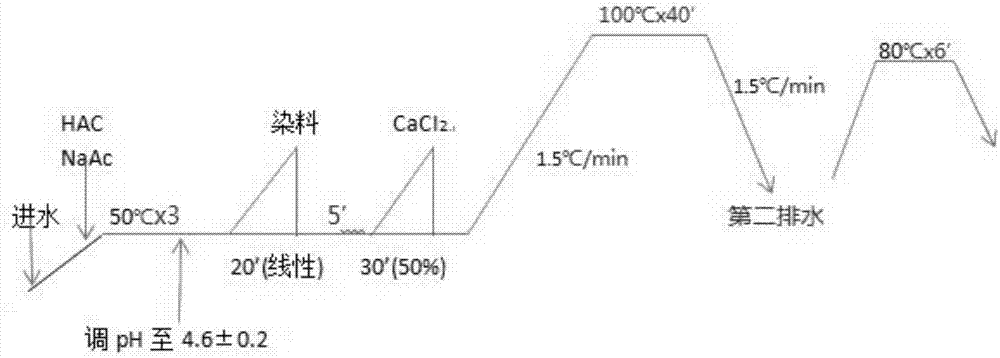
本发明属于纺织印染
技术领域:
,具体涉及一种锦纶织物的染色工艺。
背景技术:
:锦纶具有优良的性能,如比重小,手感柔软,质感轻盈,透气吸湿,染色性能好等特点,因此锦纶织物的用途很广,锦纶织物一般选用酸性染料染色。而酸性染料的湿处理牢度随染料不同差异较大,一般需固色处理,但在染大红、深紫、黑色等特深色时牢度仍达不到要求。为改善染深色的牢度问题,可采用新型反应性活性染料eriofast来染深色。张贵等人在锦纶弹力织物eriofast活性染料染色的研究中,采用eriofast活性染料染色,在锦纶弹力织物纤维上能够取得深的色相,移染性、配伍性好,不易花色,颜色稳定,但是在生产中经常出现布面刮痕问题。cn103966869a公开了一种锦纶的染色工艺,包括以下步骤:(1)坯布定型,在浸液中加入抗热泛黄助剂,浸液温度保持在180-190摄氏度,(2)第一次染色处理,染浴ph值优选4.5-5.2之间,染浴温度保持在25-45摄氏度,在染浴中加入抗皱剂和消光剂,使染温度为30-35摄氏度,升温至70-75摄氏度,(3)第二次染色处理,在染色液中加入醋酸铵使ph值保持在6.5-7.2之间,使用均染剂以加强均染,(4)低温染色,染色液中加入苯甲醇、醋酸和稀土的比例保持在1:1-1.2:0.85-1.15,染色液温度保持在40-50摄氏度进行染色。该发明锦纶的染色工艺采用在低温情况下进行染色处理,增加了染色后锦纶的弹性,提高了上染率,减少了色花的出现。但是,上述染色工艺在染深色布时也容易出现布面刮痕问题。技术实现要素:针对现有技术的不足,本发明的目的在于提供一种锦纶织物的染色工艺,染深色时,可避免布面出现刮痕的问题,染色色牢度高。为达此目的,本发明采用以下技术方案:一种锦纶织物的染色工艺,所述工艺包括如下步骤:1)配置含有活性染料eriofast的染液;2)在亚矶水流缸中加水,用ph调节剂调节ph为4.4~4.8,将锦纶织物置于亚矶水流缸含有步骤1)制得的染液中,加入氯化钙在90~110℃温度下染色;其中,所述染色的参数为:浴比为(1:11)~(1:13),染色水冲为1.1~1.3kg,机速为230~250m/min。本发明用eriofast活性染料在亚矶水流缸染深色时,通过合理调节浴比、行机条件、载布量等染色参数,可有效避免染深色时布面出现的刮痕问题,染色效果好。步骤1)中,活性染料eriofast包括eriofast黄r、eriofast黑m和eriofast藏青m;本发明所述的活性染料eriofast为亨斯迈公司生产的活性染料,eriofast黄r、eriofast黑m和eriofast藏青m分别为三种不同的活性染料的型号,具有出色的兼容性,在同一染色处方中,可以以非常相似的方式上染纤维,且色光一致,可确保染色的重现性和匀染性。优选地,所述染液包括以下组分:eriofast黄r(owf.)0.5~0.7%,例如eriofast黄的用量为0.5%、0.6%、0.7%;eriofast黑m(owf.)3~5%,例如eriofast黑的用量为3%、3.5%、4%、4.5%、5%;eriofast藏青m(owf.)3~3.5%,例如eriofast藏青的用量为3%、3.1%、3.2%、3.3%、3.4%、3.5%;优选地,步骤2)中,所述ph调节剂为醋酸和醋酸钠的混合物,其中,醋酸的用量为1~1.5g/l,例如醋酸的质量体积浓度为1g/l、1.1g/l、1.2g/l、1.3g/l、1.4g/l、1.5g/l;醋酸钠的用量为0.5~0.8g/l,例如醋酸钠的质量体积浓度为0.5g/l、0.6g/l、0.7g/l、0.8g/l。优选地,步骤2)中氯化钙占所述染液的重量百分比为3~10%,例如所述氯化钙的用量为、3%、4%、5%、6%、7%、8%、9%、10%。步骤2)中,所述浴比为(1:12)~(1:13)。如果浴比小于1:14时,由于水过多,染缸后面的布飘浮至缸前端压住前面的布,造成行机不顺,圈时过长,会出现刮痕;如果浴比大于1:10时,由于水少导致布身浮力不够,行机不顺,圈时过长,也会出现严重刮痕。步骤2)中,所述染色水冲为1.1~1.2kg。步骤2)中,所述机速为230~250m/min,机速太快或太慢,都会导致圈时太长,相对滑差变大,导致刮痕出现。步骤2)中,所述染色工艺中亚矶水流缸单管的载布量为190~200kg。所述染色工艺还包括用固色剂固色的后处理工艺。所述固色剂为eriofastfix,与其他固色剂不同,eriofastfix不会影响纤维的柔软度和亲水性,也不会引起织物的黄变,可以使织物得到良好的色牢度。优选地,所述eriofastfix与所述活性染料eriofast的质量比为1:(1.5~2),例如所述eriofastfix与所述活性染料eriofast的质量比为1:1.5、1:1.6、1:1.7、1:1.8、1:1.9、1:2。所述固色的后处理工艺所用的溶液包括以下组分:氢氧化钠1~2g/l,例如氢氧化钠的质量体积浓度为1g/l、1.1g/l、1.2g/l、1.3g/l、1.4g/l、1.5g/l、1.6g/l、1.7g/l、1.8g/l、1.9g/l、2g/l;eriofastfix3~5%,例如eriofastfix的用量为3%、3.5%、4%、4.5%、5%;苏打0.5~2g/l,例如苏打的质量体积浓度为0.5g/l、0.6g/l、0.7g/l、0.8g/l、0.9g/l、1g/l、1.1g/l、1.2g/l、1.3g/l、1.4g/l、1.5g/l、1.6g/l、1.7g/l、1.8g/l、1.9g/l、2g/l;醋酸0.5~2g/l,例如醋酸的质量体积浓度为0.5g/l、0.6g/l、0.7g/l、0.8g/l、0.9g/l、1g/l、1.1g/l、1.2g/l、1.3g/l、1.4g/l、1.5g/l、1.6g/l、1.7g/l、1.8g/l、1.9g/l、2g/l。优选地,所述固色的后处理工艺的具体过程为:亚矶水流缸中加水,用氢氧化钠调节ph为10~12,加入eriofastfix升温至70~90℃进行固色,苏打水洗、醋酸酸洗后排水。作为本发明的优选方案,所述锦纶织物的染色工艺包括如下步骤:1)配置含有活性染料eriofast的染液;2)在亚矶水流缸中加水,用ph调节剂调节ph为4.4~4.8,将锦纶织物置于亚矶水流缸含有步骤1)制得的染液中,加入氯化钙在90~110℃温度下染色;其中,所述染色的参数为:浴比为(1:11)~(1:13),染色水冲为1.1~1.3kg,机速为230~250m/min;亚矶水流缸单管的载布量为170~220kg;3)将经步骤2)染色的锦纶织物用固色剂进行固色后处理;所述固色剂为eriofastfix;所述eriofastfix与所述活性染料eriofast的质量比为1:(1.5~2)。与现有技术相比,本发明的有益效果为:本发明的锦纶织物的染色工艺,通过调节浴比为(1:11)~(1:13),水冲为1.1~1.3kg,机速为230~250m/min,亚矶单管载布量190kg~200kg,染深色时可以有效的避免布面刮痕产生,染色后沾色牢度高,可达4~5级。附图说明图1为本发明的锦纶织物的染色工艺的流程图;图2为本发明的锦纶织物的后处理工艺的流程图。具体实施方式为便于理解本发明,本发明结合附图1、2,并列举实施例如下。本领域技术人员应该明了,所述实施例仅仅是帮助理解本发明,不应视为对本发明的具体限制。本发明所用的材料和仪器设备如下所示:材料与染化料材料:锦纶含莱卡织物(74%nylon6,26%spandex),克重170g/m2。染料:eriofast系列染料黄r、黑m、藏青m(亨斯迈公司)。助剂:醋酸、醋酸钠、氯化钙、苏打、eriofastfix-01、氢氧化钠。生产设备亚矶水流缸、门富士开幅定型机、ph计等。其中,本发明的黑色染料配方如下:如图1所示,本发明的染色工艺具体过程为:1)按上述黑色染料配方配制染液;2)在亚矶水流缸中加水,用ph调节剂调节ph为4.4~4.8,升温至50℃促进ph调节剂溶解,将锦纶织物置于亚矶水流缸含有步骤1)制得的染液中,染液的在20min内添加完毕,加入氯化钙以1.5℃/min的速度升温至90~110℃温度下染色;其中,所述染色的参数为:浴比为(1:11)~(1:13),染色水冲为1.1~1.3kg,机速为230~250m/min;降温后排水。如图2所示,本发明的后处理工艺具体为:在亚矶水流缸中加水,加入氢氧化钠调节ph为10~12,以1.5℃/min的速度升温至40℃促进氢氧化钠溶解,加入eriofastfix-01后升温至85℃进行固色,降温后排水,再将固色后的锦纶织物置于亚矶水流缸中,升温至60℃用苏打水洗后降温排水,再用醋酸洗中和后排水,将固色后的锦纶织物出缸后得到染色后的锦纶织物产品。实施例1-3按图1的染色工艺对锦纶织物进行染色,通过调节不同的浴比讨论对染色的影响。其中,其它条件相同时,设计三个浴比(分别为1:11、1:12、1:13)作为实施例1、2、3进行试验。对比例1-2以浴比为1:10、1:14分别作为对比例1、对比例2,其他条件均与实施例1-3相同,染色参数及查布结果见表1。表1由表1数据可以看出,实施例1、2、3的浴比为1:11、1:12、1:13时生产时行机顺畅,布面无刮痕。对比例1的浴比为1:10和对比例2的浴比为1:14时,布面有不同程度刮痕。对比例1浴比在1:10时由于水少导致布身浮力不够,行机不顺,圈时过长,布面刮痕严重。对比例2浴比在1:14时由于水过多,染缸后面的布飘浮至缸前端压住前面的布,造成行机不顺,圈时过长,布面也会有刮痕。实施例4-6选定浴比1:12,将染色水冲设定为:1.1kg、1.2kg、1.3kg进行试验分别记为实施例4、5、6,水冲对刮痕的影响结果如表2所示。对比例3-4选定浴比1:12,将染色水冲设定为:1.0kg、1.4kgg进行试验分别记为实施例3、对比例4,水冲对刮痕的影响结果如表2所示。表2由表2数据可以看出,实施例4、5、6的水冲在1.1kg、1.2kg和1.3kg时所染织物布面无刮痕,实际生产中考虑到能耗问题,选水冲1.2kg最佳。对比例3的水冲在1.0kg和对比例4的水冲在1.4kg时,所染织物布面均有刮痕。实施例7-9在浴比为1:12,水冲1.2kg,亚矶水流缸单管载布量200kg时改变机速(230m/min、240m/min、250m/min)进行试验作为实施例7、8、9,机速对刮痕的影响结果记录如表3所示。对比例5-6在浴比为1:12,水冲1.2kg,亚矶水流缸单管载布量200kg时改变机速为220m/min、260m/min作为对比例5、6,机速对刮痕的影响结果记录如表3所示。表3由表3数据可以看出,实施例7、8、9的机速为230m/min、240m/min、250m/min时布面无刮痕,滑差小,在15-19之间,因此优选机速240m/min。对比例5、6的机速在220m/min及260m/min时均有刮痕。对比例6的机速为260m/min时产生刮痕的原因可能与机速过快有关,而对比例5的机速220m/min时产生刮痕的可能原因为机速过慢,圈时过长导致,尤其是高温时布被拉伸,圈时更长,相对滑差变大。实施例10-11每个缸种都有其设计载布参数,但在实际生产中还要根据所染织物的规格、织物的结构、染料组合等确定合适的载布量,避免生产中出现品质问题,选用170g/m2锦纶弹力织物对亚矶单管机型进行载布量试验,以载布量为190kg、200kg为实施例10、11,载布量对刮痕的影响结果如表4。对比例7-8选用170g/m2锦纶弹力织物对亚矶单管机型进行载布量试验,以载布量为210kg、220kg为对比例7、8,载布量对刮痕的影响结果如表4。表4由表四数据可以看出,实施例10、11的载布量为190kg、200kg时的布面无刮痕。而对比例7、8的载布量为210kg、220kg时的布面刮痕均较严重,且行机不顺畅。考虑到要最大化利用生产设备,提高产能,在实际生产中应将亚矶单管载布量控制在190kg-200kg为最佳。大货生产表现跟踪用改进后的条件:浴比1:12,水冲1.2kg,机速240m/min,亚矶单管载布量190kg-200kg应用大货生产,染大红、深紫、深红、黑色31缸大货,布面均无刮痕。沾色牢度测试将本发明的染色工艺实施例1-11染色后的锦纶织物的沾色牢度进行测试,测试结果如表5所示。表5色变等级(级)毛沾色腈纶沾色涤纶沾色锦纶沾色棉沾色醋纤沾色1~54~555555由表5的数据可以看出,本发明的染色工艺染色后的锦纶织物,对不同材料的的沾色牢度均较高,毛沾色牢度为4~5级,腈纶沾色、涤纶沾色、锦纶沾色、棉沾色、醋纤沾色均可达5级。综上,在用eriofast活性染料染深色时浴比选用(1:11)~(1:13),水冲1.1~1.3kg,机速230~250m/min,亚矶单管载布量190kg~200kg时生产大货,可以有效的避免布面刮痕产生。亚矶多管对锦纶织物用eriofast活性染料染深色时,只要将载布量在亚矶单管载布量的基础上增加相应倍数即可,其它参数不变。本发明通过上述实施例来说明本发明的详细工艺设备和工艺流程,但本发明并不局限于上述详细工艺设备和工艺流程,即不意味着本发明必须依赖上述详细工艺设备和工艺流程才能实施。所属
技术领域:
的技术人员应该明了,对本发明的任何改进,对本发明产品各原料的等效替换及辅助成分的添加、具体方式的选择等,均落在本发明的保护范围和公开范围之内。当前第1页12