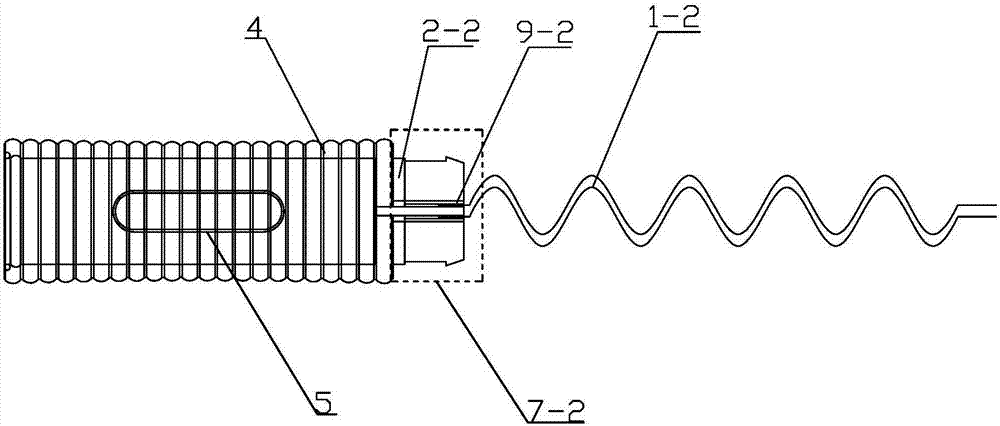
本实用新型涉及一种过氧化氢低温等离子体灭菌过程验证装置。
背景技术:
:过氧化氢低温等离子体对微生物具有广谱的杀菌作用,可杀灭细菌、真菌、病毒及芽孢,过氧化氢低温等离子体一般选择50-55℃的低温灭菌,特别适合于不耐高温及高压器械的灭菌。相比较于环氧乙烷灭菌、甲醛蒸汽熏蒸灭菌等化学灭菌方式,过氧化氢低温等离子体灭菌具有灭菌效率高,不需要通风解析;过氧化氢灭菌后的分解产物为水和氧气,对环境无污染;过氧化氢低温等离子体灭菌后器械上残留的灭菌剂量极低,便于直接使用,更加安全等特点。鉴于以上优点,近年来过氧化氢低温等离子体灭菌方式逐步在各个等级的医疗单位使用。过氧化氢低温等离子体灭菌方式也有其弊端,在灭菌过程中,过氧化氢的扩散性低,可能会造成灭菌的管腔器械内部无法进入过氧化氢气体。按照现在的灭菌监测方式,无法有效的对经过过氧化氢灭菌后的管腔器械内部的灭菌效果的验证及监测。所以急需要一种能够监测管腔器械内部灭菌情况的过程验证装置,实现对灭菌器械管腔内部的灭菌效果的生物以及化学监测。技术实现要素:本实用新型的目的是提供一种过氧化氢低温等离子体灭菌过程验证装置,通过在验证装置内部同时或者单独放置生物指示物以及化学指示物,与器械同时灭菌;通过生物指示物以及化学指示物的监测结果,模拟管腔器械内部的灭菌效果,确保对医疗器械灭菌的可靠性。能够更直接确认过氧化氢的对管腔器械的穿透效果,从而确保对医疗器械灭菌的可靠性。涉及的装置结构简单,操作简便。本实用新型一种过氧化氢低温等离子体灭菌过程验证装置,包括第一外接管,第一外接管连接内组件一端,内组件另一端插接到外组件内,外组件另一端连接第二外接管,第一外接管、内组件、外组件、第二外接管能够连通;内组件包括第一隔板,第一隔板一侧设置第一卡扣,另一侧设置内接体,第一卡扣和内接体均设有空腔,第一卡扣上设置卡槽,第一卡扣的端部设置凸台;第一隔板的中心设置通气管,通气管的一端通入第一卡扣的空腔内,另一端通入内接体的空腔内;外组件包括第二隔板,第二隔板一侧设置第二卡扣,另一侧设置外接体,第二隔板和外接体均设有空腔,第二卡扣的结构与第一卡扣的结构相同。第一隔板的直径大于第一卡扣和内接体的直径;第二隔板的直径大于第二隔板和外接体的直径;内接体的直径小于外接体的直径。外组件的外接体上设置标注区。第一外接管和第二外接管的外部均设置壳体,壳体为筒体,壳体内壁上设置卡条,卡条与卡槽对应设置。组装时,卡条与卡槽正好进行卡接。壳体的端部设有盖。第一外接管与第一密封管连接,第一密封管插接到内组件内的通气管上,实现第一外接管与内接体空腔的连通;第二外接管与第二密封管连接,第二密封管插接到外组件的通气管上,实现第二外接管与外接体空腔的连通。内组件与外组件插接的根部设置密封圈。第一隔板的通气管周围设置凸起。内组件与外组件插接后形成的空腔为测试仓。密封圈第一隔板之间新成沟槽。本实用新型通过内组件与外组件插拔式设计实现内外组件组合,测试仓内组件连接处的根部带有密封圈,实现测试仓的密封;测试仓内部空间可放置生物指示物或化学指示物。第一外接管与第二外接管均为聚四氟乙烯管,分别使用密封管即硅胶管与内组件和外组件的开口密封连接。所述测试仓组合体分别通过卡口连接带有空腔的外壳,聚四氟乙烯管腔呈螺旋状呈放于外壳内部空间中。过氧化氢低温等离子体灭菌过程验证装置的测试仓内部空间的截面积为20~100mm2,长度100~200mm。第一外接管与第二外接管单根管腔尺寸为:内径0.5-2.5mm,长度500~1500mm。本实用新型使用时,将自含式生物指示剂或者化学指示卡或者自含式生物指示剂与化学指示卡同时放置于过氧化氢低温等离子体灭菌过程验证装置测试仓的内组件的空腔内,此时将内组件插入外组件内部,并通过内组件根部的密封圈实现内外组件的完全密封。将上述自含式生物指示剂或者化学指示卡或者自含式生物指示剂与化学指示卡同时放置的过氧化氢低温等离子体灭菌过程验证装置与医疗器械放置于过氧化氢低温等离子体灭菌器内,运行正常灭菌循环程序。待灭菌完成后,将过氧化氢低温等离子体灭菌过程验证装置内外组件仓体拔开,取出内部的自含式生物指示剂以及化学指示卡,通过观察化学指示卡的颜色变化是否达到化学指示卡设定的标准色初步判断灭菌结果;然后将自含式生物指示剂取出测试仓后,按照自含式生物指示剂说明书要求的培养温度和培养时间进行细菌培养,通过自含式生物指示剂恢复培养基的颜色变化判断最终的管腔器械内部的灭菌效果。与现有技术相比,本实用新型具有以下有益效果:本实用新型采用过氧化氢低温等离子体灭菌过程验证装置,相对于直接将自含式生物指示剂或者化学指示剂直接“裸放”与过氧化氢低温等离子体灭菌器舱体内部的方法相比,能够更直接确认过氧化氢的对管腔器械的穿透效果,从而确保对医疗器械灭菌的可靠性。涉及的装置结构简单,操作简便。通过在验证装置内部同时或者单独放置生物指示物以及化学指示物,与器械同时灭菌;通过生物指示物以及化学指示物的监测结果,模拟管腔器械内部的灭菌效果,确保对医疗器械灭菌的可靠性。附图说明图1、本实用新型的内组件的结构示意图;图2、本实用新型的外组件的结构示意图;图3、第一卡扣的剖视图;图4、壳体的结构示意图;图5、壳体的剖视图;图6、第一隔板的右视图。图中,1-1、第一外接管,1-2、第二外接管,2-1、第一隔板,2-2、第二隔板,3、内接体,4、外接体,5、标注区,6、沟槽,7-1、第一卡扣,7-2、第二卡扣,8、凸台,9-1、第一密封管,9-2、第二密封管,10、密封圈,11、卡槽,12、通气管,13、壳体,14、卡条,15、凸起。具体实施方式下面结合附图及实例对本实用新型做进一步说明。实施例1本实施例所述的过氧化氢低温等离子体灭菌过程验证装置,包括第一外接管1-1,其特征在于,第一外接管1-1连接内组件一端,内组件另一端插接到外组件内,外组件另一端连接第二外接管1-2,第一外接管1-1、内组件、外组件、第二外接管1-2能够连通;内组件包括第一隔板2-1,第一隔板2-1一侧设置第一卡扣7-1,另一侧设置内接体3,第一卡扣7-1和内接体3均设有空腔,第一卡扣7-1上设置卡槽11,第一卡扣7-1的端部设置凸台8;第一隔板2-1的中心设置通气管12,通气管12的一端通入第一卡扣7-1的空腔内,另一端通入内接体3的空腔内;外组件包括第二隔板2-2,第二隔板2-2一侧设置第二卡扣7-2,另一侧设置外接体4,第二隔板2-2和外接体4均设有空腔,第二卡扣7-2的结构与第一卡扣7-1的结构相同。第一隔板2-1的直径大于第一卡扣7-1和内接体3的直径;第二隔板2-2的直径大于第二隔板2-2和外接体4的直径;内接体3的直径小于外接体4的直径。外组件的外接体4上设置标注区5。第一外接管1-1和第二外接管1-2的外部均设置壳体13,壳体13为筒体,壳体13内壁上设置卡条14,卡条14与卡槽11对应设置。组装时,卡条14与卡槽11正好进行卡接。壳体13的端部设有盖。第一外接管1-1与第一密封管9-1连接,第一密封管9-1插接到内组件内的通气管12上,实现第一外接管1-1与内接体3空腔的连通;第二外接管1-2与第二密封管9-2连接,第二密封管9-2插接到外组件的通气管12上,实现第二外接管1-2与外接体4空腔的连通。内组件与外组件插接的根部设置密封圈10。内组件与外组件插接后形成的空腔为测试仓。第一外接管1-1与第二外接管1-2呈螺旋状呈放于壳体13内部。本实用新型中测试仓内外组件的开口分别通过第一密封管9-1和第二密封管9-2与第一外接管1-1与第二外接管1-2密封连接。第一隔板2‐1的通气管12周围设置凸起15。密封圈10第一隔板之间新成沟槽6。下面完全模拟管腔器械的灭菌情况,通过与模拟管腔的对比灭菌实验说明本实用新型对管腔器械灭菌的监测效果。自制模拟管腔,取2根内径1mm,壁厚0.75mm,长度1000mm的聚四氟乙烯管腔,分别在管腔的一端开口处滴染嗜热脂肪杆菌芽孢,芽孢含量为0.75×106cfu;控制芽孢悬液进入进入聚四氟乙烯管腔内部的尺寸小于20mm;待自然干燥后,使用内径1mm,长度15mm,壁厚1.5mm的硅胶管将上述2根聚四氟乙烯管滴染芽孢端连接,备用。过氧化氢低温等离子体灭菌过程验证装置的结构、组成与实施例1中相同,在过氧化氢低温等离子体灭菌验证装置的测试仓内放置自含式生物指示剂,与上述自制的模拟管腔同时放置于过氧化氢低温等离子体灭菌器内灭菌。灭菌完成后,将上述自制模拟的管腔的滴染芽孢的部位在无菌环境中剪下并投入到经过灭菌的营养肉汤培养基中,培养7天,观察细菌生长情况。灭菌完成后,将过氧化氢低温等离子体灭菌过程验证装置内外舱体拔开,取出内部的自含式生物指示剂,按照自含式生物指示剂说明书要求的培养温度和培养时间进行恢复培养,通过自含式生物指示剂恢复培养基的颜色变化判断芽孢杀灭菌情况。下表所示为在不同过氧化氢注入条件下,自制模拟管腔与过氧化氢低温等离子体灭菌过程验证装置内的自含式生物指示剂灭菌结果。序号过氧化氢注入量自制管腔培养结果自含式生物指示剂培养结果11.0mL阳性阳性21.5mL阴性阴性32.0mL阴性阴性经过以上验证,过氧化氢低温等离子体灭菌过程验证装置内部放置自含式生物指示剂后与自制的模拟管腔同时灭菌,生物培养结果完全相同,说明过氧化氢低温等离子体灭菌过程验证装置完全可以模拟管腔器械内部的细菌杀灭情况。当前第1页1 2 3