根据不同需要进行设定,本实施例不限定陶瓷基板的厚度,对于半导体热电模块预设厚度为1.2mm,耐高温基板的材质为玻纤棉,m取2,n取5,所述半导体热电材料选用碲化铋,具体为n型碲化铋粉末和p型碲化铋粉末。
33.本实施例所述其一种半导体热电器件的制备方法包括以下步骤:s1.取一块玻纤棉材质的耐高温基板,在耐高温基板上以0.5mm中心间距钻2行5列的贯穿孔,贯穿孔的形状为长方柱形,孔的表面为边长0.3mm的正方形;取两块含有双面铜箔的陶瓷板分别作为上陶瓷基板和下陶瓷基板,通过菲林、显影、蚀刻、表面处理等工序,制成专用的印制线路陶瓷基板,所述陶瓷基板表面包含金属焊盘以及连接金属焊盘之间的金属印制线路,所述上陶瓷基板的金属印制线路和下陶瓷基板的金属印制线路交错对应。
34.s2.将n型碲化铋粉末和p型碲化铋粉末分别填入相邻的贯穿孔内并压实,在高温真空炉中让半导体热电材料完全到熔融状态后,冷却到常温,在贯穿孔内形成2*5个边长为0.3mm长方柱形的半导体热电晶粒,此时在耐高温基板的上、下表面存在有凝固的半导体热电材料溢出,需要将耐高温基板的厚度调整至预设厚度,本实施例的半导体热电模块的预设厚度为1.2mm,采用磨平工艺将耐高温基板的上、下表面磨平,至预设厚度,从而在高温基板的上表面和下表面分别形成2*5个金属焊盘;s3.在步骤s2所得金属焊盘表面镀上3~12um厚的金属锡镀层,形成含有金属锡镀层的2*5个晶粒的半导体热电模块;s4.在上陶瓷基板和下陶瓷基板与半导体热电模块上下表面金属焊盘分别相对的位置上设有相适配的金属焊盘,焊盘间通过印制线路进行连接,形成含印刷线路的陶瓷基板,在上陶瓷基板和下陶瓷基板的金属焊盘上预上焊料,本实施例中采用锡膏作为焊料,将半导体热电模块下表面的2*5金属焊盘对准下陶瓷基板上相应的2*5个金属焊盘贴装在一起;将下陶瓷板上相应的2*5个金属焊盘对准半导体热电模块的上表面2*5金属焊盘后贴装在一起;整体过回焊炉焊接或加热台焊接,得半导体热电器件。
35.实施例3参见图1~3所示,本实施例公开了一种半导体热电器件及其制备方法,所述半导体热电器件由上陶瓷基板1、下陶瓷基板3和一块半导体热电模块2组成,其中半导体热电模块2由一块耐高温基板和位于耐高温基板内部的m*n个(m,n为自然数)半导体热电材料组成。
36.本实施例中,半导体热电器件的长*宽尺寸为:12mm*13.5mm,陶瓷基板和半导体热电模块的厚度可根据不同需要进行设定,本实施例不限定陶瓷基板的厚度,对于半导体热电模块预设厚度为2.0mm,耐高温基板的材质为玻纤棉,m取8,n取8,所述半导体热电材料选用碲化铋,具体为n型碲化铋粉末和p型碲化铋粉末。
37.本实施例所述其一种半导体热电器件的制备方法包括以下步骤:s1.取一块玻纤棉材质的耐高温基板,在耐高温基板上以1.5mm中心间距钻8行8列的贯穿孔,贯穿孔的形状为正方形,孔的表面为边长1.0mm的正方形;取两块含有双面铜箔
的陶瓷板分别作为上陶瓷基板和下陶瓷基板,通过菲林、显影、蚀刻、表面处理等工序,制成专用的印制线路陶瓷基板,所述陶瓷基板表面包含金属焊盘以及连接金属焊盘之间的金属印制线路,所述上陶瓷基板的金属印制线路和下陶瓷基板的金属印制线路交错对应。
38.s2.将n型碲化铋粉末和p型碲化铋粉末分别填入相邻的贯穿孔内并压实,在高温真空炉中让半导体热电材料完全到熔融状态后,冷却到常温,在贯穿孔内形成8*8个边长为1.0 mm长方柱形的半导体热电晶粒,此时在耐高温基板的上、下表面存在有凝固的半导体热电材料溢出,需要将耐高温基板的厚度调整至预设厚度,本实施例的半导体热电模块的预设厚度为2.0mm,采用磨平工艺将耐高温基板的上、下表面磨平,至预设厚度,从而在高温基板的上表面和下表面分别形成8*8个金属焊盘;s3.在步骤s2所得金属焊盘表面镀上3~12um厚的金属锡镀层,形成含有金属锡镀层的8*8个晶粒的半导体热电模块;s4.在上陶瓷基板和下陶瓷基板与半导体热电模块上下表面金属焊盘分别相对的位置上设有相适配的金属焊盘,焊盘间通过印制线路进行连接,形成含印刷线路的陶瓷基板,在上陶瓷基板和下陶瓷基板的金属焊盘上预上焊料,本实施例中采用锡膏作为焊料,将半导体热电模块下表面的8*8金属焊盘对准下陶瓷基板上相应的8*8个金属焊盘贴装在一起;将下陶瓷板上相应的8*8个金属焊盘对准半导体热电模块的上表面8*8金属焊盘后贴装在一起;整体过回焊炉焊接或加热台焊接,得半导体热电器件。
39.以上所述,仅是本发明的较佳实施例而已,并非对本发明作任何形式上的限制。虽然本发明已以较佳实施例揭示如上,然而并非用以限定本发明。任何熟悉本领域的技术人员,在不脱离本发明的精神实质和技术方案的情况下,都可利用上述揭示的方法和技术内容对本发明技术方案做出许多可能的变动和修饰,或修改为等同变化的等效实施例。因此,凡是未脱离本发明技术方案的内容,依据本发明的技术实质对以上实施例所做的任何简单修改、等同替换、等效变化及修饰,均仍属于本发明技术方案保护的范围内。