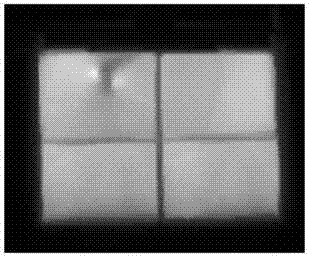
本发明涉及电热
技术领域:
,具有涉及一种基于石墨烯的高可靠性的发热膜及其制备方法。
背景技术:
:cvd(chemicalvapordeposition,化学气相沉积)制备的石墨烯薄膜作为一种由单层碳原子构成的蜂巢状二维连续的透明导电材料,表面通过合理的电路设计,在外加电场的作用下,能够将电能转化为光能,发射波长主要在5~15μm的远红外线,从而可制备主动发射红外线的理疗产品。然而,通过cvd法制备的高品质的石墨烯薄膜,其表面含氧极性基团极少,从而使得石墨烯薄膜宏观上几乎完全化学惰性,并且加工过程中,容易出现损伤;另外,无论是透明塑料基底,例如pet,还是石墨烯薄膜表面,对金属浆料的附着力都很弱,因此,对印刷在其上的印刷电极作用力弱不足以支撑多次反复弯折而保持电极不脱落的情况,也即是说,当发热膜受外力时,印刷电极极易从石墨烯表面/基底表面脱落,从而造成石墨烯发热膜发热不良或和功能丧失等问题,进而严重影响制成过程中的成品率。即使是小分子掺杂的cvd石墨烯,随着时间的推移,也会逐渐失效,导电性下降,从而影响制成品的工作状态使用可靠性,容易出现接触不良和功能丧失等问题,从而严重影响产品使用稳定性。技术实现要素:针对上述存在的技术问题,本发明提供一种基于石墨烯的高可靠性的发热膜及其制备方法。为了解决上述技术问题,本发明采用的技术方案为:一种基于石墨烯的高可靠性的发热膜,其包括自下而上依次层叠设置的透明基底、附着胶层、石墨烯复合层和电极层,其中,所述石墨烯复合层包括石墨烯层,以及位于所述石墨烯层上的阻抗匹配层,且所述阻抗匹配层与所述石墨烯层相接触;所述电极层的电极包括依次贯穿所述阻抗匹配层和石墨烯层的接触部,以及位于所述接触部顶部的搭接部,且所述接触部与所述附着胶层相接触,所述搭接部与所述阻抗匹配层相搭接。其中,所述石墨烯层的表面具有连续的二维结构。进一步地,所述石墨烯复合层还包括位于所述石墨烯层和所述阻抗匹配层之间的封装粘结层,且所述封装粘结层的厚度小于所述石墨烯层的二维结构的最大高度,使得所述阻抗匹配层与所述石墨烯层相接触。其中,所述封装粘结层为涂布在所述石墨烯层上的高分子成膜树脂固化成膜而成,和/或,所述阻抗匹配层为涂布在所述封装粘结层上的导电材料固化成膜而成。其中,所述封装粘结层的成膜厚度为100~2000nm;和/或,所述阻抗匹配层的成膜厚度为10~500nm。其中,所述封装粘结层的成膜厚度为200~500nm,和/或,所述阻抗匹配层的干膜厚度为50~200nm。进一步地,所述电极的横截面呈“t”字形。本发明还提供了一种基于石墨烯的高可靠性的发热膜的制备方法,其包括步骤:s1,将cvd法制备的石墨烯薄膜复型转移至透明基底上;s2,在石墨烯薄膜表面涂布一层高分子成膜树脂,并固化成膜得到封装粘结层;s3,在所述封装粘结层上涂布一层导电材料,并固化成膜得到阻抗匹配层;s4,按照预设的电极图案,在所述阻抗匹配层、封装粘结层和石墨烯层进行激光刻蚀,然后印刷电极浆料;其中,所述步骤s4中激光刻蚀时,所采用的激光机的激光波长为355-1064nm,功率为1-50w。其中,所述步骤s1中的石墨烯薄膜是在经过粗糙化的生长基底上制备得到的,且其表面具有连续二维结构。其中,所述步骤s1中采用的是液态胶黏剂将所述石墨烯薄膜复型转移至所述透明基底上的。进一步地,采用高温退火法对所述生长基底进行粗糙化,退火温度为980℃-1050℃,真空度至20pa-60pa,持续退火1-10min。本发明的有益之处在于:本发明公开了一种基于石墨烯的高可靠性的发热膜及其制备方法,其通过在透明基底表面形成的附着胶层,即引入能够与金属浆料中的成型树脂反应的活性组分,能够显著提高金属浆料的附着力;通过在石墨烯层上设置阻抗匹配层,从而有效提高石墨烯表面的导电性稳定性和表面极性,也降低接触阻抗,提高电极附着力;进一步,通过设置粘结层作为石墨烯层和阻抗匹配层之间的中间介质,以增强石墨烯层和阻抗匹配层之间的作用力,从而提高发热膜的加工成品率和使用可靠性,并且通过对石墨烯复合层(即石墨烯层、封装粘结层和阻抗匹配层)进行刻蚀加工,使得电极层的电极直接与附着胶层直接接触,使得印刷浆料电极附着力增强,从而有效降低电极层从石墨烯薄膜表面脱落的概率,提高了发热膜的稳定性。附图说明图1为本发明的一种基于石墨烯的高可靠性的发热膜的一实施例的结构示意图;图2为反映本发明的一种基于石墨烯的高可靠性发热膜的制备方法过程中该发热膜的结构变化的示意图;图3a为反映对照样品发热膜工作状态时的红外成像图;图3b为反映采用本发明的一种基于石墨烯的高可靠性发热膜的制备方法所制备得到的发热膜工作状态时的红外成像图;图4a为反映对照样品发热膜的银浆电极脱落的微观形貌图;图4b为反映测试样品发热膜的银浆电极未脱落的微观形貌图;图5为反映测试样品发热膜和对照样品发热膜长期工作状态下的稳定曲线对比图;图6a为反映测试样品发热膜银浆电极位置的示意图;图6b为反映测试样品发热膜的oca胶膜处撕开后银浆电极保留的示意图;图7a为反映对照样品发热膜银浆电极位置的示意图;图7b为反映对照样品发热膜的oca胶膜处撕开后银浆电极保留情况的示意图;图8a为反映测试样品发热膜银浆电极激光半刻蚀的示意图;图8b为反映测试样品发热膜银浆电极激光半刻蚀后oca胶膜处撕开后银浆电极保留情况的示意图;图9a和图9b分别反映为测试样品发热膜和对照样品发热膜的银浆电极弯折位置的示意图。具体实施方式下面结合附图,对本发明作详细的说明。为了使本发明的目的、技术方案及优点更加清楚明白,以下结合附图及实施例,对本发明进行进一步详细说明。应当理解,此处所描述的具体实施例仅仅用以解释本发明,并不用于限定本发明。实施例一参见图1,为本发明的一种基于石墨烯的高可靠性的发热膜的一实施例的结构示意图,具体地,本实施例的该发热膜包括自下而上依次层叠设置的:柔性的透明基底1、光学级的附着胶层2、石墨烯复合层和电极层6,其中,该石墨烯复合层包括石墨烯层3,位于石墨烯层3上的阻抗匹配层5。其中,该透明基底1可采用pet、pmma、pi等材料制成,基底厚度范围为1-500um,优选的基底厚度范围为20-150um。其中,该石墨烯层3具有连续的二维结构,即该石墨烯层具有较高的粗糙度。具体地,该石墨烯层3是采用cvd法在经过粗糙化的催化衬底上生长的,并通过液态胶黏剂将制备得到的石墨烯薄膜转移至透明基底1上,从而得到透明基底1、附着胶层2和石墨烯层3的三层结构。在一具体实施例中,可采用高温退火处理,物理机械打磨,化学选择性刻蚀等方法对该铜箔(即催化衬底)进行粗糙化处理,优选地,采用高温退火处理法对铜箔进行粗糙化处理,其退火温度为980℃-1050℃,真空度至20pa-60pa,持续退火1-10min,优选地,退火温度为1020℃,真空度(即气压)为40pa,持续退火5min。在一具体实施例中,该液态胶粘剂包括但不局限于热熔胶、热固化胶、光固化胶(即uv胶);优选地,采用uv胶,由于uv胶黏度较低,易于填充细小低洼区域,从而能够完全复刻该催化衬底上的粗糙纹路,并且由于其固化速度快,使得转移复型的效率高。进一步地,该uv胶含有增强层间附着力的偶联剂,可进一步提高胶层与基底和石墨烯层以及电极的附着力。其中,该阻抗匹配层5是由导电高分子材料固化成膜而形成的,且其与石墨烯层导通,优选地,导电高分子材料为聚噻吩、聚吡咯、聚苯胺及其衍生物,且该阻抗匹配层的干膜厚度为10-500nm,优选地,厚度为50-200nm。本实施例中,通过设置阻抗匹配层,一方面能够与石墨烯复合,提高表面导电性,均化表面方阻,降低石墨烯与电极的接触阻抗,同时提高耐候导电稳定性;另一方面提高表面极性,提高对其他层合材料,如银浆电极、表面封装层等的附着力。在一具体实施例中,采用pedot(聚3,4-乙撑二氧噻吩)/pss(聚对甲苯磺酸)的络合分散液,与石墨烯复合,明显提高导电性,同时,复合方阻相对于小分子掺杂石墨烯具有更长时间的稳定性。并且,导电高分子层作为复合导电层的表层,具有明显提高的表面极性,能够显著提高对表面印刷的电极线路的附着力。其中,该电极层6的电极包括依次贯穿上述阻抗匹配层5、封装粘结层4和石墨烯层3的接触部61,以及位于该接触部61顶部的搭接部62,且接触部61与附着胶层2相接触,从而使得该接触部61与石墨烯层3相导通,而该搭接部62与阻抗匹配层5相搭接,从而也使得该搭接部62与该阻抗匹配层5相导通。在一具体实施例中,根据预先设计的电极图案,使用刻蚀机激光刻蚀该石墨烯复合层,激光波长为355-1064nm(优选地,1064nm、532nm、355nm),功率为1-50w(优选地,5-20w),使得刻蚀线完全穿透由上述阻抗匹配层、石墨烯层组成的复合层,直至漏出下层的附着胶层,从而使得石墨烯复合层形成相互独立的功能区单元;然后对位印刷银浆线路,烘烤成型,得到横截面呈“t字形”银浆电极,形成若干独立而均匀连续的功能区域,其中,刻蚀图形宽度占比40%-80%,而激光刻蚀图形宽度与印刷浆料电极宽度占比10-90%。进一步地,本实施例的该红外发射膜还包括预切成型的缓冲胶层7及表面封装层8,该缓冲胶层7和表面封装层8先后依次对位贴合于电极层上,从而完成封装,并接引外部导电线路,得到红外发射膜。在一具体实施例中,缓冲胶层采用厚100μm的聚乙烯醇缩丁醛,表面封装层采用50μm厚的pet。更进一步地,为了增强石墨烯层和阻抗匹配层之间的作用力,从而提高发热膜的加工成品率和使用可靠性,还在该石墨烯复合层的石墨烯层和阻抗匹配层之间设置了一层封装粘结层。该封装粘结层4采用高分子成膜树脂,如热塑性树脂、热固性树脂、光固化树脂等,优选地,采用聚氨酯树脂,聚丙烯酸酯树脂,环氧树脂,或环丙树脂。本实施例中,该封装粘结层14的干膜厚度为100-2000nm,优选地,厚度为200-500nm,且该干膜厚度不能超过上述石墨烯层表面上高低起伏的二维结构的尖峰,即石墨烯表面二维结构的最大高度,从而保证阻抗匹配层能有效连接石墨烯层(即阻抗匹配层与石墨烯层表面上的二维结构的尖峰相接触)。当然,不同的透明基底,适用的高分子成膜树脂有所区别,要求其折射率与基底及表面封装层的折射率匹配,减少反射损失;如pet(聚对苯二甲酸己二醇酯)作为基底及表面封装层,优选的,高分子成膜树脂的折射率尽量接近1.57,优选的,主链与pet具有相似结构的脂环族聚氨酯丙烯酸酯树脂。当然,激光刻蚀时,刻蚀线完全穿透该阻抗匹配层、封装粘结层、石墨烯层,使得漏出下层的附着胶层。本实施例中,通过设置该封装粘结层,一方面能够在石墨烯层表面形成微观网状结构,实现对石墨烯的有效封装保护,同时由于其能够形成有空洞交联网络,从而保证了石墨烯层与阻抗匹配层的充分接触;另一方面其能够填充石墨烯表面的因连续二维结构引起的微观沟壑,降低雾度,同时作为一种减反膜,降低石墨烯透明薄膜的透过率损失;此外,还能够改善表面极性,提高对其他材料(如上层由导电高分子材料制成的阻抗匹配层)的层间附着力,例如阻抗匹配层(如pedot)与石墨烯的附着力差,设置一层高分子成膜树脂作为粘结层,能够明显提高上下两层的附着力,从而保证复合导电的可靠性。实施例二本发明还提供了一种基于石墨烯的高可靠性的发热膜的制备方法,具体地,本实施例的一种基于石墨烯的高可靠性发热膜的制备方法包括步骤:s1,将cvd法制备的石墨烯薄膜复型转移至透明基底上。本实施例中,该透明基底1可采用pet、pmma、pi等材料制成,基底厚度范围为1-500um,优选的基底厚度范围为20-150um。本实施例中,该石墨烯薄膜是在经过粗糙化的生长基底上制备得到的,并采用液态胶黏剂将制备得到的石墨烯薄膜复型转移到透明基底上,从而得到透明基底、附着胶层和石墨烯层的三层结构。本实施例中,可采用高温退火处理,物理机械打磨,化学选择性刻蚀等方法对该铜箔(即催化衬底)进行粗糙化处理,优选地,采用高温退火处理法对铜箔进行粗糙化处理,其退火温度为980℃-1050℃,真空度至20pa-60pa,持续退火1-10min,优选地,退火温度为1020℃,真空度(即气压)为40pa,持续退火5min。本实施例中,该液态胶粘剂包括但不局限于热熔胶、热固化胶、光固化胶(即uv胶)。由于液态胶黏剂能够充分填平石墨烯薄膜表面上由于高低起伏的连续二维结构所造成的低洼区域,消除了空气孔洞,降低薄膜整体折射率,从而提高透过率,并且当其固化后,能够完全复刻石墨烯及铜箔的微观形貌,保证了石墨烯透明薄膜具有较高的比表面积和表面粗糙度,从而提高了红外发射膜的发射率。在一具体实施例中,通过uv胶将石墨烯复型转移到50μm厚的透明基底pet上,然后去除催化衬底铜箔,得到具有高粗糙度石墨烯。由于uv胶黏度较低,易于填充细小低洼区域,从而能够完全复刻该催化衬底上的粗糙纹路,并且由于其固化速度快,使得转移复型的效率高。进一步地,该uv胶含有增强层间附着力的偶联剂,可进一步提高胶层与基底和石墨烯层以及电极的附着力。s2,在石墨烯薄膜表面涂布一层高分子成膜树脂,并固化成膜得到封装粘结层。本实施例中,该封装粘结层4采用高分子成膜树脂,如热塑性树脂、热固性树脂、光固化树脂等,优选地,采用聚氨酯树脂,聚丙烯酸酯树脂,环氧树脂,或环丙树脂,且干膜厚度为100-2000nm,优选地,干膜厚度为200-500nm,且该干膜厚度不能超过上述石墨烯层表面上高低起伏的二维结构的尖峰,从而保证后续涂布的阻抗匹配层能有效连接石墨烯层。在一具体实施例中,采用高分子成膜树脂pu-651涂布在石墨烯表面,其固含量为1.5wt%,湿膜涂布厚度为20μm,得到封装粘结层的干膜厚度约300nm。s3,在封装粘结层上涂布一层导电材料,并固化成膜得到阻抗匹配层。本实施例中,导电材料包括但不局限于有机、无极导电材料,如聚噻吩、聚吡咯、聚苯胺及其衍生物等,其干膜厚度为10-500nm,优选地,厚度为50-200nm。在一具有实施例中,该导电材料为导电高分子pedot(聚3,4-乙撑二氧噻吩)/pss(聚对甲苯磺酸)的络合分散液,其固含量为0.5wt%,湿膜涂布厚度为20μm,得到高分子导电层的干膜厚度约100nm,从而固化形成的阻抗匹配层均化复合导电层表面电阻。本实施例中,经过双层涂布的保护,即粘结层和阻抗匹配层,已经难以观察到石墨烯层。s4,按照预设的电极图案,在上述阻抗匹配层、封装粘结层和石墨烯层进行激光刻蚀,然后印刷电极浆料,得到电极层。本实施例中,采用激光机按照预设的电极图案在石墨烯复合层的对应位置进行激光刻蚀,该激光机的激光波长为355-1064nm,功率为1-50w。具体地,刻蚀线完全穿透由阻抗匹配层、封装粘结层、石墨烯层组成的复合层,直至漏出下层附着胶层,从而将石墨烯复合层分割成相互独立的功能区单元;然后对位印刷银浆线路,烘烤成型,得到呈“t”字形的银浆电极,从而形成若干独立而均匀连续的功能区域,其中,刻蚀图形宽度占比40%-80%,而激光刻蚀图形宽度与印刷浆料电极宽度占比10-90%。在一具体实施例中,采用激光波长为1064nm,功率50w的激光机进行刻蚀,且刻蚀图形宽度占比50%,而激光刻蚀图形宽度与印刷浆料电极宽度占比90%。本实施例中,该制备方法还包括封装的步骤,即具体地,将预切成型的缓冲胶层及表面封装层,与激光刻蚀后并布设电极层的石墨烯复合层分别对位贴合,完成封装,然后接引外部导电线路,从而得到能够在外接电场作用下,主动发射红外光的红外发射膜。在一具体实施例中,缓冲胶层采用厚100μm的聚乙烯醇缩丁醛,表面封装层采用50μm厚的pet。实施例三本实施例的基于石墨烯的高可靠性发热膜的制备方法包括步骤:在经过退火处理的铜箔上采用cvd法生成具有二维连续结构的石墨烯层,然后通过uv胶将制备的石墨烯薄膜复型转移至20um的透明基底pi上;在石墨烯薄膜表面涂布一层固含量为1.5wt%,厚度为16μm的高分子成膜树脂pu-651(湿膜),并固化形成厚度为200nm的封装粘结层,且该干膜厚度不能超过上述石墨烯层表面上高低起伏的二维结构的尖峰;在封装粘结层上涂布一层固含量为0.5wt%,(湿膜)厚度为10μm导电高分子pedot(聚3,4-乙撑二氧噻吩)/pss(聚对甲苯磺酸)的络合分散液,并固化成膜得到厚度为50nm的阻抗匹配层;采用激光机按照预设的电极图案,在上述阻抗匹配层、封装粘结层和石墨烯层进行激光刻蚀,其中,激光波长为355nm,功率为1w,刻蚀图形宽度占比40%;然后印刷电极浆料,得到电极层,且激光刻蚀图形宽度与印刷浆料电极宽度占比10%;最后,将预切成型的缓冲胶层及表面封装层,与激光刻蚀后并布设电极层的石墨烯复合层分别对位贴合,完成封装,然后接引外部导电线路,从而得到能够在外接电场作用下,主动发射红外光的红外发射膜。在一具体实施例中,缓冲胶层采用厚100μm的聚乙烯醇缩丁醛,表面封装层采用50μm厚的pet。实施例四本实施例的基于石墨烯的高可靠性发热膜的制备方法包括上述实施例三中的各个步骤,不同的是,本实施例中采用的是150um的透明基底pi;且在石墨烯薄膜表面涂布一层固含量为1.5wt%,厚度为40μm的高分子成膜树脂pu-651(湿膜),并固化形成厚度为500nm的封装粘结层,且该干膜厚度不能超过上述石墨烯层表面上高低起伏的二维结构的尖峰;在封装粘结层上涂布一层固含量为0.5wt%,(湿膜)厚度为40μm导电高分子pedot(聚3,4-乙撑二氧噻吩)/pss(聚对甲苯磺酸)的络合分散液,并固化成膜得到厚度为200nm的阻抗匹配层。实施例五为了说明本发明通过增设封装粘结层和阻抗匹配层能够增加发热膜的可靠性,本实施例分别提供了一种采用本发明的一种基于石墨烯的高可靠性发热膜的制备方法制备的发热膜作为测试样品,以及未设置粘结层和阻抗匹配层的发热膜作为对照样品,并分别对其进行导电性测试和弯折测试、阻抗测试等,从而得到相应的稳定性和可靠性结论,下面结合具体实施例进行详细的说明。关于测试样品发热膜,参见图2,采用本发明的一种基于石墨烯的高可靠性的发热膜的制备方法进行制备,其包括步骤:1、在催化衬底上生成具有二维连续结构的石墨烯层,得到结构ⅰ。2、通过uv胶将结构ⅰ中的石墨烯转移复型转移到50um厚的透明基底pet上,并去除催化衬底,得到具有pet基底、附着胶层和高粗糙度石墨烯层的结构ⅱ。3、在结构ⅱ中的石墨烯层表面涂布一层高分子成膜树脂pu-651,并固化成膜作为封装粘结层,得到结构ⅲ。其中,高分子成膜树脂的固含量为1.5wt%,湿膜涂布厚度为20μm,得到封装粘结层的干膜厚度约300nm,且干膜厚度未超过高低起伏的石墨烯层的尖峰,以保证涂布的阻抗匹配层能有效连接石墨烯层。4、在结构ⅲ中的封装粘结层表面继续涂布一层导电高分子pedot(聚3,4-乙撑二氧噻吩)/pss(聚对甲苯磺酸)的络合分散液,并固化成膜形成与石墨烯层连续导通的阻抗匹配层,得到结构ⅳ。其中,高分子导电子涂布液的固含量为0.5wt%,湿膜涂布厚度为20μm,得到高分子导电层的干膜厚度约100nm;形成的阻抗匹配层均化复合导电层表面电阻,且经过双层涂布保护,微观形貌已难以观察到cvd石墨烯层。5、使用1064nm波长的红外刻蚀机按照预设的电极图案在上述结构iv上对应位置激光刻蚀石墨烯复合层,并对位印刷银浆线路,烘烤成型,得到银浆电极层,得到结构ⅴ。其中,激光刻蚀时,刻蚀线完全穿透由阻抗匹配层、封装粘结层、石墨烯层组成的石墨烯复合层,直至漏出下面的附着胶层,且刻蚀图形宽度占比50%。6、将预切成型的缓冲胶层及表面封装层,与结构ⅴ分别对位贴合,完成封装,并接引外部导电线路,得到结构ⅵ,即基于石墨烯的发热膜。关于对照样品发热膜,其也采用本发明的制备方法进行制备,不同的是,没有设置粘结层和阻抗匹配层发热膜,而是直接在石墨烯层上进行激光刻蚀,布设电极层后封装,其包括步骤:1、在催化衬底上生成具有二维连续结构的石墨烯层,得到结构ⅰ;2、通过uv胶将步骤1中制备得到的石墨烯复型转移到50μm厚的透明基底pet上,得到具有高粗糙度石墨烯透明薄膜,并去除催化衬底,得到结构ⅱ;3、根据预设的电极图案,激光刻蚀石墨烯层,刻蚀至下层的uv胶层,形成相互独立的功能区单元;并对位印刷银浆线路,烘烤成型,得到银浆电极,形成若干独立而均匀连续的功能区域,得到结构ⅲ;4、将预切成型的缓冲胶层(厚100μm的聚乙烯醇缩丁醛)及表面封装层pet(50μm厚),分别与结构ⅲ对位贴合,完成封装,并接引外部导电线路,从而得到在外接电场作用下,能够主动发射红外光的透明石墨烯薄膜产品,得到结构ⅳ。本实施例中,在上述步骤3和步骤4中,由于没有封装粘结层和阻抗匹配层的保护,石墨烯层非常容易受损,宏观及微观均有明显损伤,从而造成功能缺失,影响产品的成品率。导电性测试对照样品发热膜:由于石墨烯层存在损伤,线阻远远大于加工前理论推算的线阻,且通电后,在红外成像仪中能明显看到石墨烯损伤区域呈现暗区,如图3a所示。测试样品发热膜:电学性能正常,即各电极均连续导通,无缺损,加工前方阻与加工后线阻推算匹配,表明加工过程中无损伤;通电后,在红外成像仪中,红外发射区域与设计情况一致,如图3b所示。弯折测试对照样品发热膜:在薄膜弯折机上,以10mm的弯曲半径,连续弯曲1000次,银浆电极出现部分脱落现象,如图4a所示,出现了接触不良的现象,从而影响发热膜的稳定性。测试样品发热膜:在薄膜弯折机上,以10mm的弯曲半径,连续弯曲50000次,银浆电极接触良好,无脱落,如图4b所示。接触阻抗测定:相同宽度,相同长度,相同厚底的银浆电极层,测试相同长度下的电极层线阻,其线阻差异如表1所示:表1对照样品和测试样品发热膜的电极线阻对比电极长度(cm)246810152025对照样品(ω)0.20.30.30.40.50.80.91.0测试样品(ω)0.00.00.00.10.20.30.60.7由表1中数据可知,测试样品发热膜的接触阻抗明显小于对照样品发热膜的接触阻抗。长期稳定性对比实验:将对照样品发热膜与测试样品发热膜,在相同实验环境,相同外加电场(输入电压相同)的条件下,测试两种样品的红外光发射情况,且都每天连续工作8h;然后测试两种样品接线端两极线阻变化情况,长期跟踪记录二者的线阻变化曲线如图5所示:在长期使用过程中,石墨烯红外发射区域无损伤;但对照样品发热膜的红外发射膜的线阻(即薄膜方阻)逐渐上升,在输入电压不变的情况下,输入功率逐渐下降,电光转换,红外辐照强度逐渐减弱;而测试样品发热膜的线阻则几乎保持不变。由此可知,本发明的一种基于石墨烯的高可靠性发热膜的制备方法所制备的发热膜的功能稳定性明显优于对照样品发热膜,即本发明的一种基于石墨烯的高可靠性发热膜的制备方法明显提高了石墨烯红外发热膜的可靠性。实施例六为了说明本发明通过增设封装粘结层和阻抗匹配层,并结合激光刻蚀的工艺布设电极层得到的发热膜的稳定性高,且具有长期稳定性,本实施例将本发明的制备方法制备得到的测试样品与传统的发热膜,即未设置粘结层和阻抗匹配层,也未采用激光刻蚀工艺布设电极层的发热膜,作为对照样品,分别进行测试:测试1观察测试样品发热膜的银浆电极位置实物,如图6a所示,并将测试样品发热膜从oca胶膜处撕开,观察银浆电极保留情况,如图6b所示。观测传统发热膜的银浆电极位置实物,如图7a所示,并观测从oca胶膜处撕开后银浆电极位置实物,如图7b;可以看出未经过激光刻蚀工艺加工的传统发热膜,撕开后银浆电极完全脱落,而测试样品发热膜中的激光刻蚀位置银浆保留完好。测试2本测试中的测试样品发热膜与上述实施例三中的测试样品的制备方法相同,不同的是,激光刻蚀时,使用355nm波长的紫外刻蚀机按照发热膜电极图形将对应位置的单层石墨烯进行半刻蚀,刻蚀图形宽度占比50%。印刷完成后印记那个电极位置实物,如图8a所示,从oca胶膜处撕开后银浆电极位置实物,如图8b所示。测试3将上述实施例三中的测试样品发热膜进行对折,观察银浆电极弯折后效果,如图9a,与传统发热膜对折后,如图9b,进行对比,可明显观察到未进行激光刻蚀加工的空白样品在对折后银浆电极发生脱落,而测试样品发热膜对折后未见银浆电极脱落。以上所述仅为本发明的较佳实施例而已,并不用以限制本发明,凡在本发明的精神和原则之内所作的任何修改、等同替换和改进等,均应包含在本发明的保护范围之内。当前第1页12