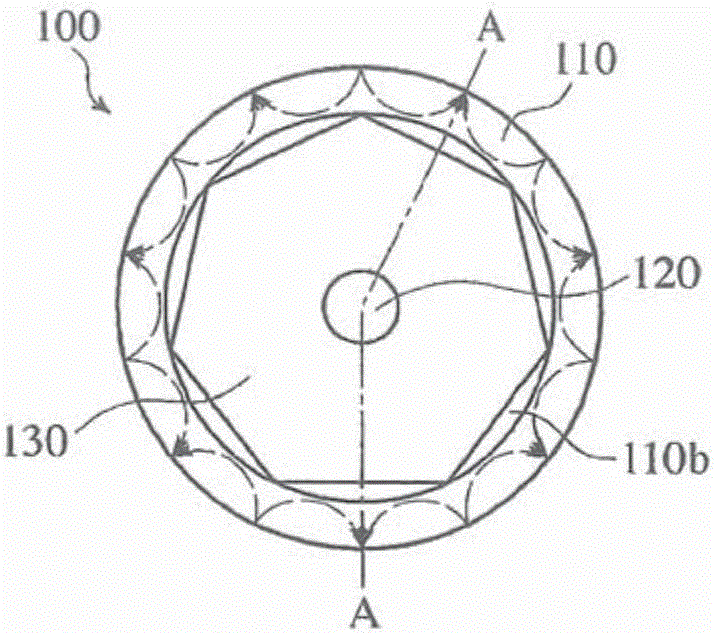
本实用新型涉及使用了R-T-B系极各向异性烧结环形磁铁的表面磁铁型旋转件。
背景技术:
:在专利文献1(日本特开2005-304178号)以及专利文献2(日本特开平7-31120号)中公开了如下的技术:在具有R-T-B系极各向异性烧结环形磁铁的表面磁铁型旋转件中,用于防止旋转件的轴部(shaft)和极各向异性烧结环形磁铁的空转的止转技术、以及防止磁铁从旋转件的轴部沿轴向脱落的所谓的防脱技术。专利文献1公开了如下的方法:在R-T-B系极各向异性烧结环形磁铁中,通过使形成于内周面的轴线方向的槽与形成于转子磁轭的外周面的轴线方向的突条部嵌合,从而防止所述转子磁轭的空转,并且记载了在对以使外周面侧具有极的方式进行了极各向异性取向的成形体进行烧结时,所述成形体收缩,利用与之相伴地产生的内周面的变形而形成所述内周面的轴线方向的槽。然而,由于所述内周面的槽是利用与形成于外周面侧的极各向异性取向相伴的烧结时的变形而设置的,因此包含一定程度的制造误差,转子磁轭的突条部与烧结环形磁铁的槽之间的位置有可能偏移。此外,为了维持烧结环形磁铁的内径的尺寸精度,需要研磨槽部以外的内周面的工序,存在增加成本这样的问题。另外,由于转子磁轭是磁性金属,因此必然增大惯性力,不适合频繁进行旋转停止的旋转件。专利文献2公开了在环状磁铁与旋转轴之间对树脂进行注塑成型而成的旋转件的一例。在环状磁铁的内周面侧实施有倒角。利用倒角部和注塑成型后的树脂,与环状磁铁和树脂的轴线方向的力对置,抑制环状磁铁沿轴线方向脱落。然而,在专利文献2所记载的实用新型中,无法同时实现防脱和止转。在先技术文献专利文献专利文献1:日本特开2005-304178号公报专利文献2:日本特开平7-31120号公报技术实现要素:实用新型要解决的课题因此,本实用新型的目的在于,提供一种使用了环形磁铁的表面磁铁型旋转件,其中,同时实现用于防止轴部与磁铁之间的空转的止转以及轴部沿轴向的防脱,并且惯性力小而容易停止旋转。用于解决课题的手段鉴于上述目的,本实用新型人对本实用新型进行了深入研究,其结果是,本实用新型人发现,在具有剖面多边形的内周面的R-T-B系极各向异性烧结环形磁铁的表面磁铁型旋转件中,通过在R-T-B系极各向异性烧结环形磁铁的轴向端面的内缘部形成倒角或者台阶部,并且向该磁铁插入在轴向中央部具有至少一处平坦部的轴部,且在轴部与磁铁内周面之间以覆盖所述倒角部或者台阶部的方式(以成为覆盖的状态的方式)填充树脂隔离件,从而起到防止轴部与磁铁的空转的止转效果,并且起到防止磁铁从轴部沿其轴向脱落的防脱效果,由此得到本实用新型。此外,本实用新型人发现,通过以形成内周面的剖面多边形的顶点沿着轴向偏斜的方式形成所述R-T-B系极各向异性烧结环形磁铁的内周面,同样也起到防止轴部与磁铁的空转的止转效果,并且起到防止磁铁从轴部沿其轴向脱落的防脱效果,由此得到本实用新型。另外,本实用新型人发现,通过使用比较轻型的材料作为隔离物,惯性力小,因此,能够作为频繁地进行旋转停止的旋转件而有效地利用,由此想到本实用新型。即,本实用新型的表面磁铁型旋转件的第一方式是一种表面磁铁型旋转件,包括:R-T-B系极各向异性烧结环形磁铁,其具有剖面圆形的外周面和剖面多边形的内周面,在所述外周面具有多个极;柱状的轴部,其插入到所述R-T-B系极各向异性烧结环形磁铁的轴中心;以及树脂隔离件,其填充在所述轴与所述R-T-B系极各向异性烧结环形磁铁之间,在所述R-T-B系极各向异性烧结环形磁铁上固定所述轴部,所述表面磁铁型旋转件的特征在于,所述R-T-B系极各向异性烧结环形磁铁在轴向端面的内缘部具有倒角部,所述轴部具有形成于轴向中央部的至少一处平坦部和在所述平坦部的轴向两端延伸设置的圆柱部,所述树脂隔离件以包括所述轴部的平坦部且成为覆盖所述倒角部的状态的方式填充在所述轴部的轴向中央部的外周面与所述R-T-B系极各向异性烧结环形磁铁的内周面之间。优选的是,所述外周面的邻接的两个极的中间位置中的至少一个与构成所述内周面的剖面多边形的顶点中的至少一个在周向上一致。优选的是,所述倒角部设置在所述轴向两端面的内缘部。优选的是,所述倒角部仅设置在多边形状的所述内缘部的各边的一部分。优选的是,所述树脂隔离件设置为不会从所述R-T-B系极各向异性烧结环形磁铁的轴向端面露出。优选的是,所述R-T-B系极各向异性烧结环形磁铁的内周面没有进行加工。优选的是,所述R-T-B系极各向异性烧结环形磁铁的极数与所述多边形的顶点个数相同。优选的是,所述R-T-B系极各向异性烧结环形磁铁的极数为所述多边形的顶点个数的两倍。优选的是,所述树脂隔离件由热塑性树脂构成。优选的是,所述树脂隔离件的填充通过注塑成型来进行。本实用新型的表面磁铁型旋转件的第二方式是一种表面磁铁型旋转件,包括:R-T-B系极各向异性烧结环形磁铁,其具有剖面圆形的外周面和剖面多边形的内周面,在所述外周面具有多个极;柱状的轴部,其插入到所述R-T-B系极各向异性烧结环形磁铁的轴中心;以及树脂隔离件,其填充在所述轴部与所述R-T-B系极各向异性烧结环形磁铁之间,在所述R-T-B系极各向异性烧结环形磁铁上固定所述轴部,所述表面磁铁型旋转件的特征在于,所述R-T-B系极各向异性烧结环形磁铁在轴向端面的内缘部具有台阶部,所述轴部具有形成于轴向中央部的至少一处平坦部和在所述平坦部的轴向两端延伸设置的圆柱部,所述树脂隔离件以包括所述轴部的平坦部且成为覆盖所述台阶部的状态的方式填充在所述轴部的轴向中央部的外周面与所述R-T-B系极各向异性烧结环形磁铁的内周面之间。本实用新型的表面磁铁型旋转件的第三方式是一种表面磁铁型旋转件,包括:R-T-B系极各向异性烧结环形磁铁,其具有剖面圆形的外周面和剖面多边形的内周面,并在所述外周面具有多个极;柱状的轴部,其插入到所述R-T-B系极各向异性烧结环形磁铁的轴中心;以及树脂隔离件,其填充在所述轴部与所述R-T-B系极各向异性烧结环形磁铁之间,在所述R-T-B系极各向异性烧结环形磁铁上固定所述轴部,所述表面磁铁型旋转件的特征在于,所述R-T-B系极各向异性烧结环形磁铁中,形成所述内周面的剖面多边形的顶点沿着轴向偏斜,所述轴部具有形成于轴向中央部的至少一处平坦部和在所述平坦部的轴向两端延伸设置的圆柱部,所述树脂隔离件以包括所述轴部的平坦部的方式填充在所述轴部的轴向中央部的外周面与所述R-T-B系极各向异性烧结环形磁铁的内周面之间。在所述表面磁铁型旋转件的第三方式的基础上,优选的是,所述R-T-B系极各向异性烧结环形磁铁在轴向端面的内缘部具有倒角部或者台阶部。在所述表面磁铁型旋转件的第二以及第三方式的基础上,优选的是,所述外周面的邻接的两个极的中间位置中的至少一个与构成所述内周面的剖面多边形的顶点中的至少一个在周向上一致。实用新型效果本实用新型的表面磁铁型旋转件通过向在轴向端面的内缘部具有倒角部或者台阶部的R-T-B系极各向异性烧结环形磁铁插入在轴向中央部具有至少一处平坦部的轴部,并且在轴部与磁铁内周面之间以覆盖所述倒角部或者台阶部的方式(以成为覆盖的状态的方式)填充树脂隔离件,能够同时实现防止轴部与磁铁的空转的止转效果和防止磁铁从轴部沿其轴向脱落的防脱效果。另外,由于本实用新型的R-T-B系极各向异性烧结环形磁铁具有剖面多边形的内周面,因此通过将在轴向中央部具有至少一处平坦部的柱状的轴部插入到磁铁、且以包括轴部的平坦部的方式填充树脂隔离件,能够可靠地防止轴部的空转,即便采用由比较轻型的材料、例如树脂等构成的柱状的轴部,也能够可靠地防止空转,因此能够将惯性力保持得较低。因此,适于作为频繁进行旋转停止的旋转件。此外,关于倒角的大小,只要仅形成在多边形的内缘部的各边的一部分就足够,能够提高倒角的作业效率,并且能够降低成本。附图说明图1(a)是示出本实用新型的旋转件的第一方式的一例的、沿包含轴部的面(图1(b)的A-A剖面)切断的局部剖视图。图1(b)是示出本实用新型的旋转件的第一方式的一例的从轴向观察到的示意图。图2(a)是示出本实用新型的旋转件的第一方式的另一例的、沿包含轴部的面(图2(b)的B-B剖面)切开的局部剖视图。图2(b)是示出本实用新型的旋转件的第一方式的另一例的从轴向观察到的示意图。图3是示出本实用新型的旋转件的第一方式的再一例的剖视图。图4(a)是示出本实用新型的旋转件的第二方式的一例的、沿包含轴部的面(图4(b)的C-C剖面)切开的局部剖视图。图4(b)是示出本实用新型的旋转件的第二方式的一例的从轴向观察到的示意图。图5是示出具有8极的极各向异性的参考例的R-T-B系烧结环形磁铁的一例的剖视图。图6是示出具有8极的极各向异性的参考例的R-T-B系烧结环形磁铁的另一例的剖视图。图7是示出包含具有14极的极各向异性以及剖面14边形的内周面的R-T-B系极各向异性烧结环形磁铁的比较例的旋转件的剖视图。图8是示出包含具有14极的极各向异性以及剖面7边形的内周面的R-T-B系极各向异性烧结环形磁铁的比较例的旋转件的剖视图。图9是示出在R-T-B系极各向异性烧结环形磁铁的轴向端面的内缘部设置的倒角部的半径A、从内周面的多边形的中心轴到顶点的距离B、以及从中心轴朝向构成多边形的边的最短距离C之间的关系的示意图。图10是在具有剖面14边形的内周面且示出14极的极各向异性的R-T-B系烧结环形磁铁中,仅对轴向端面的内缘部的各边的一部分进行了倒角的情况下的从轴向观察到的示意图。图11是在具有剖面14边形的内周面且示出14极的极各向异性的R-T-B系烧结环形磁铁中,对轴向端面的内缘部的各边以包含多边形的顶点的方式进行了倒角的情况下的从轴向观察到的示意图。图12是在具有剖面14边形的内周面且示出14极的极各向异性的R-T-B系烧结环形磁铁中,对轴向端面的内缘部的各边以超出多边形的顶点的方式进行了倒角的情况下的从轴向观察到的示意图。图13是用于说明具有剖面多边形的内周面的环形磁铁的内径的定义的剖视图。图14是示出内外径比的范围的图表。图15(a)是示出在图1以及图2所示的旋转件中使用的轴部的主视图。图15(b)是示出在图1以及图2所示的旋转件中使用的轴部的侧视图。图16(a)是示出用于本实用新型的轴部的一例的主视图。图16(b)是示出用于本实用新型的轴部的一例的侧视图。图17(a)是示出用于本实用新型的轴部的一例的主视图。图17(b)是示出用于本实用新型的轴部的一例的侧视图。图18(a)是示出在图19所示的旋转件中使用的轴部的主视图。图18(b)是示出在图19所示的旋转件中使用的轴部的侧视图。图19(a)是沿包含示出比较例的旋转件的一例的轴部在内的面切开的局部剖视图。图19(b)是示出比较例的旋转件的一例的从轴向观察到的示意图。图20是示出比较例的旋转件的另一例的从轴向观察到的示意图。图21是示出比较例的旋转件的再一例的从轴向观察到的示意图。图22是示出比较例的旋转件的再一例的从轴向观察到的示意图。图23是示出比较例的旋转件的再一例的从轴向观察到的示意图。图24是示出比较例的旋转件的再一例的从轴向观察到的示意图。图25是示意性示出磁场中成形装置的一例的剖视图。图26是图25的D-D剖视图。图27(a)是示出用于对具有剖面多边形的内周面的环形磁铁进行制造的模具的示意图。图27(b)是示出对利用图27(a)的模具成形的成形体进行烧结而得到的环形磁铁的示意图。图27(c)是示出对图27(b)的环形磁铁进行加工而得到的环形磁铁的示意图。图28(a)是示出用于对具有剖面多边形的顶点沿着轴向偏斜的内周面的环形磁铁进行制造的模具的示意图。图28(b)是示出对利用图28(a)的模具成形的成形体进行烧结而得到的环形磁铁的示意图。图28(c)是图28(b)的环形磁铁的立体图。图29是用于说明进行R-T-B系极各向异性烧结环形磁铁的轴向端面的内缘部的倒角的方法的示意图。图30是用于说明同时进行R-T-B系极各向异性烧结环形磁铁的轴向端面的内缘部以及外缘部的倒角的方法的示意图。图31是用于说明在R-T-B系极各向异性烧结环形磁铁的轴向端面的内缘部形成台阶部的方法的示意图。附图标记说明:1…R-T-B系极各向异性烧结环形磁铁1a…外周面1b…内周面2a~2h…极3a~3h…顶点20a…中间位置11…极各向异性环形磁铁11a…外周面11b…内周面12a~12h…极13a~13c…顶点20…轴部20b…圆柱部20c…平坦部21、31、41、42、43、50、51、61…环形磁铁21a…外周面21b…内周面21c…圆31c、41c、42c、43c…倒角部100…第一方式的旋转件110…环形磁铁110a、110b…倒角部110e、110f…轴向端面120、121…轴部120b、121b…圆柱部120c、121…平坦部130…树脂隔离件101…第一方式的旋转件111…环形磁铁111a、111b…倒角部111e、111f…轴向端面131…树脂隔离件102…第一方式的旋转件112…环形磁铁112a…倒角部112e、112f…轴向端面112c…锥面132…树脂隔离件200…第二方式的旋转件210…环形磁铁210a、210b…台阶部210e、210f…轴向端面220…轴部230…树脂隔离件500…磁场中成形装置501、601、701…冲模502、601、701…芯体503…成形空间504…上冲头505…上部框架506…上部液压缸507…下冲头508…下部框架509…下部液压缸511、512…支柱513…基板515、715…磁场产生线圈516…环状套筒517…槽800、810…倒角砂轮820…台阶部形成砂轮900、901、902、903、904、905…比较例的旋转件910、911、912、913、914、915…环形磁铁910b…内周面920、921、922、923、924、925…轴部920a、921a、922a、923a、924a、925a…多棱柱部920b…圆柱部930、931、932、933、934、935…树脂隔离件具体实施方式[1]表面磁铁型旋转件(1)结构(A)第一方式表面磁铁型旋转件(以下,有时仅称为“旋转件”。)的第一方式的特征在于,包括:具有剖面圆形的外周面和剖面多边形的内周面、且在所述外周面具有多个极的R-T-B系极各向异性烧结环形磁铁;向所述R-T-B系极各向异性烧结环形磁铁的轴中心插入的柱状的轴部;以及填充在所述轴部与所述R-T-B系极各向异性烧结环形磁铁之间、用于将所述轴部固定于所述R-T-B系极各向异性烧结环形磁铁的树脂隔离件,所述R-T-B系极各向异性烧结环形磁铁在轴向端面的内缘部具有倒角部,所述轴部具有形成于轴向中央部的至少一处平坦部和在所述平坦部的轴向两端延伸设置的圆柱部,所述树脂隔离件以包括所述轴部的平坦部且成为覆盖所述倒角部的状态的方式填充在所述轴部的轴向中央部的外周面与所述R-T-B系极各向异性烧结环形磁铁的内周面之间。图19(a)以及图19(b)示出比较例的旋转件。比较例的旋转件900具有:具有剖面正八边形的内周面的8极的R-T-B系极各向异性烧结环形磁铁910;插入到所述环形磁铁910的柱状的轴部920;以及填充在轴部920与环形磁铁910之间、用于将轴部920固定于环形磁铁910的树脂隔离件930。所述环形磁铁910形成为,形成内周面的剖面正八边形的顶点沿轴向成为直线。换句话说,多边形的顶点没有沿着轴向倾斜(偏斜)。轴部920具有多棱柱部920a和在多棱柱部920a的轴向两端延伸设置的圆柱部920b,多棱柱部920a的轴向长度与环形磁铁910的轴向长度以及树脂隔离件930的轴向长度大体相同。树脂隔离件930配置为,填充在轴部920的多棱柱部920a的外周面与环形磁铁910的内周面910b之间。比较例的旋转件具有剖面多边形的内周面,因此,能够防止轴部与磁铁之间的空转,但与本实用新型的第一方式的旋转件不同,在轴向端面的内缘部没有形成倒角,因此,防止轴部沿轴向脱落的效果不充分。比较例的旋转件900也可以例如像图20所示设为由具有剖面四边形的内周面的4极(或者8极或12极)的极各向异性环形磁铁911、柱状的轴部921、以及树脂隔离件931构成的旋转件901,还可以例如像图21所示设为由具有剖面六边形的内周面的6极(或者12极)的极各向异性环形磁铁912、柱状的轴部922、以及树脂隔离件932构成的旋转件902。接下来,图1(a)以及图1(b)示出本实用新型的旋转件的第一方式的一例。旋转件100具有:具有剖面正七边形的内周面的14极的R-T-B系极各向异性烧结环形磁铁110;插入到所述环形磁铁110的柱状的轴部120;以及填充在轴部120与环形磁铁110之间、用于将轴部120固定于环形磁铁110的树脂隔离件130。所述环形磁铁110在轴向端面110e、110f的内缘部具有倒角部110a、110b。该倒角部110a、110b由相对于轴向端面110e、110f大体呈45°倾斜的圆锥面构成,通过该圆锥面而形成于轴向端面110e、110f的圆形成为与正七边形的顶点重合这样的深度。环形磁铁110的内周面形成为,剖面正七边形的顶点沿轴向成为直线。环形磁铁110除了多边形的顶点个数及极数不同、以及在轴向端面110e、110f的内缘部具有倒角部110a、110b以外,与在比较例的旋转件900中使用的环形磁铁910相同。轴部120为在中央部具有一处平坦部120c的圆柱状。通过使树脂130在环形磁铁110的剖面多边形的内周面与轴的平坦部120c之间注塑成型,能够防止轴与环形磁铁之间的空转。图2(a)以及图2(b)示出本实用新型的旋转件的第一方式的另一例。除了在环形磁铁111的轴向端面111e、111f的内缘部形成的倒角部111a、111b的深度比环形磁铁110的倒角部110a、110b浅之外,旋转件101与旋转件100相同。即,环形磁铁111是仅在轴向端面111e、111f的内缘部的多边形的边的一部分进行了倒角的例子。在旋转件100以及旋转件101中,使用具有14极的极各向异性取向且具有剖面正七边形的内周面的环形磁铁110以及环形磁铁111,多边形的角数(顶点个数)少于极数。在极数较多的环形磁铁中,在由具有与极数相同的顶点个数(角数)的多边形形成内周面(例如极数为14极且内周面为14边形)的情况下,多边形的各边的长度短,并且边彼此的角度也增大,因此,在进行倒角时,难以仅在边的一部分形成倒角部。在这种情况下,通过使用具有剖面多边形的顶点个数相对于极数减少的内周面的极各向异性环形磁铁,能够增大用作防脱的倒角部分的面积。旋转件100构成为,在环形磁铁110的轴向端面110e、110f的两方的内缘部设置倒角部110a、110b,利用树脂隔离件130覆盖该倒角部110a、110b,从而抑制轴部120的轴向(图面左右方向)上的脱落。同样,旋转件101构成为,在环形磁铁111的轴向端面111e、111f的两方的内缘部设置倒角部111a、111b,利用树脂隔离件131覆盖该倒角部111a、111b,从而抑制轴部120沿轴向(图面左右方向)脱落。在这些实施方式中,优选树脂隔离件130以及树脂隔离件131分别填充为不会从环形磁铁110以及环形磁铁111的轴向端面露出。图3示出本实用新型的旋转件的第一方式的再一例。旋转件102在环形磁铁112的内周面形成锥面112c,倒角部112a仅形成在一方的轴向端面112e的内缘部,除此之外与旋转件100相同。在内周面形成有锥面112c的环形磁铁112是使用如下的模具而制造的,在利用粉末冶金法使成形体成形时,为了在成形后容易使成形体从模具脱落,该模具构成为入口侧比里侧宽。这样的模具的结构被称为脱模锥面。如图3所示,利用具有脱模锥面的模具制造出的极各向异性烧结环形磁铁112的一方的轴向端面112f的内径比另一方的轴向端面112e的内径(除了倒角部112a)大。即,在内周面侧具有锥面112c。环形磁铁112为,针对利用具有这样的脱模锥面的模具制造出的环形磁铁,仅在内径较小的一侧的轴向端面112e的内缘部形成倒角部112a而成的环形磁铁。由于环形磁铁112在内周面侧具有锥面112c,因此即便没有在两方的端面内缘部设置倒角部,通过仅在内径小的一侧(轴向端面112e)设置倒角部112a,也能够发挥双轴方向(图中的上下方向)的防脱效果。(B)第二方式表面磁铁型旋转件的第二方式的特征在于,包括:具有剖面圆形的外周面和剖面多边形的内周面、且在所述外周面具有多个极的R-T-B系极各向异性烧结环形磁铁;插入到所述R-T-B系极各向异性烧结环形磁铁的轴中心的柱状的轴部;以及填充在所述轴部与所述R-T-B系极各向异性烧结环形磁铁之间、用于将所述轴部固定于所述R-T-B系极各向异性烧结环形磁铁的树脂隔离件,所述R-T-B系极各向异性烧结环形磁铁在轴向端面的内缘部具有台阶部,所述轴部具有形成于轴向中央部的至少一处平坦部和在所述平坦部的轴向两端延伸设置的圆柱部,所述树脂隔离件以包含所述轴部的平坦部且成为覆盖所述台阶部的状态的方式填充在所述轴部的轴向中央部的外周面与所述R-T-B系极各向异性烧结环形磁铁的内周面之间。即,除了代替在R-T-B系极各向异性烧结环形磁铁的轴向端面的内缘部设置倒角部而设置有台阶部之外,表面磁铁型旋转件的第二方式与表面磁铁型旋转件的第一方式相同。图4(a)以及图4(b)示出本实用新型的旋转件的第二方式的一例。除了代替倒角部110a、110b而在环形磁铁210的轴向端面210e、210f的内缘部形成有台阶部210a、210b之外,旋转件200与第一方式的旋转件100相同。旋转件200构成为,在环形磁铁210的轴向端面210e、210f的两方的内缘部设置台阶部210a、210b,利用树脂隔离件230覆盖该台阶部210a、210b,从而抑制轴部220沿轴向(图中的左右方向)脱落。在该实施方式中,树脂隔离件230优选填充为不会从环形磁铁210的轴向端面210e、210f露出。(C)第三方式表面磁铁型旋转件的第三方式的特征在于,包括:具有剖面圆形的外周面和剖面多边形的内周面、且在所述外周面具有多个极的R-T-B系极各向异性烧结环形磁铁;插入到所述R-T-B系极各向异性烧结环形磁铁的轴中心的柱状的轴部;以及填充在所述轴部与所述R-T-B系极各向异性烧结环形磁铁之间、用于将所述轴部固定于所述R-T-B系极各向异性烧结环形磁铁的树脂隔离件,所述R-T-B系极各向异性烧结环形磁铁中,形成所述内周面的剖面多边形的顶点沿轴向偏斜,所述轴部具有形成于轴向中央部的至少一处平坦部和在所述平坦部的轴向两端延伸设置的圆柱部,所述树脂隔离件以包括所述轴部的平坦部的方式填充在所述轴部的轴向中央部的外周面与所述R-T-B系极各向异性烧结环形磁铁的内周面之间。即,除了代替在R-T-B系极各向异性烧结环形磁铁的轴向端面的内缘部设置倒角部、以使形成内周面的剖面多边形的顶点沿轴向偏斜的方式形成有内周面以外,表面磁铁型旋转件的第三方式与表面磁铁型旋转件的第一方式相同。通过使形成内周面的剖面多边形的顶点沿轴向偏斜,即便不具有倒角部或者台阶部,也能够防止轴部沿轴向脱落。表面磁铁型旋转件的第三方式也可以在R-T-B系极各向异性烧结环形磁铁的轴向端面的内缘部具有倒角部或者台阶部。(2)R-T-B系极各向异性烧结环形磁铁本实用新型所使用的R-T-B系极各向异性烧结环形磁铁(以下,有时仅称为“环形磁铁”。)具有剖面圆形的外周面和剖面多边形的内周面,在所述外周面具有多个极,并且在轴向端面的内缘部具有倒角部或台阶部,或者形成内周面的剖面多边形的顶点沿轴向偏斜。通过具有剖面多边形的内周面,在轴部与内周面之间填充树脂隔离件而形成旋转件时,防止了树脂隔离件与环形磁铁之间的空转。另外,通过在轴向端面的内缘部具有倒角部或台阶部、或者由顶点偏斜的多边形形成内周面,从而树脂隔离件与环形磁铁不会在轴向上偏移,能够防止轴部沿轴向脱落。(A)环形磁铁的形状以图5所示的8极各向异性烧结环形磁铁1为例来说明本实用新型所使用的环形磁铁的形状。R-T-B系极各向异性烧结环形磁铁1是在剖面圆形的外周面1a具有多个极2a~2h的多极各向异性(图中为8极),环形磁铁1的内周面1b的剖面为多边形(图中为八边形)。环形磁铁1的极数是多边形的顶点3a~3h的个数的整数倍,优选与顶点个数相同或者是顶点个数的两倍。环形磁铁的极数优选为4极、6极、8极、10极、12极以及14极中的任一种。特别是在极数为10极、12极或者14极的情况下,与以往相比,能够减小磁铁的径向上的厚度。关于如何设定多边形的顶点个数,根据极数适当进行调节即可。优选多边形为正多边形。内周面1b的剖面为正多边形是指,也可以包含制造上的稍许误差等,不限于数学上严格的正多边形。优选使外周面的邻接的两个极的中间位置中的至少一个(例如为中间位置20a)与构成内周面的剖面多边形的顶点3a~3h中的至少一个(例如为顶点3b)在周向上一致。通过采用这样的结构,能够容易地形成剖面多边形。例如像图5的箭头A所示,环形磁铁1内部的磁通以从一个极(例如极2a)朝向邻接的极(例如极2b)而横跨多边形的顶点3a~3h部分的方式呈圆弧状流动。顶点3a~3h部分看起来会妨碍在极间流动的磁通,但在极各向异性烧结环形磁铁中,磁通大多在外周面附近流动,因此,几乎不会发生磁效率的降低。特别是在本申请所示的内外径比的范围内,效率降低极其轻微。本实用新型所使用的极各向异性烧结环形磁铁中,烧结时的内径形状的变形与外表面侧相比而较少,容易成为与成形时的内径侧的模具形状相仿的形状。即,通过磁场中压缩成形来制作具有与极各向异性烧结环形磁铁的极数相同的个数的顶点的内径多边形,并且使外周面上的邻接的两个极的中间位置与多边形的顶点在周向上一致,在这种情况下,烧结后的内径形状成为与成形时的内径形状相仿的形状以及倾向。这是因为,在R-T-B系烧结磁铁的成形时的取向方向和与取向方向正交的方向上,烧结时的收缩程度不同(磁粉的取向方向的收缩率比与取向方向正交的方向的收缩率大,因此,具有外周面侧的极位置变得平坦、极间成为凸部这样的收缩各向异性)。需要说明的是,在本实用新型中,邻接的两个极的中间位置是根据设计上的极位置而推导的位置,包括制造上产生的偏差在内而称为中间位置。需要说明的是,内周面侧成为与外周面侧的收缩变形相仿的形状,尤其是在极数少的极各向异性磁铁的情况下,容易显著地表现出该倾向。如图6所示,即便在外周面11a具有8个极12a~12h的极各向异性烧结环形磁铁11具有剖面正三边形(具有三个顶点13a~13c)的内周面11b的情况下(极数不是多边形的顶点个数的整数倍的情况下),也具有止转的效果,但极各向异性烧结环形磁铁11的壁厚(径向的厚度)变厚,无法有效地使用磁铁材料。此外,由于重量变重且惯性力变大,因此,不适合作为频繁进行旋转停止的旋转机的转子。优选R-T-B系极各向异性烧结环形磁铁的内周面没有进行加工。通常,环形磁铁在烧结后,进行两端面的研磨、外周面的研磨以及内周面的研磨,通过省略在研磨工序中成本最高的内周面的研磨,能够有助于大幅降低成本。在不进行环形磁铁的内周面的研磨的情况下,与进行了研磨的情况相比,内径面的尺寸精度略微变差,但在本实用新型中,通过注塑成型在磁铁与轴部之间形成树脂隔离件而能够使磁铁与轴部一体化,因此,即便磁铁的内周面的尺寸精度较低,也不会产生太大的问题。(B)外周面以及内周面的结构作为环形磁铁的优选方式,举出了外周面的极数与内周面的剖面多边形的顶点个数相同的情况。然而,在采用了极数多的环形磁铁的情况下,与之相伴,多边形的顶点个数变多,内周面的剖面形状接近圆,因此,存在R-T-B系烧结环形磁铁与轴部的止转效果降低的情况。在这种情况下,优选将内周面的剖面形状设为具有极数的一半数量的顶点的多边形,此外,在极数变多的情况下,也可以将多边形的顶点个数减少为极数的1/3、1/4…。例如,如图7所示,在外周面为14极的极各向异性烧结环形磁铁的情况下,若将内周面的剖面形状设为顶点个数为14个的多边形,则剖面形状接近圆,导致止转效果降低。在该情况下,如图8所示,通过将内周面的剖面形状设为顶点个数为7个的多边形,虽然磁铁的使用效率稍微降低,但是能够在最小限度地降低使用效率的同时,获得止转效果。本实用新型所使用的环形磁铁优选具有4极、6极、8极、10极、12极或者14极的多极各向异性,并且优选外周面的极数为多边形的顶点个数的整数倍。R-T-B系极各向异性烧结环形磁铁优选为,外周面的邻接的两个极的中间位置中的至少一个与构成内周面的剖面多边形的顶点中的至少一个在周向上一致。此外,优选所述极以及所述顶点沿轴向偏斜。(C)倒角部以及台阶部图9是示出在环形磁铁31的轴向端面的内缘部设置的倒角部31c的半径(A)、从中心轴到多边形的顶点为止的距离(B)、以及从中心轴朝向构成多边形的边的最短距离(C)之间的关系的示意图。倒角部在由环形磁铁的轴向端面和内周面形成的角部(内缘部)形成为以中心轴为中心的圆状,此时的圆的半径为倒角部的半径。图10、图11以及图12示出在具有剖面14边形的内周面且具有14极的极各向异性的R-T-B系极各向异性烧结环形磁铁的轴向端面的内缘部以三种深度设置了倒角的例子。针对各个情况来说明倒角部的半径(A)、从中心轴到多边形的顶点为止的距离(B)、以及从中心轴朝向构成多边形的边的最短距离(C)之间的关系。图10示出仅在轴向端面的内缘部的各边的一部分进行了倒角的环形磁铁41。图10所示的环形磁铁41示出倒角部41c的半径A比从中心轴到多边形的顶点为止的距离B小、且比从中心轴到多边形的边为止的最短距离C大的情况。换句话说,具有B>A>C的关系。图11示出以包括多边形的顶点部分的方式进行了倒角的环形磁铁42。图11所示的环形磁铁42中,倒角部42c的半径A与从中心轴到多边形的顶点为止的距离B大体相同。换句话说,具有A=B>C的关系。图12示出以倒角部43c的半径A比从中心轴到多边形的顶点为止的距离B大的方式形成了倒角部43c的环形磁铁43。换句话说,具有A>B>C的关系。即,倒角部41c、42c、43c的大小为,图10所示的环形磁铁41最小,图11所示的环形磁铁42、图12所示的环形磁铁43依次变大。倒角部较大的一方在之后树脂成形的情况下的防脱效果较大,但如图10所示的环形磁铁41那样,采用仅在轴向端面的内缘部的各边的一部分设置的倒角部41c,也能够充分地发挥防脱效果。因此,通过不进行不必要的倒角,从而能够提高倒角作业的效率。以上,对倒角部的形状进行了说明,但关于台阶部也相同,在至少仅在轴向端面的内缘部的各边的一部分设置台阶部的情况下,也能够充分地发挥防脱效果。(D)剖面偏斜的内周面通过将环形磁铁的内周面形成为剖面多边形的顶点沿轴向偏斜,即便不形成上述的倒角部或者台阶部,也能够发挥防止轴部沿轴向脱落的效果。如后所述,通过使用使磁化线圈沿着腔体的轴向倾斜(偏斜)配置的模具进行磁场中成形,由此获得具有这样的剖面多边形的顶点沿轴向偏斜的内周面的环形磁铁。(E)内径与外径之比(内外径比)本实用新型所使用的环形磁铁的内径(D1)与外径(D2)之比D1/D2优选使用根据环形磁铁的极数P而由式:D1/D2=1-K(π/P)表示的数值。[其中,P=4时,K的值为0.51~0.70,P=6时,K的值为0.57~0.86,P=8时,K的值为0.59~0.97,P=10时,K的值为0.59~1.07,P=12时,K的值为0.61~1.18,以及P=14时,K的值为0.62~1.29。]在此,如图13所示,环形磁铁21的内径D1是与内周面21b的剖面多边形外接的圆21c的直径。当K的值变大时,内外径比变小,当K的值变小时,内外径比变大。在各个极数中,当K的值低于上述范围的下限时,环形磁铁的壁厚变薄,烧结体的强度低于因各向异性而产生的应力,有可能在烧结时(烧结体被冷却的过程)使烧结体产生裂纹,或者因使用环形磁铁时的发热等而产生裂纹。另一方面,即便K的值超过上限也能够制造磁铁,但当环形磁铁的壁厚变得过厚时,仅是增加了不必要的(在磁特性上不需要的)磁铁的量,另外,因重量增加而导致惯性力的增加,因此作为马达等的旋转件是不优选的。表1示出在各极数中根据K的值而利用D1/D2=1-K(π/P)求出的D1/D2的值的范围。【表1】极数K的值D1/D2的值4极0.51~0.700.45~0.66极0.57~0.860.55~0.78极0.59~0.970.62~0.7710极0.59~1.070.665~0.81512极0.61~1.180.69~0.8414极0.62~1.290.71~0.86为了进一步防止因极各向异性烧结环形磁铁的应力而导致的破裂的发生,并且为了抑制惯性力的增加,优选为,在极数为4极的情况下,K的值为0.51~0.64,在极数为6极的情况下,K的值为0.57~0.76,在极数为8极的情况下,K的值为0.59~0.84,在极数为10极的情况下,K的值为0.59~0.91,在极数为12极的情况下,K的值为0.61~0.99,以及在极数为14极的情况下,K的值为0.62~1.07。表2示出在各极数中根据优选的K的值的范围而利用式:D1/D2=1-K(π/P)求出的优选的D1/D2的值的范围。【表2】极数K的优选值D1/D2的优选值4极0.51~0.640.5~0.66极0.57~0.760.6~0.78极0.59~0.840.67~0.7710极0.59~0.910.715~0.81512极0.61~0.990.74~0.8414极0.62~1.070.76~0.86图14示出将这些D1/D2的值的范围、以及优选的D1/D2的值的范围相对于极数而绘制的图表。由线A示出D1/D2的值的上限,由线B示出D1/D2的值的下限。另外,由线A示出优选的D1/D2的值的上限,由线C示出优选的D1/D2的值的下限。即,由线A和线B夹持的范围是本实用新型的环形磁铁中的内外径比D1/D2的范围,由线A和线C夹持的范围是内外径比D1/D2的优选范围。根据图14明显可知,优选的内外径比D1/D2的值处于D1/D2的值的范围中的数值较大的一侧的范围,即、环形磁铁的壁厚较薄的一侧的范围内,通过使内外径比D1/D2采用这样的范围,能够抑制因应力导致的破裂的发生,并且能够利用尽可能少的磁铁量来发挥充分的磁特性,并且能够获得不增加惯性力的环形磁铁。但是,在使具有较小的外径(外径为20mm以下)的环形磁铁成形时,当采用优选的K的值时,有时产生制造效率的问题。例如,即便是相同的内外径比,与成形较大外形的环形磁铁的情况相比,在成形较小外径的环形磁铁的情况下,由于环形磁铁的壁厚的绝对值变薄,因此,成形用的模具腔体的空隙变薄,不容易向空隙供给磁粉。因此,产生了生产效率非常低这样的问题。在工业生产上考虑到制造成本,需要以一定的时间间隔进行成形作业,因此,在小外径的环形磁铁的制造中,优选进一步减小内外径比(作为K的值而采用范围内的较大一侧的值),从而将环形磁铁的壁厚、即模具腔体的空隙设定得较厚。这样在使具有较小的外径的环形磁铁成形的情况下,不仅以防止环形磁铁的破裂为目的,还需要通过将K值设定得较大,由此确保腔体的空隙,使磁粉向腔体的供给变得容易。本实用新型不仅适用于磁极与环形磁铁的轴线平行的极各向异性环形磁铁,还能够适用于作为齿槽转矩对策而使磁极相对于轴线具有角度的(偏斜的)极各向异性环形磁铁。(3)轴部如图15(a)以及图15(b)所示,图1(a)以及图2(a)所示的旋转件100以及旋转件101所使用的轴部120包括形成于中央部的平坦部120c和构成该平坦部120c以外的部分的圆柱部120b。另外,图4(a)所示的旋转件200所使用的轴部220也是与轴部120相同的形状。本实用新型的旋转件所使用的轴部只要在中央部具有平坦部,也可以在中途改变轴部的粗细。即,可以如图15(a)以及图15(b)所示,将平坦部形成为一处凹部,也可以如图16(a)以及图16(b)所示,以使平坦部对置的方式设置两处平坦部。此外,还可以如图17(a)以及图17(b)所示,构成为使轴向中央部的外径比轴部20的轴向两端部大,且在轴向中央部的外周面的至少一处设置平坦部。图19(a)以及图19(b)所示的比较例的旋转件900所使用的轴部920如图18(a)以及图18(b)所示,由多棱柱部920a和在多棱柱部920a的轴向两端延伸的圆柱部920b。多棱柱部920a形成在轴部920的轴向中央部,且成为剖面多边形,以便在与树脂隔离件930之间具有止转效果。在本实用新型的旋转件中,也能够使用图18(a)以及图18(b)所示的轴部。多棱柱部920a的剖面形状没有特别限定,例如,可以采用四边形、五边形、六边形。另外,该剖面形状可以与环形磁铁910的内周面910b的剖面形状相同,也可以不同。例如,如图22所示,也可以采用具有剖面八边形的内周面的8极的极各向异性环形磁铁913与具有剖面四边形的多棱柱部923a的轴部923的组合,如图23所示,还可以采用具有剖面八边形的内周面的8极的极各向异性环形磁铁914与具有剖面六边形的多棱柱部924a的轴部924的组合。此时,通过在图22以及图23所示的环形磁铁913以及环形磁铁914的轴向端面的内缘部形成倒角部或者台阶部,能够获得本实用新型的旋转件。另外,在圆柱状的轴部的周面也可以具有滚花。在图15(a)~图18(b)所示的轴部120、121、20、920中,圆柱部120b、121b、20b、920b是用于将旋转件与其他的设备连接的部分,优选为圆柱状。图17(a)以及图17(b)所示的轴部20的中央部以及图18(a)以及图18(b)所示的多棱柱部920a可以与在其两端部延伸设置的圆柱部一体地形成,也可以通过向设于所述中央部或者多棱柱部920a的轴中心的孔插入圆柱而形成。轴部由与环形磁铁的内径相比而尽可能小的直径构成,由此能够减小惯性力,是优选的。但是,当轴部过细时,无法得到止转效果,因此,需要考虑到止转效果而适当设定。对于轴部的材质而言,只要能够获得所需的强度,则可以采用任意的材质,能够采用非磁性体或磁性体。例如,在如径向环形磁铁那样磁通贯穿内径侧的情况下,若使用磁性体的轴部,则在磁路方面的效率很好,但在外周面极各向异性的情况下,无需考虑材料的磁性或非磁性。另外,从成本或强度的观点出发,在使用铁材料的情况下,也能够通过减小轴部的外径来降低惯性力。(4)树脂隔离件树脂隔离件填充在轴部的轴向中央部的多棱柱部或者平坦部的外周面与R-T-B系极各向异性烧结环形磁铁的内周面之间,并且以覆盖环形磁铁的轴向端面的内缘部的倒角部的方式(以成为覆盖的状态的方式)填充,通过使用比轴部轻的树脂,能够大幅降低旋转件的惯性力,并且由于加热时的轴部与环形磁铁的热膨胀的差异被树脂隔离件吸收,因此能够防止磁铁的破裂。例如如图24所示,在使用了具有较大直径的多棱柱部925a的轴部925的情况下,树脂隔离件935的径向厚度(壁厚)变薄,因此,吸收热膨胀差的效果降低。通过考虑环形磁铁的直径而适当地设定轴部的直径,由此决定树脂隔离件的径向厚度即可。树脂隔离件通过在向R-T-B系极各向异性烧结环形磁铁插入了轴部的状态下利用注塑成型来填充热塑性树脂而成。在使用轴向端面的内缘部不具有倒角部的环形磁铁进行组装的比较例的旋转件(例如图19(a)以及图19(b)所示的旋转件900)的情况下也具有如下方法:使用预先成形的树脂隔离件930和具有多棱柱部920a的轴部920,利用借助粘结剂等粘结于轴部920的多棱柱部920a以及环形磁铁910的内周面910b的方法进行固定(填充)。在使用了内周面不具有倒角部或台阶部的磁铁的比较例的旋转件的情况、且是选择了基于粘结的方法的情况下,为了防止加热时的轴部与环形磁铁的热膨胀差所引起的磁铁的破裂,作为粘结剂,优选采用加成反应型的硅系粘结剂等硬度低的粘结剂。但是,加成反应型的硅系粘结剂作为固化催化剂而含有铂金,因此,存在例如在含有胺的涂装面(环氧阳离子电沉积涂装等)上没有固化的情况,或者存在根据环境的不同而粘结性降低的情况。与之相对,通过注塑成型来填充树脂隔离件的方法由于能够扩大表面处理的选择范围,因此是在构成本实用新型的使用了R-T-B系极各向异性烧结环形磁铁的旋转件时合适的方法。需要说明的是,在任一方法中,均优选将树脂隔离件填充为不会从R-T-B系极各向异性烧结环形磁铁的端面(两端面)露出。[3]制造方法本实用新型所使用的R-T-B系极各向异性烧结环形磁铁优选实质上由R-T-B构成。在此,R为包含Y的稀土类元素中的至少一种,优选必须包含Nd、Dy以及Pr中的至少一种,T为过渡金属元素中的至少一种,优选为Fe。B为硼。R-T-B系极各向异性烧结环形磁铁优选具有24~34质量%的R、0.6~1.8质量%的B、以及剩余部分为Fe的组成。当R量小于24质量%时,残留磁通密度Br、顽磁力HcJ降低。当R量超过34%时,烧结体内部的富含稀土类的相的区域增多,因此残留磁通密度Br降低,并且组织方式也粗大化,使抗蚀性降低。在B量小于0.6质量%的情况下,作为主相的R2Fe14B相的形成所需的B不足,生成具有软磁性的性质的R2Fe17相,顽磁力HcJ降低。另一方面,当B量超过1.8质量%时,作为非磁性相的富含B的相增加,残留磁通密度Br降低。Fe的一部分也可以置换为Co,另外,也可以包括大约3质量%以下的Al、Si、Cu、Ga、Nb、Mo、W等元素。(1)磁粉的准备磁粉的粉碎优选分为粗粉碎和微粉碎来进行。实质上由R、T、B构成的原料合金的粗粉碎优选通过捣碎、颚式破碎、布朗研磨、圆盘磨、氢粉碎等来进行,微粉碎优选通过喷射磨、振动磨、球磨等来进行。为了防止氧化,均优选使用有机溶剂或非活性气体在非氧化环境中进行。粉碎后的平均粒度优选为2~8μm(F.S.S.S.)。当小于2μm时,磁粉的活性较高,容易发生氧化,因此烧结时的变形较大,磁特性也发生恶化。当超过8μm时,烧结后的结晶颗粒直径增大,容易引起磁化反转,导致顽磁力降低。(2)成形(a)第一方法R-T-B系极各向异性烧结环形磁铁的成形使用例如图25所示那样的磁场中成形装置500来进行。磁场中成形装置500具有由磁性体构成的冲模501、以及在冲模501的环状空间内呈同心状配置的剖面多边形的由非磁性体构成的芯体502,冲模501被支柱511、512支承,芯体502以及支柱511、512均被下部框架508支承。在冲模501和芯体502之间的成形空间503内分别嵌入由非磁性体构成的筒状的上冲头504和同样由非磁性体构成的筒状的下冲头507。需要说明的是,上冲头504和下冲头507的外周面侧为圆形,内周面侧为与芯体502的形状对应的多边形。下冲头507固定安装于基板513,另一方面,上冲头504固定于上部框架505。上部框架505以及下部框架508分别与上部液压缸506以及下部液压缸509连结。图26示出图25的D-D剖面。在圆筒状的冲模501的内表面形成有多个槽517,各槽517中埋设有磁场产生线圈515。在冲模501的内表面,以覆盖槽的方式设置有环状的非磁性体的环状套筒516。环状套筒516与芯体502之间为成形空间503。在图26中,各槽517内的磁场产生线圈515配置为电流沿与纸面垂直的方向流动,并且以周向上相邻的线圈的电流的朝向交替地成为相反朝向的方式连接。当在磁场产生线圈515中流动电流时,在成形空间503内产生如箭头A所示那样的磁通的流动,在磁通与环状的套筒接触的点(箭头的起点以及终点)处,形成有极性沿圆周方向依次交替地变化为S、N、S、N…的磁极(图中为8极)。此时,以使由磁场产生线圈515形成的磁极的位置与内径侧的芯体502的多边形的顶点的位置在周向上大体一致的方式配置磁场产生线圈515和芯体502。根据磁粉的取向方向的不同,R-T-B系烧结磁铁在烧结时的收缩程度不同。在极各向异性烧结环形磁铁的情况下,当使用内径以及外径均为圆形的腔体来制造磁铁时,在烧结后,外径侧成为极的位置平坦且极间相对突出的形状(极间具有顶点的多边形),内径侧成为与外径侧的变形对应的多边形、或者在外径侧突出的部分处具有凹陷的圆形。因此,在本实用新型中,芯体502的多边形的顶点配置为与邻接的两个磁极的中间位置一致。为了使磁粉取向,施加于成形空间503的磁场的强度优选为159kA/m以上,更优选为239kA/m以上。当取向磁场的强度小于159kA/m时,磁粉的取向不充分,无法获得良好的磁特性。成形压力优选为0.5~2ton/cm2。在成形压力小于0.5ton/cm2时,成形体的强度变弱而容易破损。另外,当成形压力超过2ton/cm2时,磁粉的取向紊乱而磁特性降低。(b)第二方法本实用新型所使用的、具有剖面圆形的外周面和剖面多边形的内周面、且在所述外周面具有多个极的R-T-B系极各向异性烧结环形磁铁除了使用图26所示的、具有轴剖面圆形的冲模501以及剖面多边形的芯体502的模具进行制造之外,也可以使用图27(a)所示的、具有轴剖面圆形的冲模601以及剖面圆形的芯体602的模具来制造。在对使用图27(a)所示的具有轴剖面圆形的冲模601以及剖面圆形的芯体602的模具进行磁场中成形而得到的成形体进行了烧结的情况下,如图27(b)所示,得到了与成形时的取向相仿且外周面以及内周面带圆角的八边形状的筒状的烧结体50。仅通过将该烧结体的外周面磨削加工成圆形,能够得到外周面为圆形且内周面为剖面八边形的、图27(c)所示的极各向异性环形磁铁51。需要说明的是,在本申请中,剖面多边形的内周面不仅是指在成形时由模具芯体形成的多边形状,还包含与外周面侧的变形相仿并带圆角的多边形(角部由圆弧形成的多边形:对角部进行倒角而成的多边形)。(c)第三方法例如如图28(a)所示,具有剖面多边形的顶点沿着轴向偏斜的内周面的环形磁铁是通过使用如下的模具进行磁场中成形而得到的,该模具具有轴剖面圆形的冲模701以及剖面圆形的芯体702、且使进行极各向异性取向的磁化线圈(磁场产生线圈715)沿着腔体的轴向偏斜(偏斜)配置。如图28(b)以及图28(c)所示,对利用该模具成形的成形体进行烧结而得到的极各向异性烧结环形磁铁的外周面侧具有其角部沿轴向倾斜(偏斜)的剖面多边形,并且内周面侧具有与外周面侧相仿且顶点沿轴向倾斜(偏斜)的剖面多边形(需要说明的是,关于图28(b)的内周面的偏斜,省略了图示。)。通过仅将该极各向异性烧结环形磁铁的外周面磨削加工成圆形,就能够得到外周面侧为圆形且内周面侧的剖面多边形的顶点沿着轴向偏斜的极各向异性环形磁铁。(3)烧结烧结优选在真空或者氩气环境中以1000~1150℃进行。当小于1000℃时,由于烧结不充分,无法获得所需的密度,磁特性降低。当超过1150℃时,由于过度烧结,发生变形、磁特性的降低。烧结通过在使用了Mo的耐热容器中放入Mo板并在其之上放置成形体来进行。为了防止烧结体烧粘于Mo板,优选通过机械加工等来提高Mo板的表面粗糙度,从而减少与成形体接触的接触面积。在Mo板为轧制材料且表面粗糙度较低的情况下,容易发生烧结体与Mo板的烧粘,并且在与烧结相伴的收缩的过程中,烧结磁铁有时发生变形。作为机械加工,优选喷砂处理。喷砂后的Mo板的表面粗糙度(JISR6001-1983)以Rmax计优选为5μm~100μm,更优选为7μm~50μm,进一步优选为10μm~30μm。当小于5μm时,容易发生烧结体与Mo板的烧粘,烧结后的磁铁发生变形。当超过100μm时,在收缩的过程中,烧结体卡挂于Mo板而发生变形。也能够向Mo板涂敷氧化钕等来防止烧结时的烧结体与Mo板的烧粘。(4)热处理在烧结后,优选对烧结体实施热处理。热处理可以在后述的加工前进行,也可以在加工后进行。(5)加工以及表面处理对于获得的烧结体,在将外周面、端面加工为根据需要而要求的尺寸之后,使用旋转砂轮,在轴向端面的内缘部形成倒角部或者台阶部。图29通过剖视图示意性示出在本实用新型所使用的R-T-B系极各向异性烧结环形磁铁1的轴向端面的内缘部形成了倒角部的情形。砂轮800具有圆锥台的形状,通过使圆锥台形状的侧面与环形磁铁1的轴向端面的内缘部接触,并一边旋转一边沿箭头方向按下,从而能够进行倒角。另外,也可以在外周面侧具有用于实现表面处理的膜厚均匀且防止缺口的倒角部。图30是示出在R-T-B系极各向异性烧结环形磁铁1的轴向端面的内缘部以及外缘部同时形成了倒角部的情形的示意图。砂轮810在圆盘状砂轮的单面具有圆弧状或者V字状的槽部,通过使该槽部与环形磁铁1的轴向端面的内缘部以及外缘部抵接,并一边旋转一边沿箭头方向按下,由此能够对轴向端面的内缘部以及外缘部同时倒角。图31通过剖视图示意性示出在R-T-B系极各向异性烧结环形磁铁1的轴向端面的内缘部形成了台阶部的情形。砂轮820具有圆板形状,通过使圆板面(外周附近)与环形磁铁1的端面接触,并一边旋转一边沿箭头方向按下,由此能够形成台阶部。在加工中,能够适当地使用外径研磨机、内径研磨机、平面研磨机或者外观加工机等现有的设备。可以根据需要来进行加工后的镀层、涂装、铝的真空蒸镀、化学合成处理等表面处理。接下来,根据参考例,对作为本实用新型所使用的环形磁铁的特征之一的内外径比进行说明。参考例1按照上述的制造方法,使用图25以及图26所示的磁场中成形装置制作出10个如下的极各向异性烧结环形磁铁,该极各向异性烧结环形磁铁具有包括23.5质量%的Nd、2.2质量%的Dy、6.5质量%的Pr、1.0质量%的B、剩余部分Fe及不可避免的杂质、以及作为微量的添加元素的Al、Nb以及Ga的组成,且在外周面具有8极。此外,除了根据极数而改变了磁场中成形装置的结构之外,与8极各向异性烧结环形磁铁同样地分别制作出10个4极、6极、10极、12极以及14极的极各向异性烧结环形磁铁。需要说明的是,用于制造各极数的极各向异性烧结环形磁铁的磁场中成形装置使用了如下的结构:具备与环形磁铁的极数相应的磁场产生装置,且将具有顶点数目与环形磁铁的极数相同的正多边形的剖面形状的芯体配置为,正多边形的顶点位置与邻接的两个磁极的中间位置一致。对于烧结后的环形磁铁,在以0.5mm的加工余量对外径进行了研磨之后,对两端面进行了平面研磨。没有进行内径面的研磨。各环形磁铁的内外径比如表3所示。【表3】极数内外径比4极0.66极0.78极0.7710极0.81512极0.8414极0.86对外径研磨后的环形磁铁有无裂纹进行了确认,在全部的磁铁中未产生裂纹。参考例2除了将变更磁场中成形装置的芯体的外径而得到的环形磁铁的内外径比变更为表4所示之外,与参考例1同样地制作出4极、6极、8极、10极、12极以及14极的极各向异性烧结环形磁铁。【表4】极数内外径比4极0.656极0.758极0.8210极0.86512极0.8914极0.91对外径研磨后的环形磁铁有无裂纹进行了确认,在全部的条件下,10个中的1~7个磁铁产生了裂纹。参考例3除了将变更磁场中成形装置的芯体的外径而得到的环形磁铁的内外径比变更为表5所示之外,与实施例1同样地制作出4极、6极、8极、10极、12极以及14极的极各向异性烧结环形磁铁。【表5】极数内外径比4极0.46极0.58极0.5710极0.61512极0.6414极0.66对外径研磨后的环形磁铁有无裂纹进行了确认,在全部的磁铁中,没有产生裂纹。但是,由于该磁铁的内外径比较小且重量较重,因此,不适合作为要求较小的惯性力的旋转机的旋转件。当前第1页1 2 3