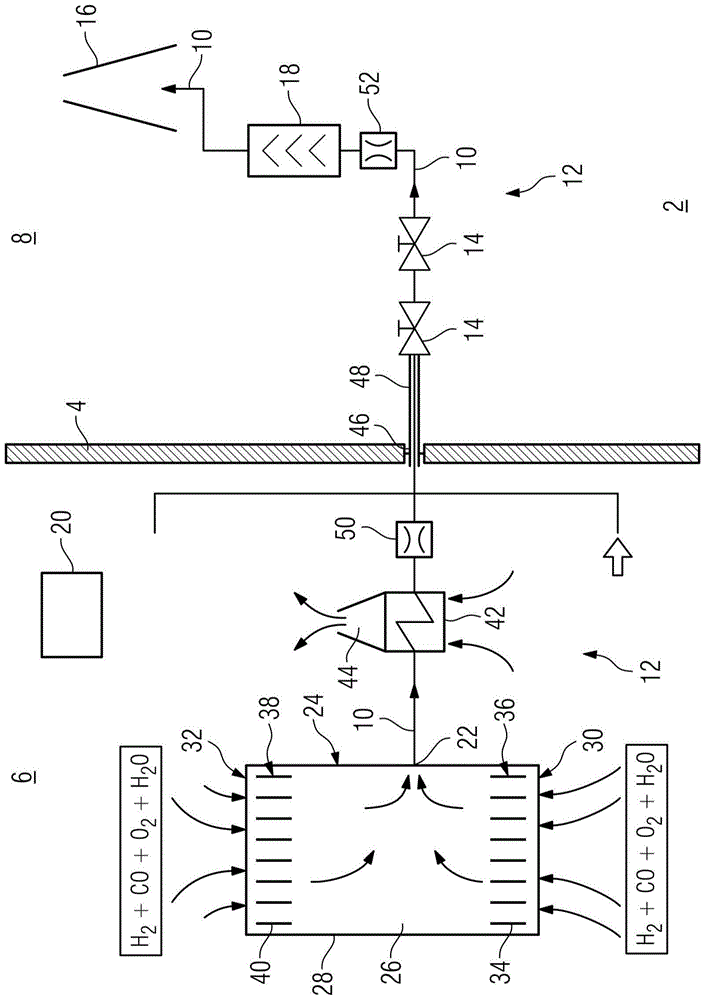
本发明涉及一种包括安全壳和至少一个从该安全壳延伸出并能够用截止阀关闭的卸压管线的核技术设备,卸压流能够在卸压操作中在截止阀打开时流过该卸压管线。
背景技术:在核电厂中发生故障和事故的情况下,比较大量的氢气和一氧化碳以及水蒸汽可能被释放到也被称为反应堆外壳、紧闭罩或安全壳的安全容器中,该安全容器将内部环境与外界环境以气密的方式屏蔽开。如果不采取应对措施,则也许会出现可燃气体聚集在安全容器环境中,以致可能形成易爆的混合物。另外尤其在从冷却循环过程释放出蒸汽的情况下,可能出现超过安全封入物的设计压力的过压。在大量核电厂中已安装了不同的系统以用于在发生事故的情况下分解氢气以及用于过压限制和反应堆外壳的卸压。这样的系统通常被相互独立地立项、设计和运行控制。与此相关地,例如根据结构形式也被称作催化复合装置的催化部件属于现有技术,其将气流中所含的氢气(H2)与氧气(O2)在催化支持的放热反应中无焰地复合成水(水蒸汽)(H2O)。相应的情况适用于一氧化碳(CO)和氧气(O2)复合成二氧化碳(CO2)。为了有效的H2/CO分解和为了避免出现不允许的局部临界浓度,通常在整个反应堆外壳中分散布置多个复合装置。另外,公开了所谓的排放系统,借此通过将反应堆外壳大气过滤排泄至环境中而使得过压状态变为可控。此时优选被动系统,其通过存在于反应堆外壳内的过压本身被驱动。但也存在以下变型,其中来自反应堆外壳的卸压流通过电动输送风扇等来激活或辅助。各个不同变型的共同点在于延伸通过安全壳的卸压管线,该卸压管线在核技术设备正常运行时由至少一个截止阀关闭。为了所期望的卸压,打开各个截止阀,使处于过压的气体-水蒸汽混合物能够从反应堆外壳内经卸压管线向外流,在此它通常在经过多级过滤、清洗和干燥以阻截带有放射性的液体、颗粒和悬浮微粒之后被排放至环境中。在某些场合中可能出现显著的H2和/或CO产量与相关压力形成进行组合的情况,从而需要反应堆外壳提前卸压。由于提前卸压,所以能够想到用于在反应堆外壳内的H2/CO分解的措施尚未发挥其作用。因而在最不利情况下假定在也被称为排气流或泄流的卸压流内在蒸汽-空气环境中存在可点燃的H2/CO浓度。如果现在该排气被引导经过未被加热的管路和过滤装置,则因为随后的蒸汽冷凝而出现可燃气体浓度的进一步提高,例如加倍。结果,形成易燃且甚至易爆的混合物,该混合物在点燃时产生明显的火焰加速,这威胁到排放和截止装置的完整性,进而在流入时可能导致不希望的严重的环境负担和污染。因此,所述排放系统例如被永久加热以免起动凝结,但或者只针对在反应堆外壳内已完成H2分解后投入使用来设计。与此相应,反应堆外壳内的复合装置系统根据功率来设计,以便利用多个复合装置实现提前的H2分解,进而在卸压开始之前可以在可想到的众多事故场景中获得尽量无氢气的环境。另外,这些复合装置迄今主要设置在主对流路径中。通常设有例如20至100台或更多的大量复合装置,这导致每小时的整体的复合装置-流通量(在此称为换气量)例如为0.3至0.6或更高的反应堆外壳大气的总体积。例如,因此在50000m3至70000m3反应堆外壳体积情况下需要15000至40000m3/h或更高的复合装置-流通量。尽管如此,在上述危急场合中不能在所有情况下保证及时在启动排气之前进行H2分解。
技术实现要素:因此,本发明基于以下任务,提出一种上述类型的核技术设备,该核技术设备是针对危急场合的可靠控制而设计的,此时在释放氢气和/或一氧化碳的同时,在安全壳内出现显著压力升高。此外,尤其应该抑制爆炸性气体混合物的出现或聚集,其可能导致在从安全壳引出的卸压管线和与之相接的设备和辅助系统中发生快速爆燃或甚至起爆。根据本发明,该任务将通过权利要求1的特征来完成。据此规定,各卸压管线在入口侧前设有位于安全壳内的气流处理装置,该气流处理装置具有被侧周面包围的带有下进流孔和上进流排流口的烟囱状流道,其中在下进流孔的上方或区域内设有用于在流道内分解氢气和/或一氧化碳的第一组催化部件或者说复合装置,并且该卸压管线具有进流口,其在第一组催化部件上方且在上进流排流口下方设置在该周面上,从而在卸压操作之前的对流运行中在截止阀关闭状态下在安全壳内有氢气和/或一氧化碳释放的故障时,存在于该安全壳内的气体混合物按照自然对流原理从下向上流过该流道,并且在卸压操作中,所述气体混合物按照强制泄流原理从下方且优选也从上方流入该流道并作为卸压流经该卸压管线流走。术语“气流”和“气体混合物”在此也包含如下情况,即,其中包含了值得一提的蒸汽成分或液体成分,即简言之,包含了气体-蒸汽混合物的或流体的通常情况。该对流也适用于以下说明。术语“截止阀”代表任何类型的关闭阀门。本发明源于以下考虑,已经开始尽可能持续阻止爆炸性气体混合物出现或聚集在卸压管线和与之相接的设备中。为了同时能尽量放弃抑制在该系统组件中的冷凝物形成的、易出故障且设备复杂的加热,应该在该卸压管线的汇入区域中已经有在卸压流(排气流)中的相应低的H2和CO浓度,确切的说,尽量已经在卸压操作开始时。这出人意料地实现了,即,被设计用于催化分解氢气和/或一氧化碳的复合装置且尤其是所谓的被动自动催化复合装置(PAR)按照上述方式直接安放在卸压管线的也被称为抽排接头的进流口之前。此时,通过设于卸压管线的进流口前方的流道的布置和构型,以尤其合适的方式支持两个不同的运行模式和在这两个模式之间的过渡:在紧接于卸压操作之前的运行阶段中,即在该卸压管线仍关闭时,在烟囱抽吸和在下烟囱端因放热复合反应而升高的催化器温度的驱动下,随着升高的H2/CO浓度而在流道内出现从下向上的自然对流流动。由此,这些复合装置在一定程度上被预热到其在随后的卸压操作中所期望的操作温度。另外,通过对流来支持在安放区域内的环境的循环,进而也支持局部H2分解。卸压操作通过打开卸压管线中的截止阀来启动。由于在反应堆外壳内室和外界环境之间的现有压力降低,存在于反应堆外壳内的气体混合物通常以前置溢流形式从烟囱两端(即从上和从下)流入该流道并从那里进入该卸压管线。此时,烟囱的侧外罩构成在反应堆外壳内的具有更高H2/CO浓度的从上方倾斜地或水平地流入的“降流”的阻挡,其因而被阻止直接进入泄压管线的进流口。在设计的特殊情况下,能够这样平衡在卸压操作中的流动状况,即,虽然烟囱状流道上流入口是敞通的,但是由于在上侧区域中出现背压,故基本上只从下方经由下进流孔流入至泄压管线。但通常该部分在卸压操作中从两端流入卸压管线。总体而言,通过所述措施以被动自动方式,即没有输入外界能量或辅助电能且没有复杂的控制措施,在气体从安全容器突然抽排和释放时以及也在瞬间起动阶段中可靠避免在卸压管线和与之相连的截止和清洁装置中的爆炸性气体的临界浓度。由抽排所引起的在烟囱状流道中的从对流运行至强制泄流的瞬间流动变化现在不再影响到催化效率,因为该烟囱内的催化器通过在预运行阶段中所预期的负载运行已处于最佳的运行温度。在本发明构想的第一个有利变型中,在卸压管线的进流口上方且在流道的上进流排流口的下方或区域内,设有用于分解流道内的氢气和/或一氧化碳的第二组催化部件。换句话说,催化部件的另一区域布置在反应堆外壳大气-抽排接头的上方,靠近烟囱上部出口。由此一来,在强制泄流的卸压操作中获得了从两侧,即从上和从下流入烟道的气体在进入卸压管线之前接受利用各自对应的催化复合装置的处理,由此保证可点燃的组成成分非常有效地减少。另外,这种布置形式在上述对流运行中造成对流增强和在气流处理装置中的特别有效的H2/CO分解(较少漏脱)。在第二有利变型中,在卸压管线内有流通限制机构,这些流通限制机构就催化复合装置的复合效率而言被如此调节,即在卸压操作中,在卸压管线的进流口区域内的氢气和/或一氧化碳的浓度小于在流道的下进流孔区域内的相应浓度的50%,优选小于在流道的下进流孔区域内的相应浓度的30%。或者,在流道的上进流排流口处的浓度也被用作参考量,但近似基于以下前提条件,在该流道的延伸高度有利地为大约1至2米时,两个浓度大多是一样大小的并且就此而言没有显著差异。可以将所述第二变型与第一变型组合起来,但正好也适用于以下情况,即,在流道的上端不存在附加的复合装置,以便在卸压操作中阻止富含H2/CO的周围环境经该流道的上进流排流口过分回吸/回流到卸压管线的进流口中。现在排气的H2/CO基本减少到低于入口浓度的50%且优选低于30%本身在安放在安全容器外的冷过滤装置/清洗装置起动时避免了在蒸汽冷凝时会出现临界的H2/CO浓度,其会威胁到该过滤装置/清洗装置的系统完整性。这对于在起动时以及连续运行中的爆炸避免而言是相当重要的。与前述设计原理一致地,有利地如此调节所述流通限制机构且如此选择流道形状,即,在卸压操作中在该卸压管线内的物质流最多是在该流道内的处于对流运行的物质流的100%,优选小于在该流道内的处于对流运行的物质流的80%。这些措施也用于避免将富含H2/CO的环境吸回到卸压管线中,否则可能因为催化器的超出最大可能复合效率的进流而出现回吸。在其它有利实施方式中,由于已知的缘故,如此调节所述流通限制机构且如此选择流道形状,即,在卸压操作中在所述催化部件或复合装置处的进流速度小于5m/s,优选小于3m/s。为了限制流通,尤其是可以在该卸压管线中设置至少一个节流阀。该节流阀也可被直接设置在卸压管线的进流口中或间接设置在卸压管线的进流口之前。作为替代或补充,被接入该卸压管线的组成部件比如过滤装置、清洗装置、截止阀或一些管线段能有助于或提供期望的节流作用。在前置的流道(烟囱)中的流动可以通过其形状参数如高度、横截面积、进流排流孔的尺寸和布置以及通过导流的或者影响流动的组装体等就所述设计目的被影响。尤其是以下催化部件属于其形状和布置影响流道内的对流和强制流动的所述组装体,其通常由多个板状件构成。所述催化部件优选通向大气,主要竖向取向,基本平行布置在不同的高度(阶梯状),以便在所述构件和构件区域之间产生浮升。另外,优选大于5mm的在溢流构件之间的距离,此时出现大于10倍距离的高度和大于50%的孔径比。在此,孔径比表示所述构件之间的可自由流通的横截面积与流道内的由所述构件整个覆盖的横截面积之比。在一个可能的变型中,所述催化部件能直接安置在该流道的进流/排流口之内/之处。该烟囱状流道也可以在类似管路构成的情况下利用分散于周面的通向大气的催化区来实现。此时,可以设有多个就流动而言并行的管线分路。该卸压管线的也被称为环境抽排接头的进流口优选根据催化复合装置在流道内的布置形式而不同安置就位。因此,当只有一个低设的催化区或区段时,该抽排接头优选安置在流道的下部分内,但在低位的催化区段的上方,以便因较长的上流动路径而使得富含H2/CO的气体混合物经流道的上进流口/上排流口流入卸压管线变得困难。在具有两个催化区段即低位的催化区段和高位的催化区段的装置中,该抽排接头优选安置在流道的中央或下部中。通常,在工作中力求获得且也达到因放热反应而永久增高的优选超过100℃至900℃的催化器温度。在有利的实施方式中,这些催化复合装置关于其在卸压操作中的工作温度而被如此设计,即该催化复合装置在进流的气体混合物的氢气浓度超过7体积%时作为点火器。就是说,当存在例如7至10体积%H2含量的可点燃浓度时,通过优选超过700℃的催化部件表面温度而进行进流气体混合物的预防性点燃。预防性点燃的优点在于,点燃和随后的燃烧相对地控制并缓和地按照爆燃方式逐渐结束,与起爆相比产生微弱的火焰促进和体积位移。即,通过在流入真正的抽排系统前在催化部件处点燃,在反应堆外壳内的可燃气体浓度高的运行阶段中也获得在排气系统中的有效浓度限制,从而现在在所有运行状况下在排气系统内非常可靠地保证了安全性。各气流处理装置和对应的排气抽排接头关于安全壳的总高度被有利地设置在下三分之一中且优选被设置在下四分之一中,因此在安全壳内的主对流路径下方。特别有利的是,设有多个例如至少五个关于安全壳的总高度而设置在下三分之一或下四分之一中的用于卸压流的气流处理装置以及设于其上且未直接作用于卸压流的多个附加的催化复合装置以用于分解氢气和/或一氧化碳,在这里,直接与排气系统合作的气流处理装置共同提供了可供使用的总复合效率的不到20%。所述附加的催化复合装置又优选如此分布,即,在安全壳的上半部内提供了可供使用的总复合效率的至少70%。通过在反应堆外壳内且尤其是在远离主对流路径的安放空间内安放和分布气流处理装置,有利地通过充分利用所出现的在反应堆外壳高度范围内的氢气分层,实现了将排气流中的氢气浓度附加地系统性限制到低于直至安全容器内的平均浓度的四分之一直至最大二分之一。气流处理装置的安放优选在反应堆外壳的远离主对流路径的空间部段内进行。尤其是在反应堆外壳的最下面的三分之一中的安放空间被证明是适当的,其具有局部封闭的盖和/或底部(尤其是无光栅)和壁并且理想地呈袋状空间形式构成。通过这样选择安放地点,理想地充分利用了在上反应堆外壳部内(如反应堆外壳高度的上三分之二内)的氢气的预期分层,从而允许将排气流中的氢气浓度附加系统性限制到低于最大直至安全容器内的平均浓度的四分之一直至最大二分之一。另外,利用散布于反应堆外壳上的、在此优选按高度密布在中间三分之一中(例如大于总数的50%)且也设置在反应堆外壳的上三分之一中的其它催化复合装置,进行H2/CO分解。通过安放在主对流路径中和具有较高浓度区域(分层)中,每个复合装置的H2分解效率再次得到提高。通过与排放抽排功能相结合的这种新型布置,现在也可以出人意料地将具有迄今15000至40000m3/h或更高的复合装置流通率和迄今大于0.3至0.6小时或更大的换气率L的待建立的总复合率减小到当前被视为必需的量的2/3至1/2,对应于现在在反应堆外壳内可获得的小于0.3至0.1小时或更小的换气率L。做到这一点是因为,现在在高浓度区域内加强且大多在蒸汽强化环境中很有效地进行H2分解。同时,在低位区域中且在排气情况下通过新型装置及其布置就浓度而言保证了不再需要在排放运行前的浓度降低以尤其实现可靠的排放。在进一步有利的实施方式中,至少一个位于安全壳内的用于卸压流的冷却装置被接入该卸压管线。此外,也可以将排气流分支为多个并行分流,至少其中一部分的所述分流被冷却。通过排气抽排装置与后置的还是被动驱动的冷却装置的组合,被催化反应器加热的排气的温度从例如400℃至500℃被降低到约150℃至300℃。由此,现在也可以在反应堆外壳贯通区域和后随装置中避免超出设计的不允许的温度负荷。该冷却装置优选在安全容器内主要在流向上直接安放在反应堆外壳穿通区域或内部过滤器区域中之前。冷却装置优选借助周围的反应堆外壳大气来对流冷却,或通过液体蒸发。换句话说,冷却装置优选被设计用于通过位于安全壳内的气体混合物的对流循环冷却和/或雾化冷却/蒸发冷却。当将冷却件布置在池槽区或实心混凝土结构区域中时,通过与所述物质(冷却介质或混凝土等)的直接接触或间接接触来加强散热,因而在冷却效率保持不变情况下实现了装置小型化。由于用自反应堆外壳流出的冷凝物被动润湿冷却面,故获得了清洁和冷却装置效能的同时提高。通过以斥污光滑表面形式构成该冷却面、将冷却面形成有耐辐射涂层或呈光滑的不锈钢表面,或许被附加处理(如抛光、电解抛光等),也在严重故障情况下实现长期有效的热传递。另外,运行安全性可通过布置后碎屑护壁而得以显著提升。在反应堆外壳穿通区域中,该卸压管线优选配设有呈热防护罩形式的热绝缘,从而在此也可能出现超过如150℃至200℃或更高的贯穿设计温度的排气温度。这导致冷却装置的尺寸显著减小。各冷却装置优选包括确切说朝向反应堆外壳敞开的辐射换热器部和对流换热器部。从卸压流至周围冷却介质的热传递例如可以通过以下方式来实现:-带有敞开的循环空气冷却通道的板式冷却件,-管式冷却件,或是带有翅片管,-半敞开式冷却件,其形状能特别有利地适应于混凝土结构,和/或-其它换热器结构。原则上,此时优选尽量敞开的无压力的扁平盒结构以尽量减小结构成本。在此情况下,也可以通过多个预制模块的组装来实现模块化结构。这样的构型是特别有利的,在这里,包含催化复合装置的烟囱状流道构成第一模块,而冷却装置构成第二模块,这两个模块优选并排紧邻(尤其是壁靠壁)安放。另外,在冷却装置内的流动路径可以有利地在卸压操作之前的备用状态下仍用破裂膜来封闭,破裂膜在卸压管线中的截止阀打开之后因随即产生的压差而(被动)开启卸压能力。复合装置的催化部件优选在使用催化活性贵金属钯(Pd)和/或铂(Pt)和/或钒(V)的情况下被装在陶瓷载体或带有陶瓷涂层(涂层)的金属载体上。可以采用单金属碱性材料或该贵金属的或许掺杂有尤其金属如铜(Cu)或镍(Ni)的混合物。为了能在最困难的故障情况下可靠运行,与包含载体件在内的总催化器相关,规定了大于陶瓷载体的0.2重量%、优选大于陶瓷载体的0.5重量%的贵金属含量。这些催化部件此时例如可以-设置在金属载体或陶瓷载体上,-作为敞开载体内的散料设置,和/或-作为格栅或蜂窝设置,比如也呈夹层构型。此时优选出现敞孔形结构,其孔径比大于50%,优选大于90%,因而能可靠地避免悬浮微粒堵塞。通过这种组合,由应用在反应堆外壳大气中引起的老化效应例如可以通过吸收碳氢化合物和焊接蒸汽、悬浮微粒加料等来补偿,而没有否则在短暂等候时间之后出现的对安全至关重要的针对多年(超过5年,优选超过10年)的工作室的自起动器功能损失,因此显著提高安全性并同时降低成本,这是因为可以避免在维护和检查工作范围内的定期更换。最后,在适当的实施方式中,在位于安全壳外的卸压管线段中设置过滤器和/或清洗器用于清洁卸压流和放射性阻截。尤其是此时可以采用已知的文丘里管清洗器型的湿型清洗器,其在适当调节的进流速度下允许特别高效的悬浮微粒截留,尤其是就含碘成分而言。借助本发明获得的优点尤其在于,通过就紧密吻合的空间和根据流动的关联性意义上将催化部件或复合装置与排气流抽排装置巧妙组合,尤其在适当设定流速和流量的情况下,尽管有相关的H2/CO浓度,仍实现了反应堆外壳的提前卸压(排放),没有威胁到后置的过滤和清洗装置,而且也能减小要装在反应堆外壳中的复合装置功率。整个卸压系统(除截止阀外)完全被动工作,没有供应辅助电能且基本没有活动部分。因此,可以获得在严重故障情况下的核技术设备的安全性的显著提高。附图说明以下将结合附图来详述本发明的各不同实施方式。在此,在极其简化的各示意图中示出:图1是包括安全壳和处于第一工作状态的用于安全壳的卸压系统的核技术设备的局部示图,图2是用于图1的卸压系统的第二工作状态的局部示图,图3是作为根据图1和图2的卸压系统的组成部分的配备有催化复合装置的处理装置和用于卸压流的后置的冷却装置的局剖透视图。具体实施方式在所有的图中,相同的或作用相同的零部件具有相同的附图标记。图1局部示出的核技术设备2是核电站,例如压水反应堆型或沸水反应堆型。核技术设备2具有也称为反应堆外壳的安全壳4,其在此呈仅局部可见的钢罩形式。安全壳4将内室6中的核系统组成部件和非核系统组成部件与外室8中的环境气密隔绝。为了能降低在发生事故时因蒸汽和气体释放而出现在内室6中的过压,而引导卸压管线10穿过安全壳4。卸压管线10构成卸压系统12的组成部分。在核技术设备2的正常运行中,卸压管线10由两个设置在安全壳4外的串联的截止阀14关闭。为了启动卸压,打开两个截止阀14,从而使得卸压流可以因从安全壳4内的卸压管线10的入口端至安全壳4外的且在此在烟囱16内的出口端的压力降低而流动。由此造成在安全壳4的内室中的所期望的压力降低。为了在卸压操作时将带有放射性裂变产物的环境负载保持在允许极限范围内,借助相应的过滤和/或清洁装置18对卸压流进行过滤和清洁,该过滤和/或清洁装置在安全壳4之外在截止阀14的下游被接入卸压管线10中。例如可以设置文丘里管型清洗器的湿型清洗器,其造成卸压流所携带的比如呈颗粒和悬浮微粒形式的放射性载体的高效回收。另外,也可以设有干燥过滤器和催化清洁装置或者类似装置。卸压系统12被设计用于消除危险事故,在危险事故中,在压力急剧升高的同时出现值得关注的在内室中的氢气H2和/或一氧化碳CO释放的情况,结果,如果没有采取应对措施,则可能产生局部或甚至整个能点燃的/可起爆的气体混合物。为了避免出现这种情况,按照本身已知的方式,多个催化复合器20分散布置在安全壳4的内室6中,它们在周围环境流入时将其中所含的氢气H2与氧气O2无焰复合成水(蒸汽)H2O,和/或相应地将一氧化碳CO与氧气O2复合成在安全壳4内起惰性化作用的二氧化碳CO2。但在危急故障情况或者事故情况(包含核熔场合)下,在复合装置20达到其预定操作温度之前,这通常持续短暂时间,并且在能通过计划的复合效率获得显著的H2浓度降低之前持续相当长的时间。因此可能出现以下问题,在安全壳4内的压力急剧升高的同时,在故障进程的较早时间段内需要也被称为排气的卸压,在上述较早的时间段内,分散于建筑物中的多个催化复合装置20尚未发挥其全部功效。因此,在这样的场合下可能出现可点燃的气体-蒸汽混合物流入卸压管线10中。由于在外室8内在一开始比较冷的管线段中有至少部分包含冷凝物的蒸汽,故对安全至关重要的组成部分(即氢气H2和一氧化碳CO)的浓度在运输路途的进一步进程中甚至还将升高。由此,在不利情况下可能超出起爆极限,给过滤和/或清洁装置18的完整无损性带来不利后果。如果人们想要在这样的情况下可靠地排除其损害,则需要相应耗费密集的、复杂且结实的、得到安全保障的结构。为了避免这种情况,在根据图1的卸压系统12中,卸压管线10的也被称为抽排接头的进流口22被很好地保护,以避免出现流入气流中的氢气H2和/或一氧化碳CO的临界浓度值。为此目的,就流动而言,在进流口22前设有气流处理装置24,其适当处理流入的气体混合物的组成。为此,气流处理装置24包括呈烟囱状的、基本竖直取向的流道26,该流道在侧面由例如通过壁件或其它系统组成部件构成的周面28界定并且基本上不允许进流气体透过。在下端,流道26具有(在此例如设于端侧的)进流孔30,并且在上端设有相应的进流排流口32。卸压管线10的进流口22就流道26的整个高度而言大致居中设置在周面28内。代替近似点状的进流口22,也可以设有围绕周面28的周边或从至少其一部分延伸出的环缝形状或类似结构作为卸压管线10的入口。还与其自身高度延伸尺寸相关地,进流口22可以不同于图1的视图地延伸构成,只要保证流入的气流已经事先经过了催化有效区域(见下)。大致在卸压管线10的进流孔30之上且在进流口22之下,用于使氢气H2和氧气O2复合生成水(蒸汽)H2O和/或使一氧化碳CO和氧气O2复合生成二氧化碳CO2的多个催化部件或者复合装置34分散设置在流道26的横截面内和/或在边缘分散设置于周面28的内周边上。例如呈板状的且相互平行地竖直取向的部件共同在流道26的下端构成第一(下)催化区36。这一类型的第二(上)催化区38位于流道26的上端,紧接设置在卸压管线10的进流排流口32下方和进流口22上方,并且包括催化复合装置40。在一个在此未示出的替代变型中只设有下催化区36。因此,卸压管线10的进流口22优选在流道26的下侧区域内更低地就位,但仍旧在催化复合装置34上方。在进流口22的下游,在流道26之外且还在安全壳4内,用于在卸压操作中出现的卸压流的冷却装置42被接入卸压管线10。冷却装置42被设计用于借助安全壳4内现有的环境的主要是对流的循环冷却,并且在必要时得到蒸发冷却和/或对环境的辐射散热的支持。为此,冷却装置42优选也构成烟囱状的、与气流处理装置24的流道26相反地但部分畅通至环境的流道44,延伸经过卸压管线10的所述至少一个管线段以散热至流过的环境。不同于图1的示意图,在冷却装置42内或者已经进一步在上游,能够实现将卸压管线10分支为多个分管线或者说分流,但其在贯穿安全壳4的穿通管路46之前又适当地汇合。为了实现蒸发冷却,可以设有在此未示出的液体喷洒装置,比如带有根据流动接合至冷凝物集槽的连管或类似机构。在直到第一截止阀14的穿通管路46区域内,本实施方式中的卸压管线10配设有呈外罩形式构成的热防护罩48。另外,在卸压管线10内形成一个或多个固定设定的或者可选能够调节或能够控制的用于限制排流流通(限量)的构件。在这里,在本实施方式中它们尤其是在冷却装置42和安全壳4的穿通管路46之间的管线段内的第一节流阀50和在第二截止阀14和设于其下游的过滤和/或清洁装置18之间的管线段内的第二节流阀52。但原则上这样的流通限制也可以在卸压管线10的其它部位形成,比如通过相应设计本来就有的导流组成部件或通过各组成部件的合作来实现。卸压系统12的运行方式如下:在核技术设备2的正常运行中,卸压管线10中的这两个截止阀14是关闭的,因而卸压流没有逸失,最多可能有总体少量气体流入卸压管线10的管头部,直到背压阻止进一步流入。抛开因在安全壳4内的温度分布而出现的自然对流不谈,还没有发生值得注意的气流处理装置24的流通。当在安全壳4内发生释放氢气H2和/或一氧化碳CO的故障时,这将发生变化。通过第一(下)和必要时通过第二(上)区域的接管其工作的催化部件或者说复合装置34、40和由此造成的局部温度升高,在流道26中的烟囱抽吸效果得到支持并且在那里潜在存在的自然对流得以加强。就是说,变热的气流从下向上流过流道26,在此同时发生所述复合反应,并且催化复合装置34、40在最短时间内处于其最佳运行温度。图1示出该装置,在这里,由相应的流动箭头表示流动状况。如果内室6中的显著过压现在同时降低,则过压降低可以仅在短暂的自然对流阶段之后随着复合装置34、40例如预热小于20分钟通过打开卸压管线10内的截止阀14被启动。图2示出卸压操作(排气)的主要流动状况。即,通过气流流入卸压管线10和经烟囱16的随后逸出,出现相对于先前的自然对流而改变的流动状况,其按照流行语可表述为强制泄流。若现在反应堆外壳大气不仅从上方而且从下方流入流道26,则在下催化区36和(只要有)上催化区38内,与组成氢气H2和一氧化碳CO相关地浓度减小,随即如此经过预处理经进流口22进入卸压管线10。在设于下游的冷却装置42中,因复合反应而在催化复合装置34、40处变热的卸压流按照所述方式主要是对流的方式对反应堆外壳大气的散热从例如在入口侧的400℃至500℃被冷却到在出口侧的150℃至300℃。这个过程一方面导致在冷却装置42的外侧区域中的反应堆外壳大气的得到烟囱抽吸支持的自然对流-循环,这在图2中也由流动箭头表示。通过节流阀50、52,如此限制经过卸压管线10的物质流,即,它优选小于在根据图1的自然对流运行中存在的经过流道26的物质流的80%。同时,流入下催化区36的和(只要有)上催化区38的催化复合装置34、40的气流的进流速度通过适当构型流动路径而被调节到低于5m/s。随之获得了在卸压管线10的进流口22区域内氢气H2和/或一氧化碳CO的浓度小于在流道26的下进流孔30区域内的相应浓度的50%,优选小于其30%(尚在催化复合装置34之前在流动方向上测量的)。通过所述措施,虽然卸压流在冷却装置42和后置的系统组成部件中冷却,且虽然所含的蒸汽成分可能与之相关地部分冷凝,但阻止了能起爆的危险爆炸性气体混合物积聚在卸压管线10的下游段内。借此尤其避免对设于安全壳外的过滤和清洁装置18的完整性的威胁。卸压系统12的多个气流处理装置24和所属的卸压管线10优选设置在安全壳4的总高度的下三分之一中。多个卸压管线10可以如图1和图2示意性所示还是在安全壳4内汇聚以保持少的穿通管路46数量。所述附加的未直接作用于卸压流的催化复合装置20优选在安全壳4内设置在较高处,尤其是中央处和还有上三分之一中。在图2中示出气流处理装置24连带后置的冷却装置42的变型,其以模块化箱形结构形式来实现。所标出的流动箭头代表在卸压操作中的流动区。在两个模块之间有一个箱形的输入集管54,其将经进流口22从带有催化复合装置34、40的流道26流入的且就H2/CO浓度而言贫瘠的气体混合物分散到冷却装置42的并联的管路55。管路55呈翅片管状构成或者带有可流过的板状件等,就像通过用弧形线围边的具体例子所示。相应地,这些并行的分流随后又通过箱形的输出集管56被合流。在冷却装置42的上侧区域中形成的辐射热区用蜿蜒箭头表示,除了经反应堆外壳大气的对流热传输之外,也通过该辐射热区从被送入管路55的排气流中散走热。流过总体用10标示的卸压管线的流通限制在这里例如通过呈环形孔板58状构成的节流阀50来实现,其设置在从输出集管56至离开而通向反应堆外壳穿通的管路件的过渡区中。附图标记列表2核技术设备4安全壳6内室8外室10卸压管线12卸压系统14截止阀16烟囱18过滤和清洁装置20催化复合装置22进流口24气流处理装置26流道28周面30进流孔32进流排流口34催化部件36下催化区38上催化区40催化部件42冷却装置44流道46穿通管路48热防护罩50节流阀52节流阀54输入集管55管路56输出集管58环形孔板CO一氧化碳CO2二氧化碳H2氢气H2O水O2氧气