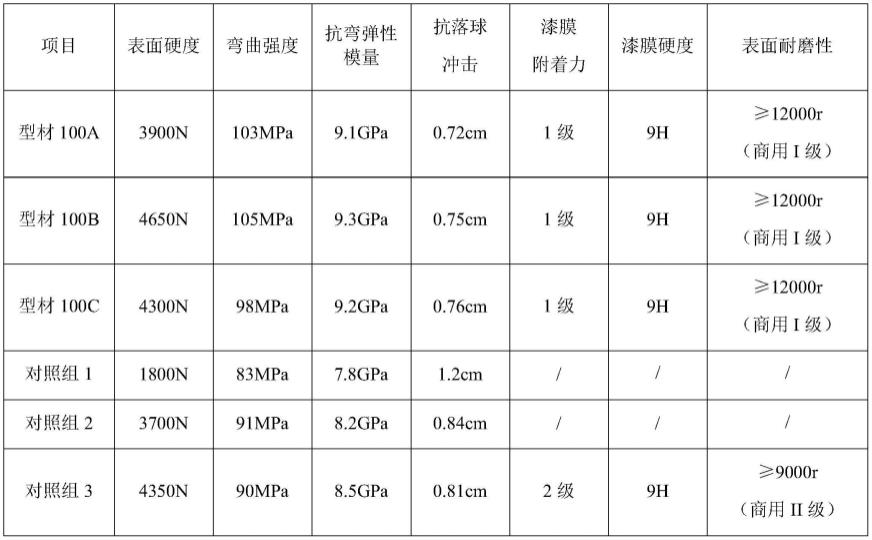
1.本发明涉及木材功能改性材料领域,具体为一种表面功能改性的型材,本发明同时还涉及制作该种表面功能改性的型材的方法。
背景技术:2.速生材资源丰富,是可循环的绿色材料。但是速生材的材质存在材质较软、密度与强度偏低等缺陷,所以在实际应用中多被制成纤维、刨花以用于人造板的制造,极少见于高附加值的利用途径,例如实木化的利用。基于此,速生材表面的功能性改性研究是提高速生材应用价值的重要研究方向之一。
3.在速生材的表面压贴耐磨贴面是一种实现其表面功能性改性的手段。一种方式是在经过密实化处理的速生材表面压贴成品的耐磨纸。如中国专利数据库中公开号为cn102107452b,名称为“一种软木实木地板及其制造方法”的发明专利中公开了在表面密实化、炭化处理的速生材表面压贴耐磨纸的技术方案,具体是首先将速生材通过热压实施表面密实化处理,随后同位热压炭化以固定压缩效果,最后通过热压在密实化表面上压贴三氧化二铝-三聚氰胺树脂浸渍纸以形成耐磨表面。
4.另一种方式是在速生材表面形成耐磨层。如公开号为cn102259450b,名称为“一种自耐磨木质复合材料及其制造方法”的发明专利中公开了在速生材表面形成耐磨表面的技术方案,具体是在速生材表面涂抹胶粘剂、气流铺装耐磨颗粒(例如三氧化二铝颗粒、二氧化硅颗粒、氢氧化铝颗粒、或碳化硅颗粒),随后在具有耐磨颗粒的表面再次涂胶,最终在速生材表面形成耐磨涂层。
5.然而,本领域技术人员可以理解,上述第一种方式存在耐磨纸与速生材基材之间的结合强度较弱的问题。的密度相对较大,且木材经热压、炭化后表面具有一定的疏水性,耐磨纸热压贴覆时,耐磨纸中的胶粘剂不容易渗透木材表面,所以耐磨纸与速生材基材之间的结合强度相对较弱。上述第二种方式则存在工艺较为复杂、在气流作用下耐磨颗粒可能分布不均的问题。与此同时,为保证耐磨颗粒在速生材表面的附着效果而实施的二次涂胶,可能导致裸露在外的耐磨颗粒数量相对较少而影响了实际的耐磨效果。
技术实现要素:6.本发明的目的在于克服上述技术问题,提供一种表面功能改性的型材;本发明同时还提供制作该种表面功能改性的型材的方法。
7.为实现上述目的,本发明的实施例提供了一种表面功能改性的型材,由上至下依次包括耐磨颗粒层、耐磨增强层,所述耐磨颗粒层与所述耐磨增强层粘结连接;所述耐磨增强层受到密实化压缩,并填充有自所述耐磨颗粒层向其渗透的熔融胶粘剂。
8.作为优选,所述型材还包括位于所述耐磨增强层的内侧且与所述耐磨增强层连接的密实化压缩层。
9.作为优选,所述型材还包括原始密度层;所述原始密度层位于所述耐磨增强层的
内侧且与所述耐磨增强层连接,或
10.所述原始密度层位于所述密实化压缩层的内侧且与所述密实化压缩层连接。
11.作为优选,所述耐磨颗粒层与所述耐磨增强层位于所述型材的同侧板面。
12.为实现上述目的,本发明的实施例还提供了一种型材表面功能改性工艺,包括通过热板热压型材的密实化处理步骤,先在所述型材的板面上覆盖耐磨纸,然后对所述型材实施所述密实化处理步骤以在所述型材上形成耐磨颗粒层与耐磨增强层;所述耐磨颗粒层由所述耐磨纸熔融再固化形成,并与所述耐磨增强层粘结连接;所述耐磨增强层受到密实化压缩,并填充有自所述耐磨纸向其渗透的熔融胶粘剂。
13.作为优选,所述密实化处理步骤同时在所述型材上形成与所述耐磨增强层连接的密实化压缩层。
14.作为优选,所述热板在接触所述耐磨纸的同时向所述型材施压并持续压缩进给直至达到设定的压缩量。
15.作为优选,在120s内完成所述热板的压缩进给,并达到18%~23%的设定的压缩量。
16.作为优选,自到达设定的压缩量之时计,将所述热板的压力与温度保持50s~90s,然后将所述热板的温度在8min~10min的时间内降至40℃以下。
17.作为优选,在实施密实化处理步骤前,所述型材的含水率是10%~14%;在实施密实化处理步骤中,所述热板的压力是3.5mpa~4.5mpa。
18.综上所述,与现有技术相比,本发明的有益效果是:
19.1、本技术技术方案的型材,耐磨增强层中填充有自耐磨颗粒层向其渗透的部分熔融胶粘剂,所以一方面,型材的密实化压缩效果受到渗透的胶粘剂的增强,使形成的耐磨增强层具有更高的密度、强度、硬度和耐磨性能,并使得到的改性型材达到免漆、免饰面的效果;另一方面,耐磨颗粒层与耐磨增强层的粘结强度更高,耐磨颗粒层不易脱落,型材的耐磨性能更好、耐磨寿命更长,自身的使用寿命也能够得到延长。
20.2、本技术技术方案的密实化处理步骤中同时实现型材的密实化压缩以及耐磨纸与型材的粘结复合,所以制备工艺相对简单、生产效率较高,并且质量相对稳定,特别是耐磨颗粒在型材表面的分布较为均匀,即处理后型材的表面各处的耐磨性大致相当。
附图说明
21.为了更清楚地说明本技术实施例或现有技术中的技术方案,下面将对实施例或现有技术描述中所需要使用的附图作简单地介绍,显而易见地,下面描述中的附图仅是本技术的一些实施例,对于本领域技术人员来讲,在不付出创造性劳动性的前提下,还可以根据这些附图获得其他的附图。
22.图1为本技术实施例1的表面功能改性的型材的结构示意图。
23.图2为本技术实施例2的表面功能改性的型材的结构示意图。
24.图3为本技术实施例3的表面功能改性的型材的结构示意图。
25.图4为本技术实施例3的表面功能改性的型材剖面密度图。
26.图5为本技术实施例4的表面功能改性的型材的结构示意图。
27.图中:100,100’、型材,200、耐磨纸,110、耐磨颗粒层,120、耐磨增强层,130、密实
化压缩层,140、原始密度层,150、密实化压缩背层。
具体实施方式
28.为了使本技术领域的人员更好地理解本技术中的技术方案,下面将结合本技术实施例中的附图,对本技术实施例中的技术方案进行清楚、完整地描述,显然,所描述的实施例仅是本技术一部分实施例,而不是全部的实施例。基于本技术中的实施例,本领域普通技术人员在没有做出创造性劳动的前提下所获得的所有其他实施例,都应当属于本技术保护的范围。
29.实施例1
30.参照图1所示的一种表面功能改性的型材100,由上至下依次包括耐磨颗粒层110、耐磨增强层120,耐磨颗粒层110与耐磨增强层120粘结连接;耐磨增强层120受到密实化压缩,并填充有自耐磨颗粒层110向其渗透的部分熔融胶粘剂。
31.借由上述结构,与现有技术的密实化型材相比较,本实施例的型材100的密实化压缩效果受到自耐磨颗粒层110向其渗透的部分熔融胶粘剂的增强,而使形成的耐磨增强层120具有更高的密度、强度、硬度和耐磨性能,从而,由耐磨颗粒层110、耐磨增强层120构成的型材表面能够达到免漆饰、免饰面而直接使用的技术效果。同时,与现有技术的技术方案(先密实化压缩后压贴耐磨纸的工艺方法)所得到的表面功能改性材料相比较,耐磨增强层120中填充有自耐磨颗粒层110向其渗透的熔融胶粘剂,所以耐磨颗粒层110与耐磨增强层120的粘结强度更高,耐磨颗粒层110不易脱落,型材100的耐磨性能更好、耐磨寿命更长,自身的使用寿命也能够得到延长。
32.具体来说,本实施例的型材100’初始状态是厚度为1mm的杨木单板,初始含水率约12%。先在型材100’上覆盖耐磨纸200,耐磨纸200是38g/m2的三氧化二铝-三聚氰胺树脂浸渍纸,此时耐磨纸200仅仅是覆盖在型材100’的表面而与型材100’的表面没有连接关系。然后,将覆盖有耐磨纸200的型材100’置于上、下压板之间,实施密实化处理步骤。密实化处理步骤中,上、下压板均是热板,温度150
±
3℃,上、下压板的初始间距2mm,厚度规厚度0.6mm。再后,待覆盖有耐磨纸200的型材100’放置到位后立即下降上压板,上压板接触耐磨纸200的同时向型材100’施压并持续压缩进给直至接触厚度规,厚度规厚度0.6mm,制得厚度0.6mm的型材100。最后,在恒温恒湿环境中调整型材100的含水率至10%左右。
33.借由上述方法,首先,在本实施例的密实化处理步骤中同时实现型材100’的密实化压缩以及耐磨纸200与型材100’的粘结复合,所以制备工艺相对简单、生产效率较高,处理得到的型材能行相对稳定,特别是耐磨颗粒在型材100的表面的分布较为均匀。
34.其次,上压板先使耐磨纸200发生熔融,此时型材100’的表面尚未发生压缩,仍保留速原始的材性特征——孔隙率相对较大,所以耐磨纸200中的部分胶粘剂、甚至耐磨颗粒能够随着上压板的压缩进给而在高温、压力引发的水分迁移的驱动力作用下渗透进入型材100’的板面。换言之,上压板的温度、压力传达至型材100’使其板面以下的单位厚度材料的屈服强度小于上压板的下压压力,板面以下的单位厚度同时发生了密实化压缩与受到耐磨纸中的部分胶粘剂、甚至耐磨颗粒的迁移渗透。板面以下的单位厚度在同时受到热压的密实化压缩与胶粘剂、甚至耐磨颗粒的迁移渗透之后形成了耐磨增强层120。所以,本实施例的改性工艺得到的耐磨增强层120与单纯通过密实化压缩步骤得到的密实化压缩表层相
比,压缩效果受到胶粘剂、甚至耐磨颗粒的增强而具有更高的密度、强度、硬度和耐磨性能,能够达到免漆饰、免饰面而直接使用的技术效果;同时,本实施例的改性工艺得到的耐磨增强层120与现有技术(先密实化压缩再压贴耐磨纸的工艺)相比,耐磨纸200与型材100’之间具有更好的连接强度,耐磨颗粒不易脱落,使制得的型材100的耐磨性能更好、耐磨寿命更长、自身的使用寿命也相对较长。
35.实施例2
36.实施例2与实施例1的区别在于,参照图2所示,型材100还包括位于耐磨增强层120的内侧且与耐磨增强层连接的密实化压缩层130,密实化压缩层130与耐磨增强层120属于原始型材100’的不同厚度层。换言之,密实化压缩层130是仅发生了密实化压缩但没有胶粘剂渗透的厚度层。在本实施例中,能够检测出胶粘剂渗透的耐磨增强层120的厚度大约是0.5mm,剩余厚度是密实化压缩层130。
37.型材100的表面功能改性方法与实施例1大致相同,不同之处在于,本实施例的型材100’初始状态是厚度为3mm的杨木单板,厚度规厚度2mm,密实化处理步骤结束后能够得到厚度2mm的型材100。最后,在恒温恒湿环境中调整型材100的含水率至10%左右。
38.延长上压板的压缩进给继续进行,或在压缩前设置一段时间的预热处理,便能够在耐磨增强层120之下形成密实化压缩层130,耐磨增强层120与密实化压缩层130之间是同一材料的自然连接,即二者属于原始型材100上受到不同处理、达到不同改性效果的两个厚度层。
39.分别将实施例1-2的型材100作为贴面材料冷压粘覆于14mm厚的多层胶合板表面,以制得厚度分别为14.6mm、16mm的实木复合地板。用于贴面的型材100较现有技术的贴面单板而言,具有免漆、耐磨的优势。制得的实木复合地板的理化性能参照表1所示。表1中,对照组1是通过将厚度自3mm压缩至2mm的杨木密实化压缩单板冷压贴覆于14mm厚的多层胶合板表面制得的实木复合地板;对照组2是采用现有技术的手段制得的耐磨密实化单板,即先将厚度为3mm的杨木单板压缩至2mm得到密实化压缩单板,再通过热压在密实化压缩单板的表面粘附耐磨纸得到耐磨密实化单板,耐磨纸是38g/m2的三氧化二铝-三聚氰胺树脂浸渍纸,最后将耐磨密实化单板冷压贴覆于14mm厚的多层胶合板表面。
40.由于目前尚没有对该种产品的理化性能检测的参考标准,特别是表面性能,因此本技术选择的性能指标、实验方法参照“人造板及饰面人造板理化性能实验方法gb/t 17657-2013”及“浸渍纸层压木质地板gb/t 18102-2020”两个标准执行。
41.表1.本技术实施例1-2的型材贴面的实木复合地板的理化性能
42.项目表面硬度漆膜附着力漆膜硬度表面耐磨性实施例14250n1级9h≥12000r(商用i级)实施例24700n1级9h≥12000r(商用i级)对照组13500n///对照组24580n2级9h≥9000r(商用ii级)
43.实施例3
44.参照图3所示的一种表面功能改性的型材100,由上至下依次包括耐磨颗粒层110、耐磨增强层120、密实化压缩层130和原始密度层140。耐磨颗粒层110与耐磨增强层120粘结连接;耐磨增强层120受到密实化压缩,并填充有自耐磨颗粒层110向其渗透的部分熔融胶
粘剂;密实化压缩层130与耐磨增强层120连接,是与耐磨增强层120共同受到密实化压缩的压缩厚度层中没有胶粘剂渗透的部分;原始密度层140是没有受到密实化压缩的型材100’的原始厚度层。当然,如果压缩量足够小,则型材100的结构将仅由耐磨颗粒层110、耐磨增强层120和原始密度层140构成。压缩量的控制是本领域技术人员能够获取的任意一种现有手段,此处不做赘述。
45.本实施例的表面改性方法通过分别贴覆三种规格的耐磨纸200得到三种型材100,三种耐磨纸200的规格分别是22g/m2(对应得到型材100a)、38g/m2(对应得到型材100b)、45g/m2(对应得到型材100c)。具体是:
46.首先,将耐磨纸200放置在型材100’的表面,型材100’是厚度为25mm的杨木板材,初始含水率约14%;同时,将上压板的温度升至142
±
2℃下压板的温度保持室温(约25℃),将型材100’连同耐磨纸200放置在下压板上。
47.随后,上压板下压开始密实化处理步骤,上压板下降至接触耐磨纸的同时开始压缩进给,压力4mpa,厚度规厚度20mm,即设定的压缩量是20
±
1%;120s后上压板接触厚度规、停止压缩进给。
48.再后,保持压力、温度60s,所以密实化处理步骤同时在型材100’上形成与耐磨增强层120连接的密实化压缩层130。
49.最后,10min内将上压板的温度降至40℃左右,泄压出料。
50.图4中示出了本实施例的三种型材100的剖面密度图,并与素材、仅单侧表层压缩的型材作比较,其中单侧表层压缩的型材的压缩工艺与本实施例大致相同,区别在于压缩前存在20s的预热。通过上述方法,型材100表面的耐磨颗粒层110形成了型材100的第一个密度峰值并在耐磨颗粒层110以下一定距离处形成第二个密度峰值。
51.现有技术认为,由于没有预热引起的水分的提前迁移,且热板(一般是上压板)接触板材之时起便发生了板材的压缩,所以无预热的单侧表面密实化处理得到的密实化压缩型材中具有峰值密度的厚度层几乎出现在板材的最表面,在由上至下的方向上逐渐降低直至某个厚度及以下保持型材100’的原始密度。然而,现有技术的漆饰处理需要经由重型砂光机砂光得到的精细砂光表面,而具有峰值密度的厚度层往往在这一过程中被完全砂除,所以现有技术一般选择经预热的单侧表面密实化处理工艺,以使密度峰值的厚度层位置向里侧推移。可以参照图4中的黑色曲线所展示的剖面密度分布。
52.但是在本技术中,发明人创造性的发现,位于最表面的耐磨纸的熔融过程需要吸收大量的热量,且耐磨纸中的胶粘剂具有一定的阻隔热量传递的效果,所以,虽然本实施例采用的是无预热的单侧表面密实化处理工艺,但在上压板进给的初期(上压板进给的速度实际上是非常缓慢的)热量首先由耐磨纸吸收并形成一定阻隔,随后才逐渐向形成100’传递,借由此传递路径能够构成实际上的预热效果,即由热压的密实化处理形成的第二个密度峰值的厚度层实际上位于型材整个厚度断面上更靠里侧的位置,并在第一个和第二个密度峰值之间形成密度相对较低的松弛带。显然,相较于第二密度峰值,松弛带的密度相对较小、孔隙率相对较大,所以松弛带的结构仍允许胶粘剂、甚至可能的耐磨颗粒的迁移渗透。
53.厘清了上述事实后,发明人推演的密实化处理步骤的进程是这样的:上压板接触耐磨纸至进给的初期(大约5s~6s的时间段内)上压板的热量用于耐磨纸的熔融并受胶粘剂的阻隔,此时,耐磨纸的熔融再固化后形成耐磨颗粒层(第一个密度峰值)。随后,压缩密
实化逐步发生,在形成的密实化压缩的厚度层中,与耐磨颗粒层连接的厚度层是相对的松弛层,部分胶粘剂受高温、压力引发的水分迁移的驱动渗透进入松弛带形成密度高于松弛带原有密度的耐磨增强层(拐点密度),将发生密实化压缩的厚度层中的余下厚度位置定义为密实化压缩层,则第二个峰值密度出现的密实化压缩层中。
54.进一步的,通过结合特定的压缩量(18%~23%)与特定的压缩进程耗时(120s内完成),能够在适当的位置形成足以阻隔胶粘剂继续渗透的密度层。换言之,胶粘剂、可能的耐磨颗粒仅能够在特定的厚度范围内发生迁移渗透。所以既能够保证胶粘剂、可能的耐磨颗粒发生迁移渗透而形成耐磨增强层;又能够避免胶粘剂过渡渗透而影响耐磨颗粒在型材表面的附着。进一步的,由密实化压缩处理形成了更靠近里侧位置的第二个密度峰值的厚度层能够进一步扩大型材的强化表层的厚度,具体体现在抗落球冲击、抗弯强度和抗弯弹性模量等指标的提高上。反过来说,如果压缩量过大、压缩进程的耗时过长,则容易使胶粘剂过度渗透而影响耐磨颗粒的附着力,并是剖面密度呈现自第一个峰值密度后直线曲线下降的密度分布形态,在没有密度的“夹心态”分布的情况下,使型材的抗落球冲击、抗弯强度和抗弯弹性模量等指标的提高效果稍有欠缺。
55.在本实施例中,由于胶粘剂的渗透,而使得原本的松弛带的密度也得到了提高。体现在图4中第一密度峰值与第二密度峰值之间的拐点密度被提高。定义自表面至拐点密度附近的厚度位置是耐磨增强层120,拐点密度附近的厚度位置至原始密度出现的厚度位置之间是密实化增强层130,以下是原始密度层140。实验测得,渗透有胶粘剂的耐磨增强层120的厚度大约是0.5mm~0.6mm,密实化增强层130的厚度大约是7mm~8mm。
56.实施例3的三种型材100的理化性能参照表2所示。其中,对照组1是素材;对照组2是采用预热工艺制得的仅单侧表层压缩的型材;对照组3是采用现有技术的手段制得的型材,先将厚度为25mm的杨木单板压缩至20mm得到密实化压缩型材,再通过热压在密实化压缩单板的表面粘附耐磨纸得到耐磨密实化单板,耐磨纸是38g/m2的三氧化二铝-三聚氰胺树脂浸渍纸。
57.表2.实施例3的三种型材100的理化性能表
[0058][0059]
实施例4
[0060]
实施例4与实施例3的区别在于,参照图5所示,一种表面功能改性的型材100,由上至下依次包括耐磨颗粒层110、耐磨增强层120、密实化压缩层130、原始密度层140和密实化压缩背层150。
[0061]
本实施例的型材100通过以下方法制得:
[0062]
首先,将耐磨纸200放置在型材100’的表面,型材100’是厚度为25mm的杨木板材,初始含水率约14%,耐磨纸200是38g/m2的三氧化二铝-三聚氰胺树脂浸渍纸;同时,将上压板、下压板的温度升至142
±
2℃使上压板、下压板之间的间距控制在27mm左右。
[0063]
随后,将型材100’连同耐磨纸200放置在下压板上,快速使上压板接触耐磨纸200。
[0064]
再后,上压板下压开始密实化处理步骤,上压板下降至接触耐磨纸的同时开始压缩进给,压力4mpa,厚度规厚度19mm,即设定的压缩量是24%;120s后上压板接触厚度规、停止压缩进给。
[0065]
再后,保持压力、温度60s,所以密实化处理步骤同时在型材100’上形成耐磨增强层110、与耐磨增强层110连接的密实化压缩层120、密实化压缩层130和密实化压缩背层150。
[0066]
最后,8min内将上压板的温度降至40℃左右,泄压出料。
[0067]
由于上压板与下压板都是热板,所以密实化压缩发生在型材100’的两个板面。由于耐磨纸200熔融再固化使热量传递发生延迟,所以实际上形成的密实化压缩背层150的厚度略大于耐磨增强层120、密实化压缩层130的厚度之和。并且,形成于密实化压缩背层150的第三密度峰值出现的厚度位置较第二密度峰值出现的厚度位置更靠近厚度的中心线。由此,相对较大的密实层厚度和更靠近厚度中心线的第三密度峰值位置能够相对较好的在型材100的背面形成与耐磨颗粒层110、耐磨增强层120、密实化压缩层130的平衡效果,使型材100的平整度更高,且更易于维持平整度。
[0068]
实施例4的型材100的理化性能参照表3所示。其中,以实施例3中型材100b、对照组
1-3作为比较。
[0069]
表3.实施例4的型材100的理化性能表
[0070]
项目表面硬度弯曲强度抗弯弹性模量抗落球冲击长度翘曲度实施例44500n117mpa9.9gpa0.70cm0.7%型材100b4650n105mpa9.3gpa0.75cm0.4%对照组11800n83mpa7.8gpa1.2cm0.3%对照组23700n91mpa8.2gpa0.84cm1.2%对照组34350n90mpa8.5gpa0.81cm1.5%
[0071]
从表3中可以得知,显然密实化压缩背层150的存在能够在一定程度上提高型材100的弯曲强度、抗弯弹性模量,使其平整度的稳定性更高。
[0072]
以上描述是为了进行图示说明而不是为了进行限制。通过阅读上述描述,在所提供的示例之外的许多实施方式和许多应用对本领域技术人员来说都将是显而易见的。因此,本教导的范围不应该参照上述描述来确定,而是应该参照所附权利要求以及这些权利要求所拥有的等价物的全部范围来确定。出于全面之目的,所有文章和参考包括专利申请和公告的公开都通过参考结合在本文中。在前述权利要求中省略这里公开的主题的任何方面并不是为了放弃该主体内容,也不应该认为申请人没有将该主题考虑为所公开的申请主题的一部分。